Наладка теплового режима работы гофроагрегата
Автор: Бойков Лев Михайлович, Нечаев Николай Сергеевич
Журнал: Технико-технологические проблемы сервиса @ttps
Рубрика: Диагностика и ремонт
Статья в выпуске: 1 (11), 2010 года.
Бесплатный доступ
На основе результатов обследования работы гофроагрегатов разработаны мероприятия по наладке теплового режима агрегатов с целью устранения дефектов при выпуске гофрокартона и повышения эффективности эксплуатации установок.
Гофроагрегат, гофрокартон, гофропресс, пароконденсатная система
Короткий адрес: https://sciup.org/148185822
IDR: 148185822
Текст научной статьи Наладка теплового режима работы гофроагрегата
В последние годы гофрированный картон (ГК) является предметом повышенного спроса, поэтому идет быстрый прирост мощностей по его производству. При этом вводятся в действие предприятия как с одним гофроагрега-том (ГА) шириной 1050 мм и скоростью 30 – 70 м/мин, так и с тремя гофроагре-гатами, каждый из которых имеет ширину 2100 мм и скорость до 360 м/мин.
Изготавливаемый на этих агрегатах гофрированный картон (гофрокартон) представляет собой пространственную структуру, состоящую из плоских слоев картона и внутреннего одного гофрированного слоя или нескольких слоев бумаги [1-6]. Он состоит из чередующихся плоских и гофрированных слоев, склеенных различными адгезивами по линии контакта. Гофрокартон – главный вид материала для изготовления картонной тары. Гофрокартон – прочный, дешевый, легкий материал, обладающий амортизационными анизотропными свойствами. Применяют двух- и трехслойные виды гофрированного картона толщиной 2,8 – 5,0 мм, пятислойные – толщиной – 7,5 – 8,0 мм.
Для образования гофрированного слоя в ГК используется бумага для гофрирования, называемая часто в зарубежной литературе «флютингом». Некоторые производства вырабатывают бумагу для гофрирования из 100 % макулатуры. Плоские слои гофрированно- го картона (лайнера) подразделяются на тест-лайнер (изготовленный в значительной части из макулатуры) и крафт-лайнер (изготовленный полностью из сульфатной небеленой целлюлозы). Гофрированный картон оценивается показателями, основными из которых являются сопротивление продавливанию, торцевому сжатию вдоль гофров и расслаиванию.
В нашей стране гофры в порядке убывания высоты используются типа А, С и В с высотой гофра соответственно 4,6; 3,6; 2,6 мм и шагом гофра – 8,9; 7,9; 6,1 мм.
Изготовление гофрокартона производится на гофрировальных агрегатах. Гофроагрегат (рис.1, 2) представляет собой ряд скомпонованных в одну линию отдельных машин и узлов, на которых осуществляется не только процесс производства гофрированного картона, но и отдельные операции по его переработке. В конечном итоге с агрегата сходят листовые заготовки картонных ящиков. Разматываемое из рулона полотно бумаги через подогреватель и увлажнитель подается к нагреваемым паром рифленым валам гофрирующей машины. Для увлажнения бумаги и картона (до 7 – 8%) перед их нагревом применяют паровые увлажнители трубчатого типа, через которые на полотно подается насыщенный пар.
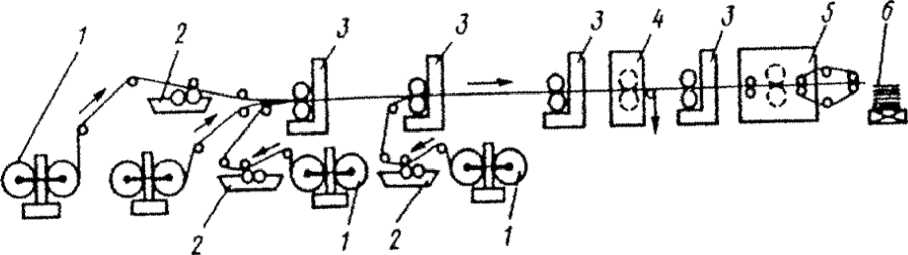
Рисунок 1 - Схема гофроагрегата: 1 - раскаты; 2 - узел нанесения клея; 3 - гофропрессы; 4 -устройство для обрезки кромок; 5 – станок для резки; 6 – укладчик картона в стопы
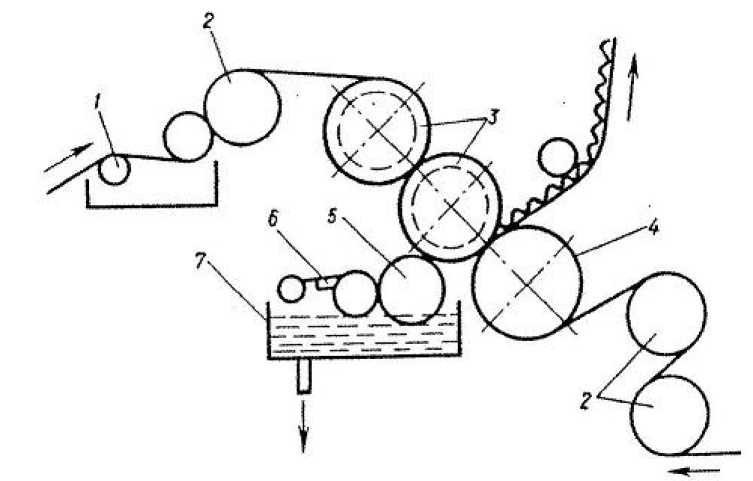
Рисунок 2 – Схема узла гофрирования : 1 – выравнивающий валик; 2 – вал натяжения бумаги; 3 – гофрировальные прессовые валы; 4 – прижимной вал; 5 – клеенаносящий вал; 6 – шабер; 7- клеевая ванна
Подогреватель бумаги снабжается насыщенным паром от 100 до 1750С, подогреватель картона работает в интервале температур пара 185 – 1900С. Основным элементом ГА является гоф-ропресс (рис. 2), состоящий из двух рифленых гофрирующих валов диаметром от 300 до 350 мм.
Перед склейкой гофрированного картона бумагу для гофрирования нагревают и пропускают через узел гофрирования, который состоит из верхней и нижней гофрирующих плит синусоидальной формы. Затем бумага проходит через пару рифленых валов, нагреваемых паром, и поступает на узел склейки. Для улучшения качества гофриро- умные устройства предварительного нагрева и шабер для нанесения на вершины гофров клеевой суспензии. После чего к вершинам гофров приклеивается поступающее через подогреватели и систему валиков полотно картона.
В результате этого образуется двухслойный ГК. После склейки этот картон поступает через мост-накопитель в клеильный узел, где склеивается со вторым плоским слоем с образованием трехслойного картона. Для изготовления пятислойного картона требуется еще один гофроперсс (ГП) и добавочное клеильное устройство в клеильный узел. В качестве клея используется крахмальный (чаще) и силикатный клей.
ванного картона предусмотрены ваку-
Окончательная склейка и формирование ГК происходит в сушильной части (на сушильном столе) ГА. Сушильная часть состоит из нижних нагревательных плит, обогреваемых паром, металлической сетки и прижимного устройства в виде валиков. Прижим валиков к сушильному столу позволяет регулировать интенсивность сушки ГК по длине и ширине полотна.
Температуру бумаги перед гофрированием целесообразно поддерживать около 127 0С, температура гофро-валов (ГВ) должна находится в интервале 178 – 182 0С.
На производительность ГА и качественное гофрирование бумаги существенно влияют такие факторы, как влажность и натяжение бумаги перед гофрированием, давление между гофро-валами и их температура.
При прохождении каждого рифа гофрирующего вала в зазоре между гофровалами бумага прогибается и растягивается.
Температурное воздействие необходимо разграничить, т.е. назначение подогрева и увлажнения перед гофрированием, во-первых, определяется необходимостью пластификации бумаги и увеличения ее растяжимости, чтобы улучшить условия прохождения бумаги зоны гофрирования. Во-вторых, при тепловом воздействии ГВ удаляется излишняя влага, кроме того, бумага в зоне сжатия пластифицируется, и в ней образуются дополнительные поперечные связи.
В производственных условиях формирование гофров в полный профиль происходит при линейном давлении не менее 70 кН/м. Концентрация клея оказывает существенное влияние на количество испаряющейся воды. Обычно используют модифицированный крахмальный клей концентрацией 20 %, а на высокоскоростных гофроаг-регатах концентрация клея – 23 – 25 % абсолютно сухого вещества.
Одной из важных проблем, влияющих на качество склейки, является слишком низкая (меньше 7-8 %) или неравномерная по ширине полотна влажность.
В сушильной части, в зависимости от скорости ГА, вида клея, слоев картона, поддерживается либо первый температурный режим сушки полотна на сушильном столе: 1 группа плит – 110 – 190 0С, 2 группа – 140 – 170 0С, 3 группа – 130 - 150 0С, либо второй режим: 110 – 140 0С, 2 – 140 – 150 0С, 3 – 150 – 160 0С, 140 – 190 0С соответственно. Температура в группах поддерживается путем регулирования подачи пара в нагревательные плиты.
Характеристика работы ГА следующая. Давление пара в главном паропроводе составляет 1,4 – 1,5 МПа; температура пара – 200 – 220 0С; температура поверхности валов гофропресса – 180 – 200 0С; давление пара на увлажнение – 0,3 – 0,6 МПа; давление пара в гофровалах и прижимном вале – 1,4 – 1,5 МПа. Вязкость клея – 25 – 35 сек.; температура клея – 30 0С. Величина зазора между клеенаносящим и прижимным валами – 0,1 – 0,3 мм; величина зазора между нижним рифленым и прижимным валами – 0,3 – 0,5 мм; величина зазора между клеенаносящим и нижним рифленым валами – 0,3 – 0,5 мм. Угол обхвата подогревателя полотном: бумаги 0 – 2000, картона – 200 – 2500. Давление воды в гидроцилиндрах рифленого и прижимного валов – 2,0 – 4,0 МПа.
Теоретический удельный расход пара для производства 1000 м 2 составляет 1,68 ГДж (0,4 Гкал); электроэнергии – 15 кВт .ч. На действующих ГА фактический удельный расход теплоты превышает теоретический в 2 – 3 раза. Кроме того, часто не соблюдается качество ГК.
На одном из ГА произведено обследование с целью устранения дефектов на готовой продукции. Дефекты связаны с наличием локальных воздушных вздутий на ГК, которые имеют неорганизованный бессистемный характер.
Характеристика работы ГА следующая: скорость ГА – 100 м/мин, ши- рина полотна - 2,1 м, масса 1 м 2 полотна бумаги для гофрирования - 125 г/м 2, начальная сухость полотна бумаги, поступающей на ГП, составляет 94%, с учетом увлажнения (2%) - 92%, производительность ГА- 2205 кг/ч, величина гофрирования - 1,4.
Произведено обследование пароконденсатной системы (ПКС) ГА с целью устранения дефектов на полотне. При этом особое внимание уделено эффективности работы ПКС и ГП. Причины дефектов следующие:
-
- недостаточно высокая температура ГВ (порядка 1760С);
-
- неравномерность прогрева ГВ;
-
- неудовлетворительная работа конденсатоотводчиков (КО) после ГВ.
Кроме того, при увеличении скорости ГА выше 100 м/мин отмечалось увеличение дефектных мест в ГК. Задача обследования сводилась к устранению вышеперечисленных дефектов и обеспечение стабильной работы ГА без дефектов продукции при скорости 100 -120 м/мин. В связи с этим, выполнен следующий объем работ [7-9]:
-
- на ГА применена параллельная схема ПКС, поэтому имеет место значительный перерасход теплоты и пара, который составляет соответственно 4,06 ГДж/кг картона (0,97 Гкал/т картона) и 1,42 т пара /т картона. Выяснены причины перерасхода тепловой энергии;
-
- изучена возможность повышения температуры пара перед ГП со 180 до 200 - 210 0С;
-
- измерена температура паропровода на участке от общего парового коллектора до ГА;
-
- измерена температура на гоф-ровалах ГП без полотна и с полотном;
-
- произведена ревизия конденса-тоотводчиков от каждого ГВ;
-
- произведены замеры температур от гофровалов и на общем конлен-сатопроводе;
-
- выполнен тепловой расчет общего паропровода для необходимого расхода пара на гофрирование бумаги марки Б-1 массой 125 г/м2;
-
- произведен расчет производительности ГА, количества теплоты и расхода пара при скорости ГА 100,110 и 120 м/мин;
-
- выполнен расчет проходного сечения конденсатоотводчиков при скорости ГА 100,110 и 120 м/мин;
-
- выполнен анализ полученных результатов, сделаны выводы и разработаны рекомендации по работе ГА без дефектов.
Выводы по работе сделаны следующие:
-
1) в главном паропроводе на участке от распределительного коллектора до ГА температура пара существенно снижена с 230 до 180 - 200 0С. Особенно это относится к паропроводу у ГП (около 180 0С), что снижает эффективность нагрева валов ГП и влияет на появление дефектов в готовом полотне ГК;
-
2) конденсатоотводчики от гоф-ровалов имеют малое проходное сечение (5 мм), что приводит к накоплению конденсата и воздуха внутри валов. Это снижает эффективность теплопередачи и приводит к дефектам;
-
3) отсутствует продувка валов паром, которая необходима для удаления конденсата и воздуха;
-
4) увлажнитель бумаги работает на перегретом паре при температуре
180 0С, который имеет очень большую скорость (50 - 75 м/мин). В результате полотно ГК увлажняется недостаточно. Как следствие, уменьшается пластичность бумаги для гофрирования;
-
5) отсутствует подогрев бумаги на подогревателе, что снижает эффективность образования гофров;
-
6) большой диаметр паропровода, по которому пар поступает к ГП и большой диаметр общего конденсато-провода от ГА;
-
7) в схеме ПКС ГП имеются кон-денсатоотводчики, которые при удалении из валов пароконденсатной смеси создают дополнительное гидравлическое сопротивление. На преодоление этого сопротивления затрачивается по-
- вышенное давление, Это приводит к увеличению расхода пара и удельного расхода теплоты;
-
8) в существующей схеме ПКС ГА отсутствует система утилизации теплоты и пара;
-
9) установлено, что наибольшее влияние на степень сушки нижнего слоя картона оказывает тепловой режим плит второй паровой группы сушильного стола, а на верхний слой – первой группы. Если в нижнем слое происходит удаление влаги клеевой прослойки, то верхний слой на этой стадии увлажняется.
Для устранения существующих дефектов готовой продукции и недостатков рекомендуется проведение следующих мероприятий:
-
- заменить общий паропровод к ГА на паропровод диаметром 60 мм;
-
- проложить новый паропровод по трассе с меньшими изгибами и меньшим гидравлическим сопротивлением. Это позволит подать к ГА перегретый пар с температурой 205 – 210 0С;
-
- отказаться от конденсатоотвод-чиков и полнее использовать теплоту парообразования;
-
- если принять существующую схему ПКС и оставить конденсатоот-волчики, то следует в них рассверлить сечение шайб до расчетного диаметра 9,2 мм, чтобы обеспечить прохождении пролетного пара;
-
- увлажнение бумаги для гофрирования следует производить насыщенным паром при давлении 0,5 - 0,6 МПа и температуре 143,6 – 151,9 0С;
-
- включить обогрев подогревателей бумаги для гофрирования (БГ) и картона для плоских слоев (КПС) паром при давлении 0,5 - 0,6 МПа;
-
- производить контроль массы 1 м 2 и влажности БГ и КПС, следить за необходимой концентрацией клея;
-
- увязать ПКС ГА, ГП и сушильного стола в одну схему. Этим достигается снижение удельных затрат теплоты.
Реализация предложенных рекомендаций позволила устранить дефекты, влияющие на качество готовой продукции, и сократить удельные затраты теплоты.