Методы измерения уровня загрузки мельниц, основанные на физических процессах современных централизованных систем смазки
Автор: Сибирцева Н.Б., Потапенко А.Н., Семилетов Н.А.
Журнал: Известия Самарского научного центра Российской академии наук @izvestiya-ssc
Рубрика: Достижения физики, химии, электроники и нанотехнологий
Статья в выпуске: 4-3 т.12, 2010 года.
Бесплатный доступ
Современные системы автоматического регулирования централизованных маслостанций, применяемые для смазки трущихся частей мельниц различного типа, предоставили новые возможности для разработки «интеллектуальных» систем измерения уровня загрузки мельниц. Эти системы позволят повысить эффективность функционирования автоматизированных систем управления мельницами в целом, что важно как с позиции энергосбережения, так и с позиции получения качества готового продукта.
Автоматизированная система, система смазки, мельница
Короткий адрес: https://sciup.org/148199458
IDR: 148199458
Текст научной статьи Методы измерения уровня загрузки мельниц, основанные на физических процессах современных централизованных систем смазки
Семилетов Николай Александрович, студент самоизмельчения, зумпф, насос гидроциклона, гидроциклон. Замкнутую схему обеспечивает гидроциклон, в верхней части которого при классификации выделяется готовый продукт, а пульпа из его нижней части возвращается в мельницу для дополнительного измельчения.
Подача исходного материала в мельницу – это один из этапов процесса измельчения, который может существенно повлиять на уровень загрузки (заполнения) мельницы и на потребляемую мощность электродвигателя этой мельницы. Увеличение уровня загрузки мельницы влияет на эффективность измельчения, так как это динамический процесс, и массы в этом процессе должны быть сбалансированными. Уровень загрузки мельницы может контролироваться по потребляемой мощности электродвигателя мельницы Р пр или по давлению масла в опорных подшипниках мельницы р м [3] (рис. 1). Для мельниц самоизмельчения стабилизация уровня загрузки барабана исходным материалом обеспечивается путём воздействия на частоту вращения привода питателя.
Из статических характеристик можно выделить два канала регулирования «потребляемая мощность Р пр – частота вращения привода питателя» или «давление масла р м – частота вращения привода питателя». В мельницах са-моизмельчения предлагается метод измерения уровня загрузки на основе совместного измерения давления масла в централизованных системах маслосмазки 2-х опорных подшипников питательной и разгрузочной цапф мельницы с помощью «интеллектуальных» датчиков давления, а затем осреднения полученных данных. Схема расположения систем централизованной смазки мельницы самоизмельче-ния показана на рис. 2.
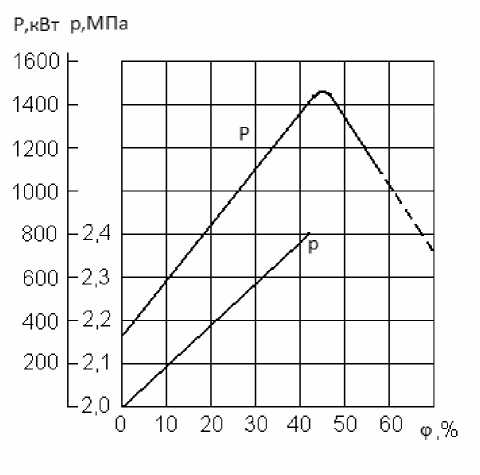
Рис. 1. Пример зависимостей Р пр и р м для мельницы самоизмельчения
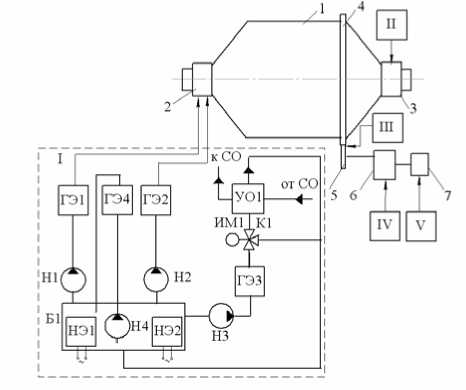
Рис. 2. Централизованные системы смазки мельницы самоизмельчения
Схема систем смазки мельницы самоиз-мельчения включает две централизованные системы жидкой смазки: питательного (I) и разгрузочного (II) подшипников цапф мельницы. Венцовая пара (III), подшипники редуктора привода (IV) и электродвигатель мельницы (V) обслуживаются специализированной станцией густой смазки [2]. Элементы оборудования (рис. 2) следующие: мельница самоиз-мельчения, питательная (2) и разгрузочная (3) цапфы, венцовая 4 и приводная 5 шестерни, редуктор 6 и электродвигатель 7. Загрузочная и разгрузочная части мельницы 1 включают цапфы 2 и 3, связанные с её торцевыми крышками и опираются на подшипники с баббитовой заливкой (смазываются жидкой смазкой). В состав централизованной системы подшипника 2 входят насосы высокого Н1 и низкого Н2 давления, циркуляционный насос Н3 для охлаждения масла, погружной насос Н4 для перемешивания масла в маслобаке, элементы гидросистем ГЭ1 – ГЭ4 (фильтры, обратные и предохранительные клапаны и др.), устройство охлаждения УО (маслоохладитель), через который по одним каналам циркулирует нагретое масло, а по другим – охлаждающая жидкость из системы охлаждения СО, регулирующий клапан К1 с электрическим приводом ЭМ и маслобак Б1 с нагревательными элементами НЭ. Локальные системы автоматического регулирования (САР) с помощью контроллеров обеспечивают регулирование температуры в контурах охлаждения масла подшипников мельницы самоизмельчения путем изменения расхода холодной воды через маслоохладитель УО.
В условиях непрерывной работы мельницы, высокие температуры ведут к опасным ситуациям для трущихся частей механизмов мельницы. В связи с этим в централизованных системах смазки предусмотрено охлаждение масла на базе маслоохладителя. Анализ режимов работы системы смазки мельницы показывает следующее. Во-первых, возможно получение первичной информации от датчиков давления, находящихся в системах централизованной смазки I и II (см. рис. 2), для использования этой информации в автоматизированной системе загрузки мельницы, так как изменяется давление при изменении степени загрузки мельницы. Во-вторых, для получения функциональной связи между загрузкой мельницы и давлением в гидросистеме насо-са/насосов систем централизованной смазки необходимо обеспечить стабилизацию расхода масла в системах I и II мельницы. В-третьих, необходимо предусмотреть компенсацию возмущающих воздействий в работе систем централизованной смазки I и II с учетом нагрева или охлаждения масла в различные периоды года. Для компенсации возмущающих воздействий в централизованных системах смазки подшипников предусмотрено основное охлаждение жидкой смазки маслобака Б1 на базе маслоохладителя УО1, как показано на рис. 3.
Для этой системы охлаждения масла предусматриваются условия, чтобы Б1 и УО1 находились в непосредственной близости от мельницы с возможностью регулирования температуры циркулирующей жидкой смазки на основе применения локальной САР3, что позволяет уменьшить время запаздывания в гидросистемах. Обозначения на схеме (рис. 3) следующие: маслобак Б1, насос Н3 с электроприводом М3, предохранительный клапан КП1, клапан обратный КО1, маслофильтры Ф1 и Ф2, реле перепада давления РД1 и РД2, шаровые краны К2-К8, трёхходовой клапан К1 с исполнительным механизмом ИМ1, маслоохладитель УО1 и система охлаждения СО.
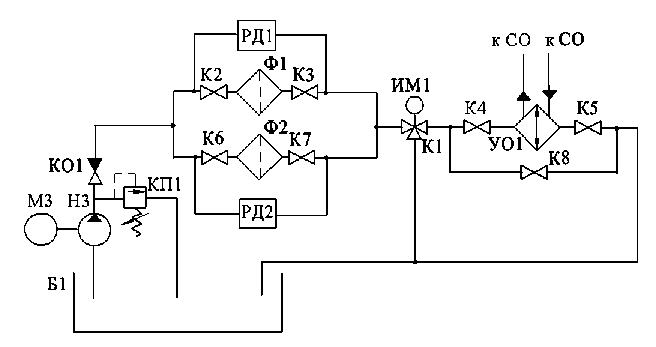
Рис. 3. Схема системы охлаждения жидкой смазки гидробака
Регулирование температуры жидкой смазки маслобака осуществляется при помощи изменения расхода жидкой смазки через маслоохладитель. Регулируемая величина локальной САР - температура масла, а регулирующая величина - расход жидкой смазки через УО1. Следует отметить, что выбранный канал регулирования позволяет практически исключить дополнительное охлаждение жидкости в маслоохладителе гидросистемы насоса низкого давления Н2. Как показала практика, уравнение динамики описываемого физического процесса можно представить в виде неоднородного дифференциального уравнения 2-го порядка следующего вида
Т 1 Т 2 d Tt2't) + ( Т +Т 2 )dTdr) + T0 (t) ^ k 1 G0 dt dt
, (1)
где k 1 - коэффициент передачи объекта управления (процесса охлаждения жидкой смазки); т 1 т 2 - постоянные времени распределённого объекта управления; Т о ( t ) - температура масла на сливе в бак Б1; G0 ( t ) - расход жидкой смазки через маслоохладитель УО1. Уравнение неразрывности струи с учётом разделения потоков с помощью трёхходового клапана К1 имеет следующий вид
G c ( t ) = G t ( t ) + G 1 ( t ) , (2)
где Gc ( t ) - расход жидкой смазки в трубопроводе на сливе жидкой смазки в Б1; G 1 ( t )- расход жидкой смазки через перемычку, связывающую трёхходовой клапан К1 с трубопроводом на сливе жидкой смазки в Б1. Учитывая, что GB = Gc= const в каждый момент времени ( GB ( t ) - расход жидкой смазки на входе трёхходового клапана К1), то из (2) следует соотношение:
G t ( t ) = G c ( t ) - G 1 ( t ) . (3)
Рассмотрим участок на сливе жидкой смазки в Б1 с учётом расход жидкой смазки через перемычку, связывающую трёхходовой клапан К1 с трубопроводом на сливе жидкой смазки в Б1 и расход жидкой смазки через маслоохладитель УО1. С учетом закона сохранения количества теплоты и уравнения (3) получим следующее выражение:
G c ( t ) Тс ( t ) = G 1 ( t ) Т в ( t ) + ( G c ( t ) - G 1 ( t )) Т о (t) , (4)
где Т с ( t ) - температура жидкой смазки в трубопроводе на сливе жидкой смазки в Б1; Т в ( t ) -температура жидкой смазки через перемычку, связывающую трёхходовой клапан К1 с трубопроводом на сливе жидкой смазки в Б1, причём температура жидкой смазки на вход трёхходового клапана К1 и температура жидкой смазки через перемычку равны; То ( t ) - температура жидкой смазки после маслоохладителя УО1. В этом случае мы получаем математическую модель исследуемого процесса в виде системы из 3-х уравнений (1), (2) и (4). В качестве способа исследования особенностей этого процесса на основе системы уравнений (1), (2) и (4) целесообразно использовать метод фазовой плоскости. В этой математической модели величина T 3( t ) является одним из регулируемых параметров. Это позволяет исследовать алгоритмы управления для локальных САР с учетом схемы (см. рис. 3) для обеспечения энергосбережения.
Применение подобных систем возможно и для многокамерных сепараторных цементных мельниц замкнутого цикла. Основной существующий метод измерения уровня измельчаемых компонентов в шаровых мельницах основан на электроакустическом принципе, заключающемся в измерении шума в одной из камер цементной мельницы, как правило, в 1-ой камере. Такой подход не позволяет определять уровень загрузки мельницы в камерах отдельно, что часто приводит к переизмельчению материала.
Выводы: применение гидравлического метода измерения, основанного на измерении давления масла в централизованных системах маслосмазки, совместно с электроакустическим позволит определить уровень загрузки мельницы, причём на основе данных датчиков давления в централизованной системе смазки уровень загрузки мельницы в целом, а на основе шумового сигнала – уровень загрузки первой камеры шаровой мельницы. Использование специализированного программно-технического комплекса даст возможность вычисления соотношения измельчаемых компонентов в её камерах, а также интеграцию этой системы в автоматизированную систему диспетчерского управления мельницами. Рассмотренные принципы позволят увеличить производительность мельниц и в целом повысят эффективность автоматизированной системы управления мельницами.
Список литературы Методы измерения уровня загрузки мельниц, основанные на физических процессах современных централизованных систем смазки
- Госман, А.И. Централизованные системы смазки для дробильно-измельчительного оборудования//Горная промышленность. 2004. №4. С. 29-32.
- Зябрев, М.А. Автоматизированные централизованные системы смазки горных и обогатительных машин/М.А. Зябрев, В.А. Зябрев, М.И. Шупиченко, М.В. Полянский//Материалы научно-практической конференции НПО «РИВС-2008». -СПб., 2008. С. 49-51.
- Троп, А.Е. Автоматическое управление технологическими процессами обогатительных фабрик/А.Е. Троп, В.З. Козин, Е.В. Прокофьев. М.: Недра, 1986. 303 с.