Металлографитовые спеченные композиты с использованием механоактивированных материалов
Автор: Мамина Л.И., Беляев С.В., Чупров И.В., Безруких А.И., Баранов В.Н., Костин И.В.
Журнал: Журнал Сибирского федерального университета. Серия: Техника и технологии @technologies-sfu
Статья в выпуске: 4 т.7, 2014 года.
Бесплатный доступ
Проведены исследования по созданию недорогой металлографитовой вставки для пресс матрицы, применяемой в процессе совмещенного литья и прокатки прессования. Установлено, что механоактивация исходных материалов улучшает спекаемость образцов и повышает их физико-механические свойства (прочность и твердость). В процессе исследования были разработаны составы, обеспечивающие высокие эксплуатационные свойства металлографитовых вставок. Разработаны технологические режимы подготовки и спекания материалов, позволяющие сократить время технологического процесса на 40-50 % и не требующие создания специальной защитной атмосферы.
Металлографиты, спеченные композиты, механоактивация, процессы совмещенного литья и прокатки прессования, антифрикционные вставки, порошковая металлургия
Короткий адрес: https://sciup.org/146114852
IDR: 146114852
Текст научной статьи Металлографитовые спеченные композиты с использованием механоактивированных материалов
Металлографитовые спеченные композиты находят широкое применение в промышленности в качестве антифрикционных вставок, в подшипниках скольжения и в узлах трения [1]. В литейном производстве антифрикционные вставки могут использоваться в механизмах поворота ковшей, в запорном механизме ковша, а также в узлах трения машин для литья под давлением, под низким давлением и др.
Для обеспечения высоких физико-механических свойств готовых композитов при их спекании требуются высокие технологические условия, вплоть до обеспечения инертной среды, при этом содержание графита в металлической матрице в большинстве случаев не должно превышать 3 % [2], так как графитовые включения ввиду низкой смачиваемости многими металлами срабатывают как концентраторы напряжений, значительно снижая физико-механические свойства готовых изделий.
Получить беспористый и бездефектный материал можно с применением технологии штамповки, при которой осуществляются следующие этапы: 1) выбор состава и предварительная
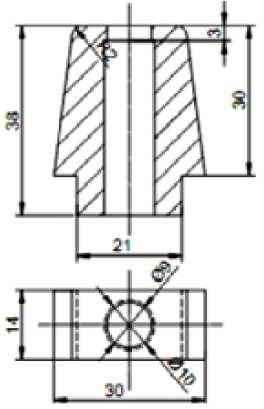
Рис. 1. Металлографитовая вставка подготовка порошковых материалов; 2) холодное прессование порошковой смеси; 3) спекание образцов при температуре 0,7 – 0,8Тпл основного компонента; 4) горячая допрессовка образца до необходимой плотности (непосредственно штамповка порошкового материала); 5) механическая обработка и получение готового изделия.
В работе проводились исследования по созданию недорогой сменной композитной антифрикционной вставки в районе обжимного пояска пресс-матрицы, применяемой в процессах совмещенного литья и прокатки-прессования – СЛиПП (рис. 1).
Результаты исследования и их обсуждение
В качестве материалов для графитсодержащей композитной вставки были выбраны композиции на основе медных и железных порошков со скрытокристаллическими и кристаллическими графитами марок ГЛ-1 (ГОСТ 5279-74) и ГЛС-2 (ГОСТ 5420-74). Целью проводимых экспериментов было нахождение оптимальных технологических режимов штамповки металлографитовых порошков, необходимого соотношения металла к графиту и выбор оптимально -го времени активации металлографитового композита, при котором сохранялись как высокие физико-механические свойства металлической матрицы (твердость, прочность), так и высокие антифрикционные свойства композита.
Известно, что механоактивированные вещества характеризуются термодинамической неустойчивостью, меняются их термодинамические потенциалы (свободная энергия, энтальпия, энтропия) вследствие структурных преобразований [3–5]. При этом частицы, находящиеся в поверхностном слое твердого тела, имеют некоторую избыточную энергию (за счет большого скопления дислокаций и различных поверхностных дефектов), и в результате поверхностный слой, находясь в упруго напряженном состоянии, обладает большим запасом потенциальной энергии, чем внутренние слои. За счет поверхностной избыточной энергии происходит более активное физико-химическое взаимодействие частиц порошка при холодном прессовании, что значительно повышает однородность композита, а значит, и его физико-механические свойства. К тому же, как было показано Ф.В. Ленелом [6], начальные стадии процесса спекания порошков осуществляются не за счет диффузионного переноса материала, а за счет его пласти-– 468 – ческого деформирования вследствие дислокационного переноса, т.е. механоактивация может повысить интенсивность процесса спекания за счет наличия на поверхности активированных частиц порошка большого количества свободных дислокаций.
На первом этапе работы была приготовлена смесь медного и графитового порошков в различном соотношении компонентов. Композицию подвергли механоактивации в центробежнопланетарной мельнице АГО-2. Оптимальные режимы механоактивации композиции были выбраны, основываясь на предыдущих исследованиях влияния режимов механоактивации графитовых материалов на свойства готовых изделий [7–9].
Спекание образцов проводили при температуре 750-800 °С в течение 8-15 мин под слоем механоактивированного кристаллического графита (ГЛ-1) для того, чтобы предотвратить окисление металла и выгорание графита в образце. Данный защитный слой при выгорании создавал вокруг образца избыточную концентрацию СО, который и защищал металлографитовый композит от окисления.
Холодное прессование порошков, а также их горячую допрессовку после спекания осуществляли в специально разработанных пресс-матрицах (рис. 2). При этом готовые образцы представляли собой цилиндрические «таблетки» диаметром 20 мм и высотой 4-7 мм.
Полученные образцы подвергли механическим испытаниям на твердость и прочность.
Составы, технологические режимы получения композитов и результаты механических испытаний приведены в табл. 1, 2.
Установлено (табл. 2), что с увеличением содержания графита в образцах физикомеханические свойства композитов значительно снижаются (рис. 3, 4), что объясняется влиянием графита, который практически не растворяется в медной матрице. При перемешивании с медным порошком на поверхности медных частиц образуется углеродная «шуба», затрудняющая процессы взаимной диффузии, а следовательно, снижается плотность и однородность металлической матрицы, получаемой после спекания и горячей допрессовки композитов.
В результате проведенного исследования было выявлено оптимальное соотношение графитов марок ГЛ-1 и ГЛС-2 в медной матрице композита, равное 1:3, при котором образцы имели наиболее высокие механические показатели (рис. 5).
Влияние дополнительных легирующих компонентов (лигатуры Al-Ni, свинца, титана) на механические свойства медно-графитовых композитов было незначительным и полностью
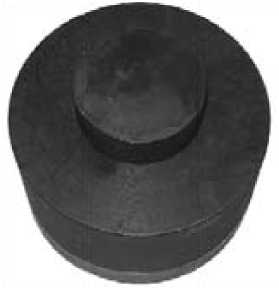
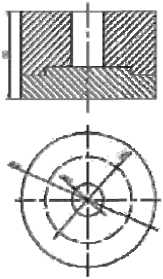
Рис. 2. Пресс-матрица для прессования металло-графитового композита: а – общий вид; б – чертеж пресс-матрицы
Таблица 1. Составы медно-графитовых композитов
Номер образца |
Состав композита |
|||||
Cu, % |
ГЛ, % |
ГЛС, % |
Al-Ni, % |
Ti, % |
Pb, % |
|
1 |
96 |
3 |
1 |
0 |
0 |
0 |
2 |
96 |
1 |
3 |
0 |
0 |
0 |
3 |
96 |
2 |
2 |
0 |
0 |
0 |
4 |
90 |
2 |
2 |
6 |
0 |
0 |
5 |
92 |
1 |
3 |
3 |
1 |
0 |
6 |
88 |
3 |
3 |
5 |
1 |
0 |
7 |
89 |
1 |
3 |
3 |
0 |
4 |
8 |
92 |
0 |
4 |
0 |
0 |
4 |
Таблица 2. Технологические режимы получения медно-графитовых композитов и результаты механических испытаний
Номер образца |
Технологические режимы |
Твердость, НВ |
Предел прочности на сжатие, МПа |
||
Давление холодного прессования, МПа |
Температура спекания, °С |
Время спекания в печи, мин |
|||
1 |
261 – 299 |
740 – 770 |
10 |
63,9 |
82 |
2 |
10 |
76 |
116 |
||
3 |
10 |
68 |
78 |
||
4 |
15 |
56,3 |
94 |
||
5 |
15 |
71,1 |
133 |
||
6 |
15 |
46,6 |
59 |
||
7 |
30 |
64,5 |
80 |
||
8 |
25 |
51,7 |
55 |
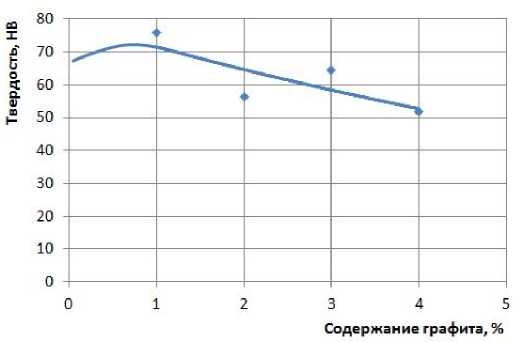
Рис. 3. Зависимость твердости композитов от суммарного содержания графита
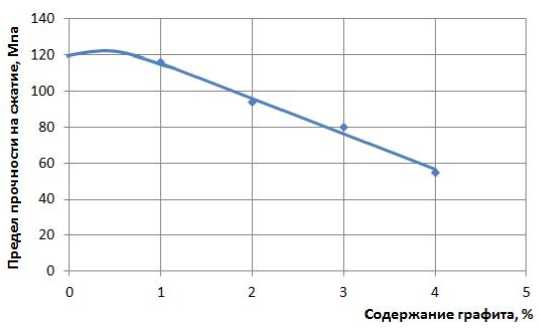
Рис. 4. Зависимость прочности на сжатие композитов от суммарного содержания графита
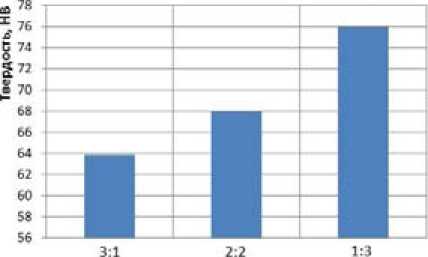
Соотношение ГЛ:ГЛС ч 140
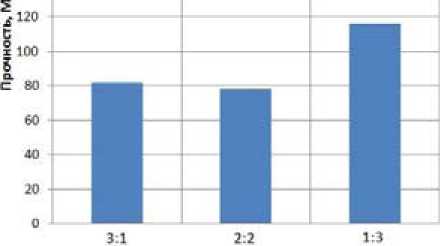
Соотношение ГЛ:ГЛС
Рис. 5. Оптимальное соотношение графитов в композитах компенсировалось влиянием графита как более вредной примеси в металлической матрице меди. При этом применение дополнительных легирующих элементов удорожает стоимость композита, поэтому от их использования в составе композитов решено было отказаться.
На втором этапе исследования изготовили железографитовые композитные вставки. Для их изготовления использовали следующие материалы: железный порошок марки ПЖВ3 по
Таблица 3. Состав железографитовых композитов и результаты механических испытаний
Номер образца |
Состав композита |
Твердость, НВ |
||
Fe, % |
ГЛ, % |
ГЛС, % |
||
9 |
96 |
1 |
3 |
161 |
10 |
92 |
2 |
6 |
154 |
11 |
98 |
0,5 |
1,5 |
175 |
ГОСТ 9849-86, графит литейный скрытокристаллический марки ГЛС-2 по ГОСТ 5420-74, графит литейный кристаллический марки ГЛ-1 по ГОСТ 5279-74.
Технология прессования и получения железографитовых композитов заключалась в следующем. Порошки предварительно взвешивали, исходя из процентного соотношения компонентов, равномерно перемешивали. Затем дисперсные композиции прессовали в пресс-матрице под давлением 299 МПа. Не вынимая образцы из пресс-матрицы, их спекали при температуре 1000 °С в течение 20 мин для получения равномерной металлической матрицы с включениями графита. После спекания осуществляли горячую допрессовку до необходимой плотности (близкой к плотности чистого железа) под давлением в 892МПа и остаточной температуре в 500 °С.
Подробный состав композитов и результаты их испытаний на твердость приведены в табл. 3.
Как видно из полученных данных, железографитовые композиты обладают почти в 1,5-2 раза большей твердостью по сравнению с медно-графитовыми (табл. 3), что объясняется как большей прочностью железной основы, так и хорошей растворимостью графита в железе (до 6,67 %), и, как следствие, образованием более твердой фазы цементита при спекании композиций.
Заключение
Применение метода штамповки c механоактивацией композиционных материалов позволило значительно снизить пористость и повысить однородность прессуемых композитов. При этом за счет более равномерного внедрения графитовых частиц в металлическую матрицу (вследствие повышения активности исходных материалов) удалось снизить влияние графитовых включений на поверхностную твердость материала, тем самым повысив эксплуатационные характеристики металлографитовой композитной основы, и увеличить содержание графитов в металлической матрице до 4-6 % (а значит, и антифрикционные свойства) при сохранении высоких эксплуатационных характеристик готовых металлографитовых вставок.
В процессе экспериментального исследования были определены оптимальные технологические режимы подготовки и прессования композиций, а также оптимальное время спекания образцов в печи, которое составляет не более 15-20 мин. Дальнейшее увеличение времени спекания приводит к расслоению образцов при прессовании вследствие сильного окисления металлографитовой композиции.
Разработанные железографитовые спеченные композиты за счет большей твердости оказались предпочтительнее для использования в качестве вставок для пресс-матриц СЛиПП, тогда как медно-графитовые вставки показали более высокие антифрикционные свойства и могут быть применимы в различных узлах трения.