К выбору марки резины при сервисном обслуживании амортизирующих устройств
Автор: Мосур В.Г., Шарков О.В.
Журнал: Технико-технологические проблемы сервиса @ttps
Рубрика: Диагностика и ремонт
Статья в выпуске: 1 (67), 2024 года.
Бесплатный доступ
Выполнен сравнительный анализ эксплуатационных свойств резины различных марок для изготовления демпфирующих элементов механических амортизирующих устройств. В качестве критерия сравнения принята величина ресурса наработки до начала разрушения материала. Показано, что наибольшим ресурсом при циклическом наружении обладают упругие элементы из резины марки 51-1562 на основе изопренового каучука.
Сервисное обслуживание, демпфирующий элемент, вибрация, разрушение, ресурс
Короткий адрес: https://sciup.org/148328330
IDR: 148328330
Текст научной статьи К выбору марки резины при сервисном обслуживании амортизирующих устройств
Снижение вибрационных и ударных нагрузок при работе различного технологического оборудования – актуальная проблема современной техники [1–5]. Одним из путей уменьшения вибрационных нагрузок является применение амортизатор различных конструктивных схем. По принципу действия амортизаторы можно разделить на механические (сухого трения), гидравлические (вязкого трения), электромагнитные, комбинированные и др. Механические амортизаторы [6–11] имеют достаточно простую конструкцию, в которой для гашения колебаний применяют металлические (пружины, рессоры) или неметаллические (резина, полиуретан, полиизобутилен) упругие элементы.
При изготовлении неметаллических демпфирующих элементов часто в качестве материала используют резину [10–14]. Резина является продуктом вулканизации каучука, который обладает небольшой себестоимостью, что и обусловило его частое использование в различных изделиях. В качестве примеров использования резиновых демпфирующих элементов можно назвать виброизоляторы вентиляторов типа ВР-200 [15], амортизаторы для корабельных систем и оборудования типа АКСС [16]. Резиновые демпфирующие элементы обладают рядом достоинств: простотой конструкции и технологии изготовления; высокой удельной энергоёмкостью; способностью к значительным деформациям; нечувствительностью к воздействию пыли и воды. Среди недостатков таких элементов можно отметить следующие: различная величина статической и динамической жёсткости; возникновение остаточных деформаций при действии циклической нагрузки; отклонение свойств резины одной марки от номинального значения; чувствительность к температуре эксплуатации.
При проектировании резиновых демпфирующих элементов предпочтение следует отдавать литьевым маркам, так как они имеют низкий процент остаточной деформации при сжатии и сохраняют свойства при низких и высоких температурах в сравнении с вальцуемыми и термопластичными полиуретанами. В процессе эксплуатации и сервисного обслуживания амортизаторов возникает задача замены отработавших свой ресурс демпфирующих элементов. Выполним анализ возможности применения некоторых марок резин, при изготовлении демпфирующих элементов. К резинам (табл. 1), обладающим хорошей долговечностью в условиях циклического деформирования и диссипативного разогрева можно отнести марки на основе: изопренового каучука (51–1562); уретанового каучука (СКУ–8); бутадиен-нитроль-ного каучука (ИРП1–1401).
Таблица 1 - Механические характеристики резины
Опыт применения резиновых демпфирующих элементов в различных амортизирующих устройствах показывает, что резина, как материал, достаточно хорошо противостоит разрушающему воздействию различных повреждающих факторов (масла, технических жидкостей, озона, солнечной радиации и др.). Обычно, повреждение резиновых элементов при воздействии данных, а также механических факторов сосредотачиваются в поверхностном слое. Несмотря на это, основным фактором, влияющим на ресурс резиновых демпфирующих элементов, является диссипативный разогрев, величина которого влияет на окислительные процессы в резине и как следствие на скорость старения.
Точная количественная оценка эксплуатационных характеристик (прочности, несущей способности, долговечности и др.) резиновых демпфирующих элементов представляет собой сложную задачу, т.к. механические характеристики эластомеров могут изменяться в определенном диапазоне. Например, на величину модуля упругости резины оказывают влияние твердость, степень вулканизации, величина деформации и др. факторы. Причем особенностью технологического процесса изготовления резины является отклонение её физических и механических свойств от номинальных значений, даже для элементов одной партии, которые могут превышать 10…15 %.
Закон Гука, по которому модуль упругости Е постоянная величина, а напряжение т пропорционально относительной деформации е для резины справедлив только для ограниченного диапазона деформаций. Согласно ГОСТ ISO 7743–2013 «Резина и термопласты. Определение упругопрочностных свойств при сжатии» зависимость т = еЕ применима при деформации до 5 %, для больших величин деформации от 5 до 30 % необходимо использовать модифицированную зависимость т = еЕ/ (1 - е ). При этом деформации при работе резиновых демпфирующих элементов могут достигать и больших значений. Отношение динамического модуля упругости к статическому может меняться в диапазоне от 1,18 до 2,0 и более [17].
Предел прочности при растяжении и относительное удлинение, которые часто приводятся в справочниках, на практике имеют ограниченное применение, т.к. эти величины достигаются нии изделия.
Обычно для каждого конкретного случая функционирования демпфирующих элементов используют свои приближенные зависимости. Так для резиновых демпфирующих элементов упругих муфт [18] допустимое напряжение принимают: [т] = (0,12...0,15)Е (муфты с торобразной оболоч кой); [т] = (0,15...0,20)Е (муфты с упругим диском).
В процессе эксплуатации резиновые демпфирующие элементы подвергаются деформациям сжатия, изгиба, кручения, сдвига и нескольким видам деформации одновременно. В большинстве случаев демпфирующие элементы амортизаторов работают в условиях циклического сжатия.
В настоящее время существуют различные подходы к оценке работы резиновых элементов при циклическом нагружении [18–25].
В качестве сравнения эксплуатационных свойств демпфирующих элементов примем ресурс работы до разрушения. Воспользуемся зависимостью для определения ресурса работы резинового элемента, с учетом развивающихся в материале повреждений [23]
t = т C exp
U 0 - YT
RT
где т — константа материала резина, тй =1*10-13 с.; C - коэффициент повреждаемости материала; Uo - энергия активации процесса разрушения материала; у - структурно-чувствительный коэффициент; т - напряжение; R - газовая постоянная, R =8,32*10 3 Дж/(моль*К); T - температура диссипативного разогрева.
Коэффициент, учитывающий повреждаемость материала вследствие образования микротрещин, определяется как [23]
C = ln--- А р ^ ---,
Ар„ - АРкр где Ар„ - концентрация перенапряжённых связей в материале, которые могут разрушиться под действием тепловых флуктуаций; Ар^ - критическая концентрация повреждений в объёме резины.
Коэффициент C при эксплуатации резиновых элементов с температурой диссипативного разогрева до 323 К (50 ºС) можно принять равным 3,5, с температурой больше 323 К - 4,5 [23].
Структурно-чувствительный коэффициент характеризует прочностные свойства упругого материала, он является функцией напряжения и температуры диссипативного разогрева y = f (^, T) • Она определяется экспериментально или выбирается из справочников. Например, для резины марки 51–1562 [23]
Y = 103,9 - 8,3 ^ - 0,23 T .
На рис. 1 приведена гистограмма сравнительной оценки теоретического ресурса резины различных марок, выполненного по формуле 1.
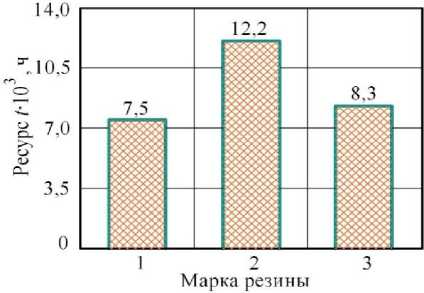
Рисунок 1 – Ресурс упругих элементов из резины марок: 1 – ИРП-14010; 2 – 51–1562; 3 – СКУ–8
Как видно из полученных результатов ресурс рассматриваемых марок резины изменяется в диапазоне от 7,5 до 12,2 тыс. ч. Наибольшим ресурсом обладает элементы, выполненные из резины марки 51–1562, ресурс элементов из резины марок СКУ–8 и ИРП-14010 соответственно меньше в 1,46 и 1,62 раза.
Согласно данным источника [23] для инженерной практики достаточно ресурса 6…12 тыс. ч., причем его величина зависит от условий эксплуатации и может быть выше. Например [23], для резины марки 51–1562 при циклическом нагружении при сдвиге с частотой 70 с-1 и температуре диссипативного разогрева 52…56 ºС наработка до отказа может быть больше 30 тыс. ч.
Список литературы К выбору марки резины при сервисном обслуживании амортизирующих устройств
- Куклин М.В. Снижение шума и вибрации в системах судовой гидравлики // Судостроение. 2019. № 5 (846). С. 34–35.
- Ломакин В.О., Михеев К.Г., Веселов А.А., Фоменко В.Д. Исследование возможности моделирования вибраций корпуса насоса из-за воздействия нестационарных гидродинамических сил // Известия высших учебных заведений. Машиностроение. 2022. № 12 (753). С. 107–115. doi: 10.18698/0536-1044-2022-12-107-115.
- Губарев П.В., Больших И.В., Шабаев В.В. Анализ существующих диагностических комплексов для контроля уровня вибрации узлов локомотивов // Сборка в машиностроении, приборостроении. 2020. № 7. С. 318–320.
- Fayziev S.K., Haydarova N.M. Methods of reducing the vibration and noise level in sewing machines // Modern innovations, systems and technologies. 2022. Vol. 2. No 2. P. 428–439. doi: 10.47813/2782-2818-2022-2-2-0428-0439.
- Ghazali M.H.M., Rahiman W. Vibration analysis for machine monitoring and diagnosis: A Systematic review // Shock and vibration. 2021. 9469318. https://doi.org/10.1155/2021/9469318.
- Курзина Е.Г., Колмаков А.Г., Филиппов В.Н., Семак А.В., Курзина А.М. Демпфирующие композиты из материалов с различающимися упруго-гистерезисными свойствами для сэндвич-амортизаторов железнодорожного транспорта // Материаловедение. 2020. № 1. С. 25–32.
- Алексеев А.Е., Думанский И.О., Прохоров А.В. Пластинчатые амортизаторы-демпферы в натяжных устройствах ленточнопильных станков // Известия высших учебных заведений. Лесной журнал. 2021. № 5 (383). С. 142–149. doi: 10.37482/0536-1036-2021-5-142-149.
- Белодедова А.А. Анализ применения амортизаторов для защиты от вибрации // Природные и техногенные риски (физико-математические и прикладные аспекты). 2023. № 2 (45). С. 67–73.
- Величкович А.С. Некоторые конструктивные особенности оболочечных пружин для буровых амортизаторов // Химическое и нефтегазовое машиностроение. 2007. № 8. С. 26–28.
- Danilin A.N., Kurbatov A.S., Zhavoronok S.I. Simulation of a multi-frequency stockbridge vibration damper oscilations with energy scattering hysteresis // International Journal for computational civil and structural engineering. 2020.Vol. 16. No 4. P. 29–37. doi: 10.22337/2587-9618-2020-16-4-29-37.
- Galluzzi R., Circosta S., Amati N., Tonoli A. Rotary regenerative shock absorbers for automotive suspensions // Mechatronics. 2021. Vol. 77. 102580. https://doi.org/10.1016/j.mechatronics.2021.102580.
- Смирнов О.В. Изготовление упругих демпфирующих элементов амортизаторов из металлической резины // Динамика систем, механизмов и машин. 2004. № 3. С. 79–82.
- Кеглин Б.Г. Выбор и исследование резин для вагонных амортизаторов удара // Каучук и резина. 1984. № 1. С. 32–33.
- Белкин А.Е., Хоминич Д.С. Расчет больших деформаций арочного амортизатора с учетом объемной сжимаемости резины // Вестник Московского государственного технического университета им. Н.Э. Баумана. Серия Машиностроение. 2012. № 2 (87). С. 3–11.
- Черныш А.А., Яковлев С.Н. Экспериментальное определение температуры нагрева полиуретанового амортизатора при динамическом нагружении // Вестник государственного университета морского и речного флота им. адмирала С.О. Макарова. 2019. Т. 11. № 5. С. 893–901. doi: 10.21821/2309-5180-2019-11-5-893-901.
- Long X-H., Ma Y-T., Yue R., Fan J. Experimental study on impact behaviors of rubber shock absorbers // Construction and building materials. 2018. Vol. 173. P. 718–729. https://doi.org/10.1016/j.conbuildmat.2018.04.077.
- Вентклиматстрой [Электронный ресурс] URL: https://pritochka.ru/products/vibroizolyatory-vr-201-vr-202-vr-203/ (дата обращения 15.10.2023).
- Научно-исследовательский институт резиновых покрытий и изделий [Электронный ресурс] URL: https://www.niirpi.com/produktsiya/amortizatory/amortizatory-korabelnye-so-strahovkoj-tipa-akss/ (дата обращения 20.10.2023).
- Потураев В.Н., Дырда В.И. Резиновые детали машин. Москва: Машиностроение, 1977. 214 с.
- Михайлов Ю.К., Иванов Б.С. Муфты с неметаллическими упругими элементами. Ленинград: Машиностроение, 1987. 145 с.
- Семенов В.К., Белкин А.Е. Математическая модель вязкоупругого поведения резины при циклическом нагружении // Известия высших учебных заведений. Машиностроение. 2014. № 2 (647). С. 46–51.
- Дудченко А.А., Башаров Е.А. Определение теплообразования в слоях резины слоистой балки типа торсион при циклическом нагружении // Труды МАИ. 2011. № 42. С. 1–15.
- Пелевин А.Г., Свистков А.Л., Адамов А.А., Bernd L., Heinrich G. Алгоритм поиска констант в модели механического поведения резины // Механика композиционных материалов и конструкций. 2010. Т. 16. № 3. С. 313–328.
- Прокопчук Н.Р., Кудинова Г.Д., Асловская О.А., Гугович С.А. Исследование влияния циклических деформаций и озона на долговечность резин // Труды Белорусского государственного технологического университета. Серия 3. Химия и технология неорганических веществ. 1996. № 4. С. 76–81.
- Дырда В.И. Резиновые элементы вибрационных машин. Киев: Наукова думка, 1980. 164 с.
- Park J., Kim Y.,Yoon J.W., So H., Lee J., Ko S. Finite element modeling and durability evaluation for rubber pad forming process // IOP Conference series: Materials science and engineering. 2019. Vol. 651. 012096. doi: 10.1088/1757-899X/651/1/012096.
- Moon S-I., Cho I-J., Woo C-S., Kim W-D. Study on determination of durability analysis process and fatigue damage parameter for rubber component // Journal of mechanical science and technology. 2011. Vol. 25. P. 1159–1165. https://doi.org/10.1007/s12206-011-0221-6.