Эколого-экономическая эффективность комбинирования технологий добычи металлов
Автор: Голик Владимир Иванович
Журнал: Горные науки и технологии @gornye-nauki-tekhnologii
Статья в выпуске: 10, 2012 года.
Бесплатный доступ
Показано, что одной из глобальных проблем современности является охрана недр при нарастающем воздействии горных работ на окружающую природную среду. В результате плохо подлежащих управлению процессов добычи минерального металлического сырья в недрах и на земной поверхности формируются техногенные месторождения, эксплуатация которых традиционными методами невозможна, а их запасы воздействуют на окружающую среду с катастрофическими последствиями. В предлагаемой статье сформулировано направление охраны окружающей среды путем минимизации объема извлекаемых из недр на земную поверхность минеральных ресурсов с прогнозированием уровня деформаций земной поверхности в зависимости от величины развивающихся при разработке месторождений в массиве напряжений. На основании выполненных комплексных исследований определено, что отходы добычи, обогащения и выщелачивания металлических руд могут быть использованы при управлении массивом с закладкой пустот твердеющими смесями, изготовленными из продуктов переработки хвостов обогащения и с использованием массивов из хвостов подземного выщелачивания металлов, которые под влияние химических процессов приобретают прочность до 1.0 МПа. Сформулированы принципы комбинирования способов управления состоянием массива по интегральному критерию «сохранность земной поверхности», как гаранта разъединения зоны горных работ и зоны обитания живого вещества. Моделированием установлено, что заполнение пустот даже малопрочными смесями снижает напряжения в рудовмещающем массиве в 1,3-1,7 по сравнению с вариантом без заполнения пустот. Для оценки эффективности управления состоянием массива и земной поверхности использован введенный автором ранее коэффициент геомеханической опасности. Рекомендованы технологические приемы управления массивом в ходе разработки месторождений комбинированными технологиями в рамках единого проекта, в том числе, методика определения прочности сооружаемых в пустотах искусственых массивов. Сделан вывод, что комбинирование традиционных и инновационных технологий представляет собой реальное направление охраны недр и природных систем, обеспечивающее экономический эффект за счет полноты и безотходности использования недр при минимальных затратах на переоснащение горных предприятий.
Недра, земная поверхность, минеральные ресурсы, деформации, массив, напряжения, отходы, добыча, переработка, металлы, руды, хвосты, обогащение, извлечение металла, твердеющие смеси, прочность, комбинирование, технологии, охрана недр
Короткий адрес: https://sciup.org/140215421
IDR: 140215421
Текст научной статьи Эколого-экономическая эффективность комбинирования технологий добычи металлов
Среди глобальных проблем человечества привлекают внимание две взаимосвязанные: обеспечение минеральными ресурсами и утилизация отходов переработки уже добытых ресурсов. Простому использованию отходов, например, в строительной индустрии препятствует наличие неизвлеченных химических элементов, а возможности технологий глубокой переработки отходов уступают возможностям извлечения минералов из недр.
Вследствие неподтверждения преобладавшего в прошлом столетии мнения о приоритете научного прогресса технологий переработки над технологиями добычи на земной поверхности формируются техногенные месторождения, запасы которых увеличиваются нарастающими темпами.
Наступает время, когда придется рассчитываться за выборочную выемку наиболее богатых минералов с оставлением в недрах некондиционных для чвоего времени минеральных ресурсов, возвращение к которым обходится дороже, чем вовлечение в эксплуатацию новых месторождений.
Обе группы некондиционных минералов являются генераторами потоков химических растворов тяжелых металлов и солей. Наиболее опасно воздействие горных работ на окружающую среду при разрушении земной поверхности в процессе горных работ. Поэтому критерием безопасности горных технологий считается сохранность земной поверхности, а наиболее выгодной технология, обеспечивающая минимум затрат при соблюдении указанного критерия.
Приоритетным направлением безопасности Земли становится минимизация объема извлекаемых из недр руд с восполнением дефицита необходимых для жизнеобеспечения металлов за счет переработки первичных хвостов, с использованием вторичных хвостов для сохранности земной поверхности путем заполнения технологических пустот твердеющими смесями на основе хвостов обогащения или хвостами подземной переработки руд.
Инструментом реализации этой стратегии является комбинирование технологий переработки руд на земной поверхности и в подземных выработках, чтобы в ходе разработки месторождений извлекались все запасы металлов до допустимых по санитарным нормам значений.
Количественным критерием экологической корректности комбинирования применяемых технологий является исключение критических деформаций земной поверхности на любой стадии эксплуатации месторождений [1].
Преимущество комбинированного управления состоянием массива в том, что в результате регулирования напряжений в массиве создаются разгруженные от критических напряжений участки, в пределах которых появляется возможность использования сравнительно менее прочных отходов поверхностного и подземного извлечения металлов.
Для количественной оценки состоянием массива используется коэффициент геомеханической опасности, представляющий собой отношение максимальных напряжений в модели к пределу прочности материала при растяжении. Сравнение технико-экономичесикх показателей технологий, удовлетворяющих критерию сохранности земной поверхности, по величине коэффициента геомеханической опасности используется при выборе технологии разработки месторождений [2].
Установлено, что заполнение пустот даже малопрочными смесями снижает напряжения в рудовмещающем массиве в 1,3—1,7 по сравнению с вариантом без заполнения пустот.
В зависимости от состояния пустот напряженное состояние массива изменяется существенно (табл. 1.1.).
Таблица 1.1.
Величина напряжений при отработке моделей, МПа.
Состояние среды в модели |
Висячий бок |
Лежачий бок |
||
ax |
y |
ax |
y |
|
Без заполнения пустот |
8.9 |
7.8 |
7.7 |
6.9 |
С заполнением хвостами подземного выщелачивания |
5.4 |
5.0 |
4.8 |
3.9 |
С заполнением твердеющими смесями |
5.0 |
4.4 |
4.8 |
4.7 |
По величине коэффициента геомеханической опасности предпочтительнее заполнение пустот твердеющими смесями (табл. 1.2).
Таблица 1.2.
Характеристика напряженности массивов в моделях.
Состояние пустот |
Максимальные напряжения, МПа |
Коэфф. опасности |
Без заполнения пустот |
8.9 |
1.1 |
С заполнением хвостами подземного выщелачивания |
5.4 |
0.67 |
С заполнением твердеющими смесями |
5.0 |
0.62 |
Максимальные напряжения и коэффициент опасности закономерно изменяются в зависимости от состояния массива (рис. 1).
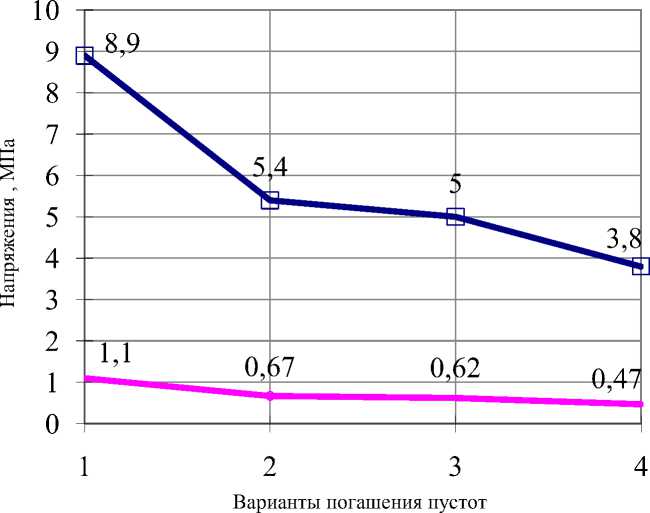
Рис.1. График изменения напряжений при различном погашении пустот: 1 - не заполнены; 2 - заполнены хвостами подземного выщелачивания;
3 - заполнены смесями на основе хвостов обогащения; 4 - заполнены смесями из стандартных материалов.
Верхняя кривая – максимальные напряжения, нижняя кривая – коэффициент опасности.
Опасность разрушения массива и земной поверхности изменяется более плавно, чем величина действующих напряжений, что говорит о наличии запаса прочности материала заполнения пустот и возможности оптимизации их состава за счет использования хвостов обогащения и подземного выщелачивания.
До 70% металлов из потерянных некондиционных руд выщелачиваются в подземных выработках при воздействии на них реагентами, оставляя в хвостах выщелачивания количество металлов, сравнимое с нормами ПДК, а кольматированные минеральными примесями хвосты выщелачивания являются аналогами твердеющих смесей, обладая прочностью от 0.2 до 1,0 МПа [3].
Для каждого из трех основных месторождений Северного Кавказа получены результаты исследований твердеющих смесей, изготовленных на основе хвостов различной крупности с добавлением портландцемента (табл. 2 -4).
Таблица 2.
Результаты исследования составов с цементом и мелким заполнителем.
Расход портландцемента, кг/м3 |
30 |
60 |
80 |
100 |
120 |
180 |
Прочность садонских кубов, МПа |
0,50 |
0,75 |
0,81 |
0,92 |
1,00 |
1,30 |
Прочность тырнаузских кубов, Мпа |
0,41 |
0,53 |
0,66 |
0,74 |
0,87 |
1,15 |
Прочность урупских кубов, Мпа |
0,48 |
0,69 |
0,78 |
0,87 |
0,92 |
1,24 |
Таблица 3.
Прочность смесей с цементом и комбинированным заполнителем, МПа.
3 Расход портландцемента, кг/м |
30 |
60 |
80 |
100 |
120 |
180 |
Мизурские кубы |
0,65 |
0,82 |
0,93 |
0,99 |
1,27 |
1,65 |
Тырныаузские кубы |
0,51 |
0,63 |
0,74 |
0,89 |
0,99 |
1,50 |
Урупские кубы |
0,62 |
0,73 |
0,88 |
0,91 |
1,08 |
1,55 |
Таблица 4.
Прочность смесей с крупным заполнителем, МПа.
Расход портландцемента, кг/м3 |
30 |
60 |
80 |
100 |
120 |
180 |
Мизурские кубы |
1,15 |
2,42 |
2,93 |
3,4 |
3,7 |
4,9 |
Тырнаузские кубы |
1,01 |
2,22 |
2,75 |
3,26 |
3,52 |
4,6 |
Урупские кубы |
1,11 |
2,31 |
2,80 |
3,31 |
3,60 |
4,75 |
Зависимость прочности смесей от расхода портландцемента описывается математическими моделями.
Для Тырныаузского месторождения:
ПрТырн 2,828 0,0011x 3,5z+ 0,933z2 +0,009xz, где x расход портландцемента, кг/м3.
Для Урупского месторождения:
ПрТырн 3,052 0,0023 x 3,573 z + 0,943 z 2 +0,0092 xz ,
Тырн
Способ управления массивом с использованием хвостов выщелачивания для целей управления массивом применяли в качестве при разработке месторождения урановых руд Быкогорского на Северном Кавказе.
В ходе экспериментального определения полноты подземного выщелачивания проба массой 1000 кг руды (0,20% свинца и 0,23% цинка) была разделена на части по 10 кг, которые выщелачивали в полиэтиленовых колоннах (перколяторах) различными реагентами. Оптимальным реагентом оказалась серная кислота (табл. 5).
Таблица 5.
Результаты выщелачивания металлов раствором серной кислоты.
Объем Раствора, дм3 |
Содержание, мг/дм3 , в колоннах |
|||||||||
№1 |
№2 |
№3 |
№4 |
№5 |
||||||
Pb |
Zn |
Pb |
Zn |
Pb |
Zn |
Pb |
Zn |
Pb |
Zn |
|
10 |
3,2 |
2,5 |
4,5 |
2,7 |
4,0 |
2,3 |
3,6 |
2,4 |
3,8 |
2,2 |
20 |
5,2 |
17,8 |
5,6 |
18,4 |
5,4 |
17,9 |
5,7 |
18,8 |
5,5 |
18,3 |
30 |
6,2 |
28,6 |
6,6 |
27,5 |
7,2 |
28,9 |
7,0 |
29,1 |
6,8 |
29,7 |
40 |
7,7 |
35,4 |
7,5 |
33,0 |
8,0 |
35,8 |
7,9 |
34,9 |
8,4 |
34,7 |
50 |
8,5 |
65,3 |
9,0 |
68,9 |
8,6 |
68,2 |
8,9 |
69,9 |
9,4 |
71,8 |
Статистическая обработка экспериментальных данных методами регрессионного анализа позволяет построить адекватные выборочные уравнения полиномиальной регрессии процесса выщелачивания.
Зависимость выщелачивания свинца от объема раствора серной кислоты имеет вид (выборочное корреляционное отношение R Pb 0,9787):
y 2, 056 +0,1897 x 0,00107 x 2
Зависимость выщелачивания цинка от объема раствора серной кислоты имеет вид (выборочное корреляционное отношение ( R Zn 0,9567):
y 1,868 +0,1143 x +0,023 x 2
Исследованиями определено, что технологические характеристики некондиционного для традиционной добычи минерального сырья позволяют применить для его переработки технологии, параметры которых определяются методом поиска оптимальных методов.
Технология добычи руд на основе комбинирования способов управления состоянием массива с закладкой пустот продуктами переработки хвостов обогащения и с использованием массивов из хвостов подземного выщелачивания металлов включает в себя элементы[4] :
-
- исследование геомеханики рудовмещающего массива;
-
- разделение месторождения на безопасные по критическим напряжениям участки;
-
- выемка кондиционных по содержанию руд для заводской переработки с закладкой выработанного пространства твердеющими смесями;
-
- выщелачивание остальных запасов с использованием хвостов подземного выщелачивания для управления массивом.
Разделение рудовмещающего массива на безопасные участки состоит в определении безопасных участков производства добычных работ, исходя из условий (рис.3):
-
- оптимизация величины пролетов сводов естественного равновесия вмещающих горные выработки пород, опирающихся на искусственные массивы из прочных твердеющих смесей;
-
- увязка расположения выработок по геомеханическим условиям с геологическими и экономическими факторами добычи богатых руд по критерию минимальной стоимости работ и максимального использования недр.
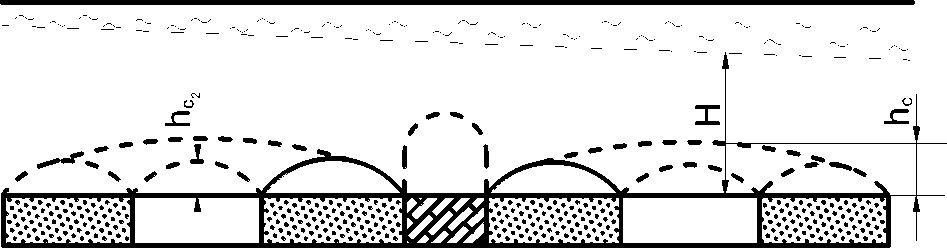
Рис.2. Схема разделения массива на безопасные пролеты: Н – расстояние от верхней границы оруденения до наносов; hc – высота сводов естественного равновесия в пределах безопасного участка; блоками выделена прочная закладка; точками выделена малопрочная закладка
Прочность твердеющей закладки на основе утилизированных хвостов обогащения и выщелачивания рассчитывается с запасом на экстремальные условия: природная и наведенная сейсмика, тектоническая нарушенность, водообильность и т.п.
Добыча руд для заводской переработки осуществляется в условиях разгрузки от критических напряжений, поэтому прочность искусственного массива может быть снижена. Использование технологий введения массива в условия объемного сжатия: анкерное упрочнение массивов, создание отрезных щелей для разгрузки участков месторождений, формирование искусственных массивов с заданной прочностью и т.п. увеличивает прочность искусственных массивов на 15-20%.
Результатом комбинированного управления состоянием массива может быть существенное сокращения расхода компонентов твердеющих смесей.
К примеру, если рудное тело шириной 100 м не обеспечивает устойчивости массива без закладки выработанного пространства твердеющими смесями прочностью 4-5 МПа, то при разделении его на два полупролета шириной 50 м в кровле образуется свод с меньшей высотой, позволяющий уменьшить прочность закладки до 2,0-2,5 МПа. Если этот пролет разделить еще на два полупролета шириной по 25 м каждый, то структурные блоки заклиниваются в нижнем слое пород, образуя плоскую кровлю выработок, позволяющую заполнить пустоты смесями прочностью 0,5-1,0 МПа.
Реализация принципов комбинирования осуществляется на основе единого единого проекта освоения запасов способами добычи, технологически взаимосвязанными между собой [5].
Целью разработки месторождения становится не эффективное выборочное извлечение богатых запасов с получением сиюминутного эффекта, а создание благоприятных условий для того, чтобы доход от освоения недр был максимальным.
Искусственные массивы из твердеющей закладочной смеси подразделяются нами по нормативной прочности: малопрочные - до 1,2; прочные - до 2,5; очень прочные - более 2,5 МПа. Нормативная прочность твердеющих смесей зависит от выполняемой функции в системе активного управления массивом пород с переводом массивов в режим объемного сжатия.
Вусловиях разгрузки от высоких напряжений твердеющие смеси для закладки технологических пустот могут быть приготовлены из доступных материалов - утилизируемых хвостов обогащения.
Прочность искусственных массивов определяется по номограмме (рис. 3).
При использовании комбинированной технологии управления состоянием массива необходим учет важного обстоятельства: податливость слабых целиков перераспределяет давление на более жесткие целики, которые могут выйти из строя и осложнить геомехническую ситуацию. Для повышения надежности управления несущая способность искусственных массивов повышается подпором закладочным материалом на величину, оцениваемую коэффициентом 1,1 - 1,5.
Для управления состоянием массива важно, чтобы кровля выработок сохраняла плоскую форму, т.е. растягивающие и сжимающие напряжения не были критическими. Величина пролета обнажения кровли плоской кровли определяется из способности структурных блоков к самозаклиниванию в нижнем слое:
L = пред- 2 , где d1 и d2 - соответственно, горизонтальный и вертикальный размеры структурных блоков, м; к2 - коэффициент запаса.
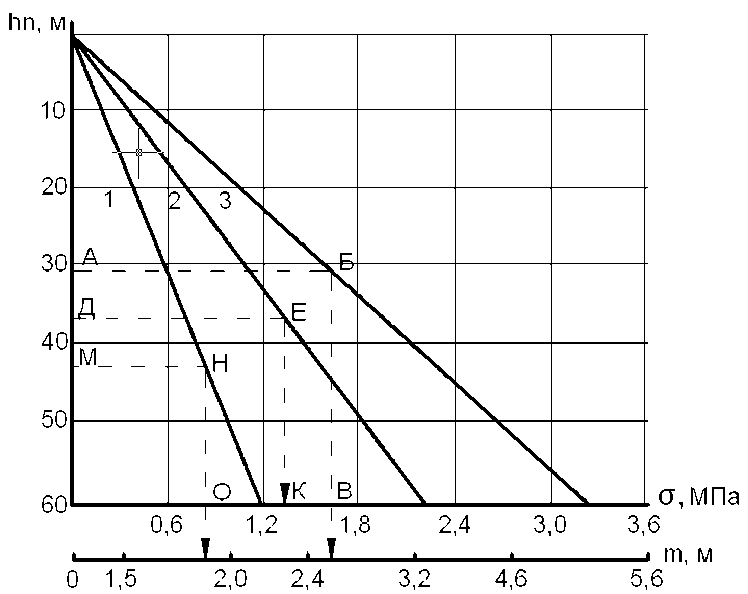
Рис. 3. Номограмма определения прочности искусственных массивов (s) и толщины несущих перекрытий (m): 1, 2, 3 - соответственно, графики напряжений, создаваемых массой закладки, пригрузкой пород и результирующих: Ключ: А®Б®В и ®à для обрушения пород; М®Н®О и О®П для плоских пролетов.
Высота свода нарушенных горными работами пород: hc = a'/v, где a* - полупролет свода; v - коэффициент устойчивости трещиноватых пород.
V 2
d R"
r Rсж d1 Rсж
где d r , d 1 - размеры вертикального и горизонтального размеров структурных блоков; R" сж , R' сж - временное сопротивление пород сжатию в направлении распора свода и в направлении действия массы пород.
Условие сохранения земной поверхности:
H' > hc, где H' - фактическая глубина верхней границы пустот от границы выветренных пород и рыхлых отложений, м; hc - высота свода нарушенных горными работами пород.
При несоблюдении этого условия земная поверхность может быть сохранена за счет закладки твердещими смесями так, чтобы при уменьшенной высоте выработанного пространства условие все же обеспечивалось.
Технологии с подземным выщелачиванием металлов из руд осуществляются в рамках комбинирования с вовлечением в эксплуатацию некондиционных и забалансовых руд в пределах разгруженных от высоких напряжений участков месторождения.
Большинство пригодных для выщелачивания месторождений приурочено к массивам, состоящим из серии рудных тел преимущественно крутого падения. Оруденение локализуется в трещинах мощностью 1,5 м. Суммарная мощность балансовых руд в пределах 7 - 20 м, причем промышленные руды сопровождаются ореолом забалансовых руд, которые по составу, характеру минерализации и технологическим свойствам аналогичны балансовым, но значительно беднее.
Для выщелачивания наиболее приемлемы условия: коэффициент разрыхления 1,3-1,6, коэффициент крепости пород по шкале проф. М.М. Протодьяконова от 8 до 15, примеси глинистыхчастиц не более 10%, наличие карбонатных пород не более 10%.
По сравнению с традиционной отработкой способ подземного выщелачивания исключает операция по выдаче руды на поверхность, доставку ее на завод, дробление и измельчение, гидрометаллургический процесс извлечения метала, транспортировку и складирование хвостов, которые, оставаясь в выработанном пространстве, после естественного твердения вследствие кольматации участвуют в управлении состоянием массива [6].
Магазинирование забалансовых запасов для выщелачивания осуществляется вариантами традиционных систем. Очистные блоки имеют размеры: площадь - 600 - 1000 м2, высота - 30 - 90 м, ширина - 20 - 25 м.
Руду в блоках выщелачивания отбивают, добиваясь величины коэффициента разрыхления рудной массы - 1,15 - 1,20. Блоки подземного выщелачивания располагают так, чтобы компенсационным пространством служили пустоты, образованные выемкой балансовых запасов месторождения.
Для отбойки, чаще всего, применяют гранулиты с плотностью заряжания скважин 9 кг/м и расходом 1,3 кг/м3 отбитой горной массы.
Выщелачивают сернокислыми растворами в замкнутом цикле. Например, вначале в качестве растворителя применяют 5 %-ный раствор серной кислоты. Продолжительность подачи раствора серной кислоты - 2 -4 суток. Затем концентрацию раствора снижают до 3 %. Раствор подают до тех пор, пока в продуктивных растворах, наряду с остаточной кислотностью, не снижается резко концентрация металла. После этого орошение прекращают, а блок "выстаивается" в течение 20 - 25 суток. После снижения содержания металла блок вновь орошают раствором серной кислоты с концентрацией от 3 до 2 %. Продолжительность выщелачивания 6 - 7 мес.
Продуктивные растворы перерабатывают в сорбционных комплексах, представляющих собой ионнообменные фильтры. Проходя через колонны и фильтруясь через слой анионита, растворы оставляют на нем металл. После прохождения растворов через последнюю колонну содержание металла в маточных растворах приближается к допустимому ПДК.
Кислотность продуктивных растворов не ниже 0,02 %, так как при низкой кислотности процесс ухудшается, а в нейтральных растворах прекращается совсем. Кислотность растворов, на которой работают колонны, составляет 0,2 - 0,3 %.
Разработка способов экологически корректной эксплуатации месторождений на основе комбинирования традиционных и инновационных технологий представляет собой реальное направление охрана недр и природных систем при нарастающем воздействии горных работ на окружающую природную среду.
Включение в эксплуатацию некондиционных минеральных ресурсов является альтернативой освоению новых месторождений, что особенно важно в условиях дефицита средств у горных предприятий.
Работа выполнена при финансовой поддержке гранта Министерства образования и науки Российской Федерации: Государственный контракт № 16.515.11.5039 «Разработка безотходных экологически безопасных способов добычи и переработки руд месторождений Северного Кавказа на основе комбинирования традиционных и инновационных технологий»
Список литературы Эколого-экономическая эффективность комбинирования технологий добычи металлов
- Голик В.И., Исмаилов Т.Т. Управление состоянием массива. -М.: МГГУ, 2006.
- Голик В.И., Комащенко В.И.Природоохранные технологии управления состоянием массива на геомеханической основе. -М.:КДУ.2010.
- Исмаилов Т.Т., Голик В.И., Дольников Е.Б. Специальные способы разработки месторождений полезных ископаемых. -М: МГГУ, 2006.
- Ляшенко В.И., Голик В.И., Козырев Е.Н. Комбинированные технологии добычи полезных ископаемых с подземным выщелачиванием.//Горный журнал, 2008. -№12.
- Голик В.И., Разоренов Ю.И. Проектирование горных предприятий. -Новочеркасск: ЮРГТУ, 2007.
- Голик В.И.Разработка месторождений полезных ископаемых. -Владикавказ: МАВР, 2006.