Конечно-элементное моделирование формообразующих операций передела лист-труба с учётом деформации валкового инструмента и сварочных деформаций
Автор: Залавин Я.Е., Баталов Г.С., Машенцева М.С.
Журнал: Вестник Южно-Уральского государственного университета. Серия: Металлургия @vestnik-susu-metallurgy
Рубрика: Обработка металлов давлением. Технологии и машины обработки давлением
Статья в выпуске: 1 т.25, 2025 года.
Бесплатный доступ
Работа посвящена исследованию формообразующих операций, применяемых в производстве труб большого диаметра (ТБД) с использованием трехвалковой листогибочной машины (вальцев). В программном комплексе Marc.Mentat разработаны конечно-элементные модели процессов вальцевой формовки, догибки кромок, сборки, сварки и экспандирования трубы. Объектом исследования является труба диаметром 1420 мм с толщиной стенки 21,6 мм и длиной 12 м из стали группы прочности X70. В модели трубы использовались тонкостенные (Shell) элементы, что позволяло относительно быстро осуществлять процесс моделирования без существенной потери точности расчетов. Проведено комплексное конечно-элементное моделирование формообразующих операций передела лист-труба с учетом деформации верхнего валка листогибочной машины и сварочных деформаций. Установлено, что при каждой технологической операции в трубе возникает неоднородное напряженно-деформированное состояние (НДС), которое оказывает влияние на конечную геометрию труб. Показано, что наибольшую неоднородность НДС в трубу вносят вальцевая формовка и догибка кромок. Разработанная комплексная конечно-элементная модель может быть использована исследователями и технологами для расчета настроек технологического оборудования и энергосиловых параметров формообразующих операций.
Формообразующие операции, трубы большого диаметра, вальцевая формовка, догибка кромок, сборка, сварка, экспандирование, компьютерное моделирование
Короткий адрес: https://sciup.org/147248042
IDR: 147248042 | DOI: 10.14529/met250103
Текст научной статьи Конечно-элементное моделирование формообразующих операций передела лист-труба с учётом деформации валкового инструмента и сварочных деформаций
G.S. Batalov, , M.S. Mashentseva, , TMK Research, LLC, Chelyabinsk, Russia
Магистральные трубопроводные системы играют ключевую роль в современной инфраструктуре, обеспечивая транспортировку углеводородов на большие расстояния. Одним из критически важных факторов, обеспечивающих эксплуатационную надежность трубопроводов, является высокая точность геометрических параметров труб.
Совершенствование технологии производства труб большого диаметра для транспортировки нефти и газа становится всё более актуальным в условиях современных вызовов, связанных с безопасностью, экологичностью и операционной эффективностью данных процессов [1, 2].
Формовку основного периметра труб большого диаметра осуществляют на прессах либо в вальцах [3–5].
В технологических линиях производства ТБД с применением вальцевой формовки для получения трубной заготовки под сварку лист вначале изгибают в трехвалковых вальцах до заданного радиуса, затем выполняют догибку плоских участков в клети догибки кромок, после чего выполняется сборка трубы и сварка технологического шва, затем производят сварку основных швов и пошаговое экспанди-рование.
На сегодняшний день для совершенствования технологии производства труб большого диаметра и освоения новых видов трубной продукции успешно применяются средства конечно-элементного моделирования [6–14].
По данным литературных источников, как правило, исследуется один или несколько формообразующих процессов.
При моделировании технологических процессов методом конечных элементов принимают следующие допущения: геометрические и механические свойства заготовки изотропны; деформирующий инструмент абсолютно жесткий; сварочные деформации не учиты-
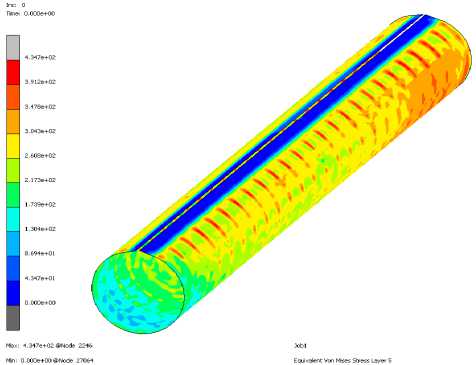
а)
Рис. 1. Результаты моделирования процесса вальцевая формовка: а – общий вид расчётной модели после моделирования процесса формовки; b – распределение эквивалентных напряжений по телу верхнего валка Fig. 1. Simulation results of the roller forming: a – general view of the computational model after modeling the molding process; b – distribution of equivalent stresses over the upper roll body
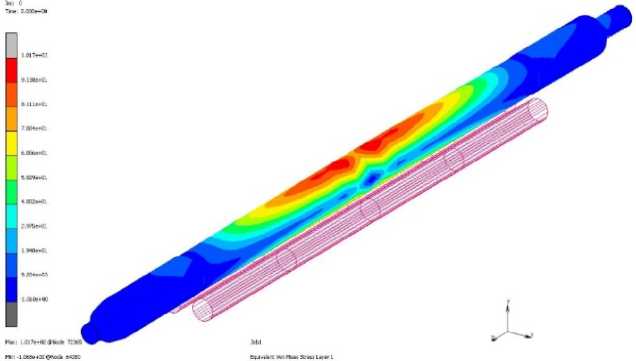
b)
ваются; история напряженно-деформированного состояния заготовки, полученная в результате выполнения предшествующих операций, не учитывается.
В рамках данного исследования разработана комплексная конечно-элементная модель передела лист-труба с применением вальцевой формовки с учетом деформации верхнего валка машины вальцевой формовки, сварочных деформаций и учета истории накопления напряженно-деформированного состояния (НДС) заготовки от операции к операции. Материал исходной заготовки изотропный.
При моделировании технологических операций применяли тонкостенные (Shell 140) оболочечные элементы.
Вальцевая формовка
Моделирование процесса вальцевой формовки трубной заготовки осуществлялось в три прохода верхним валком диаметром 900 мм при расстоянии между нижними валками 600 мм с начальной шириной листа 4353 мм и толщиной 21,6 мм. При этом верхний валок задавался как упругое деформируемое тело, нижние валки задавались как жесткие тела.
На рис. 1а представлено распределение эквивалентных напряжений по объему трубной заготовки после вальцовой формовки. Видно, что трубная заготовка имеет весьма большую неоднородность остаточных напряжений.
Учет деформации верхнего валка (рис. 1b) в конечно-элементной модели позволяет оценить влияние остаточных напряжений, возникающих в трубной заготовке после формовки, на результат дальнейших операций, а также производить подбор усилия противоизгиба для получения требуемой формы межкромочного зазора после формовки.
Догибка кромок
В отличие от прессовой технологии получения трубной заготовки под сварку, при вальцевой технологии кромку подгибают после формовки основного периметра заготовки. Догибку кромок осуществляют в двухвалковой клети с профилированными валками (рис. 2а) в несколько проходов.
Неравномерность высоты подгибки кромок может быть связана как с краевым эффектом, так и с потерей устойчивости кромки вследствие ее удлинения. Последний негативный эффект может быть минимизирован путем правильного распределения деформации между проходами.
Моделирование догибки кромок производили в три прохода [15] с нижним приводным и верхним холостым валками.
Результаты моделирования догибки кромок, представленные на рис. 2b в виде поля напряжений показывают, что в процессе до-гибки возникают достаточно большие продольные деформации кромки, что соответствует литературным данным [16, 17].
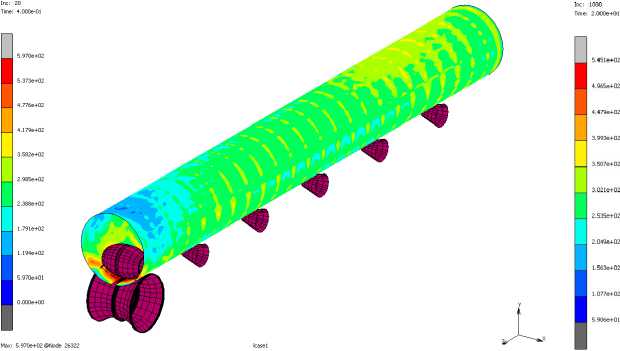
а)
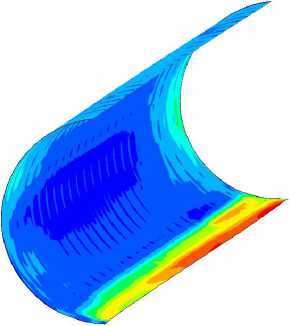
b)

с)
Рис. 2. Результаты моделирования процесса догибки кромок: а – распределение остаточных пластических деформаций в прикромочной зоне после догибки; b – форма кромки после догибки в 1-м проходе; c – форма кромки после догибки во 2-м проходе
Fig. 2. Simulation results of the edge bending: a – distribution of residual plastic deformations in the edge zone after bending; b – the shape of the edge after bending in the 1st pass; c – the shape of the edge after bending in the 2nd pass
Также стоит отметить неравномерную высоту подгибки кромок по длине трубы (рис. 2с). Для наглядности масштаб деформированной кромки был увеличен в 4 раза. Из рис. 2с видно, что на переднем конце трубы за счет большей высоты подгибки кромок вертикальный диаметр будет меньше, чем на заднем конце.
Сборка
Сборку трубной заготовки моделировали с учетом накопленного НДС после предыдущих технологических операций. При моделировании тепловым воздействием от технологического шва пренебрегали, так как его влияние на НДС трубы незначительно.
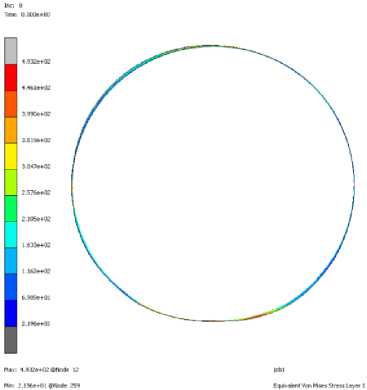
а)
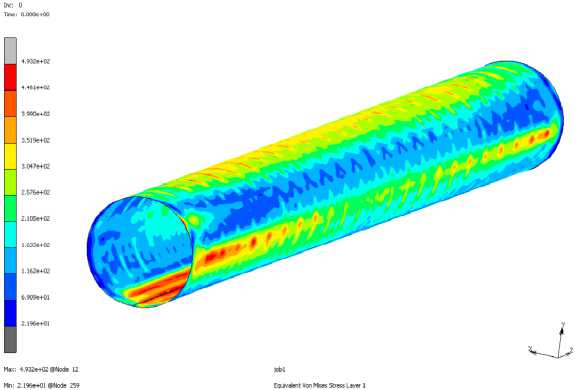
b)
Рис. 3. Результаты моделирования процесса сборки: а – форма поперечного сечения сваренной трубы; b – распределение эквивалентных остаточных напряжений по телу трубы
Fig. 3. Simulation results of the assembling: a – the shape of the cross-section of the welded pipe; b – distribution of equivalent residual stresses over the pipe body
Роликовые балки располагали под углом 90, 30, и 0° относительно вертикали.
На рис. 3а представлен профиль трубы после сборки, а на рис. 3b – распределение напряжений.
Проведенное моделирование показывает, что напряженно-деформированное состояние трубы после сборки неоднородно. В области действия валков догибки кромок в трубе сохраняется область повышенных остаточных напряжений.
Сварка
Процесс сварки трубной заготовки моделировали с учетом накопленного НДС после предыдущих технологических операций. Процесс сварки моделировали с учетом локального нагрева трубы до 1500 °С движущимся ис- точником тепла [18]. На риc. 4 представлено НДС трубы после сварки.
В процессе сварки происходило увеличение вертикального и уменьшение горизонтального диаметров, что соответствует наблюдаемым искажениям поперечного сечения трубы под действием термоцикла сварки [19, 20].
Экспандирование
Моделирование процесса экспандирова-ния осуществляли с учетом НДС от предшествующих формообразующих операций. Коэффициент экспандирования составлял 1,2 %. Экспандерная головка, состоящая из 12 сегментов, перемещалась от заднего конца к переднему с перекрытием шагов 50 мм.
На рис. 5 представлено распределение остаточных эквивалентных напряжений в трубе
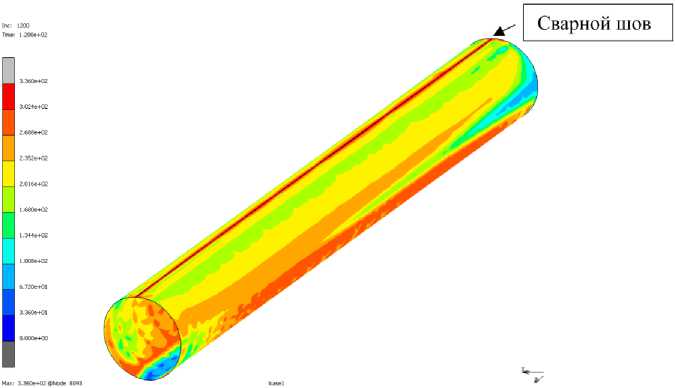
Рис. 4. Общий вид расчетной модели после моделирования процесса сварки Fig. 4. General view of the calculation model after modeling the welding process
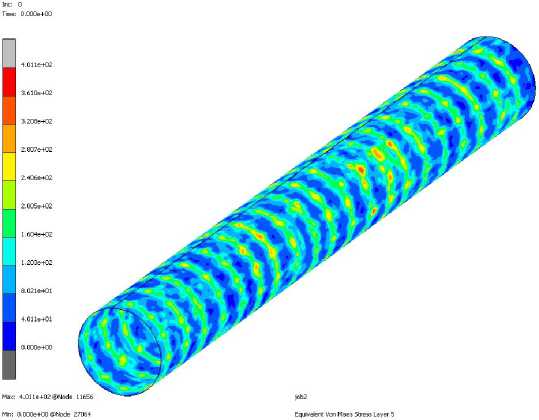
Рис. 5. Результат моделирования процесса экспандирования Fig. 5. The result of modeling the expansion process
Результаты измерений конечно-элементных моделей после экспандирования Measurement results of finite element models after expansion
С целью установления количественного влияния неоднородности напряженно-деформированного состояния на геометрические характеристики трубы после экспандирования проведено моделирование процесса экспанди-рования «идеальной» трубы.
Под «идеальной» трубой понимается труба без предыстории формоизменения, поперечное сечение которой представляет эллипс, построенный в CAD-системе. Разница между большой и малой осями эллипса была равна величине овальности трубы с предысторией НДС – 15,5 мм. Поперечное сечение вытягивалось на длину 12 метром и разбивалось на тонкостенные элементы. Задание перемещений головки экспандера в варианте с идеальной трубой аналогично варианту трубы с предысторией НДС.
Геометрические параметры двух труб после экспандирования приведены в таблице.
Выводы
-
1. Проведено комплексное конечно-элементное моделирование формообразующих операций передела лист-труба, учитывающее наследование напряженно-деформированного состояния трубы от операции к операции.
-
2. Средняя величина овальности труб, произведенных по технологии RB-forming, составляет 7–8 мм. Моделирование отдельной операции экспандирования без накопленной деформации не дает точной оценки изменения геометрических параметров. Поэтому для более точного прогнозирования необходимо учитывать НДС за предыдущие переделы в объемной постановке.
-
3. Разработанная конечно-элементная модель может быть применена для расчета настроек вальцовочной машины, установки до-гибки кромок, сборочно-сварочной машины и экспандера.