Кинематика методов хонингования
Автор: Ханов А.М., Муратов К.Р., Гашев Е.А., Пепелышев А.В.
Журнал: Известия Самарского научного центра Российской академии наук @izvestiya-ssc
Рубрика: Современные технологии в промышленности, строительстве и на транспорте
Статья в выпуске: 4-4 т.13, 2011 года.
Бесплатный доступ
Проведен анализ по кинематическому признаку существующих методов хонингования. Установлено, что чем разнообразнее и сложнее траектория движения режущих зерен, тем полнее используется режущая способность инструмента и тем лучше условия для получения требуемых параметров шероховатости и точности геометрической формы обрабатываемых поверхностей.
Методы хонингования, производительность, точность геометрической формы, шероховатость поверхности, кинематика станков
Короткий адрес: https://sciup.org/148200247
IDR: 148200247
Текст научной статьи Кинематика методов хонингования
Хонинговальные станки обеспечивают сложное рабочее движение путем комбинации вращательного, возвратно-поступательного и одного или двух колебательных движений. По кинематическому признаку методы хонингования делятся на две основные группы [4]: а) традиционный метод хонингования; б) вибрационные методы хонингования. При традиционном методе хонингования траектория рабочего движения инструмента образуется в результате вращения и возвратно-поступатель-ного движения вдоль оси обрабатываемой детали. Такая кинематика обуславливает типичную для традиционного хонингования сетку следов обработки в виде пересекающихся винтовых линий. Единственным параметром траектории, позволяющим в какой-то мере варьировать количественные и качественные показатели процесса, является угол скрещивания следов обработки 2α , зависящий от соотношения скоростей вращения VKP и скорости возвратно-поступательного движения Voc . Скорость резания V является геометрической суммой скоростей вращения и возвратно-поступательного движения инструмента
V
I—;-----. a = arctg---
-
V = V^ + vOc. VvKP
;
При повторных ходах возможно совпадение или смещение фаз положений брусков. Это зависит от размера брусков, их количества и от соотношения скоростей вращательного и возвратно-поступательного движений [5]. Поэтому при заданных условиях обработки определяется оптимальное значение Voc / VKP из условий обеспечения наименьшего относительного смещения фаз положений брусков и количества двойных ходов, необходимое для равномерного заполнения обрабатываемой поверхности следами резания. Это способствует снижению шероховатости и повышению точности геометрической формы.
При традиционной кинематике не полностью используется режущая способность брусков, так как наибольшее участие в резании принимают зерна, встречные направлению движения, а остальные – меньше, поскольку попадаю во впадины образованные предыдущими зернами. Для интенсификации процесса и более полного использования режущей способности инструмента при традиционном методе хонингования применяют схему обработки с периодическим реверсированием вращения [6]. На рис. 1 схематично изображено контактирование отдельного зерна с обрабатываемой поверхностью в трех различных фазах: а – начало работы зерна; б – притупившееся зерно; в – контактирование зерна при реверсе вращения. В результате более интенсивного самозатачивания брусков при увеличении частоты реверсирования, относительный износ брусков возрастает. Шероховатость поверхности изменяется незначительно.
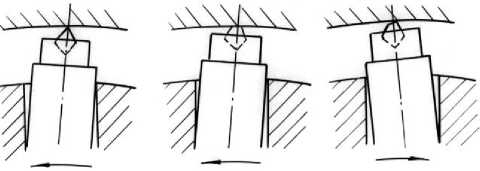
а) б) в)
Рис. 1. Схема контактирования режущего зерна при традиционном методе хонингования с периодическим реверсированием вращения
Вибрационное хонингование осуществляется путем наложения на основные движения дополнительных колебательных движений. Методы вибрационного хонингования могут быть классифицированы по характеру осциллирующего движения. Известны схемы вибрационного хонингования с осевой, круговой, радиальной и комбинированной осцилляцией. Наиболее изучен процесс вибрационного хонингования с осевой осцилляцией [3, 7]. По сравнению с традиционным хонингованием виброхонингование с осевой осцилляцией позволяет существенно увеличить производительность процесса в 1,5-2 раза [8] по мере увеличения частоты и амплитуды колебаний. Интенсивность износа брусков при этом также увеличивается, но в меньшей мере, чем съем металла. Положительным является также то, что при виброхонинговании съем металла носит незатухающий характер и со временем изменяется незначительно. Сравнительные результаты съема металла при хонинговании с различными видами осцилляций, осевой, радиальной и комбинированной (осевая с радиальной), показали целесообразность применения осевой осцилляции [3].
Для хонинговальных станков в большинстве случаев применяются нерезонансные механизмы осцилляции, как для осевых, так и для круговых колебаний [9]. Механизмы осцилляции с резонансными колебаниями, как правило, не допускают перестройки частоты и амплитуды колебаний и поэтому мало распространены. Нерезонансные механизмы выполняются обычно с регулируемыми параметрами и надежно работают в диапазоне частот 1-1000 Гц при амплитудах до 20 мм. При проектировании регулируемых механизмов с нерезонансными колебаниями следует исходить из оптимальной амплитудно-частотной характеристики, предельной по мощности и усилию колебаний. При этом необходимо учитывать, что при увеличении частоты мощность, расходуемая на резание, растет значительно медленнее, чем мощность колебаний, поэтому с повышением частоты к.п.д. механизма осцилляции уменьшается. Это связано с тем, что инерционные нагрузки, определяемые массой колеблющихся частей, в большей мере зависят от частоты колебаний и меньше от амплитуды. Поэтому, видимо, виброхонингование с осевой осцилляцией рекомендуется применять при обработке отверстий с диаметром до 50 мм [2].
Хонингование с осевой осцилляцией было реализовано на ранее выпускающихся вертикальных хонинговально-доводочных станках ОЗПС следующих моделей: 3820, 3821. Параметры колебаний: амплитуда 0-4 мм; частота 250-630 кол/мин. В настоящее время осевая осцилляция применяется на вертикальных и горизонтальных хонинговальных станках фирмы Sunnen products company [10], а также на станке модели «Хон-1», который разработан и выпускается Владимирским ВПКО «Техника». Станок предназначен для обработки отверстий диаметром от 6 до 50 мм, длинной 150-200 мм. Кинематическая схема станка представлена на рис. 2. На направляющих 4 станины смонтирована каретка 5 с приспособлением 6 , в которой закрепляется обрабатываемая деталь 7 . Каретка 5 шарнирно связана с коромыслом 9 , одно плечо которого шарнирно связано с приводом 11 возвратно-поступательного движения, а другое – шарниром 12 соединено с механизмом осцилляции 13 . Таким образом, каретке 5 и обрабатываемой детали 7 одновременно сообщаются осевые колебания и возвратнопоступательное движение относительно вращающегося от привода 2 инструмента 3 . Амплитуда и частота колебаний регулируются бесступенчато.
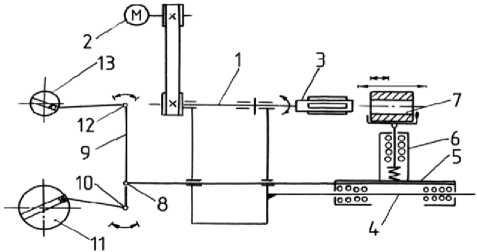
Рис. 2. Кинематическая схема хонинговального станка «ХОН-1»
Процесс хонингования с круговой осцилляцией реализован на опытном вертикально-хонинговальном станке модели 3К83 [11], который выпускался Стерлитамакским станкозаводом. Кинематическая схема станка показана на рис. 3. Круговые колебания генерируются с помощью шарнирного четырехзвенника 9 , ведущий кривошипный вал которого через клиноременный вариатор 10 с электродвигателем 8 . Круговые колебания с помощью дифференциала 4 суммируются с основным вращением, которое сообщается шпинделю 1 от основного электродвигателя 7 через коробку скоростей 5 , дифференциал 4 и гильзу 2 . Благодаря этому шпиндель 1 и связанная с ним хонинговальная головка (на схеме не показана) получают вращение с переменной скоростью. Для регулировки частоты и амплитуды круговых колебаний предусмотрена возможность бесступенчатого изменения числа оборотов ведущего кривошипа и изменения величины его радиуса. Возвратно-поступательное движение сообщается шпинделю от гидроцилиндра 3 .
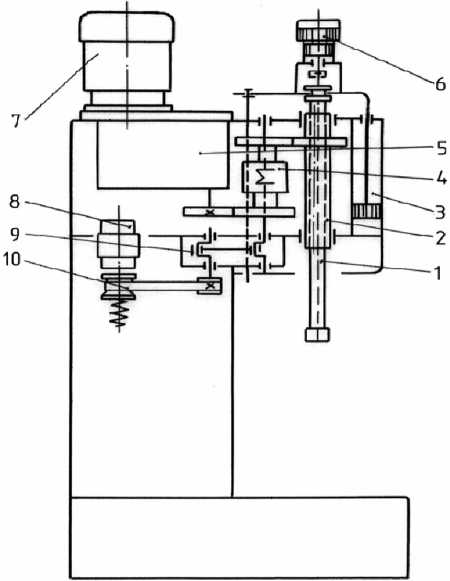
Рис. 3. Кинематическая схема станка 3К83 с круговой осцилляцией
При вибрационном хонинговании, как с круговыми, так и с осевыми колебаниями различают два вида траекторий: однонаправленные, при которых скорость основного движения больше максимальной скорости колебания и разнонаправленной, когда скорость колебаний больше скорости основного движения. Разнонаправленная траектория при круговой осцилляции, развернутая на плоскость, показана на рис. 4а.
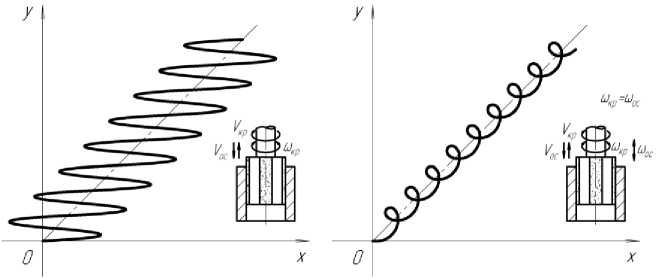
а) б)
Рис. 4. Траектория движения режущих зерен: а) при вибрационном хонинговании; б) при вихревом хонинговании
Траекторию движения абразивного зерна при вибрационном хонинговании, развернутую на плоскость, можно выразить параметрическими управлениями:
-для осевой осцилляции:
X = VKР ■t; Y = Bsin rot + V ■ t
KP OC
-для круговой осцилляции:
X = A sin rot + VKp-t; Y = Voc ■ t где t – время; А, В – амплитуды соответственно круговых и осевых колебаний; ю - круговая частота колебаний;
Развитием вибрационного хонингования является метод вихревого хонингования, разработанной в Рижском техническом университете [12]. Основное отличие от предыдущих методов заключается в том, что инструменту одновременно сообщаются осевые и круговые колебания с одинаковыми частотами. На рис. 5 показана кинематическая схема устройства, реализующая вихревой метод хонингования. На шпинделе 1 станка закреплен корпус 2 устройства. Соосно со шпинделем неподвижно установлено коническое зубчатое колесо 3 , с которым связаны блоки зубчатых колес конических 4 и цилиндрических 5 , находящимися в зацеплении с зубчатыми колесами 6 , на которых закреплены кривошипные пальцы 7 . Кривошипные пальцы 7 с помощью вращательных пар 8 и поступательных пар 9 соединены с хонголовкой 10 . При вращении шпинделя 1 и связанного с ним корпуса 2 конические колеса 4 окатываются по неподвижному колесу 3 и передают с помощью колес 5 вращение колесам 6 с кривошипными пальцами 7 . Благодаря тому, что кривошипные пальцы 7 связаны с хонголовкой с помощью вращательных 8 и поступательных 9 пар, хонинговальная головка совершает сложное движение по петлеобразной траектории, описанной на цилиндрической поверхности. Развертка траектории на плоскость показана на рис. 4б.
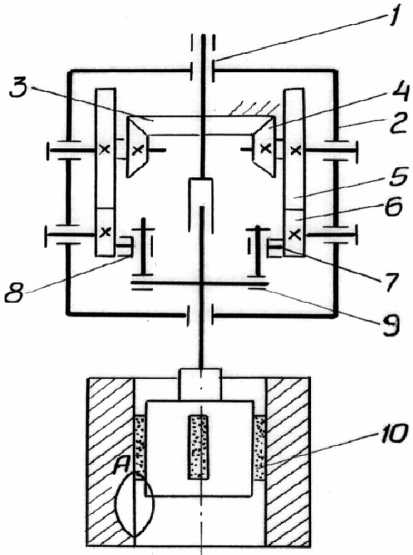
Рис. 5. Кинематическая схема вихревого метода хонингования
Параметрические уравнения, описывающие траекторию рабочего движения инструмента при вихревом методе хонингования, имеют вид:
X = А sin rot + VKр • t Y = В sin re t + Voc t;
Таким образом, как при вихревом, так и при вибрационном хонинговании значительно усложняется траектория рабочего движения инструмента. Это позволяет более полно использовать режущую способность инструмента, уменьшить длину срезаемой стружки, повысить производительность и стабильность процесса хонингования. Кроме того, изменяя соотношения скоростей, а также амплитуду и частоту колебаний, можно варьировать конфигурацию траектории. Однако в силу ограниченных возможностей кинематики эти методы хонингования не располагают необходимым комплексом управляющих воздействий для обеспечения требуемой точности геометрической формы и шероховатости обрабатываемых поверхностей.
В Пермском национальном исследовательском политехническом университете разработан и изготовлен хонинговально-доводочный станок «Растр Ц20» [13] с комплексным рабочим движением инструмента. Станок предназначен для финишной обработки прецизионных отверстий диаметром до 20 мм и длиной до 150 мм в деталях топливной и гидравлической аппаратуры. По компоновке станок выполнен с вертикальным расположением шпинделя, весь комплекс движений сообщается инструменту. В отличие от хонинговальных станков с традиционной кинематикой данный станок позволяет осуществлять различные методы хонингования, имеющие усложненные траектории рабочего движения, с тонко регулируемыми параметрами. Кинематическая схема станка представлена на рис. 6 и состоит из привода вращения шпинделя с механизмами колебательных движений и привода возвратнопоступательного перемещения инструмента вдоль оси обрабатываемой детали. Привод вращения и колебательных движений содержит электродвигатель 1, связанный клиноременной передачей 2 с промежуточным валом 3. Последний посредством клиноременного вариатора 4 и зубчатой передачи 5 соединен с коническим дифференциалом и механизмом 6 осевых колебаний, который выполнен в виде двух торцовых кулачков, взаимодействующих через два шарика связанных одним сепаратором с опорной шайбой 7, жестко закрепленной на шпинделе 8. Конический дифференциал содержит одинаковые центральные колеса 9, 10 и сателлиты 14. Общая ось сателлитов 14 выполнена в виде изогнутого Z-образного вала 15, кинематически связанного с помощью вилки 16 со шпинделем 8, причем один из сателлитов жестко соединен с валом, а другой - с возможностью свободного вращения. На валах центральных колес 9 и 10 конического дифференциала установлены двусторонние муфты 11 и 12, предназначенные для стопорения колес относительно корпуса шпиндельной коробки 13 или сообщения им вращения от вариатора 4 и передачи 5. Привод возвратно-поступательного движения шпиндельной коробки 13 по колонне 19 включает реверсивный электродвигатель 17, ходовой винт 18, работающий в паре с гайкой, закрепленной на шпиндельной коробке. Скорость поступательного движения регулируется частотой вращения электродвигателя, а величина и положение хода бесконтактными конечными переключателями. В зависимости от технологического назначения операции (предварительное, окончательное) путем переключения муфт 11 и 12 устанавливается метод хонингования и задается соответствующая траектория рабочего движения инструмента. Станок реализует два метода виброхонингования с различными частотами осциллирующего движения и растровый метод хонингования, отличающийся сложной и неповторяющейся траекторией рабочего движения с тонко регулируемыми параметрами.
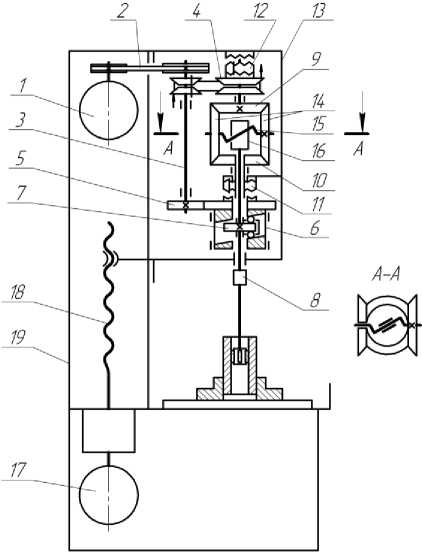
Рис. 6. Кинематическая схема хонинговальнодоводочного станка «Растр Ц20»
Введем обозначения: ю 1, ю 2 - частоты вращения центральных колес 9 и 10 конического дифференциала; ю шп - частота вращения шпинделя; ю кр - частота круговых колебаний шпинделя; ю ос - частота осевых колебаний шпинделя; ioc - передаточное отношение механизма осевых колебаний; iKp - передаточное отношение от центральных колес к сателлитам дифференциального механизма. Рассмотрим вариант работы станка, когда муфта 11 включена вниз и центральному колесу 10 конического дифференциала сообщается вращение, а колесо 9 зафиксировано муфтой 12 относительно корпуса 13 . Строго говоря, в этом случае дифференциальный механизм становится планетарным. При пуске станка по циклу включается реверсивный электродвигатель 17 и с помощью ходового винта 18 инструмент, закрепленный в шпинделе 8 , поступательное движение вдоль оси обрабатываемой детали. Одновременно включается электродвигатель 1 и движение клиноременной передачей 2 передается на промежуточный вал 3 , который через зубчатую передачу 5 и муфту 11 сообщает вращение центральному колесу 10 конического дифференциала. При этом второе центральное колесо 9 зафиксировано с помощью двусторонней муфты 12 относительно корпуса 13 . Сателлиты 14 , обкатываясь по неподвижному колесу 9 , сообщают с помощью Z-образного вала 15 и вилки 16 быстрое вращение шпинделю 8 с частотой равной половине частоты вращения колеса 10 [14].
юшп ю2 /2
Кроме того, за счет вращения Z-образного вала вокруг собственной оси шпинделю дополнительно сообщаются круговые колебания, амплитуда которых равна углу наклона Z-образного вала. Частота круговых колебаний ровна частоте вращения Z-образного вала и определяется из выражения:
® кр— (® 2 /2) i Kp = юшп i Kp
Вследствие малой амплитуды круговых колебаний суммарное движение, сообщаемое шпинделю представляет собой однонаправленное (без реверса) вращение с переменной скоростью.
Одновременно с промежуточного вала 3 через зубчатую передачу 5 вращение передается торцовым кулачкам механизма 6, которые через синхронно вращающиеся шарики сообщают опорной шайбе 7 и шпинделю 8 осевые колебания. Амплитуда колебаний определяется углом скоса торцовых кулачков и диаметром кольцевых канавок на опорной шайбе, а частота пропорциональна алгебраической разности скоростей вращения шпинделя и кулачков механизма 6. Такой механизм позволяет безударно и с минимальными инерционными нагрузками генерировать колебания с большой частотой. В описанном варианте включения двусторонних муфт 11 и 12 шпиндель и торцовые кулачки механизма 6 вращаются в одном направлении, в результате шпинделю сообщаются низкочастотные осевые колебания, У« = (у - У. ) ■ im , учитывая что Юшп=to2/2, ωос=ωшп iос. При таком соотношении всех элементарных движений, включая и поступательное движение шпиндельной коробки, реализуется метод виброхонингования с однонаправленной траекторией как показано на рис. 7а рабочего движения инструмента. При переключении муфты 11 вверх, а муфты 12 вниз, центральное
колесо 10 конического дифференциала фиксируется относительно корпуса 13 , а колесу 9 через клиноременный вариатор 4 сообщается вращение в направлении обратном предыдущему случаю. В результате движение обкатки сателлитов 14 по неподвижному колесу 10 и вращение шпинделя 8 реверсируются. Частоты вращения и круговых колебаний шпинделя определяются частотой ω 1 вращения центрального колеса 9
ω
шп
У
У, = бУ ■ i кр шп кр
;
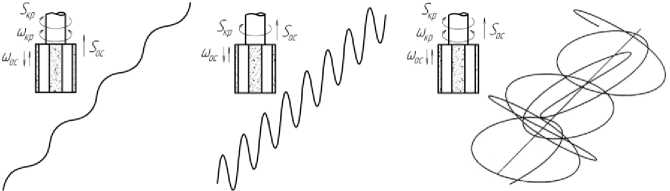
а) б) в)
Рис. 7. Виды траекторий инструмента на станке «Растр Ц20»
В данном варианте включения муфт шпиндель и торцовые кулачки механизма 6 вращаются в противоположных направлениях, в результате шпинделю сообщаются высокочастотные осевые колебания.
Уос = (У2
-
( У шп )) i oc при
ω =ω
Уос = 3 ■ Ушп ■ ioc
Такое соотношение элементарных движений характерно для виброхонингования с разнонаправленной траекторией рабочего движения (рис. 7б). Кроме того, вследствие вращения шпинделя с переменной скоростью в обоих вариантах виброхонингования осевые колебания генерируются с непрерывно изменяющейся начальной фазой [15]. Возможность периодического реверсирования вращения шпинделя позволяет более полно использовать режущую способность инструмента и обеспечивает равномерный его износ.
Принципиальное отличие растрового метода хонингования [16] от традиционного и вибрационных методов заключается в том, что главное движение резания есть результат комбинации двух синусоидальных колебаний с различными частотами и амплитудами во взаимно перпендикулярных направлениях – круговых и осевых. Для равномерного распределения образующейся сетки по всей обрабатываемой цилиндрической поверхности инструменту или обрабатываемой детали дополнительно
сообщаются возвратно-поступательное и вращательное движения с малыми скоростями, которые представляют собой соответственно осевую (S OC ) и круговую (S KP ) подачи. Растровая траектория рабочего движения инструмента реализуется путем переключения муфт 11 и 12 вниз. В этом случае центральные колеса 9 и 10 конического дифференциала получают вращение в противоположных направлениях и с разными скоростями. Частота вращения колеса 10 постоянная, а колеса 9 может регулироваться в небольшом диапазоне с помощью клиноременного вариатора 4 , причем в середине диапазона регулирования частоты вращения колес 9 и 10 по модулю равны. За счет разности скоростей центральных колес шпинделю сообщается медленное вращение (круговая подача), величина и направление которой регулируются и определяется из выражения:
ω
шп
ω +ω
= ± —---
Одновременно от Z-образного вала 15 и механизма 6 шпиндель получает круговые и осевые колебания, рассогласованные по частоте.
ω кр
ω +ω
—2------- ■ i кр • Ус = (У ± Ут ) ■ ioc
ОС 2 ^Ш1 ОС
;
При растровом хонинговании средние скорости колебательных движений значительно
превышают скорость вращения и поступательного движения. При таком соотношении скоростей образуется сложная и неповторяющаяся сетка следов обработки как показано на рис. 7в, причем плотность сетки можно бесступен-чато изменять путем регулирования круговой подачи и скорости поступательного движения. Таким образом, предлагаемая конструкция станка позволяет простыми техническими средствами реализовать на одном оборудовании различные методы хонингования, отличающиеся траекторией рабочего движения инструмента.
Выводы: проведенный анализ показал, что чем разнообразнее и сложнее траектория движения режущих зерен, тем полнее используется режущая способность инструмента, интенсифицируется процесс резания и тем лучше условия для управления формированием макро и микрорельефа обрабатываемых поверхностей.
Список литературы Кинематика методов хонингования
- Кремень, З.И. Абразивная доводка/З.И. Кремень, А.И. Павлючук//Под ред. Г.Ф. Кудасова. -М.: Машиностроение, 1967. 114 с.
- Куликов, С.И. Прогрессивные методы хонинговагия/С.И. Куликов, Ф.Ф. Ризванов и др. -М.: Машиностроение, 1983. Т. 13. С. 5.
- Фрагин, И.Е. Новое в хонинговании. -М.: Машиностроение, 1980. 96 с.
- Справочная книга по отделочным операциям в машиностроении/Под ред. М.Г. Космачева. -Л.: Лениздат, 1966. 544 с.
- Кудояров, Р.Г. Точность деталей машин при алмазном хонинговании. -М.: Изд-во МАИ, 2002. 170 c.
- Исаков, А.Э. Хонингование с дозированной подачей и оборудование для его реализации//В кн.: Хонингование цилиндрических и фасонных поверхностей. -Пермь, 1988. С. 64-67.
- Мурахвер, А.С. Определение оптимальной амплитуды при вибрационном хонинговании//Материалы республиканской научно-теоретической конференции молодых ученых и аспирантов. -Самарканд, 1968. С. 36-41.
- Подураев, В.Н. Алмазное вибрационное хонингование отверстий в стальных закаленных деталях/В.Н. Подураев, А.А. Суворов, В.И. Карпов//В сб.: Синтетические алмазы в промышленности. -Киев, Наукова думка, 1974. С. 167-172.
- Мисевич, В.С. Проектирование механизмов осцилляции для металлорежущих станков//Станки и инструмент. 1968. №7. С. 5-7.
- Sunnen SV-1000 series vertical honing machines. Catalog. Sunnen products company. 2007.
- Вопросы расчета и конструирования оснастки, обеспечивающей повышение точности при хонинговании. Труды УАИ. -Уфа, 1973. Вып. 44. 159 с.
- А.с. № 378313. Устройство для сообщения колебательного движения хонинговальной головке./И.К. Воробьев, П.А. Давыдов, А.В. Сандалов//М., 1973. Б.И. №19.
- Некрасов, В.П. Станки с растровой кинематикой для финишной обработки поверхностей постоянной кривизны/В.П. Некрасов, Р.А. Муратов//Современные организационные, технологические и конструкторские методы управления качеством. Сборник научных трудов. -Пермь: ГОУ ВПО ПГТУ, 2006. С. 96-116.
- Вопилкин, Е.А. Расчет и конструирование механизмов приборов и систем. -М.: Высшая школа, 1980. 463 с.
- Зиновьев, А.Л. Введение в теорию сигналов и цепей/А.Л. Зиновьев, Л.И. Филиппов. -М.: Высшая школа, 1968. 280 с.
- Муратов, К.Р. Растровое хонингование и его кинематические возможности/К.Р. Муратов, А.М. Ханов//Материалы ХII Всероссийской научно-технической конференции «Аэрокосмическая техника, высокие технологии и инновации -2009». -Пермь, 2009. С. 114-116.