Моделирование процесса сверления с помощью SPH и конечно-элементного методов
Автор: Горбунов Игорь Вадимович, Ефременков Иван Валерьевич, Леонтьев Виктор Леонтьевич
Журнал: Известия Самарского научного центра Российской академии наук @izvestiya-ssc
Статья в выпуске: 1-5 т.16, 2014 года.
Бесплатный доступ
В статье рассматривается создание и исследование компьютерных моделей сверления титанового сплава методом SPH и методом конечных элементов (МКЭ или FEM). Модели предназначены для проведения исследований механической обработки и оптимизации технологических параметров резания.
Механическая обработка, сверление, моделирование
Короткий адрес: https://sciup.org/148202952
IDR: 148202952
Текст научной статьи Моделирование процесса сверления с помощью SPH и конечно-элементного методов
Экспериментальные данные. В качестве исходных данных и данных для сравнения при построении моделей процесса сверления были взяты результаты экспериментальных исследований сверления титанового сплава. Автор работы [1] провел эксперимент сверления титанового сплава Ti-6Al-4V сверлом (Greenfield Industries 44210), изготовленным из быстрорежущей стали класса M2. При сверлении скорость вращения шпинделя составляла 730 об/мин, подача сверла – 0,051 мм/об.
Общие параметры моделей. Для проведения исследований в CAD-системе Siemens NX по геометрическим параметрам (таблица 1) была построена твердотельная модель спирального сверла (рис. 1).
Таблица 1. Геометрические параметры сверла Greenfield Industries 44210
Параметр |
Значение |
диаметр сверла |
4 мм |
угол при вершине |
118 градусов |
угол наклона винтовой канавки |
30 градусов |
толщина поперечной кромки |
0,7 мм |
При проведении расчётов использовалась модель RIGID (абсолютно жесткий материал) режущего инструмента (спирального сверла) для уменьшения процессорного времени расчета. В качестве материала сверла использовалась быстрорежущая сталь Р6М5, являющаяся российским аналогом зарубежной быстрорежущей стали класса М2.
Модель заготовки представляет собой цилиндр, диаметр которого равен двум диаметрам сверла и имеет высоту 6,35 мм. В качестве упругих и пластических свойств материала заготовки, характеризующих диаграмму напряжённости (рис.
2), использовались физические свойства титанового сплава ВТ6 – российского аналога сплава Ti-6Al-4V. Связи, ограничивающие движение заготовки, накладывались на её боковую поверхность. Расчёт процесса сверления продолжался до прохождения режущим инструментом заготовки насквозь.
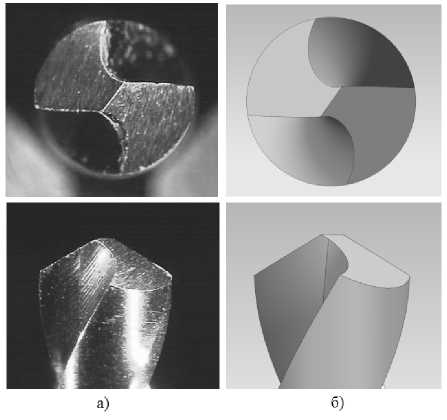
Рис. 1. Фотографии (а) и модель (б) применяемого спирального сверла
Моделирование заготовки и процесса сверления в LS-DYNA методом SPH. Метод SPH (Smoothed Particle Hydrodynamics – гидродинамика сглаженных частиц) является бессеточным Лагранжевым методом, в котором локальные системы координат движутся вместе с SPH частицами.
Согласно методу SPH заготовка представляется дискретными элементами, называемыми частицами. Эти частицы характеризуются пространственным расстоянием или «длиной сглаживания», обычно представляемым в уравнениях параметром h . Величина h характеризует расстояние, на котором свойства частиц «сглаживаются». Это значит, что любой физический параметр любой частицы получается суммированием соответствующих величин всех частиц, расположенных от неё на расстоянии 2 h .
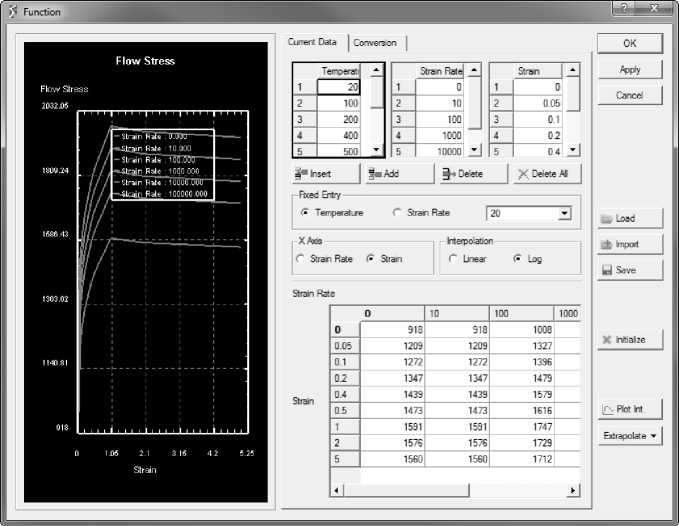
Рис. 2. Диаграмма напряжённости материала Ti-6Al-4V в DEFORM
Например, температура в точке t зависит от температуры всех частиц на расстоянии 2h от t . Влияние каждой частицы на свойства оценивается в соответствии с её плотностью и в соответствии с расстоянием от нее до интересующей частицы. Математически это описывается функцией ядра. В качестве функции ядра часто используется функция Гаусса. Такой принцип близкодействия позволяет экономить в расчётах вычислительные ресурсы, исключая относительно малое влияние отдалённых частиц. Значение любой физической величины A в точке X задаётся формулой:
A (X) = Ej mjA W(|X - Xj|,h), где mj - масса частицы j, Aj - значение величины A для частицы j, pj - плотность, связанная с частицей j, W – функция ядра.
Назначая каждой частице её собственную длину сглаживания и разрешая ей изменяться во времени, разрешающую способность симуляции можно подстраивать к локальным условиям.
Здесь приводятся результаты расчётов процесса резания, выполненных с использованием метода SPH [2] («SPH method applied to high speed cutting modeling»), которые говорят о том, что этот метод удобен в случае сильных деформаций, и что он полноценно отображает процесс отделения стружки. При этом время, затрачиваемое на вычисления, равно или незначительно ниже, чем при использовании метода конечных элементов, в котором проводится частая перестройка сетки и используется Лагранжево-Эйлерова формулировка ALE (рис. 3).
В модели материала используется тип состояния материала Plastic_Kinematic, в котором, помимо основных свойств учитываются свойства, отвечающие за пластическое состояние материала. Значения, описывающие свойства материала, содержатся в таблице окна интерфейса LS-Dyna (рис. 4). Важным является добавление нового пункта в список опций контроля метода решения. Для этого открывается пункт Control и в появляющееся окно вносятся параметры поведения заготовки в процес- се её резания.
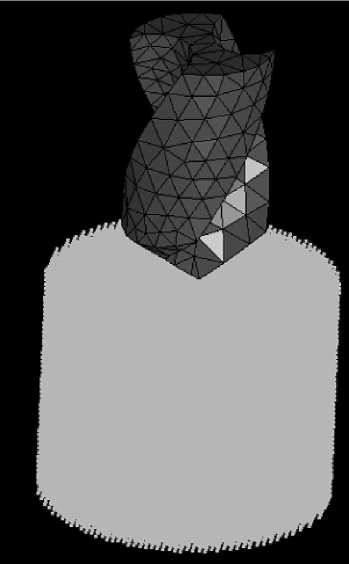
Рис. 3. Модель заготовки и экспортированная из Siemens NX модель сверла
В модели материала используется тип состояния материала Plastic_Kinematic, в котором, помимо основных свойств учитываются свойства, отвечающие за пластическое состояние материала. Значения, описывающие свойства материала, содержатся в таблице окна интерфейса LS-Dyna (рис.
4). Важным является добавление нового пункта в список опций контроля метода решения. Для этого открывается пункт Control и в появляющееся окно вносятся параметры поведения заготовки в процессе её резания.
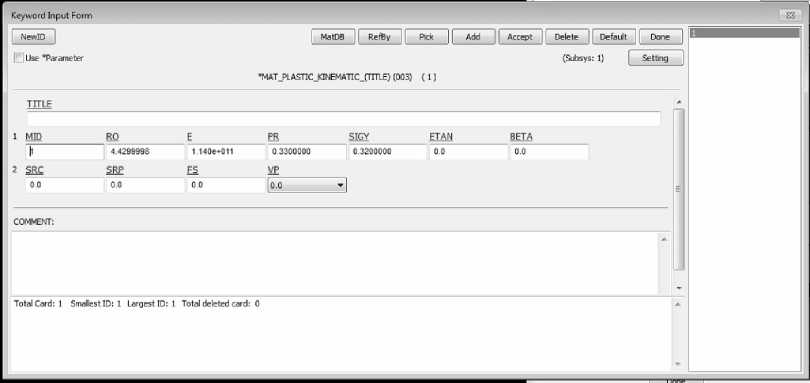
Рис. 4. Свойства заготовки в LS-Dyna
Моделирование процесса сверления в DEFORM конечно-элементным методом. Система DEFORM специализируется на создании и исследовании моделей процессов обработки материалов резанием и давлением. Программный пакет DEFORM содержит отдельные шаблоны для различных видов обработки материалов: ковки, прокатки, точения, сверления и др. Такие шаблоны позволяют быстро создавать различные модели обработки, не вдаваясь в конкретные особенности пакета и численных методов [3] . Пользователи задают только технологические параметры операций (скорость вращения шпинделя при осевой обработки, подача), твердотельные модели и свойства материалов режущего инструмента и заготовки.
Созданная в Siemens NX модель режущего инструмента была разбита на 3363 конечных элемента, содержащих 881 узел, с дополнительным сгущением сетки на конце сверла (рис. 5). Модель заготовки была создана с помощью встроенного в DEFORM модуля создания геометрии, а затем разбита на 10 тысяч конечных элементов со сгущением сетки в окрестности оси цилиндра.
Настройки решателя выбирались по умолчанию: тип решателя – Lagrangian Incremental, деформации вычислялись методом разрежённых матриц с использованием прямого итерационного метода. В процессе расчёта из-за больших деформаций заготовки и сгущения сетки модели в процессе расчета к заключительному этапу сверления заготовка стала принимать конусообразную форму (рис. 6). Это связано с небольшим (по сравнению с режущим инструментом) диаметром модели заготовки. Для предотвращения описанных деформаций диаметр модели заготовки был увеличен на 1/3.
Симуляция модели продолжалась более 104 часов с общим количество шагов по времени более
93500. В силу резко возросшего времени на вычисление последних шагов симуляция была приостановлена. Время решения шага занимало от 0,4 с на начальном этапе симуляции до 48 с в конце, не включая дополнительное время, потраченное на перестроение конечно-элемент-ной сетки. Большую часть времени (92-97%) составляло проведение вычислительных итераций деформации объектов. В процессе симуляции система DEFORM провела более 8000 автоматических перестроений конечно-элементной сетки заготовки. Общее время, затраченное на перестроение конечно-элементной сетки – 27 часов 12 минут. В процессе симуляции модель режущего инструмента вошла в заготовку на глубину 3,38 мм, что эквивалентно 4,3 с сверления.
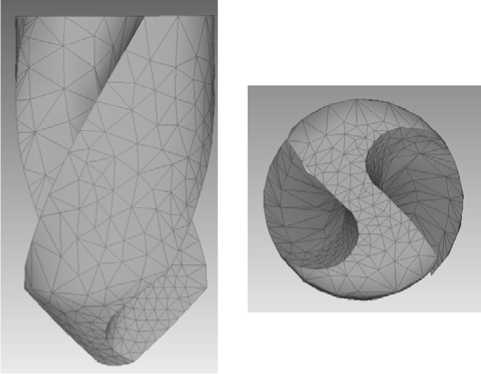
Рис. 5. Конечно-элементная сетка сверла в DEFORM
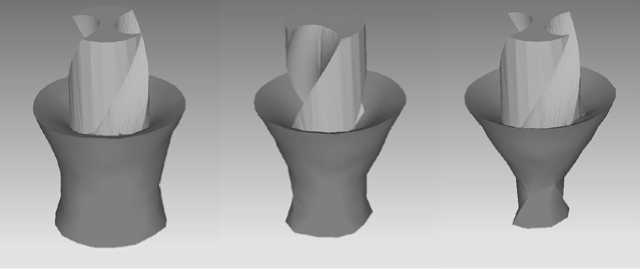
Рис. 6. Изменение геометрии заготовки в процессе симуляции сверления
Одной из особенностей полученных результатов является образование стружки только по одному режущему лезвию (рис. 7). Это было вызвано слишком большим размером конечных элементов при скорости подачи равной 0,051 мм/об. Малая скорость подачи привела к тому, что одно из режущих лезвий сверла, «срезая» часть заготовки, оставляло небольшое углубление (рис. 8а), а второе режущее лезвие деформировало заготовку без образования стружки (рис. 8б).
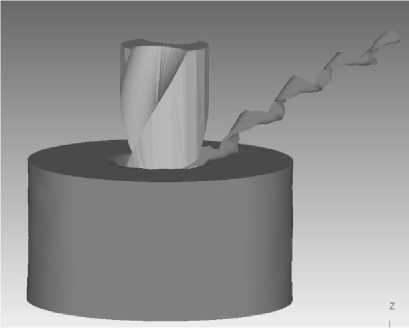
Рис. 7. Модель сверления в DEFORM
Анализ результатов. По результатам моделирования был проведен анализ использованных САЕ-систем. Время, потраченное на расчет процесса сверления в программном продукте LS-Dyna, заняло примерно 49 часов при количестве 18700 элементов SPH в заготовке и 1216 КЭ на инструменте. В системе DEFORM расчёт сверления модели заготовки, состоящей из 10014 конечных элементов, сверлом из 3363 конечных элементов занял более 104 часов. САЕ-система DEFORM выгодно отличается от LS-DYNA, поскольку значительная часть настроек модели задается автоматически, пользователь вводит только геометрические параметры объектов (или загружает их из СAD файлов), выбирает используемые материалы и задаёт технологические параметры обработки.
Создание контактного взаимодействия, теплопередача, ориентация твердотельных моделей инструмента и заготовки, выбор конечных элементов и настройка симуляции производятся автоматически. Это позволяет использовать данный пакет программ инженерам, не являющимся специалистами в области конечно-элементного моделирования, и быстро создавать и изменять модели механической обработки. При моделировании в LS-Dyna PrePost геометрию также можно экспортировать из любого CAD-продукта.
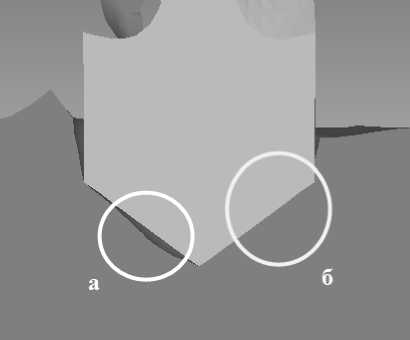
Рис. 8. Влияние модели сверла на модель заготовки при сверлении (разрез)
Для создания объекта методом SPH необходимо знать особенности этого метода и принципы его работы для задания его параметров. Помимо этого необходимо знать и другие значения для задания условий контакта инструмента и заготовки, типы материалов и другие параметры. При моделировании в DEFORM процесса сверления шаг между витками стружки увеличивался к концу расчёта. На 15470 шаге расстояние между витками составляло около 2,3 мм (рис. 9), а на 77578 шаге – около 4,2 мм (рис. 10). Диаметр конуса стружки был примерно одинаков – 1,5-1,7 мм.
Создание контактного взаимодействия, теплопередача, ориентация твердотельных моделей инструмента и заготовки, выбор конечных элементов и настройка симуляции производятся автоматически. Это позволяет использовать данный пакет программ инженерам, не являющимся специалистами в области конечно-элементного моделирования, и быстро создавать и изменять модели механической обработки. При моделировании в LS-Dyna PrePost геометрию также можно экспортировать из любого CAD-продукта.
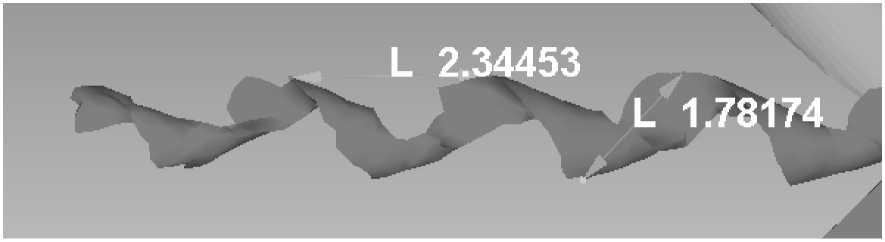
Рис. 9. Вид и геометрические параметры стружки на 15470 шаге
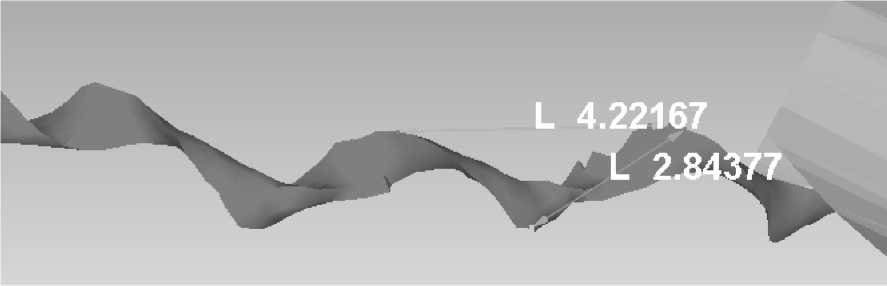
Рис. 10. Вид и геометрические параметры стружки на 77578 шаге
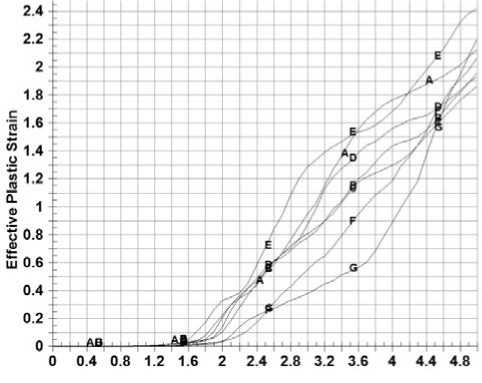
Рис. 11. График упругой деформации выбранных конечных элементов, расположенных в центральной области заготовки на пути движения сверла
схожих результатов необходимо настраивать процесс резания в методе SPH со сгущением элементов.
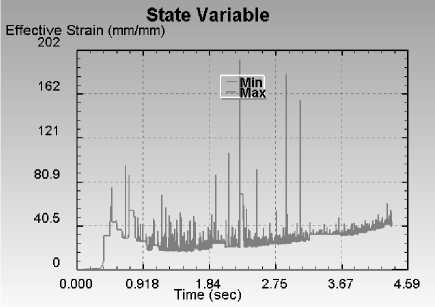
Рис. 12. График упругой деформации в заготовке после окончания расчета в DEFORM
График показывает, что в момент начала взаимодействия инструмента с заготовкой появляется упругая деформация. Этот момент характеризует процесс возникновения стружки в процессе сверления. Сравнивая эти данные с результатами статьи [2], в которой говорится, что график показывает ступенчатое возрастание деформации вплоть до уравновешенного состояния, можно сделать вывод, что метод SPH сглаживает показания во время расчета, усредняя получаемые результаты. График деформаций, полученный в LS-Dyna, показывает, что эти результаты отличаются от результатов, полученных с помощью DEFORM (рис. 12). Это связано, в первую очередь, с различными методами построения модели. Для получения
State Variable
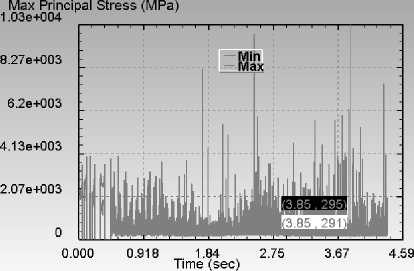
Рис. 13. Главные напряжения в заготовке по окончании расчета в программном продукте DEFORM
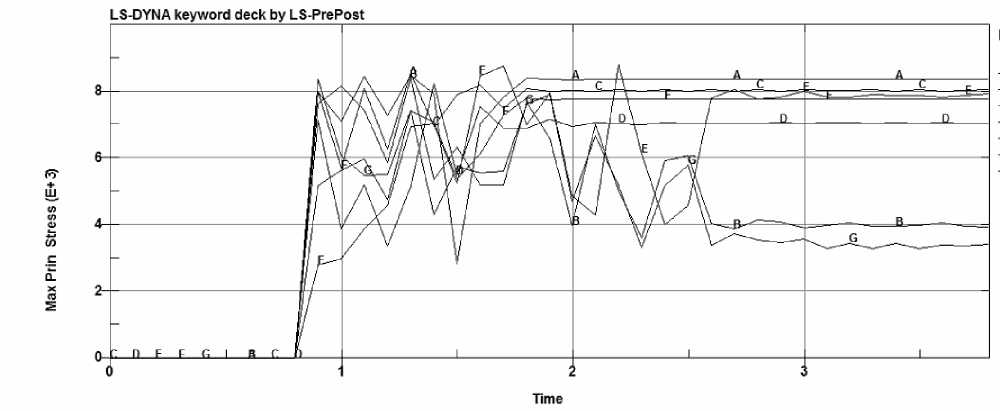
Рис. 14. Главные напряжения в конечных элементах заготовки, расположенных в центральной области заготовки на пути движения сверла
Кроме графиков упругих деформаций, в статье [2] показаны графики главных напряжений. После завершения расчета в DEFORM имеется график главных напряжений в заготовке (рис. 13). Результаты расчета в LS-Dyna главных напряжений, возникающих в заготовке, близки результатам, полученным в программном продукте DEFORM (рис. 14).
Выводы: конечно-элементный метод моделирования процессов сверления подходит для заготовок небольшой толщины при большой скорости подачи сверла – при таких условиях конечноэлементная сетка модели заготовки редко перестраивается. Метод SPH дает усредненные значения выбранных параметров, но для получения максимальных или минимальных результатов необходимо отдельно в настройках процесса вычисления задавать дополнительные условия. Кроме этого, метод демонстрирует «естественное» отделение элементов объекта при различных пластических и упругих деформациях, есть возможность рассмотреть поведение отдельных частиц. Сам процесс расчет регулируется и подстраивается под возможности вычислительной машины. Метод пригоден для создания различных процессов механообработки.
Работа выполнена в рамках государственного задания Минобрнауки России.
Список литературы Моделирование процесса сверления с помощью SPH и конечно-элементного методов
- Zhang, P.F. Mechanical drilling processes for titanium alloys: a literature review/P.F. Zhang, N.J. Churi, Z.J. Pei, C. Treadwell//Machining Science and Technology. 2008. Vol. 12, No. 4. Pp. 417-444.
- Limido, J. SPH method applied to high speed cutting modelling/J. Limido, C. Espinosa, M. Salaun, J. L. Lacome//International Journal of Mechanical Sciences. 2007. Т.49, №7. С. 898-908.
- Горбунов, И.В. Особенности моделирования процессов механической обработки в САЕ-системах/И.В. Горбунов, И.В. Ефременков, В.Л. Леонтьев, А.Р. Гисметулин//Известия Самарского научного центра Российской академии наук. 2013. Т. 15, № 4(4). С. 846-853.