Low-toxic core sands for mould cores pattern - making in a heated rig
Автор: Evstifeyev Evgeny N., Savuskan Tatyana N., Lopatukhina Tatyana A.
Журнал: Журнал Сибирского федерального университета. Серия: Техника и технологии @technologies-sfu
Статья в выпуске: 8 т.7, 2014 года.
Бесплатный доступ
The innovative method of physical and chemical analysis was first used for core sand research that, unlike the method of tests and errors, radically shortens the scope of an experimental work in order to find the optimal core sands compoundings. Some results of the investigations based on the physical and chemical analysis for obtaining the compoundings of low - toxic core sands using hot hardening of a new generation without containing resins are presented. Such compoundings impart more advanced technical, economical and ecological indicators to the process of cores moulding using a heated rig. The development of such mixtures relies on low - toxic technical lignosulphonates (LTTLS) binders containing a modifier. The mixture of vat residues of organic synthesis in water having volume relationship in the proportion of 6:1 was used as a modifier. The search of technological additions set increasing LTTLS binder properties was conducted. To put into practice the declared purpose we investigated the additions of marshalit, boric acid and iron minium influences on the mixtures properties. It was demonstrated that only the joint use of the above - mentioned three technological additions may result in an effective influence of each of them on mixtures properties. An additional introduction of «KO» solution in kerosene turned out to be effective, as well. The given research results lie in presenting mixtures compoundings based on LTTLS having physical and mechanical indicators usually characterizing resins mixtures. Some mixtures containing the additions of a wasted zinc - chromium catalyst having good ecological properties and being applicable to the cores molding of a wide range of pig iron and steel castings were elaborated.
Core sand, heated / cold rig, low-toxic technical lignosulphonate binders, mould cores pattern-making, technological additions, breaking strength compounding
Короткий адрес: https://sciup.org/146114917
IDR: 146114917
Текст научной статьи Low-toxic core sands for mould cores pattern - making in a heated rig
hardening technology is the application, in the majority of cases, of polymerization catalysts of binders. As a result of this, there appears the problem of perfecting technical, economic, sanitary and hygienic indicators for solving the following tasks:
-
– minimization of toxic synthetic resins content or its complete exclusion from the components of core sand;
-
– reduction of binders expenditures several times as little;
-
– improvement of sanitary and hygienic labour conditions at the foundry throughout different stages of cores moulding.
We should remark that the problem of indicators perfecting may be solved in different ways including:
-
– combination of synthetic resins;
-
– choice of special catalysts hot hardening;
-
– development of principally new low – toxic binding compositions based on low – toxic technical lignosulphonates (LTTLS) and technological additions to them that improve physical, mechanical and technological properties of mixtures produced.
The application of the first and the second ways of solving the problem of indicators improvement makes it possible to reduce the toxic resins content in mixtures but, nevertheless, such an approach cannot radically solve the problem of bettering sanitary and hygienic labour conditions. That’s why the development of low-toxic binding compositions having the resins properties is very actual because it envisages the prospects of appearing new generation of core sands that will meet the ecological requirements of modern production.
Initial substance and research methods
In our research we have used LTTLS with different bases – sodium, sodium together with calcium, ammonium – that represent different pulp and paper mills waste products.
We have applied vat residues of organic synthesis of different chemical productions as a modifier of technical lignosulphonate. We have limited the scope of our research objects taking into account the grounds that vat residues of organic synthesis should contain substances that are able to form cross chemical bonds between macromolecules of LTTLS under the conditions of heating core sand. Such substances, in particular, may be found in the production of vat residues of 1.4-butandiol, γ-butirolacton fabrications that were applied in the process of obtaining a new modifier representing a mixture of vat residues of organic synthesis [1]. The mentioned mixture was dissolved in water in volume relationship looking like vat residues of organic synthesis: Н2О = 6:1 for preparing a modifier.
Bonding LTTLS [2] was prepared by mixing LTTLS with a modifier of vat residues of organic synthesis for 3 – 5 minutes to achieve a fluidity state. The modifier sharply decreases viscosity of technical lignosulphonate and that results in stabilizing a colloid system increasing binder covering properties.
Core sands were prepared in laboratory runners of LM – 1 model made of three things: 1) quarts sand with 1K02A brand from Verkhne-Dneprovsk sand-pit; 2) technological additions and 3) low-toxic lignosulphonate binder.
Some samples in the form the eights and cylinders for conducting testing were produced from a mixture by its packing with three blows of laboratory impact testing machine of LU-type.
Standard samples were dried at temperature of 250±10 °C in the drying laboratory cabinet of SNOL-3.5.3.5.3.5/3-M2 type with an automatic temperature control. To define core strength in a hot state the standard sample in the form of an eight was, first, heated for 5 minutes at the temperature of 250 °C, then, it was rapidly placed (during 10 – 15 seconds) into a clam device of a breakage machine of LRU-1 type. To research physical, mechanical and technological mixtures properties we have used laboratory equipment of «Tsentrozap» firm.
Core sands research based an the initial and modified technical lignosulphonates
Some facts concerning «hot» strength of core sands based on the initial and modified technical lignosulphonates (vat residues of the organic synthesis) amounting to 15 % of different pulp and paper mills are given in table 1.
As we can see from table 1cores strength in a hot state depends on the base kind and it decreases in the following sequence for initial technical lignosulphonates:
NH 4 + > Na+ > (Na+ + Ca2+)
For modified technical lignosulphonates the dependence of cores strength on the base kind is quite reverse [3]:
(Na+ + Ca2+) > Na+ > NH 4 +
Such relationship does not refer to the concentrates of Kondopoga pulp and paper mill because they contain a great amount of different kinds of additions such as nutrient salts, neutralizing substances, foam suppressors that are applied in yeast growing and in, the long run, they contain yeasts itself.
Having analysed table 1 data we may conclude that it is the most preferable to use modified concentrates of Syas and Kama pulp and paper mill to mould cores in a hot rig. The foundry binders properties based on technical lignosulphonates concentrates depend mostly on the modifier origin. Low «hot» cores strength complicates the task of developing low-toxic mixture of hot hardening using exclusively low-toxic lignosulphonates. To solve this task we should choose such a set of technological
Table 1. Strength of Cores in a Hot State Produced of Core Sand Based on Initial and Modified Technical Lignosulphonates of Different Pulp and Paper Mills
Water influence on the sands properties
Low – toxic lignosulphonate binder has a viscosity according to VZ-4 over the range of 80100 s. This binder is of little use for molding cores in a hot rig, such technology demands a binger having viscosity of 25-60 s (according to VZ-4). That’ s why we turned our attention, first of all, to the research of water amount influence on LTTLS based on technological and physico-mechanical mixtures properties. LTTLS, together with water in the mixtures compositions, reached 5 %, the time of binder mixing with sand amounting to 3 minutes. The obtained results are presented in Fig. 1.
Figure 1 shows that even a small amount of water addition to LTTLS sharply reduces binder viscosity. So, the addition of only 6 % of water reduces binder viscosity 1.5 times as much. However, this did not result in the reduction of dry substances content in LTTLS. At low viscosity (45 s according to VZ-4) low-toxic lignosulphonate binder preserved high content of dry substances amounting to 54 %. These two mutually exclusive indicators turned out to be successfully combined in low-toxic lignosulphonate. Taking this fact into consideration we may admit that low-toxic lignosulphonate binder is that very substance that having a low viscosity, on one hand, imparts necessary wet strength to a hot hardening mixture, but, one the other hand, having a great amount of dry substances this kind of a binder will add a sufficient, for the process, strength to the hardened cores.
It should be underlined that diluting LTTLS with water did not result in falling hardened cores strength (Fig. 1.). On the contrary, 5 and 10-minute samples strength has slightly increased. We might explain this in the following way: increasing cores strength is conditioned by the increase of contacts number of low-viscous binder with the grains of quarts sand and the relief of stress relaxation owing to the thickness diminishing of low-toxic lignosulphonate film. But low-toxic lignosulphonate binder imparts low breaking strength to the mould cores (1.1 – 1.4 MPa). «Hot» cores strength is low, too, amounting only to 0.3 MPa. Consequently, this means that low-toxic lignosulphonate greatly yields to resins.
Finally, as a result of many experiments conducted we have found an effective set of technological additions looking like this: marshalit – boric acid – iron minium, this
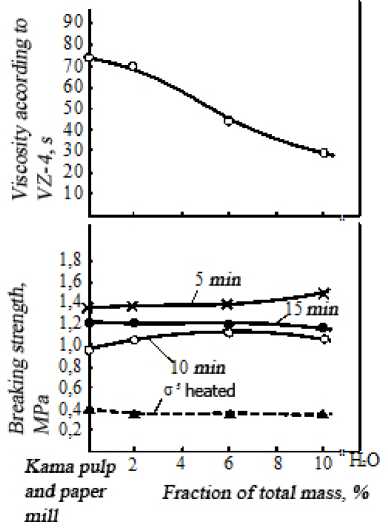
Fig. 1.Water influence on low-toxic lignosulphonate binder viscosity and strength of standard cores hardened at the temperature of (250±10), °С
very sequence giving the possibility to the mixture characteristics based on LTTLS to approach the properties of resins compositions of hot hardening.
Marshalit influence on mixtures properties
The above-described mixtures obtained on the basis of low-viscous LTTLS had «wetness» effect that is they possessed seemingly increased humidity in spite of the fact that humidity content in the mixture was close to the norm being over the rouge of 1.8-2.0 %. Besides that, we were able to watch the phenomenon of adhesion of these mixtures to the metallic rig and hands skin.
To reduce these negative effects we used marshalit addition (dustlike quartz SiO2). Mixtures compositions contained 5 % LTTLS having viscosity if 44 s according to VZ-4. The carried out investigations proved that the marshalit quantity increase reduces mixtures compressive strength. This phenomenon is directly linked with mixtures fluidity increase.
As a rule, mixtures based on LTTLS are rather «heavy» to the touch. Marshalit additions make mixtures «lighter» and noticeably reduce the «wetness» sensation. It follows from above-mentioned statement that marshalit betters technological potentialities of mixtures based on LTTLS and makes them more suitable for cores moulding in a hot rig.
Marshalit addition to the mixtures containing LTTLS appeared to be useful not only for obtaining their technological properties but physic-mechanical ones, as well. The strength of 5 and 10 – minute samples in comparison with the samples of LTTLS mixtures without marshalit increased to 1.56 and 1.20 MPa, respectively. Cores strength in a hot state increased to 0.4 MPa, too.
Having analysed the results of our investigations we may conclude that marshalit addition to mixtures with LTTLS is very effective and may serve as the basis for its combining with other technological additions. Optimal marshalit content in a mixture amounts to 1-2 %.
Boric acid influence on mixtures properties
Boric acid choice (Н 3 ВО 3 ) as a technological addition to the mixtures with LTTLS is connected with its ability to melt at the temperature of 170.9 °C. At heating boric acid is gradually losing water and is changed, first, into metaboric acid (НВО 2 ) and, then, into boric anhydride (В 2 О 3 ). Going Н 3 ВО 3 into НВО2 begins at the temperature about 100 °C.
Melting and caking of boric acid results in oxyborate polymeric complexes formation. This enables to get increasing cores strength in a hot state. However, considerable increase of boric acid in the mixture composition causes worsening the process of shaking the cores out of casting. That’s why the optimal boric acid content in the mixture should not exceed 0.3-0.5 %. Boric acid in this concentration interval influences badly the cores strength in a hot state. It may be explained by the fact that at cores cooling boric acid crystallization in the places of its localization causes immediate stresses in the film structure of LTTLS. After this a sharp reduction of cooled cores strength follows.
Iron minium influence on mixtures properties
Iron minium (Fe3O4) as an addition to core sand was selected taking into consideration its ability to produce heat. Thus, such an addition is expected to speed up the process cores drying.
The research results demonstrate that iron minium addition sharply reduces 3-minute samples strength. Loss of cores strength takes place, in our opinion, because heat energy is, first of all, – 952 – accumulated by iron minium particles but not by binders. Under the conditions of short duration cores heating the particles of Fe3O4 are unable to become an additional conductor of a heat energy.
Iron minium addition influence starts to appear only at 10-minute sample withstanding the temperature of (250±10) °C. Core strength becomes 1.7 times as much. If 10 – minute core withstanding in the drying cabinet corresponds to its 2-3-minute hardening in the hot rig, then we have to admit that the Fe 3 O 4 addition is useful. In the mixtures iron minium fraction should not exceed more than 0.5 %.
Compoundings of mixtures based on LTTLS and a set of mixtures in the form of SiO2 – H3BO3 – Fe3O4
Our investigations proved the necessity of joint application of three types of technological additions. It is this approach that causes an effective influence of each of the additions on the physico-mechanical and technological mixtures properties. The above-mentioned set of technological additions of granular substances provides the mould cores with breaking strength increase up to 1.8-2.3 MPa.
High cores strength may be obtained at the content of H 3 BO 3 amounting in the mixtures up to 0.8-1.0 %. Such amount of boric acid seems to be not achievable in the real production. Taking this conclusion into account we should orient ourselves to obtaining cores strength of 1.60-1.65 MPa that corresponds to the fraction of boric acid in the mixure reaching 0.3-0.4 %.
In the final analysis we’ve got a basic compounding of core sand for a heated rig. Its composition includes the following substances in percentage:
Quartz sand100
Marshalit2.0
Iron minium0.5
Boric acid0.4
LTTLS binder
5.5
While using this mixture we’ll have maximum core strength that does not exceed 1.60 MPa. Such strength is sufficient only for cores of a simple configuration. Besides, it is desirable to perfect its technological properties: to better fluidity, to increase survivability, to reduce hydroscopity.
All our further research was aimed at mixture finishing off according to the requirements of fabricating complicated cores.
At choosing casting binder of «KO» type as a technological addition we took into consideration its abilities to be effectively combined with LTTLS binder. To increase the mixture fluidity casting binder of «KO» type was diluted with kerosene in the volume relationship of 3:2.The results obtained are given in Fig. 2.
Fig. 2 shows that if a mixture has 0.25-0.35 % of «KO» solution in kerosene, then 10 and 15-minute isotherms of strength reach their maximum values of 2.85 and 2.63 MPa, respectively. The subsequent increase of «KO» solution content reduces the strength of these cores.
It is important to note that the speed of cores hardening after introducing a technological «KO»-kerosene addition type into the mixture did not reduce. Sufficiently high level of cores «hot» strength is a good proof of our approach. Furthermore, such an addition reduces mixtures drying in the nozzles and decreases cores hydroscopity.
It is significant to have the compounding of a mixture with minimal additions content that provides the mixture with sufficient physic-mechanical properties and satisfactory technological properties displayed in a real production.
Our investigations enabled us to find the working limits in percentage for all mixture compounding components.
Quartz sand 100
Marshalit 1.5-2.0
Iron minium 0.4-0.5
Boric acid 0.3-0.5
LTTLS binder 4.5-5.5
«KO» solution in kerosene 0.25-0.35
The ingredients mixture content is presented according to the sequence of their introduction into the runners for mixture preparing.
Physical and mechanical mixture properties are the following:
Humidity, % 1.8-2.1
Gas permeability, units. 200
Breaking strength, MPa, of standard simples in a hot state after 5 minutes at the temperature of
250±10 °C 0.5-0.6
Breaking strength, MPa, of standard samples hardened at the temperature of 250±10 °C during
5 minutes 1.4-1.7
10 minutes 2.1-2.6
15 minutes 1.8-2.4
Compressive strength of a wet mixture, kPa 3.0-4.0
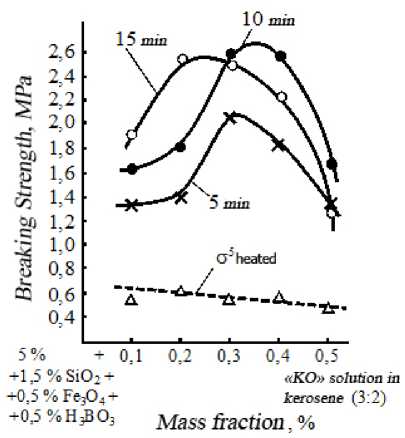
Fig. 2. The dependence of breaking strength of standard cores made of mixtures with LTTLS and the additions set of SiO – Н 3 ВО – Fe 3 О 4 on their content of «KO» solution in kerosene
Having analysed the above – described mixtures properties we may state that an effective set of technological additions has been obtained and it provides mixtures based on LTTLS with satisfactory fluidity and sufficiently high breaking strength in hot and cold states.
VPK – 402 polyelectrolyte additions influence on the mixtures survivability
Good results of increasing mixture survivability are connected with some tested technological additions (bishofite, the solutions of CaCl 2 , NaNO 3 and some others), among which the best effect producing polyelectrolyte of VPK-402 type (poly N-dimetil-3.5-dimetilenpiperediniya chloride). This polyelectrolyte is completely diluted in water, the most inferior alcohol, the solutions of acids and alkalies, it is not inflammable, not dangerously explosive, not toxic and does not have any unpleasant odour. We have investigated this electrolyte influence on mould cores strength and their hygroscopicity. The results obtained look like the following.
If we increase the percentage to polyelectrolyte in a mixture up to 0.3 %, the strength of 15-minute samples, first, decreases, then, sharply increases and after reaching 0.5 % the mould cores strength, in comparison with an initial mixture without VPK-402, raises 0.4 MPa as much and reaches 2.5 MPa. It is also important to emphasize that such addition favours gradual increase of «hot» cores strength up to 0.8 MPa.
VPK-402 substance imparts to the mixture an ability to withstand drying up from its surface. Survivability of the developed mixture increases 3-4 times as much and as a result of this under the direct contact with the atmosphere air the mixture can be stored without any noticeable changes during 5-6 hours.
Mixture compounding based on LTTLS having the indicators of resins mixtures
As it was shown above, the created set of technological additions in the form of such sequence as «marshalit – boric acid – iron minium» functions effectively; if it includes «KO» binder, the latter, unfortunately, deteriorating the ecological significance of a developed compounding. That’s why we had to continue the search of substances increasing strength of LTTLS containing moulding cores using molecules lacing of lignosulphonates.
The waste products of Novocherkassk synthetic mill in the form of zinc – chromium catalyst were used as a LTTLS lacing agent, the latter, in terms of oxides, having the following composition in percentage [4]:
Zinc oxide Basis
Chromium oxide (III) 29-31
Tungsten oxide 0.05-0.1
Alkali metals oxides, not more than 0.04
Zinc-chromium catalyst waste products in the form of grey powder obtained at methanol production comprise many tons. The powder participates in ion exchange reactions with LTTLS forming the element having a mesh structure that increases mould cores strength.
There existed the whole procedure of mould cores mixtures preparation involved in our experiments. First, quartz sand was being mixed with technological additions for 1 minute. Then, – 955 –
LTTLS was introduced in percentage of 5 % of mixture total amount and, at last, the process of intermingling was taking place for 3 minutes more.
Table 2 introduces the compoudings of the developed mould cores mixtures №№ 1-5 in comparison with the composition of mixture № 6, all the mixtures being obtained using LTTLS without any technological additions. Physical and mechanical properties of mixtures are given in table 3.
As we may conclude according to table 3 a mixture with the developed set of technological additions as compared to a mixture without them provides 2-2.27 as much increase of cores in a hot state strength. It is especially important that such increase of «hot» strength of cores has been achieved without resins application. Mould cores fabricated of brought forward mixture have «hot» strength close to that of resins cores, giving the possibility to carry out their hardening in the similar modes.
Table 3 shows as well that the developed mixture allows us to increase cores strength in a cold state 1.5-2.0 times as much.
In the process of mould cores fabricating in a heated rig the melt of boric acid, partially, dissolves the oxides of zinc-chromium catalyst waste producing the corresponding salts that lace them supplementary by means of the ion exchange reactions with the macromolecules of LTTLS. Such phenomenon results in the cores strength increase both in hot and cold states.
Table 2. Mixtures based on LTTLS and a set of technological additions
Names of mixtures ingredients |
Content of ingredients in mixtures in percentage |
|||||
№ 1 |
№ 2 |
№ 3 |
№ 4 |
№ 5 |
№ 6 |
|
Quartz sand |
94.8 |
93.3 |
91.2 |
89.1 |
87.6 |
95.0 |
Zinc-chromium catalyst waste products |
0.7 |
0.8 |
1.0 |
1.2 |
1.3 |
- |
Marshalit |
0.5 |
1.0 |
1.5 |
2.0 |
2.5 |
- |
Iron minium |
0.1 |
0.3 |
0.5 |
0.7 |
0.9 |
- |
Boric acid |
0.4 |
0.6 |
0.8 |
1.0 |
1.2 |
- |
LTTLS binder |
3.5 |
4.0 |
5.0 |
6.0 |
6.5 |
5.0 |
Table 3. Physical and mechanical properties of cores mixtures based on LTTLS
Names of mixtures properties |
Mixtures properties indicators |
|||||
№ 1 |
№ 2 |
№ 3 |
№ 4 |
№ 5 |
№ 6 |
|
Wet mixtures compression strength, kPa |
4.5 |
4.7 |
5.1 |
5.6 |
6.0 |
4.4 |
Gas impermeability of wet mixture, units |
163 |
156 |
146 |
143 |
134 |
163 |
Breaking strength, MPa, of standard samples in a hot state after 5-minute hardening at the temperature of 250 ± 10 °C |
0.56 |
0.69 |
0.72 |
0.86 |
0.83 |
0.32 |
Breaking strength, MPa, of standard samples after drying at the temperature of 250 ± 10 °C for 5 min |
1.42 |
1.88 |
1.93 |
2.12 |
2.06 |
1.20 |
10 min |
1.65 |
2.16 |
2.42 |
2.87 |
2.90 |
1.46 |
15 min |
1.78 |
2.22 |
2.94 |
3.20 |
3.23 |
1.53 |
The put forward mixture compounding has the following composition in percentage [4]:
LTTLS binder 4.0-6.0
Wasted zinc-chromium catalyst 0.8-1.2
Boric acid 0.6-1.0
Marshalit 1.0-2.0
Iron minium 0.3-0.7
Quarts sand the rest
The optimal content of a wasted zinc-chromium catalyst in the mixture ranges over 0.8 to 1.2 %. If its content in the mixture is less than 0.8 % and higher than 1.2 %, the cores strength in a hot state reduces.
The optimal boric acid content in the mixture is 0.6-1.0 %. If the boric acid content is less than 0.6 %, then the strength of the cores in a cold state reduces, but when it is higher than 1.0 %, then the compressive strength of a wet mixture increases, its sand-blast fluidity worsening.
The mixture based on LTTLS with the proposed technological additions was tested in the foundry of «Zaporozharmatura» PO with using on automaton of 4532 B model for moulding «Corpus DU-15» cores. The cores hardening mode did not change that is the hardening time was 60 seconds, hardening temperature-270 °C. All cores were moulded according to the technological requirements and quality. They had smooth surface, they were sharp-edged and they demonstrated manipulation strength. To reduce cores hydroscopity we used a special coating on an organic basis that provided cores with a prolonged storage and reduced casting burnt-on sand.
Conclusion
-
1. The research stated the influence of marshalit, boric acid and iron minium on the mixtures properties and presented a set of technological additions increasing LTTLS bonding properties up to those of the resins level. In the process of research it was proved that only the joint use of three technological additions works well for effective putting into practice the influence of each of the additions on physical, mechanical and technological mixtures properties. A supplementary introduction of an addition in the form of «KO» binder solution in kerosene turned out to be very effective. Isotherms of strength of 10 and 15 minute-samples reached their maximum of 2.48 and 2.58 MPa, respectively. As a result of the research carried out we have the development of fixed mixture compounding based on LTTLS with physical and mechanical indicators typical of resins mixtures.
-
2. The developed mixtures compoundings with the addition of wasted zinc-chromium catalyst resulted in the possibility of excluding from the compounding the mixture of a toxic «KO» binder. The worked out mixtures compositions are characterized by having physical and mechanical inticators typical to those of resins mixtures. In addition to these positive moments the advanced mixtures compositions meet the ecological requirements in their application to modern foundry.