Экспериментальное исследование процесса инерционного прессования труб
Автор: Космацкий Ярослав Игоревич, Фокин Николай Владимирович
Журнал: Вестник Южно-Уральского государственного университета. Серия: Металлургия @vestnik-susu-metallurgy
Статья в выпуске: 2 т.14, 2014 года.
Бесплатный доступ
Обоснована задача проведения экспериментального исследования процесса инерционного прессования труб. Приведены результаты исследования влияния энергосиловых параметров аккумулирующего устройства при различном конструктивном исполнении пресс-игл на величину пресс-остатка. Определены зависимости, обеспечивающие выбор оптимальных силовых параметров аккумулирующего устройства.
Инерционное прессование труб, пресс-остаток, профилировка прессового инструмента
Короткий адрес: https://sciup.org/147156873
IDR: 147156873
Текст научной статьи Экспериментальное исследование процесса инерционного прессования труб
Теоретическое исследование граничных условий реализации процесса инерционного прессования труб, заключающегося в протягивание металла из контейнера готовой частью изделия, выполненное в работе [1], позволило разработать рекомендации по совершенствованию способа инерционной выпрессовки пресс-остатка и устройства, обеспечивающих, в совокупности, полное устранение указанной величины. В частности, установлено, что для гарантированного устранения пресс-остатка требуется приложение дополнительных усилий, создаваемых аккумулирующим устройством, принцип действия которого описан в работе [2], компенсирующих в случае их недостатка со стороны инерционного воздействия готовой части трубы.
Согласно разработанному способу прессования полых профилей [3] обеспечивается аккумулирование кинетической энергии при прессовании за счет дооснащения гидравлического пресса аккумулирующим устройством, с максимальными усилиями, соизмеримыми со средними максимальными значениями усилий прессования, и последующая ее передача металлу заготовки, в частности, пресс-остатку.
С целью подтверждения результатов численного анализа проводилось экспериментальное исследование процесса инерционного прессования труб.
Соответствующее оборудование и инструмент конструировались для дальнейшего использования на сервогидравлической машине статических и динамических испытаний Shimadzu Servopulser максимальным усилием 196 кН испытательного комплекса ОАО «Российский научно-исследовательский институт трубной промышленности». Для исследований использовалось 45 образцов-заготовок 0 19 х 6,25 мм длиной 20 мм из свинца марки С2.
Аккумулирующее устройство исполнялось пружинами сжатия высотой H0 = 190 мм, изго- товленными с требованиями по ГОСТ 13773–86, усилиями максимальной деформации Pа.у от 40,0 до 50,0 кН. Общий вид установки для проведения экспериментального исследования представлен на рис. 1.
Рис. 1. Комплекс прессового инструмента для физического моделирования процесса инерционного прессования труб: 1 – заготовка; 2 – центрирующая втулка; 3 – контейнер; 4 – крышка стакана; 5 – матрица; 6 – матрицедержатель; 7 – пресс-штемпель; 8 – пресс-игла; 9 – пружина сжатия; 10 – стакан;
11 – стойка опорная; 12 – пресс-шайба
При проведении экспериментального исследования исследовались не только взаимосвязь энергосиловых параметров аккумулирующего устройства и величины пресс-остатка, но и влияние геометрических параметров профилировки пресс-иглы, с целью определения оптимальных соотно- шений усилия аккумулирующего устройства и геометрических параметров профилировки прессового инструмента, обеспечивающих изготовление труб-образцов с максимальным коэффициентом выхода годного металла.
Исследование проводилось при прессовании труб-образцов 0 10 х 2,5 мм со скоростью v = 0,25 мм/с , с применением следующих разн овидностей геометрических параметров профил ировок пресс- игл, представленных на рис. 2, с н оминальным диаметром D ИГ = 6,0 мм :
-
- максимальный диаметр D ИГmax = 6,0 мм , угол конусности ф = 0 ° , длина цилиндрического участка L ц = 40,0 мм ;
-
- максимальный диаметр D ИГmax = 12,5мм, угол конусности ф = 30 ° , длина цилиндрического участка L ц = 34,0 мм ;
-
- максимальный диаметр D ИГmax = 19,0мм, угол конусности ф = 45 ° , длина цилиндрического участка L ц = 34,0 мм .
Экспериментальное исследование выявило различный характер изменения усилия прессования P , в зависимости от используемого аккумулирующего устройства. На рис. 3 приведены графические зависимости изменения среднего значения усилия прессования от времени рабочего цикла процесса при реализации способа с применением пяти различных аккумулирующих
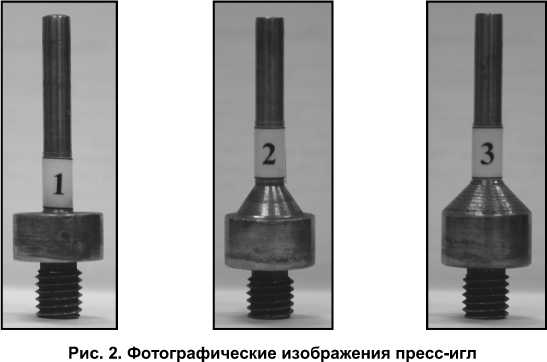
(маркировка пресс-игл соответствует их порядковой нумерации)
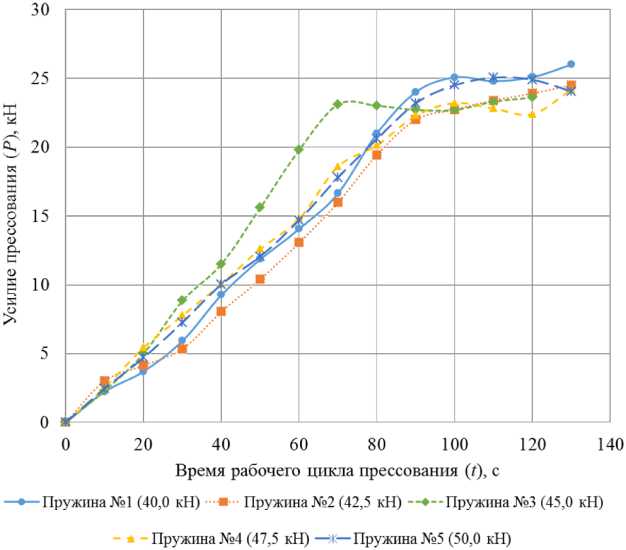
Рис. 3. Зависимости средних значений усилия прессования от длительности рабочего цикла с применением аккумулирующих устройств различного усилия максимальной деформации:
Pmax1=26,0кН, Pmax2=24,5кН, Pmax3=23,6кН, Pmax4=23,2кН, Pmax5=25,1кН устройств. Эти графические зависимости позволяют проследить изменение усилия прессования в независимости от изменения геометрических параметров профилировок используемых пресс-игл.
Различия в представленных диаграммах зависимости усилия прессования от времени рабочего цикла процесса обусловливаются энергосиловыми параметрами установленного аккумулирующего устройства, в частности, усилием максимальной деформации P а.у . Как видно из зависимостей рис. 3, минимальное значение максимального усилия прессования достигается при использовании пружины сжатия № 4.
В свою очередь, такие геометрические параметры профилировки пресс-иглы, как D ИГmax и ф , также оказывают влияние на величину максимального значения усилия прессования P maх [4].
На рис. 4 представлены графические зависимости изменения усилия прессования в течение рабочего цикла процесса, в зависимости от используемых пресс-игл. Для анализа раздельного влияния профилировки пресс-иглы и силовых параметров аккумулирующего устройства, в этом случае, пружины сжатия не применялись.
В соответствии с графическими зависимостями (см. рис. 4), можно сделать вывод о том, что с увеличением D ИГ D ИГmax , т. е. с уменьшением угла конусности пресс-иглы ф , затрачивается большее усилие на выпрессовку металла.
Таким образом, по совокупности полученных результатов, представленных на рис. 3 и 4, можно предположить, что наиболее энергосберегающими условиями обладает процесс прессования труб-образцов 0 10 х 2,5 мм с использованием аккумулирующего устройства № 4 (Рау = 47,5 кН ) и пресс-иглы № 3 (5ИГ /D^max = 0,32), что подтверждается наименьшими средними значениями максимального усилия прессования: Pax = 23,2 кН и P = 21,0 кН , соответственно.
max 3
Однако, последующее определение значений коэффициентов выхода годного металла (рис. 5), вносит соответствующую конкретизацию в допущенное предположение.
Таким образом, применение аккумулирующего устройства, выполненного, в частном случае, пружиной сжатия с усилием максимальной деформации Р а .у3 = 45,0 кН, обеспечивает мини-
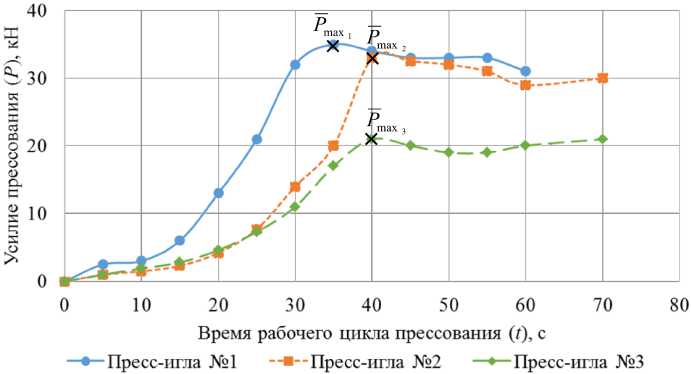
Рис. 4. Зависимости средних значений усилия прессования от рабочего цикла процесса при использовании пресс-игл 3 профилировок (без аккумулирующего устройства): P max1 = 35,0кН , P max2 = 33,0кН , P max3 = 21,0кН
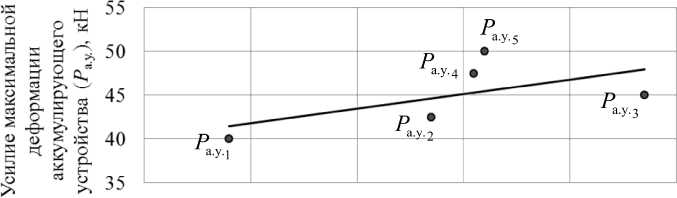
65,5 66,5 67,5 68,5 69,5 70,5
Рис. 5. Зависимость коэффициента выхода годного металла при прессовании труб от усилия максимальной деформации применяемого аккумулирующего устройства:
k 1 = 66,4% , k 1 = 68,2% , k 1 = 70,4% , k 1 = 68,6% , k 1 = 68,7%
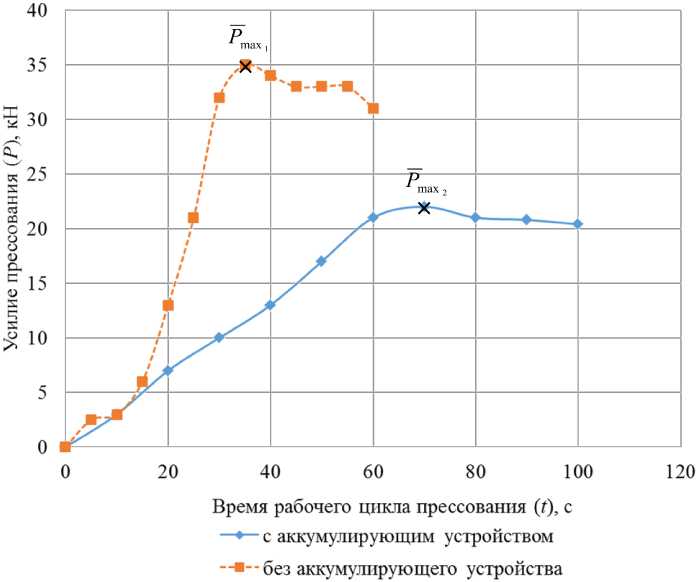
Рис. 6. Зависимость среднего значения усилия прессования от времени рабочего цикла процесса: P max = 35, 0 кН , P max = 21, 0 кН
мальный расходный коэффициент металла при прессовании труб-образцов 0 10 х 2,5 мм.
Следовательно, ресурсосберегающим способом инерционного прессования труб с использованием аккумулирующего устройства является способ, при котором используется пружина сжатия № 3 и пресс-игла № 3.
Эффективность применения при прессовании труб аккумулирующего устройства, обоснованного исполнения, наглядно продемонстрирована на рис. 6. Согласно представленным зависимостям значение максимального усилия прессования P max при реализации процесса без пружины сжатия значительно выше, чем при прессовании с ее применением. Это объясняется тем, что усилие прессования расходуется не только на выпрессовку трубы, но и на деформацию пружины, которая аккумулирует кинетическую энергию, необходимую для последующего процесса инерционной выпрессовки пресс-остатка.
Передача металлу заготовки накопленной энергии осуществляется постепенно в течение всего рабочего цикла процесса, обеспечивая, при этом плавное возрастание усилия прессования P . В соответствии с представленной на рис. 6 графической зависимостью, длительность процесса с применением аккумулирующего устройства выше, что объясняется работой деформации, названного устройства.
Для унификации способа инерционного прессования полых профилей с использованием акку- мулирующего устройства, по результатам проведенного экспериментального исследования найдена зависимость, обеспечивающая возможность определения необходимого усилия максимальной деформации аккумулирующего устройства:
Р -К-Р пр max , гдеK – коэффициент пропорциональности. Исходя из анализа результатов экспериментального исследования рекомендуемое значение K = 1,7 ...1,9; Pmax – максимальное значение усилия прессования, определяемое условиями процесса, в том числе, геометрическими параметрами профилировки инструмента [1, 4].
Список литературы Экспериментальное исследование процесса инерционного прессования труб
- Космацкий, Я.И. Совершенствование технологии изготовления горячепрессованных труб на основе новых технических решений: дис. … канд. техн. наук/Я.И. Космацкий. -Челябинск, 2012. -213 с.
- Космацкий, Я.И. Совершенствование процесса инерционной выпрессовки пресс-остатка/Я.И. Космацкий//Материалы 65-й научной конференции. Секции технических наук. -Челябинск: Издат. центр ЮУрГУ, 2013. -Т. 2. -С. 11-14.
- Заявка № 2013133135 Российская Федерация, МПК B 21 J 5/00 (2009.01). Способ прессования полых профилей и устройство для его осуществления/Космацкий Я.И., Выдрин А.В, Баричко Б.В. и др. -№ 2011111040/02(016238); заявл. 16.07.13. -10 с. (уведомление о положительном результате формальной экспертизы от 25.09.2013).
- Выдрин, А.В. Математическое моделирование процесса прессования труб переменного сечения/А.В. Выдрин, И.Ю. Пышминцев, Я.И. Космацкий//Сталь. Производство труб. -2013. -Вып. 2. -С. 39-41.