Математическое моделирование изменения прочностных характеристик микролегированных сталей в процессе термодеформационной обработки
Автор: Чикишев Денис Николаевич, Пожидаева Евгения Борисовна
Журнал: Известия Самарского научного центра Российской академии наук @izvestiya-ssc
Рубрика: Современные наукоемкие инновационные технологии
Статья в выпуске: 4-3 т.16, 2014 года.
Бесплатный доступ
Выполнено компьютерное моделирование изменения прочностных характеристик микролегированных сталей на основе метода конечных элементов и нейронных сетей. Проанализировано влияние химических элементов и технологических параметров термомеханической обработки на механические свойства трубной стали в интервале толщин 15-25 мм.
Термодеформационная обработка, прочность, деформация, микролегированная сталь, нейронная сеть, структурно-фазовые превращения, математическое моделирование
Короткий адрес: https://sciup.org/148203274
IDR: 148203274
Текст научной статьи Математическое моделирование изменения прочностных характеристик микролегированных сталей в процессе термодеформационной обработки
является наиболее предпочтительной, т.к. при расчете сопротивления металла деформации используются реальные параметры процесса (температура, степень и скорость деформации). Однако при этом требуется разработка новой методики определения СМД, а также разработка альтернативного подхода к определению прочностных характеристик микролегированных сталей различных классов прочности, широко используемых при производстве толстолистового проката. Принципы нейросетевого моделирования, положенные в основу новой методики определения СМД, позволят исследовать изменение прочностных характеристик микролегированных сталей с учетом влияния технологических параметров термомеханической обработки, а также химического состава деформируемого материала и температур структурно-фазовых превращений.
Математическое моделирование изменения прочностных характеристик микроле-гированных сталей в процессе термодеформационной обработки. Для детального анализа влияния микролегирующих элементов на механические свойства трубных сталей эффективным является применение нейросетевого моделирования (дополнительный модуль SNN программного пакета Statistica). Модель учитывает влияние следующих параметров процесса: химический состав стали (C, Si, Mn, S, P, Cr, Ni, Cu, Al, N, V, Ti, Nb, Mo, B), параметры процесса (температура нагрева сляба, толщина сляба, толщина листа, количество проходов на 1-ой стадии прокатки, температура начала и конца 1-ой стадии прокатки, толщина промежуточного раската, температура начала и конца 2-ой стадии прокатки, температура начала и конца ускоренного охлаждения, скорость охлаждения. Модель позволяет рассчитывать предел текучести, временное сопротивление разрыву и относительное удлинение стали. Анализ влияния микролегирующих элементов на механические свойства проводили следующим образом: в нейросеть задавали базовый химический состав (табл. 1) и базовые параметры процесса (табл. 2), а затем варьировали один из химических элементов (Nb, V, Ti, Cr, Ni, Cu, Mo, B) при неизменных остальных условиях процесса.
Таблица 1. Базовый химический состав
C |
Si |
Mn |
S |
P |
Cr |
Ni |
Cu |
Al |
N |
V |
Ti |
Nb |
Mo |
B |
0,07 |
0,32 |
1,67 |
0,002 |
0,009 |
0,05 |
0,26 |
0,14 |
0,038 |
0,005 |
0,045 |
0,019 |
0,048 |
0 |
0,0004 |
Таблица 2. Базовые технологические параметры процесса
Температура нагрева сляба, 0С |
Толщина сляба, мм |
Толщина листа, мм |
Количество проходов на 1 стадии |
Температура начала 1 стадии, 0С |
Температура конца 1 стадии, 0С |
Толщина раската, мм |
Температура начала 2 стадии, 0С |
|
1210 |
300 |
20 |
10 |
1050 |
1030 |
90 |
860 |
|
температура конца 2 стадии, 0С |
температура начала ускоренного охлаждения, |
температура конца ускоренного охлаждения, 0С |
скорость охлаждения, 0С/сек |
|||||
855 |
820 |
600 |
16 |
Анализ и обобщение полученных данных. Ниобий повышает предел текучести на 3540 МПа и временное сопротивление разрыву стали на 15-20 МПа (рис. 1а), увеличивает относительное удлинение на 1,5-2,0%. Ванадий увеличивает предел текучести на 20-25 МПа и временное сопротивление разрыву на 60-65 МПа (рис. 1б), снижает относительное удлинение на 1%.
Титан увеличивает предел текучести на 1015 МПа и временное сопротивление разрыву на 25-30 МПа (рис. 2а), снижает относительное удлинение на 1%. Хром увеличивает предел текучести на 20-25 МПа и временное сопротивление разрыву на 40-45 МПа (рис. 2б), снижает относительное удлинение на 3%.
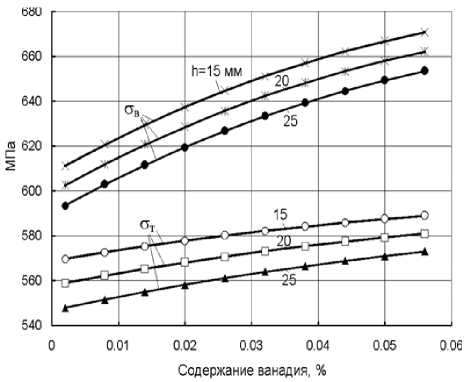
б)
Рис. 1. Влияние содержания Nb (а) и V(б) на предел текучести и временное сопротивление разрыву с учетом толщины листа (h)
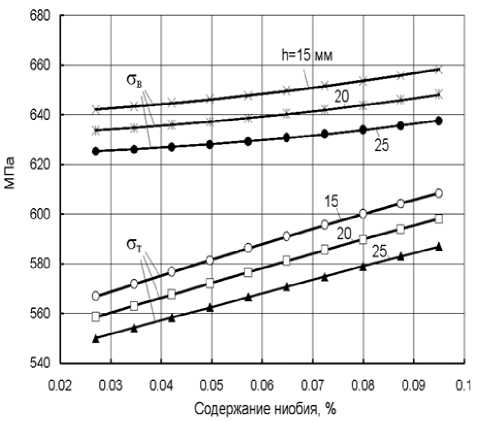
а)

Содержание титана, % а)
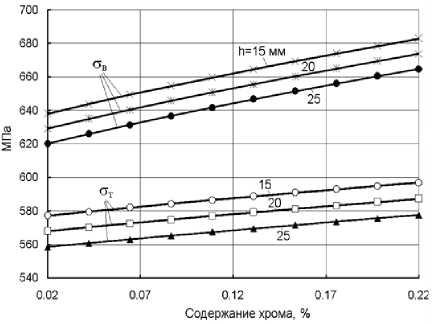
б)
Рис. 2. Влияние Ti (а) и Cr (б) на предел текучести и временное сопротивление разрыву
Никель увеличивает предел текучести на 30 МПа и временное сопротивление разрыву на 10-15 МПа (рис. 3а), снижает относительное удлинение на 1,5%. Медь увеличивает предел текучести на 20-25 МПа и увеличивает временное сопротивление разрыву на 20 МПа (рис. 3б), увеличивает относительное удлинение на 1,52,0%.
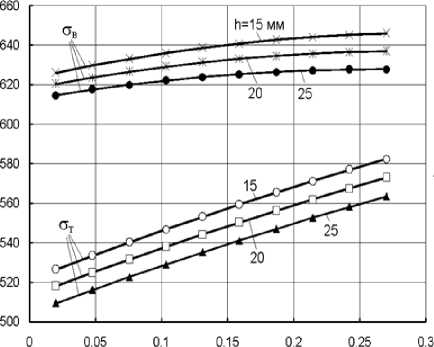
Содержание никеля, % а)
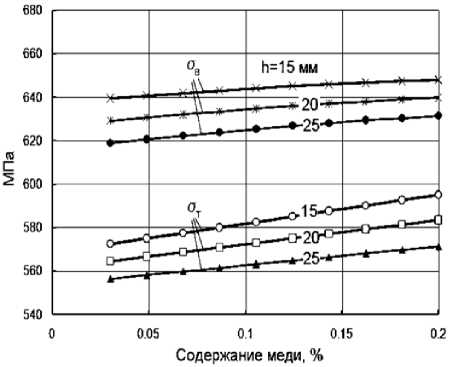
б)
Рис. 3. Влияние Ni (а) и Cu (б) на предел текучести и временное сопротивление разрыву
Молибден увеличивает предел текучести на 30-35 МПа и временное сопротивление разрыву на 60-65 МПа (рис. 4а), снижает относительное удлинение на 4%. Бор увеличивает предел текучести на 25-30 МПа и временное сопротивление разрыву на 35-40 МПа (рис. 4б), снижает относительное удлинение приблизительно на 4%.
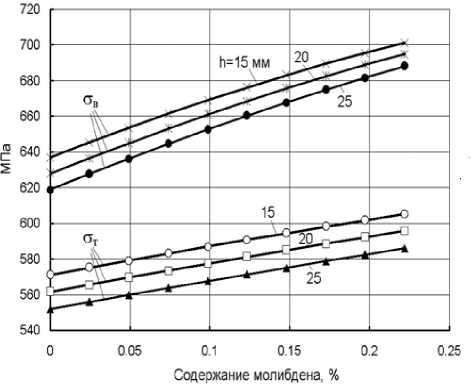
а)
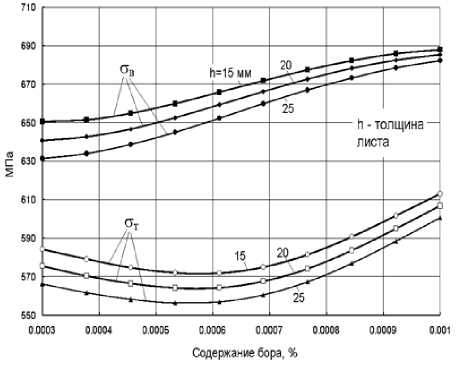
б)
Рис. 4. Влияние Mo (а) и B (б) на предел текучести и временное сопротивление разрыву
Рассмотрим фактическое влияние технологических воздействий на изменение механических свойств толстолистового проката класса прочности К60 толщиной 15,7-19,0 мм. Графические материалы получены на основе обработки статистических данных со стана 5000. Фактическое увеличение толщины сляба с 250 мм до 300 мм приводит к возрастанию предела текучести приблизительно на 10-15 МПа и временного сопротивления разрыву на 10-15 МПа (рис. 5а). Фактическое снижение температуры нагрева сляба в печи с 1200-1220ºС до 1180-1200ºС приводит к снижению предела текучести на 15-20 МПа и временного сопротивления разрыву на 10-15 МПа (рис. 5б).
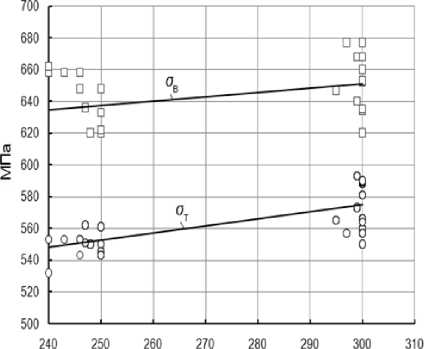
Толщина сляба, мм а)
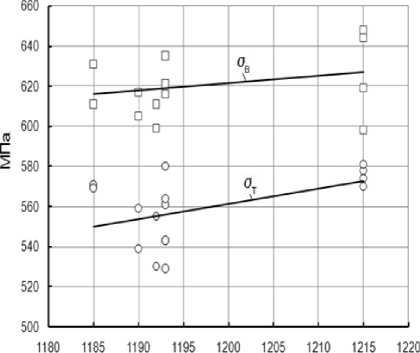
Температура нагрева сляба в печи.°C
б)
Рис. 5. Фактическое влияние исходной толщины сляба (а) и температуры нагрева сляба в печи (б) на предел текучести и временное сопротивление разрыву
Фактическое снижение температуры конца ускоренного охлаждения с 600ºС до 560ºС приводит к увеличению предела текучести на 15-20 МПа и временного сопротивления разрыву на 10-15 МПа (рис. 6), при этом относительное удлинение снижается на 1%.
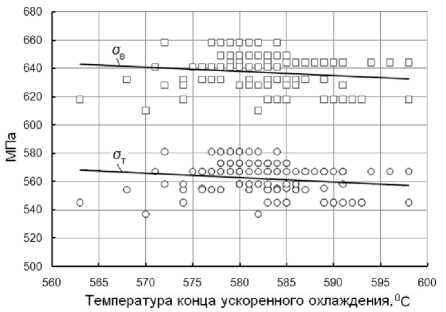
Рис. 6. Фактическое влияние температуры конца ускоренного охлаждения на предел текучести и временное сопротивление разрыву
Фактическое увеличение скорости охлаждения с 16ºС/сек до 20ºС/сек приводит к увеличению предела текучести приблизительно на 20 МПа и снижению временного сопротивления разрыву на 10 МПа (рис. 7), при этом относительное удлинение снижается на 1,0-1,5%.
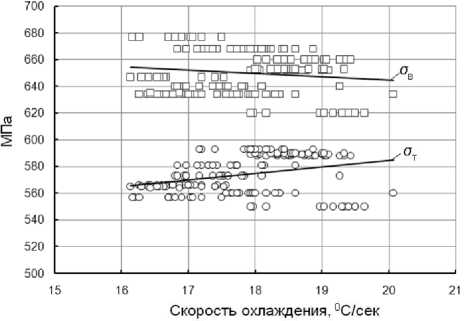
Рис. 7. Фактическое влияние скорости охлаждения на предел текучести и временное сопротивление разрыву
Таким образом, анализ фактического изменения свойств толстолистового проката при изменении технологических параметров процесса показал хорошую сходимость результатов моделирования и эксперимента для предела текучести и временного сопротивления разрыву.
Выводы и рекомендации. На основе нейросетевого моделирования выполнен анализ влияния химических элементов и технологических параметров термомеханической обработки на механические свойства трубной стали К60 в интервале толщин 15-25 мм, при этом установлено следующее:
– ниобий (каждые 0,025%) повышает предел текучести на 20-25 МПа и временное сопротивление разрыву стали на 15-20 МПа;
– ванадий (каждые 0,025%) увеличивает предел текучести на 10-15 МПа и временное сопротивление разрыву на 30 МПа;
– титан (каждые 0,005%) увеличивает предел текучести на 10-15 МПа и временное сопротивление разрыву на 25-30 МПа;
– хром (каждые 0,2%) увеличивает предел текучести на 20-25 МПа и временное сопротивление разрыву на 40-45 МПа;
– никель (каждые 0,1%) увеличивает предел текучести на 30 МПа и временное сопротивление разрыву на 10-15 МПа;
– медь (каждые 0,2%) увеличивает предел текучести на 20-25 МПа и увеличивает временное сопротивление разрыву на 20 МПа;
– молибден (каждые 0,2%) увеличивает предел текучести на 30-35 МПа и временное сопротивление разрыву на 60-65 МПа;
– бор (каждые 0,0005%) увеличивает предел текучести на 25-30 МПа и временное сопротивление разрыву на 35-40 МПа.
– снижение температуры нагрева сляба в печи с 1220 до 12000С способствует менее полному растворению карбонитридов ниобия и, как следствие, снижению прочностных характеристик стали – предела текучести на 20 МПа и временного сопротивления разрыву на 30 МПа;
– увеличение толщины сляба с 250 мм до 300 мм приводит к возрастанию предела текучести приблизительно на 10 МПа и временного сопротивления разрыву приблизительно на 25 МПа, что обусловлено увеличением числа обжатий на первой стадии прокатки и способствует более полному прохождению рекристаллизации и, следовательно, дополнительному измельчению зерна аустенита. Более мелкое зерно аустенита способствует формированию более мелкого зерна феррита после γ→α превращения;
– снижение температуры конца прокатки на 500С с 8700С до 8200С увеличивает предел текучести стали приблизительно на 20 МПа, при этом временное сопротивление разрыву практически не меняется;
– увеличение скорости охлаждения на каждые 40С/сек увеличивает предел текучести стали на 15-20 МПа и временное сопротивление разрыву на 14-18 МПа;
– снижение температуры конца ускоренного охлаждения на 500С с 6000С до 5500С увеличивает предел текучести стали на 20 МПа и временное сопротивление разрыву на 15 МПа, при этом относительное удлинение снижается на 1%.
-
2.
-
3.
-
5.
-
6.
Список литературы Математическое моделирование изменения прочностных характеристик микролегированных сталей в процессе термодеформационной обработки
- Pesin, A.M. A. Asymmetric rolling: Theory and Technology/A.M. Pesin, V.M. Salganik, H. Dyja et al.//Hutnik-wiadomosci hutnicze. 2012. No 5. P. 358-363.
- Чикишев, Д.Н. Модернизация технологии производства крупногабаритных тел вращения/Д.Н. Чикишев, А.М. Песин, В.М. Салганик, Э.М. Дригун//Мат-лы 63-й научно-техн. конф. по итогам научно-иссл. работ за 2003-2004 гг.: Сб. докл. Т.1. -Магнитогорск: МГТУ, 2004. С. 7-10.
- Песин, А.М. Развитие технологии совмещенного процесса прокатки и пластической гибки/А.М. Песин, Э.М. Дригун, Д.Н. Чикишев//Труды шестого конгресса прокатчиков (Липецк, 18 -21 октября 2005 г.), -М.: Объединение прокатчиков, 2005. С. 76-81.
- Санкин, Ю.В. Моделирование и совершенствование процесса холодной пластической гибки крупногабаритных тел вращения/Ю.В. Санкин, В.С. Блинов, Д.Н. Чикишев//Мат-лы 64-й научно-техн. конф. по итогам научно-иссл. работ за 2004-2005 гг.: Сб. докл. -Магнитогорск: ГОУ ВПО «МГТУ», 2006. Т.1. С. 27-31.
- Салганик, В.М. Совершенствование процесса толстолистовой прокатки микролегированных сталей различных классов прочности на основе дилатометрических исследований/В.М. Салганик, С.В. Денисов, Д.Г. Набатчиков и др.//Производство проката. 2011. №5. С. 5-8.
- Чикишев, Д.Н. Совершенствование технологии производства деталей крупногабаритных тел вращения на основе математического моделирования процессов деформирования толстых стальных листов. Дисс. на соиск. уч. степ. канд. техн. наук. -Магнитогорский государственный технический университет им. Г.И. Носова, 2007. 132 с.
- Чикишев, Д.Н. Современные концепции разработки низколегированных сталей для топливно-энергетического комплекса России/Д.Н. Чикишев, Е.Б. Блондинская, П.С. Тарасов, К.Э. Соколова//Наука и производство Урала. 2014. №10. С. 92-94.
- Салганик, В.М. Современное состояние производства заготовок для труб большого диаметра/В.М. Салганик, Д.Н. Чикишев, Е.Б. Блондинская//Наука и производство Урала. 2014. №10. С. 92-94.