Измерение производительности питателя при выпуске угля из подкровельной толщи на основе технологии машинного зрения
Автор: Никитенко М.С., Кизилов С.А., Захаров Ю.Н., Худоногов Д.Ю., Игнатова А.Ю.
Журнал: Горные науки и технологии @gornye-nauki-tekhnologii
Рубрика: Разработка месторождений полезных ископаемых
Статья в выпуске: 4 т.7, 2022 года.
Бесплатный доступ
Технология выпуска угля из подкровельной пачки использует так называемый гравитационный выпуск, когда уголь выпускается из-под кровли «самотеком» под действием силы тяжести. Выпуск при этом можно производить на главный конвейер (забойный - расположенный в закрепленном пространстве), центральный (в западной литературе - задний) и хвостовой (завальный - расположенный в незакрепленном пространстве). Наиболее распространенными на данный момент времени являются комплексы с выпуском на завальный конвейер. Целью исследования является измерение производительности механизированного пластинчатого питателя, подающего уголь от выпускного окна крепи на конвейер в технологии отработки мощных пластов с выпуском на забойный конвейер. Для достижения цели предлагается осуществлять измерение объема с применением технологии машинного зрения. Исследованы способы расчета единичного объема на измерительном участке на трехмерной модели. Проведены лабораторные исследования, в рамках которых оценены относительные погрешности. Исследования позволили формализовать: способ сбора данных для расчета единичного объема угля; методику расчета единичного объема на измерительном участке; способ расчета производительности питателя на основе системы машинного зрения, а также подходы для физического упрощения сцены, исследуемой машинным зрением. Относительная погрешность менее 10 % при имеющейся точности измерений для построения карты высот говорит о достаточности для инженерного использования предложенного способа расчета. Разработанный математический аппарат для расчетов единичного объема угля на измерительном участке и измерения производительности питателя позволяют создавать алгоритмическое обеспечение с использованием элементарных математических функций: сложение, вычитание, умножение и деление. Данный аспект важен, так как снижает планку требований к среде разработки программного обеспечения, а соответственно, расширяет номенклатуру аппаратных средств, пригодных для выполнения задач расчета производительности питателя.
Горное дело, добыча угля, лавный комплекс, производительность, выпуск угля, забойный конвейер, объем горной массы, машинное зрение, распознавание образов, распознавание видеоизображений, карта высот
Короткий адрес: https://sciup.org/140296153
IDR: 140296153 | DOI: 10.17073/2500-0632-2022-09-22
Текст научной статьи Измерение производительности питателя при выпуске угля из подкровельной толщи на основе технологии машинного зрения
Технология выпуска угля из подкровельной пачки использует так называемый гравитационный выпуск, когда уголь выпускается из-под кровли «самотеком» под действием силы тяжести [1, 2]. Выпуск при этом можно производить на главный конвейер (забойный – расположенный в закрепленном пространстве), центральный (в западной литературе – задний) и хвостовой (завальный – расположенный в незакрепленном пространстве) [3]. Наиболее распространенными на данный момент времени являются комплексы с выпуском на завальный конвейер [4–7].
В Российской Федерации предложен подход осуществлять управляемый выпуск угля, перемещая поток горной массы с помощью механизированного питателя из выпускного окна на главный конвейер [8, 9]. К его основным преимуществам относятся небольшие габаритные размеры секции крепи, сравнимые с габаритами крепи для классического лавного очистного комплекса, а также возможность производить одновременный групповой выпуск из нескольких секций, реализуя перспективные технологии добычи угля с использованием волнового и площадного выпуска [8, 9]. Реализация столь сложных технологических https://mst.misis.ru/
2022;7(4):264–273
процессов, как волновой и площадной выпуск, требует разработки системы, контролирующей в реальном времени объём угля, подаваемый питателем из выпускного окна крепи на главный конвейер [9–12]. При групповом выпуске превышение объёма подачи угля выше расчётного значения из одного питателя может привести к перегрузу конвейера у точек разгрузки следующих питателей и просыпанию угля.
В ФИЦ УУХ СО РАН (FRC CCC SB RAS) на основе дискретно-событийных моделей рассчитаны оптимальный объем выпускаемого угля для каждой секции крепи, последовательность и рациональное количество работающих питателей, позволяющие обеспечить равномерность выпуска и максимальную загрузку конвейера [13–15]. Однако шахтного оборудования, способного эффективно выполнять задачу по измерению объема выпускаемого пластинчатым питателем угля, в заданных условиях на рынке не представлено.
В мировой практике известны решения, применяющие источники когерентного света (лазерные излучатели) подсветки сыпучих веществ для определения их объема. Одним из распространенных применений таких устройств являются измерители производительности конвейеров машинным зрением [16–19], которые с помощью триангуляции создают массив значений, характеризующий высоту слоя перемещаемого конвейером вещества в месте его пересечения лазерным лучом. Однако данный способ позволяет измерять только объем сыпучего вещества, перемещаемого через сканер с постоянной скоростью. Существует оборудование, которое использует лазерные 3D-сканеры (трехмерные LIDAR) для определения объемов сыпучих веществ, перемещаемых с разными скоростями или находящихся в статичном состоянии [20, 21]. Однако вопрос применения технологии в условиях угольных шахт слабо проработан за редким исключением, как, например, австралийский проект ExScan, который пока не вышел на стадию коммерческих продаж и является штучным экспериментальным изделием [22].
Проведенный анализ показал, что в литературе представлено достаточно много работ, связанных с лазерной оценкой объема, работающих с применением машинного зрения. Однако конкретных подходов к измерению объема горной массы, перемещаемой питателем в условиях выпуска угля подкровельной толщи не выявлено. Проблема перегруза в современных комплексах с гравитационным выпуском решается малым количеством одновременно работающих на выпуск секций – от 1 до 5 шт. При этом используется дополнительный конвейер, что сводит возможность перегруза до минимума. Также расположение конвейера в незакрепленном пространстве делает последствия перегруза менее опасными, чем при выпуске на главный конвейер, но может приводить к увеличению потерь угля. На данный момент времени автоматизированными средствами при выпуске угля факт наличия угля не фиксируется. При подходе, описанном в [3], заслонка выпускного окна открывается на заданный промежуток времени, а за- тем закрывается без обратной связи и учета успешности проведения выпуска. Наличие выпускаемого угля фиксируется визуально в районе перегружателя. Главной проблемой измерения производительности пластинчатого питателя является отсутствие потока угля с постоянной скоростью, так как пластинчатый питатель выполняет возвратно-поступательные движения с частотой близкой к 1 Гц. Такой тип питателя перемещает уголь дискретно небольшими партиями с частотой дискретизации, равной частоте работы питателя. Конструктивные особенности и способ работы питателей подобного типа не позволяют применить стандартные способы измерения производительности на основе взвешивания или сканирования формы потока на конвейерах.
Для опытно-конструкторской разработки задачу измерения объёма угля, подаваемого каждым питателем на конвейер, авторы разделили на несколько подзадач:
-
1. Разработать способ расчета производительности исходя из данных о единичном объеме и скорости его замещения.
-
2. Выбрать математический аппарат расчета единичного объёма угля, находящегося на измерительном участке.
-
3. Разработать методику для первичной верификации и валидации расчета единичного объёма угля, находящегося на измерительном участке.
-
4. Провести первичные верификацию и валидацию расчета единичного объёма угля, находящегося на измерительном участке.
-
5. Провести анализ результатов первичных верификации и валидации, на основе которого выбрать алгоритм для получения расчетных данных системой машинного зрения.
Методы
Первоначально определено место проведения замеров вдоль зоны перегрузки угля питателем от впускного окна до конвейера. Практически на всем пути транспортировки угля от впускного окна до конвейера работа питателя при возвратно-поступательном движении может менять порядок распределения выпускаемой горной массы при её перемещении. Единственный участок транспортировки, на котором направление движения угольной массы приобретает определённое направление и постоянную скорость замещения, – выпускной лоток. Выпускной лоток представляет собой откидной элемент, смонтированный на питателе, по которому уголь поступает с питателя на конвейер через технологический проем между ним и секцией крепи. Одним из возможных методов расчета производительности питателя является расчет объема угля на некотором заданном участке лотка питателя (измерительном участке) с последующим определением времени замещения данного участка новой порцией угля. Математический аппарат для расчета производительности питателя в этом случае сводится к расчету объёма тела, представляющего собой объём угольной массы на измерительном участке в единицу времени:
2022;7(4):264–273
р пит
= v ед сиу,
где Р пит – производительность питателя, м3/с; V ед – единичный объем угля на измерительном участке, м3; Т сиу – частота смены измерительного участка, с-1, прямо пропорциональна частоте работы питателя и поступает в формулу расчета от средств автоматизации лавного комплекса.
Исходя из этого задаются входные данные, необходимые для расчета объёма угля на измерительном участке. Соответственно, для измерения объема выпускаемого угля в единицу времени необходимо измерить его объем и скорость замещения на измерительном участке. Оптимальная производительность питателя в соответствии с дискретно-событийной моделью выпуска [13] рассчитывается в килограммах за секунду. Таким образом, через насыпную плотность угля рассчитывается производительность
Наличие светового маркера значительно упрощает распознавание видеосцены машинным зрением, создавая на картинке сцены четкий контрастный по освещённости и цвету участок относительно других объектов, который требуется обработать, исключив лишнюю информацию из изображения на стадии предпроцессинга. Такой подход определит алгоритмы распознавания образов, снизив требования к компьютерной мощности устройства, на котором производится обработка видеосигнала.
Результаты
Для расчета объема угля на измерительном участ-
ке измерялась его высота только в точках пересечения световых маркеров, формируя таким образом карту
высот измерительного участка.
Представим измерительный участок в виде сово-
Р пит.
кг/с = ρ уг ⋅ V ед ⋅ T сиу ,
где ρ уг – насыпная плотность угля на участке разрабатываемого пласта.
Скорость замещения является величиной, получаемой на основании данных при пусконаладочных работах, и зависит от фракции выпускаемого угля и частоты работы питателя. При измерении объема форма измерительного участка – прямоугольник. Измеряемая угольная масса, находящаяся на площади участка измерения, имеет переменную высоту по всей его площади. Для расчёта объёма угля необходимы данные, характеризующие его высоту относительно уровня измерительного участка в заданных точках.
Наиболее очевидным выбором для получения набора данных, необходимых для работы математического аппарата, является система машинного зрения, совмещенная с нейросетевым интерфейсом распознавания образов [13, 14]. Однако для корректной работы нейросети, распознающей образы, как правило, требуется значительная обучающая выборка, которой не будет до введения в опытную работу лавного комплекса с соответствующей конструкцией. А низкое качество изображения, получаемого с современных видеокамер, сертифицированных для установки на лавных комплексах, ограничивает возможность применения классических алгоритмов распознавания видеосцены. Это однозначно говорит об актуальности и необходимости упрощения анализируемой видеосцены до её компьютерной обработки.
Для решения такой задачи предложено спроецировать на исследуемую поверхность прямоугольную сетку лазерных лучей контрастного цвета (далее – световые маркеры). Световые маркеры обеспечат проекцию на неровную поверхность и изменят свою форму с прямолинейной на форму того участка, на который он спроецировался, что позволит получить информацию о форме участка под световым маркером. Следующий шаг – определить координаты светового маркера относительно уровня измерительного участка в любой его точке в ручном режиме без использования методик нейросетевого распознавания видеоряда.
купности параллелограммов с равными по размерам основаниями и высотой, соответствующей данным из карты высот. Сумма объемов полученных параллелограммов будет являться объемом фигуры на исследу-
емом участке.
Первичная верификация предложенного способа выполнена на референсной фигуре с криволинейной поверхностью – полусфере, объём которой можно предварительно рассчитать по формуле, задав габа-
ритные размеры, сопоставимые с размером измерительного участка на реальном питателе. Ожидаемый объем полусферы V ож рассчитан по формуле (1) и составил 261,8 · 106 мм3:
V ож
3 п
.
Входные данные: радиус r , мм, 500; шаг сетки световых маркеров по оси x, мм, X = 50 – const; шаг сетки световых маркеров по оси y, мм, Y = 50 – const; координата точки по оси x – хi ; координата точки по оси y – y n ; высота слоя, мм, на точке с координатами – h x,y .
Таким образом, эталонная фигура, объём которой рассчитывается согласно предложенному методу, имеет в своём основании круг радиусом 500 мм. Зона измерения представлена квадратом, имитирующим измерительный участок на поверхности питателя, размером 1000 × 1000 мм. Референсная фигура вписана в зону измерения. Световые маркеры представлены сечениями на зоне измерения по вертикали и горизонтали с шагом 50 мм в обоих направлениях.
Для сбора данных предложено произвести условное рассечение референсной фигуры по местам прохождения световых маркеров, получив таким образом набор малых фигур. Тогда малая фигура представляет собой объёмное тело с двумя равными параллельными боковыми поверхностями, которые являются криволинейными трапециями, полученными в результате рассечения полусферы в координате h y . Объем малой фигуры V 1 можно рассчитать по формуле:
V = S бп ■ Y, (4)
где S бп – площадь боковой поверхности ; Y – размер малой фигуры по оси у . Площадь криволинейной
2022;7(4):264–273
трапеции – вычисляется с помощью определённого криволинейного интеграла. При расчёте производительности питателя не требуется высокая точность в результатах, расчетный объём пренебрежимо мал относительно общей секундной производительности, но важна скорость проводимых вычислений. Для проведения расчета высоты прямоугольников hx с шагом Х заносятся в таблицу. Полученная таблица представляет карту высот для расчета объема малой фигуры. Тогда S бп можно рассчитать по формуле:
xг
S бп = X £ h ; (5)
x = 1
соответственно:
x 2
-
V , = YX £ h. . (6)
x = 1
Следовательно, объем всей эталонной фигуры V расч представлен в виде суммы объемов всех прямоугольных параллелепипедов, входящих в состав всех малых фигур, на которые была разделена референсная фигура. Тогда V расч рассчитывается по формуле:
y 2 x 2
V расч = XY ££ h x,y , (7)
y = 1 x = 1
где y2x2
££h.,y - y=1 x=1
сумма всех высот, измеренных в сечениях образца, с координатами h x,y .
Референсная фигура была построена с использованием CAD системы моделирования FreeCAD. Полученная объёмная модель полусферы последовательно рассекалась по оси Х с заданным в условии шагом, затем создавалась карта высот криволинейной поверхности в каждом полученном сечении, которое представляло собой малую фигуру. Высоты измерялись с шагом X . Процесс последовательного получения координат высот в качестве данных для формирования карты высот показан на рис. 1.
Далее данные высот занесены в таблицу, общий вид которой показан на рис. 2.
Полученная карта высот имитирует информацию от системы машинного зрения. Для контроля достоверности результатов измерений по данным таблицы построена диаграмма поверхности, показанная на рис. 3, а .
Диаграмма поверхности, построенная с использованием MS Excel, показывает, что замеры при построении карты высот выполнены без грубых ошибок и ими можно пользоваться для первичной верификации способа расчета объёма.
Как видно из рис. 1, сечениями Y образуются малые тела, имеющие плоские боковые стороны и основание, ограниченные сверху криволинейной поверхностью, что соответствует предложенному методу расчета. Таким образом, вся референсная фигура представляется в виде набора соответствующих прямоугольных параллелепипедов, имеющих основание размером X на Y . На рис. 3, б показано изображение упрощенного референсного тела, полученного в результате преобразования всех малых тел в прямоугольные параллелепипеды.

аб
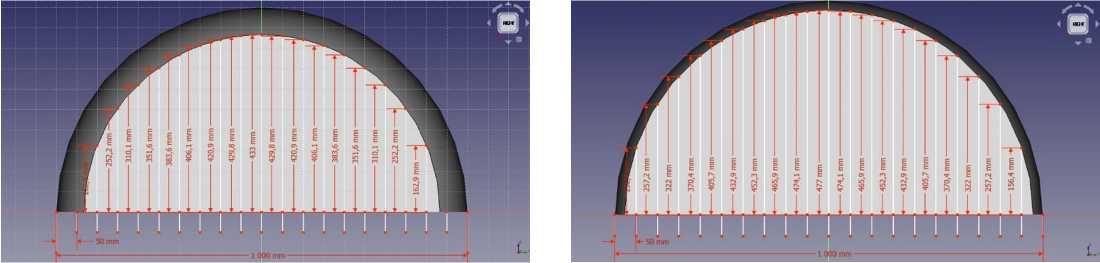
вг
Рис. 1. Процесс получения координат высот вершин прямоугольников по сечениям для формирования карты высот: а – сечение 2; б – сечение 4; в – сечение 6; г – сечение 8
2022;7(4):264–273
Координаты высот |
h х |
h x + 1 |
hx + i |
|
h y |
h x, y |
h x + 1, y |
h x + i, y |
|
h y +1 |
h x, y + 1 |
h x + 1, y + 1 |
h x + i , y + 1 |
|
h y + n |
x, y + n |
h x + 1, y + n |
x + i , y + n |
Рис. 2. Общий вид таблицы данных карты высот: hx,y – высота от нулевой отметки с координатами x , y до кривой, ограничивающей поверхность сечения в месте разреза
Chart Title
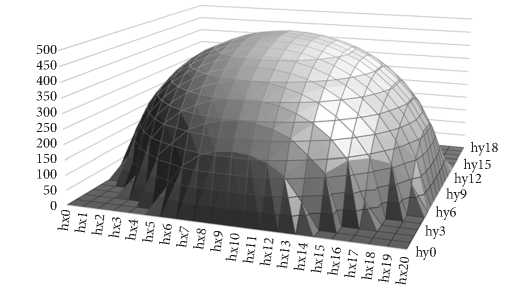
0–50 50–100 100–150 150–200 200–250 250–300 300–350 350–400 400–450 450–500
а
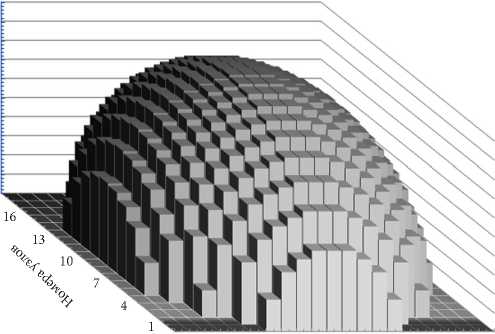

Номера сечений
б
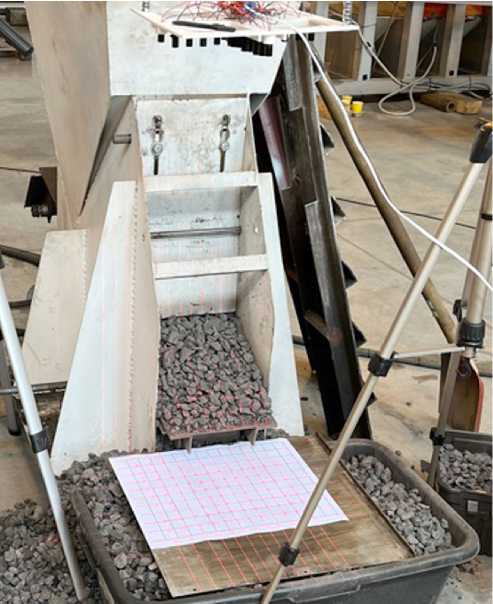
Рис. 4. Процесс валидации методики на модели измерительного участка
Рис. 3. Представление референсной фигуры: а – в виде диаграммы поверхности по данным измерений; б – полученное методом прямоугольников на основе измерения
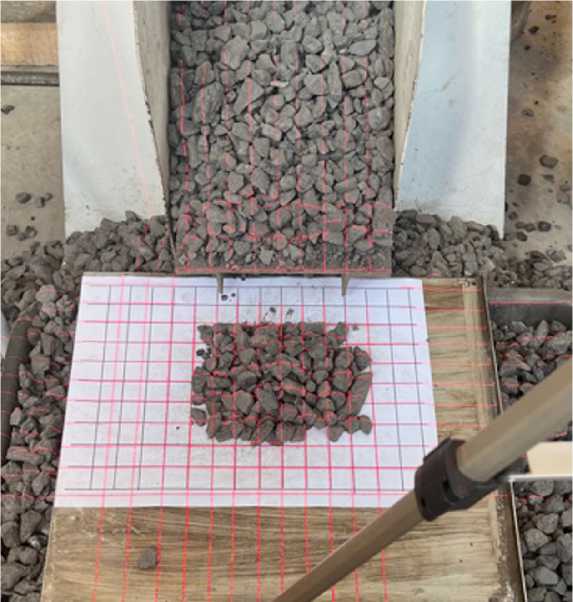
2022;7(4):264–273
Рассчитанный по формуле (7) объем референсной фигуры составил 259,3 · 106 мм3. Относительная погрешность измерения – 0,95 % от ожидаемого результата.
Для валидации методики проведена серия лабораторных экспериментов с применением средств проецирования лазерной сетки на плоскую поверхность (измерительный участок), имитирующую выпускной лоток питателя секции крепи. В ходе экспериментов на измерительном участке размещался известный объем угля (рис. 4) с заранее измеренными насыпной плотностью и весом, что позволило рассчитать его объем математически.
Для построения карты высот используемый слой угля зондировался металлической спицей в месте пересечения лазерных лучей, затем уровень угля фиксировался на спице маркером. По данным измерений строилась карта высот, которая представлена в табл. 1, где y – координата точки измерения в поперечном сечении измерительного участка с точкой отсчета со стороны питателя, а x –координата точки измерения в продольном сечении измерительного участка с точкой отсчета в крайней левой части координатной сетки.
Таблица 1
Карта высот угля на измерительном участке, мм
h x, y |
x 1 |
x 2 |
x 3 |
x 4 |
x 5 |
x 6 |
x 7 |
x 8 |
y 1 |
10 |
27 |
8 |
5 |
16 |
16 |
0 |
0 |
y 2 |
14 |
23 |
11 |
27 |
15 |
26 |
23 |
0 |
y 3 |
20 |
25 |
35 |
34 |
40 |
13 |
35 |
17 |
y 4 |
18 |
19 |
34 |
43 |
32 |
29 |
27 |
12 |
y 5 |
25 |
20 |
30 |
25 |
26 |
21 |
20 |
0 |
y 6 |
20 |
5 |
12 |
26 |
28 |
21 |
13 |
0 |
y 7 |
0 |
0 |
17 |
13 |
10 |
8 |
24 |
0 |
Исходя из насыпной плотности угля и веса отобранной пробы рассчитан ожидаемый объем V ож = 0,74 · 106 мм3.
Размер ячеек сетки световых маркеров hx = 25 мм, hy = 25 мм.
Использовав формулу (5), получаем расчетный объем V расч = 0,63 · 106 мм3.
Относительная ошибка V расч от V ож составила 13,55 %.
Полученная относительная ошибка достаточно велика, что связано с двумя факторами: 1 – несовершенство примененных методов измерения; 2 – упрощение методики расчета объема, плохо учитывающее неоднородность поверхности объема угля и его распределение по измерительному участку.
Для компенсации в расчете неоднородности поверхности объема измеряемого угля предложен расчет методом прямоугольников с двойным пересчетом в противоположных направлениях и последующим усреднением результата:
^ расч1
( У 2 - 1 X 2 X 2 У 2 X 2 X 2 A
22 h x.y + 2 h .„ 2 - i + 22 h .„ + 2 hti yx
^ y = 1 X = 1 X = 1 y = 2 X = 1 X = 1 у
Применим формулу (8) к данным из табл. 1. Тогда V расч1 = 0,67 · 106 мм3.
Относительная ошибка V расч1 от V ож составила 8,87 %.
Обсуждение результатов
Использованный в эксперименте способ построения карты высот слоя угля имеет погрешность, так как работа ведется с насыпным материалом переменной фракции, соответственно, при проведении измерения часто происходят смещения частиц. Несмотря на это представленный выше подход показывает точность при прямом расчете объема с относительной погрешностью менее 14 %. Применение измерений с проходом в два противоположных направления относительно поперечного сечения измерительного участка с последующим усреднением результата позволяет снизить относительную погрешность для данного случая практически на 5 %. Результат в 5 % является непостоянной величиной и зависит от распределения объема угля относительно поперечного сечения измерительного участка. Относительная погрешность менее 10 % при имеющейся точности измерений для построения карты высот говорит о достаточной для инженерного использования точности предложенного способа расчета и небольшом влиянии погрешностей отдельных измерений на общий результат расчета объема.
На данный момент времени, учитывая результаты валидации, можно составить формулу расчета производительности питателя, кг/с, подставив (8) в (2). Тогда:
p пит.кг/с—
^y 2 - 1 x 2 x 2 y 2 x 2 X 2 A
EXhxy + Xhxy2-1+ XXhxy + Xhx2 YX v y—1 X—1 X—1 y—2 x—1 x —1 ^
(9) р уг Т сиу .
Полученная формула (9) позволила начать разработку программного обеспечения для машинного зрения, измеряющего высоту слоя угля в точках пересечения световых маркеров.
Заключение
Предложенный способ позволяет проводить оперативную оценку объёма горной массы, перемещаемой пластинчатым питателем с использованием технологий машинного зрения. Решена задача контроля объёма выпускаемого питателем угля при отработке мощных пластов лавными комплексами с выпуском на забойный конвейер с точностью, достаточной для практического применения. Разработанный математический аппарат для расчетов единичного объема угля на измерительном участке (формула (8)) и измерения производительности питателя (формула (9)) позволяет создавать алгоритмическое обеспечение с использованием элементарных математических функций: сложение, вычитание, умножение и деление. Данный аспект важен, так как снижает планку требований к среде разработки программного обеспечения, а соответственно, расширяет номенклатуру аппаратных средств, пригодных для выполнения задач расчета производительности питателя.
2022;7(4):264–273
2022;7(4):264–273
2022;7(4):264–273
Список литературы Измерение производительности питателя при выпуске угля из подкровельной толщи на основе технологии машинного зрения
- Клишин В. И., Анферов Б. А., Кузнецова Л. В. Направления совершенствования разработки мощных пластов с выпуском угля подкровельной толщи. В: Инновации в топливно-энергетическом комплексе и машиностроении (ТЭК-2017). Сборник трудов Международной научно-практической конференции. Кемерово: Кузбасский государственный технический университет имени Т.Ф. Горбачева; 2017. С. 57-63.
- Клишин В. И., Клишин С. В. Состояние и направление развития технологии разработки мощных угольных пластов механизированными крепями с выпуском. Известия Тульского государственного университета. Науки о Земле. 2019;(1):162-174.
- Peng S. S. Longwall mining. 3rd edition. Leiden: CRC Press/Balkema; 2020. 562 p.
- Le T. D., Mitra R., Oh J., Hebblewhite B. A review of cavability evaluation in longwall top coal caving. International Journal of Mining Science and Technology. 2017;27(6):907-915. https://doi.org/10.1016/j.ijmst.2017.06.021
- Mundry S., Sandgathe C. Automated Cat longwall top coal caving. In: Efficient Mining of High Seams with Automated LTCC Operations. Caterpillar Inc.; 2018. Pp. 12-14. URL: http://s7d2.scene7.com/is/content/Caterpillar/CM20180716-40601-27335 (Дата обращения: 01.08.2022).
- Medhurst T., Rankine R., Kelly M. Development of a method for a longwall top coal caveability assessment. In: Coal operators’ conference. 12-14 February 2014. Wollongong: University of Wollongong; 2014. Pp. 42-50. URL: https://ro.uow.edu.au/cgi/viewcontent.cgi?article=2159&context=coal
- Le T. D. Longwall Top Coal Caving mechanism and cavability assessment. [PhD thesis in Mining Engineering]. Sydney; 2018. https://doi.org/10.26190/unsworks/20236
- Клишин В. И., Шундулиди И. А., Ермаков А. Ю., Соловьев А. С. Технология разработки запасов мощных пологих пластов с выпуском угля. Новосибирск: Наука; 2013. 248 с.
- Клишин В. И., Опрук Г. Ю., Варфоломеев Е. Л., Борисов И. Л. Взаимодействие механизированных крепей с межслоевой толщей в системах с выпуском угля. Горный информационно-аналитический бюллетень. 2018;(S48):87-94. https://doi.org/10.25018/0236-1493-2018-11-48-87-94
- Кизилов С. А., Никитенко М. С., Неоджи Б. и др. Автоматизация управления технологическими процессами при отработке мощных пластов с выпуском угля подкровельной толщи. Горная промышленность. 2017;(6):96-99. URL: https://mining-media.ru/en/articles/articleen/13196-automation-of-processcontrol-in-thick-seam-mining-with-top-coal-caving
- Nikitenko M. S., Kizilov S. A., Nikolaev P. I., Kuznetsov I. S. Technical devices of powered roof support for the top coal caving as automation objects. In: IOP Conference Series: Materials Science and Engineering. XI All-Russian Scientific and Practical Conference (with international participation) “Automation systems in education, science and production, 2017”. 14-16 December 2017, Novokuznetsk, Russian Federation. 2017;354:012014. https://doi.org/10.1088/1757-899X/354/1/012014
- Nikitenko M. S., Kizilov S. A. Technical and technological platforms for creating robotized complexes for the development of thick seam deposits. In: IOP Conference Series: Earth and Environmental Science, Volume 377, International Scientific and Research Conference on Knowledge-based technologies in development and utilization of mineral resources. 4-7 June 2019, SibSIU, Novokuznetsk, Russia. 2019;377:012033. https://doi.org/10.1088/1755-1315/377/1/012033
- Стародубов А. Н., Зиновьев В. В., Клишин В. И., Крамаренко В. А. Применение имитационного моделирования для исследования режимов выпуска угля подкровельной толщи. В: 9-я всероссийская научно-практическая конференция по имитационному моделированию и его применению в науке и промышленности. Екатеринбург; 2019. С. 540-547. URL: http://simulation.su/uploads/files/default/2019-immod-540-547.pdf
- Starodubov A., Sinoviev V., Totskiy A., Klishin V. Review of mining equipment with controlled robotized subvel caving with specialized software. In: E3S Web of Conferences. Vth International Innovative Mining Symposium. 2020;174:03012. https://doi.org/10.1051/e3sconf/202017403012
- Starodubov A. N., Sinoviev V. V., Klishin V. I. The development of simulating system of robotized technologies for thick and acute coal seams. Journal of Physics: Conference Series. 2021;1749(1):012040. https://doi.org/10.1088/1742-6596/1749/1/012040
- Heyduk A. Bulk density estimation using a 3-dimensional image acquisition and analysis system. In: E3S Web of Conferences. Mineral Engineering Conference MEC2016. 2016;8:01060. https://doi.org/10.1051/e3sconf/20160801060
- Heyduk A. Laser triangulation in 3-dimensional granulometric analysis. Archives of Mining Sciences. 2016;61(1):15-27. https://doi.org/10.1515/amsc-2016-0002
- Min F., Lou A., Wei Q. Design and experiment of dynamic measurement method for bulk material of large volume belt conveyor based on laser triangulation method. In: IOP Conference Series Materials Science and Engineering. 7th Annual International Conference on Material Science and Environmental Engineering. 15-16 November 2019. Wuhan, Hubei, China. 2020;735(1):012029. https://doi.org/10.1088/1757-899X/735/1/012029
- Fojtík D. Measurement of the volume of material on the Conveyor Belt measuring of the volume of wood chips during transport on the Conveyor Belt using a laser scanning. In: Proceedings of the 2014 15th International Carpathian Control Conference (ICCC). 28-30 May 2014. Velke Karlovice, Czech Republic. Pp. 121-124. https:// https://doi.org/doi.org/10.1109/CarpathianCC.2014.6843581
- Amorim L. L., Mutz F., De Souza A. F. et al. Simple and effective load volume estimation in moving trucks using lidars. In: 32nd SIBGRAPI Conference on Graphics, Patterns and Images (SIBGRAPI). 28-30 October 2019. Rio de Janeiro, Brazil. Pp. 210-217. https://doi.org/10.1109/SIBGRAPI.2019.00036
- Zeng F., Wu Q., Chu X., Yue Z. Measurement of bulk material flow based on laser scanning technology for the energy efficiency improvement of belt conveyors. Measurement. 2015;75:230-243. https://doi.org/10.1016/j.measurement.2015.05.041
- Dunn M., Reid P., Malos J. Development of a protective enclosure for remote sensing applications-case study: laser scanning in underground coal mines. Resources. 2020;9(5):56. https://doi.org/10.3390/resources9050056
- Macpherson T., Churchland A., Sejnowski T. et al. Natural and artificial intelligence: a brief introduction to the interplay between AI and neuroscience research. Neural Networks. 2021;144:603-613. https://doi.org/10.1016/j.neunet.2021.09.018
- Акулов М. С., Гладких С. А., Ланкина М. Ю., Бакланов А. Н. Обработка фото и видеоизображений с помощью нейронных сетей в программе LABVIEW. Современные наукоемкие технологии. 2019;(3-1):12-17. URL: https://top-technologies.ru/ru/article/view?id=37434