Экспериментальное исследование процесса прессования труб переменного сечения
Автор: Космацкий Ярослав Игоревич
Журнал: Вестник Южно-Уральского государственного университета. Серия: Металлургия @vestnik-susu-metallurgy
Статья в выпуске: 39 (298), 2012 года.
Бесплатный доступ
Обоснована задача проведения экспериментального исследования процесса прессования труб переменного сечения. Проведена экспериментальная проверка корректности и достоверности методики расчета профилировки инструмента для прессования труб с уменьшением толщины стенки на ее заднем участке. Уточнены особенности протекания данного процесса, что позволило производить соответствующие расчеты с минимальным значением относительной погрешности.
Прессование, труба переменного сечения, усилие прессования
Короткий адрес: https://sciup.org/147156733
IDR: 147156733
Текст научной статьи Экспериментальное исследование процесса прессования труб переменного сечения
ческими параметрами: цилиндрический, обеспечивающий получение трубы с номинальной толщиной стенки: D Р , L Р ; конический, обеспечивающий плавное уменьшение стенки на заднем конце прессованной трубы: D Р , D ИГmax , L ИГ ; цилиндрический участок, учитывающий толщину пресс-остатка, толщину матрицы и длину отрезаемого с пресс-остатком патрубка: D ИГmax , L Ц , причем такие геометрические параметры пресс-игл, как D Р и L Ц , являются постоянными для всех пресс-игл и равны 5 и 18 мм соответственно [2].
На рис. 1 изображен используемый прессовый инструмент в сборе.
Значения геометрических параметров пресс-игл приведены в таблице.
Исследование проводилось при изготовлении труб 0 10 х 2,5 мм из заготовок 19 х 6,25 мм, 0 19 х 5,75 мм, 0 19 х 5,25 мм длиной 20 мм из свинца марки С2 (ГОСТ 3778–98) с использованием соответствующих пресс-игл с коническим участком.
С помощью статистического метода обработки экспериментальных данных были построены в одной системе координат графические зависимости усилия прессования и рабочего диаметра пресс-игл № 2, 4, 5 от времени одного рабочего цикла процесса прессования. На рис. 2 изображены
При прессовании труб переменного сечения деформационные условия процесса часто лимитируются удельными давлениями прессования, которые достижимы в данном контейнере пресса или допустимы условиями прочности прессового инструмента [1].
Для подтверждения достоверности результатов представленного в работе [2] математического исследования влияния геометрических параметров прессового инструмента на изменение толщины стенки на заднем участке передельных и редуцированных труб потребовалось проведение экспериментального исследования процесса прессования труб с использованием пресс-игл с коническим участком.
Исследование проводилось на экспериментальной площадке Российского научно-исследовательского института трубной промышленности, с использованием универсальной машины для испытания на прочность «EU 100», оснащенной индуктивным измерительным преобразователем давления.
Выбор оптимальной стратегии для управления экспериментом на основе априорных сведений об изучаемом процессе потребовал изготовления пресс-игл с различными геометрическими параметрами.
Каждая пресс-игла имеет на своей рабочей части три участка с соответствующими геометри-
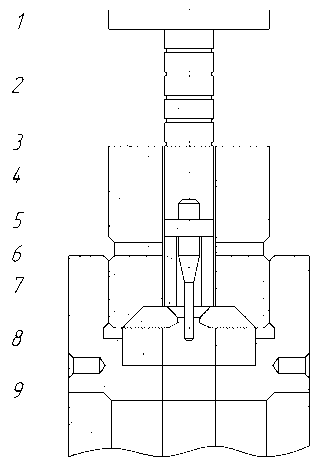
Рис. 1. Комплекс прессового инструмента для физического моделирования процесса прессования: 1 – пуансон; 2 – контейнер; 3 – пресс-шайба; 4 – пресс-игла; 5 – заготовка; 6 – матрица; 7 – упор матрицы; 8 – упор контейнера; 9 – удлинитель
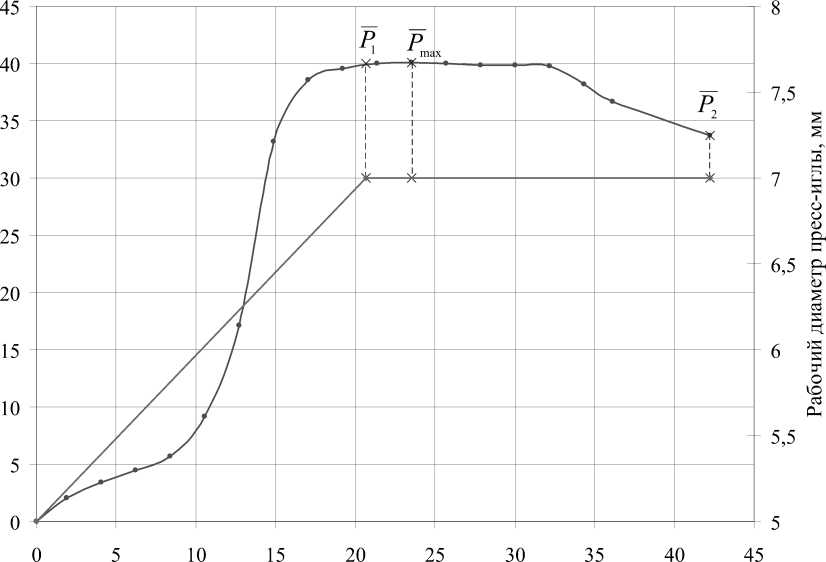
Геометрические параметры пресс-игл
№ пресс-иглы |
L Р , мм |
D ИГmax , мм |
L ИГ , мм |
1 |
7 |
7 |
15 |
2 |
12 |
7 |
10 |
3 |
17 |
7 |
5 |
4 |
12 |
6 |
10 |
5 |
12 |
8 |
10 |
Среднее значение одного рабочего цикла процесса прессования, с
Образцы №4, №5, №6 Пресс-игла №2
Рис. 2. Зависимость среднего значения усилия прессования от рабочего диаметра пресс-иглы
(скорость прессования V = 0,484 мм/с ): P 1 = 40,0 кН , P max = 40,1 кН , P 2 = 33,8 кН
Космацкий Я.И.
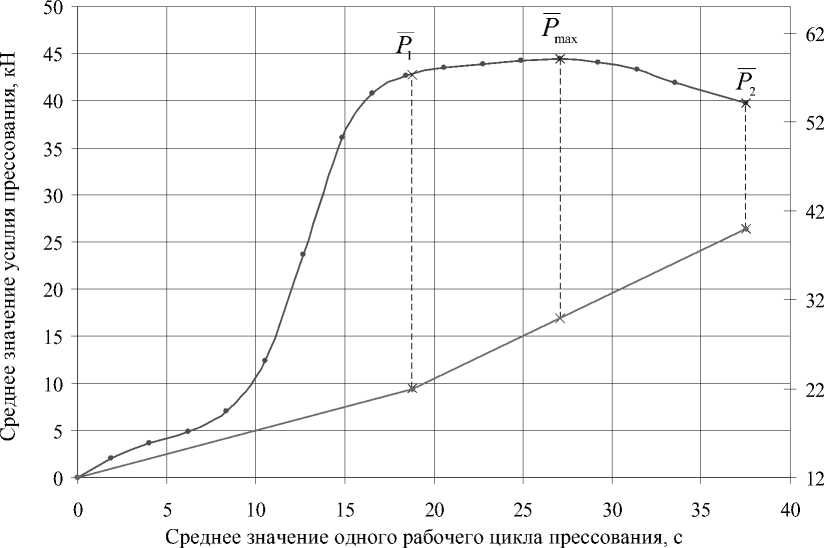
Образцы №1, №2, №3 Пресс-игла №1
Рис. 3. Зависимость среднего значения усилия прессования от рабочей длины пресс-иглы
(скорость прессования v = 0,533 мм/с ): P 1 = 42,8 кН , P max = 44,5 кН , Р 2 = 39,8 кН
соответствующие пресс-игле № 2 графические зависимости.
Анализ графических зависимостей на рис. 2, показывает, что соответствие максимального усилия прессования P max равного 40,1 кН цилиндрическому участку пресс-иглы объясняется тем, что на длину цилиндрического участка приходится заключительная стадия процесса прессования – выпрессовка заднего участка трубы с утоненной стенкой, обеспечивающая образование заднего участка трубы, уходящего в отход, – во время которой установившееся течение металла нарушается.
Для анализа изменения величины усилия прессования по длине пресс-иглы на основе полученных экспериментальных данных с помощью статистического метода их обработки были построены в одной системе координат графические зависимости усилия прессования и рабочей длины пресс-игл № 1, 2, 3 от времени одного рабочего цикла процесса прессования. На рис. 3 изображены соответствующие пресс-игле № 1 графические зависимости.
Анализ графических зависимостей на рис. 3 показывает, что рабочей длине LИГ = 10 мм конического участка пресс-иглы соответствует основная стадия процесса, характеризуемая установившимся течением металла. Значению максимально- го усилия прессования Pmax равного 44,5 кН, возникающего в заключительной стадии, во время которой установившееся течение металла нарушается, соответствует цилиндрический участок пресс-иглы, длина которого LЦ равна 18 мм.
Для определения фактических значений геометрических размеров экспериментально изготовленных труб были построены в двухкратном увеличение абрисы продольных планок соответствующих стенок, некоторые из которых представлены на рис. 4.
Для построения абрисов продольных планок соответствующих стенок использовался программный комплекс «Corel Draw X4». Последующая обработка и определение размеров продольных планок стенок труб с точностью до десятых долей осуществлялись с применением программного комплекса «КОМПАС-3D V10».
Таким образом, проведена экспериментальная проверка корректности и достоверности методики расчета профилировки инструмента для прессования труб с уменьшением толщины стенки на ее заднем участке, в результате которой уточнены особенности протекания данного процесса, представленные в работе [3], позволяющие производить соответствующие расчеты с минимальным значением относительной погрешности.
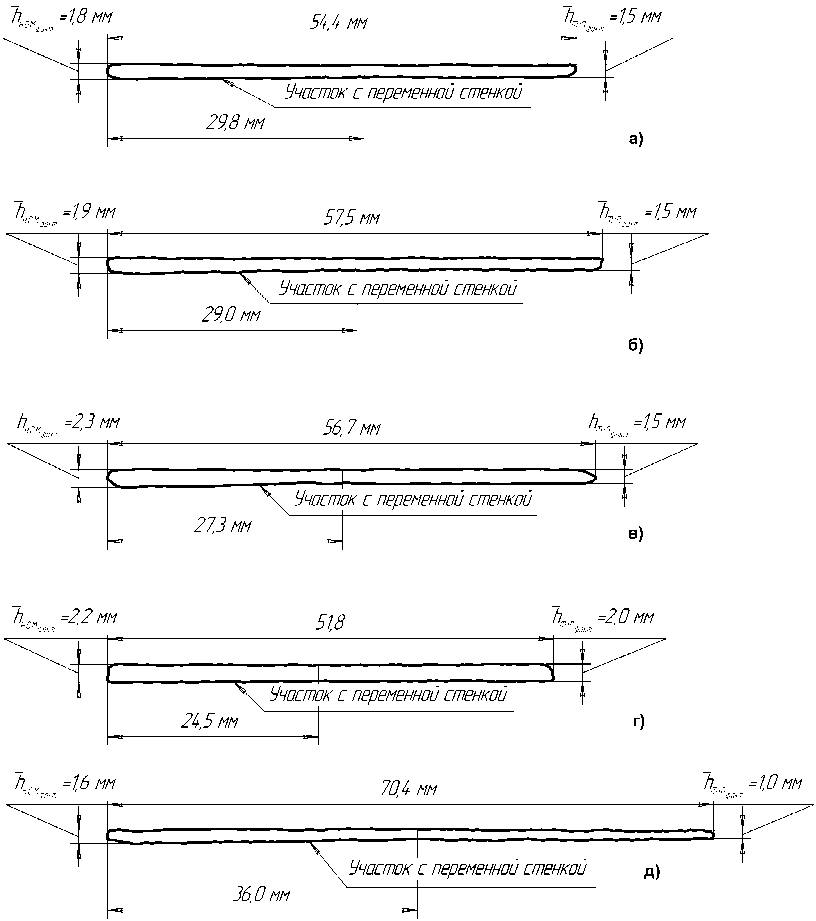
Рис. 4. Абрисы продольных планок соответствующих стенок: а – образец № 1; б – образец № 5; в – образец № 7; г – образец № 10; д – образец № 15
Список литературы Экспериментальное исследование процесса прессования труб переменного сечения
- Зиновьев А. В. Технология обработки давлением цветных металлов и сплавов: учеб. для вузов/А.В. Зиновьев, А.И. Колпашников, П.И. Полухин. -М.: Металлургия, 1992. -512 с.
- Баричко Б.В. Снижение расходного коэффициента при изготовлении труб/Б. В. Баричко, Я.И. Космацкий//Вестник ЮУрГУ. Серия «Металлургия.». -2010. -Вып. 15. -№ 34 (210). -С. 68-70.
- Совершенствование технологии редуцирования в ТПЦ-2. Разработка режимов калибровки, обеспечение снижения затрат на производство прессованных труб: отчет о НИР (закл.): 1.21.1-К-67/09/Российский научно-исследовательский институт трубной промышленности; рук.: А.В. Выдрин; исполн.: Я.И. Космацкий, П.А. Мальцев. -Челябинск, 2011. -103 с.