Модифицирование серого чугуна составами на основе нанодисперсных порошков карбидов вольфрама и титана
Автор: Полубояров В.А., Коротаева З.А., Жданок А.А., Горбунов Ф.К.
Журнал: Журнал Сибирского федерального университета. Серия: Техника и технологии @technologies-sfu
Статья в выпуске: 2 т.12, 2019 года.
Бесплатный доступ
Проведены эксперименты по модифицированию чугунов китайского производства, аналогичных российским маркам (СЧ-18 - СЧ-30), с использованием составов на основе смеси карбидов вольфрама и титана (нанодисперсные порошки карбидов были получены методом самораспространяющегося высокотемпературного синтеза (СВС) в сочетании с предварительной механической активацией (МА)). Были исследованы модификаторы состава WС:TiС = 70:30 с металлами-протекторами: хромом (50/50, модификатор М1); хромом и медью (25/25/50, модификатор М2) в пределах концентраций керамической фазы - 0,01-0,2 %; модификаторы вводили в форму и ковш. Были исследованы две конструкции литейных форм. Применение модификаторов при внутриформенном модифицировании может увеличить предел прочности при растяжении до 18,5 %, относительную коррозионную стойкость в соляной кислоте - до 58,8 %. При модифицировании в ковше прочность образцов увеличилась до 25-29 % лишь после 3,5 месяцев хранения. Полученные результаты свидетельствуют о том, что при исследовании процессов модифицирования серого чугуна модификаторами, содержащими нанодисперсные керамические фазы (WС, TiС), необходимо учитывать не только концентрации и состав модификаторов, но и различные технологические параметры (конструкция, объем литейной формы, способ введения модификаторов и другие).
Внутриформенное модифицирование, серый чугун, карбиды титана и вольфрама, коррозионная стойкость, металл-протектор, механическая активация, предел прочности при растяжении, твердость
Короткий адрес: https://sciup.org/146281184
IDR: 146281184 | DOI: 10.17516/1999-494X-0128
Текст научной статьи Модифицирование серого чугуна составами на основе нанодисперсных порошков карбидов вольфрама и титана
Увеличение эксплуатационных характеристик (прочности при разрыве, твердости, износостойкости, коррозионной стойкости и в конечном итоге срока службы) чугунов, сталей является актуальной задачей. Качество отливок зависит от многих технологических параметров, которые оказывают влияние на процессы кристаллизации расплава (температура заливки, формовочная смесь, химический состав, объем отливки, перегрев металла при выплавке и др.) [1]. Кроме того, перечисленные технологические факторы оказывают влияние на состав и количество фаз, размер зерна, различные дефекты кристаллической решетки.
В настоящее время большой интерес приобретает использование наноматериалов в металлургии для улучшения качества изделий. Модифицирующие наноразмерные тугоплавкие частицы могут, во-первых, служить центрами зародышеобразования и кристаллизации, тем самым увеличивая их количество, во-вторых, блокировать диффузию соответствующих атомов к зарождающимся и растущим кристаллам, замедляя их рост [2-9]. Экспериментально установлено, что чем больше зародышей в единице объема расплава, тем больше кристаллов образуется, тем они мельче и тем выше механические свойства металла [10, 11].
По этой причине в сплавах намеренно стараются облегчить формирование зародышей кристаллизации. Вещество, способствующее образованию зародышей, называют модификатором, а саму операцию – модифицированием.
Согласно [12] частицы, находящиеся в объеме металла, оказывают влияние на динамику дислокаций, так как создают препятствия для их движения. Такой материал можно рассматривать как дисперсно-упрочненный композит. Под действием приложенного напряжения источники дислокаций образуют дислокационные петли, окружающие частицы. Число петель дислокаций n зависит от расстояния между частицами:
n = l p ^ /G m^ ^L
где lp - расстояние между частицами; ст - приложенное напряжение; Gm - модуль сдвига материала матрицы; b → – вектор Бюргерса дислокации. Напряжение сдвига, действующего на частицу, равно:
Т = l p О ' /G m |b > | ,
а предел текучести материала, упрочненного частицами, равен:
^ (C p G m IM/ l pO» , (3)
где Gр – модуль сдвига материала частицы; С – постоянная, характеризующая тип материала. Причем модуль сдвига материала частицы G р должен превосходить модуль сдвига материала матрицы Gm, иначе упрочнения не произойдет. Если частица не смочена материалом, то тогда между материалом и частицей будет пузырь с модулем сдвига, равным нулю, поэтому из формулы (3) видно, что предел текучести равен нулю и, следовательно, материал разупрочняется. Чтобы частицы другой фазы могли изменять свойства материала, они должны смачиваться этим материалом. В противном случае эти частицы выступают в качестве дефектов структуры, ухудшающих свойства материала.
Механохимия может существенно облегчить путь к достижению положительного результата. Обработка в высокоэнергетических активаторах планетарного типа позволяет не только измельчать материал, но и активировать частицы порошков, а дополнительное плакирование частиц дает возможность получать модификаторы, хорошо смачиваемые расплавами [13-16].
Несмотря на большое количество модификаторов, предлагаемых на рынке, проблема получения модификаторов на основе тугоплавких ультрадисперсных частиц, смачиваемых расплавом, равномерно распределенных в металлической матрице, и проблема получения стабильных результатов при модифицировании служат объектом пристального внимания многих исследователей.
Целью настоящей работы является повышение служебных характеристик литых изделий из серого чугуна посредством введения в расплавы структурирующих добавок на основе на-нодисперсных карбидов вольфрама и титана, полученных комбинированным методом (само-распространяющимся высокотемпературным синтезом в сочетании с предварительной механической активацией).
Методика эксперимента
Эксперименты по модифицированию были проведены с использованием чугунов китайского производства (аналогичных российским маркам СЧ-18 – СЧ-30). Нанодисперсные порошки карбидов вольфрама и титана состава WС:TiС = 70:30 были получены методом СВС в сочетании с предварительной механической активацией по методике, описанной в [17].
Так как керамические материалы плохо смачиваются расплавом чугуна, порошки были дополнительно обработаны в активаторе АГО-3 с металлами-протекторами хромом и медью. Были получены модификаторы состава: (WС, TiС)/Cr/Cu : 50/50/0 (модификатор М1) и (WС, TiС)/Cr/Cu : 25/25/50 (модификатор М2 ). Модификаторы применяли в виде порошков, концентрации модификаторов (керамической фазы) – в пределах 0,01-0,2 %.
Выплавка чугуна производилась в индукционной печи, емкость тигля 400 кг. Чугун разливали при температуре 1350 °С, при этом индукционная печь была постоянно включена. Модифицирование проводили в форме (масса металла 20-40 кг) и ковше, при этом в ковш заливали количество металла, необходимое для последующей заливки одной или двух форм (предварительно ковш прогрели газом для удаления влаги). Состав материала для изготовления литейных форм – песчано-глинистая смесь (ПГС) и холодно-твердеющая смесь (ХТС).
В ходе экспериментов отливали до десяти образцов: один – без модификатора (на нижний фильтр помещали пустую алюминиевую фольгу), остальные – с различными модификаторами, завернутыми также в алюминиевую фольгу. Были подобраны технологические режимы, при реализации которых не происходило вытекания металла из форм, не было перелива и выплесков чугуна.
Каждую отлитую заготовку (после полного остывания) взвешивали и рассчитывали количество введенного модификатора.
Среднее значение предела прочности при растяжении получали по шести измерениям, что обеспечивало корректность получаемых данных. Для характеристики твердости материалов использовали метод Бринелля. Измерения проводили в различных точках образца (не менее пяти отпечатков) и сравнивали их значения со значениями, полученными при исследовании контрольного образца.
Коррозионную стойкость исследовали по ГОСТ 9.908 ‒ 85 на двух подготовленных образцах чугуна (модифицированном и контрольном). Для измерения относительной коррозионной стойкости образцы должны иметь примерно одинаковый диаметр и высоту, т.е. поверхность, контактирующая с агрессивной средой, должна быть одинаковой. Испытания проводили в 25%-ной соляной кислоте.
Модифицирование серого чугуна.
Исследование влияния различных технологических параметров на служебные характеристики
Исследование влияния концентрации модификатора и способа введения. Для экспериментов использовали модель литейной формы (№ 1), которая представляет собой систему из стояка посредине заготовки длиной до 300 мм (верхний диаметр 150 мм, нижний – 100 мм) и шести цилиндров вокруг стояка (диаметром 30-40 мм). Заливка металла производится в цен-– 195 – тральную часть, откуда металл сифонной заливкой (снизу вверх) поступает в цилиндрические заготовки [13]. Для того чтобы модификатор не всплывал, в форму устанавливали два керамических фильтра, между которыми помещали модификатор. Состав материала для изготовления литейных форм – песчано-глинистая смесь (ПГС). Использовали модификаторы М1 и М2, концентрации керамической фазы модификаторов – в пределах 0,013-0,062 %.
Химический состав контрольного образца чугуна (без модификатора) дан в табл. 1.
Условия модифицирования (состав, количество модификатора, способ введения) изложены в табл. 2: образец 1 – контрольный без модификатора, образцы 2-4 – с модификатором М2, образец 5 – с модификатором М1 . Во второй и третий образцы модификаторы были помещены в стояк формы (между двумя фильтрами), в четвертый и пятый образцы модификаторы ввели в ковш под струю металла (количество металла в ковше такое же, как в форме, – примерно 40 кг).
Свойства образцов чугуна – предел прочности при растяжении, твердость по Бринеллю, а также изменение прочности и твердости относительно контрольного (немодифицированного) образца даны в табл. 3. Увеличение прочности при растяжении составило от 1,1 до 18,5 % (образцы 2-5), увеличение твердости по Бринеллю составило от 2,8 до 11,3 (образцы 3-5), у образца 2 твердость снизилась на 6,6 % относительно контрольного образца 1.
Относительная коррозионная стойкость увеличилась от 7,2 до 44,1 %, причем максимальные значения 37,6 и 44,1 % получены при модифицировании в ковше (образцы 4 и 5 соответственно).
На рис. 1-3 приведены микрофотографии шлифов образцов чугуна. У всех модифицированных образцов (рис. 2, 3) наблюдается измельчение графитовых включений по сравнению
Таблица 1. Химический состав чугуна
Table 1. Chemical composition of cast iron
Элементы |
C |
Si |
Mn |
P |
S |
Cr |
Ti |
Cu |
W |
Массовая доля элементов, % |
3,27 |
1,92 |
0,68 |
0,056 |
0,014 |
- |
0,09 |
0,022 |
0,017 |
Таблица 2. Условия модифицирования
Table 2. Conditions of modification
Номер |
Модификатор |
|||
Название |
Состав (WС,TiС)/Cr/Cu, % |
Концентрация керамической фазы, % |
Способ введения |
|
1 |
- |
- |
- |
- |
2 |
М2 |
25/25/50 |
0,033 |
форма |
3 |
М2 |
25/25/50 |
0,013 |
форма |
4 |
М2 |
25/25/50 |
0,034 |
ковш |
5 |
М1 |
50/50/0 |
0,062 |
ковш |
Таблица 3. Свойства образцов чугуна
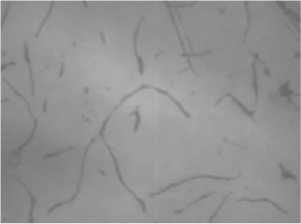
х400
Рис. 1. Микрофотография немодифицированного образца
Table 3. Properties of cast iron samples
Номер |
Предел прочности при растяжении, МПа |
Твердость, единиц HBW |
Изменение прочности, % |
Изменение твердости, % |
Изменение относительной коррозионной стойкости, % |
1 |
178 |
177 |
|||
2 |
211 |
166 |
18,5 |
-6,6 |
13,7 |
3 |
209 |
197 |
17,4 |
11,3 |
7,2 |
4 |
190 |
182 |
6,7 |
2,8 |
44,1 |
5 |
180 |
194 |
1,1 |
9,6 |
37,6 |
Fig. 1. Microphotographs of unmodified sample
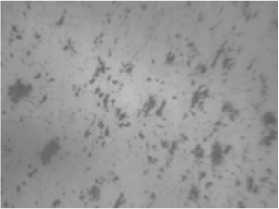
х400 а
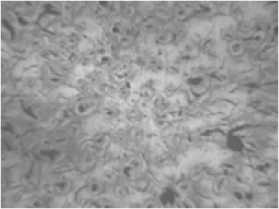
х400
б
Рис. 2. Микрофотографии образцов, модифицированных в форме: а) образец 2 (WС, TiС – 0,033 %); б) образец 3 (WС, TiС – 0,013 %)
Fig. 2. Microphotographs of samples modified in the form: a) sample 2 (WС, TiС – 0.033 %); б) sample 3 (WС,
TiС – 0.013 %)
с контрольным образцом 1 (рис. 1). Образцы, модифицированные в форме (рис. 2, образцы 2 и 3) и ковше (рис. 3, образцы 4 и 5), отличаются распределением и формой графитовых включений.
Исследование влияния «естественного старения». После 3,5 месяцев хранения («естественного старения») прочность образцов 2 и 3, модифицированных в форме, уменьшилась
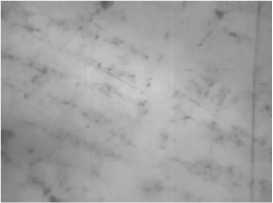
×400 а
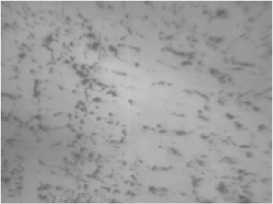
×400 б
Рис. 3. Микрофотографии образцов, модифицированных в ковше: а) образец 4 (WС, TiС – 0,034 %); б) образец 5 (WС, TiС – 0,062 %)
Fig. 3. Microphotographs of samples modified in the ladle: a) sample 4 (WС, TiС – 0.034 %); б) sample 5 (WС,
TiС – 0.062 %)
Таблица 4. Влияние «естественного старения»
Table 4. Influence of “natural aging”
Прочность образцов 4 и 5, модифицированных в ковше (концентрации керамических частиц 0,034 и 0,062 %), увеличилась на 29,4 и 25,3 % относительно контрольного (К1) (табл. 4, 5-й столбец); изменение (увеличение) прочности в результате «старения» для этих образцов составило 15,8 и 18,3 % соответственно (табл. 4, 6-й столбец).
Влияние концентрации модификатора на коррозионную стойкость. Влияние концентрации модификатора на коррозионную стойкость исследовали на двух марках чугуна, аналогичных российским маркам СЧ-20 и СЧ-30. Использовали модель литейной формы (№ 2) в виде «стакана», масса чугуна 19 кг. Состав материала для изготовления литейных форм – ПГС и ХТС. Использовали модификатор М2 , концентрации керамической фазы модификатора – в пределах 0,01-0,2 %.
В пределах концентраций керамической фазы 0,025-0,2 % относительная коррозионная стойкость в 0,1 М соляной кислоте увеличилась с 22,7 до 58,8 % (образцы 2-7, табл. 5); при кон- – 198 –
Таблица 5. Влияние концентрации модификатора на относительную коррозионную стойкость
Table 5. Influence of modifier concentration on relative corrosion resistance
Выводы
-
1. Модифицирование в форме № 1.
-
1.1. Применение модификатора М2 (концентрация керамической фазы 0,033 %) при вну-триформенном модифицировании серого чугуна способствует увеличению прочности при растяжении на 18,5 %, относительной коррозионной стойкости в соляной кислоте – на 13,7 %, но снижает твердость на 6,6 % относительно контрольного образца. При концентрации керамической фазы модификатора 0,013 % увеличиваются и прочность при растяжении (на 17,4 %), и твердость (на 11,3 %), относительная коррозионная стойкость – на 7,2 %.
-
1.2. При обработке расплава в ковше модификатором М2 (концентрация керамической фазы 0,034 %) прочность при растяжении увеличилась на 6,7 %, твердость – на 2,8 %; относительная коррозионная стойкость в соляной кислоте увеличилась на 44,1 %.
-
1.3. При обработке металла в ковше модификатором М1 (концентрация активной фазы 0,062 %) прочность при растяжении увеличилась незначительно (на 1,1 %), твердость – на 9,6 %, относительная коррозионная стойкость – на 37,6 %.
-
1.4. После 3,5 месяцев хранения прочность при растяжении контрольного образца (К1) и образцов, модифицированных в форме, практически не изменилась, а прочность образцов, модифицированных в ковше (концентрации керамических частиц 0,034 и 0,062 %), увеличилась на 29,4 и 25,3 % относительно контрольного (К1).
-
-
2. Модифицирование в форме № 2.
-
2.1. Относительная коррозионная стойкость образцов чугуна в соляной кислоте в пределах концентраций керамической фазы 0,025-0,2 % увеличилась с 22,7 до 58,8 %.
-
-
3. Полученные результаты свидетельствуют о том, что при исследовании процессов модифицирования серого чугуна (СЧ-18 – СЧ-30) модификаторами, содержащими нанодисперс-ные керамические фазы (WС, TiС), необходимо учитывать не только концентрации и состав
модификаторов, но и различные технологические параметры (конструкция, объем литейной формы, способ введения модификаторов и др.).
Список литературы Модифицирование серого чугуна составами на основе нанодисперсных порошков карбидов вольфрама и титана
- Задиранов А.Н., Кац А.М. Теоретические основы кристаллизации металлов и сплавов. М.: Издательство Российского Университета дружбы народов, 2007. 228 с.
- Крушенко Г.Г., Ямских И.С., Бонченков А.А., Мишин А.С. Повышение качества чугунных отливок с помощью нанопорошков. Металлургия машиностроения, 2002, 2 (9), 20 21.
- Жуков М.Ф., Черский И.Н. Упрочнение металлических, полимерных и эластомерных материалов ультрадисперсными порошками плазмохимического синтеза. Новосибирск: Наука. Сибирская издательская фирма РАН, 1999. 312 с.
- Сабуров В.П., Черепанов А.Н., Жуков М.Ф. Плазмохимический синтез ультрадисперсных порошков и их применение для модифицирования металлов и сплавов. Новосибирск: Наука. Сибирская издательская фирма РАН, 1995. 344 с.
- Хрычиков В.Е., Калинин В.Т., Кривошеев В.А., Доценко Ю.В., Селиверстов В.Ю. Ультрадисперсные модификаторы для повышения качества отливок. Литейное производство, 2007, (7), 2 5.
- Пинкин В.Ф., Каренгин А.Г., Осиненко С.А. Модифицирование высокохромистого чугуна ИСЦ ультрадисперсным порошком. Литейное производство, 1994, (3), 7.
- Влас М.И., Калинин В.Т., Хрычиков В.Е., Кривошеев В.А., Меняйло Е.В., Кондрат А.А. Модифицирование износостойких чугунов ультра-и нанодисперсными материалами. Системные технологии, 2010, 1(66), 150 162.
- Полубояров В.А., Коротаева З.А., Селютин Г.Е., Гаврилов Ю.Ю. Возможности метода механохимических воздействий для приготовления нанодисперсий и модифицирования ими полимеров, металлов, а также для создания керамических материалов. Перспективные материалы, 2009, (3), 351 361.
- Полубояров В.А., Черепанов А.Н., Коротаева З.А., Ушакова Е.П. Способ внепечного модифицирования чугунов и сталей. Пат. 2344180, Российская Федерация, опубл. 20.01.2009.
- Затуловский С. С. Суспензионная разливка. Киев: Наукова думка, 1981. 260 с.
- Лезник И.Д., Беркун А.Ф., Будашева Т.Б., Чебурков Е.М. Способ суспензионной разливки чугунов. Пат. 2142355, Российская Федерация, опубл. 10.12.1999.
- Миркин Л.И. Физические основы прочности и пластичности (Введение в теорию дислокаций). М.: МГУ, 1968. 538 с.
- Полубояров В.А., Коротаева З.А., Жданок А.А., Кузнецов В.А., Степанова Н.В. Внутриформенное модифицирование чугунов. Исследование влияния модификаторов на основе карбида кремния на процессы кристаллизации серого чугуна. СООБЩЕНИЕ 1. Известия высших учебных заведений. Черная металлургия, 2014, 6, 20 24.
- В. А. Полубояров, З. А. Коротаева, А. А. Жданок, В. А. Кузнецов, А. В. Самохин. Внутриформенное модифицирование чугунов. Исследование влияния модификаторов, полученных плазмохимическим и СВС методами, на эксплуатационные характеристики серого чугуна. СООБЩЕНИЕ 2. Известия высших учебных заведений. Черная металлургия, 2015, 8, 561 566.
- Полубояров В.А., Коротаева З.А., Жданок А.А., Кузнецов В.А., Самохин А.В. Внутриформенное модифицирование чугунов. Влияние состава и концентрации наноразмерных модификаторов на эксплуатационные характеристики серого чугуна. СООБЩЕНИЕ 3. Известия высших учебных заведений. Черная металлургия, 2015, 58 (10), 728 734.
- Vladimir A. Poluboyarov, Zoya A. Korotaeva, Alexander A. Zhdanoka and Victor A. Kuznetzov. Nanodisperse Hadfield (110G13L) Steel Modification, Journal of Siberian Federal University. Engineering &Technologies, 2016, 9(1), 117 125.
- Полубояров В.А., Жданок А.А., Коротаева З.А., Кузнецов В.А. Получение WC и W2C из смеси порошков вольфрама, титана и сажи методом самораспространяющегося высокотемпературного синтеза. Неорганические материалы, 2014, 50(5), 508 511.