К концепции шахтного подземного выщелачивания металлов
Автор: Габараев О. З., Габараева А. О., Дедегкаева Н. Т., Болотбеков Ж.
Журнал: Горные науки и технологии @gornye-nauki-tekhnologii
Рубрика: Разработка месторождений полезных ископаемых
Статья в выпуске: 4 т.5, 2020 года.
Бесплатный доступ
Актуальность проблемы восполнения выбывающих запасов для обеспечения минеральной безопасности России объясняется изменением экономической системы России, изменением географии добычи металлов и ослаблением минерально-ресурсной базы горного производства при переходе от открытого способа к подземному. Приведены сведения о шахтном выщелачивании металлов в историческом срезе. Показана роль российских ученых и научно-исследовательских организаций в исследовании процессов добычи металлов выщелачиванием. Приведены примеры применения технологии на рудниках СССР, СНГ и стран дальнего зарубежья с характеристикой особенностей осуществления. Сформулированы основные недостатки шахтного подземного выщелачивания: низкая скорость получения металлов и трудность осуществления контроля полноты процесса извлечения металлов в продукционный раствор. Отмечено, что при подземном выщелачивании даже хорошо раздробленных руд процесс длится годами, что снижает привлекательность технологии по сравнению с традиционными способами добычи металлов в равных условиях. Описаны известные и новые перспективные методы интенсификации процесса с целью увеличения скорости извлечения металлов в раствор. На примере Северокавказских месторождений Садонской группы показана целесообразность применения технологии подземного выщелачивания для доработки ныне потерянных для традиционной технологии запасов. Охарактеризована роль профессора Остроушко И. А. в изыскании и внедрении способов извлечения металлов, оставленных в отработанных пространствах рудников, в частности, путем извлечения металлов из сточных вод месторождений Садона. Даны сведения о современном состоянии использования технологии. Сделан вывод о недостаточности использования этой перспективной технологии в практике разработки вскрываемых руд в условиях отдельных регионов. Впервые уточнены детали общей концепции подземного выщелачивания: возможность применения шахтного выщелачивания руд не только в благоприятных условиях, но и при невыдержанных элементах залегания и неравномерной минерализации, возможность выщелачивания не только некондиционных для традиционных технологий руд, но и балансовых запасов, и сформулирована возможность подземного блокового выщелачивания как альтернатива традиционным технологиям в конкретных условиях, например, на месторождениях Северного Кавказа.
Добыча металлов, шахтное подземное выщелачивание, продуктивный раствор, руда, интенсификация процесса, потерянные запасы
Короткий адрес: https://sciup.org/140250771
IDR: 140250771 | DOI: 10.17073/2500-0632-2020-4-349-357
Текст научной статьи К концепции шахтного подземного выщелачивания металлов
Актуальность проблемы восполнения выбывающих запасов для обеспечения минеральной безопасности России объясняется изменением экономической системы России, изменением географии добычи металлов и ослаблением минеральноресурсной базы горного производства при переходе от открытого способа к подземному [1–3].
О промышленном выщелачивании цветных металлов известно с ХVI в. (Испания). Широкое освоение способа связано с добычей меди на руднике «Кананеа» в Мексике (1924 г.) и на Урале (1930–1940 годы). Подземное выщелачивание металлов из руд в России было предсказано академиком А.Е. Ферсманом.
В настоящее время подземное выщелачивание применяется для добычи цветных металлов в США, России, Франции, Японии, Австралии, ФРГ и др. странах [4–7].
Исследованиями по добыче полезных ископаемых методами выщелачивания на гео-технологических предприятиях ранее других начали заниматься ИПКОН РАН, ВНИИХТ, ВНИПИПТ, СКГМИ (ГТУ) и лаборатории предприятий атомной отрасли.
Опытно-промышленные испытания шахтного подземного выщелачивания были начаты на Блявинском руднике Медногорского медно-сер-ного комбината в 1971 г. Наибольшие успехи достигнуты при выщелачивании меди, урана и золота на предприятиях атомной отрасли СССР.
Как правило, объектами подобных исследований служили руды месторождений, отработка которых традиционными методами была экономически нецелесообразна [8–11]. В 1970-х годах был отработан первый блок балансовых руд, а в настоящее время Приаргунский комбинат выщелачиванием добывает половину своей продукции.
Еще в 1974 г. этим методом получали 20 % мировой добычи меди. Его доля в мировом производстве некоторых полезных ископаемых достигает величины 80% [12–15]. Только в США подземным выщелачиванием ежегодно добывают 300 тыс. тонн меди и 4 тыс. тонн урана.
Целью исследований по указанной проблеме являются в том числе обобщение и систематизация сведений о добыче металлов методами выщелачивания. Задачей исследования является обоснование технологически корректных, безопасных и экономически эффективных параметров технологий шахтного выщелачивания с использованием натурных и лабораторных методов, включая ретроспективный анализ практики выщелачивания в первую очередь на предприятиях урановой отрасли.
Общая часть
Условия применения . Возможность применения технологий выщелачивания определяется в основном минералогическим составом руды и составом породообразующих минералов.
Процесс выщелачивания урана из кусковой руды можно разделить на два периода: начальный, когда уран извлекается с поверхностных и приповерхностных частей рудных кусков, и конечный, когда уран извлекается из глубины куска. Переход урана из руды в раствор реагента заключается в прямом взаимодействии поверхности минералов с растворителем, фильтрующимся через слой руды, и в диффузионном перемещении растворенных солей в подвижном поровом растворе (рис. 1).
2020;5(4):349-357
МИСиС
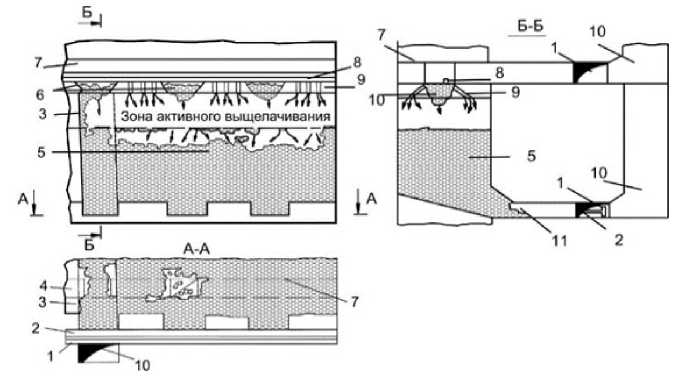
Рис. 1. Блок подземного выщелачивания металлов: план и разрезы:
1 – этажные штреки; 2 – приемник растворов; 3 – отрезная щель; 4 – отрезной восстающий; 5 – руда; 6 – рудоспуски; 7 – верхний штрек; 8 – трубопровод для подачи раствора; 9 – скважины для подачи раствора; 10 – восстающие;
11 – выпускные выработки
Fig. 1. In-situ metal leaching block: plan and sections:
1 – level drifts; 2 – pregnant solution receiver; 3 – slot; 4 – slot raise; 5 – ore; 6 – ore passes;
7 – upper gangway; 8 – solution supply pipeline; 9 – holes for solution supply; 1 0 – raises; 11 – drawpoints
Tаблицa 1
Типизация шахтных систем разработки выщелачивания (по Голику В. И.)
Typification of ISL methods (according to V. I. Golik)
Типы магазина |
Варианты |
Условия применения |
В естественно-управляе- |
Из отбитой руды |
Устойчивые вмещающие |
мых массивах |
Из поданной извне руды |
породы |
В разрушенных массивах |
Под несущими перекрытиями |
Неустойчивые породы, склонные к обрушению |
Под разделяющими перекрытиями |
||
Без перекрытий |
||
В искусственно-закрепленных массивах |
С твердеющей закладкой |
Породы любой устойчивости |
С деревянной крепью |
||
С бетонной крепью |
||
В массивах из хвостов выщелачивания |
Кольматированные продуктами выщелачивания |
Породы, пригодные для выщелачивания |
С укреплением цементными растворами |
||
С химическим закреплением |
Выщелачивание полиметаллических руд с низкой пористостью (менее 5 %) и незначительной проницаемостью растворов (менее 1 м/с) требует их предварительного дробления буровзрывным способом и магазинирования. В СНГ и за рубежом эффективна скважинная отбойка руд с короткозамедленным взрыванием в зажатой среде. В качестве компенсационного пространства используются очистные выработки, суммарный объем которых составляет 30 % объема вовлекаемых в отработку руд.
Условия применения систем разработки приведены в табл. 1.
Технологию шахтного выщелачивания с обрушением руд целесообразно применять при разработке руд различной крепости и устойчивости мощностью от нескольких до десятков метров. Она позволяет управлять как крупностью дробления руд, так и контурами обрушаемой камеры, поэтому может найти применение при разработке рудных тел с невыдержанными элементами залегания и неравномерной минерализацией.
Практика шахтного выщелачивания. Опытно-промышленный блок впервые в мировой практике был отработан в крепких слоистых породах месторождения Восток на предприятии
2020;5(4):349-357
МИСиС
МАЭП в Северном Казахстане. Особенность его заключалась в том, что выщелачивались не забалансовые некондиционные для традиционных технологий руды, а балансовые.
Параметры блока: длина по простиранию 60 м, высота 36–65 м, средняя мощность 20 м. Подготовительно-нарезные работы включали в себя проведение блоковых восстающих, штреков оросительного, бурового, дренажно-бурового и дренажного горизонта, буровых рассечек, сбоек и отрезного восстающего.
Для бурения скважин применяли станки НКР-100 М, при частичном выпуске использовали погрузочно-доставочные машины МПДН-1 и ЛБ 125/1000.
Отбойку руды осуществляли с двух подэтажей – бурового и дренажно-бурового вертикальными восходящими веерами скважин диаметром 85 мм по сетке 2,5×2,6 м.
Орошение блока производилось как секционно (попеременно восточная и западная половины), так и по всей поверхности, кроме того, в середине эксперимента был подключен промежуточный горизонт орошения на уровне бурового подэтажа. Орошение осуществляется через скважины-оросители в отбитой руде горизонтально, обсаженные перфорированными трубами.
Контрольными выработками по замагази-нированной руде установлено:
-
- удовлетворительное дробление получено лишь в зонах выпуска;
-
- междуштрековые целики раздроблены на крупные обломки размерами более 300 мм и до 1 м;
-
- часть контура отбойки у бортов оказалась недробленой.
В блоке было произведено рыхление частично выщелоченной руды путем выемки целика, в результате чего образовалась пустота, которую погасили путем взрывания скважинными зарядами. Горная масса более чем на 50% была недоступной для выщелачивания.
Улучшению показателей выщелачивания способствует качественное дробление горного массива (рис. 2).
При подготовке руды этажным принудительным обрушением ее отбивали взрыванием зарядов глубоких скважин на всю высоту этажа. Эта технология перспективна для разработки мощных трещиноватых рудных залежей, не склонных к слеживанию, когда рудная минерализация приурочена к трещинам скола или тектоническим швам.
Такая технология применялась на урановом месторождении Северного Казахстана для отработки балансовых запасов системой слоевого обрушения. Выщелачивали забалансовые руды на двух горизонтах с высотой этажа 40 м. Отбойку руды производили глубокими скважинами.
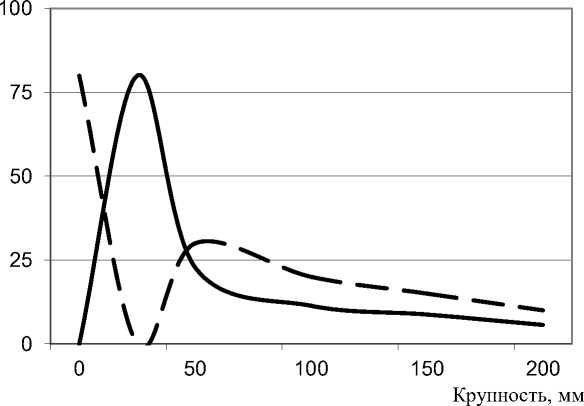
Рис. 2. Извлечение металлов из руд при подготовке:
1 – с магазинированием; 2 – с этажным обрушением
Fig. 2. Extraction of metals from ores using preparation:
1 – with shrinkage; 2 – with block caving
2020;5(4):349-357
МИСиС
Для равномерного разрыхления горной (рудной) массы на нижнем горизонте образовывали горизонтальную подсечку высотой 12 м. Подсечные скважины взрывались с опережением на 1–2 ряда относительно скважин в камере. Буровые выработки верхнего горизонта использовались для прокладки по ним оросительных трубопроводов, а невзорванные части скважин – для орошения горной массы.
Во всех случаях стремились рационально совместить функции подготовительно-нарезных выработок (рис. 3).
Технико-экономические показатели системы приведены в табл. 2.
Подобной технологией отработано урансодержащее месторождение Северного Казахстана (Целинный горно-химический комбинат), приуроченное к интрузивному массиву, сложенному лейкократовыми гранит порфирами. Сближенные рудные тела жильного типа
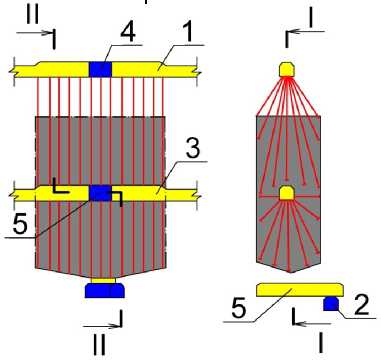
Рис. 3. Подготовка блока к выщелачиванию с совмещением функций выработок:
1 – оросительно-буровой штрек; 2 – нижний этажный штрек; 3 – буровой штрек; 4 – верхняя рассечка отрезной щели;
5 – нижняя рассечка отрезной щели; 6 – заходка
Fig. 3. Preparation of a block for leaching with combining mine working functions:
1 – sprinkling-drill drift; 2 – lower level drift; 3 – drill drift; 4 – slot upper crosscut; 5 – slot lower crosscut; 6 – cut
имели мощность от 1 – 5 см до 0,5 – 1,5 м и крутое (80 – 90 о ) падение. Рудная минерализация была приурочена к различного рода трещинам. Руда и вмещающие породы имели коэффициент крепости 8 – 15 по М.М. Протодьяконову.
На этом руднике использован вариант, при котором нижнюю подсечку образуют обрушением вееров нисходящих скважин из выработок верхнего горизонта и взрыванием концов дренажных скважин, пройденных с горизонта откатки.
Блоки характеризовались параметрами, м: высота 30 – 90; ширина 20 – 25; длина 30 – 40. Растворы подавались на горизонт орошения, где осуществлялась разводка оросительных систем. Продуктивные растворы улавливали с помощью скважин, пробуренных из выработок нижнего горизонта до зеркала подземных вод через 1,5 – 2 м.
Технико-экономические показатели процессов подготовки руд к подземному шахтному выщелачиванию приведены в табл. 3.
Таблица 2
Показатели технологии с этажным обрушением Performance of block caving
Наименование |
Показатели |
Производительность труда забойного рабочего, м 3 /смену |
17,7 |
Производительность бурения скважин, м/смену |
12,1 |
Удельный расход ВВ, кг/м 3 |
1,2 |
Выход горной массы с 1 пог. м скважины |
5,6 |
Удельный вес подготовительно-нарезных выработок, % |
4–6 |
Таблица 3
Основные технико-экономические показатели Key performance indicators
Наименование показателей |
Величина |
Производительность труда забойного рабочего, м 3 /смену |
14–17 |
Производительность труда бурильщиков, м/смену |
12,1 |
Удельный расход ВВ, кг/м 3 |
0,9–1,2 |
Удельный вес подготовительно-нарезных выработок, % |
6–12 |
2020;5(4):349-357
МИСиС
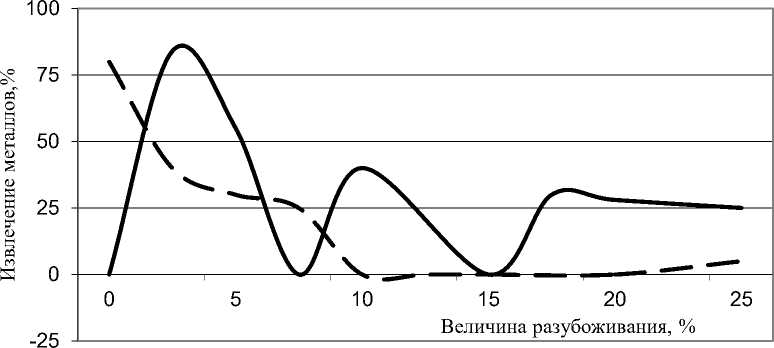
Рис. 4. Зависимость извлечения металлов от величины разубоживания руд при подготовке блоков :
1 – с магазинированием; 2 – с этажным обрушением
Fig. 4. Dependence of metal recovery on ore dilution during block preparation:
1 – with shrinkage; 2 – with block caving
Установлено, что на показатели извлечения металлов весьма существенно влияет разубоживание руд (рис. 4).
Интенсификация процессов выщелачивания. Основным недостатком шахтного подземного выщелачивания является низкая скорость получения металлов. При подземном выщелачивании даже хорошо раздробленных руд процесс длится 1 – 2 года, что значительно больше времени добычи традиционными способами. С целью увеличения скорости выщелачивания применяют методы интенсификации процесса.
Химические способы интенсификации выщелачивания имеют ограниченные возможности. Так, увеличение концентрации растворов кислот и щелочей более 5–8% не увеличивает скорость выщелачивания, а приводит к выщелачиванию пустых карбонатных и силикатных пород, что снижает содержание металлов в концентратах и удорожает процесс. Количество металлов, которое окисляется под действием «парникового эффекта», можно рассчитать на основании минералогического состава руд и данных воздушной и гидрометаллометрических съемок.
Исследования влияния поверхностно-активных веществ на скорость выщелачивания показали, что увеличение ее возможно в 1,5 – 2 раза за счет добавок.
Биологические способы интенсификации выщелачивания по результативности значительно превосходят химические. Путем адаптации, а также используя мутагенные факторы, получают культуры новых бактерий с большей скоростью выщелачивания.
2020;5(4):349-357
МИСиС
Физические способы интенсификации процессов выщелачивания обеспечивают увеличение скорости за счет активизации процессов окисления, уменьшения крупности руд и т.п., что позволяет эффективно производить добычу полезных ископаемых при кучном и подземном выщелачивании. Термическое воздействие увеличивает скорость выщелачивания в 2 – 3 раза при повышении температуры среды до +35 °С при бактериальном выщелачивании и до +80 °С – при химическом выщелачивании.
При воздействии электрическим током низкого напряжения скорость выщелачивания меди увеличивается в 2 – 3 раза. Воздействие током высокой частоты на сульфидные руды повышает скорость выщелачивания в 5 – 6 раз.
Основой механического способа интенсификации является перемещение кусков частично выщелоченной руды силой тяжести, воздействием взрыва, механизмами и машинами.
В практике выщелачивания производились опыты по рыхлению блоков выщелачивания взрыванием зарядов ВВ в отбитой руде и скважинах. Ударное воздействие взрывов невелико ввиду значительного (20 – 40%) объема пустот в материале, подвергаемом рыхлению, воздействие наблюдалось в зоне радиусом порядка нескольких диаметров заряда.
Применение технологий подземного выщелачивания возможно, например, для доработки Архонского, Садонского, Згидского, Холстинского и Фиагдонского месторождений (РСО-Алания). В их выработанном пространстве с суммарной площадью проекции на вертикальную плоскость 2,3 млн м 2 , осталось в виде эксплуатационных потерь и в боковых оруденелых породах около 54 млн тонн рудной массы, отработка которой традиционными технологиями невозможна.
Несмотря на наличие исследований в области физико-химических технологий добычи металлов, некоторые их области изучены недостаточно. Это прежде всего применение теории и передового опыта выщелачивания к условиям отдельных регионов.
С результатами исследований по рассматриваемой проблеме корреспондируют исследования по сопутствующим направлениям горного дела, включающим подготовку руд к выщелачиванию, осуществление контроля процесса и др. [16 – 20].
Заключение
Дефицит металлов для промышленности может быть восполнен расширением области применения технологий шахтного подземного выщелачивания металлических руд. Накопленный опыт разработки металлических месторождений позволяет детализировать концепцию развития прогрессивных природо- и ресурсосберегающих технологий добычи металлов подземным способом.
Обоснование корректных, безопасных и эффективных технологий шахтного выщелачивания включает в себя ретроспективный анализ практики выщелачивания на предприятиях урановой отрасли.
Технология шахтного выщелачивания с обрушением руд позволяет управлять крупностью дробления руд и контурами обрушаемых массивов при невыдержанных элементах залегания и неравномерной минерализацией в процессе разработки мощных залежей, особенно когда рудная минерализация приурочена к трещинам скола или тектоническим швам.
Опыт подтверждает возможность выщелачивания не только некондиционных для традиционных технологий руд, но и балансовых.
Технологии подземного выщелачивания могут продлить сроки эксплуатации месторождений с комфортными условиями отработки, например, на Северном Кавказе, отработка которых традиционными технологиями неэффективна.
Возможности технологий добычи металлов выщелачиванием могут быть расширены за счет творческого применения теории и передового опыта к условиям отдельных регионов.
2020;5(4):349-357
МИСиС^
Список литературы К концепции шахтного подземного выщелачивания металлов
- Разоренов Ю.И., Голик В. И., Куликов М. М. Экономика и менеджмент горной промышленности: учеб. пособие для студентов высших учебных заведений, обучающихся по горно-геологическим специальностям. Новочеркасск; 2010.
- Дмитрак Ю. В., Камнев Е. Н. АО "Ведущий проектно-изыскательский и научно-исследовательский институт промышленной технологии" - путь длиной в 65 лет. Горный журнал. 2016;3:6-12.
- Ghorbani Y., Franzidis J.-P., Petersen J. Heap Leaching Technology - Current State, Innovations, and Future Directions: A review. Mineral Processing and Extractive Metallurgy Review. 2016;37(2):73-119.
- Jarvie-Eggart M. E. Responsible Mining: Case Studies in Managing Social & Environmental Risks in the Developed World. Englewood, Colorado: Society for Mining, Metallurgy and Exploration; 2015. 804 р.
- Дмитрак Ю. В., Цидаев Б. С., Дзапаров В. Х., Харебов Г. Х. Минерально-сырьевая база цветной металлургии России. Вектор ГеоНаук. 2019;2(1):9-18.
- Голик В. И., Буй Х. Н., Масленников С. А., Анищенко В. И. Использование свойств дискретных пород для оптимизации процессов погашения выработанного пространства. Горные науки и технологии. 2019;4(3):213-219.
- DOI: 10.17073/2500-0632-2019-3-213-219
- Гавришев С. Е., Бурмистров К. В., Осинцев Н. А. Концепция устойчивого функционирования и развития горнотехнических систем в переходные периоды. Известия Тульского государственного университета. Науки о Земле. 2019;(3):145-160.
- Голик В. И., Разоренов Ю. И., Страданченко С. Г., Хашева З. М. Принципы и экономическая эффективность комбинирования технологий добычи руд. Известия Томского политехнического университета. Инжиниринг георесурсов. 2015;326(7):6-14.
- Golik V. I., Doolin A. N., Komissarova M. A., Doolin R. A. Evaluating the effectiveness of utilization of mining waste. International Business Management. 2015;9(6):1119-1123.
- Дзапаров В. Х. Угроза безопасности жизнедеятельности региона РСО-Алания. Вестник Магнитогорского государственного технического университета им. Г.И. Носова. 2009;3(27):75-76.
- Ляшенко В. И. Природоохранные технологии освоения сложноструктурных месторождений полезных ископаемых. Маркшейдерский вестник. 2015;(1):10-15.
- Oxley A., Smith M. E., Caceres O. Why heap leach nickel laterites? Minerals Engeneering. 2016;88:53-60
- Sinclair L., Thompson J. In situ leaching of copper: Challenges and future pro spects. Hydrometallurgy. 2015;157:306-324.
- Ляшенко В. И., Хоменко О. Е., Голик В. И. Развитие природоохранных и ресурсосберегающих технологий подземной добычи руд в энергонарушенных массивах. Горные науки и технологии. 2020;5(2):104-118.
- DOI: 10.17073/2500-0632-2020-2-104-118
- Мельников И. Т., Гавришев С. Е., Михайлов А. Г., Пыталев И. А., Шевцов Н. С., Васильев К. П. Новый подход для оценки эффективности работы горно-обогатительных комбинатов. Горная промышленность. 2012;5(105):60-66.
- Разоренов Ю. И., Белодедов А. А., Шмаленюк С. А. Определение потерь и разубоживания при разработке месторождений полезных ископаемых. Горный информационно-аналитический бюллетень (научно-технический журнал). 2009;(9):47-50.
- Дмитрак Ю. В., Вержанский А. П. Тенденции применения оборудования для тонкого измельчения горных пород. Горный информационно-аналитический бюллетень. 2000;(6):184-188.
- Комащенко В. И. Применение современных способов инициирования и конструкций скважинных зарядов для повышения качества дробления массивов горных пород. Устойчивое развитие горных территорий. 2015;2(24):12-17.
- Ляшенко В. И., Стусь В. П. Охрана окружающей среды в зоне влияния уранового производства. Безопасность жизнедеятельности. 2015;3:37-44.
- Качурин Н. М., Стась Г. В., Корчагина Т. В., Змеев М. В. Геомеханические и аэрогазодинамические последствия подработки территорий горных отводов шахт Восточного Донбасса. Известия Тульского государственного университета. Науки о Земле. 2017;1:170-182.