Литые металломатричные композиционные материалы электротехнического назначения
Автор: Бабкин В.Г., Терентьев Н.А., Перфильева А.И.
Журнал: Журнал Сибирского федерального университета. Серия: Техника и технологии @technologies-sfu
Статья в выпуске: 4 т.7, 2014 года.
Бесплатный доступ
Исследованы способы изготовления, структура и свойства литых металломатричных композиционных материалов на основе алюминия и меди (КМ), упрочненных дисперсными высокомодульными тугоплавкими частицами, синтезированными в расплаве. Благодаря высоким показателям электропроводности и прочности в сочетании с необходимой пластичностью предложены перспективы их применения в электротехнике взамен традиционных алюминиевых и медных сплавов, легированных переходными и редкоземельными металлами.
Металломатричные композиционные материалы, синтез армирующих фаз, механические свойства, электропроводность
Короткий адрес: https://sciup.org/146114857
IDR: 146114857
Текст научной статьи Литые металломатричные композиционные материалы электротехнического назначения
Технически чистый алюминий и медь широко применяются для проводников электрического тока, различных теплообменников, конденсаторов, шин, электродов, разрывных контактов и т.п. С целью повышения эксплуатационных свойств электротехнических изделий для их изготовления применяют низколегированные сплавы на основе алюминия и меди. Например, термостойкость и жаропрочность проводниковой и электродной меди повышают добавками циркония, кобальта, никеля, хрома, титана [1], а для производства термостойкой катанки используют сплавы системы Al-Zr [2]. Однако легирование алюминия и меди существенно снижает электропроводность материала. Степень снижения электропроводности очень зависит от содержания легирующего элемента в твердом растворе и в меньшей степени – от его выделения из раствора с образованием интерметаллидных или керамических тугоплавких избыточных фаз.
В последние годы возрос интерес к дискретно-армированным литым металломатричным композиционным материалам. В работе [3] описывается способ получения литых композиционных материалов для разрывных электроконтактов. Он основан на механическом замешивании порошка карбида вольфрама с размером частиц < 15 мкм в расплав меди при воздействии низкочастотными колебаниями. Показана возможность упрочнения матрицы частицами карбидов. Твердость литых объемно-упрочненных композитов Cu-WC превышает таковую чи-
Отечественный и зарубежный опыт показывает, что наиболее перспективными компонентами для синтеза армирующих фаз в расплавах алюминия и меди являются переходные металлы с недостроенными внутренними электронными оболочками и химически активные неметаллические добавки бор и углерод. Переходные металлы IV-VI периодов Периодической системы Менделеева образуют с алюминием твердые растворы по перетектической реакции с малой предельной растворимостью элементов в алюминии. Переходные металлы, например Ti, Cr и Zr, также образуют с медью системы с очень ограниченной растворимостью. Бор имеет малую предельную растворимость в алюминии и меди, а растворимость углерода в этих металлах значительно меньше, чем бора.
С понижением температуры уменьшается растворимость переходных металлов в твердых растворах на основе алюминия и меди, что является основой для термической обработки сплавов и последующего повышения твердости и прочности за счет дисперсионного твердения. Однако первичные интерметаллиды, образующиеся в процессе кристаллизации, имеют игольчатую морфологию и склонны к укрупнению [8].
Наиболее перспективны, на наш взгляд, для повышения жаропрочности и термостойкости алюминия и меди растворимые в них тугоплавкие высокомодульные фазы, синтезированные в расплаве и не содержащие металла растворителя (бориды и карбиды ПМ) или сложно построенные жаропрочные фазы с высокой электропроводностью, например углеродсодержащая боридная фаза C2Al3B48. Исходными компонентами для синтеза таких фаз в расплавах Al и Cu являются переходные металлы и неметаллические элементы (B, C), имеющие химическое сродство к переходным металлам выше, чем к алюминию и меди. О возможности синтеза тугоплавких керамических частиц в расплавах алюминия и меди судили по величине термодинамического потенциала реакций их образования. Результаты расчетов представлены в табл. 1.
Значения AG°T использовали для оценки химического сродства реагирующих веществ и прочности продуктов реакции при высоких температурах, а также для расчета значений константы равновесия соответствующих реакций.
Анализ полученных зависимостей AG°T=f(T) и lg K=f(T) показывает возможность синтеза тугоплавких упрочняющих фаз в широком интервале температур. В системе Al-C-(Zr, Ti) наиболее предпочтительны реакции образования карбидов циркония и титана, при этом выше 1000 К исключается возможность образования карбида алюминия, который является гидрофильным и снижает адгезионную связь наполнителя и матрицы. Например, в системе Al-C-B высоки потенциальные возможности образования боридов алюминия и маловероятно образо- – 417 –
Таблица 1. Температурные зависимости энергии Гиббса и константы равновесия реакций образования некоторых упрочняющих фаз
4AlB12+2C=C2Al3B48+Al с образованием «алмазоподобного бора» (C2Al3B48), что подтверждается многими исследованиями (см., например, [10]).
Медь не карбидообразующий элемент, поэтому в системе Cu-C-переходный металл возможно образование карбидов по реакциям 1, 2, 4 и 5.
Возможность применения карбидов и боридов для создания новых композиционных материалов требует решения проблемы совместимости их с расплавом алюминия и меди. Известно достаточно большое количество работ по смачиваемости медью и алюминием неметаллических металлоподобных соединений [11-13]. В этих работах смачивание карбидов и боридов металлическими расплавами исследовали методом лежащей капли. Некоторые экспериментальные данные цитируемых авторов и полученные в настоящей работе представлены на рис. 1 (а, б). Медь, химически не взаимодействующая с карбидами (TiC, B4C) и боридами (TiB2, ZrB2), не смачивает эти тугоплавкие соединения в широком интервале температур. Значения краевых углов составляют 130-140°. Карбид и борид хрома смачиваются расплавленной медью. При 1100 °С краевой угол смачивания медью Cr 3 C 2 и CrB 2 составляет 45 и 25° соответственно, при дальнейшем повышении температуры происходит плавное уменьшение углов смачивания (рис. 1).
Расплав алюминия до температуры 900-950 °С не смачивает карбиды титана, циркония и бора, а при температурах выше 1000-1050 °С краевой угол смачивания резко уменьшается до нуля (рис. 2). Такая зависимость обнаружена в ряде работ (см., например, [11]), что связано с возгонкой пленки оксида алюминия на поверхности капли и интенсификацией химических реакций на межфазной границе алюминия с компонентами твердой фазы.
Работа адгезии расплава меди к карбидам титана и циркония, определенная по известному соотношению Wa=σж(1+cosθ) при температурах 1100-1350 °С, низка и не превышает 300 МДж/м2 [11], что указывает на отсутствие химического взаимодействия на границе раздела фаз. Поэтому для обеспечения необходимой прочности композиционного материала систем Cu-TiC(ZrC) и Cu-TiB 2 (ZrB 2 ) в расплав меди необходимо вводить адгезионно-активные компоненты, напри- – 418 –
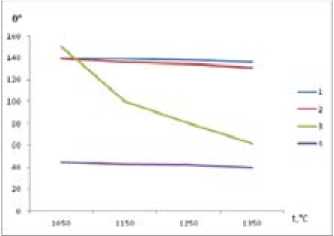
а)
Рис. 1. Температурная зависимость краевого угла смачивания медью: а) карбидов (1 – B 4 C; 2 – TiC; 4 – Cr 3 C 2 ) и расплавом Cu+2Cr карбида титана – 3 [11] и б) боридов [12]: 1 – ZrB 2 , 2 – TiB 2 , 3 – W 2 B 5 , 4 – CrB 2 .
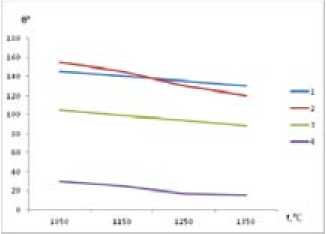
б)
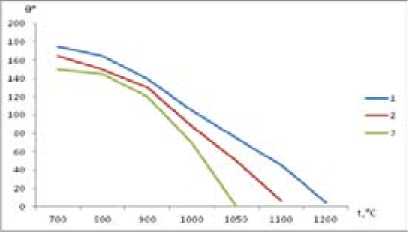
Рис. 2. Температурная зависимость краевого угла смачивания карбидов алюминием: 1 – B 4 C, 2 – ZrC, 3 – TiC
мер Cr. Расплав системы Cu – 2 мас. % Cr смачивает карбид титана при температурах выше 1200 °С (см. рис. 1, а, кривая 2). Упрочнение меди частицами Cr3C2 и CrB2 возможно без дополнительного введения в её состав адгезионно-активных веществ.
При образовании армирующих частиц в расплаве алюминия необходимо не только улучшить смачивание частиц карбидов жидкой фазой, но и предотвратить их химическое взаимодействие с расплавом алюминия. Это может быть достигнуто введением в расплав межфазноактивной добавки, например стронция, который снижает σ А-Ме и практически не растворяется в алюминии.
Таким образом, предварительные исследования указывают на возможность целенаправленного синтеза карбидных и боридных упрочняющих частиц непосредственно в процессе литья. В следующей серии опытов оценили свойства и эффективность разработанных литых металломатричных композиционных материалов электротехнического назначения.
Опыты проводили на образцах, вырезанных из слитков сплавов систем Al (Cu) – армирующие частицы, приготовленных в индукционной тигельной печи.
В табл. 2 приведены свойства литых образцов из композиционного сплава системы Cu-TiC в сравнении со свойствами литой и деформированной меди, а на рис. 3 — микроструктура композиционного материала.
Таблица 2. Механические свойства и электропроводность алюминия и композиционных материалов на основе алюминия.
Содержание упрочняющей фазы |
Предел прочности σВ, кгс/мм2 |
Относительное удлинение δ, % |
Удельное электросопротивление, Ом ∙ мм2/м |
|||
В литом состоянии |
После прокатки |
В литом состоянии |
После прокатки |
В литом состоянии |
После прокатки |
|
Исходный алюминий |
6,9 |
14,0 |
39,6 |
12,0 |
0,0301 |
- |
0,15 % |
8,8 |
17,2 |
20,4 |
7,0 |
0,0290 |
0,0293 |
0,30 % |
9,0 |
17,9 |
20,0 |
6,1 |
0,0294 |
0,0299 |
0,60 % |
11,1 |
- |
5,4 |
- |
0,0345 |
- |
Таблица 3. Механические свойства меди и композиционного материала на основе меди
Состояние материала |
σ В , МПа |
Δ, % |
ψ |
НВ |
Исходное литое состояние технической меди |
160 |
25 |
- |
40 |
Литой композиционный материал системы Cu-TiC |
350 |
10 |
16 |
- |
Проволока из технической меди (суммарная деформация 90 %) |
450 |
3 |
35 |
125 |
Из табл. 3 следует, что прочность композиционного материала по сравнению с исходной медью возросла более чем в два раза, что свидетельствует о надежной связи между составляющими материала. Увеличение сцепления между твердой и жидкой фазами обусловлено легированием меди поверхностно-активным хромом.
На рис. 3 показано, как улучшение смачивания, отражающего изменение межфазной энергии, влияет на структуру композита. Видно равномерное распределение упрочняющих частиц в объеме матрицы, что благоприятно сказывается на свойствах композита.
В техническом алюминии, применяемом в качестве матричного компонента, содержатся примеси Ti и V, которые существенно уменьшают электропроводность композиционного материала. Введение бора в расплав алюминия в количестве, равном половине весового содержания Ti и V, способствует образованию мелкодисперсных соединений TiB2 и VB2, которые нерастворимы в жидком и твердом алюминии и в меньшей степени оказывают влияние на электропроводность. Добавление бора в большем количестве, чем необходимо для вывода Ti и V, приводит к образованию частиц C 2 Al 3 B 48 по вышеуказанной реакции.
Для выяснения влияния синтезированных частиц «алмазоподобного бора» на электропроводность и физико-механические свойства из полученных литых КМ вырезали образцы, микроструктура которых изображена на рис. 4 (а, б).
Видно равномерное распределение упрочняющих частиц ≤ 1-2 мкм, преобладающий размер частиц менее 1 мкм, и в отличие от известных решений полностью отсутствуют включения игольчатой морфологии.
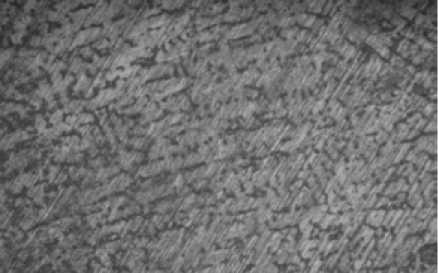
Рис. 3. Микроструктура КМ на основе меди, упрочненного дискретными частицами TiC (х200)
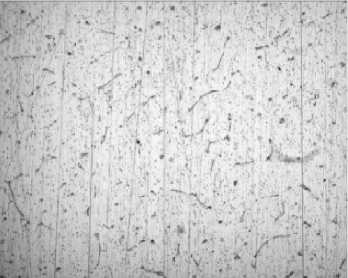
а) при 0,15 мас. % боридной фазы
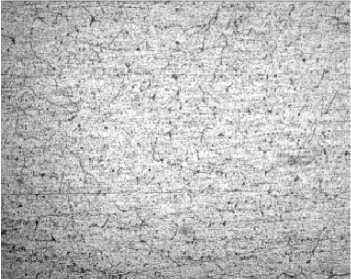
б) при 0,3 мас. % боридной фазы
Рис. 4. Микроструктура КМ на основе алюминия, упрочненного частицами C 2 AI 3 B 48 при увеличении х200
Механические свойства и электропроводность полученных КМ в литом состоянии и после прокатки (суммарная деформация 60 %) приведены в табл. 2.
С увеличением содержания керамических частиц в КМ до 0,3 мас. % предел прочности на разрыв (оВ) увеличивается более чем на 30 %, а после прокатки - более чем в 2 раза по сравнению с деформированным техническим алюминием. Это объясняется высокой адгезионной связью частиц C2Al3B48, когерентных с матрицей и кристалографической совместимостью со сплавом матрицы. Следует отметить, что даже после высокой степени обжатия (более 60 %) композитный материал сохраняет достаточную пластичность (5=6-7 %). При увеличении содержания керамических частиц в КМ до 0,6 масс.% предел прочности увеличивается более чем на 60 %, однако относительное удлинение снижается до 5,4 % и существенно увеличивается электросопротивление, что неприемлемо для композиционных сплавов электротехнического назначения, поэтому содержание упрочняющих фаз в композиционном материале не должно превышать 0,3 мас. %. Существенным отличием от всех известных композиционных сплавов электротехнического назначения разработанный нами материал наряду с повышенной прочностью имеет высокую электропроводность, соответствующую стандартам для проводников электрического тока. При обработке расплава технического алюминия бором электропровод- ность повышается на 7 % и остается достаточно высокой при упрочнении матрицы дисперсными частицами C2Al3B48. Известно, что карбид бора является полупроводником, однако высокая электропроводность в системе C-Al-B зависит от декомпенсации ковалентных связей между атомами бора и углерода из-за наличия атомов алюминия и появления дополнительных зон проводимости [13].
Таким образом, экспериментальные закономерности значительно расширяют сведения о возможности получения литых металломатричных композиционных материалов, армированных частицами, синтезированными в расплаве, и их применения для изделий электротехнического назначения.