Методологические принципы выбора состава и разработки технологии нанесения плазменных защитных покрытий
Автор: Докукина И.А.
Журнал: Известия Самарского научного центра Российской академии наук @izvestiya-ssc
Рубрика: Механика и машиностроение
Статья в выпуске: 3-2 т.11, 2009 года.
Бесплатный доступ
В настоящей статье автор формулирует основные методологические принципы проектирования плазменных технологий получения специальных покрытий. Определены выходные параметры управления состоянием технологической системы и свойствами получаемых покрытий.
Методологические принципы, плазменные технологии, получение специальных покрытий
Короткий адрес: https://sciup.org/148205467
IDR: 148205467
Текст научной статьи Методологические принципы выбора состава и разработки технологии нанесения плазменных защитных покрытий
Разработка технологии получения защитных покрытий, как и любая технология, базируется на определенных методологических принципах, которые позволяют существенно упростить пути достижения конечной цели – повышение ресурса, надежности и технико-экономической эффективности летательных аппаратов за счет создания на поверхности деталей этих изделий специальных функциональных слоев [1].
Практика показывает, что в основном разработка ТЗ на проектирование функционального слоя ложится на технолога, т.е. он вынужден в каждом конкретном случае заниматься фундаментальными и прикладными проблемами различных научных направлений, осуществляя выбор материалов и конструкции многослойных функциональных слоев (рис 1, поз. 5.), в том числе с возможностью внесения конструктивных изменений в деталь.
При этом необходимо иметь в виду, что не существует универсальных материалов для функциональных слоев даже одного технического назначения. Например, триботехнические материалы, хорошо зарекомендовавшие себя при одних температурах и в условиях жидких смазок, могут быть совершенно не эффективными при других температурах, других смазках или их отсутствии.
Кроме того, говоря о функциональном слое, необходимо иметь в виду, что в абсолютном большинстве случаев речь должна идти о необходимости создания многослойной и многофазной системы, в которой каждая компонента системы решает свои функциональные задачи. Причем, в понятие функциональный слой необходимо включать приповерхностный слой детали, подвергнутый специальной обработке перед нанесением покрытия.
Создание такой многокомпонентной системы определяется не только условиями эксплуатации наружного слоя, а и необходимостью согласования термомеханических, химических, электрических и других свойств каждого из слоев между собой и конструкционным материалом детали.
Однако практика показывает, что выбор материалов функционального слоя определяет только потенциальные возможности этого слоя. Степень же достижения этих возможностей определяется технологическим методом его получения. Практика также показывает, что не существует
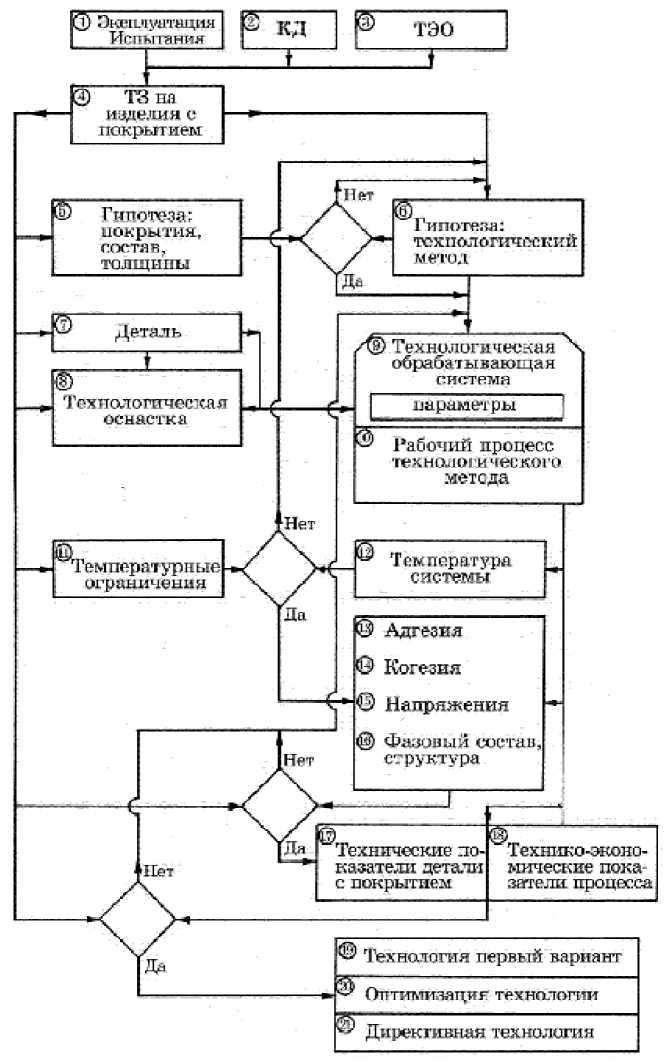
Рис. 1. Схема процесса проектирования технологии получения изделия с покрытием
универсального технологического метода, в должной степени пригодного для большинства задач создания функциональных слоев. Каждый метод имеет свою область эффективного применения, как по виду и структуре материала в слое, так и по технико-экономическим показателям. Следовательно, под каждую конкретную задачу должен подбираться оптимальный технологический метод напыления (рис. 1, поз. 6).
Таким образом, разработка технологии получения ЗП должна базироваться на многовариантности решений по составам покрытий и методам их получения, а также учитывать зависимость служебных характеристик покрытий от технологического метода его получения, свойств поверхности, на которую оно наносится, и условий эксплуатации изделия.
В абсолютном большинстве случаев покрытия наносятся на готовые детали, прошедшие соответствующую термообработку. Это приводит к необходимости соблюдения ограничений на диапазон изменения температуры { Т } при напылении (рис. 1, поз. 7). Температурные ограничения и возможности технологического метода (ТМ) приводят к термодинамическим ограничениям на скорость и полноту протекания топохимических, гетерогенных и плазмохимических реакций образования химических связей и химических соединений.
Такие ограничения могут приводить к тому, что выбранный ТМ перестанет удовлетворять задачам ТЗ по качеству покрытия и технико-экономическим показателям по производительности, себестоимости и т.д.
В связи с этим возникает необходимость решения двух больших фундаментальных проблем технологии напыления.
Первая проблема - создание высокоинформативных экспериментальных методов и математических моделей определения температурных полей в многослойных системах в период их формирования (рис. 1, поз. 12).
Вторая проблема – разработка физических принципов получения покрытий, при которых возникает возможность преодолевать термодинамические и теплофизические ограничения за счет активации протекания реакций, применения специальных физико-химических эффектов и технологических приемов.
Однако решение этих двух проблем еще не позволяет перейти к проектированию технологии напыления, т.к. общеизвестно, что получаемые покрытия могут самопроизвольно разрушаться под действием временных и остаточных напряжений как в процессе напыления, так и остывания детали с покрытием или на ранних стадиях испытания и эксплуатации изделия.
Действительно, только после установления диапазона управляющих параметров ТМ (рис. 1, поз.9), при которых температура в системе покрытие-основа не превышает допустимые для данных материалов ограничения (поз. 11), а покрытие не отслаивается и не разрушается под действием механических временных и остаточных напряжений, возникающих при напылении (поз.13-15), можно переходить к оптимизации процесса для обеспечения нужных эксплуатационных свойств изделия с покрытием.
Это приводит к необходимости решения третьей крупной проблемы технологии напыления - создание высокоинформативных экспериментальных методов и математических моделей определения остаточных напряжений, возникающих в многослойных системах в период их формирования (поз. 15).
Следовательно, в методологическом плане при разработке технологии напыления можно выделить специфические проблемы, характеризующие конкретную деталь и конкретный функциональный слой, а также две общие проблемы, которые в математическом плане являются подобными для разных материалов и методов напыления.
В соответствии с приведенной итерационной схемой (рис. 1) только после решения перечисленных задач можно переходить к получению функциональных слоев заданного состава и структуры, к выявлению уровня получаемых физико-механических и эксплуатационных показателей с последующей их оптимизацией и разработкой директивных технологий (поз. 17-21).
Технологический процесс, как и любой технологический процесс представляет собой сложную систему, разработка которой должна проводиться в рамках общесистемного подхода с привлечением системного анализа [2, 3]. При таком подходе создание математической модели технологического процесса базируется на создании ряда частных, но взаимосвязанных моделей, описывающих определенные стороны сложной системы.
Важнейшим этапом математического моделирования является структуризация сложной системы и корректное выделение входных, управляющих, возмущающих и выходных параметров для всей системы в целом и для каждого выделенного структурного элемента.
В качестве входных параметров общей системы при разработке технологии с конкретным типом средств технологического оснащения можно выбрать параметры, описывающие эксплуатационные свойства детали без покрытия (геометрические размеры, микротвердость, шероховатость, износостойкость, коэффициент трения, предел прочности, предел выносливости, коэффициент отражения электромагнитных волн и т.д.). Тогда выходными будут параметры, описывающие эти эксплуатационные свойства, но уже детали с покрытием. Важным элементом управления сложной технологической системы является то, что к группе выходных параметров необходимо отнести также параметры, описывающие технико-экономические свойства самой технологической системы (энергоемкость, производительность, вероятность выполнения технологического задания по данному параметру и т.д.). На основе выходных технологических параметров детали и технико-экономических параметров системы может быть составлена управляющая целевая функция, с помощью которой проводится комплексная оптимизация самой технологической системы и выбор значений управляющих параметров для достижения целей оптимизации.
Формирование выходных параметров и изменение их значений осуществляется в результате воздействия управляющих параметров на состояние технологической системы и физикохимический механизм протекания конкретных процессов изменения свойств детали с наращиваемым на ней покрытием.
Управляющие параметры могут быть разбиты на две группы: регулируемые и нерегулируемые. Регулируемые параметры – это параметры режима обработки, т.е. те технологические параметры, значение которых можно оперативно изменить при управлении процессом.
Нерегулируемые управляющие параметры – это такие параметры, которые описывают свойства конкретной детали и свойства конкретной технологической обрабатывающей системы. Эти параметры при получении покрытия на конкретной детали и конкретном оборудовании невозможно изменять оперативно, но они оказывают большое влияние на свойства получаемого изделия с покрытием.
Влияние свойств детали и обрабатывающей системы, которые должны быть формализованы и выделены в управляющие нерегулируемые параметры, является сложной конструкторско-технологической задачей, без решения которой невозможно дальнейшее совершенствование технологии получения ЗП.
Возмущающие факторы приводят, с одной стороны, к статистическому разбросу управляющих и выходных параметров, а с другой стороны, могут приводить к таким систематическим изменениям в свойствах детали с покрытием, которые относят к нестабильности самой технологии. Например, конструктивные особенности обрабатывающей системы могут создавать условия для возникновения микроду-говых привязок на детали в процессе напыления, особенности вакуумной системы могут создавать условия для повышенного содержания углеводородных компонент в остаточной атмосфере камеры, недостаточный и неравномерный прогрев камеры перед ее разгерметизацией может приводить к повышенной конденсации паров воды на стенках внутри вакуумной камеры и т.д.
В соответствии с задачами системного анализа на следующем этапе выделяются структурные блоки технологического метода, проводится системный анализ этих структурных блоков и выделяются входные, выходные и управляющие параметры для каждого структурного блока. При этом выходные параметры одного блока должны быть входными для следующего блока. На этом этапе при системном анализе конкретного блока необходимо перейти от технологических управляющих параметров к физическим. Такой переход определяется тем, что большинство технологических управляющих параметров имеют косвенное отношение к реальным физико-химическим механизмам технологического метода. Действительно, например, ток дуги при плазменном газо-термическом напылении влияет на температуру (энтальпию) плазменной струи и, следовательно, на температу- ру нагрева порошка. Но энтальпия плазменной струи также зависит от состава и расхода плазмообразующего газа. Поэтому анализ нагрева порошка удобнее проводить, выделив в качестве управляющего физического параметра энтальпию плазменной струи, а ее зависимость от тока дуги, состава и расхода плазмообразующего газа рассматривать в отдельном структурном блоке.
Таким образом, только после выделения физических управляющих параметров возникает возможность перехода к математическому моделированию реального процесса. Физические управляющие параметры по такому же принципу, как и технологические управляющие параметры, подразделяются на регулируемые и нерегулируемые. Нерегулируемые физические параметры часто называют параметрами состояния системы.
Проведенная структуризация технологического метода получения ЗП позволяет перейти к разработке математических моделей подсистем технологического метода (микроуровень САПР ТП) и выделения с их помощью минимально достаточного количества управляющих воздействий и безальтернативных рекомендаций. Безальтернативные рекомендации в качестве требований к деталям, покрытиям и процессу должны дополнять исходные данные для постановки задач проектирования. В то же время минимизированное количество управляющих воздействий должно обеспечить эффективное управление эксплуатационными свойствами деталей с покрытием в рамках решения либо прямых задач математического моделирования, либо задач оптимального проектирования.
Проводимые исследования и обзор литературных данных показывают, что необходимым предварительным условием разработки износостойкого покрытия является выбор совокупности параметров, определяющих уровень служебных характеристик поверхностного слоя. При анализе влияния параметров на ресурс изделия целесообразно разделить их на две группы. В одну внести свойства, определяющие характер взаимодействия изделие-контртело, а в другую – свойства, определяющие изнашивание собственно поверхности.
Первая группа определяет потенциально достижимый уровень износостойкости и связана в основном с физико-механическими особенностями материала: твердость, шероховатость, химическая инертность и т.д. Накопленные теоретические знания позволяют в этом случае прогнозировать износостойкость.
Ко второй группе характеристик относится уровень напряжений и дефекты, возникающие на поверхности при напылении и эксплуатации покры- тия и определяющие реальную скорость ее износа.
Как показывают исследования динамики износа, свойства второй группы имеют большее значение для результирующей износостойкости, так как износ определяется в большинстве случаев не непрерывным износом, а локальным разрушением, инициируемым остаточными напряжениями и дефектами покрытия. Таким образом, параметры второй группы определяют в какой степени потенциальные возможности параметров первой группы могут быть реализованы.
Список литературы Методологические принципы выбора состава и разработки технологии нанесения плазменных защитных покрытий
- Барвинок В.А. Плазма в технологии, надежность, ресурс. М.: Наука и технологии, 2005. 452 с.
- Барвинок В.А., Богданович В.И., Плотников А.Н., Докукина И.А. Математическое моделирование и физика процесса нанесения плазменных покрытий из композиционных плакированных материалов/Межд. центр научной и техн. информации. М.: 1998. 98 с.
- Барвинок В.А. Термомеханика формирования напряжений и тепловых полей в телах с изменяемой геометрией. М.: Наука и технологии, 2007. 306 с.