Электролитно-плазменное упрочнение поверхностных слоев алюминиевого сплава
Автор: Комбаев К.К., Квеглис Л.И.
Журнал: Журнал Сибирского федерального университета. Серия: Техника и технологии @technologies-sfu
Статья в выпуске: 4 т.11, 2018 года.
Бесплатный доступ
В данной статье приведены результаты исследований влияния электролитно-плазменной обработки на структурно-фазовое превращение образцов алюминиевого сплава. Разряд зажигался от источника постоянного тока. При включении напряжения происходит ионизация и кипение электролита. При возникновении пузырькового кипения вокруг активного электрода наблюдаются большие пульсации силы тока. Вследствие образования газопаровой рубашки и прохождения через нее электрического тока образуется низкотемпературная плазма, которая имеет характерный голубой цвет свечения оболочки вокруг детали. На поверхности изделия возбуждается электрическая микродуговая плазма, в которой от тепловыделения происходит интенсивный разогрев заготовки. После микродугового оксидирования на поверхности образца наблюдается микроструктура закалки и искусственного старения в потоке электролита. В результате закалки в потоке электролита твердый α-раствор меди в алюминии и точечные мелкодисперсные включения растворяются от температуры микроплазмы, фазы, окисляясь, образуют корунд алюминия. Рентгеноструктурный анализ образцов после электролитно-плазменной обработки выявил увеличение интенсивности и уширение дифракционных линий относительно исходного состояния, что свидетельствует об остаточном напряжении поверхности, которая в процессе эксплуатации обеспечивает повышение износостойкости детали. Средняя микротвердость после электролитноплазменной обработки составляет 746 МПа, что примерно в 2,5 раза выше, чем у исходного материала.
Алюминий, электролитно-плазменная обработка, микродуговое оксидирование, микроструктура
Короткий адрес: https://sciup.org/146279375
IDR: 146279375 | DOI: 10.17516/1999-494X-0069
Текст научной статьи Электролитно-плазменное упрочнение поверхностных слоев алюминиевого сплава
Рис. 1. Диаграмма состояния Al-Cu: штриховая линия – температура закалки
Fig. 1. The phase diagram of Al-Cu: dashed line is quenching temperature
После закалки следует старение, при котором сплав выдерживают при нормальной температуре несколько суток (естественное старение) или в течение 10-24 ч при повышенной температуре 150-200 °С (искусственное старение) [3].
Однако после закалки со старением поверхность окисляется, требует механической обработки, и получаемые покрытия не обеспечивают высокой износостойкости восстановленной поверхности.
Методика проведения исследований
Микроплазменная обработка применяется для весьма узкого круга материалов и в подавляющем большинстве направлена на получение прочного и износостойкого оксидного слоя на поверхности анода из алюминия и его сплавов [4]. Между тем потенциал этого метода еще не раскрыт, что связано с малой изученностью закономерностей формирования микроплаз-менных разрядов на поверхности анода и катода в различных электролитах и их влияния на структуру и свойства поверхности электродов. Для разработки технологии нанесения различных покрытий на поверхность детали при помощи микроплазменных разрядов в электролитах требуется изучить закономерности их формирования и воздействия на поверхность катода. Известно альтернативное устройство для микродугового оксидирования (МДО) колодцев корпуса шестеренного насоса из сплава алюминия [5]. Наиболее сильное структурное упрочнение алюминиевых сплавов проявляется при микродуговом оксидировании.
Для исследования микродугового оксидирования образцы размером 10×10×20 мм (рис. 2) вырезали из сплава алюминия AЛ3 ГОСТ2685-75 алмазным диском толщиной в 1 мм, который погружен в охлаждающую жидкость. При малых оборотах резания n = 350 об/мин и низкой нагрузке m = 250 г образец не испытывает термической деформации [6].
Экспериментальные исследования и механические испытания проводили в Региональной университетской лаборатории инженерного профиля «ІРГЕТАС» ВКГТУ им. Д. Серикбаева (г. Усть-Каменогорск) и в научно-технологическом парке «Лаборатории инженерного профиля» КазНТУ им. К.И. Сатпаева (г. Алматы) [7]. Элементный состав алюминиевого образца исследовали на растровом электронном микроскопе JSM-6390LV фирмы JEOL (Япония) с приставкой энергодисперсионного микроанализа INCAEnergy фирмы «OXFORD Instruments» [8]. Определяемые элементы – от бора до урана. Качественный и количественный фазовый анализ структуры образцов алюминиевого сплава проводили на рентгеновском дифрактометре ДРОН-3 в фильтрованном излучении медного анода, также «X′Pert PRO» фирмы «PANanalytical», с применением Cu -Kα -излучения [9].
Разряд зажигался от источника постоянного тока. На рис. 3 а изображена схема источника постоянного тока, который состоит из кнопочного поста, пускателя, диодного моста, дросселя, автомата, амперметра, вольтметра и других электроприборов. Катод – образец из алюминия (AЛ3: 1,5-3,0 Cu; 0,35-0,6 Mg; 4,5-5,5 Si; 0,6-0,9 Mn), погружен на глубину 4-6 мм в электролит – 10%-ный водный раствор Na 2 CO 3 [10].
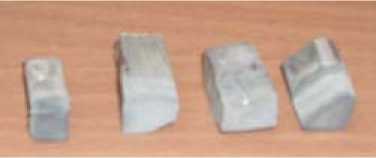
Рис. 2. Образцы для микродугового оксидирования
Fig. 2. Pieces for micro arc oxidation
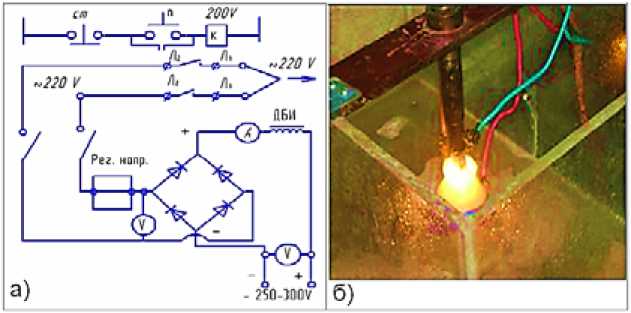
Рис. 3. Схема источника постоянного тока для микродугового оксидирования алюминиевых сплавов: а) электросхема источника постоянного тока, б) микродуговое оксидирование алюминия
Fig. 3. Scheme of a constant current source for micro arc oxidation of aluminum alloys: a) the electro scheme of constant current source, б) micro arc aluminum oxidation
При включении напряжения на поверхности изделия возбуждается электрическая микродуга (рис. 3 б ), в которой от тепловыделения происходит интенсивный разогрев заготовки. Анод, имеющий форму диска диаметром 50 мм, толщиной 2 мм, с просверленными отверстиями Ø4 мм, изготовлен из нержавеющей стали 12Х18Н10Т.
Необходимо отметить тот факт, что качество поверхностного слоя, получаемого при ми-кродуговом оксидировании, в значительной степени зависит от режимов процесса. От них зависит мощность искровых разрядов и, соответственно, энергия воздействия на упрочняемую поверхность. При плавном увеличении приложенного постоянного напряжения происходит электролиз соли, при этом, согласно закону Ома, растет и ток (участок 0 – А, рис. 4). Для данного участка характерно пропорциональное увеличение силы тока при увеличении напряжения. При этом увеличивается и температура электролита, что является следствием прохождения тока через электролит [11].
При достижении определенного значения напряжения (100–180 В) на поверхности катода – детали начинает вскипать электролит, происходит активное выделение пузырьков у поверхности (пузырьковое кипение). При пузырьковом кипении температура детали близка к температуре кипения воды. При возникновении пузырькового кипения вокруг активного электрода наблюдаются большие пульсации силы тока. Их амплитуда значительно уменьшается при разогреве детали свыше 470 °C [12]. При дальнейшем повышении выпрямленного напряжения появляется пленочное кипение (точка А, рис. 4), для которого характерно исчезновение пузырькового кипения и резкое падение силы тока вследствие того, что образующаяся газопаровая оболочка имеет большее электрическое сопротивление, чем жидкий электролит (участок А – В, рис. 4). Поскольку газопаровая рубашка является менее электропроводной, то основное падение напряжения происходит именно в этой зоне, где и выделяется большее количество тепла. Вследствие образования газопаровой рубашки и прохождения через нее электрического тока образуется низкотемпературная плазма, которая имеет характерный голубой цвет свечения оболочки вокруг детали. Чем
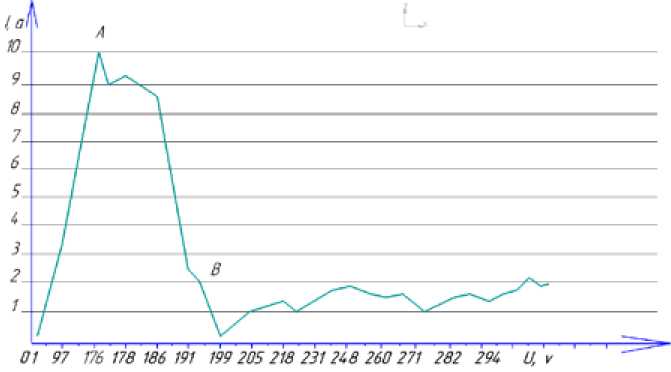
Рис. 4. Вольтамперная характеристика процесса электролитно-плазменной обработки
Fig. 4. Voltage-current characteristic of the electrolytum-plasma treatment ярче голубой цвет горения плазмы, тем больше в ней содержится ионов, в том числе ионов-модификаторов. При дальнейшем увеличении напряжения наблюдается образование аномального разряда [13].
Результаты исследований и их обсуждение
Экспериментально установили оптимальные режимы микродугового оксидирования алюминия: напряжение U =200 В, сила тока I =10 А, время нагрева t=2 с, время закалки в потоке электролита t=24 с, общее количество циклов n=15 [14]. Предварительно установили зависимость температуры нагрева от времени нагрева, охлаждения и напряжения, которое выражено формулой:
Т= 4.5xt 2наг + 4.8xU- 18хt 0X л. , (1)
где Т – температура нагрева образца; tнаг. – время нагрева; tохл. – время охлаждения в потоке электролита; U – напряжение источника питания.
Микродуга возникает между катодом и жидким электролитом [15]. Особое влияние на структурные превращения оказывает периодическое повышение температуры при подключении источника питания, которая возрастает выше точки фазового α →Ж-превращения (548 °С). После отключения источника питания микродуга гаснет, что обеспечивает доступ электролита к разогретому сплаву и его быстрое охлаждение (закалка).
В структуре алюминиевого сплава в равновесном состоянии присутствуют зерна α-твердого раствора (рис. 5 а ), в состав которого входят медь, марганец и магний, дисперсные включения Mg2Si.
После микродугового оксидирования наблюдается микроструктура закалки и искусственного старения в потоке электролита (рис. 5 б ). В результате закалки твердый а -раствор меди в алюминии и точечные мелкодисперсные включения растворяются от температуры микроплазмы, эти фазы, окисляясь, образуют корунд алюминия. Результаты элементного анализа после
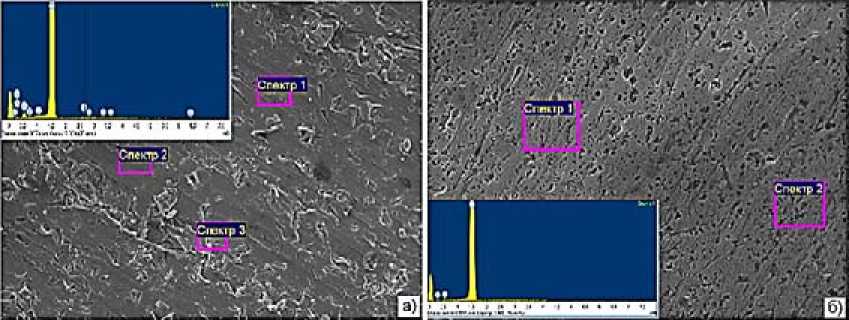
Рис. 5. Микроструктура алюминиевого сплава АЛ3: а) в исходном состоянии, б) после микродугового оксидирования
Fig. 5. The microstructure of aluminum alloy AL3: a) in the initial state, б) after the micro arc oxidation микродугового оксидирования (табл. 1) свидетельствуют о появлении кислорода и включении соответствующих элементов упрочняемому сплаву алюминия.
Включения выделились из твердого α -раствора в процессе искусственного старения. После старения поверхностный слой алюминия оксидируется. Элементы, выделяясь в дисперсной форме, упрочняют сплав. Могут быть обнаружены частицы CuAl2 и частицы магния [16]. Для выявления структурно-фазовых превращений алюминия в результате термического воздействия микродугового оксидирования провели рентгеноструктурный анализ [17]. Рентгеноструктурный анализ образцов алюминия в исходном состоянии поставки и после микродуго-вого оксидирования (рис. 5) выявил наличие линий α -фазы на основе Аl.
После микродугового оксидирования наблюдается увеличение интенсивности и уширение дифракционных линий (рис. 6 б ) относительно исходного состояния (рис. 6 а ), что свидетельствует об остаточном напряжении поверхности, которая в процессе эксплуатации обеспечивает повышение качества детали.
Для определения фазового состава образца алюминиевого сплава, обработанного ми-кродуговым оксидированием, осуществили компьютерную статистическую обработку результатов [18]. Рентгенофазовый анализ образцов показал наличие фаз оксида алюминия. Значения межплоскостных расстояний свидетельствуют, что угловые положения дифракционных линий образцов совпадают не полностью, а их интенсивности отличаются значительно (табл. 2).
Таблица 1. Элементный состав алюминия после МДО (к рис. 5 б )
Table 1. Elemental composition of aluminum after MDO
Спектр |
O |
Na |
Al |
Si |
Cu |
Итог |
Спектр 1 |
2.58 |
- |
97.42 |
- |
- |
100.00 |
Спектр 2 |
4.95 |
0.32 |
93.49 |
0.76 |
0.48 |
100.00 |
(все результаты в весовых %).
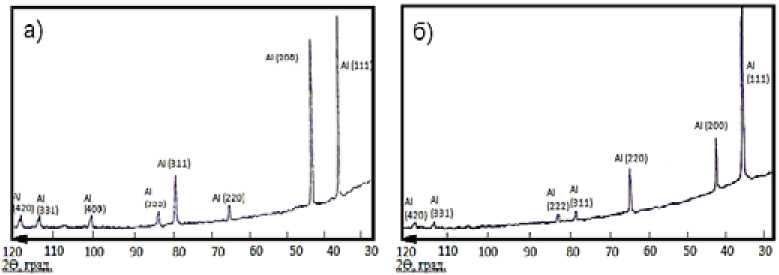
Рис. 6. Рентгеновская дифрактограмма алюминиевого сплава: а) – в исходном состоянии, б) – после микродугового оксидирования
Fig. 6. X-ray diffraction pattern of an aluminum alloy: a) in the initial state, б) after the micro arc oxidation
Таблица 2. Фазовый состав образца алюминия после МДО
Table 2. Phase composition of the aluminum sample after MDO
№ |
I, мм |
2θ, град |
θ, град |
Sin θ |
d/n, A |
I, % |
d/n, A |
I, % |
hkl |
d/n, A |
I, % |
hkl |
1 |
680 |
38,64 |
19,32 |
0,3308 |
2,330 |
100 |
2,338 |
100,0 |
111 |
2,315 |
45 |
401 |
2 |
56 |
44,84 |
22,42 |
0,3814 |
2,021 |
8,0 |
2,024 |
47,0 |
200 |
2,019 |
45 |
112 |
3 |
50 |
65,3 |
32,65 |
0,5395 |
1,429 |
7,0 |
1,431 |
22,0 |
220 |
1,426 |
10 |
710 |
4 |
11 |
78,42 |
39,21 |
0,6322 |
1,219 |
2,0 |
1,221 |
24,0 |
311 |
|||
5 |
10 |
82,58 |
41,29 |
0,6599 |
1,168 |
1 |
1,169 |
7 |
222 |
|||
6 |
7 |
112,2 |
56,1 |
0,8300 |
0,929 |
1 |
0,929 |
8 |
331 |
|||
7 |
7 |
116,62 |
58,31 |
0,8509 |
0,906 |
1 |
0,905 |
8,0 |
420 |
Таблица 3. Результаты микротвердости после МДО
Table 3. Microhardness results after MDO
№ |
z1 |
z3 |
z2 |
z4 |
zr |
zb |
z |
d |
H,МПа |
L,мкм |
Hcp |
Нср-Н |
(Нср-Н)^2 |
1 |
250 |
408 |
172 |
325 |
158 |
153 |
155,5 |
34,21 |
777,56 |
0 |
746 |
-32,06 |
1027,89 |
2 |
250 |
411 |
160 |
320 |
161 |
160 |
160,5 |
35,31 |
729,87 |
100 |
746 |
15,63 |
244,33 |
3 |
250 |
412 |
161 |
320 |
162 |
159 |
160,5 |
35,31 |
729,87 |
200 |
746 |
15,63 |
244,33 |
4 |
250 |
407 |
164 |
322 |
157 |
158 |
157,5 |
34,65 |
757,94 |
300 |
746 |
-12,44 |
154,71 |
5 |
250 |
405 |
163 |
325 |
155 |
162 |
158,5 |
34,87 |
748,41 |
400 |
746 |
-2,90 |
8,44 |
6 |
250 |
407 |
160 |
324 |
157 |
164 |
160,5 |
35,31 |
729,87 |
500 |
746 |
15,63 |
244,33 |
7 |
250 |
410 |
160 |
323 |
160 |
163 |
161,5 |
35,53 |
720,86 |
600 |
746 |
24,64 |
607,21 |
8 |
250 |
410 |
163 |
320 |
160 |
157 |
158,5 |
34,87 |
748,41 |
700 |
746 |
-2,90 |
8,44 |
9 |
250 |
409 |
164 |
318 |
159 |
154 |
156,5 |
34,43 |
767,66 |
800 |
746 |
-22,16 |
490,87 |
10 |
250 |
408 |
164 |
322 |
158 |
158 |
158 |
34,76 |
753,15 |
900 |
746 |
-7,65 |
58,51 |
11 |
250 |
411 |
164 |
322 |
161 |
158 |
159,5 |
35,09 |
739,05 |
1000 |
746 |
6,45 |
41,61 |
12 |
250 |
410 |
163 |
321 |
160 |
158 |
159 |
34,98 |
743,71 |
1100 |
746 |
1,79 |
3,22 |
13 |
250 |
407 |
161 |
320 |
157 |
159 |
158 |
34,76 |
753,15 |
1200 |
746 |
-7,65 |
58,51 |
14 |
250 |
409 |
162 |
324 |
159 |
162 |
160,5 |
35,31 |
729,87 |
1300 |
746 |
15,63 |
244,33 |
15 |
250 |
408 |
163 |
321 |
158 |
158 |
158 |
34,76 |
753,15 |
1400 |
746 |
-7,65 |
58,51 |
Это может быть обусловлено тем, что при обработке от высокой температуры плазмы возникает внутреннее напряжение. Источниками напряжений являются: градиенты температур по сечению; неоднородность химического состава; структурные несовершенства; разная ориентировка кристаллов в пространстве; различный удельный объем и различные коэффициенты линейного расширения фаз [19].
Микротвердость возросла на всех режимах обработки микродугового оксидирования сплава алюминия. Средняя микротвердость, достигнутая при микродуговом оксидировании, составляет 746 МПа (табл. 3), что примерно в 2,5 раза выше, чем у исходного материала (рис. 7).
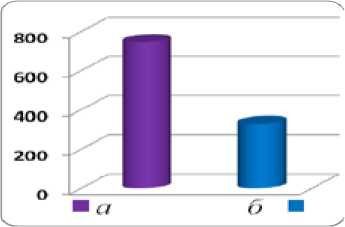
Рис. 7. Среднее значение микротвердости: а – после МДО, б – в исходном состоянии
Fig. 7. The average value of micro hardness: a – after mаo, б – in the initial state
После микродугового оксидирования наблюдается повышение значений микротвердости (рис. 7 а ) относительно исходного состояния (рис. 7 б ), что, безусловно, повышает эксплуатационные качества деталей из алюминиевого сплава.
Выводы
Для упрочнения алюминиевого сплава вместо традиционной термической обработки предложена альтернативная технология электролитно-плазменного упрочнения. Образцы из алюминиевого сплава АЛ3 ГОСТ2685-75 подвергались циклическому нагреву от температуры микроплазмы и закаливались в потоке электролита. Нагрев до температуры структурно-фазовых превращений происходит при значительно низких энергозатратах по сравнению с традиционной термообработкой. Экспериментально установили оптимальные режимы микродугового оксидирования алюминия: напряжение источника питания U =200 В, сила тока I = 10 А, время нагрева t=2 с, время закалки t=24 с, общее количество циклов n=15. Предварительно установили зависимость температуры нагрева от времени нагрева, охлаждения и напряжения, которая выражена формулой: Т= 4.5хt2наг + 4.8хи - 18хtохл. После микродугового оксидирования наблюдается микроструктура закалки и искусственного старения в потоке электролита. В результате закалки твердый а -раствор меди в алюминии и точечные мелкодисперсные включения растворяются от температуры микроплазмы, эти фазы, окисляясь, образуют корунд алюминия. Рентгеноструктурный анализ образцов после электролитно-плазменной обработки выявил увеличение интенсивности и уширение дифракционных линий относительно исходного состояния, что свидетельствует об остаточном напряжении поверхности, которая в процессе эксплуатации обеспечивает повышение износостойкости детали. Средняя микротвердость после электролитно-плазменной обработки составляет 746 МПа, что примерно в 2,5 раза выше, чем у исходного материала.
Список литературы Электролитно-плазменное упрочнение поверхностных слоев алюминиевого сплава
- Pogrebnjak A.D., Kylyhkanov M.K., Gritsenko B.P., Duvanov S.M., Pogrebnjak N.A., Ponaryadov V.V. Technical Physics Letters, Moscow, 2006, 32(12). 1060-1063.
- Новиков. А.Н., Кузнецов Ю.А., Хромов В.Н. Устройство для микродугового оксидирования колодцев корпуса шестеренного насоса. Патент RU2147324C1
- Комбаев К.К., Кылышканов М.К., Лопухов Ю.И. Влияние электролитно-плазменной обработки стали 18ХН3МА-Ш на поверхностную микроструктуру и твердость. Журнал Сибирского федерального университета, серия «Техника и технологии», 2009, 2(4), 394-399
- Комбаев К.К., Смагулов Д.У., Кылышканов М.К. Структурно-фазовые превращения в стали 18ХН3МА-Ш при электролитно-плазменной обработке. Вестник КазНТУ им. К.И. Сатпаева, 2010. 3(79), 199-206
- Тюрин Ю.Н., Погребняк А.Д. Электрическое нагревание с использованием жидкого электрода. Технология поверхности и покрытия, 142-144 (2001), 293-299
- Кылышканов М.К., Комбаев К.К. Методы поверхностного упрочнения чугуна на основе электролитно-плазменной обработки. Вестник ВКГТУ. Усть-Каменогорск, 2008, 3, 46-49
- Кылышканов М.К., Комбаев К.К. Методы поверхностного упрочнения деталей на основе электролитно-плазменной обработки. Вестник ВКГТУ. Усть-Каменогорск, 2008. 4, 59-61
- Комбаев К.К., Кылышканов М.К. Влияние режимов электролитно-плазменной закалки на структуру и свойства стали бурового долота. Труды КарГТУ. Караганда, 2009, 2, 16-18
- Комбаев К.К., Кылышканов М.К., Скаков М.К. Исследование влияния электролитно-плазменной обработки на структуру и износостойкость стали бурового инструмента. Вестник КазНТУ. Алматы, 2010, 1(77), 105-111
- Комбаев К.К., Кылышканов М.К., Лопухов Ю.И. Исследование свойств модификации поверхности после электролитно-плазменной обработки стали 18ХН3МА-Ш. Вестник Национальной инженерной академии Республики Казахстан. Алматы, 2009, 2(32), 142-146
- Кожа Е., Комбаев К.К., Смагулов Д.У. Элктролиттi -плазмалық өңдеу кезiндегi азкөмiртектi легiрленген болаттағы құрылымдық фазалық өзгеру. Вестник КазНТУ им. К.И. Сатпаева. Алматы, 2014, 3(103), 300-307
- Еркин К., Смагулов Д.У., Комбаев Қ. Электролиттi-плазмалық өңдеуден кейiнгi болаттың беткi қабатының құрылысы мен қасиеттерiнiң өзгеруi. Қазақстан-Британ Техникалық университетiнiң хабаршысы Алматы, 2017, 2-3(41-42), 101-105.
- Комбаев К.К., Смагулов Д.У., Кожа Е., Ахметова Г.Е. Лабораторная установка для электролитно-плазменной обработки стали. Нанотехнологии наука и производство, 2016, 4, 49-55
- Тюленин А.Н., Тюрин Ю.Н., Граднев А.И. Гистерезис вольтамперных характеристик источников питания. МИТОМ., М., 1988, 1, 9-12
- Комбаев К.К., Скаков М.К., Путренко Н.Ф. Заключение о выдаче патента на полезную модель «Стенд для испытания материалов на трение и износ». МПК G01N 3/56 (2009.01)
- Кылышканов М.К., Комбаев К.К., Погребняк А.Д. Пат. 23178 РК. Способ электролитно-плазменного упрочнения деталей бурового долота. Дата подачи 06.05.2009г., зарегистрировано 20.09.2010 г., МПК С21D1/78 (2009.01), C21D 1/34 (2009.01)
- Комбаев К.К., Кожа Е., Смагулов Д.Ю. и Саде Б. Структурные фазовые переходы низкоуглеродистых сплавов при электролитно-плазменной обработке. 2016, 2-я Международная конференция по искусственному и промышленному проектированию. Beiging, China, 2016. Part 2. C. 491-495
- Кожа Е., Смагулов Д.Ю., Ахметова Г.Е., Комбаев К.К. Лабораторная установка для электролитической плазменной обработки стали. Известия Национальной академии наук Республики Казахстан. Алматы, nas rk, 2017, 4 (424), 219-225
- Комбаев К.К. Разработка технологии электролитно-плазменной обработки низкоуглеродистой легированной стали бурового инструмента. Монография, Алматы «Эверо», 2015. 92 с.