Изучение научно-технологических основ совместной переработки отвальных медных шлаков и отработанного медного электролита
Автор: Харченко Елена Михайловна, Жумашев Калкаман Жумашевич
Журнал: Вестник Южно-Уральского государственного университета. Серия: Металлургия @vestnik-susu-metallurgy
Статья в выпуске: 36 (253), 2011 года.
Бесплатный доступ
Проблема переработки отвальных медных шлаков является одной из актуальных проблем, решение которой может служить дополнительным источником цветных и черных металлов, а также улучшить состояние окружающей среды в районах действия предприятий. Рассмотрены теоретические основы твердофазного восстановления компонентов шлака углеродом с целью создания новой комплексной технологии совместной переработки шлаков медеплавильного производства и отработанного медного электролита с расширением ассортимента выпускаемой продукции.
Медные шлаки, медный электролит, переработка
Короткий адрес: https://sciup.org/147156677
IDR: 147156677
Текст научной статьи Изучение научно-технологических основ совместной переработки отвальных медных шлаков и отработанного медного электролита
К настоящему времени в Казахстане накоплено огромное количество техногенных отходов, содержащих цветные и черные металлы. Такая ситуация характерна для предприятия ТОО «Корпорация Казахмыс».
Согласно литературным данным наиболее большие объемы неизвлекаемых медьсодержащих продуктов сосредоточены именно в таких отходах металлургического передела, как шлакоотвалы: 31 млн т отходов, по количеству меди в данных отходах – это около 250 тыс. т [1].
Металлургические шлаки следует рассматривать не только как источник дополнительного получения цветных металлов, но и как весьма ценное сырье для других видов промышленности. Все это определило необходимость разработки технологических мероприятий по утилизации данного вида отходов.
По результатам фазового анализа медь в шлаках представлена сульфидами (халькозин, халькопирит, борнит) до 80 %, восстановленной и окисленной формами. Целью настоящего исследования является получение представления о поведении ферритных и арсенатных фаз шлаков в условиях твердофазного карботермического восстановления, поскольку при огневом рафинировании черновой меди от примесей, таких как Pb, As образуются ок- сиды указанных металлов и меди, что способствует образованию наиболее термически устойчивых соединений между ними – ортоарсенатов меди и свинца и их переходу в шлаковую фазу [1–4].
Дифференциальный термический анализ (ДТА) смесей шлака медеплавильного завода и СаО показывает на взаимодействие выше 700 °С (экзоэффект), которое сопровождается вытеснением основных оксидов (меди, свинца, железа) из состава силикатов и арсенатов. Это дает основание о возможности образования ферритных фаз. Однако уловить наличие этих фаз при работе с техногенными шлаками затруднено ввиду стеклообразно-сти и относительно низкого содержания меди и свинца.
Научно-практический интерес представляет поведение указанных фаз (ферритов и арсенатов) при карботермическом восстановлении шлака с точки зрения разделения металлов в различные продукты. Таким приемом могло быть селективное восстановление меди при относительно низкой температуре и перевод в кислый раствор или же полное восстановление меди, свинца и железа. Восстановленное железо способствует восстановлению меди из сульфидных фаз.
Результаты термодинамического анализа реакций 1–17 (табл. 1) показывают, что в зависимости
Элемент | eобщ | SiO2 | CaO | Cu | S | Pb | Zn |
% | 34,75 | 38,8 | 6,8 | 0,57 | 1,64 | 0,11 | 0,8 |
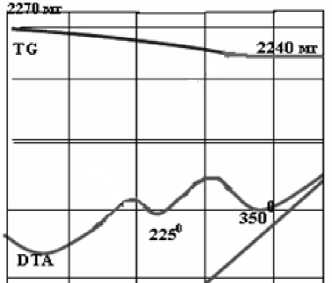
Рис. 1. ДТА смеси Cu2O–PbO–2FeO и С (Еак = 173,4 кДж/моль)
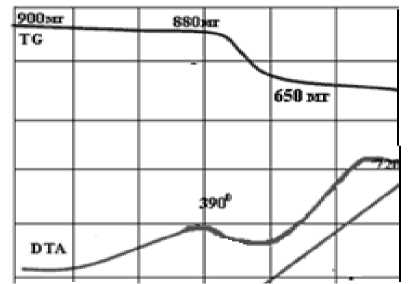
Рис. 2. ДТА смеси ортоарсената свинца и углерода (Еак = 132,3 кДж/моль)
ция восстановленных продуктов без и с добавкой СаО. Добавление в шихту СаО способствует более быстрому восстановлению железа:
Fe2SiO4 + 2CaO = Ca2SiO4 + 2FeO, ∆H°(900 К) = –192,53 кДж/моль, ∆H°(1100 К) = –225,55 кДж/моль.
Магнитная сепарация восстановленного шлака не дала ожидаемых результатов. Селективное извлечение железа в магнитную фракцию не достигается. Так выход магнитной фракции при сепарации шлака, восстановленного при температуре 1000 °С в течение 60 минут без добавления СаО, составляет ~36 %, а при тех же условиях, но с добавлением СаО – 49 %; при 1100 °С и 60 мин – 49 и 55 % соответственно. Это связано с равномерным распределением железа в SiO2 и вязкость последнего не позволяет их разделить, а при добавлении в шихту СаО поверхность железа покрывается Са2SiO4, также могут образовываться немагнитные железокальциевые силикаты (по данным РФА).
В то же время существующая потребность ПО «Балхашцветмет» в железном купоросе, диоксиде кремния и отсутствие технологии переработки отработанного медного электролита послужили основанием для разработки технологической схемы их совместной переработки, представленной на рис. 3.
Схема включает в себя три основные стадии: подготовка отвального шлака и его восстановление, использование металлизованного огарка для нейтрализации кислых стоков, в частности отработанного медного электролита того же медьзавода. Химический состав отвального медного шлака Балхашского медеплавильного завода приведен в табл. 2.
На стадии подготовки шлак измельчают, шихтуют углеродом и получают гранулы размером 5–10 мм.
Восстановление проводили в агло-шахтной печи [5]. В результате укрупненных испытаний по восстановлению отвального медного шлака углеродом кокса в агло-шахтной печи при температуре 1050–1100 °С было получено 350 кг окатышей со степенью металлизации 91 %, которые были использованы для нейтрализации отработанного медного электролита, г/л: Cu – 10,3; As – 2,7; H2SO4 – 150.
Нейтрализация проводилась в условиях перемешивания при 20 °С в течение часа. Результаты представлены в табл. 3.
Как видно по результатам опытов 1 и 2, при расходе восстановленного шлака соответственно 10 и 20 кг на 100 л электролита в раствор переходит около 90 % железа и достигается полная цементация меди из электролита.
Повышение расхода восстановленного шлака до 30 кг/0,1м3 и выше приводит к снижению степени перехода железа в раствор, т.е. достигается полнота нейтрализации кислоты (рН ≈ 4,8).
После фильтрации образующийся твердый силикатный остаток с цементной медью тщательно промывают водой, высушивают и направляют в конвертерный цех медеплавильного завода. Фильтрат и промывные воды соединяются, затем от-правлются на стадию кристаллизации. Полученные кристаллы железного купороса (FeSO4.7H2O) поступали на цинковый завод ПО «Балхашцвет-мет» для автоклавного выщелачивания сульфидных свинцово-цинковых концентратов.
Предложенная технология позволила совместно перерабатывать до 20 т отвальных шлаков и
Восстановитель (коксовая мелочь) Р=82кт/т
Дробление
Фнгыровине
ОК11 ышн
О +5-1 Омм
Восстановлен нын шлак (Чк- 91%, Си = 0,65 %)
Подготовка сырых материалов твердый силикатный остаток и цокнтнхя медь Си-534
Цсмапацтпюс выщелачивание в мешалках 1 = 20 °Сл= 1чк
Нейтрализация отработанного электролита
Электроют
H>SO< 150 г/л
Отвальный медный шлак
БГМК "
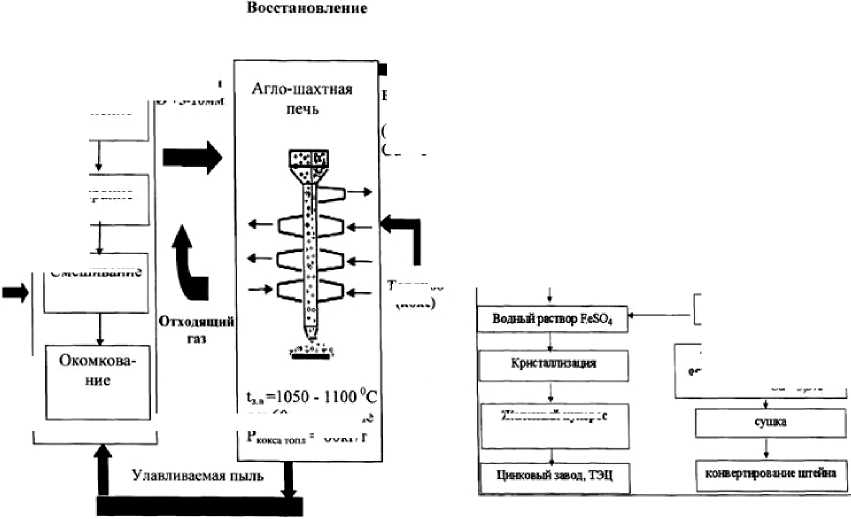
Смешивание
Желпмхй кнюрос т = 60мни и выше = бОкг/т
Рис. 3. Технологическая схема совместной переработки отвального медного шлака и отработанного медного электролита БМЗ
Истирание
Топливо (кокс)
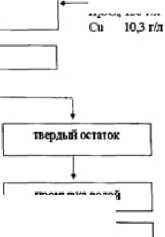
промывка водой фнлыровате
Результаты нейтрализации электролита восстановленным шлаком
Таблица 3
№ опыта | Расход восстановленного шлака, кг/ 0,1м3 | Содержание меди в растворе, кг/ м3 | Содержание железа в растворе, кг/м3 | Степень растворения, % |
1 | 10 | Следы | 33,7 | 89,9 |
2 | 20 | Следы | 67,5 | 90,0 |
3 | 30 | Следы | 98,1 | 87,3 |
4 | 40 | Следы | 98,1 | 65,4 |
80 м3 отработанного медного электролита в сутки с получением товарной продукции.
Таким образом, результаты твердофазного восстановления компонентов шлака позволили предложить новую комбинированную, безотходную схему переработки отработанного медного электролита и отвального шлака и параллельно решить задачи – частично заменить привозной дефицитный кварцевый песок, используемый при конвертировании штейна, вернуть медь в технологический цикл из двух отходов и заменить дефицитный и дорогой железный скрап, традиционно применяемый для нейтрализации электролита.
Список литературы Изучение научно-технологических основ совместной переработки отвальных медных шлаков и отработанного медного электролита
- Медиханов, Д.Г. Вовлечение в переработку сырья техногенных месторождений БГМК/Д.Г. Медиханов//Сб. науч. работ по проблемам БГМК, посвященный 10-летию независимости Республики Казахстан. -Балхаш. -2001. -С. 137-142.
- Поиск путей повышения комплексности использования сырья корпорации «Казахмыс»/А.Н. Квятковский, В.М. Бобров, Е.А. Ситько и др.//Сб. науч. работ по проблемам БГМК, посвященный 10-летию независимости Республики Казахстан. -Балхаш. -2001. -С. 19-23.
- Махметов, М.Ж. Термическая устойчивость и растворимость арсенатов/М.Ж. Махметов, Л.Г. Горохова. -Алма-Ата, 1988. -109 с.
- Краткий справочник физико-химических величин/под ред. А.А. Равделя и А.М. Пономаревой. -10 изд., испр. и доп. -СПб.: Иван Федоров, 2003. -240 с.
- Инновационный патент РК № 20339. Аглошахтная печь//К. Жумашев. -2008.