К вопросу механизма модифицирования МДО-покрытий частицами нанопорошка CuO
Автор: Козлов А.В., Коломейченко А.В.
Журнал: Агротехника и энергообеспечение @agrotech-orel
Статья в выпуске: 1 (1), 2014 года.
Бесплатный доступ
В статье представлены результаты исследований по повышению износостойкости деталей машин за счет использования в них МДО-покрытий, модифицированных частицами нанопорошка оксида меди (СuO). Показан механизм внедрения частиц в поры МДО-покрытия. Представлена математическая модель, которая позволяет определить электрический ток, проходящий через систему металл - оксид - раствор-носитель - электролит, посредством которого осуществляется включение частиц нанопорошка CuO в упрочненный слой сформированный на детали из алюминиевого сплава.
Модифицирование, мдо-покрытие, частица, нанопорошок, модель, ток пробоя, сопротивление, вторичная обработка
Короткий адрес: https://sciup.org/14769981
IDR: 14769981
Текст научной статьи К вопросу механизма модифицирования МДО-покрытий частицами нанопорошка CuO
Наиболее важным моментом в образовании микродуговых разрядов (МДР) при микродуговом оксидировании (МДО) являются процессы возникновения парогазовых пузырьков (ПГП) и зажигания в них микроразрядов. В результате теплового воздействия МДР окисная пленка локально нагревается до температуры выше 2000°С, что приводит к оплавлению стенок поровых разрядных каналов и появлению в МДО-покрытии кристаллических модификаций оксидов алюминия, в том числе и высокотемпературных, за счет дегидратации оксогидроксидов и полиморфных превращений. На основании анализа литературных данных и собственных проведенных исследований нами было сделано предположение, что включение частиц CuO в состав МДО-покрытий, при дуговом электрофорезе, может обеспечить существенное повышение антифрикционных свойств подвижных соединений деталей машин, содержащих покрытия данного типа в условиях граничной смазки или трения без смазочного материала.
В отличие от общепринятого дугового электрофореза, где включение частиц порошков металлов в МДО-покрытие происходит прямо из электролита, в котором и происходит МДО, этот процесс предлагается осуществлять в две стадии. В начале МДО, а затем дуговой электрофорез с увеличенной концентрацией частиц CuO на поверхности уже сформированного оксидокерамического покрытия. Первая стадия (первичная обработка) предусматривает полное формирование МДО-покрытия на алюминиевом сплаве. Затем удаление рыхлого, технологического слоя. Нанесение и закрепление частиц CuO на поверхность МДО-покрытия. Далее идет вторая стадия, которая предусматривает дуговой электрофорез (вторичная обработка), для расплавления и закрепления меди в оксидокерамическом покрытии. Достоинством такого решения будет включение частиц антифрикционного металла только в поры и поверхностный слой МДО-покрытия. Это позволит существенно снизить расход применяемого порошка и повысить антифрикционные свойства внешнего упрочненного слоя. Данное обстоятельство связано с тем, что в трении двух твердых тел участвует только внешняя поверхность МДО-покрытия. Поэтому улучшение антифрикционных свойств по всей толщине упрочненного слоя не требуется.
Проанализировав имеющиеся на Российском рынке порошковые материалы, их свойства и стоимость, мы пришли к выводу, что для повышения антифрикционных свойств МДО-покрытий наиболее целесообразно использовать порошки CuO. Такой порошок часто применяют в материаловедении, в качестве добавок к электродным материалам для изготовления высокопроводящих кислородных электродов с высокой электрохимической активностью, что по нашему мнению будет благоприятно сказываться на включениии порошка в состав МДО-покрытия при воздействии на него ИР. Помимо этого, данный выбор порошка основан на анализе литературных источников. В частности С.Г. Красиков описывает преобразование пары трения «сталь-бронза» в пару трения «медь – медь» [1]. Поэтому, минуя медьсодержащие порошки, мы остановили свой выбор на порошке из чистой меди.
В связи с тем, что размеры пор в МДО-покрытии колеблются в интервале от 2 до 6 мкм [2], что для лучшей заполняемости (по глубине упрочненного слоя) при дуговом электрофорезе потребуется порошок фракцией менее 1 мкм, который является наноразмерным. Порошок должен находиться в составе раствора, который при нанесении на сформированное при первичной обработке МДО-покрытие, позволит зафиксировать его частицы на поверхности упрочненного слоя до начала вторичной обработки. Для приготовления основы раствора-носителя мы решили выбрать дистиллированную воду и один из компонентов электролита, а именно Na2SiO3, который применяется в промышленности в качестве компонента клеевых растворов. Выбор Na2SiO3 для основы раствора-носителя основан на том, что он является компонентом электролита и не сможет повлиять на изменение химического состава МДО-покрытия при вторичной обработке.
В качестве способа для включения частиц нанопорошка CuO в состав МДО-покрытия, как указывалось выше, будем использовать дуговой электрофорез. Кроме этого ранее указывалось, что МДР при МДО проходит сквозь парогазовый пузырек, который образуется в порах упрочненного слоя. После нанесения раствора-носителя на поверхность МДО-покрытия верхняя часть пор в нем окажется занятой частицами CuO, а сама пора внутри будет полой. В этом случае при вторичной обработке воздействие ИР будет проходить по пути наименьшего сопротивления, т.е. через поры в упрочненном слое. В это же время он окажет воздействие на нанопорошок CuO, который будет находиться в зоне единичной поры. Под действием ИР нанопорошок CuO расплавится и займет полость поры. Таким образом и произойдет модифицирование его внешнего слоя, медь (Cu) будет включена в состав упрочненного слоя. На рисунке 1 представлен предлагаемый нами механизм модифицирования МДО-покрытия частицами нанопорошка CuO.
В работе В.В. Пронина [3] рассмотрены теоретические представления о кинетической закономерности роста МДО-покрытия на алюминиевом сплаве, и представлена динамика процесса зарождения МДР в элементарной ячейке. В этой модели учтена форма ЭДС источника технологического тока. Однако, в нашем случае МДО-покрытие уже сформировано, поэтому ИР будет в основном проходить через поры МДО-покрытия. Кроме этого при вторичной обработке появляется дополнительное сопротивление в виде раствора-носителя СuO.
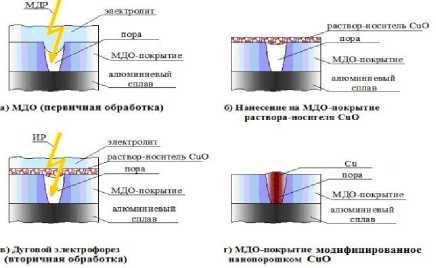
Рисунок 1 - Механизм модифицирования МДО-покрытия
частицами нанопоршка CuO
В связи с этим модель, представленная в работе [3] получила в нашей работе дальнейшее развитие применительно к вторичной обработке (дуговому электрофорезу) МДО-покрытия. При рассмотрении начальных условий задачи, также как и в работе [3] был сделан ряд допущений. В расчетах не учитывался ионный ток в системе и сопротивление электролита в порах МДО-покрытия. В нашем случае задача была сведена к определению изменения электронного тока, проходящего через систему металл - оксид -раствор-носитель CuO - электролит (МОРЭ), от напряжения на ячейке.
После теоретических исследований уравнение позволяющее определять общий ток, проходящий через систему МОРЭ, приняло следующий окончательный вид:
, А ■ to- cos ( to t ) А ■ to ■ sin ( to t )
I = e" mt +--- л +--- /2 (2/ +
| to | Ra ■ I to + m2)
R э -I — + m I
+ (( R e + R s + R p ) ■ С ) - 1 ■
/ m +
А ■ sin ( to t )

А ■ to- cos ( to t ) R э - ( to 2 + m 2 )
где Rб - сопротивление барьерного слоя на дне сквозной поры МДО-покрытия;
С - емкость МДО-покрытия;
Rэ - сопротивление электролита;
R р - сопротивление раствора-носителя нанопорошка CuO;
R в - сопротивления воздуха в порах;
А – текущее амплитудное напряжение;
to - угловая частота;
коэффициент _1 1 .
( R , + R6 + Rp ) С R = ■ С
Уравнение (1) представляет собой модель, которая показывает изменение тока пробоя при вторичной обработке МДО-покрытия и учитывает электрофизические параметры сквозной пористости, раствора-носителя CuO и электродвижущей силы источника питания. Полученное уравнение четко показывает обратно пропорциональную зависимость тока от напряженности электрического поля в МДО-покрытии, сопротивления раствора-носителя CuO, электролита, МДО-покрытия и воздуха в его порах. Оно объясняет потребность в большей силе тока в момент начала вторичной обработки МДО-покрытия с нанесенным на него раствором-носителем CuO, чем при МДО. Полученная модель также позволяет контролировать продолжительность вторичной обработки по стабилизации электрического тока.
Экспериментальные исследования показали, что модифицирование частицами нанопорошка CuO МДО-покрытия снижает коэффициент трения в подвижном соединении рабочих поверхностей деталей в 1,5-2 раза, а износостойкость такого подвижного соединения повышается в 2 раза.
Список литературы К вопросу механизма модифицирования МДО-покрытий частицами нанопорошка CuO
- Коломейченко А.В. Повышение износостойкости деталей из алюминиевых сплавов специализированными покрытиями/А.В. Коломейченко, А.В. Козлов//Строительные и дорожные машины. -2013. -№ 1. -С. 20-26.
- Коломейченко А.В. Технологии повышения долговечности деталей машин восстановлением и упрочнением рабочих поверхностей комбинированными методами с применением микродугового оксидирования: монография/А.В. Коломейченко. -Орел: Изд-во Орел ГАУ, 2013. -230 с.
- Пронин, В.В. Разработка технологии формирования изоляционных покрытий на деталях из алюминиевых сплавов методом микродугового оксидирования : автореф. дис. … канд. техн. наук/В.В. Пронин. -Орёл., 2006. -19 с.