Изнашивание вооружения ковша карьерного одноковшового экскаватора
Автор: Хромой Михаил Рувимович, Свинарчук Василий Петрович, Свинарчук Петр Васильевич
Журнал: Горные науки и технологии @gornye-nauki-tekhnologii
Статья в выпуске: 8, 2010 года.
Бесплатный доступ
Исследованы особенности изнашивания вооружения ковша карьерного одноковшового экскаватора. Разработана конструкция вооружения ковша экскаватора, сохраняющая постоянный угол заострения зуба в течение длительного периода его эксплуатации. Study of wear characteristics of weapons scoop shovels career. The design of the weapons shovel bucket, retain permanent tooth wedge ange for a long time is developed.
Карьерный одноковшовый экскаватор, вооружение ковша, процесс копания, эффект самозатачивания
Короткий адрес: https://sciup.org/140215185
IDR: 140215185
Текст научной статьи Изнашивание вооружения ковша карьерного одноковшового экскаватора
Современные карьерные одноковшовые экскаваторы (рис. 1) производят разрушение массива породы последовательным отделением стружки. Процесс отделения породы от массива включает в себя резание, перемещение породы в ковше и трение ковша о породу. В прочных горных породах, предварительно разрыхленных взрывом, экскаватор не срезает стружку, термин «резание» принимается условно, а рабочий процесс представляет собой преодоление сопротивлений, возникающих при поступлении в ковш отдельных кусков породы различной грануляции.
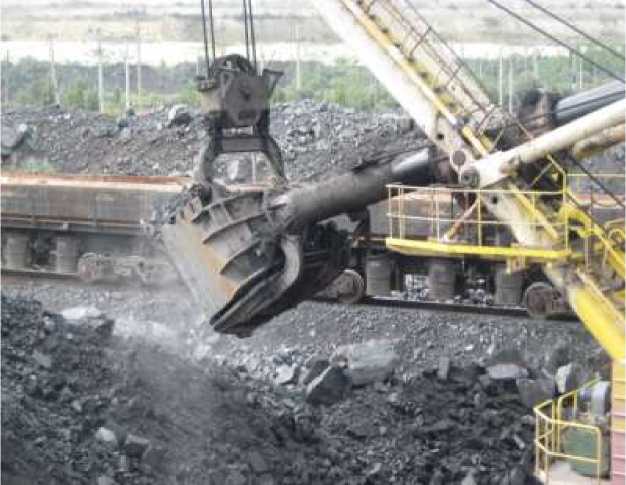
Рис. 1. Карьерный гусеничный экскаватор ЭКГ-10 на участке перегрузки руды Стойленского карьера
Ковш экскаватора перемещается в двух направлениях. Одно из них -главное движение - подъем ковша, при котором происходит отделение стружки, а другое - напор, при котором изменяется её толщина. Скорость напора ковша значительно меньше скорости его подъема, а соотношение этих двух скоростей определяет траекторию движения ковша в вертикальной плоскости [1].
Вооружение ковша карьерного экскаватора представляет собой зубья клиновидной формы, облегчающие процесс разрушения породы за счет увеличения на него удельной нагрузки до 2,5 раз.
Кинематические и геометрические параметры зуба определяют взаимное положение его рабочих граней и поверхности забоя в процессе перемещения зуба в пространстве с некоторой скоростью (у).Траектория перемещения каждого зуба ковша экскаватора (рис. 2) в процессе работы определяется взаимно перпендикулярными векторами скоростей подъема (vп) и напора(у н ).
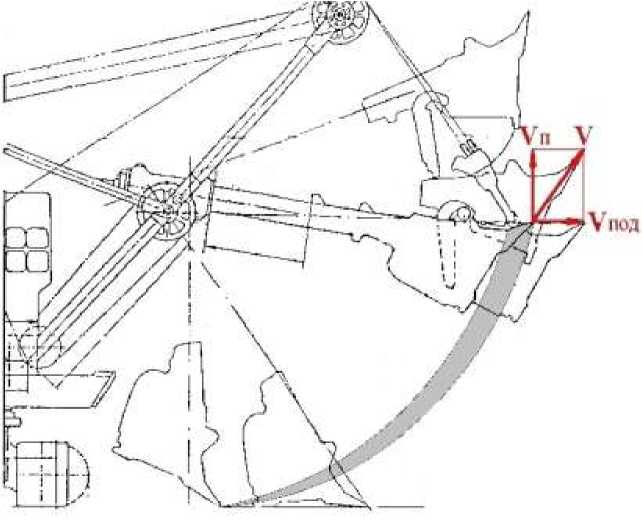
Рис. 2. Траектория перемещения ковша и его вооружения в процессе экскавации
В процессе экскавации зубья ковша подвергаются абразивному изнашиванию, приводящему к изменению их формы и затуплению. С затуплением зубьев требуются большие усилия для отделения стружки от породного массива. Износ зубьев до величин, превышающих допускаемые заводскими инструкциями по эксплуатации, вызывает увеличение сопротивления экскавации примерно в полтора раза [2].
В настоящее время на железорудном карьере ОАО «Стойленский ГОК» используются сменные зубья ковша, отливаемые из высокамарганцовистой стали 110Г13Л. В соответствии с инструкцией по технической эксплуатации, величина износа зубьев ковша не должна превышать 120^140 мм, что соответствует углу заострения зуба (α) равному 60º (рис.3). Зубья с износом более 140мм считаются непригодными для дальнейшей эксплуатации. Однако, на практике в условиях дефицита зубьев их предельный износ может достигать до 200 мм (рис. 3а), что соответствует углу заострения зуба (α) превышающему 60º. Работа экскаваторов с такими зубьями характеризуется увеличенными нагрузками на основные привода и металлоконструкцию, ухудшением условия наполнения ковша, повышенным износом режущей кромки и передней стенки ковша.
Зубья ковша конструкции ООО «ИЗ КАРТЭКС», отвечая основным прочностным требованиям, имеют недостаточную износостойкость с существенным увеличением начального угла (αо) заострения зуба с αо = 22…25º до α ≥ 60º (рис.3). При работе в тяжелых условиях добычных забоев Стойленского карьера ресурс этих зубьев не превышает 4 – 6 смен.
Угол резания δ оказывает значительное влияние на сопротивление породы резанию и определяется по зависимости
δ = α + γ з , º (1)
здесь α – угол заострения зуба, º; γ з – задний угол зуба, º.Угол выдержан в пределах 5…8º (см. рис. 3).
Vn V
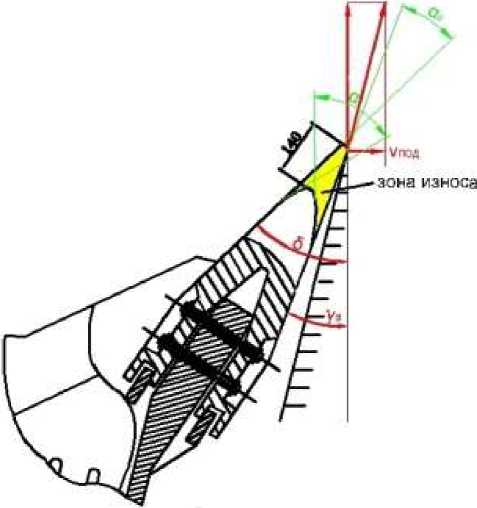
Рис. 3. Зуб конструкции « ИЗ КАРТЭКС» с предельным износом в 200 мм, и предельным углом заострения α ≥ 60º
Угол резания (δ) устанавливается в пределах 30…40º. Увеличение угла резания от 40 до 60º удваивает лобовые сопротивления внедрению зуба, а чрезмерное уменьшение угла резания (менее 30º) может сопровождаться ростом сопротивления, особенно при резании вдоль напластования горных пород [1].
Для уменьшения общих сопротивлений внедрению ковша в породу считается целесообразным исключать из участия в резании боковые стенки 108
ковша, поэтому они отодвинуты от средней части и наклонены назад под углом 30…40º [2].
Рудоуправление Стойленского ГОКа совместно с Московским государственным горным университетом в течение 2008–2009 гг поэтапно занимались совершенствованием технологии изготовления и конструкции зубьев ковша экскаватора ЭКГ –10 с целью увеличения износостойкости.
Первый этап включал работы по совершенствованию технологии литья высокомарганцовистых сталей. Было проведено изучение микроструктур поверхности зубьев полученных по традиционной технологии литья из высокамарганцовистой стали 110Г13Л с последующей термообработкой отливок. Так, закалка в воде при температуре 1050 ºС выявила в микроструктуре поверхности зуба крупнозернистый аустенит; закалка в воде при температуре 1050 ºС с двухчасовым отпуском при 550 ºС привела к выделению карбидов по границам зерен и появлению внутри зерна трооститных участков; после деформации образца материала зуба и последующей закалки в воде при температуре 1050 ºС были выявлены зерна аустенита со следами деформации; после высоких контактных нагрузок образца материала зуба и анализа его поверхностной зоны был выявлен аустенит, претерпевший частичное мартенситное превращение. Все это в конечном итоге не приводит к увеличению износостойкости зубьев.
Одним из методов повышения износостойкости зубьев ковша экскаватора в несколько раз является метод борирования (насыщение карбидом бора) рабочих поверхностей зуба при литье [3]. Согласно этому методу технологический процесс изготовления зубьев конструкции «ИЗ КАРТЭКС » включает:
-
– формовку в опоки (в качестве формовочной смеси использовался песок с жидким стеклом);
-
– окраску внутренней поверхности формы смесью карбида бора с поливинилбутиральным лаком;
-
– сушку формы и стержней в камерной печи с газовым обогревом. (температура сушки 150 о С, время повышения температуры до 300…350 ºС составило 1,5 часа; охлаждение при закрытых заслонках камеры и погашенных форсунках 3,5…4 часа; общая продолжительность сушки 5,5 часов).
Далее изготовление отливок соответствовало технологическому процессу, принятому в ОАО «Оскольский завод металлургического машиностроения» (ОЗММ).
Анализ микроструктуры материала поверхности зуба после борирования выявило наличие боридного слоя на глубине до 2 мм, что позволит повысить износостойкость в 2,5…3 раза.
Экспериментальная партия борированных зубьев конструкции «ИЗ КАРТЭКС» в количестве 25 шт. была изготовлена в ОАО «ОЗММ» и испытана в период с 5 октября по 13 ноября 2008 г. Испытания проводились на пяти экскаваторах ЭКГ–10, работавших в участках добычи руды железорудного карьера ОАО «Стойленский ГОК». Зубья устанавливались на ковшах с короткой, средней и длинной передними стенками.
Второй этап включал работы по совершенствованию формы зубьев в результате которых была предложена модернизированная конструкция зуба с увеличенным на 70…80% объемом его истираемой части (см. рис. 4).
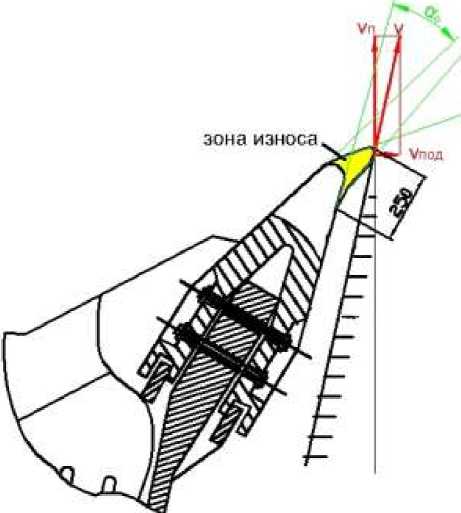
Рис. 4. Зуб модернизированная конструкция
Такая форма зуба позволяет сохранить начальный угол заострения (αо = α = 22…25º) одинаковым до замены зубьев, то есть до величины предельного износа в 250 мм.
Одновременно с экспериментальной партией борированных зубьев конструкции «ИЗ КАРТЭКС » была изготовлена экспериментальная партия зубьев модернизированной конструкции в количестве 25 шт. Их испытания проводились на пяти экскаваторах в период с 16 октября по 25 ноября 2008 г.
Результаты испытаний борированных и неборированных зубьев базовой конструкции «ИЗ КАРТЭКС » приведены табл. 1, а результаты испытаний модернизированных зубьев экскаватора ЭКГ–10 – в табл. 2.
Таблица 1
Результаты испытаний зубьев базовой конструкции
п/п № |
Номер экскаватора |
Период эксплуатации комплекта зубьев |
Объем добычи, тыс. т |
Примечание |
|
Установка |
Замена |
||||
1 |
№ 51 |
05.10.08 |
10.10.08 |
53,466 |
борированный |
2 |
№ 51 |
10.10.08 |
16.10.08 |
39,84 |
неборированный |
3 |
№ 53 |
14.10.08 |
22.10.08 |
74,47 |
борированный |
4 |
№ 53 |
22.10.08 |
31.10.08 |
42,93 |
неборированный |
5 |
№ 53 |
10.11.08 |
13.11.08 |
36,6 |
неборированный |
6 |
№ 57 |
15.10.08 |
21.10.08 |
44,6 |
борированный |
7 |
№ 57 |
21.10.08 |
29.10.08 |
40,98 |
неборированный |
8 |
№ 57 |
29.10.08 |
01.11.08 |
30,7 |
неборированный |
9 |
№ 75 |
15.10.08 |
22.10.08 |
90,05 |
борированный |
10 |
№ 75 |
22.10.08 |
29.10.08 |
56,99 |
борированный |
11 |
№ 65 |
10.10.08 |
16.10.08 |
94,21 |
борированный |
Средний объем добычи руды на 1 комплект неборированных зубьев базовой конструкции составил Q = 191, 05/5 = 38, 21 тыс. т, средний объем добычи руды на 1 комплект борированных зубьев составил: Q = 413,786/6= 68, 96 тыс. т
Таблица 2
Результаты испытаний зубьев модернизированной конструкции
п/п № |
Номер экскаватора |
Период эксплуатации комплекта зубьев |
Объем добычи, тыс. т |
|
Установка |
Замена |
|||
1 |
№ 51 |
16.10.08 |
23.10.08 |
70,27 |
2 |
№ 53 |
31.10.08 |
09.10.08 |
119,64 |
3 |
№ 53 |
13.11.08 |
25.11.08 |
118,89 |
4 |
№ 57 |
05.11.08 |
11.11.08 |
55,39 |
5 |
№ 57 |
11.11.08 |
19.11.08 |
36,33 |
6 |
№ 57 |
19.11.08 |
26.11.08 |
74,4 |
7 |
№ 65 |
16.10.08 |
31.10.08 |
156,94 |
8 |
№ 65 |
31.10.08 |
13.11.08 |
164,03 |
9 |
№ 75 |
29.10.08 |
18.11.08 |
173,55 |
Средний объем добычи руды на 1 комплект зубьев составил Q = 969,425/9 =107, 7 тыс. т
Для корректной оценки результатов, приведенных в табл. 1, в качестве критерия оценки износостойкости был принят относительный массовый износ - I , соответственно для базовой ( I 5аз) и базовой борированной ( I б б) конструкции зуба, определяемой по формуле
I баз = I бб =100[ G иб ] / G б , % (2)
и для модернизированной конструкции зуба (см. табл. 2)
I м =100[ G им ] / ( G б +[ G им ]), % (3)
где [ Оиб ], [Оим] - предельный массовый износ базовой и модернизированной конструкции зубьев (определяется как разность между массой зуба до и после эксплуатации), соответственно, кг; О б - вес базовой конструкции зуба, кг, О б = 206 кг [2].
Зависимость результатов расчетов относительного массового износа (3) и (4) от объема добычи (см. результаты табл. 1 и табл. 2) приведены на рис. 5.
Анализ испытаний зубьев на износостойкость по этой зависимости показал, что наибольшей износостойкостью обладает зуб модернизированной конструкции (см. рис. 5). Относительный массовый износ зуба модернизированной конструкции при увеличении добычи уменьшился в:
-
• 3,33 раза по сравнению с зубьями базовой неборированной конструкции;
-
• 2,5 раза по сравнению с борированными зубьями базовой конструкции.
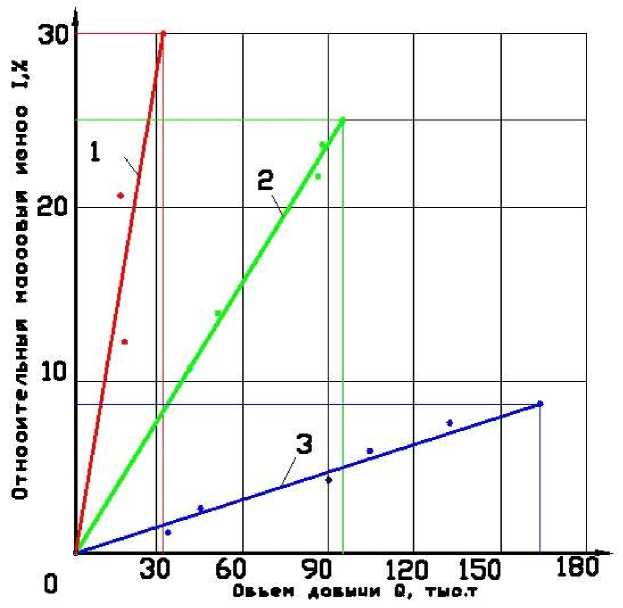
Рис. 5. Зависимость относительного массового износа от объема добычи:
1- базовая конструкция зуба; 2- базовая борированная конструкция зуба; 3 - модернизированная конструкция
Таким образом, эксплуатация вооружения ковша карьерного экскаватора даже с неборированными зубьями модернизированной конструкции позволяет увеличить средний объем добычи руды в:
-
• 2,82 раза по сравнению с зубьями базовой неборированной
конструкции;
-
• 1,5 раза по сравнению с борированными зубьями базовой
конструкции.
В то время как средний объем добычи руды борированного зуба конструкции « ИЗ КАРТЭКС» по сравнению с неборированным увеличился только в 1,8 раза.
Список литературы Изнашивание вооружения ковша карьерного одноковшового экскаватора
- Ветров Ю.А. Резание грунтов землеройными машинами. -М.: Машиностроение, 1971. -360 с.
- Подэрни Р.Ю. Механическое оборудование карьеров (ГОРНОЕ МАШИНОСТРОЕНИЕ). Учебник для вузов. -6-е изд., перераб. и доп. -М.: Издательство МГГУ, 2007. -680 с.: ил.
- Фролов К.В. Машиностроение. Материалы в машиностроении. Стали и чугуны. Энциклопедия в сорока томах. -Раздел II, Том II-2. -М.: Машиностроение, 2001. -781 с.