Изучение влияния концентрации дисперсных частиц на величину временного сопротивления разрушению центробежно-литых стальных заготовок
Автор: Аникеев Андрей Николаевич, Чуманов Валерий Иванович, Чуманов Илья Валерьевич
Журнал: Вестник Южно-Уральского государственного университета. Серия: Металлургия @vestnik-susu-metallurgy
Рубрика: Краткие сообщения
Статья в выпуске: 1 т.13, 2013 года.
Бесплатный доступ
Изложена методика исследования дисперсно-упрочненных центробежно-литых стальных заготовок для определения величины временного сопротивления разрушению в различных сечениях. Приводятся результаты исследования влияния концентрации дисперсных частиц на величину временного сопротивления разрушению.
Дисперсные частицы, центробежное литье, концентрация дисперсных частиц, величина временного сопротивления разрушению
Короткий адрес: https://sciup.org/147156796
IDR: 147156796
Текст краткого сообщения Изучение влияния концентрации дисперсных частиц на величину временного сопротивления разрушению центробежно-литых стальных заготовок
Разработка новых видов материалов является важнейшей задачей современной промышленности, поскольку развивающиеся отрасли добычи минерально-сырьевых ресурсов, металлургии, машиностроения, предъявляют все более высокие требования к механическим свойствам металлов [1]. Альтернативой традиционно использующимся металлам могут служить композиционные дисперсно-упрочненные заготовки, полученные методом центробежного литья.
Целью данного исследования является определение влияния концентрации дисперсных частиц карбидов на величину временного сопротивления разрушению центробежно-литых заготовок.
Исследование концентрации дисперсных частиц было проведено на сканирующем электронном микроскопе фирмы «JEOL JSM – 6460 LV» путем прямого подсчёта количества частиц на определенную площадь исследуемого образца при одинаковом увеличении [2]. Результаты исследования представлены в табл. 1.
Для величины временного сопротивления разрушению из различных сечений каждой заготовки было получено по шесть образцов размерами кв. 10x65 мм (10x10x65 мм): 1, 1 - с внешней стороны; 2, 2* – ½ радиуса заготовки; 3, 3* – внутренний край (рис. 1). Дублирование места вырезки образца с одного сечения производилось для опре- деления изменения свойств по высоте заготовки. Образцы клеймятся следующим образом: первая цифра – номер заготовки; вторая цифра – вышеописанный номер места вырезки образца.
Для проведения испытаний на разрыв и определения величины сопротивления разрушению используется разрывная машина типа УТС 110М-5.
Испытания показали, что значимых отличий в величине сопротивления разрушению образцы, вырезанные с одного сечения одной заготовки, не показали. Результаты испытаний представлены в табл. 2.
На основании полученных данных была построена диаграмма, отражающая величину сопротивления разрушению полученного материала в различных сечениях (рис. 2).
Исследование показало, что введение дисперсных частиц карбидов существенно повлияло на предел прочности полученного материала, причем в различных сечениях полученных заготовок предел прочности различен. В результате анализа полученных данных выявлено, что даже в заготовках, не имеющих в своем составе дисперсных частиц карбидов, предел прочности по сечению различен. Так, для образцов № 11 и 51 характерно увеличение исследуемого параметра по сравнению с образцами № 12, 13 и 52, 53, что объясняется более мелкой кристаллической структурой, полу-
Таблица 1
Плотность распределения частиц карбида вольфрама по сечению полученных заготовок
Номер заготовки |
Кол-во введенной дисперсной фазы WC |
Плотность распределения дисперсных частиц |
||
Внешний слой заготовки, шт./мкм2 |
Середина заготовки, шт./мкм2 |
Внутренний слой заготовки, шт./мкм2 |
||
1 |
0 |
0 |
0 |
0 |
2 |
40 |
0,4 |
0 |
0 |
3 |
80 |
0,6 |
0 |
0 |
4 |
120 |
2,5 |
0 |
0 |
5 |
0 |
0 |
0 |
0 |
6 |
120 |
2,8 |
0 |
0 |
7 |
240 |
5,1 |
2,6 |
0,5 |
8 |
360 |
5,1 |
3,5 |
3,4 |
Таблица 2
Результаты испытаний предела прочности образцов
Шифр образца |
Максимальное усилие P max , Н |
Врем. сопр. σB, Н/мм2 |
Шифр образца |
Максимальное усилие P max , Н |
Врем. сопр. σB, Н/мм2 |
11 |
4606 |
366,71 |
51 |
4945 |
393,7 |
12 |
4238 |
337,4 |
52 |
4313 |
343,3 |
13 |
3241 |
258,04 |
53 |
4079 |
324,7 |
21 |
5524 |
439,8 |
61 |
6317 |
502,9 |
22 |
4322 |
344,1 |
62 |
4402 |
350,4 |
23 |
4172 |
332,1 |
63 |
4272 |
340,1 |
31 |
5883 |
468,9 |
71 |
8856 |
605,09 |
32 |
4441 |
353,5 |
72 |
5987 |
476,6 |
33 |
4289 |
341,48 |
73 |
5427 |
432,08 |
41 |
6983 |
555,9 |
81 |
8931 |
611,06 |
42 |
4711 |
375,07 |
82 |
8247 |
556,6 |
43 |
4197 |
333,41 |
83 |
7824 |
522,9 |
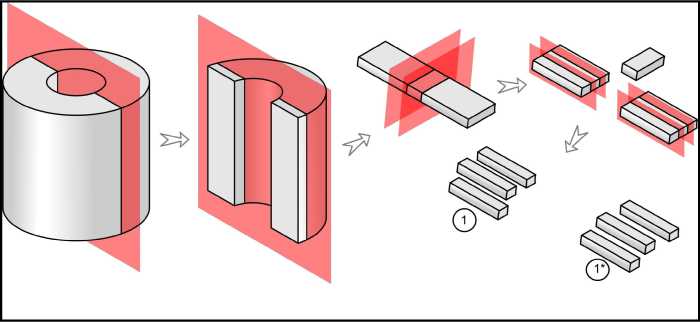
Рис. 1. Схема вырезки образцов из полученных заготовок
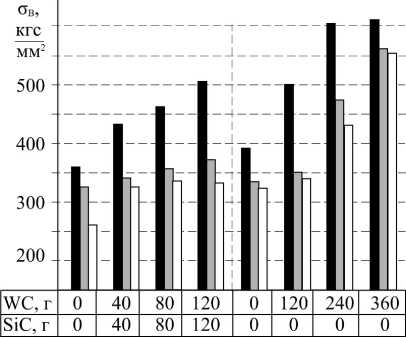
внешняя сторона
I I середина
I I внутренняя сторона
Рис. 2. Диаграмма предела прочности полученного материала ченной вследствие быстрой кристаллизации в начальные моменты разливки [3].
Наибольшие значения предела прочности наблюдаются в заготовках № 7 и 8, имеющих максимальную концентрацию введенных карбидов. Причем для образцов № 71 и 81 характерны мак- симальные значения предела прочности: 605,09 и 611,06 кгс/мм2 соответственно. В то же время, для образцов № 82 и 83 характерно незначительное уменьшение исследуемого параметра по сравнению с параметром образца № 81 (556,6, 522,9 и 611,06 кгс/мм2 соответственно). Это объясняется
Аникеев А.Н., Чуманов В.И., Чуманов И.В.
Изучение влияния концентрации дисперсных частиц на величину временного сопротивления разрушению… незначительным различием концентраций введенных карбидов по сечению заготовки №8.
Таким образом, можно сделать следующие выводы:
-
1. Определено, что концентрация введенных дисперсных частиц неодинакова в различных сечениях различных заготовок.
-
2. Получены данные, что образцы, вырезанные с разных мест одного сечения каждой заготовки, существенных отличий в величине сопротивления разрушению не имеют.
-
3. Выявлено, что в заготовках, не имеющих дисперсных карбидов, предел прочности различен по сечению заготовок, что объясняется более мелкой кристаллической структурой, полученной в результате быстрой кристаллизации во внешних поверхностных слоях по сравнению с внутренними.
-
4. Наибольшие значения предела прочности наблюдаются в заготовках, имеющих максимальную концентрацию введенных карбидов.
НИР проведена в рамках проекта РФФИ № 12-08-00896, а также поддержана ФЦП «Научные и научно-педагогические кадры инновационной России» на 2009 - 2013 годы (регистрационный номер заявки на участие в конкурсе № 2012-1.1-12-000-2003-7624).
Список литературы Изучение влияния концентрации дисперсных частиц на величину временного сопротивления разрушению центробежно-литых стальных заготовок
- Филлипов, М.А. Износостойкие стали для отливок/М.А. Филлипов, А.А. Филиппенков, Г.Н. Плотников. -М.: Металлургия, 2009. -358 с.
- Упрочнение металлических материалов дисперсными тугоплавкими частицами/А.Н. Аникеев, И.В. Чуманов, В.И. Чуманов//Проблемы черной металлургии и материаловедения. -2010. -№ 1. -С. 24-29.
- О возможности введения твердых тугоплавких частиц при получении трубной заготовки методом центробежного литья/А.Н. Аникеев, И.В. Чуманов, В.И. Чуманов и др.//Вестник ЮУрГУ. Сер. «Металлургия». -2009. -№ 36 (169). -С. 24-27.