Модифицирование карбидо-кремниевой керамики иерархическими системами «многослойные углеродные нанотрубки - кремний»
Автор: Заворин А. В., Мосеенков С. И., Серкова А. Н., Кузнецов В. Л.
Журнал: Журнал Сибирского федерального университета. Серия: Техника и технологии @technologies-sfu
Рубрика: Исследования. Проектирование. Опыт эксплуатации
Статья в выпуске: 4 т.16, 2023 года.
Бесплатный доступ
С использованием метода реакционного спекания под давлением были получены образцы пористой керамики на основе карбида кремния. В качестве связующего использовали мелкокристаллический кремний в совокупности с многослойными углеродными нанотрубками (МУНТ) с нанесенными частицами кремния. Давление при прессовании составляло 30 МПа, температура варьировалась в диапазоне 1420-1480 °C, содержание МУНТ от 0 до 4 масс. % и связующего Si от 20 до 25 масс. %. Структура полученной керамики исследована методами оптической и растровой электронной микроскопии. Были установлены основные закономерности формирования структуры спеченной модифицированной керамики в зависимости от условий проведения спекания. Методом трёхточечного изгиба были исследованы физико-механические свойства полученных образцов
Sic-керамика, многослойные углеродные нанотрубки, растровая электронная микроскопия, реакционное спекание, метод трёхточечного изгиба
Короткий адрес: https://sciup.org/146282639
IDR: 146282639
Текст научной статьи Модифицирование карбидо-кремниевой керамики иерархическими системами «многослойные углеродные нанотрубки - кремний»
В настоящее время керамические материалы на основе карбидных матриц, благодаря своим уникальным физико-химическим свойствам – механической прочности, термической и химической устойчивости, имеют широкое практическое применение. Они используются в качестве компонентов сверхпрочных инструментов для обработки металлов, различных уплотнений и дисков регуляторов в водопроводных кранах и клапанах, подшипниках скольжения, в качестве бронепластин, в аэрокосмической промышленности и других практических приложениях [1]–[6]. Вместе с тем для получения готовых изделий из таких керамик требуется проведение спекания при очень высоких температурах (до 2200–2400 °C), что накладывает особые требования на используемую аппаратуру для их получения, а также обуславливает высокие энергозатраты на проведение процесса спекания. Все это приводит к увеличению себестоимости получения продукции на основе карбидных матриц и ограничивает их практическое использование.
В настоящее время разрабатываются подходы для «ультранизкотемпературного» получения карбидных керамик, заключающиеся в использовании связующего с более низкой температурой плавления для получения готовых керамических изделий. Для этого, как правило, используют матрицы на основе бора (B 4 C), кремния (SiC), гафния (HfC) и др. [7], [8], а Si, Al и другие материалы в качестве связующего. При этом формирование конечных изделий может осуществляться путем реакционного спекания в сочетании с горячим прессованием или инфильтрацией расплава связующего [9], [10]. Необходимо отметить, что реакция Si+C -> SiC протекает с уменьшением мольного объема, поэтому в зависимости от используемого метода возможно получать как высоко-, так и низкопористые изделия [11]–[16]. Как правило, прочность получаемых данным методом материалов ниже, чем используемых карбидных матриц, и определяется прочностью используемого связующего. Это ограничивает область практического применения таких материалов. Одним из возможных способов увеличения механической прочности получаемых материалов на основе карбидных матриц со связующим при реакционном спекании является армирование связующего путем добавления углеродных и неорганических наполнителей [17]–[19]. Многослойные углеродные нанотрубки (МУНТ) могут выступать одной из таких добавок. Они обладают уникальными физико-химическими свойствами: высокой механической прочностью, высокой электро- и теплопроводностью, что позволяет использовать их в различных практических приложениях, таких как армирующий компонент в полимерных, керамических и металлических матрицах, в производстве суперконденсаторов и др. [20]–[27]. В процессе получения керамических изделий, в зависимости от температуры проведения процесса, может происходить взаимодействие МУНТ со связующим и их превращение в вискеры и т.п., что будет способствовать образованию мелкокристаллической структуры композитов, дополнительно способствуя увеличению прочности получаемых материалов.
Для эффективного использования МУНТ с целью армирования связующего требуется, с одной стороны, их равномерное диспергирование по объему связующего или поверхности спекаемых частиц, а с другой стороны – сохранение максимального аспектного отношения нанотрубок. Как правило, для этого используют добавки ПАВ совместно с ультразвуковой обработкой суспензий МУНТ [28] либо обработку в планетарной мельнице с добавлением различных растворителей [29], [30]. Данный путь получения сопровождается введением дополнительных жидкофазных стадий в процесс получения керамических изделий и может значительно удорожать получение керамических изделий. Из наших предыдущих работ известно [31], что с увеличением диаметра модуль упругости МУНТ уменьшается. Таким образом, нанотрубки с большим диаметром легче равномерно распределить в смеси, чем более тонкие, за счет их меньшей прочности. Для увеличения диаметра МУНТ их поверхность может быть дополнительно модифицирована, например, частицами кремния, которые также будут выступать в роли дополнительных центров взаимодействия МУНТ со связующим, увеличивая тем самым работу адгезии МУНТ к связующему и к наполнителю композита.
Таким образом, целью данной работы являлось определение возможности использования МУНТ, модифицированных частицами кремния, в качестве армирующего компонента при получении карбидных керамик путем «ультранизкотемпературного» реакционного горячего прессования карбида кремния при использовании в качестве связующего – кремния в соче-– 436 – тании с МУНТ, модифицированных наночастицами кремния. Исследовано влияние условий механической обработки на получение равномерных смесей исходных порошков компонентов композитного материала и воспроизводимость определяемых прочностных характеристик композитов.
Экспериментальная часть
Исходные МУНТ с нанесенными частицами кремния
Для получения образцов SiC-керамики были использованы образцы МУНТ с нанесенными частицами Si, полученные ранее. В работе [32] описан способ их получения и охарактеризование структуры полученных материалов. Так, исходные МУНТ были получены в Институте катализа СО РАН, путем пиролиза этилена на Fe – Co катализаторе при температуре 670 °C. Для удаления остаточного катализатора полученные нанотрубки кипятили в 15 % HCl в течение 2 часов. После удаления катализатора МУНТ были промыты большим количеством дистиллированной воды для удаления ионов H+ и Cl-. Чистота промывных вод контролировалась путем измерения её электропроводности, величина которой не превышала 20 мкмСм/см. Сушка отмытых нанотрубок проводилась в сушильном шкафу при T=80 °C в течение 72 часов [33], [34]. По данным ПЭМ (JEM-2010, JEOL), их средний диаметр составлял 9.5 нм (3.7–22.0 нм), удельная поверхность, по данным БЭТ (ASAP 2400), – 270 м2/г, насыпная плотность – 0.12 г/ см3. Осаждение частиц кремния на поверхность МУНТ проводили путем газофазного химического осаждения кремния из моносилана SiH 4 (99,994 %) в реакторе с псевдоожиженным слоем при 500 °C. Строение и структура полученных композитов была исследована с использованием TEM (JEM-2010, JEOL), SEM (JSM6460-LV JEOL), XRD (Thermo Scientific ARL X′TRA powder X-ray diffractometer Switzerland) and Raman spectroscopy (T64000 Horiba) [32]. На рис. 1 приведены характерные ПЭМ-изображения композитов МУНТ-Si.
Порошок SiC использовали коммерчески доступный (Волжский абразивный завод) с размером зерен 0.9–1.5 мкм (F2000), который был дополнительно отмыт в разбавленной соляной кислоте (1:1) для удаления примесей металлов, отмыт дистиллированной водой до нейтральной реакции и высушен на воздухе при T=80 °C в течение 48 часов.
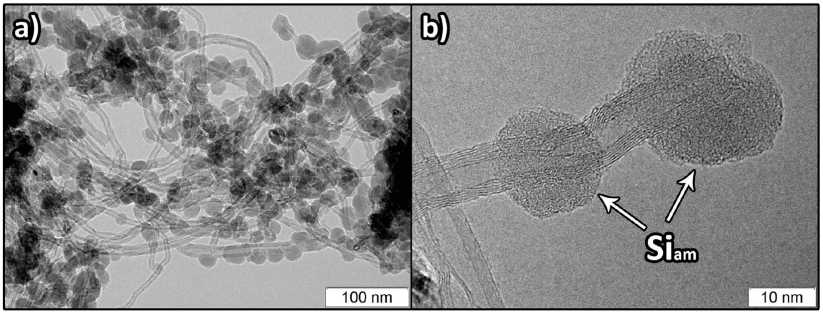
Рис. 1. Типичные ПЭМ-изображения исходных композитов МУНТ-Si
Fig. 1. Typical TEM images of the initial MWCNT-Si composites
Порошок кремния, используемый в качестве связующего компонента, был предварительно измельчен в планетарной мельнице (30 g, 15 мин). В работе использовали фракцию порошка размером менее 40 мкм, полученную путем фракционирования на ситах. Подготовленный таким образом порошок кремния отмывали от примесей Fe раствором соляной кислоты (1:1), после отмывали дистиллированной водой до нейтральной реакции и сушили на воздухе при T=80 °C в течение 48 часов.
Получение смесей компонентов керамики (SiC+Si+МУНТ-Si)
Исследование влияния режима смешения компонентов керамики (SiC+Si+МУНТ-Si) на равномерность распределения компонентов проводили в горизонтальной планетарной мельнице АГО-2 (Новосибирск, Россия). Барабаны (V=200 см3) были выполнены из стали 40Х, помольные шары (диаметр 5 мм, масса 300 г) – из стали ШХ20СГ. Навеска смеси для обработки составляла 10 г. Для уменьшения намола перед смешением компонентов проводили предварительную футеровку поверхности барабанов и шаров смесью аналогичного состава в течение 5 мин при ускорении шаров 26.6 g. Ускорение шаров варьировали в диапазоне 3.1–26.6 g, время обработки составляло до 10 мин, что позволило реализовать как режим перемешивания аналогично барабанной мельнице, так и дополнительное диспергирование компонентов в процессе смешения.
Получение набора модифицированных керамик высокотемпературным спеканием
Спекание образцов смесей (SiC+Si+МУНТ-Si) проводили в графитовой пресс-форме, выполненной из графита марки МПГ-7 (рис. 2). Для минимизирования воздействия кислорода воздуха, который может привести к деструкции МУНТ в композитах МУНТ-Si, между пуансонами и образцом помещали жертвенный слой МУНТ. Предварительно пресс-форму с образцом помещали в сушильный вакуумный шкаф (ЛАБТЕХ), прогревали при 150 °C в течение 30 мин,
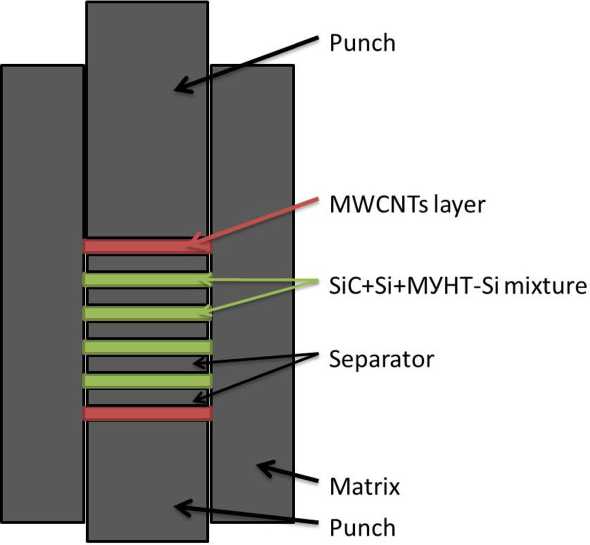
Рис. 2. Схема расположения образцов и дополнительных слоев МУНТ для поглощения кислорода в пресс-форме
Fig. 2. Scheme of samples position and MWCNTs additional layers to absorb oxygen in the press-form вакуумировали до остаточного давления 5 мм рт. ст. и напускали в него аргон высокой чистоты, выдерживали 5 мин и повторяли процедуру откачки два раза.
Подготовленную таким образом пресс-форму с образцами помещали в установку для горячего прессования. Для нагрева пресс-формы был использован индукционный нагреватель, а обечайка и пуансоны пресс-формы выступали в качестве тигля индукционной печи. Для защиты спекаемых образцов от кислорода воздуха в объем индуктора вокруг пресс-формы подавали аргон высокой чистоты (2.5 л/мин). Спекание образцов проводили в два этапа. На первом этапе образцы нагревали до температуры 1100 °C со скоростью ~ 40 °C/мин и выдерживали при этой температуре 30 мин и давлении 1 Мпа для обеспечения взаимодействия МУНТ с нанесенными частицами Si и создания центров кристаллизации SiC на их поверхности [35]. На втором этапе к образцу прикладывали фиксированное давление (варьировалось для разных экспериментов, приведено в табл. 1) и нагревали со скоростью 30 °C/мин до требуемой температуры. Образец выдерживали определенное время при заданных температуре и давлении и охлаждали со скоростью ~ 30 °C/мин до температуры 1000 °C.
Охарактеризование структуры и свой ств образцов
Охарактеризование равномерности смешения исходных компонентов проводили с использованием оптической микроскопии на отражение (МИКРОМЕД ПОЛАР-1) и растровой электронной микроскопии (JSM6460-LV JEOL). Структуру полученных керамических композитов исследовали с использованием оптической микроскопии на отражение, ПЭМ (JEM-2200FS JEOL) и РЭМ (JSM6460-LV JEOL и Hitachi Regulus 8230).
Измерение прочности на изгиб и модуля упругости полученной модифицированной керамики проводили методом 3-точечного изгиба согласно ГОСТ Р 57749–2017, с использованием образцов спеченной керамики в виде балочек прямоугольного сечения с высотой 2.5 мм и шириной 3.0 мм (рис. 3). Радиус скругления опор составлял 1 мм, расстояние между центрами опор составляло 15 мм. Образец нагружался с постоянной скоростью наконечника – 0.5 (±0.01) мм/мин. Силу, действующую на образец, измеряли с точностью 0.01 Н.
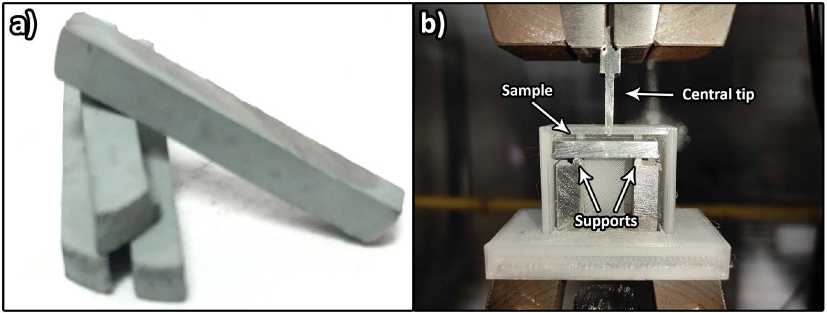
Рис. 3. a – керамические образцы прямоугольного сечения; b – расположение образца на опорах и центрального наконечника
Fig. 3. a – ceramic samples of rectangular section; b – the location of the sample on the supports and the central tip
Результаты и обсуждение
Получение гомогенных смесей исходных порошков и исследование их структуры
Получение гомогенных смесей исходных компонентов и равномерное распределение в них МУНТ является одним из ключевых факторов, определяющих свойства конечных изделий. Поэтому на данном этапе основной задачей являлось определение условий смешения компонентов керамики, а также разработка доступных способов оценки равномерности получаемых смесей. Для этого получали смеси компонентов (МУНТ-Si, Si и SiC) при различных режимах работы планетарной мельницы, структуру которых охарактеризовывали методами оптической микроскопии и РЭМ. На рис. 4 приведены характерные изображения оптической микроскопии смесей.
Можно видеть, что смешение при 3.1 g приводит к перемешиванию порошков агрегатов МУНТ-Si и SiC, при этом структура агрегатов МУНТ-Si сохраняется вне зависимости от времени обработки. Смешение при 10.4 g приводит к частичному разрушению агрегатов композита. Так, при времени обработки 5 мин на изображениях можно видеть агрегаты размером до 10 мкм, а при 10 мин агрегатов на изображениях не наблюдается. Получение смесей при 21.8 g и более позволяет получить равномерное распределение композита в смеси с SiC уже при времени смешения 5 мин. Для получения характеристики качества смешения компонентов было предложено использовать отклонение оттенка пикселей от среднего на изображениях оптической микроскопии, так как присутствующие агломераты МУНТ-Si имеют интенсивный черный цвет. Для этого изображения оптической микроскопии получали при фиксированных
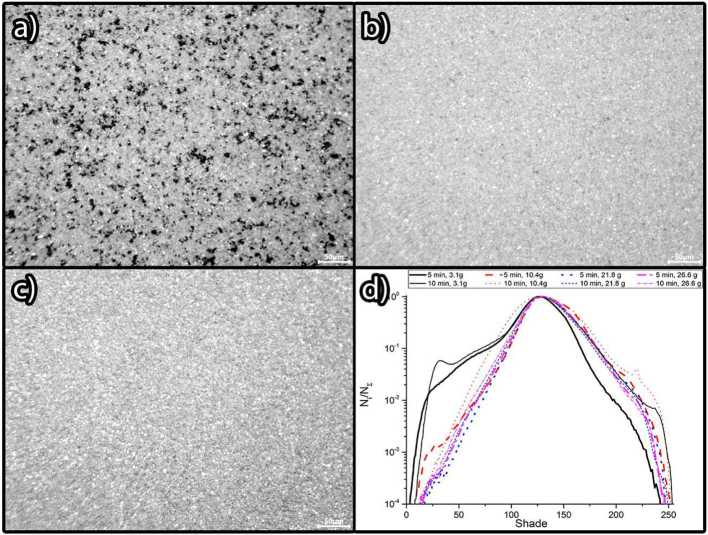
Рис. 4. Характерные изображения оптической микроскопии смесей, полученных при различных условиях обработки: a – 5 мин, 3.1 g; b – 5 мин, 10.4 g; c – 5 мин, 21.8 g; d – гистограммы изображений оптической микроскопии образцов, полученных при различных условиях смешения (см. пояснения в тексте)
Fig. 4. Typical images of optical microscopy of mixtures obtained under various processing conditions. a – 5 min, 3.1 g; b – 5 min, 10.4 g; c – 5 min, 21.8 g; d – histograms of optical microscopy images of samples obtained under various mixing conditions (see explanations in the text)
значениях освещения и выдержки фотокамеры микроскопа в формате градации серого (0–255, grayscale 8-bit). После, с использованием программного обеспечения ImageJ [36], проводили коррекцию гистограммы так, чтобы минимум оттенка соответствовал 0, максимум 255, а максимум распределения соответствовал оттенку 127, и проводили определение распределения числа пикселей по их оттенку (рис. 4 d). Можно видеть, что для смесей, полученных при ускорении шаров 3.1g, вне зависимости от времени смешения характерно наличие большой доли пикселей с оттенком 10–50 на изображениях микроскопии, соответствующих агломератам МУНТ-Si. Увеличение ускорения шаров до 10.4 g приводит к значительному уменьшению доли таких пикселей, однако наблюдается увеличение доли пикселей с оттенком 210–250, соответствующих частицам Si или SiC. Увеличение ускорения шаров до 21.8 g приводит к тому, что на гистограммах уменьшается доля оттенков, соответствующих агломератам МУНТ-Si или частицам Si и SiC, а дальнейшее увеличение ускорения шаров и времени обработки не приводит к значительным изменениям в гистограммах образцов.
Для определения распределения МУНТ-Si по поверхности частиц Si и SiC морфология смесей была исследована методом РЭМ (рис. 5). Было установлено, что получение смесей при 10.4 g в течение 5 мин, с одной стороны, позволяет разрушить практически все агрегаты композита МУНТ-Si, с другой стороны, приводит к формированию ажурных агрегатов композита размером до 3 мкм в пространстве между зернами SiC (рис. 5 a, b). При этом увеличение времени обработки до 10 мин не приводит к разрушению агрегатов в межзеренном пространстве смеси (рис. 5 c, d), что, по-видимому, обусловлено недостаточной энергией воздействия при смешении. В смесях, полученных при 21.8 g и времени смешения 5 мин, не было зарегистрировано ни крупных, ни ажурных агрегатов композита МУНТ-Si в межзеренном пространстве смеси (рис. 5 e, f).
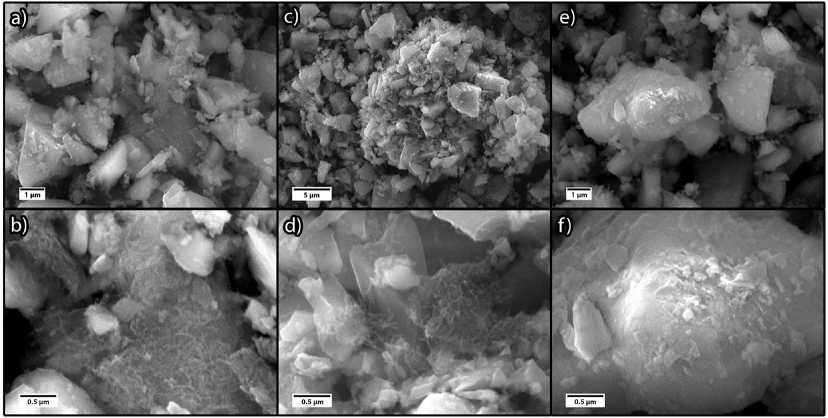
Рис. 5. Характерные РЭМ-изображения смесей SiC и МУНТ-Si композитов, полученных при различных условиях обработки в планетарной мельнице: a, b – 5 мин, 10.4 g; c, d – 10 мин, 10.4 g; e, f – 5 мин, 21.8 g
Fig. 5. Typical SEM images of mixtures of SiC and MWCNT-Si composites obtained under various processing conditions in a planetary mill: a, b – 5 min, 10.4 g; c, d – 10 min, 10.4 g; e, f – 5 min, 21.8 g
Таким образом, проведенное исследование влияния параметров получения смесей на их структуру и распределение МУНТ-Si показало, что для разрушения агрегатов композита МУНТ-Si и их равномерного распределения по поверхности частиц Si и SiC ускорение шаров должно быть не менее 21.8 g, а время смешения не менее 5 мин. Установлено, что метод оптической микроскопии совместно с анализом гистограмм можно использовать для охарактеризования равномерности распределения МУНТ-Si в смесях и использовать для оперативного контроля качества получаемых смесей при масштабном получении керамики.
Получение набора модифицированных керамик высокотемпературным спеканием
C использованием методики высокотемпературного спекания, описанной выше, были получены образцы модифицированной керамики (НК) с различным содержанием связующего кремния (20–25 масс. %) и композитов МУНТ-Si (0–4 масс. %, доля композита МУНТ-Si приведена в пересчете на МУНТ). В табл. 1 приведены основные характеристики полученных образцов карбидо-кремниевой керамики, а также условия их получения.
Исследование структуры спеченных смесей оптической микроскопией
Структура полированных шлифов полученных образцов модифицированной керамики была исследована с использованием оптической микроскопии (рис. 6). Можно видеть, что частицы SiC равномерно распределены по поверхности спеченного образца. При этом на поверхности присутствуют крупные частицы SiC размером до 4–10 мкм, пространство между которыми равномерно заполнено более мелкими частицами SiC.
Было проведено определение распределения частиц SiC на поверхности образца по размерам (рис. 6 c). Можно видеть, что основное количество наблюдаемых частиц (67 %) имеют размер менее 1 мкм и 90 % частиц SiC имеют размер менее 2.5 мкм. В то же время это составляет только
Таблица 1. Условия получения и основные характеристики образцов карбидо-кремниевой керамики SiC+Si+МУНТ-Si (НК)
Table 1. Preparation conditions and main characteristics of samples of silicon carbide ceramics SiC+Si+МУНТ-Si (НК)
Шифр |
Образец |
ω Si связ, масс. % |
ω МУНТ, масс. % |
T, °C |
τ, мин |
P, МПа |
ρ, г/см3 |
НК-11 |
SiC+Si+ МУНТ-Si |
20 |
1 |
1420 |
1 |
30 |
1,84 |
НК-12 |
SiC+Si+ МУНТ-Si |
20 |
2 |
1420 |
1 |
30 |
1,90 |
НК-14 |
SiC+Si+ МУНТ-Si |
20 |
4 |
1420 |
1 |
30 |
1,85 |
НК-20 |
SiC+Si |
25 |
0 |
1480 |
5 |
30 |
- |
НК-21 |
SiC+Si+ МУНТ-Si |
25 |
1 |
1480 |
5 |
30 |
2,00 |
НК-22 |
SiC+Si+ МУНТ-Si |
25 |
2 |
1480 |
5 |
30 |
2,01 |
НК-24 |
SiC+Si+ МУНТ-Si |
25 |
4 |
1480 |
5 |
30 |
1,96 |
НК-31 |
SiC+Si+ МУНТ-Si |
25 |
1 |
1480 |
5 |
30 |
2,03 |
НК-32 |
SiC+Si+ МУНТ-Si |
25 |
2 |
1480 |
5 |
30 |
2,01 |
НК-34 |
SiC+Si+МУНТ-Si |
25 |
4 |
1480 |
5 |
30 |
1,98 |
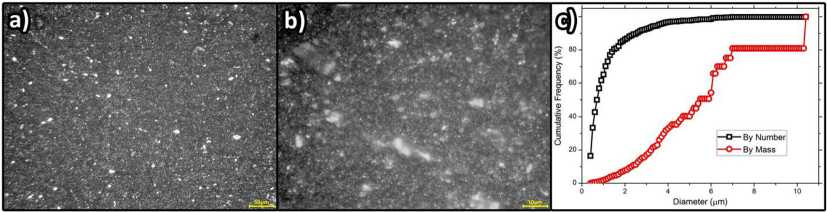
Рис. 6. Характерные изображения оптической микроскопии поверхности модифицированной керамики на примере образца НК-24 (SiC+25 %-Si+4 %-МУНТ-Si): a – х500; b – х1000; c – кумулятивное распределение частиц SiC по размерам (по числу и по массе)
Fig. 6. Typical images of optical microscopy of the surface of modified ceramic for example sample of НК-24 (SiC+25 %-Si+4 %-МУНТ-Si): a – х500; b – х1000; c – cumulative size distribution of SiC particles (by number and by mass)
11.2 % от массы всего SiC, наблюдаемого на поверхности образца. Таким образом, на основании проведенного анализа изображений оптической микроскопии можно сделать вывод, что в структуре полученных спеченных образцов крупные частицы (4–10 мкм) SiC равномерно окружены более мелкими частицами SiC и эта структура равномерно окружена кремнием. Полученные величины плотности образцов (1.84–2.03 г/см3, табл. 1) также указывают на присутствие пустот в структуре образцов. Также ввиду малого размера подавляющего числа частиц SiC, образующего структуру модифицированной керамики, метод оптической микроскопии не позволяет выявить различий в микроструктуре между полученными спечёнными образцами.
Исследование структуры модифицированных керамик РЭМ
Микроструктура полученных образцов НК была исследована методами ПЭМ и РЭМ.
На рис. 7 приведены характерные ПЭМ-изображения и электронограммы полученных образцов НК. Установлено, что в результате спекания возможно формирование искривленных (рис. 7 a) и прямых (рис. 7 b, c) вискеров SiC как с поликристаллической структурой (рис. 7 a, b), так и в виде монокристалла (рис. 7 c). Анализ структуры показал наличие различных межплоскостных расстояний, характерных для ромбоэдрической (2.45, 2.54Å), гексагональной (2.37, 2.59, 2.68Å) и кубической (2.21, 2.52Å) решеток SiC [37]–[39].
Исследование структуры сломов образцов НК методом РЭМ (рис. 8 и 9) позволило установить, что продукты превращений МУНТ равномерно распределены по поверхности сломов керамик, как правило, на границах крупных частиц SiC. Установлено, что для эффективного расплавления кремния и скрепления частиц SiC температура проведения спекания должна составлять не менее 1480 °C. Так, на рис. 8 можно видеть, что практически все наблюдаемые частицы (часть из которых – кремний) имеют острые грани, что указывает на то, что частицы не расплавлялись в процессе спекания при T=1420 °C. В отличие от этого для образцов керамик, полученных при температуре 1480 °C, большая часть мелких частиц имеет округлые границы (рис. 9), что указывает на то, что они расплавлялись в процессе спекания керамики. На основе данных по плотности керамик SiC+Si установлено, что необходимо добавление как минимум 22 масс. % кремния для заполнения пустот между частицами SiC в процессе горячего спекания.
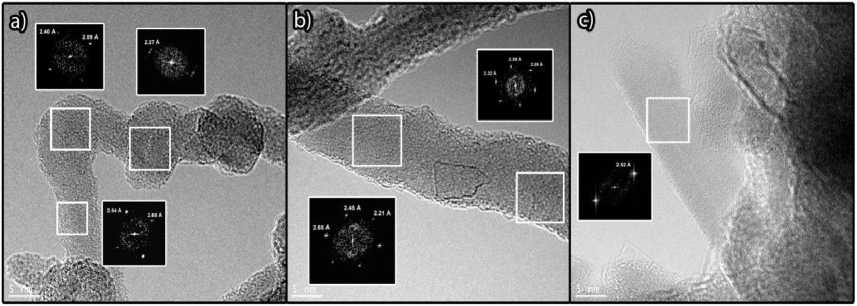
Рис. 7. ПЭМ-изображения и электронограммы вискеров SiC, полученных в результате спекания образцов НК
Fig. 7. TEM images and electron diffraction patterns of SiC whiskers obtained by sintering samples of НК
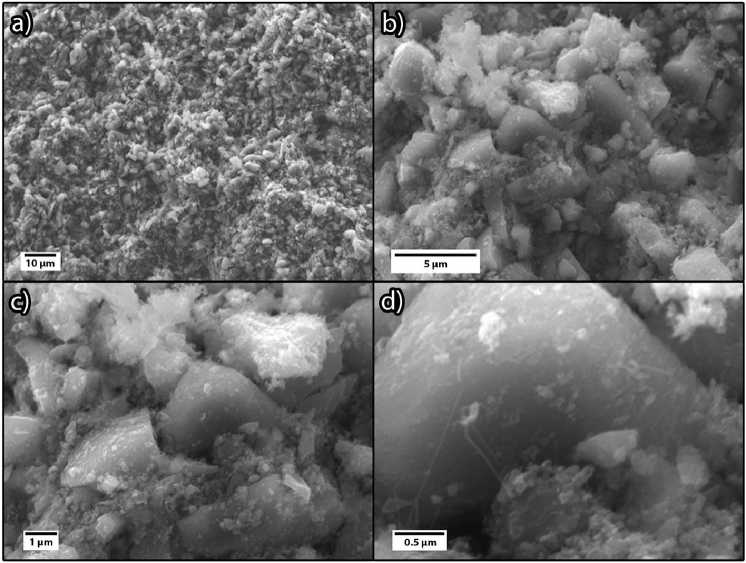
Рис. 8. Характерные РЭМ-изображения образца спеченной модифицированной керамики НК-14, полученной путем горячего прессования при температуре 1420 °C в течение 1 мин при давлении 30 Мпа
Fig. 8. Typical SEM images of a sample of sintered modified ceramics НК-14 obtained by hot pressing at a temperature of 1420 °C for 1 min at a pressure of 30 MPa
Анализ большого числа РЭМ-изображений сломов керамики показал, что МУНТ (продукты их превращений) равномерно распределены по всей поверхности сломов. Их основные места расположений – границы крупных частиц SiC, что может быть обусловлено возникновением в этих местах застойных зон в процессе смешения порошков SiC с кремнием и с композитом МУНТ-Si или их вытеснением в процессе спекания при высокой температуре.
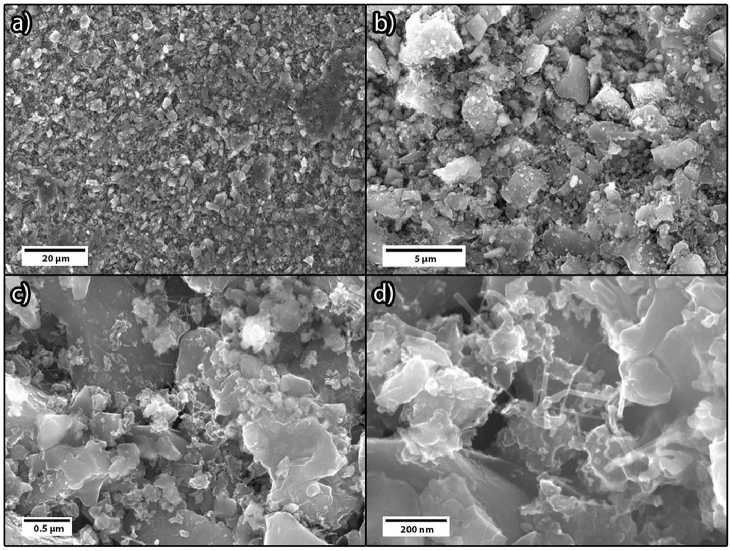
Рис. 9. Характерные РЭМ-изображения образца спеченной модифицированной керамики НК-22, полученной путем горячего прессования при температуре 1480 °C в течение 5 мин при давлении 30 Мпа
Fig. 9. Typical SEM images of a sample of sintered modified ceramics НК-22 obtained by hot pressing at a temperature of 1480 °C for 5 min at a pressure of 30 MPa
Охарактеризование механических свой ств модифицированной керамики
На основе полученных данных в процессе испытаний методом 3-точечного изгиба были рассчитаны предел прочности при изгибе и модуль упругости при изгибе образцов модифицированной керамики (рис. 10). Было установлено, что добавление МУНТ-Si приводит к увеличению прочности керамики на 10–20 %. Максимальные значения предела прочности композитов (59.80, 61.83, 72.34 и 52.55 МПа) были получены при спекании образцов керамики НК-20 – НК-24 с содержанием связующего кремния 25 масс. %, МУНТ – 0, 1, 2 и 4 масс. %, при T = 1480 °C, P = 30 МПа и τ = 5 мин. При увеличении содержания МУНТ до 2 масс. % наблюдается увеличение прочности образцов на 12.5 МПа. Дальнейшее увеличение содержания МУНТ до 4 масс. %, приводит к уменьшению прочности образцов, что, по-видимому, связано с увеличением пористости образца и уменьшением контактов между спекаемыми частицами. Уменьшение содержания связующего кремния в спекаемых смесях до 20 масс. %, МУНТ до 1 масс. %, времени до 1 мин и температуры до 1420 °C приводит к значительному уменьшению предела прочности до 22.60 МПа (образец НК-11).
Было установлено, что образцы с наибольшим значением предела прочности при изгибе имеют более низкие значения модуля упругости при изгибе (на 20–30 %), что наблюдается для образцов НК-21 и НК-22 при содержании МУНТ 1 и 2 масс. % и связующего кремния 25 масс. %, (рис. 10 b). При содержании нанотрубок 0 и 4 масс. % и связующего кремния 25 масс. %, образцы демонстрируют высокие значения модуля упругости (выше на 50–60 %) относи- – 445 –
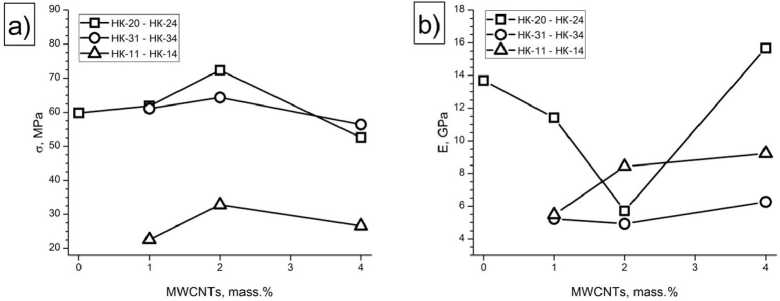
Рис. 10. a – зависимость предела прочности и b – модуля упругости при изгибе для модифицированной керамики от концентрации МУНТ и условий проведения спекания
Fig. 10. a – dependence of tensile strength and b – modulus of elasticity in bending for modified ceramics on the concentration of MWCNTs and sintering conditions тельно остальных образцов (НК-20 и НК-24). Образцы (НК-22 и НК-31 – НК-34), демонстрирующие одни из самых высоких значений предела прочности, показывают одни из самых низких показателей модуля упругости при содержании МУНТ в 1, 2 и 4 масс. %.
Проведенное охарактеризование предела прочности и модуля упругости при изгибе образцов керамики, полученных в повторных экспериментах по спеканию в одних и тех же условиях (серии образцов НК-21 – НК-24 и НК-31 – НК-34), показало хорошую воспроизводимость результатов для предела прочности (рис. 10 a) и удовлетворительную воспроизводимость для модуля упругости (рис. 10 b) полученных образцов керамики. Это указывает на достоверность полученных значений предела прочности и модуля упругости методом 3-точечного изгиба образцов модифицированной керамики.
Так, образцы керамики, полученные при температуре спекания 1480 °C, давлении 30 МПа и времени 5 мин, демонстрируют наибольшие показатели прочности при изгибе (72.34 МПа), по сравнению с остальными спеченными образцами керамики. Для всех полученных серий образцов модифицированной керамики установлена обратная зависимость между величинами предела прочности и модулем упругости при изгибе. Установлено, что при увеличении содержания МУНТ в исходной смеси свыше 2 масс. % наблюдается уменьшение предела прочности получаемой керамики. Показана хорошая воспроизводимость величины предела прочности образцов керамики, получаемых в разных экспериментах по спеканию.
Выводы
Были получены образцы спеченной SiC керамики с различным содержанием связующего компонента и композита МУНТ-Si и определены оптимальные условия проведения спекания (температура, давление, время спекания). Для эффективного спекания и скрепления частиц SiC были определены необходимые количества связующего компонента, минимальные температура и время спекания смесей.
С использованием методов оптической микроскопии, просвечивающей и растровой электронной микроскопии установлено, что в результате проведения высокотемпературной обра-– 446 – ботки крупные частицы SiC равномерно окружены более мелкими частицами SiC и эта структура окружена кремнием, а МУНТ трансформируются в вискеры SiC, которые равномерно распределены на границах крупных частиц карбида кремния.
Установлено, что образцы керамики, полученные при температуре спекания 1480 °C, давлении 30 МПа и времени 5 мин, демонстрируют наибольшие показатели прочности при изгибе (72.34 МПа), при содержании МУНТ 2 масс. %, по сравнению с остальными полученными образцами керамики. Для всех серий образцов модифицированной керамики установлена обратная зависимость между величинами предела прочности и модулем упругости при изгибе. Установлено, что при увеличении содержания МУНТ в исходной смеси свыше 2 масс. % происходит уменьшение предела прочности получаемой керамики. Показана хорошая воспроизводимость величины предела прочности образцов керамики, получаемых в разных экспериментах по спеканию.
В то же время полученные образцы керамики имеют плотность 1,84–2,03 г/см3, что составляет 62–69 % от теоретической. Такие показатели плотности свидетельствуют о том, что полученные образцы имеют высокую пористость, что открывает возможность использования полученных материалов в качестве высокотемпературных керамических фильтров.
Список литературы Модифицирование карбидо-кремниевой керамики иерархическими системами «многослойные углеродные нанотрубки - кремний»
- Oguntuyi S. D. et al. Improvement on the fabrication OF SiC materials: Processing, reinforcing phase, fabricating route – A review. International Journal of Lightweight Materials and Manufacture, 2022.
- Xu M. et al. Recent advances and challenges in silicon carbide (SiC) ceramic nanoarchitectures and their applications. Materials Today Communications, 2021, 28.
- Khodaei M., Yaghobizadeh O., Naghavi Alhosseini S. H., Esmaeeli S., Mousavi S. R. The effect of oxide, carbide, nitride and boride additives on properties of pressureless sintered SiC: A review. Journal of the European Ceramic Society, 2019, 39(7), 2215–2231.
- Zhang W. Tribology of SiC ceramics under lubrication: Features, developments, and perspectives. Current Opinion in Solid State and Materials Science, 2022, 26(4).
- Гаршин А.П., Кулик В. И., Нилов А. С. Ударопрочные материалы на основе технической керамики: достижения и перспективы повышения их баллистической эффективности. Научные исследования и разработки, 2016, 4, 53–67. [Garshin A. P., Kulik V. I., Nilov A. S. Impact-resistant materials based on technical ceramics Achievements and prospects for increasing their ballistic efficiency. Scientific research and development, 2016, 4, 53–67 (in Rus.)].
- Житнюк С.В., Сорокин О. Ю., Журавлева П. Л. Керамика на основе карбида кремния, полученная спеканием гранулированного порошка. Композиционные материалы, 2020, 2(86), 50–59 [Zhitnyuk S. V., Sorokin O. Yu. , Zhuravleva P. L. Silicon carbide ceramics obtained by sintering granular powder. Composite materials, 2020, 2(86), 50–59 (in Rus.)].
- Solodkyi I.V. et al. Low-Temperature Synthesis of Boron Carbide Ceramic. Journal of Superhard Materials, 2018, 20(4), 236–242.
- Hayun S., Frage N., Dariel M. P. The morphology of ceramic phases in BxC–SiC–Si infiltrated composites. Journal of Solid State Chemistry, 2006, 179(9), 2875–2879.
- Popov O., Vleugels J., Huseynov A., Vishnyakov V. Reactive sintering of TiB 2-SiC–CNT ceramics. Ceramics International, 2019, 45(17), 22769–22774.
- Parveez B., Kittur M. I., Badruddin I. A., Kamangar S., Hussien M., Umarfarooq M. A. Scientific Advancements in Composite Materials for Aircraft Applications: A Review. Polymers, 2022, 14(22).
- Роман О.В., Ковалевская А. В., Фомихина И. В., Григорьев С. В. Разработка карбидной и нитридной керамики повышенной прочности. Литье и металлургия, 2005, 4(36), 157–162 [Roman O. V., Kovalevskaya A. V., Fomikhina I. V., Grigoriev S. V. Development of high-strength carbide and nitride ceramics. Lit’e metallurgia, 2005, 4(36), 157–162 (in Rus.)].
- Ding S., Zhu S., Zeng Y., Jiang D. Effect of Y 2O3 addition on the properties of reaction-bonded porous SiC ceramics, Ceramics International, 2006, 32(4), 461–466.
- Yuan B., Wang G., Li H., Liu L., Liu Y., Shen Z. Fabrication and microstructure of porous SiC ceramics with Al2O3 and CeO2 as sintering additives. Ceramics International, 2016, 42(11), 12613–12616.
- Bai C.-Y. et al. Fabrication and properties of cordierite–mullite bonded porous SiC ceramics. Ceramics International, 2014, 40(4), 6225–6231.
- Zhou Y. et al. Preparation and characterization of tubular porous silicon carbide membrane supports. Journal of Membrane Science, 2011, 369(1–2), 112–118.
- Ma Y., Ma Q.-S., Suo J., Chen Z.-H. Low-temperature fabrication and characterization of porous SiC ceramics using silicone resin as binder. Ceramics International, 2008, 34(2), 253–255.
- Zvonarev E. V., Ilyushchanka A. Ph., Vitko Zh. A., Osipov V. A., Babura D. V. Effect of reaction sintering modes on the structure and properties of carbide ceramics. Vescì Akademìì navuk Belarusì. Seryâ fizika-tehničnyh navuk, 2019, 63(4), 407–415.
- Савиных А.С., Гаркушин Г. В., Разоренов С. В., Румянцев В. И. Динамическая прочность реакционно-спеченной керамики карбида бора. Журнал технической физики, 2015, 85(6), 77–82 [Savinykh A. S., Garkushin G. V., Razorenov S. V., Rumyantsev V. I. Dynamic Strength of Reaction Sintered Boron Carbide Ceramics Journal of Technical Physics. Technical physics, 2015, 85(6), 77–82 (in Rus.)].
- Шикунов С.Л., Курлов В. Н. Получение композиционных материалов на основе карбида кремния силицированием углеродных матриц. Журнал технической физики, 2017, 87(12) [Shikunov S. L., Kurlov V. N. Preparation of composite materials based on silicon carbide by siliconization of carbon matrices. Technical physics, 2017, 87(12) (in Rus.)]
- Rathinavel S., Priyadharshini K., Panda D. A review on carbon nanotube: An overview of synthesis, properties, functionalization, characterization, and the application. Materials Science and Engineering B, 2021, 268.
- Mathur R.B., Singh B. P., Pande S. Carbon Nanomaterials. Taylor & Francis Group, 2016, 284.
- Rajesh Jesudoss Hynes N. et al. Synthesis, properties, and characterization of carbon nanotube-reinforced metal matrix composites. Nanocarbon and its Composites. Elsevier, 2019, 849.
- Morris J.E., Iniewski K. Graphene, Carbon Nanotubes, and Nanostructures: Techniques and Applications. Taylor & Francis Group, 2013, 355.
- Peng H., Qingwen L., Chen T. Industrial applications of carbon nanotubes. Amsterdam, Elsevier, 2017, 492.
- Peigney A., Laurent C. H. Carbon nanotubes-ceramic composites. Ceramic-Matrix Composites. Elsevier, 2006, 614.
- Imani Yengejeh S., Kazemi S. A., Öchsner A. Carbon nanotubes as reinforcement in composites: A review of the analytical, numerical and experimental approaches. Computational Materials Science, 2017, 136, 85–101.
- Curtin W. A., Sheldon B. W. CNT‑reinforced ceramics and metals. Materials Today, 2004, 7(11), 44–49.
- Shutilov R. A., Kuznetsov V. L., Moseenkov S. I., Karagedov G. R., Krasnov A. A., Logachev P. V. Vacuum-tight ceramic composite materials based on alumina modified with multi-walled carbon nanotubes. Materials Science and Engineering: B, 2020, 254.
- Karagedov G. R., Shutilov R. A., Kolesov B. A., Kuznetsov V. L. The effect of carbon nanotubes introduction on the mechanical properties of reaction bonded boron carbide ceramics. Journal of the European Ceramic Society, 2021, 41(12), 5782–5790.
- Matsuoka M., Tatami J., Wakihara T., Komeya K., Meguro T. Improvement of strength of carbon nanotube-dispersed Si 3 N 4 ceramics by bead milling and adding lower-temperature Sintering aids. Journal of Asian Ceramic Societies, 2014, 2(3), 199–203.
- Elumeeva K. V. et al. Reinforcement of CVD grown multi-walled carbon nanotubes by high temperature annealing. AIP Advances, 2013, 3(11).
- Zavorin A. V. et al. Chemical Vapor Deposition of Silicon Nanoparticles on the Surface of Multiwalled Carbon Nanotubes. J Struct Chem, 2020, 61(4), 617–627.
- Kuznetsov V. L. et al. Raman spectra for characterization of defective CVD multi-walled carbon nanotubes: Raman spectra for characterization of defective CVD MWCNTs. physica status solidi (b), 2014, 251(12), 2444–2450.
- Usoltseva A., Kuznetsov V., Rudina N., Moroz E., Haluska M., Roth S. Influence of catalysts’ activation on their activity and selectivity in carbon nanotubes synthesis. phys. stat. sol. (b), 2007, 244(11), 3920–3924.
- Заворин А. В., Мосеенков С. И., Селютин А. Г., Серкова А. Н., Цэндсурэн Ц.-О., Кузнецов В. Л. Влияние термической обработки на структуру композитов МУНТ-Si. 2022, 76–77. [Электронный ресурс] – Режим доступа: http://conf.nsc.ru/SRTCFM‑2022/en/invitation – Заглавие с экрана. [Zavorin A. V., Moseenkov S. I., Selyutin A. G., Serkova A. N., Tsendsuren Ts.-O., Kuznetsov V. L. Effect of heat treatment on the structure of MWCNT-Si composites. 2022, 76–77. Electronic resourse] – Access: http://conf.nsc.ru/SRTCFM‑2022/en/invitation.
- Schneider C. A., Rasband W. S., Eliceiri K. W. NIH Image to ImageJ: 25 years of image analysis. Nat Methods, 2012, 9(7), 671–675.
- Thibault W. The American Mineralogist. Journal of the mineralogical society of America, 1944, 9–10, 327–362.
- Marlene M.C., Eoise E. H. et al. Standard X‑ray Diffraction Powder Patterns, Washington, U. S. Government printing office, 1976, 122.
- Shaffer P.T.B. A review of the structure of silicon carbide, Acta Crystallogr B Struct Sci, 1969, 25(3), 477–488.