Методологические аспекты совершенствования технологического оборудования для технического обслуживания, ремонта, испытания, контроля и диагностики автотранспортных средств
Автор: Блянкинштейн И.М.
Журнал: Журнал Сибирского федерального университета. Серия: Техника и технологии @technologies-sfu
Статья в выпуске: 3 т.5, 2012 года.
Бесплатный доступ
В области совершенствования технологического оборудования для технического обслуживания, ремонта, контроля и диагностики автотранспортных средств имеются методологические проблемы. В результате их формализации и решения разработаны математические модели зависимостей выходных параметров автотранспортных средств от входных управляющих воздействий, методология анализа структуры, параметров и технологии применения лазерной измерительной системы, методика оценки конкурентоспособности, технического уровня и качества технологического оборудования, методика сертификации технологического оборудования по потребительским свойствам, концепции виртуальных средств контроля и диагностики параметров автотранспортных средств.
Технологическое оборудование, квалиметрия, сертификация, потребительские свойства, концепции контроля и диагностики автотранспортных средств
Короткий адрес: https://sciup.org/146114647
IDR: 146114647
Текст научной статьи Методологические аспекты совершенствования технологического оборудования для технического обслуживания, ремонта, испытания, контроля и диагностики автотранспортных средств
Технологическое оборудование для технического обслуживания и ремонта (ТОиР), испытания, контроля и диагностики автотранспортных средств (АТС) является важной составляющей производственно-технической базы автотранспортных и автосервисных предприятий, станций диагностики и испытательных центров. Технический уровень технологического оборудования влияет на все основные показатели и аспекты деятельности названных предприятий: производительность, качество и себестоимость ТОиР, испытаний и контроля АТС, условия труда персонала и его безопасность, ресурсосбережение, защиту окружающей среды и безопасность АТС, а следовательно, и на эффективность работы предприятия в целом. Поэтому разработка научно-методических основ совершенствования и использования технологического оборудования представляет значительный резерв повышения эффективности, безопасности и снижения затрат при производстве и эксплуатации АТС.
Названное особенно актуально для оборудования и средств измерения, используемых для контроля параметров АТС в процессе ТОиР, при проведении государственных технических осмотров, сертификационных испытаний и пр. Являясь наиболее наукоемким классом технологического оборудования, концептуально построенным в соответствии с требованиями действующих стандартов и правил испытаний, контрольное оборудование в ряде случаев предполагает участие человека в реализации процедур испытаний, что обусловливает влияние человеческого фактора на результаты испытаний и измерений. В результате субъективных оценок в эксплуатацию могут выпускаться АТС, потенциально небезопасные для окружающей среды и человека. Поэтому разработка новых концепций технологического оборудования для контроля параметров АТС, не зависящего от человеческого фактора, тесно связана с совершенствованием действующей нормативной базы: нормативов и требований, установленных техническими регламентами, а также методов испытаний и измерений, изложенных в стандартах и правилах.
В смежных отраслях науки и производства появляются и находят применение новые эффективные виды измерителей, например, лазерные инструменты, виртуальные средства контроля и диагностики на основе систем технического зрения, но в силу специфики измерений параметров автомобилей и отсутствия методологии создания и применения таких средств они пока не находят широкого использования в сфере производства и эксплуатации АТС.
Общей методологической проблемой, касающейся всех классов технологического оборудования, выступает несовершенство методов оценки конкурентоспособности, технического уровня и качества образцов и, в частности, отсутствие методики аналитического определения весомости основных свойств, что важно не только для выбора и эффективного использования образцов, но и для оценки эффективности конструкторско-технологических решений по видам технологического оборудования.
Весомую роль в повышении конкурентоспособности и качества технологического оборудования должна играть его сертификация по потребительским свойствам. Однако сложившаяся на сегодняшний день система добровольной сертификации продукции по потребительским свойствам не востребована рынком, в том числе и по причинам методологического характера. Следовательно, совершенствование методологии сертификации технологического оборудования также является важной научно-практической проблемой.
Решение комплекса указанных проблем осложняется недостатком сведений о закономерностях процессов формирования показателей контролируемых свойств АТС, обусловленных влиянием человеческого фактора, а также о потенциальных свойствах и технических параметрах технологического оборудования, методологии его создания, оценки и применения.
Формализация объекта исследования
Решение обозначенных проблем предполагает создание теоретических основ контроля параметров АТС и совершенствование оборудования с учетом закономерностей, проявляющихся в системе «Оператор - АТС - технологическое оборудование - средство измерения -среда».
Формализованная с позиций системного подхода схема процесса измерения параметров АТС, включающая участников процесса измерения, их внешние и внутренние взаимосвязи, – 264 –
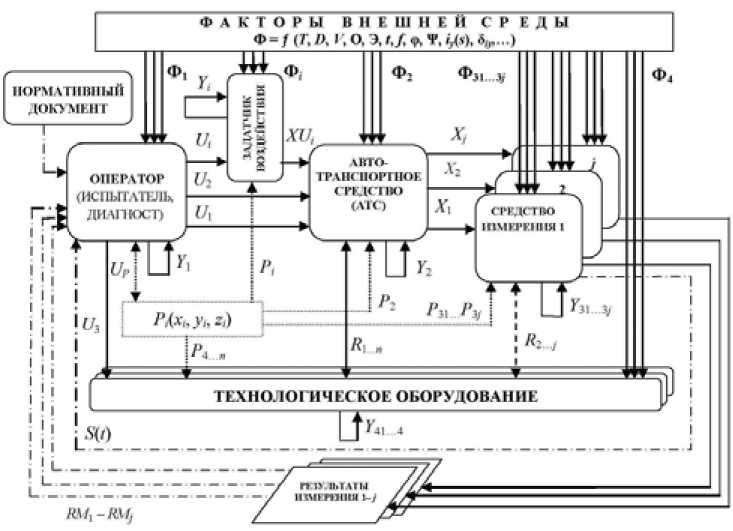
Рис. 1. Структурная схема системы «Оператор – АТС – технологическое оборудование – средство измерения – среда»: аналоговый входной управляющий сигнал или выходной параметр; информационная связь представлена на рис. 1. Правилоустанавливающим документом для испытания или диагностирования АТС является стандарт или методика, регламентирующие процедуру испытаний по данному свойству. Руководствуясь требованиями этого нормативного документа (НД), оператор в соответствии со своим пониманием методики готовит и реализует процедуру испытаний. В процессе испытания оператором на объект подаются управляющие воздействия U,, U2, ., Ui, предусмотренные НД (например, нажатие на педаль акселератора, нажатие на педаль тормоза и т.п.). При этом на выходе объекта испытаний измеряются функциональные параметры Х, Х2, ..., Xj, которые характеризуют качество процесса функционирования объекта (например, дымность отработавших газов (ОГ), расход топлива и т.п.). Иногда для создания управляющих воздействий могут применяться специальные технические средства – задатчики управляющих воздействий.
Внешними факторами, воздействующими на всех участников системы, являются параметры окружающей среды (на схеме - векторы Ф 1 , Ф2 , Ф31-3 j , Ф 4 , .., Ф i ). В общем случае к ним можно отнести следующие параметры: Т - температура окружающей среды, °С; D - атмосферное давление, мм рт. ст.; V – влажность воздуха, %; О – освещенность, лк; Э – электромагнитные излучения; t - время, с; f - коэффициент качения колеса; ф - коэффициент сцепления; Т - коэффициент общего дорожного сопротивления; iy ( 5 ) - продольные уклоны участка (макропрофиль дороги, %); 5 iy - микропрофиль дороги, мм, и пр. Внешняя среда влияет на всех участников процесса измерения: на психофизиологическое состояние оператора, характер формирования и результаты протекания рабочих процессов в узлах и агрегатах испытуемого АТС и технологического оборудования, процессы, протекающие в измерительном приборе.
Каждый участник процесса измерения характеризуется собственными внутренними параметрами, оказывающими влияние на функционирование рассматриваемой системы. Например, внутренние параметры оператора, влияющие на процесс измерения, - это Y 1 = /( Y antr , Y phiz , Y psih , Y intel ), т.е. его антропометрические ( Y antr ), физиологические ( Y phiZ ), психические ( Y psih ) данные, интеллектуальные способности ( Y intel ) и пр. Внутренние параметры испытуемого АТС Y 2 = f(Y st , Y usm , Y ts , ..) и технологического оборудования Y 41 = /(Y st , Yt s , —) — это параметры технического состояния ( Yst ), параметры используемых эксплуатационных материалов ( Y usm ), тепловой режим ( Y ts ) и пр. Внутренние параметры применяемых средств измерений Y 31 = / (Y st , Y mch , Yts , ...) - это также параметры их технического состояния ( Y st ), метрологические характеристики ( Y mch ), тепловой режим ( Y ts ) и др.
В общем случае процесс измерения функциональных параметров объекта испытаний осуществляется следующим образом. Предварительно должно обеспечиваться регламентированное нормативным документом взаимное расположение АТС, средств измерений и оператора (управляемый фактор P i ( x i , у, z i ), реализуемый дискретно). Однако, как показывает опыт, в случае контроля, например геометрических параметров АТС указанному фактору зачастую не уделяется должного внимания и в эксплуатационной документации к измерительным системам отсутствуют четкие рекомендации по параметрам взаимного расположения.
Далее, согласно нормативному документу, оператором проводятся подготовительные операции по задействованию технологического оборудования, предусмотренного методикой испытаний, по обеспечению мер безопасности при измерении, прогрев испытуемого АТС, прогрев и, при необходимости, калибровка средства измерения и т.п. В соответствии с рекомендациями нормативного документа и пошаговыми инструкциями S ( t ), предусмотренными программным обеспечением применяемого прибора, оператор воздействует на орган(-ы) управления испытуемого АТС (например, входное управляющее воздействие U । - угол поворота рычага управления подачей топлива дизеля), а выходные характеристики (например: X । - дымность ОГ; X 2 - частота вращения коленчатого вала; X j - прочие факторы) регистрируются измерительным прибором, анализируются на предмет корректности, усредняются и в виде результата измерения сообщаются оператору (на схеме обозначено информационной связью RM ).
Технологическое оборудование, используемое при испытаниях, диагностике, ТОиР АТС, характеризуется широким разнообразием функциональных возможностей и показателей назначения. Вопрос комплексной оценки технического уровня и качества технологического оборудования методологически не решен в должной мере, что при широком предложении на рынке оборудования затрудняет как его выбор при приобретении, так и определение направления совершенствования конструкции при модернизации. Анализ процесса формирования системы показателей качества технологического оборудования на этапах жизненного цикла (рис. 2) показывает, что один из важных инструментов повышения качества продукции – сертификация по потребительским свойствам в отношении технологического оборудования – не работает, в результате чего потребители на рынке технологического оборудования не имеют объективной информации о качестве образцов оборудования, что затрудняет его выбор.
Из анализа формализованных схем процессов, приведенных на рис. 1 и 2, можно сделать следующие выводы.
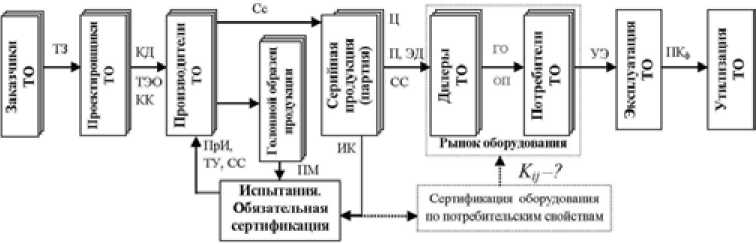
Рис. 2. Формирование информации о показателях качества технологического оборудования на этапах жизненного цикла: ТЗ – техническое задание; КД – конструкторская документация; ТЭО – техникоэкономическое обоснование; КК – карта технического уровня и качества продукции; Сс – себестоимость; ПрИ – протоколы испытаний; ТУ – технические условия; СС – сертификат соответствия требованиям безопасности; ПМ – программа-методика испытаний; ИК – инспекционный контроль; Ц – цена; П – паспорт; ЭД – эксплуатационная документация; ГО – гарантийные обязательства; ОП – обучение персонала; УЭ – условия эксплуатации; ПК ф – показатели качества фактические; K ij – комплексный показатель качества образца оборудования; существующая схема; отсутствующее звено
-
1. При стабильных или искусственно зафиксированных значениях факторов внешней среды и неизменных внутренних параметрах ведущая роль в проведении измерений остается за человеком .
-
2. В силу сложившихся традиций и уровня развития измерительной техники и технологии при испытании и диагностировании АТС характер формирования во времени управляющих воздействий U(t) не регистрируется измерительными приборами либо не учитывается при обработке результатов измерений . В действующих нормативных документах по испытанию АТС процесс реализации управляющего воздействия U 1 , возлагаемый на оператора, не всегда сформулирован четко и конкретно, что обусловливает возможность его вариаций и, как следствие, наличие значительных разбросов результатов измерений. Например, при измерении дымности ОГ дизелей по ГОСТ Р 41.24 – 2003 (Правила ЕЭК ООН № 24) процесс воздействия на орган управления трактуется следующим образом: «…При работе дизеля в режиме холостого хода быстрым , но не резким нажатием на педаль газа обеспечивают максимальную подачу топливного насоса, которую поддерживают до достижения дизелем максимальной частоты вращения и включения регулятора…». В этой формулировке отсутствуют количественные характеристики входного управляющего воздействия. Аналогичные расплывчатые формулировки можно обнаружить и в других нормативных документах, касающихся испытания АТС.
-
3. При контроле геометрических параметров АТС недостаточно внимания уделяется фактору Pi(хi, уi, zi) – параметрам взаимного расположения контролируемого АТС и измерительного прибора .
-
4. Вопрос комплексной оценки технического уровня и качества технологического оборудования не решен методологически, что при широком предложении на рынке технологического оборудования затрудняет как его выбор при приобретении, так и определение направления совершенствования конструкции при модернизации .
-
5. Добровольная сертификация оборудования по потребительским свойствам как инструмент повышения качества продукции не работает вследствие несовершенства ее мето- – 267 –
дологии, что препятствует развитию технологического оборудования и средств контроля на новых методологических принципах .
Следовательно, предстоит установить связь, построить математические модели и получить научно обоснованные оценки влияния управляющих воздействий на результаты измерения функциональных параметров АТС Х 1 и Х 2 , разработать методологию и получить комплексные оценки K kj технического уровня и качества образцов технологического оборудования, сформулировать методологию его сертификации по потребительским свойствам, разработать концептуальные и теоретические основы создания виртуальных средств контроля и диагностики параметров АТС на основе элементов систем технического зрения.
В формализованном виде первый функционал можно представить как
Х(t ) = / ( U , ( t ), U 2.j = const), (1)
где Х i ( t ) - выходной функциональный параметр АТС (дымность ОГ дизелей на режиме свободного ускорения, расход топлива, плавность хода и пр.); U 1 ( t ) - функция перемещения педали управления подачей топлива; t - время . Все другие внешние и управляемые параметры принимают постоянные значения (неизменны).
Второй функционал можно представить как
Х - = / ( P i ( х , У, z), U v. = const), (2)
где Х 2 - погрешность измерения геометрических параметров АТС; P i ( x i , уi , z) - параметры взаимного расположения контролируемого АТС и элементов 3D-лазерной измерительной системы.
Третий функционал можно представить как
K kj = / ( Q 1 , Q 2 , Q i , j, Q n ), (3)
где Kkj - комплексный показатель качества j -го образца оборудования, j = 1, j, m ( m - количество образцов технологического оборудования в рассматриваемом массиве); Qi - свойства технологического оборудования, i = 1, ..., n ( n - количество рассматриваемых свойств технологического оборудования).
Методология и основные результаты решения задач
Для анализа закономерностей формирования оценок показателей контролируемых свойств АТС, обусловленных влиянием индивидуальных данных человека (функционал 1), разработаны статические и динамические модели, отражающие характер формирования выходных параметров АТС в зависимости от входных управляющих воздействий, на примере измерения дымности ОГ дизелей в режиме свободного ускорения.
Статические модели построены на основе корреляционно-регрессионного анализа зависимостей максимальной (пиковой) дымности ОГ на режиме свободного ускорения от параметров режима испытания (времени перемещения педали управления подачей топлива от фт!п до фтах) в виде аддитивных (составных) моделей вида
D = D „уст + ae-,b , (4)
n max где Dуст - измеренное значение дымности (%, м-1) в установившемся режиме на максималь-nmax ной частоте вращения коленчатого вала; ae–bt – составляющая дымности, учитывающая режим свободного ускорения, a и b – коэффициенты уравнения; t – длительность режима свободного ускорения, с.
Динамические модели построены на основе дифференциальных и разностных уравнений с использованием метода последовательной линеаризации (МПЛ) [1].
Наилучшие результаты дала модель с двумя входами (первый вход – положение педали управления подачи топлива u[t ], второй вход - частота вращения коленчатого вала u t[ t ]) второго порядка и выходом (дымность ОГ) y [t] четвертого порядка:
y [ t ] = а 1 ' y [ t — 1] + а 2 ' y [ t — 2] + a 3 ' y [ t — 3] + а 4 ' y [ t — 4] + а 5 ' u [ t — 1] +
+ а 6 ■ u [ t — 2] + а 7 ■ U i [ t — 1] + а ■ и [ t — 2], (5)
y [0] = y [—1] = y [—2] = y [—3] = 0, где αi – коэффициенты уравнения.
В результате расчетно-экспериментальных исследований выявлена зависимость формирования показателей дымности ОГ дизелей на режиме свободного ускорения от входного управляющего воздействия: темп нажатия на педаль управления подачей топлива влияет на величину дымности ОГ дизелей и его необходимо учитывать при измерении.
Построенные статические и динамические модели зависимости дымности ОГ дизелей на режиме свободного ускорения от темпа нажатия на педаль управления подачей топлива позволили количественно установить, что показатели дымности ОГ отечественных автомобилей, находящихся в реальной эксплуатации, не укладываются в оговоренный ГОСТ Р 52160–2003 диапазон устойчивости 0,25 м–1. Поэтому необходимо либо увеличить допустимый диапазон устойчивости дымности ОГ, либо контролировать темп нажатия на педаль управления подачей топлива датчиком и корректировать дымность ОГ с учетом его показаний [2].
Разработанная концепция измерения дымности ОГ дизелей на режиме свободного ускорения, основанная на регистрации темпа нажатия на педаль управления подачей топлива и приведения результата измерения дымности ОГ к стандартизированному значению темпа, позволяет исключить влияние человеческого фактора на результаты измерений, снизить вероятность ошибки при оценке технического состояния АТС, разбросы в результатах измерений и, как следствие, сократить продолжительность измерений и затраты на них (патент РФ № 2215276).
Задача оценки влияния фактора P i ( x i , y i , z i ) - параметров взаимного расположения контролируемого АТС и измерительного прибора – на среднеквадратические отклонения (СКО) измерений (функционал 2) рассмотрена на примере лазерной измерительной системы на основе трех излучателей, работающих в дискретном режиме определения координат контрольных точек АТС.
Для решения задачи был разработан алгоритм расчета погрешности измерения геометрических параметров АТС, элементы которого применяются при решении навигационных задач, а именно вариант определения теоретической погрешности на основе активно-дальномерного метода расчета координат точек [3]. При этом определение – 269 – положения точки на поверхности АТС и ее СКО сведено к решению системы уравнений второго порядка численным методом, а в качестве измеряемого параметра при определении пространственных координат принимали расстояния от измерителей до контрольных точек автомобиля – дальность.
Результат измерения можно представить в общем виде как
R изм i = R i + A (6)
где R i – истинное значение дальности; Δ – среднеквадратическая погрешность измерения.
Связь дальности с координатами в пространстве определяется системой уравнений
R i = V ( x-x ) 2 + ( У. - У ) 2 + ( zz ) 2 , (7)
где i = 1, ..., 3 - текущий номер лазерного измерителя; x i , y i , z i - пространственные координаты i -го лазерного измерителя; x , y, z - искомые координаты контрольной точки на поверхности автомобиля.
Система уравнений с тремя неизвестными (7) решалась итерационным методом Гаусса– Ньютона. Координаты начального приближения x 0, y 0, z 0, используемые для первоначального решения системы, определены из априорных данных о месте контрольной точки. Для линеаризации уравнений использовался ряд Тейлора.
В результате решения задачи для различных вариантов расположения элементов системы выявлена зависимость формирования среднеквадратических погрешностей измерения 3D-лазерными системами от расположения элементов измерительной системы между собой и относительно контролируемого АТС. Эти факторы необходимо учитывать и оговаривать в правилах по эксплуатации измерительных систем.
Разработанная методология анализа позволила научно обосновать следующие требования к структуре, параметрам и технологии применения дискретной лазерной измерительной системы, обеспечивающим минимальную среднеквадратическую погрешность измерения геометрических параметров АТС в условиях эксплуатации:
-
1) расстояния D между измерителями дискретной лазерной системы и до контролируемой точки должны быть равными, т.е. образовывать равностороннюю пирамиду;
-
2) при измерении отрезка L между контрольными точками АТС грани пирамиды должны быть не меньше его длины.
При отклонении от указанных требований происходит увеличение среднеквадратических погрешностей измерения геометрии АТС в соответствии с моделью экспоненциального вида c усеченным двумерным полиномом 3-го порядка в показателе степени
A = a 0 • exp[ a t D + a 2 D 2 + a 3 L 2 + a 4 L 2 D + a 5 L 2 D 2 + a 6 L 3],
R2 = 0,89-0,99, (8)
где R2 - коэффициент детерминации.
Разработанные концепции лазерных измерительных систем для определения геометрических параметров АТС в условиях эксплуатации позволяют бесконтактным способом осуществлять измерения без использования специальных мишеней (патенты РФ № 2239505, № 2291751, № 2314492) [4].
Для решения задачи разработки методологии оценки технического уровня и качества технологического оборудования, применяемого при ТОиР, испытаниях и контроле параметров АТС (функционал 3), использованы элементы классической квалиметрии.
При рассматриваемом подходе формируется массив однородного по назначению оборудования, для каждого образца которого требуется найти комплексный показатель технического уровня и качества, а сам массив ранжировать.
Согласно квалиметрии совокупность свойств, формирующих качество оборудования, разлагается до уровня простых и измеряемых свойств. Комплексный показатель качества K kj оборудования определяется как среднее взвешенное арифметическое
n
кь= УО G, kj ssyi-'i, i=1
где Qij – простые свойства оборудования, i = 1, …, n – порядковый номер оцениваемого свойства образца оборудования ( n – количество рассматриваемых свойств оборудования), j = 1, …, m – порядковый номер образца оборудования ( m - количество образцов оборудования в рассматриваемом массиве); Gi – коэффициенты весомости свойств оборудования.
Поскольку значения отдельных показателей свойств имеют разные единицы измерения, проводится нормирование значений этих показателей по следующей формуле:
q - q 6р
K j = ~j ч‘ , (10)
-
4 qY - qip
где Ку - нормированный (относительный) показатель i-го свойства j-го образца оборудования; бр эт qi – браковочное значение i-го показателя; qi – эталонное значение i-го показателя.
Итоговая оценка качества j- го варианта объекта может быть вычислена по формуле
n
K kj = Z K j G i , i = 1
где Kkj - комплексный показатель качества j -го объекта.
Неизвестные значения коэффициентов весомости получали из решения системы линейных алгебраических уравнений
K 11 G 1 + K 21 G 2 + ^ + K n 1 G n + C - K k 1 ,
K 12 G 1 + K 22 G 2 + ... + K n 2 G n + C - K k 2 ,
K 1 m G 1 + K 2 m G 2 + ^ + K nm G n + C - K km .
В правой части уравнений системы (12) значения Kkj заменяли значениями общего показателя эффективности Э j образцов технологического оборудования (прибыль за нормативный срок службы), полученными на основе имитационного моделирования работы образцов технологического оборудования в идентичных условиях эксплуатации с заданной производственной программой. Используя показатели эффективности, полученные для каждого образца (из массива) технологического оборудования в идентичных условиях эксплуатации, аналитически рассчитывали коэффициенты весомости свойств технологического оборудования и комплексный показатель качества K kj каждого образца.
Проведенная по изложенной методике оценка технического уровня и качества массива автомобильных двухстоечных подъемников показала, что известные в отрасли методические подходы к оценке технического уровня и качества технологического оборудования, основанные на условии равновесомости свойств либо на их экспертных оценках, не всегда правомерны. В этой связи представляется целесообразной комплексная оценка технического уровня, качества и конкурентоспособности технологического оборудования на основе квалиметрии с элементами имитационного моделирования.
Аналитически рассчитанные коэффициенты весомости одних и тех же свойств для различных условий эксплуатации (загрузки поста) принимают различные значения. Это означает, что в разных условиях эксплуатации сильнее проявляются и становятся более значимыми те или иные свойства технологического оборудования.
Рассчитанный комплексный коэффициент качества имеет высокую тесноту связи с прибылью от использования технологического оборудования (R2 = 0,78-0,89), что подтверждает обоснованность использования его в качестве критерия эффективности и конкурентоспособности технологического оборудования для ТОиР АТС.
Анализ технического уровня и эффективности различных видов технологического обо -рудования по предложенной методике позволяет оценивать конкурентоспособность образцов, выявлять показатели и свойства, оказывающие наиболее весомое влияние на качество технологического оборудования для ТОиР и определять пути его повышения [5].
В рамках решения задачи совершенствования методологии сертификации технологического оборудования по потребительским свойствам предлагается видоизменить парадигму добровольной сертификации, дополнив традиционный подход вариантом
K k 1 > K k 2 > K k 3 > K kj > - > K km , (13)
где Kkj - комплексный показатель качества j -го объекта, j = 1, ..., m ( m - количество образцов оборудования в рассматриваемом массиве).
Таким образом, предлагается, используя методологию определения комплексного показателя K kj технологического оборудования, изложенную выше, ранжировать массив конкурентных образцов оборудования и удостоверять ранжированный ряд образцов сертификатом. Предлагается название «Сертификат потенциальных свойств изделия». Выдавать такие сертификаты должны независимые и компетентные органы по сертификации, получившие аккредитацию на данный вид работ. Названный сертификат будет удостоверять, что образец продукции А лучше (на основании комплексного показателя качества Kkj ) образца В, а образец В лучше С и т.д. – для конкретных условий эксплуатации.
Наличие сравнительной информации по техническим характеристикам и комплексному показателю качества образцов продукции позволит потенциальным приобретателям грамотно выбрать оборудование для своих специфических условий эксплуатации и тем самым «голосовать рублем» за качественную и соответствующую их условиям продукцию, а также вследствие имеющегося авторитета всей сертификационной отрасли подстегнет производителей к совершенствованию потребительских свойств производимой ими продукции.
В рамках решения поставленных задач сформулированы концептуальные и теоретические основы создания виртуальных средств контроля и диагностики параметров АТС с использованием элементов систем технического зрения, исходя из которых научно обоснованы:
-
• метод виртуального измерения дымности ОГ дизелей, предусматривающий видеосъемку и обработку в режиме реального времени изображений ОГ на фоне черно-белого экрана, отличающийся от известных тем, что позволяет разделять поток ОГ на компоненты, формирующие черноту ОГ (частички сажи), и компоненты, формирующие белизну ОГ (белесые частички несгоревшего топлива, масла и паров воды), а также проводить их раздельную обработку и анализ в дальнейшем. Разделение дымности ОГ на черные и белесые компоненты, а также прямое измерение цвета изображений ОГ дизелей в системе RGB предлагаемым методом значительно повышает информативность оценки технического состояния дизелей и обеспечивает снижение затрат на диагностирование АТС и его себестоимости (патент РФ № 2366930);
-
• метод виртуального контроля суммарного люфта рулевого управления, предусматривающий регистрацию веб-камерами входного (тестового) воздействия на рулевое колесо и выходного воздействия (реакции) управляемого колеса, а также вычисление суммарного люфта рулевого управления, основанное на элементах аналитической геометрии по координатам точек, выделенных на изображениях с синхронизированных кадров двух видеопотоков (патент РФ № 2457457 от 27.07.2012), в режиме реального времени.
Заключение
Таким образом, методология системного подхода к совершенствованию технологического оборудования для контроля параметров АТС с учетом закономерностей, проявляющихся в системе «Оператор - АТС - технологическое оборудование - средство измерения - среда», позволяет формализовывать объекты исследований и находить новые решения задач, способствующих повышению технического уровня, качества и конкурентоспособности отечественного технологического оборудования для ТОиР, испытаний, контроля и диагностики АТС.