Качество поверхности и долговечность подшипников после дробеструйных способов обработки
Автор: Дмитриев В.А.
Журнал: Известия Самарского научного центра Российской академии наук @izvestiya-ssc
Рубрика: Машиностроение и машиноведение
Статья в выпуске: 3 т.23, 2021 года.
Бесплатный доступ
Изложены и уточнены результаты исследований параметров качества поверхности и точности колец подшипников после финишной абразивной обработки дорожек качения (шлифования и суперфиниша) и после гидродробеструйного (ГДУ) упрочнения или упрочнения микрошариками (УМШ) с применением смазочно-охлаждающих жидкостей.
Качество, долговечность, подшипники, дробеструйная обработка
Короткий адрес: https://sciup.org/148322166
IDR: 148322166 | DOI: 10.37313/1990-5378-2021-23-3-24-28
Текст научной статьи Качество поверхности и долговечность подшипников после дробеструйных способов обработки
Повышение надежности и долговечности опор качения наряду с конструкторскими решениями может быть достигнуто путем рационального воздействия на поверхностные слои деталей технологическими методами. Использование традиционных способов ППД, основанных на вдавливании деформирующего инструмента в обрабатываемую поверхность (обкатывание шариком, роликом, алмазное выглаживание) нетехнологично при обработке маложестких тонкостенных кольцевых деталей со сложной конфигурацией поверхности, имеющих малоразмерные конструктивные элементы в виде галтелей и канавок. Поэтому получила распространение схема обработки, при которой отсутствует жесткая кинематическая связь деформирующего инструмента с обрабатываемой поверхностью. К подобной схеме относятся способы дробеструйной обработки с применением СОЖ на пневмодробеструйных и гидродробе-струйных установках [1, 2].
зависимости шероховатости поверхности от режимов обработки:
к.-с^цр^кТ. , мкм где p – рабочее давление на выходе сопла-эжектора, МПа; d – диаметр дроби, мм; t – время обработки участка поверхности, с; R a исх – параметр исходной шероховатости, мкм.
После логарифмирования получим линейное уравнение регрессии в виде:
У = lgRa = ^0 + РгХу + ^2^2 + №+М, где Y – истинное значение шероховатости поверхности в логарифмическом масштабе; X1, X2, X3, X4 – логарифмы соответственно p, d, t, Ra исх; Ро —Р* ~ искомые коэффициенты, оценка которых должна быть определена.
В результате эксперимента будет получена эмпирическая модель вида:
У = Ьо I Ь^ + Ь2Х2 + Ь3Х3 + Ь4Х4 , где У – оценка V = lgRa , b0 … b4 – оценки коэффициентов Ро — Ра .
В табл. 1 указаны основные уровни и интервалы варьирования контролируемых факторов режима при обработке дорожек качения колец радиальных роликоподшипников по плану ДФЭ 24-1.
Используя встроенные статистические функции пакета MS Excel, в табл.2 приведены результаты статистического оценивания линейного уравнения регрессии и его коэффициентов.
Из анализа уравнения следует, что в принятой локальной области определения факторов (см. табл.1) фактор Х3 – время обработки поверхности – оказался статистически незначим, что не получило отражения в ранее выполненной работе [3]; повышение рабочего давления и, следовательно, возрастание кинетической энергии деформирующего тела приводит к увеличению шероховатости обработанной поверхности вследствие увеличения глубины остаточного отпечатка; увеличение диаметра дроби способствует уменьшению
Таблица 1. Уровни факторов и интервалы их варьирования
Уровни факторов |
Обозначение |
p, МПа |
d, мм |
t, c |
R a исх |
Основной |
0 |
0,28 |
1,25 |
37,5 |
0,29 |
Интервал варьирования |
Axi |
0,12 |
1,15 |
22,5 |
0,21 |
Верхний |
1 |
0,4 |
2,4 |
60 |
0,5 |
Нижний |
-1 |
0,16 |
0,1 |
15 |
0,085 |
Таблица 2. Оценка параметров уравнения регрессии
Переходя от уравнения регрессии в кодированном виде к выражению с натуральными значениями переменных и потенцируя, получим искомую зависимость:
. „(o-M-nSstop) ^(O.B9+1.1 bFsp)
, мкм.
Я p2,02,^0,143
Приведенные на рис. 1 графики изменения параметра шероховатости поверхности дорожки качения колец показывают, что в пределах применяемых режимов упрочняющей обработки достигается уменьшение шероховатости лишь шлифованных поверхностей с Raисх=0,32…0,63 мкм. Минимальные значения параметра Ra составляют 0,17…0,19 мкм после УМШ и 0,11…0,13 мкм после ГДУ.
Результаты измерений (табл.3) высотных и шаговых параметров шероховатости Rmax, Rz, Ra, волнистости Нв, огранки Ног, отклонений от прямолинейности образующей дорожки качения h, а также значений параметров начального участка опорной кривой свидетельствуют о том, что чем ниже исходная шероховатость и интенсивнее режимы дробеструйной обработки, тем в большей степени возрастают высотные параметры шероховатости обработанной поверхности и погрешности формы в поперечном и продольном сечениях кольца.
При переходе от шлифования к суперфинишированию наряду с уменьшением высотных параметров шероховатости наблюдается снижение относительной опорной длины профиля поверхности дорожки качения на начальных уровнях сближения, особенно характерное для Ra ≤ 0,08 мкм. Известно, что такие поверхности с остроконечными вершинами выступов и низкой опорной способностью слабо сопротивляются контактным нагрузкам,
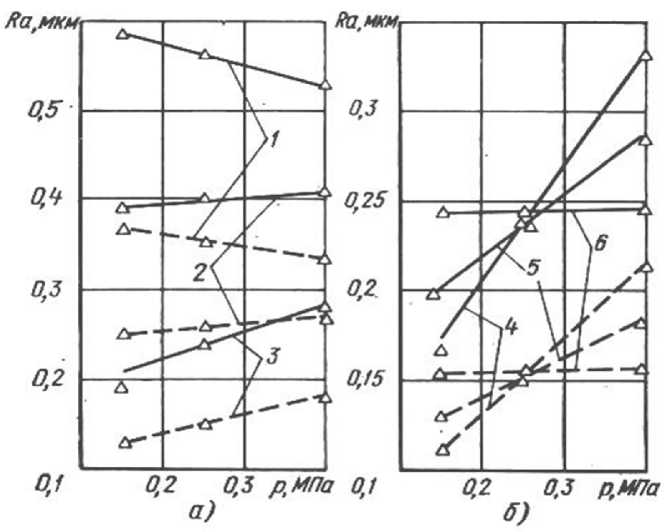
Рис. 1. Зависимости параметра Ra после УМШ (сплошные линии) и ГДУ (штриховые линии) от давления p на выходе сопла-эжектора:
а – при t = 30 c и Raисх= 0,5 мкм (1); Raисх= 0,25 мкм (2); Raисх= 0,08 мкм (3); б – при Raисх= 0,08 мкм и t = 60 c (4); t=30 с (5); t = 15 с (6)
плохо удерживают смазку и характеризуются повышенным износом приработки. Применение для этих поверхностей УМШ или ГДУ, несмотря на некоторое увеличение высотных параметров шероховатости, значительно уменьшает следы абразивной обработки, формирует характерный микрорельеф с наличием масляных карманов, удерживающих смазку, повышает опорную способность профиля и контактную жесткость поверхности качения, что способствует увеличению сопротивляемости различным видам износа и сохранению заданных зазоров в подшипнике.
На рис. 2 приведены результаты исследований микротвердости Н0,981 и остаточных напряжений ( о6 -цо5) в ,поверхностном слое дорожек качения внутренних колец подшипников 6-32205Д1 в зависимости от способов обработки и длительности стендовых испытаний при максимальных контактных напряжениях □zmQX = 2200 МПа. При исследовании остаточных напряжений использовался метод колец и полосок, а напряжения в кольцах подшипников рассчитывали по формулам, приведенным в работе [4], полученным на основе авторского свидетельства [5]; здесь ( Об - ^ – компо-
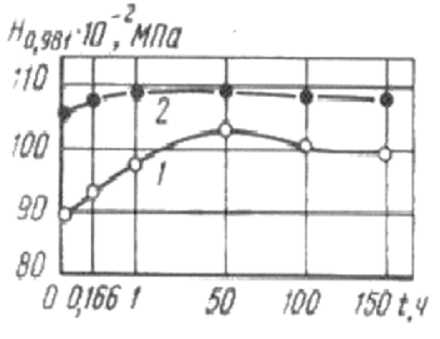
Рис. 2. Влияние способов обработки и продолжительности стендовых испытаний подшипника на изменение физико-механических характеристик:
1 – суперфиниширование; 2 – суперфиниширование + УМШ (р=0,2 МПа; t=40с);
3 – суперфиниширование + УМШ + 50 ч стендовых испытаний
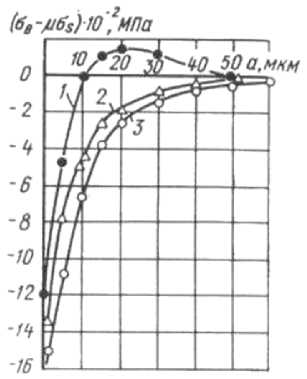
Таблица 3. Параметры шероховатости поверхности дорожки качения колец
Из приведенных данных следует, что величина и градиент остаточных напряжений и микротвердости, возникающих при упрочняющей обработке, не претерпевают существенных изменений в процессе многократных циклических нагружений при качении. Стабилизация напряжений и микротвердости происходит вследствие ограничения дополнительного наклепа во время испытаний в связи с интенсив- ной пластической деформацией при предварительном упрочнении. При этом достигается эффект «тренировки» рабочих поверхностей, приводящий к сокращению продолжительности приработки и уменьшению её негативного влияния на работу опоры.
Критерием эффективности выбранного способа и режима обработки являются результаты стендовых испытаний подшипников. Приведенные в табл.4 результаты сравнительных стендовых испытаний роликоподшипников типа 32118Р2 после суперфиниша и дополнительного упрочнения микрошариками показывают, что
Таблица 4. Результаты стендовых испытаний подшипников 32118Р2
ВЫВОДЫ
Выбор способа и режимов упрочняющей обработки маложестких кольцевых деталей следует осуществлять с учетом их конструктивных особенностей, технологических требований к параметрам микрогеометрии, точности размеров и формы.
Стабилизация качества поверхности дорожек качения колец, достигаемая дополнительной упрочняющей обработкой, обусловливает повышение и стабилизацию эксплуатационных характеристик опор качения.
Список литературы Качество поверхности и долговечность подшипников после дробеструйных способов обработки
- Кузнецов Н.Д., Цейтлин В.И. Эквивалентные испытания газотурбинных двигателей. М.: Машиностроение, 1976. 216 с.
- Петросов В.В. Гидродробеструйное упрочнение деталей и инструмента. М.: Машиностроение,1977.168 с.
- Кузнецов Н.Д., Волков В.И., Дмитриев В.А. Влияние дробеструйных способов обработки на качество поверхности и долговечность подшипников // Вестник машиностроения. - 1984. №3. - С. 14-18.
- Букатый С.А., Дмитриев В.А. Определение остаточных напряжений в кольцах подшипников качения после механической обработки // В кн.: Прогрессивные технологические методы повышения надежности и долговечности деталей машин и инструментов: Межвуз. сб., Куйбышев: КпТИ, 1980. С. 99-103.
- А. с. 996855 СССР, МКИ3 G 01 B 5/30. Способ определения остаточных напряжений в кольцевых деталях / С.А. Букатый, В.А. Дмитриев, Д.Д. Папшев (СССР). - № 3332266/25-28; эаявл. 19.08.81; опубл. 15.02.83, Бюл. № 6. - 4 с.