Моделирование знаний в задаче поиска причин неисправностей
Автор: Димитров Валерий Петрович, Борисова Людмила Викторовна, Хубиян Капрел Луспаронович
Журнал: Инженерные технологии и системы @vestnik-mrsu
Рубрика: Процессы и машины агроинженерных систем
Статья в выпуске: 3, 2021 года.
Бесплатный доступ
Введение. В статье изложено описание подхода к решению задачи поиска причин неисправностей в сложных технических системах на основе моделирования знаний экспертов. Для решения задач диагностики многоуровневых систем, к которым относятся и зерноуборочные комбайны, широко применяются интеллектуальные информационные системы. Формальное описание знаний предметной области является основой построения базы знаний таких систем. Рассмотрена последовательность построения базы знаний экспертной системы, основанной на продукционных правилах. Материалы и методы. Подход базируется на использовании таблицы функции неисправностей. В качестве объекта диагностирования рассмотрена одна из подсистем электрооборудования зерноуборочного комбайна - «открытие створок крыши бункера». Основой построения последовательности элементарных проверок является система логических уравнений, описывающих как исправное, так и возможные неисправные состояния подсистемы. Результаты исследования. Сформирована структурно-логическая модель. В результате анализа таблицы функции неисправности определены совокупности элементарных проверок. Выполнен анализ весомости данных проверок на основе четырех критериев. Определена оптимальная последовательность проверок и построено дерево решений для поиска причины неисправности, которое является основой формирования базы знаний интеллектуальной информационной системы. Приводится фрагмент базы знаний. Обсуждение и заключение. Предложенный подход моделирования экспертных знаний повышает результативность работы блока поиска причин неисправностей интеллектуальной системы поддержки принятия решений. Он позволяет структурировать базу экспертных знаний и устанавливать оптимальную последовательность элементарных проверок. Это позволяет определить оптимальную последовательность применения продукционных правил базы знаний, что обеспечивает сокращение времени восстановления работоспособности комбайна.
Интеллектуальная информационная система, принятие решений, зерноуборочный комбайн, диагностика неисправностей, продукционные правила, база знаний
Короткий адрес: https://sciup.org/147236037
IDR: 147236037 | DOI: 10.15507/2658-4123.031.202103.364-379
Текст научной статьи Моделирование знаний в задаче поиска причин неисправностей
Эффективность и результативность уборки зерновых и других культур в значительной степени определяется сменным временем использования зерноуборочного комбайна. При этом основными процессами, помимо управления комбайном, являются технологическая настройка рабочих органов и поиск причин неисправностей [1].
Одним из перспективных направлений повышения эффективности является использование различных информационных технологий, которые на современных зерноуборочных комбайнах применяются в следующих направлениях1:
– контроль и регулирование режимов работы двигателя и рабочих органов;
-
- измерение и регистрация показателей процесса уборки (количество убранных площадей, бункерного зерна, влажность, «наработка» двигателя и других агрегатов и т. д.);
– индикация интенсивности потерь после очистки и молотильно-сепариру-ющего устройства (МСУ);
- автоматическая настройка комбайна на уборку определенной культуры, регулирование загрузки молотилки, вождение (для более поздних моделей) и др.
Целью настоящего исследования является разработка общей схемы формализации знаний предметной области «поиск неисправности» для построения модели в виде системы продукционных правил.
Обзор литературы
Оперативно найденная причина неисправности, которая является результатом реализации комплекса диагностических процедур, позволяет в полевых условиях избежать значительных потерь различного рода за счет снижения времени простоев комбайна. Однако диагностирование реализовано фрагментарно и выполняется в основном в следующем виде:
– штатное диагностирование МСУ, то есть измерение текущих значений параметров и фиксирование их предельных состояний в виде сообщений о несоответствиях. При этом диагноз формируется вручную лицом, принимающим решение (ЛПР), оператором;
– индикация кодов неисправностей (преимущественно для систем электрооборудования и электроники), что является визуализацией внешнего признака без преобразования его в вербальное описание. ЛПР при этом выполняет поиск причины вручную 2 .
Управление техническим состоянием современных сельскохозяйственных машин как мехатронных систем неразрывно связано с выполнением значительного количества диагностических процедур. Постановка диагноза предполагает необходимость обработки эвристических знаний. Эффективность реализации диагностирования определяется стратегией, принятой ЛПР, и зависит от его компетентности. Следовательно, некомпетентность ЛПР может нивелироваться наличием готового к использованию набора ранжированных стратегий поиска решения [2–5]. В связи с этим разработка и внедрение систем поддержки принятия решений при поиске причин неисправностей является актуальной.
Для решения задач диагностики предлагаются различные подходы. Рассматривается определение диагностических параметров топливной системы двигателей зерноуборочных комбайнов на основе технологических и конструктивных параметров технического состояния [6]. В результате исследований структурной схемы топливной системы двигателей определены параметры технического состояния ее элементов. Указывается, что применение технологических карт совместно с диагностическими средствами позволит снизить расход топлива на 5–10 %. Предлагается метод, основанный на сочетании нейронной сети BP (BPNN) и теории доказательств DS, для диагностики неисправности блокировки зерноуборочного комбайна [7]. В качестве объекта исследования рассматривались шнек жатки, молотильный барабан и зерновой шнек, а также измельчитель соломы [8]. Эффективность внедрения современных компьютерных систем технического диагностирования и их использования анализируется в ряде работ [9-12]. Отмечается важность определения оптимальной периодичности проведения проверок, при которой затраты на ремонт и потери от простоя машин будут минимальными [13].
В настоящее время активно развивается направление построения диагностических экспертных систем, основанных на методологии теории нечетких множеств [14–16].
Таким образом, анализ научно-исследовательских работ позволяет утверждать, что диагностика сельскохозяйственных машин ‒ это многоцелевой, многофакторный процесс. Число уникальных объектов, связанных с конструктивными особенностями машин велико. Широкое использование различных подсистем (автоматики, электрики, гидравлики и др.) приводит к развитию особенностей разработки алгоритмов поиска неисправностей. Важной является разработка приборной базы диагностики машин и организации технического обслуживания. Внедрение интеллектуальных информационных систем (ИИС) поддержки принятия решений становится перкспективным направлением совершенствования процесса поиска неисправностей в полевых условиях. В основе предлагаемого подхода формирования модели предметной области в виде системы продукционных правил, составляющих основу базы знаний ИИС, лежат построение таблиц функций неисправностей для анализа пространства состояний изучаемого объекта диагностирования и формирование структурно-логической модели, описывающей причинно-следственные связи элементов.
Материалы и методы
Один из эффективных и широко распространенных способов описания поиска причин неисправностей, то есть формирования рационального комплекса стратегий, основан на моделировании знаний экспертов. В связи с этим выбор формального описания семантических пространств предметной области становится центральной научной проблемой3. На рисунке 1 представлена обобщенная схема формализации предметной области.
Далее при анализе предметной области в качестве объекта диагностирования рассмотрена система электрооборудования зерноуборочного комбайна ACROS-550. Электрооборудование зерноуборочного комбайна является важнейшей подсистемой, на долю которой приходится до 30 % отказов [17]. Применяя принцип декомпозиции, по функциональному назначению выделим конечную подсистему «открытие створок крыши бункера» электрооборудования зерноуборочного комбайна.
Принципиальная схема данной подсистемы приведена на рисунке 2.
Рисунок 2 содержит следующие обозначения: FU1.1, FU1.2, FU3.1 – предохранители блока предохранителей 111.3732; FU 8.3, FU8.4 - предохранители блока предохранителей 46.3722; KV10, KV11, KV22 – реле 753.3777; SA2 - выключатель стартера и приборов ВК353; А6 – силовой привод DD24-21B5-24-385; А7 – пульт управления комбайна ПУ-142-03 ЮГИШ.426471.032; Or-1 - цепь провода 1 оранжевый; R-2 - цепь провода 2 красный; R-2A - цепь провода 2А красный; R-2C - цепь провода 2С красный; Y-20 - цепь провода 20 желтый; B-4 – цепь провода 4 черный; Р-80 – цепь провода 80 розовый; Р-81 – цепь провода 81 розовый; G-734 - цепь провода 734 зеленый; R-733 - цепь провода 733 красный; Bl-730 – цепь провода 730 голубой; Br-736 – цепь провода 736 коричневый; Or-737 - цепь провода 737 оранжевый.
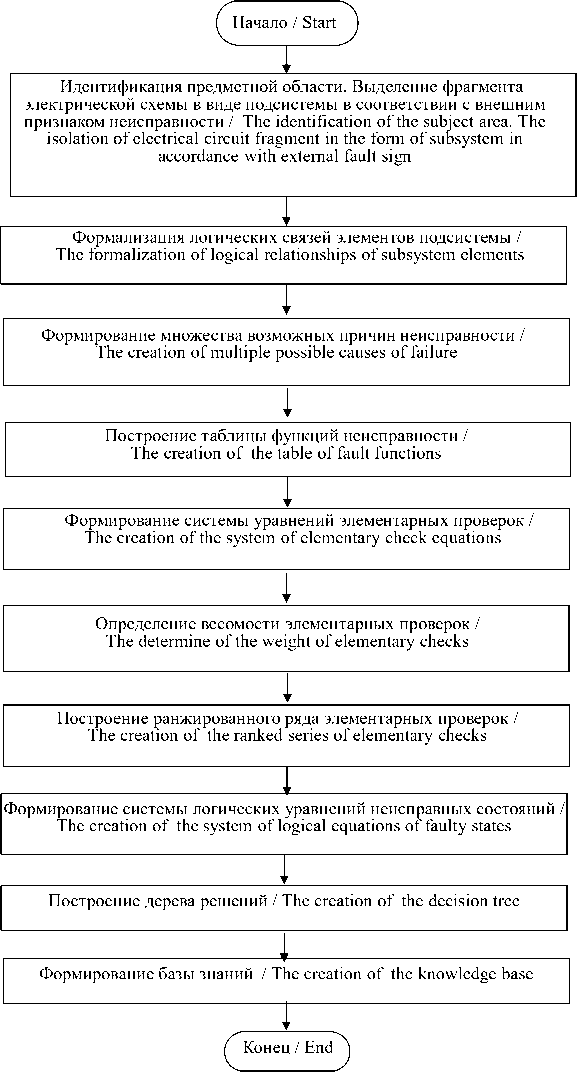
Р и с. 1. Схема этапов формализации задачи поиска неисправности
F i g. 1. Scheme of the steps to formalize the problem of troubleshooting
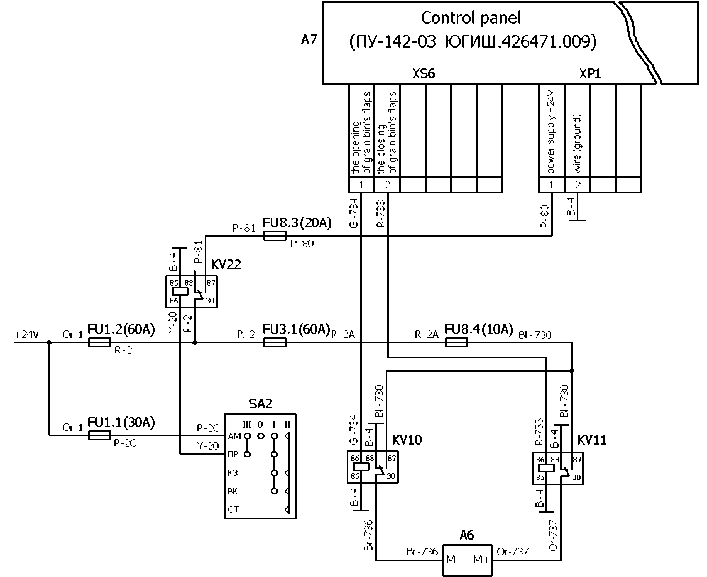
Р и с. 2. Фрагмент принципиальной схемы электрооборудования зерноуборочного комбайна ACROS-550. Подсистема «управление створками крыши бункера»
F i g. 2. Fragment of the circuit diagram of the ACROS-550 combine harvester electrical equipment. Subsystem “hopper roof flap control”
Пространство состояний изучаемой подсистемы может быть представлено в виде таблицы функции неисправностей (ТФН) (табл. 1) 4 .
При этом принято, что n j - обозначение элементарных проверок; e i - бинарное значение, характеризующее техническое состояние изучаемых элементов подсистемы (0 или 1); Rji – результаты проверок, значения которых представлены на пересечении строк πj и столбцов ei.
Структурно-логическая модель, описывающая причинно-следственные связи элементов подсистемы «открытие створок крыши бункера» и необходимая для построения ТФН, приведена на рисунке 3. Условные обозначения элементов подсистемы соответствуют рисунку 2.
Рисунок 3 содержит следующие обозначения: 1 - FU1.1; 2 - R-2C; 3 -SA2; 4 – FU1.2; 5 – B-4 (на выводе 85 обмотки реле KV22); 6 - Y-20; 7 - R-2; 8 – KV22; 9 – Р-81; 10 – FU3.1; 11 – FU 8.3; 12 - R-2A; 13 - Р-80; 14 - B-4 (в разъеме ХР1 ПУ-142-03); 15 – FU8.4; 16 - А7; 17 - Bl-730; 18 - G-734; 19 -B-4 (на выводе 85 обмотки реле KV10); 20 – B-4 (на выводе 88 нормально замкнутого контакта реле KV11); 21 – KV10; 22 – KV11; 23 – Br-736; 24 – Or-737; 25 – А6; Х 1 – внешнее
Т а б л и ц а 1
T a b l e 1
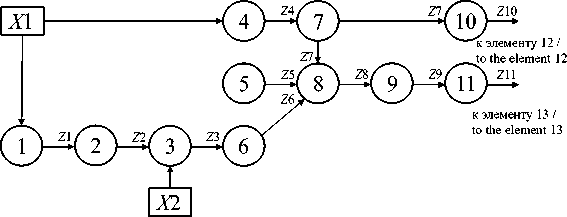
Z 22
Z 15
Z 10
Z 11
от элемента 10 / from item 10
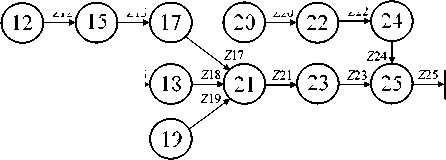
Z 12
Z 20
Z 17
Z 18
Z 23
Z 19
Z 13
Z 14
Z 16
от элемента 11 / from item 11
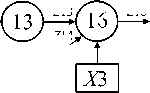
Y
ТФН подсистемы электрооборудования «управление створками крыши бункера» Troubleshooting table for the electrical equipment subsystem “hopper roof flap control” |
|||||||||||||||||||
Π |
г |
E |
|||||||||||||||||
e 0 |
e 1 |
e 2 |
e 3 |
e 4 |
e 5 |
е 6 |
е 7 |
е 8 |
е 9 |
е 10 |
e 11 |
e 12 |
e 13 |
e 14 |
e 15 |
e 16 |
e 17 |
e 25 |
|
π 1 |
1 |
0 |
1 |
1 |
1 |
1 |
1 |
1 |
1 |
1 |
1 |
1 |
1 |
1 |
1 |
1 |
1 |
1 |
1 |
π 2 |
1 |
0 |
0 |
1 |
1 |
1 |
1 |
1 |
1 |
1 |
1 |
1 |
1 |
1 |
1 |
1 |
1 |
1 |
1 |
π 3 |
1 |
0 |
0 |
0 |
1 |
1 |
1 |
1 |
1 |
1 |
1 |
1 |
1 |
1 |
1 |
1 |
1 |
1 |
1 |
π 4 |
1 |
1 |
1 |
1 |
0 |
1 |
1 |
1 |
1 |
1 |
1 |
1 |
1 |
1 |
1 |
1 |
1 |
1 |
1 |
π 5 |
1 |
1 |
1 |
1 |
1 |
0 |
1 |
1 |
1 |
1 |
1 |
1 |
1 |
1 |
1 |
1 |
1 |
1 |
1 |
π 6 |
1 |
0 |
0 |
0 |
1 |
1 |
0 |
1 |
1 |
1 |
1 |
1 |
1 |
1 |
1 |
1 |
1 |
1 |
1 |
π 7 |
1 |
1 |
1 |
1 |
0 |
1 |
1 |
0 |
1 |
1 |
1 |
1 |
1 |
1 |
1 |
1 |
1 |
1 |
1 |
π 8 |
1 |
0 |
0 |
0 |
0 |
0 |
0 |
0 |
0 |
1 |
1 |
1 |
1 |
1 |
1 |
1 |
1 |
1 |
1 |
π 9 |
1 |
0 |
0 |
0 |
0 |
0 |
0 |
0 |
0 |
0 |
1 |
1 |
1 |
1 |
1 |
1 |
1 |
1 |
1 |
π 10 |
1 |
1 |
1 |
1 |
0 |
1 |
1 |
0 |
1 |
1 |
0 |
1 |
1 |
1 |
1 |
1 |
1 |
1 |
1 |
π 11 |
1 |
0 |
0 |
0 |
0 |
0 |
0 |
0 |
0 |
0 |
1 |
0 |
1 |
1 |
1 |
1 |
1 |
1 |
1 |
π 12 |
1 |
1 |
1 |
1 |
0 |
1 |
1 |
0 |
1 |
1 |
0 |
1 |
0 |
1 |
1 |
1 |
1 |
1 |
1 |
π 13 |
1 |
0 |
0 |
0 |
0 |
0 |
0 |
0 |
0 |
0 |
1 |
0 |
1 |
0 |
1 |
1 |
1 |
1 |
1 |
π 14 |
1 |
1 |
1 |
1 |
1 |
1 |
1 |
1 |
1 |
1 |
1 |
1 |
1 |
1 |
0 |
1 |
1 |
1 |
1 |
π 15 |
1 |
1 |
1 |
1 |
0 |
1 |
1 |
0 |
1 |
1 |
0 |
1 |
0 |
1 |
1 |
0 |
1 |
1 |
1 |
π 16 |
1 |
0 |
0 |
0 |
0 |
0 |
0 |
0 |
0 |
0 |
1 |
0 |
1 |
0 |
0 |
1 |
0 |
1 |
1 |
π 17 |
1 |
1 |
1 |
1 |
0 |
1 |
1 |
0 |
1 |
1 |
0 |
1 |
0 |
1 |
1 |
0 |
1 |
0 |
1 |
π 18 |
1 |
0 |
0 |
0 |
0 |
0 |
0 |
0 |
0 |
0 |
1 |
0 |
1 |
0 |
0 |
1 |
0 |
1 |
1 |
π 19 |
1 |
1 |
1 |
1 |
1 |
1 |
1 |
1 |
1 |
1 |
1 |
1 |
1 |
1 |
1 |
1 |
1 |
1 |
1 |
π 20 |
1 |
1 |
1 |
1 |
1 |
1 |
1 |
1 |
1 |
1 |
1 |
1 |
1 |
1 |
1 |
1 |
1 |
1 |
1 |
π 21 |
1 |
0 |
0 |
0 |
0 |
0 |
0 |
0 |
0 |
0 |
0 |
0 |
0 |
0 |
0 |
0 |
0 |
0 |
1 |
π 22 |
1 |
1 |
1 |
1 |
1 |
1 |
1 |
1 |
1 |
1 |
1 |
1 |
1 |
1 |
1 |
1 |
1 |
1 |
1 |
π 23 |
1 |
0 |
0 |
0 |
0 |
0 |
0 |
0 |
0 |
0 |
0 |
0 |
0 |
0 |
0 |
0 |
0 |
0 |
1 |
π 24 |
1 |
1 |
1 |
1 |
1 |
1 |
1 |
1 |
1 |
1 |
1 |
1 |
1 |
1 |
1 |
1 |
1 |
1 |
1 |
π 25 |
1 |
0 |
0 |
0 |
0 |
0 |
0 |
0 |
0 |
0 |
0 |
0 |
0 |
0 |
0 |
0 |
0 |
0 |
0 |
Р и с. 3. Структура и логические связи элементов подсистемы «открытие створок крыши бункера» зерноуборочного комбайна ACROS-550
F i g. 3. Structure and logical connections of the elements of the “opening of the hopper roof flaps” subsystem of the ACROS-550 combine harvester
370 Процессы и машины агроинженерных систем воздействие (напряжение +24 В на входе блоков предохранителей FU1 и FU2); Х2 - внешнее воздействие (нажатие клавиши «открытие створок крыши бункера» на пульте ПУ-142-03); Х3 – внешнее воздействие (установка ключа стартера SA2 в положение I); Z1-Z25 - обозначения выходов элементов логической модели; Y – выходной параметр (перемещение штока силового привода).
Проверки n j е П выполняются в соответствии с системой уравнений (1) (см. рис. 3).
я т : Z 1 = e i л X 1
к 2 : Z2 = e 2 л Z, к 3 : Z3 = e 3 л Z2 л X2
к 4 : Z 4 = e 4 л X 1
к 5 : Z 5 = e 5
к 6 : Z 6 = e 6 л Z 3
к 7 : Z 7 = e 7 л Z 4
к 8 : Z 8 = e 8 л Z 5 л Z 6 л Z 2
к к к10
к 11
к 12
к к 14 к 16 к 17 к 18 Я 19 к 20 к 21 к 22 к 23 к 24 к 25
Z 9 = |
= e 9 л |
Z 8 |
||
Z 10 |
= e 10 |
л Z 7 |
||
Z 11 |
= en |
л Z 9 |
||
Z 12 |
= e 12 |
л Z 10 |
||
Z 13 |
= e 13 |
л Z 11 |
. |
(1) |
Z 14 |
= eM |
|||
Z 15 |
= e 15 |
л Z 12 |
||
Z 16 |
= e 16 |
л Z 13 л |
2 Z 14 л X 3 |
|
Z 17 |
= e 17 |
л Z 15 |
||
Z 18 |
= e 18 |
л Z 16 |
||
Z 19 |
= e 19 |
|||
: Z 20 |
= e 20 |
|||
Z 21 |
= e 21 |
л Z 17 / |
x Z 18 л Z 09 |
|
: Z 22 |
= e 22 |
л Z 20 |
||
: Z 23 |
= e 23 |
л Z 21 |
||
: Z 24 |
= e 24 |
л Z 22 |
||
: Z 25 |
= e 25 |
л Z 23. |
л Z 24 |
Задача определения минимальной совокупности элементарных проверок решается посредством анализа ТФН. Сравнив попарно столбец е0 со столбцами е 1, е2, „., е. (i = 1, 2, „., 25), последовательно выделяем множество состояний Ul е U(l = 1, 2, „., | U) которые описываются конъюнкцией дизъюнкций параметров zj = πj ∈ Π (2):
325 25 325
AV z h = А ( z 1 1 V z 2 1 V z 3 1 V z 4 1 V z 5 1 V ... V z 25 1 ) l .
1 = 1 h = 1 1 = 1
Уравнение (2) раскрывается в виде системы уравнений (3):
U . П 01 - ( z 1 V z 2 V z 3 V z 6 V z 8 V z 9 V v z 11 V z 13 V z 16 V z 18 V z 21 V z 23 V z 25 ) 1
тт П02 - (z2 V z3 V z6 V z8 V z9 V z 11
U 2 :X
V z 13 V z 16 V z 18 V z 21 V z 23 V z 25 ) 2
^
тт П03 - (z3 V z4 V z6 V z8 V z9 V z 11
U 3 :
V z 13 V z 16 V z 18 V z 21 V z 23 V 25 ) 3
U 325 : П 025 - ( z 26 ) 325
При этом выражение, адекватно описывающее техническое состояние объекта диагностирования и содержащее минимальную совокупность элементарных проверок при допущении, что неисправным может быть только один любой элемент объекта диагностирования, имеет вид:
325 25
ЛV z hl = ( z 1 л z 2 л z з л z 4 л z 5 л l = 1 h = 1
-
л z 6 л z 7 л z 8 л z 9 л z 10 л z 11 л z 12 л
-
л z 13 л z 14 л z 15 л z 16 л z 17 л z 18 л
-
л z 19 л z 20 л z 21 л z 22 л z 23 л z 24 л z 25 ). (4)
Результаты исследования
Алгоритм диагностирования (в виде определенной последовательности элементарных проверок), представленный выражением (4), можно уточнить, используя значения весомости каждой проверки, полученные, например, на основе метода анализа иерархий (МАИ) [18]. Использовались следующие 4 критерия: К1 - доступность элемента; К2 - наличие инструмента; КЗ - блочность элемента; К4 – частота появления отказа.
Ниже приведены результаты расчета вектора глобальных приоритетов (табл. 2) и уточненная, в соответствии с рассчитанными приоритетами, последовательность элементарных проверок (3). Определение весомости критериев К1–К4 относительно друг друга в данной статье не приведено. В результате расчетов определен вектор глобальных приоритетов (табл. 2), в соответствии с которым устанавливается оптимальная последовательность элементарных проверок.
Обобщением вышеизложенного является описание в виде конъюнкции переменных исправного состояния: «при наличии напряжения питания ( х 1 ) и установке выключателя стартера и приборов ВК353 в положение «I» ( х 3), и нажатии на клавишу <ф> управления створками крыши бункера пульта ПУ-142-03 ( х 2) происходит открытие створок крыши бункера»:
Y = ( X 1 А X 2 A X з A Z 25 A Z 24 A Z 23 А
A z 22 А z 21 А z 20 А z 19 А z 18 А z 17 А z 16 А
А z 15 А z 14 А z 13 А z 12 А z 11 А z 10 А z 9 А
А z 8 А z 7 А z 6 А z 5 А z 4 А z 3 А z 2 А z 1 ).
При возможных неисправных (при наличии напряжения питания
( х 1 ) и установке выключателя стартера и приборов ВК353 в положение «I» ( х 3 ), и нажатии на клавишу <ф> управления створками крыши бункера пульта ПУ-142-03 ( х 2) не происходит открытие створок крыши бункера) состояниях подсистемы «управление створками крыши бункера» электрооборудования зерноуборочного комбайна ACROS-550
Y = ( x 1 A x 2 A x 3 A z 25 A z 24 A z 23 А
A z 22 A z 21 A z 20 A z 19 A z 18 A z 17 A z 16 A
A z 15 A z 14 A z 13 A z 12 A z 11 A z 10 A z 9 A
A Z 8 A Z 7 A Z 6 A Z 5 A Z 4 A Z 3 A Z 2 A Z 1 );
Y = ( x 1 A x 2 A x 3 A Z 25 A Z 24 A Z 23 A
A z 22 A z 21 A z 20 A z 19 A z 18 A z 17 A z 16 A
A z 15 A z 14 A z 13 A z 12 A z 11 A z 10 A z 9 A
A z 8 A z 7 A z 6 A z 5 A z 4 A z 3 A z 2 A z 1 );
...
Y = ( x 1 A x 2 A x 3 A z 25 A z 24 A z 23 A
A z 22 A z 21 A z 20 A z 19 A z 18 A z 17 A z 16 A
A z 15 A z 14 A z 13 A z 12 A z 11 A z 10 A z 9 A
A z 8 A z 7 A z 6 A z 5 A z 4 A z 3 A z 2 A z 1 ).
Ниже приведены построенные на основе рассмотренных зависимостей дерево решений (рис. 4), а также фрагмент модели знаний в виде продукционных правил, используемых при построении базы знаний экспертной системы. Представление знаний в виде продукционной модели является наиболее распространенным способом [19].
Т а б л и ц а 2
T a b l e 2
Значения вектора глобальных приоритетов (фрагмент)
Values of the global priorities vector (fragment)
Причины / Reasons |
П1 |
П2 |
П3 |
П4 |
П5 |
П6 |
П7 |
П8 |
П9 |
П10 |
П11 |
П12 |
П13 |
П22 |
П23 |
П24 |
П25 |
Значения век тора глобальных приори тетов / Values 0,0070,0080,0100,011 0,0130,0140,0160,0230,0290,0310,0320,0360,047 … 0,0660,0670,0680,071 of the global priorities vector
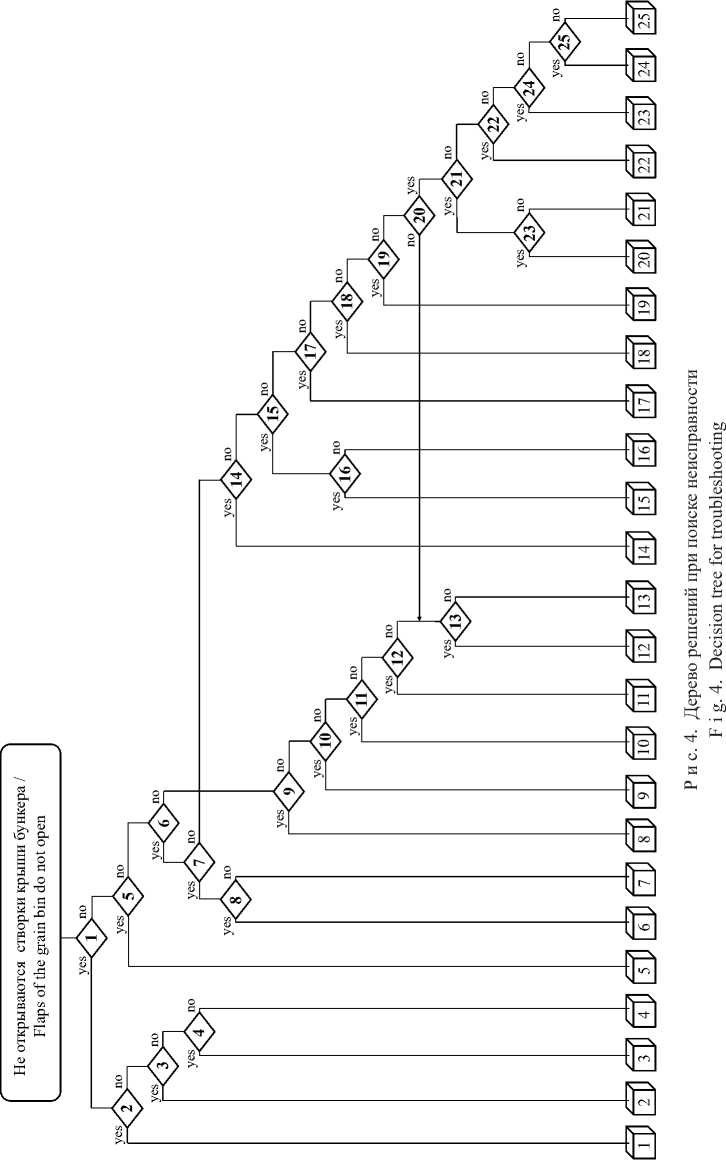
В ромбиках на рисунке 4 представлены следующие вопросы: 1 – есть напряжение +24 В на проводе Bг-736 у силового привода DD24-21B5-24-385 (блок А6)? 2 – есть соединение на «массу» на проводе Or-737 у силового привода DD24-21B5-24-385 (блок А6)? 3 – есть соединение на «массу» на выводе 30 общего контакта реле KV11(провод Or-737)? 4 - есть соединение на «массу» на проводе В-4 у вывода 88 нормально замкнутого контакта реле KV11? 5 – есть напряжение +24 В на выводе 30 общего контакта реле KV10 (провод Br-736)? 6 – есть напряжение +24 В на проводе Bl-730 у вывода 87 нормально разомкнутого контакта реле KV10? 7 - есть напряжение +24 В на проводе G-734 у вывода 86 обмотки реле KV10? 8 – есть соединение на «массу» на проводе B-4 у вывода 85 обмотки реле KV10? 9 – есть напряжение +24 В на проводе Bl-730 у предохранителя FU8.4 (10А)? 10 – есть напряжение +24 В на проводе R-2A у предохранителя FU8.4 (10А)? 11 – есть напряжение +24 В на проводе R-2A у предохранителя FU3.1 (60А)? 12 - есть напряжение +24 В на проводе R-2 у предохранителя FU3.1 (60А)? 13 - есть напряжение +24 В на проводе R-2 у предохранителя FU1.2 (60А)? 14 – есть напряжение +24 В на проводе G-734 в разъеме XS6 пульта управления ПУ-142-03 (блок А7)? 15 - есть напряжение +24 В на проводе Р-80 в разъеме ХР1 пульта управления ПУ-142-03 (блок А7)? 16 – есть соединение на «массу» на проводе B-4 в разъеме ХР1 пульта управления ПУ-142-03 (блок А7)? 17 – есть напряжение +24 В на проводе Р-80 у предохранителя FU8.3 (20А)? 18 – есть напряжение +24 В на проводе Р-81 у предохранителя FU8.3 (20А)? 19 – есть напряжение +24 В на выводе 87 нормально разомкнутого контакта реле KV22 (провод Р-81)? 20 – есть напряжение +24 В на проводе 374
Том 31, № 3. 2021
R-2 у общего вывода 30 реле KV22? 21 – есть напряжение +24 В на проводе Y-20 у вывода 85 обмотки реле KV22? 22 – есть соединение на «массу» на проводе В-4 у вывода 85 обмотки реле KV22? 23 – есть напряжение +24 В на выводе ПР выключателя стартера и приборов ВК353 (SA2)? 24 – есть напряжение +24 В на проводе R-2C у вывода AM выключателя стартера и приборов ВК353 (SA2)? 25 - есть напряжение +24 В на проводе R-2C у предохранителя FU1.1(60А)? В кубиках на рисунке 4 представлены возможные причины неисправности: 1 - неисправен силовой привод DD24-21B5-24-385 (блок А6); 2 – неисправна цепь провода Or-737; 3 – неисправно реле KV11; 4 – неисправна цепь провода B-4 (соединение на «массу» вывода 88 нормально замкнутого контакта реле KV11); 5 – неисправна цепь провода Br-736; 6 – неисправно реле KV10; 7 – неисправна цепь провода B-4 (соединение на «массу» вывода 85 обмотки реле KV10); 8 – неисправна цепь провода Bl-730; 9 – неисправен предохранитель FU8.4 (10А); 10 – неисправна цепь провода R-2A; 11 - неисправен предохранитель FU3.1 (60А); 12 - неисправна цепь провода R-2; 13 - неисправен предохранитель FU1.2 (60А); 14 – неисправна цепь провода G-734; 15 - неисправен пульт управления А7 (ПУ-142-03); 16 - неисправна цепь провода B-4 (соединение на «массу» в разъеме ХР1 пульта управления ПУ-142-03 (блок А7); 17 – неисправна цепь провода Р-80; 18 - неисправен предохранитель FU8.3(20А); 19 – неисправна цепь провода Р-81;
20 - неисправно реле KV22; 21 - неисправна цепь провода В-4 (соединение на «массу» вывода 85 обмотки реле KV22); 22 – неисправна цепь провода Y-20; 23 - неисправен выключатель стартера и приборов ВК353 (SA2); 24 – неисправна цепь провода R-2C; 25 - неисправен предохранитель FU1.1(60А).
ЕСЛИ при установке выключателя стартера и приборов ВК353 (SA2) в положение «I» и нажатии на клавишу «↑» управления створками крыши бункера пульта управления
ПУ-142-03 (блок А7) не происходит открытие створок крыши бункера ...
правило 25
И есть напряжением +24 В на проводе Bг-736 у силового привода DD24-21B5-24-385 (блок А6),
И есть соединение на «массу» на проводе Or-737 у силового привода DD24-21B5-24-385 (блок А6),
И есть соединение на «массу» на выводе 30 общего контакта реле KV11(провод Or-737),
И есть соединение на «массу» на проводе В-4 у вывода 88 нормально замкнутого контакта реле KV11,
И есть напряжение +24 В на выводе 30 общего контакта реле KV10 (провод Br-736),
И есть напряжение +24 В на проводе Bl-730 у вывода 87 нормально разомкнутого контакта реле KV10,
И есть напряжение +24 В на проводе G-734 у вывода 86 обмотки реле KV10,
И есть соединение на «массу» на проводе B-4 у вывода 85 обмотки реле KV10,
И есть напряжение +24 В на проводе Bl-730 у предохранителя FU8.4 (10А),
И есть напряжение +24 В на проводе R-2A у предохранителя FU8.4 (10А),
И напряжение +24 В на проводе К-2С у предохранителя FU 1.1(60А) отсутствует ,
ТО неисправен предохранитель FU1.1(60А).
Для устранения неисправности замените предохранитель FU1.1(60А).
Знание атрибута «исправен»/ «неисправен» определяется дополни- тельными диагностическими операциями, например: измерение напряжения на входе катушки электромагнита, измерение напряжения на выходе выключателя и т. п.
Обсуждение и заключение
Задача поиска причин неисправностей в системах и агрегатах сложных сельскохозяйственных машин является важной. Ее решение в условиях уборки зависит в основном от практического опыта и компетентности механизатора или мастера-диагноста. Для обеспечения информационной поддержки при решении задач диагностирования неисправностей с целью сокращения времени на поиск причин неисправностей целесообразно использование интеллектуальных информационных систем (экспертных систем). При построении таких систем необходимо иметь модель знаний процесса принятия решений. На основе рассматриваемой стратегии поиска неисправности в системах и агрегатах машины предложена методика структуризации знаний предметной области. Данная методика иллюстрирована примером анализа подсистемы электрооборудования зерноуборочного комбайна ACROS-550. Показано, что для определения оптимальной последовательности элементарных проверок целесообразно использовать различные критерии оценки весомости проверок. В результате анализа и моделирования рассматриваемой предметной области (электрооборудование комбайна) сформирована база знаний, включающая более 1 200 продукционных правил.
Использование данного подхода при внедрении интеллектуальной информационной системы поддержки принятия решений позволит увеличить коэффициент использования эксплуатационного времени работы комбайна, уменьшить время простоев на устранение неисправностей и, как следствие, повысить результативность уборочных работ.
Поступила 15.03.2021; одобрена после рецензирования 25.04.2021; принята к публикации 14.05.2021
Об авторах:
Все авторы прочитали и одобрили окончательный вариант рукописи.
Список литературы Моделирование знаний в задаче поиска причин неисправностей
- Выбор стратегии в задаче корректировки регулировочных параметров комбайна / Л. В. Борисова, И. Н. Нурутдинова, В. П. Димитров [и др.]. - DOI 10.15507/2658-4123.030.202001.060-075 // Инженерные технологии и системы. - 2020. - Т. 30, № 1. - С. 60-75. - Рез. англ.
- Research of Vibroacoustic Diagnostics of Fuel System of Engines of Combine Harvesters / I. Rogovskii, L. Titova, A. Novitskii, V. Rebenko. - DOI 10.22616/ERDev2019.18.N451 // Proceedings of International Scientific Conference "Engineering for Rural Development" (22-24 May 2019). - Jelgava, 2019. - Pp. 291-298.
- Research of Diagnostic of Combine Harvesters at Levels of Hierarchical Structure of Systems and Units of Hydraulic System / I. L. Rogovskii, B. S. Liubarets, S. A. Voinash [et al.]. - DOI 10.1088/17426596/1679/4/042038. - Текст : электронный // Journal of Physics: Conference Series. - 2020. - Vol. 1679.
- Дунаев, А. В. Актуальность стандартов по техобслуживанию и ремонту сельхозтехники / А. В. Дунаев, В. А. Казакова, В. А. Шинкевич // Стандарты и качество. - 2018. - № 1. - С. 36-38. -URL: https://ria-stk.ru/stq/adetail.php?ID=165761 (дата обращения: 12.03.2021). - Рез. англ.
- Liang, Z. Grain Sieve Loss Fuzzy Control System in Rice Combine Harvesters / Z. Liang, Y. Li, L. Xu. - DOI 10.3390/app9010114. - Текст: электронный // Applied Sciences. - 2019. -Vol. 9, Issue 1.
- Research of Daubechies Wavelet Spectrum of Vibroacoustic Signals for Diagnostic of Diesel Engines of Combine Harvesters / L. L. Titova, Yu. M. Chernik, Yu. O. Gumenyuk, M. M. Korobko. - DOI 10.1088/1755-1315/548/3/032030. - Текст : электронный // IOP Conference Series: Earth and Environmental Science. - 2020. - Vol. 548, Issue 3.
- Blockage Fault Diagnosis Method of Combine Harvester Based on BPNN and DS Evidence Theory / J. Chen, K. Xu, Y. F. Wang [et al.]. - DOI 10.1117/12.2265524. - Текст : электронный // Proceedings of 17th International Conference on Electronics and Information Engineering (23 January 2017). - Nanjing, 2017.
- Evaluation of Bearing Reliability of Combine Harvester Straw Chopper / E. Jotautiene, A. Juostas, A. Janulevicius, A. Aboltins. - DOI 10.22616/ERDev2019.18.N332 // Proceedings of International Scientific Conference "Engineering for Rural Development" (22-24 May 2019). - Jelgava, 2019. - Pp. 625-629.
- Чеботарев, М. И. Экспертный метод факторного анализа эксплуатационной надежности зерноуборочных комбайнов / М. И. Чеботарев, Б. Ф. Тарасенко, Е. А. Шапиро. - DOI 10.21515/19904665-136-006 // Научный журнал КубГАУ. - 2018. - № 136. - С. 71-86. - Рез. англ.
- Гумелёв, В. Ю. Оптимизация поиска неисправностей электрооборудования автомобиля / B. Ю. Гумелёв. - Текст : электронный // Исследования в области естественных наук. - 2014. - № 4. -URL: http://science.snauka.ru/2014/04/6722 (дата обращения: 12.03.2021). - Рез. англ.
- Афоничев, Д. Н. Повышение эффективности использования систем технического диагностирования в сельском хозяйстве / Д. Н. Афоничев, И. И. Аксенов // Вестник Воронежского государственного аграрного университета. - 2015. - № 4 (47). - С. 109-114. - URL: https://www.elibrary. ru/item.asp?id=24986080 (дата обращения: 12.03.2021).
- Operation Faults Monitoring of Combine Harvester Based on SDAE-BP[J] / X. Chenbo, Y. Guangyou, L. Lang [et al.]. - DOI 10.11975/j.issn.1002-6819.2020.17.006 // Transactions of the Chinese Society of Agricultural Engineering. - 2020. - Vol. 36, Issue 17. - Pp. 46-53.
- Design of Fuzzy Logic Control System Incorporating Human Expert Knowledge for Combine Harvester / M. Omid, M. Lashgari, H. Mobli [et al.]. - DOI 10.1016/j.eswa.2010.03.010 // Expert Systems with Applications. - 2010. - Vol. 37, Issue 10. - Pp. 7080-7085.
- Разработка диагностических интеллектуальных систем на основе онтологий / М. А. Грищенко, Н. О. Дородных, С. А. Коршунов, А. Ю. Юрин. - DOI 10.18287/2223-9537-2018-8-2-265-284 // Онтология проектирования. - 2018. - Т. 8, № 2 (28). - С. 265-284. - Рез. англ.
- Chen, J. Remote Fault Information Acquisition and Diagnosis System of the Combine Harvester Based on LabVIEW / J. Chen, P. Wu, K. Xu. - DOI 10.1142/9789814733878_0041 // Applied Mechanics, Mechatronics and Intelligent Systems. - 2016. - Pp. 285-292.
- Development on Electrical System Performance Test Stand for Combine Harvester / D. Sun, D. Chen, S. Wang, X. Wang. - DOI 10.1016/j.ifacol.2018.08.195 // IFAC-PapersOnLine. - 2018. -Vol. 51, Issue 17. - Pp. 363-367.
- Electrical Modification and Experimental Study of Combine Harvester Reaping Unit / P. Wang, M. Tian, H. Wang [et al.]. - DOI 10.1088/1757-899X/790/1/012168. - Текст : электронный // IOP Conference Series: Materials Science and Engineering. - 2020. - Vol. 790.
- Khan, A. U. Analytical Hierarchy Process (AHP) and Analytic Network Process Methods and Their Applications: A Twenty Year Review from 2000-2019 / A. U. Khan, Y. Ali. - DOI 10.13033/ijahp. v12i3.822. - Текст : электронный // International Journal of the Analytic Hierarchy Process. - 2020. -Vol. 12, Issue 3.
- Рябов, С. Ю. Интеллектуальный подход к автоматизации технологических и производственных процессов / С. Ю. Рябов. - DOI 10.15827/0236-235X.133.106-113 // Программные продукты и системы. - 2021. - № 1. - С. 106-113. - Рез. англ.