К вопросу оценки условий эксплуатации и прогнозирования остаточного ресурса двигателей внутреннего сгорания
Автор: Головин Сергей Иванович, Ревякин Максим Михайлович, Жосан Артур Александрович
Журнал: Агротехника и энергообеспечение @agrotech-orel
Рубрика: Технологии и средства технического обслуживания в сельском хозяйстве
Статья в выпуске: 3 (24), 2019 года.
Бесплатный доступ
В настоящее время, в связи с тенденциями развития техники, остро стоит вопрос о полной реализации назначенного ресурса, т.е. заложенного заводом изготовителем. Для решения этой задачи необходим постоянный контроль за процессами, происходящими в двигателе, а также управление этими процессами на протяжении всего периода эксплуатации двигателя. В качестве информирующего индикатора используется параметр железо как продукт изнашивания в системе смазки. Выделен наиболее перспективный способ оценки условий эксплуатации и прогнозирования остаточного ресурса, заключающийся в сравнении различных скоростей изнашивания комплектующих элементов объекта исследования. Выявлен основной аспект в процессе контроля параметров двигателя: учет данных о массовой доле железа в масле, об общей наработке и наработке до последней замены смазочного материала. Представлена блок-схема алгоритма диагностики и прогнозирования остаточного ресурса двигателя, а также алгоритм функционирования программного продукта по вычислению остаточного ресурса двигателя при различных условиях эксплуатации. Предложенный способ оценки условий эксплуатации и прогнозирования остаточного ресурса двигателей является оптимальным так как позволяет диагностировать объекты различных марок и достаточно вариативен. Представлена блочная (позиционная) модель функционирования программного продукта в сочетании с применением электронных вычислительных средств, включающая в себя информационный блок данных о наработке двигателя до последней замены масла, времени работы масла, марке двигателя и мобильного энергетического средства, заводском номере, заводском номере двигателя, хозяйственном номере, месте работы объекта, данные об операторе и дате отбора пробы, а также вычислительный блок.
Двигатель, остаточный ресурс, прогнозирование, информатор, железо в системе смазки, алгоритм работы программного продукта, изнашивание
Короткий адрес: https://sciup.org/147229211
IDR: 147229211
Текст научной статьи К вопросу оценки условий эксплуатации и прогнозирования остаточного ресурса двигателей внутреннего сгорания
Введение. Поддержание оптимальных условий эксплуатации позволяет максимально использовать ресурс, заложенный как в детали двигателя, так и в двигатель в целом [3]. Возникает вопрос, как осуществить решение данной задачи. Основные трудности в решении данной задачи состоят в том, что необходим постоянный контроль за условиями эксплуатации, так как лишь в этом случае будет достигнут ощутимый результат, а также какой информатор следует выбрать в качестве индикатора.
Основная часть. Наиболее приемлемой, с нашей точки зрения, является информация о содержании железа как продукта изнашивания деталей двигателя в системе смазки [2,4, 5]. Выбор данного информатора обусловлен его высокой информативностью: его значение в течении времени работы масла изменяется на два порядка. К тому же, что очень важно, в базовых маслах и присадках к ним железо не должно содержаться, а если эти соединения не являются активными по отношению к маслам, из которых изготовлены детали двигателя, следовательно, железо может поступать в масло только в результате процессов трения при работе двигателя.
Один из перспективных способов оценки условий эксплуатации и прогнозирования остаточного ресурса двигателей может заключаться в сравнении эксплуатационной и ресурсной скоростей изнашивания деталей исследуемого объекта [1]. Измеряются скорости массой железа поступающей в систему смазки за единицу времени работы двигателя. По полученному значению производится прогнозирование остаточного ресурса с учетом сохранения существующих условий эксплуатации или приведения их к значению, обеспечивающему ресурс заявленный заводом-изготовителем. С целью повышения надежности и точности средние скорости поступления железа в систему смазки необходимо определять с учетом того, что продукты износа деталей, и, в том числе железо, находятся в масле, РМЦ и удаляются с угоревшим маслом. Контролировать все эти параметры достаточно сложно, поэтому целесообразно использовать информацию только о массовой доле железа в масле, общей наработке двигателя и наработке до последней замены масла. Для этого необходим соответствующий программный продукт, при помощи которого по уставленным закономерностям работы системы смазки, математическим моделям износа деталей двигателя и его техническим данным будет осуществляться контроль за условиями эксплуатации.
Предлагаемый способ оценки условий эксплуатации и прогнозирования остаточного ресурса двигателя позволяет осуществлять контроль условий эксплуатации в соответствии с требованиями, обеспечивающими заявленный ресурс, не требует проведения предварительных дорогостоящих испытаний на предмет определения параметров необходимых показателей [6, 7], позволяет диагностировать двигатели любых марок, а также управлять условиями эксплуатации и прогнозировать остаточный ресурс с учетом степени износа деталей до момента отбора пробы в двух вариантах:
– при условии сохранения в дальнейшем определенного коэффициента условий эксплуатации;
– при условии доведения его, в результате соответствующих мероприятий, до значения, при котором обеспечивается ресурс двигателя, т .е. равном единице.
В первом случае прогнозируемый остаточный ресурс определяется по формуле
= T - ^ X К , (1)
T O
KУЭ где Т 1 – наработка на момент диагностирования, мото-ч;
Т – межремонтная наработка двигателя, мото-ч;
К УЭ - коэффициент условий эксплуатации.
во втором случае
To = T - T 1 X K y3 .
Коэффициент условий эксплуатации вычисляем по формуле
K УЭ
J X ,
J y
где J X - фактическая скорость изнашивания мг/мото-ч;
Jy - ресурсная скорость изнашивания мг/мото-ч.
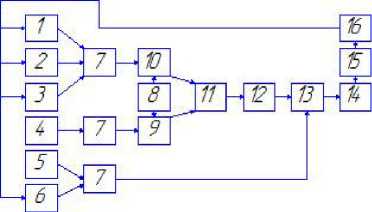
Рисунок 1 – Блок-схема алгоритма проведения диагностики и
прогнозирования остаточного ресурса двигателя
Таким образом алгоритм диагностики и прогнозирования производится по блок-схеме, представленной на рисунке 1.
В начале отбирается проба масла из поддона картера двигателя и определ яется содержание в нем железа (блок 1 на рисунке 1).
♦ ~
Вычисление массы Fe с 1 цилирзо до пределноеа износа
*
Вы-сслепое массы .Be со tax цилиедрзб
А
Вычхзление массы Fe с 1 иопуной мейси до предел, нога износа
* ~
Вычисление массы fie со tax шту+ых шеа
♦
Вычглеуе массы Fe с / короной шейки до пае^ънзго износа
з .
Вычисление .массы Fe со tax кцзечых ива
*
Вычзс/Ение массы Fe с прочих двтагей ВЕигателя
t
В<уная расчетная масса Fe аз Всех деталей'
■ 3 ■
Вдод дзных .по азд^зхаав Fe 5 псоде .масла одьата
1 Z
ВычзслечЕ массы Fe 6 мос/е на маменп дипгнасттбоия
Вычзсленое зтакжзв ^езьнагз параметра
t
Вычвлензе массы железа 5 отложаит маслаби/ътра за Время с момента замены .масла

Рисунок 2 – Алгоритм работы программного продукта (начало)
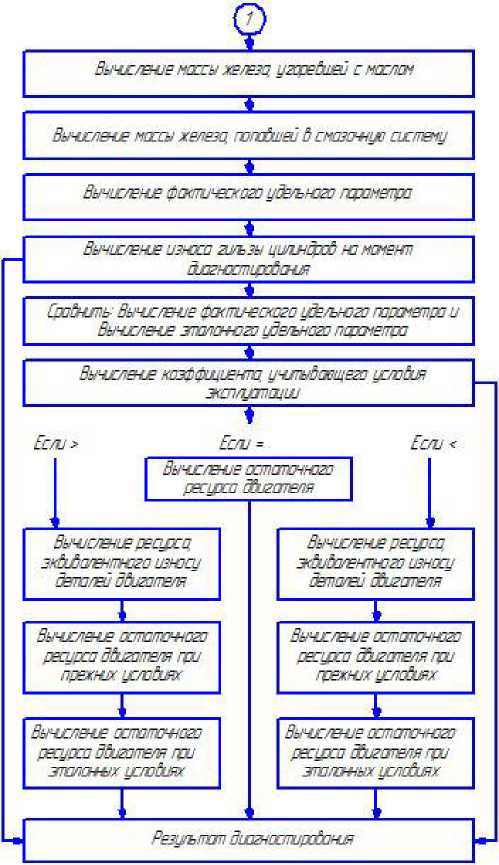
Рисунок 2 – Алгоритм работы программного продукта (окончание)
Затем осуществляется сбор информаций о наработке двигателя до последней замены масла, время работы масла, марка двигателя (блоки 2, 3, 4), а также информация о марке мобильного
энергетического средства, его заводском номере, заводском номере
двигателя, хозяйственном номере (при наличии), месте работы объекта, данные об операторе и дате отбора пробы (блоки 5 и 6).
Вся вышеуказанная информация вводится в персональный компьютер через интерфейс. Далее программный продукт функционирует по следующей схеме: в блоке 7 аккумулируется информация позиций (блоков) 1 – 6 и, используя информацию блока 8 (база данных), по программному продукту вычисляется ресурсная и эксплуатационная скорости изнашивания деталей двигателя (блок 9 и 10). В блоке 11 производится оценка условий эксплуатации двигателя, а в позиции 12 – поиск решений и вычисляется остаточный ресурс двигателя, согласно алгоритму, представленному на рисунке 2.
После этого в позициях 13 и 14 происходит сохранение в памяти персонального компьютера результатов диагностирования и, при необходимости вывод их печать.
В случае, если условия эксплуатации двигателя не соответствуют техническим требованиям, по желанию потребителя специалистами устраняются причины приведшие к такому результату (позиции 15 и 16) и диагностика повторяется.
Выводы. Таким образом поэтапное функционирование программного продукта с использованием в качестве диагностического информатора содержание железа как продукта изнашивания в системе смазки двигателей характеризует предлагаемый способ оценки условий эксплуатации и прогнозирования остаточного ресурса двигателя как наиболее простой и не затратный с экономической точки зрения.
Список литературы К вопросу оценки условий эксплуатации и прогнозирования остаточного ресурса двигателей внутреннего сгорания
- Головин, С.И. Увеличение ресурса дизелей / А.А. Жосан // Тракторы и сельхозмашины. -2006. № 12. С. 35.
- Головин С.И. Реализации назначенного ресурса дизеля / С.И. Головин // В сборнике: Особенности технического оснащения современного сельскохозяйственного производства. / Сборник материалов к Всероссийской научно-практической конференции молодых ученых. - Орел, 2012. С. 87-91.
- Жосан А.А. Система РИКОС как способ обеспечения и поддержания целевой динамичности мобильных энергетических средств / А.А. Жосан, С.И. Головин, М.М. Ревякин // В сборнике: Состояние и перспективы энерго- и ресурсосберегающих технологий в АПК Материалы Международной научно-практической конференции. - Орел, 2009. С. 52-57.
- Жосан, А.А. Обеспечение ресурса двигателей тракторов агропромышленного комплекса путем контроля условий эксплуатации по химмотологическому параметру моторного масла /С.И. Головин // Монография / Орел, 2013.
- Ревякин М.М. Реализация назначенного ресурса двигателя путем контроля условий эксплуатации по параметру удельного химмотологического показателя моторного масла / М.М. Ревякин // Агротехника и энергообеспечение. - Орел, 2017. №2 (15). С. 62 - 67.
- Жосан А. А. Современный подход и реалии диагностирования машино-тракторных агрегатов/ А.А. Жосан, М.М. Ревякин //ЭНЕРГО- И РЕСУРСОСБЕРЕЖЕНИЕ XXI ВЕК Сборник материалов VI-ой Международной научно-практической интернет-конференции.- 2008. - С. 141-142
- Фомичёв Е.В. Диагностирование как способ получения информации о техническом состоянии сельскохозяйственных машин и повышения их надежности / Е.В. Фомичёв, М.М. Ревякин // Агротехника и энергообеспечение. - Орел, 2014. № 1 (1). С. 356-361.