Мониторинг технического состояния редукторов частотно-регулируемого электропривода шахтных ленточных конвейеров
Автор: Кузин Е.Г., Герике Б.Л.
Журнал: Горные науки и технологии @gornye-nauki-tekhnologii
Рубрика: Энергетика, автоматизация и энергоэффективность
Статья в выпуске: 1, 2016 года.
Бесплатный доступ
Приводятся результаты анализа простоев шахтных ленточных конвейеров, и рассматривается актуальность проведения мониторинга их технического состояния. Показаны результаты мониторинга состояния редукторов частотно-регулируемого привода конвейера по параметрам смазочного масла и параметрам вибрации.
Ленточный конвейер, частотно-регулируемый привод, техническая диагностика, вибродиагностика, анализ смазочных материалов
Короткий адрес: https://sciup.org/140215854
IDR: 140215854 | DOI: 10.17073/2500-0632-2016-1-13-18
Текст научной статьи Мониторинг технического состояния редукторов частотно-регулируемого электропривода шахтных ленточных конвейеров
В настоящее время эксплуатируется большое количество ленточных конвейеров. В ближайшее время ожидается увеличение как их количества, так и производительности, а также расстояния транспортирования горной массы. Растет энерговооруженность и техническая оснащенность ленточных конвейеров, широко внедряется частотнорегулируемый электропривод. От работоспособного состояния конвейеров зависит работа всего предприятия в целом.
Повышающиеся объемы добычи угля комплексно-механизированными очистными забоями вместе с увеличением безопасности производства работ требуют создания надежных транспортных систем. Высокая эффективность и бесперебойность в работе с одновременным снижением энергопотребления - основная задача, стоящая перед производителями поточных линий шахтных ленточных конвейеров. Другой не менее важной задачей является сокращение затрат на их техническое обслуживание и ремонт. Для обеспечения безотказности работы ленточного конвейера в течение как можно более продолжительного времени необходимо определить причины выхода из строя различных составляющих элементов [1].
Анализ простоев, вызванных отказами редуктора ленточного конвейера, показывает от 7,4 до 18,2% от общего числа отказов, и составляет в среднем 12%. Необходимо отметить, что процент отказов стыков ленты преобладает в общем числе отказов. При этом отказы происходят часто, но среднее время на их устранение составляет 1,5–2 ч. Отказы, вызванные неисправностью редуктора происходят редко, но при этом среднее время на восстановление составляет от 24 до 48 ч.
Таким образом, распознавание фактического технического состояния редукторов шахтных ленточных конвейеров является весьма актуальной задачей.
Факторы, влияющие на сигнал вибрации от редуктора, можно разделить на четыре основные группы: проектирование, технология производства, монтаж, и изменение состояния в процессе эксплуатации [2].
Влияние первых двух групп, как правило, устраняют изготовители. Ошибки монтажа обычно проявляются в дисбалансе и расцентровке и выявляются при первом замере вибрации. Основной задачей является распознавание изменения состояния при эксплуатации. На сегодняшний день, анализ вибрации является сильнейшим и наиболее распространенным методом выявления и определения неисправности шестерен редуктора [3].
В работе приведены данные по мониторингу параметров смазочного масла и вибрации шахтного ленточного конвейера 3ЛЛ1600 длиной L 850 м , технической производительностью Q = 3500 т/ч , скоростью движения ленты v = 0-4 м/с .
В приводах конвейеров используются редукторы Moventas Santasalo:
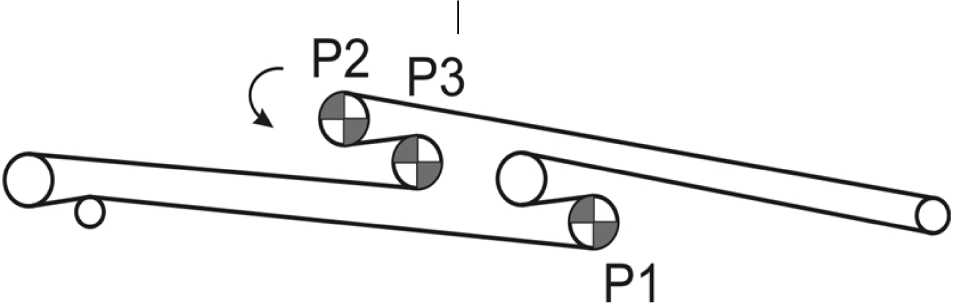
Рис. 1. Схема обводки приводных барабанов лентой и расположение редукторов
тип коническо-цилиндрический
D3RST82XO;
передаточное число i 20, 6128 ;
номинальная механическая мощность при сервис-факторе FS 1 P м.ном 995 кВт;
номинальная термическая мощность при сервис-факторе FS 1, и температуре окружающей среды t 20°С
P т.ном 779 кВт ;
допустимая температура масла t 90°С.
м установленная мощность двигателя P 500кВт;
частота вращения быстроходного вала n 1500 об/мин (25 Гц).
Частотно-преобразовательная станция шахтная типа ЧПСШ-1250/6-0,69-2-УХЛ5 предназначена для бесступенчатого электрического регулирования скорости и крутящего момента одно- или многодвигательного привода ленточного конвейера и подачи напряжения питания на все вспомогательные устройства станции и конвейера в подземных горных выработках шахт, опасных по газу (метан) и угольной пыли в соответствии с требованиями ПБ [4].
На рис. 1 приведены схема обводки приводных барабанов лентой и расположение редукторов с условными названиями Р1 – Р3.
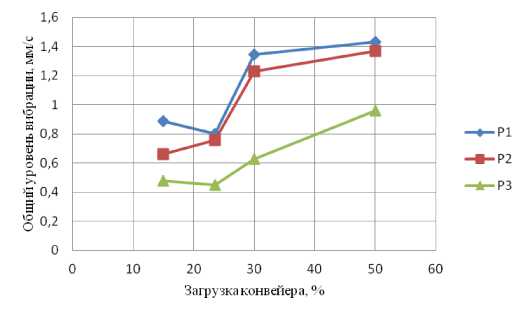
Рис. 2. График зависимости общего уровня вибрации в диапазоне частот 2-200 Гц от загрузки конвейера
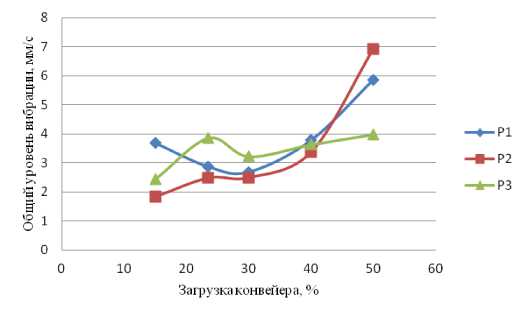
Рис. 3. График зависимости общего уровня вибрации в диапазоне частот 100–2000 Гц от загрузки конвейера
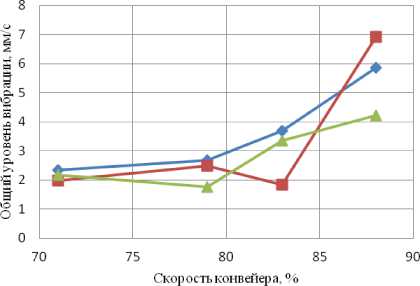
Рис. 4. График зависимости общего уровня вибрации в диапазоне частот 100–2000 Гц от скорости конвейера
Кинематическая вязкость (КВ) по ГОСТ 6258-85
Редуктор |
Температура, °С |
Норма |
Образец от 29.08.14 |
Образец от 19.02.15 |
Образец от 12.03.15 |
Образец от 06.07.15 |
||
КВ, мм2/с |
КВ, мм2/с |
КВ, мм2/с |
КВ, мм2/с |
ВУ |
КВ, мм2/с |
|||
Р1 |
40 |
320,00 |
297,70 |
307,00 |
325,20 |
45,40 |
345,00 |
|
100 |
24,10 |
25,33 |
24,17 |
24,50 |
3,50 |
25,33 |
||
Р2 |
40 |
320,00 |
335,50 |
345,50 |
341,40 |
46,30 |
351,20 |
|
100 |
24,10 |
24,67 |
24,50 |
25,83 |
3,58 |
26,00 |
||
Р3 |
40 |
320,00 |
304,80 |
308,60 |
335,50 |
43,30 |
329,70 |
|
100 |
24,10 |
23,33 |
24,67 |
24,67 |
3,58 |
26,00 |
В течение двух месяцев от начала работы производились замеры параметров вибрации в зависимости от загрузки и скорости ленточного конвейера (рис. 2–4). Данные о загрузке и скорости записывались по показаниям мониторов частотнопреобразовательной станции ЧПСШ.
Проанализировав параметры вибрации, можно сделать вывод, что наиболее загруженным является редуктор Р1, а наименее загруженным Р3, что соответствует классической теории расчета тягового усилия на приводных барабанах ленточных конвейеров [5].
Особенностью приводов с регулируемой частотой вращения является зависимость уровней вибрации от частоты вращения приводного двигателя, а также наличие дополнительных помех и шумов [12]. Для стадии приработки минимальные уровни вибрации наблюдаются для уровней загрузки 25–30%.
Далее проводился анализ параметров смазочного масла и вибрации в зависимости от наработки ленточного конвейера в соответствии с требованиями нормативных документов [6–11].
Данные о кинематической вязкости приведены в табл. 1 и на рис. 5. Результаты накопления механических примесей для редуктора Р1 приведены в табл. 2, а основных примесей для остальных редукторов показаны на рис. 6, 7.
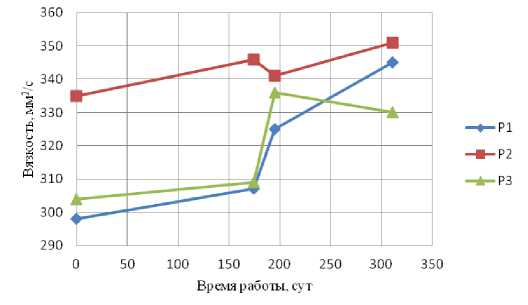
Рис. 5. График изменения кинематической вязкости масла от наработки
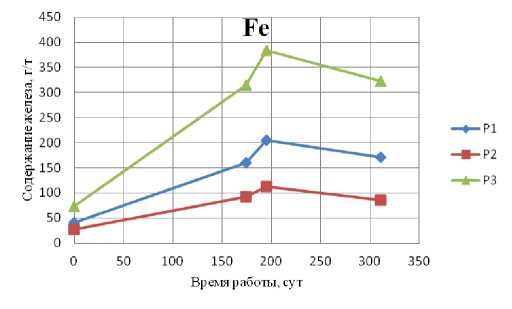
Рис. 6. График изменения содержания железа от наработки
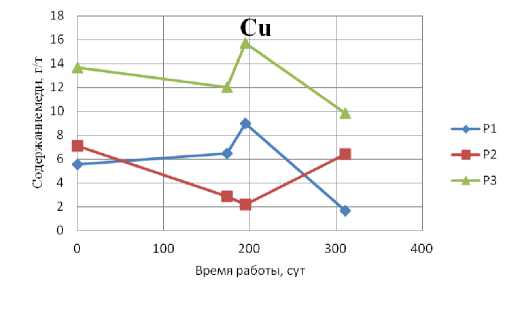
Рис. 7. График изменения содержания меди от наработки
Продукты износа редуктора Р1, г/т
Элементы |
Допустимые пределы |
Образец от 29.08.14 |
Образец от 19.02.15 |
Образец от 12.03.15 |
Образец от 06.07.15 |
Fe |
126 - 200 |
40,340 |
160,120 |
204,800 |
171,520 |
Si |
21 - 30 |
37,640 |
33,880 |
44,550 |
39,830 |
Cu |
100 - 150 |
5,526 |
0,480 |
8,960 |
1,650 |
Al |
4 - 7 |
1,518 |
1,540 |
2,380 |
2,000 |
Cr |
2 - 5 |
0,683 |
1,300 |
1,070 |
1,150 |
Pb |
- |
2,547 |
3,450 |
4,230 |
2,480 |
Sn |
- |
5,781 |
9,340 |
7,900 |
6,980 |
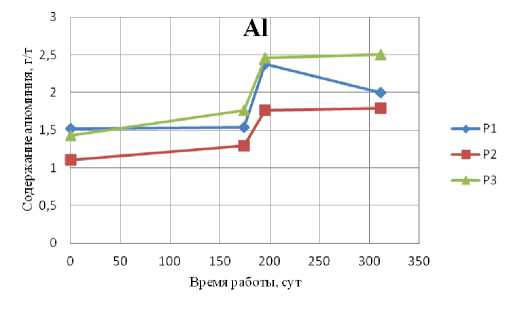
Рис. 8. График изменения содержания алюминия от наработки
Данные о температуре вспышки в открытом тигле приведены в табл. 3.
Анализ изменения параметров масла показывает, что в процессе работы вязкость возрастает за счет испарения низкокипящих фракций. При этом, чем выше начальная вязкость, тем меньше накапливается механических примесей, менее интенсивно идут процессы износа: 1 – 28.08.14, 2 – 19.02.15, 3 – 12.03.15, 4 – 06.07.15 подшипников и зубьев шестерен в редукторе (см. рис. 5–8).
На рис. 9–11 представлены спектры среднего квадратичного значения виброскорости в диапазоне, характерном для зубцовых частот редукторов. Замеры проводились согласно [4] для точки вторичного вала в осевом направлении, сильнее всего характеризующего вибрацию на частотах зубозацепления первой пары шестерен.
Проанализировав спектры (см.
редукторе Р1, а меньшие – в редукторе Р3.
Завод-изготовитель редукторов Moventas Santasalo рекомендует производить первую замену через 800–1000 ч работы, а далее через 10 000 ч работы или один раз в год. Фактически первая замена масла не производилась, только доливка через 5000 ч. Состояние масла в данный момент удовлетворительное в редукторах Р1 и Р2, в редукторе Р3 превышены концентрации механических примесей железа (Fe).
Таким образом, результаты мониторинга с начала эксплуатации конвейеров позволяют выбрать критерии хорошего состояния элементов редуктора в зависимости от его нагрузки и скорости и разработать рекомендации по замене смазочных масел в зависимости от местоположения редуктора в технологической схеме конвейера.
Температура вспышки в открытом тигле, °С (ГОСТ 26378.4-84)
Редуктор |
Норма (DIN ISO 2592) |
Образец от 29.08.14 |
Образец от 19.02.15 |
Образец от 12.03.15 |
Образец от 06.07.15 |
Р1 |
255 |
226 |
222 |
238 |
236 |
Р2 |
255 |
248 |
228 |
235 |
215 |
Р3 |
255 |
234 |
225 |
230 |
235 |
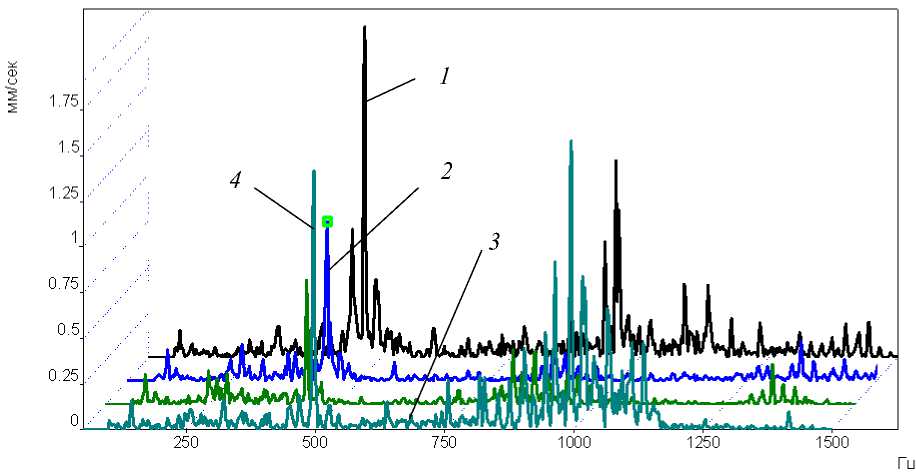
Рис. 9. Сравнение спектров виброскорости в диапазоне от 100 до 1500 Гц редуктора Р1: 1 – 28.08.14; 2 – 19.02.15;
3 – 12.03.15; 4 – 06.07.15
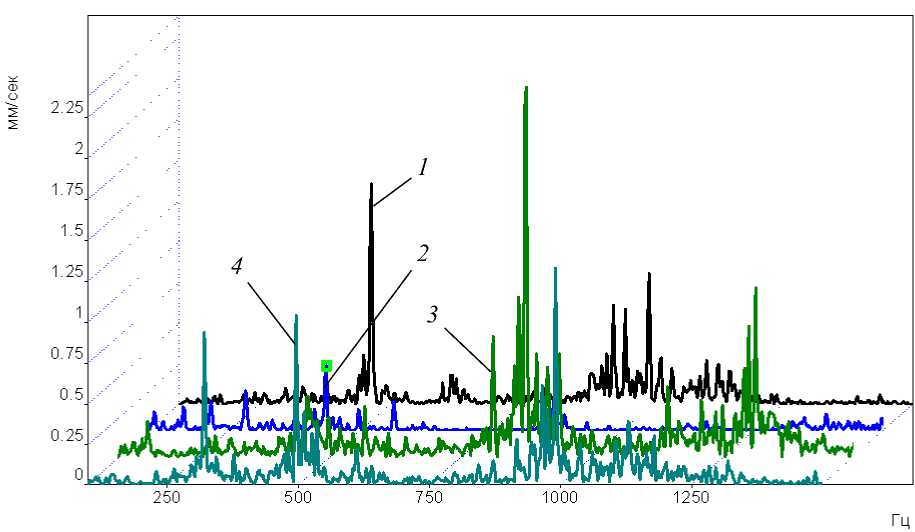
Рис. 10. Сравнение спектров виброскорости в диапазоне от 100 до 1500 Гц редуктора Р2: 1 – 28.08.14; 2 – 19.02.15;
3 – 12.03.15; 4 – 06.07.15
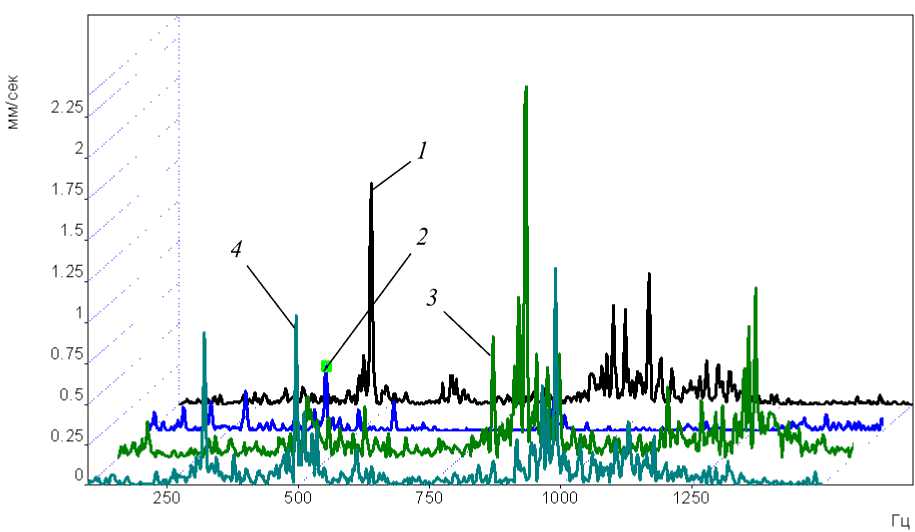
Рис. 11. Сравнение спектров виброскорости в диапазоне от
100 до 1500 Гц редуктора Р3: 1
28.08.14; 2 – 19.02.15;
3 – 12.03.15; 4 – 06.07.15
Список литературы Мониторинг технического состояния редукторов частотно-регулируемого электропривода шахтных ленточных конвейеров
- Герике Б.Л., Абрамов И.Л., Герике П.Б. Вибродиагностика горных машин и оборудования. Учеб. пособие. Кемерово, 2007. 167 с.
- Bartelmus W.: Vibration condition monitoring of gearboxes. Machine Vibration 1992 nr1 s.178-189.
- Ali Rostami, Rohallah Panahi Leavoli, Jalaleddin Ghezavati, Mohommad Homaei. Gearbox fault Detection using vibration signals based on the method of Hilbert. Indian Journal of Scientific Research 1(2): p. 675-689, 2014.
- Конвейер шахтный ленточный грузопассажирский 3ЛЛ 1600. Руководство по эксплуатации. ООО «Центр транспортных систем», Кемерово, 2011.
- Васильев К.А. Транспортные машины и оборудование шахт и рудников: учеб. пособие/К.А. Васильев, А. К. Николаев, К.Г. Сазонов. СПб.: Изд-во «Лань», 2012. -544 с.
- ГОСТ ИСО 10816-1-97 Контроль состояния машин по результатам измерений вибрации на невращающихся частях.
- ГОСТ 6258-85. Нефтепродукты. Метод определения условной вязкости
- ГОСТ 26378.4-84. Нефтепродукты отработанные. Метод определения температуры вспышки в открытом тигле.
- ГОСТ Р 52659-2006. Нефть и нефтепродукты. Методы ручного отбора проб.
- ГОСТ 25371-97. Нефтепродукты. Расчет индекса вязкости по кинематической вязкости.
- ГОСТ 6370-83. Нефть, нефтепродукты и присадки. Метод определения механических примесей.
- J. Obuchowski, A. Wylomańska, R. Zimroz, "Recent Developments in Vibration Based Diagnostics of Gear and Bearings Used in Belt Conveyors", Applied Mechanics and Materials, Vol. 683, pp 171-176. doi:10.4028/http://www.scientific.net/AMM.683.171.