Комплексная автоматизация машиностроительного проектирования и производства при программном базировании деталей на станках с ЧПУ
Автор: Носов Николай Васильевич, Черепашков Андрей Александрович, Горяинов Дмитрий Сергеевич, Хрустицкий Кирилл Владимирович
Журнал: Известия Самарского научного центра Российской академии наук @izvestiya-ssc
Рубрика: Машиностроение и машиноведение
Статья в выпуске: 4-2 т.18, 2016 года.
Бесплатный доступ
В статье обсуждаются проблемы автоматизации конструкторско-технологической подготовки производства деталей сложной формы на станках с числовым программным управлением. Предлагается и описывается комплексная методика проектирования заготовок деталей и управляющих программ для станков с ЧПУ, основанная на использовании современных технологий автоматизированного проектирования и электронных средств измерений.
Компьютерные технологии в машиностроении, сапр, чпу
Короткий адрес: https://sciup.org/148204690
IDR: 148204690
Текст научной статьи Комплексная автоматизация машиностроительного проектирования и производства при программном базировании деталей на станках с ЧПУ
цессы, составляющие в своем комплексе основу конструкторско-технологической подготовки производства (КТПП), в существенной мере взаимозависимы. И уже на этапе моделирования формообразующих поверхностей машиностроительных деталей необходимо учитывать с какой точностью, какими инструментами и на каком оборудовании они будут изготовлены. В свою очередь все перечисленные вопросы обязательно должны быть учтены и конкретизированы при выборе стратегии обработки и параметров управляющих программ.
Геометрическая модель, созданная конструктором в среде машиностроительных САПР, определенным образом преобразуется технологом в модели заготовок, разрабатываемых технологом, также средствами САПР. При этом можно утверждать, что современные методы автоматизации проектирования существенно меняют традиционные подходы к проектированию заготовок и разработке технологических процессов.
Как правило, размеры заготовок включаются в технологическую размерную цепь, по которым строится координатная система, с использованием основных и вспомогательных баз (поверхностей) . В тоже время обрабатываемая деталь присоединяется к деталям технологической системы путем совмещения ее технологических баз с исполнительными поверхностями приспособления или станка, в связи с этим координатная система меняет свое положение и строятся на исполнительных поверхностях приспособления или станка. Совмещая координатные системы указанным способом, получим совокупность координатных систем, связанных между собой. Но, поскольку каждая составляющая технологической системы лишена соответствующего числа степеней свободы, то на образовавшую координатную систему следует наложить определенные связи. Роль связей при обработке выполняют опорные точки на поверхности заготовки или инструмента. Таким образом, перемещение опорных точек можно представить как функции свойств связей и действующих технологических факторов.
Запишем уравнение движения таким образом, чтобы в него вошли факторы, вызывающие нарушение траектории относительного движения резца и заготовки. Для этого надо каждое перемещение и поворот каждой координатной системы заменить функциями перемещений их опорных точек. А перемещения опорных точек в свою очередь представить как функции свойств, связей и действующих факторов.
В итоге должно быть записано уравнение координат точек режущих кромок (заданных в координатной системе инструмента) в координатной системе, построенной на технологических базах детали, то есть
^д = АС^и.Уи^и.О,Уд = Л(«юУ^^и>0>
Уд = А(^и.Уи^иЛ), 2д = /з (Ли# Уи,2и> О, где xД, уд, zД – координаты точки М режущих кромок инструмента в координатной системе детали, хИ, уИ, zИ – координаты точки М режущих кромок инструмента в координатной системе инструмента, t – параметр движения.
Рассмотрим положение точки М режущей кромки инструмента при переходе из одной координатной системы в другую. Установлено положение точки М при последовательном переходе через все координатные системы эквивалентной схемы в координатную систему детали.
Получено уравнение движения точки М, которое содержит радиус-векторы (ri) начала координатных систем и матрицы (Mi) трех последовательных поворотов каждой координатной системы, то есть
R = f
В свою очередь
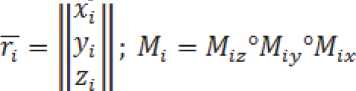
,
Таким образом, уравнение движения точки М будет содержать по шесть параметров, определяющих положения каждой координатной системы в эквивалентной системе.
Последовательное установление функциональных связей между действующими факторами и перемещениями опорных точек, между перемещениями опорных точек и шестью параметрами положения каждой координатной системы, между последними и радиус-вектором точки поверхности обработанной детали, позволяет математически описать связи между действующими факторами и суммарной погрешностью обработки. Определяя погрешность обработки в каждой точке поверхности, находим погрешность всей обработанной поверхности детали. Это позволит с помощью известных методик определить точность детали по размеру, применительно к относительным поворотам и геометрической формы ее поверхностей.
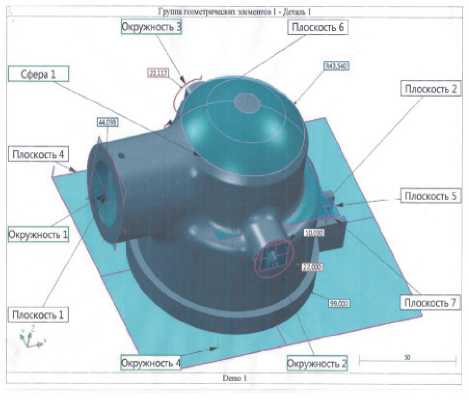
Рис. 1. Трехмерная модель корпусной детали (обозначены основные и вспомогательные конструкторские базы)
где xi, yi, zi – координаты начала (точки ) i-й координатной системы,
Miz, Miy, Mix – матрицы поворотов i-й координатной системы вокруг осей OZ, OY, OX.
При этом
^ix
M;y
1 о о
о cos(p sirup
COSO) о —sina)
о
о
О —sirup cosy si тио
О
COSO)
;
;
Методика определения погрешностей установки заготовки, статической и динамической настройки технологической системы принципиально не отличается от методики определения суммарной погрешности обработки. Отличие заключается лишь в эквивалентных схемах.
Построение эквивалентной схемы для расчета погрешностей на каждом этапе начинается с выявления размерных цепей установки, статической и динамической настроек. Отличие размерных цепей определяет отличие эквивалентных схем и вида уравнения относительного движения.
Как следует из изложенного, основными этапами построения математической модели является: выбор показателя точности, построение эквивалентной схемы, запись уравнения относительного движения и ввод в уравнение движения действующих факторов и качественных характеристик.
С помощью такого рода математических моделей и средствами САПР можно решать широкий спектр задач, связанных с расчетом, обеспечением и прогнозированием точности машин как на этапе их конструирования, изготовления, так и в процессе эксплуатации.
Совместить координатные технологические системы ( заготовки , приспособления и станка) не всегда представляется возможным , особенно при обработке на универсальных станках. При обработке заготовок на станках с ЧПУ данное совмещение можно осуществить с помощью программного базирования .
Согласование процессов геометрического моделирования на конструкторском и технологическом этапах КТПП способствует достижению оптимального результата проектирования, обеспечивающего повышение качества выпускаемых изделий и повышение производительности обрабатывающего оборудования (см. рис. 1).
Разработка технологических процессов для оборудования с ЧПУ, оснащенного электронными средствами измерения, позволяют использовать методы так называемого «программного» базирования. В отличие от традиционных методов базирования заготовок (см. рис. 2), давно и успешно используемых для универсального обрабатывающего оборудования, управляемого квалифицированным рабочим, программным будем называть метод базирования на станках с ЧПУ, оснащенных программно-управляемыми электронными средствами измерения.
Программное базирование отличается от «ручных» методов, тем, что средствами программирования решается обратная задача - коррекции положения основных осей обработки станка с ЧПУ относительно координат базовых точек, измеренных на поверхности заготовки, закрепленной на станке [2].
При этом становится возможной относительно грубая, но достаточно простая и быстрая установка заготовки на столе станка (см. рис. 3). Необходимыми условиями для реализации этого метода на станках с ЧПУ выступают возможности многоосевой отработки (3-6 осей) и наличие встроенных цифровых средств измерений.
С точки зрения технолога при этом при разработке высокоавтоматизирован-ного технологического процесса объединяются ресурсы конструкторских, технологических и измерительных баз. Совмещение механической обработки и измерений в одной программе позволяет существенно сократить общую длительность цикла
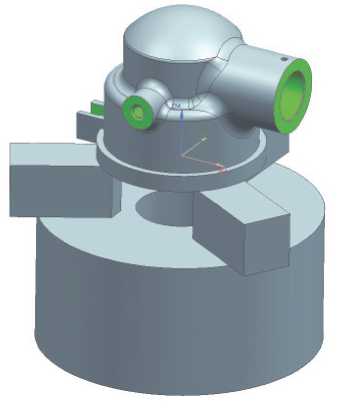
Рис. 2. Схема установки корпусной детали при фрезеровании с традиционной схемой базирования

Рис. 3. Схема установки корпусной детали при фрезеровании с программным базированием изготовления, и, что самое важное, резко повысить точность и безошибочность выдерживания размеров и допусков.
Следует заметить, что идеи адаптивной обработки деталей, когда предлагалось корректировать процесс резания в зависимости от результатов измерений [3], не новы. Но возможности современного цифрового оборудования, в сочетании с функционалом прикладного программного обеспечения САПР придают качественно новые качества технологиям машиностроения и позволяют комплексно автоматизировать проектно-производственные стадии жизненного цикла изделий.
Программное базирование целесообразно осуществлять от основных Комплексная система АСТПП адаптивного изготовления корпусных деталей позволяет:
Применить автоматизацию запрограммированных циклов измерений, для обеспечения распознавания точной установки заготовки в специальное приспособление.
Определить параметры смещения и поворота осей обработки по отношению к истинному положению заготовки.
Рассчитать автоматически все параметры (размеры) заготовки при обработке на станке от смещенных осей.
Комплексная методика автоматизации проектирования и производства изделий на станках с ЧПУ позволяет одновременно с повышением ка- чества обработки деталей существенно сократить сроки изготовления изделий. конструкторско-измерительных элементов 3D-модели заготовки (3D-деталь с припусками).
Произвести автоматическое программное базирование заготовки, при котором не требуется предварительной или вспомогательных конструкторских баз обрабатываемых деталей, что позволяет исключить погрешности базирования в приспособлении, погрешности от смены баз, погрешности обработки технологических баз (см. рис. 4).
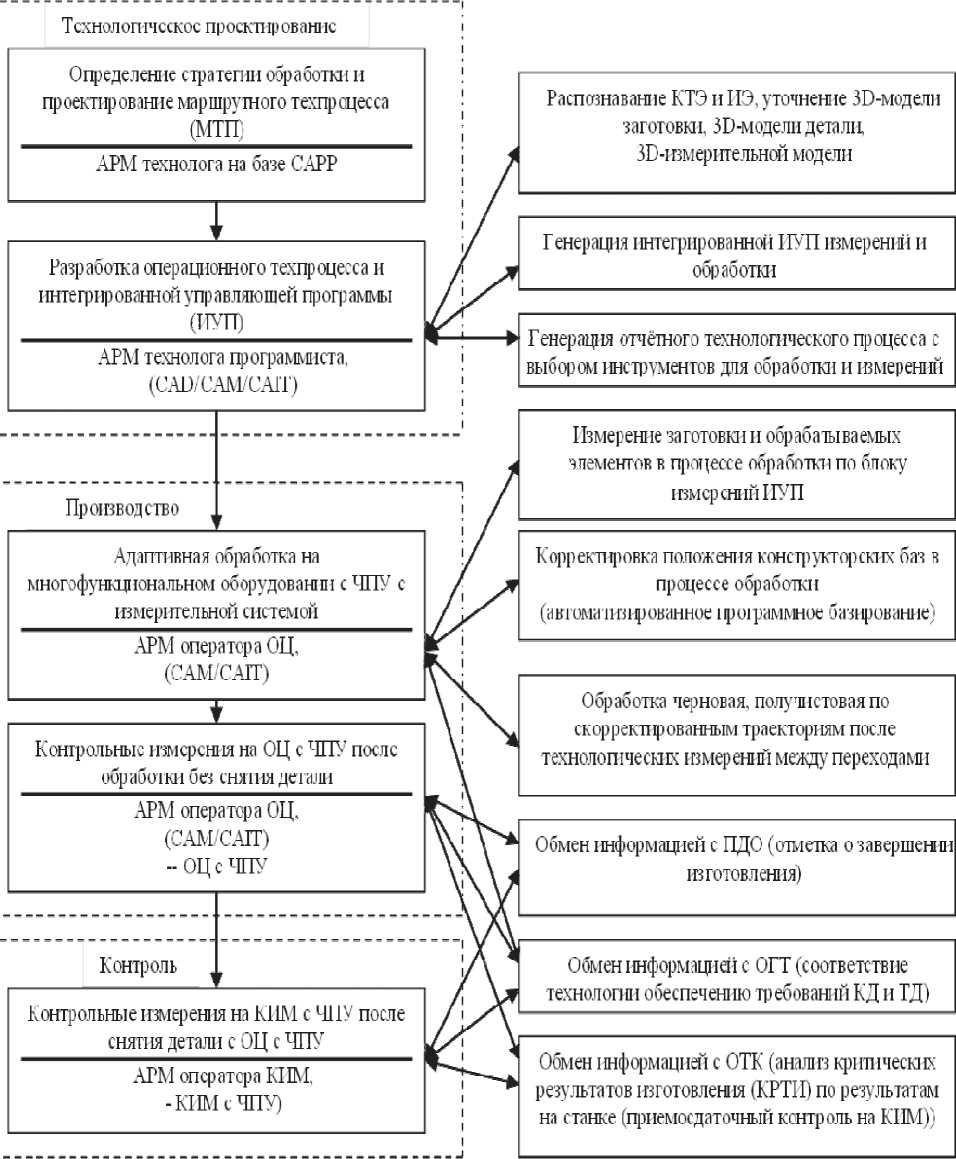
Производство
Контроль
Тсхнолоп псскос просктир ованис
Корректировка положения конструкторских баз в процессе обработки (автоматизированное прозраммное базирование)
Измерение заготовки и обрабатываемых элементов в процессе обработки по блоку измерений ПУП
Разработка операционного техпроцесса и интегрированной управляющей программы ______________ (ПУП) ______________ АРМ технолога программиста.
(CAD/CAM/CA1T)
Адаптивная обработка на многофункциональном оборудовании с ЧПУ с измерительной системой
АРМ оператора ОЦ.
(САМ/САП)
Контрольные измерены на ОЦ с ЧПУ после обработки без снятия детали АРМ оператора ОЦ. (САМ/САП) - ОЦ с ЧПУ
Определение стратегии обработки и проектирование маршрутного техпроцесса ______________(МТИ)______________ АРМ технолога на базе САРР
Контрольные измерения на КИМ с ЧПУ после снятия детали с ОЦ с ЧПУ
АРМ оператора КИМ,
-КИМ с ЧПУ)
Обмен информацией с ОТК (анализ критических результатов изготовления (КРТП) по результатам на станке (приемосдаточный контроль на КИМ))
Обработка черновая, полутптеговая по скорректированным траекториям после технолоптческих измерений между переходам!
Распознавание КТЭ и ПЭ, уточнение ЗБ-модели заготовки. 3D-Mодели детали ЗБ-измерительной модели
Обмен информацией с ПДО (отметка о завершено! изготовлены)
Генерация интегрированной ПУП измерений и обработки
Генерация отчётного технологического процесса с выбором инструментов для обработки и измерений
Обмен информацией с ОГТ (соответствие технологии обеспеченно требований КД и ТД)
Рис. 4. Функциональная схема комплексной АСТПП адаптивного производства корпусных деталей
Для изучения эффективности и иллюстрации возможностей комплексных процессов автоматизации предлагается использовать «S»-образные кривые (рис. 5), построенные по аналогии с методикой исследования приведенной в [4].
В данном случае может быть использован интегральный критерий качества изготовления, учитывающий погрешности конструкторских ( Pk ) и технологических ( Pt ) моделей, базирования ( Pb ) и изготовления ( Pm ):
F = f (P k , , P t , P b , P m ) . (1)
По горизонтальной оси откладывается продолжительность исследуемых процессов. В случае традиционной - ручной методики число операции КТПП велико и достигается минимально допустимый по технологии уровень качества. При использовании средств автоматизации, за счет повышения точности моделирования и использования оптимизации стратегии обработки на станках с ЧПУ, обеспечивается повышение качества и снижение трудоемкости. Наибольший уровень качества при одновременном снижении временных затрат прогнозируется при комплексной методике автоматизации проектирования и изготовления изделий на станках с ЧПУ. В данной статье рассматривается подтвержденная практикой и теоретическими исследованиями авторов концепция комплексной методики автоматизации проектирования и изготовления изделий на станках с ЧПУ и предлагаются объективные методы ее исследования.
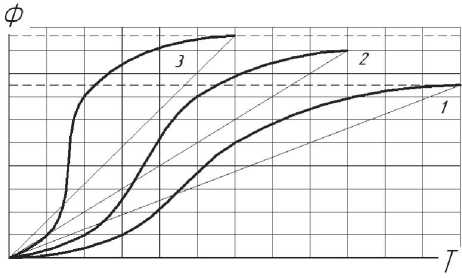
Рис. 5. Сравнение эффективности процессов КТПП: 1– традиционная технология;
2 – автоматизация локальных процедур проектирования;
3 – комплексная автоматизированное проектирование и производство на станках с ЧПУ
Список литературы Комплексная автоматизация машиностроительного проектирования и производства при программном базировании деталей на станках с ЧПУ
- Черепашков А.А., Носов Н.В. Компьютерные технологии, моделирование и автоматизированные системы в машиностроении: учебник для студ. высш. учеб. заведений. Волгоград: Инфолио, 2009. 650 с.
- Хрустицкий К.В., Черепашков А.А. Комплексная автоматизация технологической подготовки производства и управления процессами механической обработки корпусных деталей машин//Вест. Самар. гос. аэрокосм. ун-та. 2012. № 5(36). Ч. 1. С. 61 -71.
- Адаптивное управление станками . М.: Машиностроение, 1973. 688 с.
- Черепашков А.А. Методика оценки эффективности подготовки целевого персонала машиностроительных САПР//Изв. Самар. науч. центра РАН. 2011. Т. 13. № 4(3). С. 897 -899.