Методика проектирования экструзионного инструмента
Автор: Пятов В.В., Голубев А.Н.
Журнал: Вестник Витебского государственного технологического университета @vestnik-vstu
Рубрика: Технология и оборудование легкой промышленности и машиностроения
Статья в выпуске: 1 (42), 2022 года.
Бесплатный доступ
Предметом исследования является технология автоматизированного проектирования экструзионного инструмента, в частности, экструзионной матрицы и силового шнека экструдера для переработки вязко - пластичных сжимаемых сред. Приведена расчетная схема зоны деформации при проектировании экструзионной матрицы, представлен алгоритм и дан фрагмент расчетов ее геометрических параметров. Для шнека с прямоугольным профилем канала показано распределение касательных напряжений, даны алгоритм и пример расчетов геометрических параметров канала шнека. Рассмотренная технология проектирования построена на основе теоретической модели, связывающей реологические свойства и триботехнические характеристики перерабатываемого материала с геометрическими параметрами экструзионного инструмента. Приведены примеры конструкций формующей головки и силового шнека экструдера, спроектированных на основании выполненных расчетов. Результаты работы могут быть полезны при разработке специализированной САПР деталей и узлов экструзионного оборудования.
Экструзия, шнековые машины, вязко-пластичная среда, экструзионная матрица, шнек, технология проектирования
Короткий адрес: https://sciup.org/142235816
IDR: 142235816 | DOI: 10.24412/2079-7958-2022-1-80-88
Текст научной статьи Методика проектирования экструзионного инструмента
EXTRUSION, SCREW MACHINES, VISCO-PLASTIC MEDIUM, EXTRUSION DIE, SCREW, DESIGN TECHNOLOGY
The subject of the research is the technology of computer-aided design of an extrusion tool, in particular, an extrusion die and a power screw of an extruder for processing viscous-plastic compressible media.
The calculation scheme of the deformation zone in the design of an extrusion die is given, an algorithm and a fragment of calculations of its geometric parameters are offered. For a screw with a rectangular channel profile, the distribution of shear stresses is shown, an algorithm and an example of calculating the geometric parameters of the screw channel are proposed. The considered design technology is based on a theoretical model that relates the rheological properties and tribotechnical characteristics of the processed material with the geometric parameters of the extrusion tool.
Examples of designs of the forming head and the power screw of the extruder, designed on the basis of the performed calculations, are shown. The results of the work can be useful in the development of specialized CAD for parts and assemblies of extrusion equipment.
Постановка задачи
В статье рассматривается задача разработки методики проектирования шнековых машин (экструдеров), позволяющая автоматизировать расчет и проектирование формующих головок и силовых шнеков с оптимальными геометрическими характеристиками. На входе даны эксплуатационные и геометрические свойства изделия
(требования заказчика), а также физические и технологические свойства формуемой среды (главным образом реологические и трибологические ее характеристики). На выходе автоматизированная система, построенная на основе разработанной методики, должна быть способна формировать конструкторскую документацию (3D-модели и чертежи), необходимую для изготовления оборудования.
Теория экструзии в основном развивалась по отдельности в разных отраслях народного хозяйства, в зависимости от свойств перерабатываемых материалов. В последнее время получили большое развитие численные методы исследования пластической деформации, моделирующие процесс экструзии [1, 2], существуют математические модели, позволяющие рассчитывать технологические параметры, например, при экструзии брикетов порошков алюминия [3]. Прямое заимствование полученных результатов для процессов переработки других материалов, как правило, невозможно, поскольку по реологическим и технологическим свойствам перерабатываемые экструзией материалы сильно отличаются друг от друга. В статье описана методика проектирования инструмента, применяемого для переработки пластично-вязких сред, построенная на основе теоретической модели экструзии подобных сжимаемых сред [4]. В частности, приведены примеры расчетов, выполняемых при проектировании экструзионной матрицы и силового шнека экструдера.
Исходные данные для проектирования
Рассмотрим пример расчета экструзионной матрицы и силового шнека для экструдирования изделия в виде трубы с наружным диаметром 30 мм и внутренним диаметром 20 мм . Материал – бронзовый сферический порошок марки БрОФ-10-1 с фракцией -200+160 мкм , пластифицирующая добавка – технически очищенный парафин.
Методика проектирования матрицы
Расчетная схема для проектирования матрицы изображена на рисунке 1. Параметры калибрующей части определяются геометрией изделия: радиус выходного сечения конуса матрицы r1 = 15 мм, радиус дорна r0 = 10 мм,длина цилиндрической (калибрующей) части матрицы z2 - z1 = 20 мм. Угол наклона образующей кону са а = 300; большее значение этого параметра ведет к ухудшению качества прессовок, а меньшее – к неоправданному увеличению энергоемкости процесса формования.
Давление р0 на входе в коническую часть матрицы равно давлению, при котором материал теряет газовую фазу и становится несжимаемым. Оно определено по результатам исследования уплотняемости пластифицированных порошков: р0 = 60 МПа . Предел текучести и коэффициент внешнего трения при этом давлении для выбранного материала равны соответственно a s = 12 МПа и f = 0,13. Радиус входной части конуса матрицы рассчитан по формуле [4]
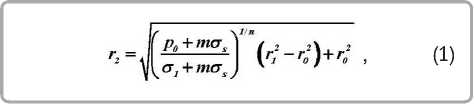
где коэффициент m зависит от коэффициента трения f и угла наклона образующей конуса а (таблица 1).
Алгоритм и результаты расчетов по проектированию матрицы представлены в таблице 1. Методики, устройства и оснастка для измерения необходимых технологических свойств материалов и коэффициентов подробно рассматриваются в монографии [4]. Результаты расчетов матрицы представлены на рисунке 2.
Методика проектирования шнека
Проектирование шнека целесообразно начинать с выбора профиля винтового канала. В работе [4] было получено уравнение, позволяющее рассчитать профиль канала по заданному распределению напряжений в материале. В соответствии со сделанными допущениями, канал шнека имеет постоянное по длине сечение и считается прямолинейным. Движущая сила возникает в результате трения о подвижную поверхность и давления, действующего на входе в канал (если оно есть). Ось z направлена от выхода канала к его входу, то есть от матрицы экструдера к бункеру. Начало отсчета совпадает с границей раздела между каналом шнека и матрицей, давление в этой точке р0 . Ось x направлена по ширине канала, ось у - по его высоте (глубине).
Полученные в [4] уравнения позволяют, задаваясь функцией распределения касательных
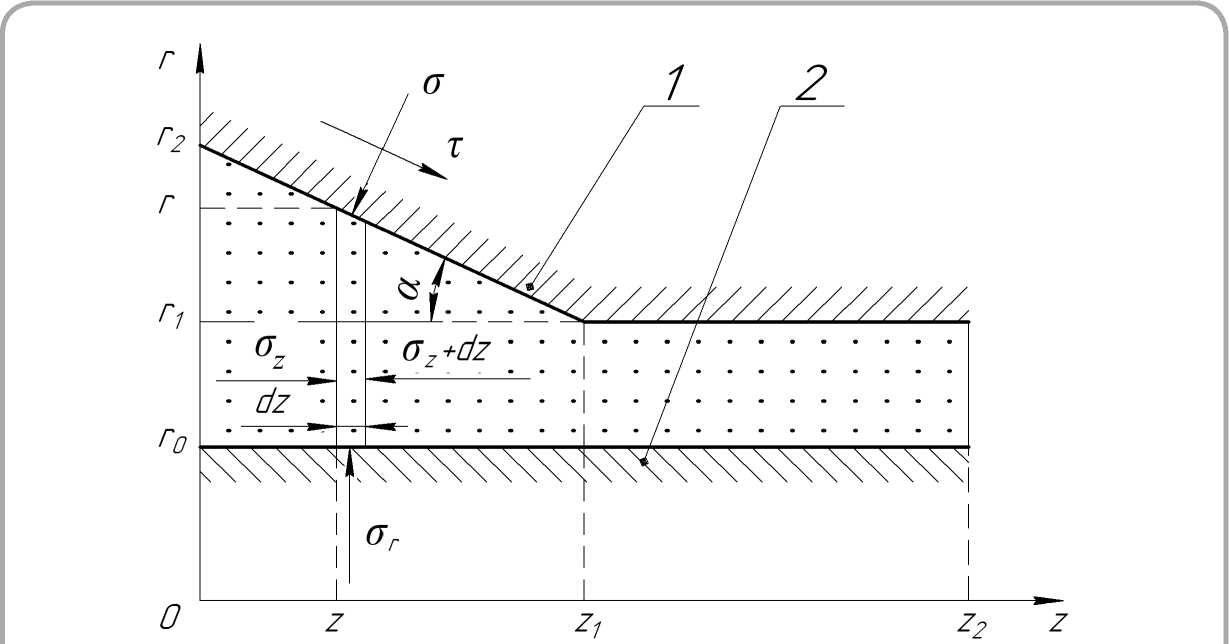
Рисунок 1 – Схема зоны деформации: 1 – поверхность матрицы, 2 – поверхность дорна
Таблица 1 – Алгоритм расчетов по проектированию матрицы
Источник |
Обозначение параметра |
Название параметра |
Размерность |
Формула |
Значение |
Заданные параметры |
r0 |
Внутренний радиус изделия |
ì |
– |
0,01 |
r1 |
Наружный радиус изделия |
ì |
– |
0,015 |
|
Выбранные значения |
z2 - z1 |
Длина калибрующей части |
ì |
– |
0,02 |
α |
Угол подъема образующей |
радиан |
π / 6 |
0,524 |
|
Измеренные величины |
σs |
Предел текучести |
МПа |
12 |
|
f |
Коэффициент трения |
– |
– |
0,13 |
|
p0 |
Критическое давление |
МПа |
– |
60 |
|
Результаты вычислений |
p |
Коэффициент |
1/м |
2 fr 1 r1r0 |
31,2 |
σ1 |
Напряжение на выходе конуса |
МПа |
a s [ e- (--) - 1 ] |
10,397 |
|
k |
Коэффициент |
– |
f + tgg 1f tg |
0,765 |
|
n |
Коэффициент |
– |
k ctg a - 1 |
0,325 |
|
m |
Коэффициент |
– |
1 f + tga f 1 + tg a |
4,081 |
|
r2 |
Радиус основания конуса |
ì |
(1) |
0,0302 |
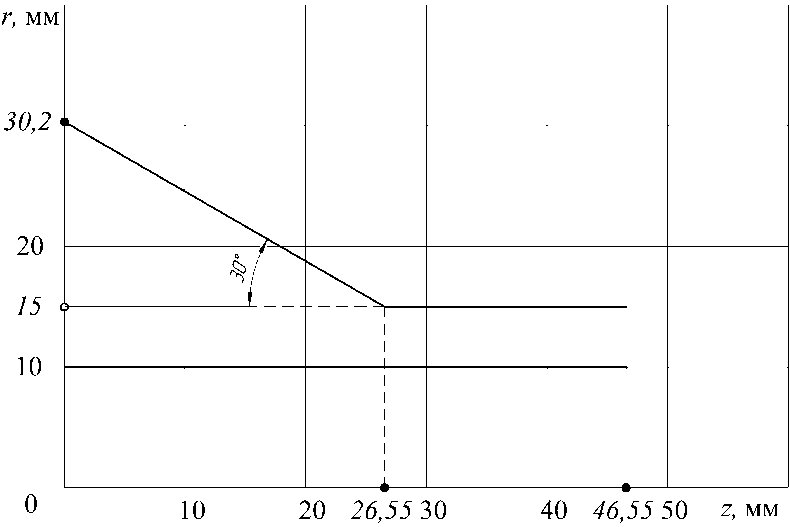
Рисунок 2 – Результаты расчета матрицы
напряжений по глубине канала τ = f(y) , найти соответствующую этой функции зависимость x = f(y) , тем самым определив геометрию профиля канала. При этом удобно пользоваться безразмерными величинами размеров и напряжений, полученными путем деления всех размеров x на ширину канала x0 и всех напряжений т на напряжение на неподвижной поверхности канала τ0 .
В частности, если требуется обеспечить постоянство касательных напряжений по глубине и задаться функцией τ = f(y) = const (рисунок 3 а ), то зависимость x = f(y) окажется прямой линией, проходящей через точки ( 0 , Н ) и ( х0 , 0 ), что соответствует треугольному профилю канала (рисунок 3 б ).
Так как используемый для фильтров сферический бронзовый порошок, пластифицированный парафином, обладает высокой пластичностью, для расчетов шнека был выбран не треугольный, а технологически более простой квадратный профиль со стороной 5 мм . У такого профиля, наоборот, x = f(y) = const (рисунок 4 б ), соответствующее этому профилю рассчитанное распределение касательных напряжений по глубине
τ = f(y) показано на рисунке 4 а .
Радиус шнека r2 и давление на выходе из канала р0 уже были определены при расчете матрицы. Угол подъема канала γ можно выбрать произвольно (лучше из интервала 10-200).
Длина канала рассчитана по формуле [4]
z^rfln^-*"^ U'-PoVjygH-e')
длина прессующей части шнека – по формуле
, (3)
а соответствующее ей число витков канала равно
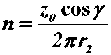
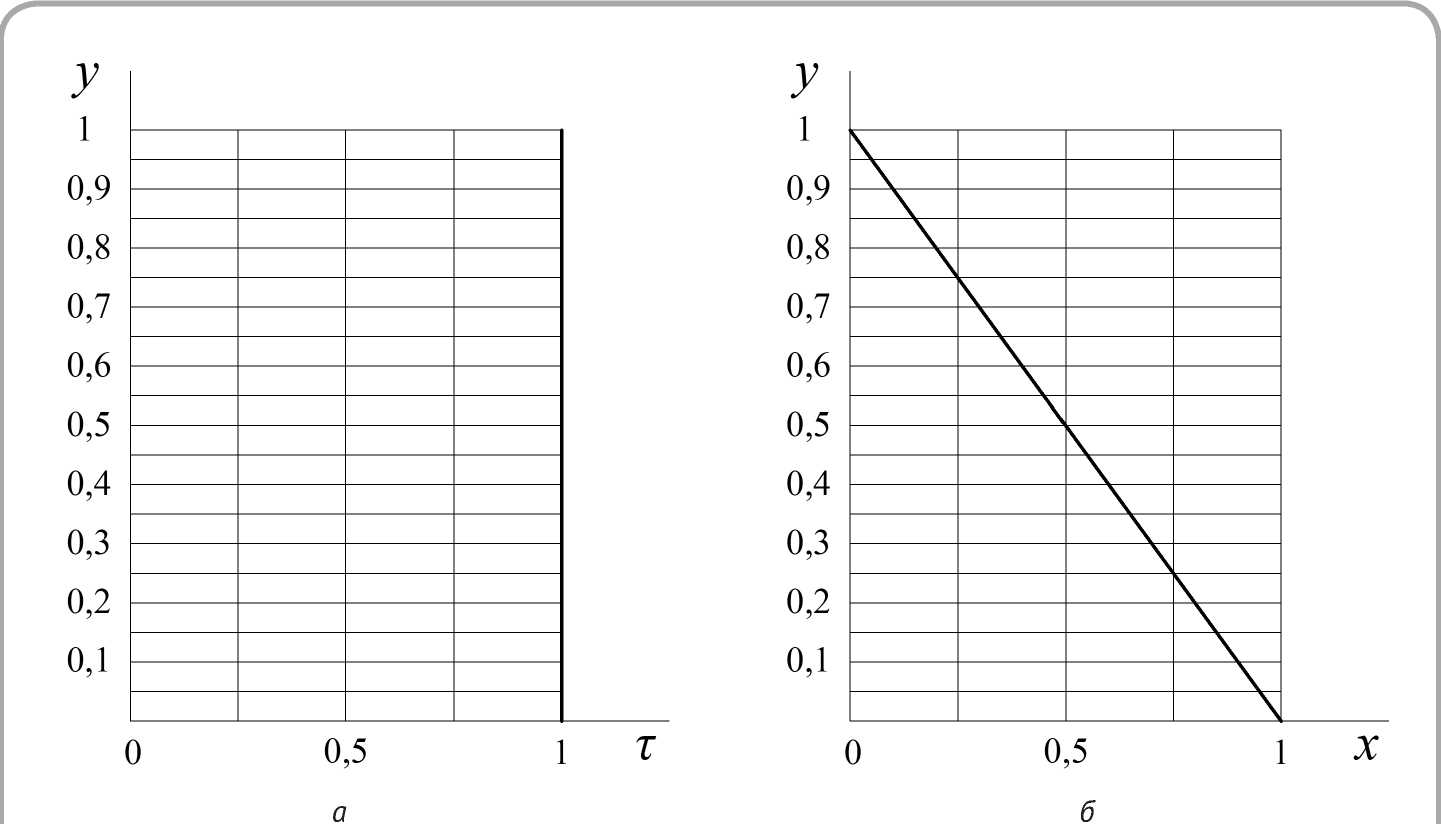
Рисунок 3 – Распределение касательных напряжений τ = f(y) = const (а) и соответствующий ему треугольный профиль канала x = f(y) (б)
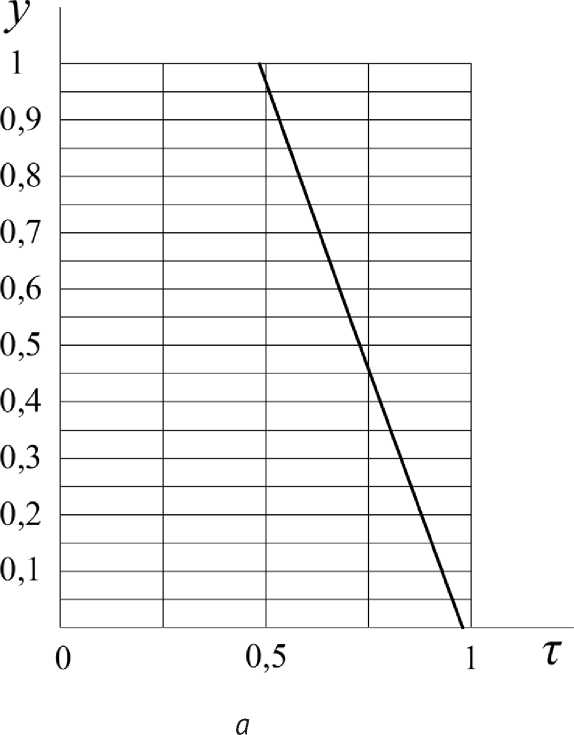
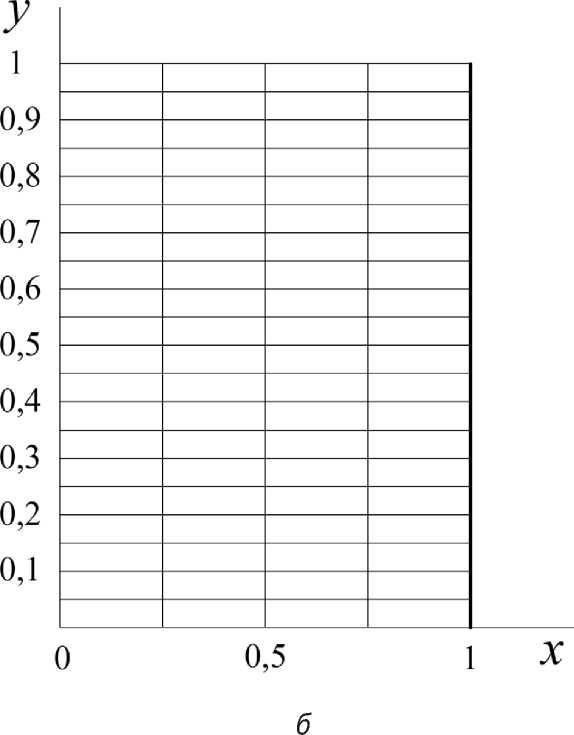
Рисунок 4 – Распределение касательных напряжений τ = f(y) (а) и соответствующий ему прямоугольный профиль канала x = f(y) = const (б)

Алгоритм и результаты расчетов по проектированию шнека представлены в таблице 2.
Разработка и применение прикладной САПР
В современной практике конструирования для выполнения расчётов и разработки конструкторской документации широко применяются трехмерные CAD-системы, например, КОМПАС-
3D, SolidWorks, NX. Имеющийся базовый функционал таких систем позволяет автоматизировать множество операций, непосредственно связанных с геометрическим моделированием и получением на основе построенных моделей ассоциативных чертежей. Однако экструдеры – это специализированное оборудование, и для
Таблица 2 – Алгоритм и результаты расчетов параметров канала шнека
С целью автоматизации расчетов и построений моделей и чертежей формующего инструмента (экструзионной матрицы) и силовых шнеков выполнена экспериментальная разработка специализированной прикладной системы автоматизированного проектирования. Приложение интегрировано в САПР КОМПАС-3D через использование при написании программного кода интерфейсов прикладного программирования (API). Такая интеграция позволяет использовать для трехмерных построений геометрическое ядро системы КОМПАС-3D и на выходе получать готовые трехмерные модели и сборки деталей и узлов с рассчитанными оптимальными геометрическими характеристиками. Приложение содержит базу данных исследованных в рамках данной работы материалов и позволяет выполнять расчет и построение 3D-модели формующей головки, геометрический и силовой расчет шнека, а также расчеты допустимых скоростей вращения шнека при заданных геометрических параметрах. Практика показала, что реализация разработанных методик проектирования шнека и формующей головки в виде прикладной САПР способствует снижению времени подготовки конструкторской документации для этих наиболее ответственных и специализированных узлов шнекового экструдера. На основании выполненных расчетов и построенных 3D-мо-делей облегчается доработка конструкторской документации. Для примера на рисунках 5 и 6 представлены доработанные готовые чертежи из комплекта конструкторской документации на шнек и формующую головку экструдера, построенные с применением разработанной методики и прикладной САПР.
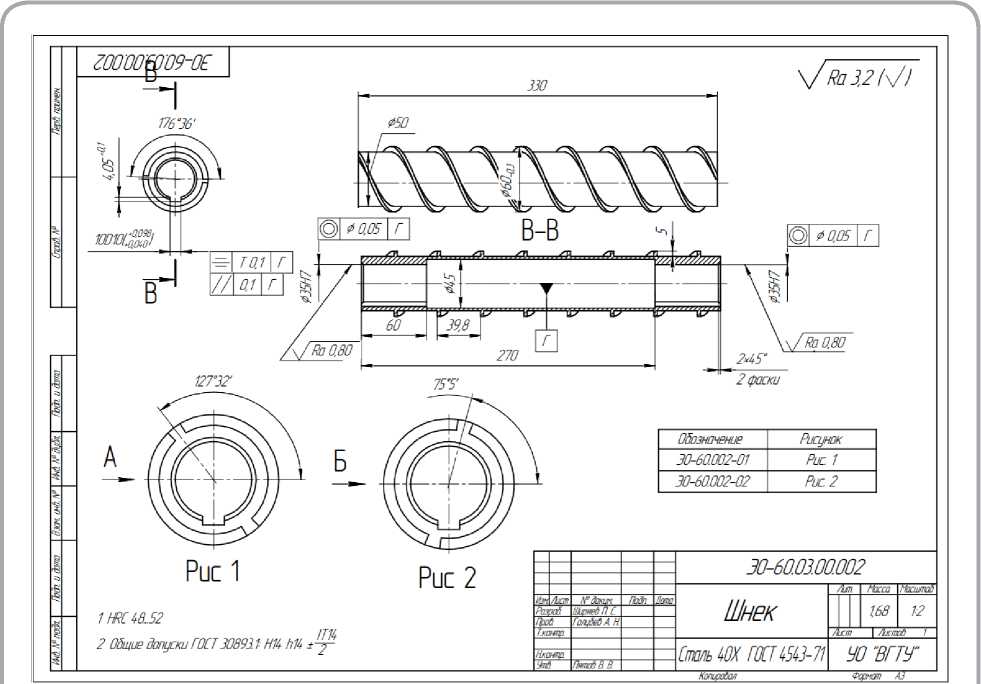
Рисунок 5 – Пример рабочего чертежа секции силового шнека экструдера
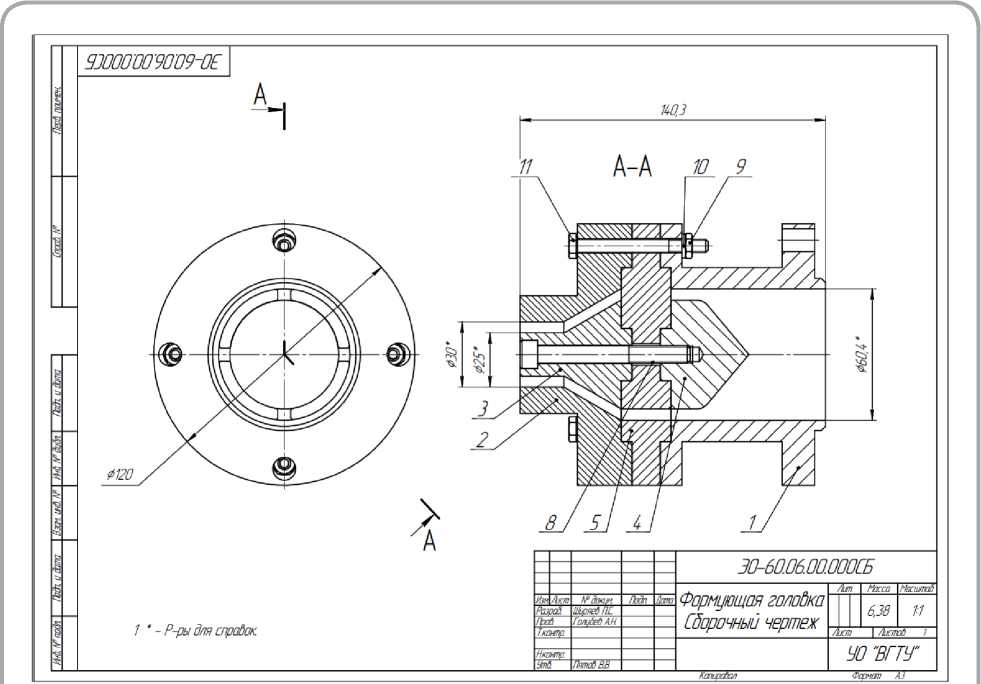
Рисунок 6 – Пример сборочного чертежа формующей головки экструдера
ВЫВОДЫ
Реализация разработанной выше технологии проектирования шнека и формующей головки в виде прикладной САПР способствует снижению времени подготовки конструкторской документации для этих наиболее ответственных и специализированных узлов шнекового экструдера. В свою очередь, узлы экструдера, включающие преимущественно типовые (не специализированные) детали машин (подшипниковые узлы, муфты, приводы, станины из сварных металлоконструкций), не требуют разработки специализированных приложений, их можно эффективно проектировать с применением базового функционала трехмерных САПР и их стандартных машиностроительных конфигураций.
Список литературы Методика проектирования экструзионного инструмента
- Цеменко, В. Н., Фук, Д. В., Ганин, С. В. (2016), Определение реологических характеристик и моделирование процесса экструзии порошковых пористых материалов. Часть 1. Порошковое тело, Научно - технические ведомости Санкт-Петербургского государственного политехнического университета, 2016, No 243, с. 124.
- Цеменко, В. Н., Фук, Д. В., Ганин, С. В. (2016), Определение реологических характеристик и моделирование процесса экструзии порошковых пористых материалов. Часть 2. Пористое тело, Научно - технические ведомости Санкт-Петербургского государственного политехнического университета, 2016, No 243, с. 134.
- Григорьев, А. А., Дмитрюк, А. И. (2020), Расчет технологических параметров экструзии брикетов порошков алюминия, Научно - технические ведомости СПбГУ, Естественные и инженерные науки, 2020, том 26, No 1, с. 53.
- Пятов, В. В. Экструзия пластично-вязкой среды : монография / В. В. Пятов, А. Н. Голубев ; УО "ВГТУ". - Витебск, 2018. - 211 с.