Метод и устройство вибростабилизационной обработки для снижения эксплуатационного дисбаланса гибких роторных систем
Автор: Корнеев Н.В.
Журнал: Известия Самарского научного центра Российской академии наук @izvestiya-ssc
Рубрика: Механика и машиностроение
Статья в выпуске: 3 т.9, 2007 года.
Бесплатный доступ
В статье рассмотрены основные подходы в области стабилизации остаточных напряжений, вли- яющих на эксплутационный дисбаланс роторных конструкций турбоагрегатов. Разработано и предложено новое устройство для вибростабилизации указанных конструкций. Приведены ре- зультаты экспериментальных исследований.
Короткий адрес: https://sciup.org/148197998
IDR: 148197998
Текст научной статьи Метод и устройство вибростабилизационной обработки для снижения эксплуатационного дисбаланса гибких роторных систем
Тольяттинский государственный университет сервиса
В статье рассмотрены основные подходы в области стабилизации остаточных напряжений, влияющих на эксплутационный дисбаланс роторных конструкций турбоагрегатов. Разработано и предложено новое устройство для вибростабилизации указанных конструкций. Приведены результаты экспериментальных исследований.
Стабильность геометрии ротора, т.е. неизменность его геометрии в процессе эксплуатации, существенно влияет на его эксплуатационный дисбаланс и определяется множеством факторов, среди которых важную роль играют внутренние напряжения в его конструкции [1].
Среди всего многообразия деталей входящих в состав ротора существенную роль играет центральный вал, который является несущим звеном конструкции, и в большей степени определяет работоспособность роторной системы в целом.
Стабильность геометрических форм и размеров роторов зависит от многих факторов, например, неоднородность пластической деформации при изготовлении, неравномерность остывания при термообработке (ТО) наружных и внутренних слоев металла заготовки, неравномерность твердости по длине и диаметру, неоднородная размерность зерен и кристаллов металла, релаксация остаточных напряжений, возникающих при сборке, механической и ТО.
Указанные факторы, влияющие на остаточные напряжения в деталях и создающие эти напряжения, определяются одной причиной – неравномерностью их на всех операциях, начиная от процесса получения заготовки и заканчивая операциями сборки.
Остаточные напряжения, которые получают детали в процессе обработки не успевают релаксировать и при сборке передаются друг другу вызывая деформацию ротора, увеличение динамических прогибов, повышение дисбаланса ротора. Термические де- формации при сборке создают дополнительные остаточные напряжения, которые в большинстве случаев увеличивают уже существующие в деталях остаточные напряжения. Все это вызывает нестабильность геометрии ротора, отражаясь на его работоспособности, а в конечном итоге на работоспособности роторных машин.
Общим свойством остаточных напряжений является то, что они всегда бывают чисто упругими [2], даже если возникают в результате пластической деформации. Эти напряжения могут быть сняты всеми теми способами, которые приводят к ослаблению упругих деформаций, соответствующих остаточным напряжениям, с последующей диссипацией упругой потенциальной энергии, накопленной в материале. Но это может сопровождаться пластической деформацией и возникновением новых остаточных напряжений.
Следует отметить, что снижать остаточные напряжения каждой детали для стабилизации геометрии ротора дело крайне сложное и экономически нецелесообразное. Необходимо снижение остаточных напряжений и температурных деформаций центральных элементов ротора, т.е. основных, несущих на себе функции определяющие работоспособность ротора в целом. Такими элементами могут быть вал ротора, рабочие диски ротора и д.р.
Такие широко известные методы как отпуск, низкотемпературный отжиг, искусственное старение, естественное старение будут здесь неприемлемы. Низкая эффективность этих методов обусловлена тем, что для их осуществления необходимы большие ка- питальные вложения, а длительность процесса очень большая.
Относительно новым методом снятия остаточных напряжений является вибростабилизация. По современным представлениям [3] при вибрационном методе снятия внутренних напряжений в металл вводится энергия колебаний. При этом в детали возникают дополнительные напряжения (сжатия, растяжения, изгиба), которые, суммируясь с первоначальными остаточными напряжениями, создают еще более напряженное состояние. Благодаря этому в поликристаллическом материале происходят сдвиги кристаллической решетки, сопровождающиеся перераспределением напряжений, а атомы переходят в равновесное состояние. В конечном счете, остаточные напряжения в пределах отдельных зерен и по их границам уменьшаются.
Для получения максимальных напряжений частоту вибрации во всех случаях стремятся выбрать близкой к частоте собственных колебаний детали. В условиях возникающего при этом резонанса колебаний амплитуда деформации детали получается максимальной, а следовательно, максимальными будут и создаваемые вибрации [4].
Применение данного метода теоретически возможно для стабилизации геометрии и внутренней структуры материала ротора, однако как указывалось выше необходимо провести стабилизацию ротора в сборе, что связано с трудностями. На производстве широко применяется вибростабилизация маложестких деталей, так как для создания в них напряжений перегрузки не требуется значительных усилий. В качестве основной трудности при вибростабилизации роторов можно выделить отсутствия стандартных мощных вибраторов, способных создать необходимые напряжения перегрузки.
Нами предлагается следующая конструкция вибратора, далее генератор крутильных колебаний (ГКК) для проведения вибростабилизации формы и размеров роторов турбокомпрессорных агрегатов “Синтезгаз” (ОАО “Азотреммаш”) (рис. 1) [5].
Генератор крутильных колебаний, включает в себя корпус 1, центральное зубчатое колесо 2, привод 3, передающий вращение на центральное зубчатое колесо 2, две одинако-
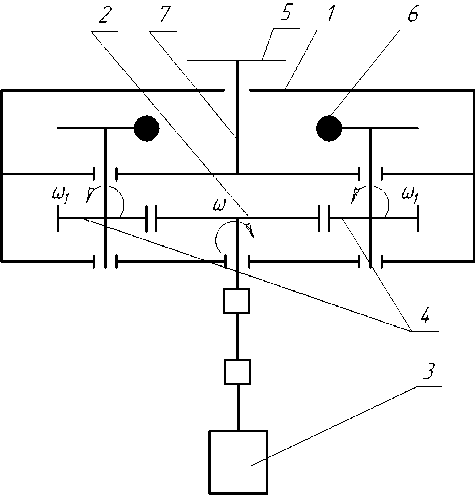
Рис. 1. Модель генератора крутильных колебаний вые шестерни 4, получающие вращение от центрального зубчатого колеса 2, узел крепления 5, соединяющий генератор с изделием.
С целью создания гармонически изменяющегося с течением времени значительного крутящего момента, передаваемого на изделие, через узел крепления, на указанных шестернях закрепляются два неуравновешенных груза 6, создающих равные по модулю и противоположные по фазе дисбалансы, причем узел крепления и корпус связаны посредством торсиона 7, крутильная жесткость которого подбирается из условия резонанса между угловой скоростью вращения шестерен ω 1 и собственной круговой частотой колебаний генератора ω 0 , т.е. согласно формуле:
ω1 =ω0 , где ω1 = iω , ω – угловая скорость вращения центрального колеса, 1/с.
Значение определяется по формуле:

где С – крутильная жесткость торсиона; θ – полярный момент инерции генератора.
В качестве схемы для осуществления процесса вибростабилизации ротора, целесообразно использовать схему изображенную на рис. 2, так как ротор конструктивно выполнен таким образом, что свободными поверхностями для крепления ГКК и приложения нагрузки могут быть использованы толь-
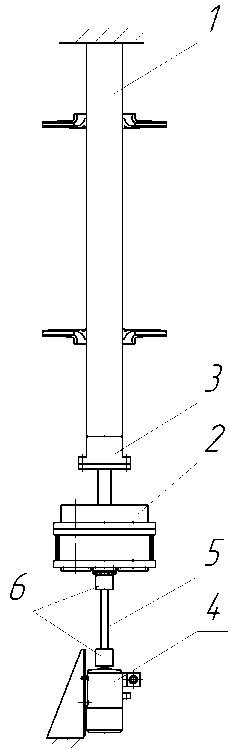
Рис. 2. Схема вибростабилизации ротора ко поверхности расположенные по краям: ротор 1 с одного конца крепится жестко, к другому его концу крепится генератор крутильных колебаний 2, посредством узла крепления 3. Привод генератора представляет собой двигатель 4, который за счет гибкого вала 5 и муфт 6 передает вращение на центральное колесо генератора.
Такая схема вибростабилизации ротора имеет ряд существенных преимуществ:
-
- вибростабилизация проводится не только вала, а узла в целом, что обеспечивает стабилизацию всей конструкции в целом, так как передаваемое динамическое усилие способствует не только стабилизации вала и деталей закрепленных на нем, но и их само-установки в оптимальном положении. Существенным является то, что такая схема повышает стабильность центрирования рабочих колес;
-
- возможность передачи значительных переменных усилий при высокой частоте колебаний, так как ω 1 = ω 0 ;
-
- реальное равномерное распределение переменного усилия по всей поверхности вала ротора, ввиду того, что резонанс в системе возникает не за счет равенства собственной крутильной частоты колебаний ротора, которая с технологической точки зрения является недостижимой для генератора, а за
счет равенства ω 1 = ω 0 , т.е. резонанса в конструкции ГКК.
Для проведения экспериментальных исследований влияния вибрационного нагружения на стабильность формы и геометрии роторов турбоагрегатов, были проведены серии экспериментов по вибростабилизации роторов компрессорных агрегатов “Синтезгаз” в производственных условиях ОАО “Азотрем-маш”, согласно целевой программы Роснау-ки РФ “Поддержка молодых российских ученых…” и гранта Президента РФ конкурс МК-5891.2006.8.
На специальном стенде была проведена обработка гибких роторов компрессорных агрегатов “Синтезгаз” в сборе. В качестве режимов для вибростабилизации роторов было принято: время обработки, T – 5…20 мин; возникающие касательные напряжения на валу, от действия динамического крутящего момента варьировались от 8…12 МПа.
Расчетные и экспериментальные данные, полученные в [1], свидетельствуют, что значительная часть дисбаланса роторов определяется торцевыми биениями дисков, которые в свою очередь являются результатом погрешностей установки самих дисков на вал. Согласно сделанным теоретическим предположениям проведем исследование возможностей вибростабилизации в отношении самоустановки в оптимальное положении деталей закрепленных на валу. С этой целью были проведены замеры торцевого биения дисков δ(T) согласно схеме на рис. 3, до виб ростабилизации роторов δ0(T) и после нее δв(иTб). . Замеры проводились на высокоточном станке с ЧПУ посредством индикатора часового типа с ценой деления 0,001мм по 12 точкам равнорасположенным по окружности диска, при этом ротор был установлен в центрах.
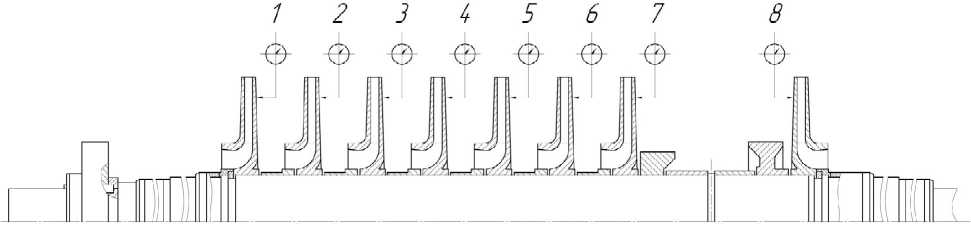
Рис. 3. Схема замера торцевых биений дисков ротора К-601
Таблица. Результаты замеров торцевых биений дисков ротора К-601
Номер диска |
( T ) δ 0 , мм |
δ в ( и T б ) . , мм, при Т=5 мин |
δ в ( и T б ) . , мм, при Т=10 мин |
δ в ( и T б ) . , мм, при Т=20 мин |
1 |
0,032 |
0,021 |
0,021 |
0,023 |
2 |
0,043 |
0,035 |
0,033 |
0,035 |
3 |
0,045 |
0,022 |
0,022 |
0,024 |
4 |
0,041 |
0,027 |
0,027 |
0,027 |
5 |
0,052 |
0,031 |
0,030 |
0,035 |
6 |
0,034 |
0,020 |
0,020 |
0,030 |
7 |
0,055 |
0,039 |
0,037 |
0,039 |
8 |
0,034 |
0,021 |
0,024 |
0,024 |
В табл. приведены усредненные результаты замеров торцевых биений дисков ротора К-601 до и после вибростабилизации.
Укажем, что значения торцевых биений, которые должны быть выдержаны на готовом изделии, согласно карты технического контроля, равны 0,04 мм.
Анализ полученных результатов свидетельствует, что вибростабилизация роторов в сборе является эффективным методом борьбы с дисбалансом, а следовательно и с роторной вибрацией. Торцевые биения дисков снижаются в среднем 0,01…0,03 мм, причем сле- дует отметить, что 90% дисбаланса роторов турбоагрегатов связано именно с торцевыми биения дисков. Согласно таб. эффективное время стабилизации формы и геометрии роторов составляет не более 10 мин, дальнейшая обработка, как показали экспериментальные данные, нецелесообразна.
На рис. 4, 5 представлены гистограммы и дифференциальные плотности распределения величины торцевого биения дисков исследуемых роторов, соответственно, до и после вибростабилизации с режимом обработки T=5мин.
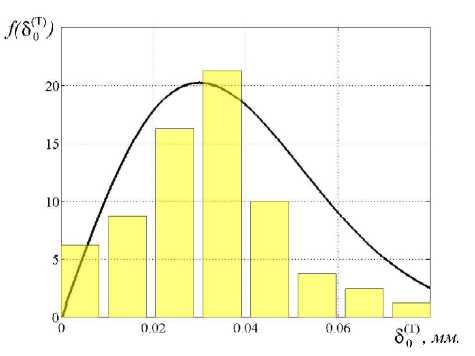
Рис. 4. Гистограмма и выравнивающее распределение величины торцевого биения дисков ротора К-601 до вибростабилизации
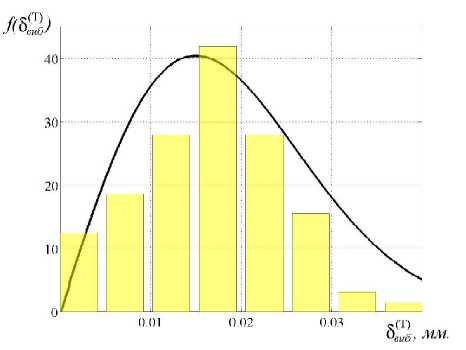
Рис. 5. Гистограмма и выравнивающее распределение величины торцевого биения дисков ротора К-601 после вибростабилизации
Анализ результатов представленных на рис. 4 и 5 позволяет сделать следующие выводы: модули торцевых биений подчиняются распределению Релея, как до вибростабилизации, так и после нее. Значение параметров распределений величины торцевого биения дисков, для рассматриваемых здесь конструкций роторов, до вибростабилизации a ( ^ 0 T ) ) =0,02^0,03 мм, а после вибростабилизации снижается в среднем в 2 раза и составляет а ( з вТб ) =0,012^0,015 мм.
Работа выполнена при поддержке гранта Президента РФ № МК-5891.2006.8
Список литературы Метод и устройство вибростабилизационной обработки для снижения эксплуатационного дисбаланса гибких роторных систем
- Корнеев Н.В., Кустарев Ю.С. Управление дисбалансом высокоскоростных роторных систем. М.: Компания Спутник+, 2006.
- Третьяков А.В. Механические свойства сталей и сплавов при пластической деформации. М.: Машиностроение. 1971.
- Технологические процессы пластического деформирования в машиностроении/под ред. Беляева В.И. Минск, 1989.
- Шпеер Ф.З., Федосеев В.Л. Эффективность применения виброобработки при изготовлении крупногабаритных деталей//Вестник машиностроения, 1983. № 7.
- Патент РФ № 2254173 Н.В. Корнеев, А.И. Глейзер, О.И. Драчев Генератор крутильных колебаний. Опубл. 20.06.2005. Бюл. №17.