Научное обоснование применения тепловой и электрохимической обработки для повышения эффективности пенной сепарации алмазосодержащих руд
Автор: Коваленко Евгений Геннадьевич, Двойченкова Галина Петровна, Поливанская Валерия Владимировна
Журнал: Горные науки и технологии @gornye-nauki-tekhnologii
Статья в выпуске: 3, 2014 года.
Бесплатный доступ
С применением термохимического анализа процессов фазообразования в водной среде и на поверхности минералов проведено научное обоснование и выбор условий операций теплового и электрохимического кондиционирования питания и оборотной воды пенной сепарации алмазосодержащего сырья. Проведенными расчетами показано, что оборотная вода и жидкая фаза пульпы пересыщена по ионам кальция и карбоната, а образование карбонатных минералов на поверхности алмазов возможно как в операции измельчения, так и пенной сепарации. Результатами экспериментов показано, что применение тепловой обработки и электрохимически обработанной оборотной воды позволяет уменьшить концентрацию угольной кислоты и подкислить жидкую фазу, что обеспечивает растворение карбонатных пленок с поверхности алмаза и повышение его флотируемости.
Пенная сепарация, алмазосодержащее сырье, карбонатные пленки, оборотная вода, термохимические расчеты, диаграммы устойчивости
Короткий адрес: https://sciup.org/140230075
IDR: 140230075
Текст научной статьи Научное обоснование применения тепловой и электрохимической обработки для повышения эффективности пенной сепарации алмазосодержащих руд
Важной причиной снижения показателей процесса пенной сепарации алмазов является гидрофилизация поверхности алмазов вследствие воздействия ионно-молекулярных компонентов жидкой фазы пульпы [1]. Задача повышения показателей обогащения алмазосодержащих кимберлитов может быть решена на основе применения физических и физико-химических методов воздействия на твердую и жидкую фазу пульпы, обеспечивающих предотвращение зарастания или очистку поверхности алмазов. В качестве таких операций были применены и доказали свою эффективность подогрев питания пенной сепарации и бездиафрагменная электрохимическая обработка оборотной воды [2].
Для повышения эффективности применения этих операций необходимо исследовать реакции, протекающие на поверхности и выбрать оптимальные условия протекания процессов активации поверхности алмазов.
Моделирование и анализ процессов фазообразования в водной среде и на поверхности минералов были осуществлены на основе термодинамического анализа межфазных химических реакций, выполненного в виде диаграмм термодинамически стабильных соединений в координатах lg[CO3] – pH.
Методика термодинамического моделирования образования и растворения окисленных и солеобразных минералов соответствовала общепринятой для расчета диаграмм термодинамической стабильности [3]. Определение границ устойчивости минералов включало составление реакции перехода, расчет стандартного изобарно-изотермического потенциала реакции (ΔG0), расчет константы реакции, определение связи между параметрами системы координат диаграммы из уравнения константы реакции.
Значения ΔGo компонентов реакции брались из соответствующей справочной литературы [4, 5]. Величина логарифма константы (lgK) реакций рассчитывалась с применением уравнения lgKр = - ΔGр0/RT*2,303
где: R - универсальная газовая постоянная (8,314 Дж/моль*К); Т -температура,оК; 2,303 – коэффициент перехода к десятичному логарифму.
При проведении анализа в расчет принимались реакции, проходящие с участием ионов кальция и магния, карбонатных и гидроксидных минералов. В табл. 1 и 2 представлены термодинамические константы индивидуальных веществ и реакции, протекающих с участием ионов кальция, магния и железа.
Таблица 1.
Стандартные энтальпии образования (AHo обр. ), стандартные энергии Гиббса образования (AGo обр ) и их стандартные энтропии So веществ
Вещество и состояние |
AHo обр кДж/моль |
AGo обр кДж/моль |
So Дж/(моль К) |
1 |
2 |
3 |
4 |
Ca2+ (р-р; бесконечн.Н 2 О) |
-543,1 |
-552,8 |
56,5 |
CaCO 3 (к) |
-1206,8 |
-1128,4 |
91,7 |
Ca(OH) 2 (к) |
-985,1 |
-897,1 |
83,4 |
CaSO 4 (к) |
-1436,3 |
-1323,9 |
106,7 |
Mg2+ (р-р; бесконечн.Н 2 O) |
-468,1 |
-457,3 |
-133,9 |
MgO (к) |
-601,5 |
-569,3 |
27,07 |
Mg(OH) 2 (к) |
-924,7 |
-833,7 |
63,2 |
MgСO 3 (к) |
-1095,85 |
-1012,15 |
65,10 |
MgCO 3 ∙Mg(OH) 2 ∙3H 2 O |
-2901,7 |
-2584,1 |
127,4 |
CaMg(CO3)2 |
-2336,1 |
-2175,7 |
157,5 |
Fe2+ (р-р; бесконечн.Н2O) |
-87,9 |
-84,94 |
-113,4 |
FeСO3 (к) |
-738,15 |
-665,1 |
95,4 |
Продолжение табл. 1.
1 |
2 |
3 |
4 |
Fe(OH) 2 (к) |
-562 |
-479,7 |
88 |
Fe(OH) 3 (к) |
-827 |
-699,6 |
105 |
Fe 2 O 3 (к) |
-822 |
-740 |
87 |
Fe 3 O 4 (к) |
-1117,13 |
-1014,17 |
146,19 |
Таблица 2.
Термодинамические параметры реакций с участием карбонатных и гидроксидных породообразующих минералов
№ № |
Уравнения реакций |
AG0 кДж/мо ль |
LgK |
1 |
CaCO 3 + H+ = Ca2++ НCO 3 - |
-10,7 |
1,88 |
2 |
MgCO 3 + H+ = Mg2++ НCO 3 - |
-32,63 |
5,72 |
3 |
CaMg(CO 3 ) 2 + 2H+ = Ca2++Mg2++2НCO 3 - |
-9,36 |
1,64 |
4 |
CaCO 3 + 2H+ = Ca2++ Н 2 CO 3 |
-47,1 |
8,25 |
5 |
MgCO 3 + 2H+ = Mg2++ Н 2 CO 3 |
-69,01 |
12,10 |
6 |
CaMg(CO 3 ) 2 + 4H+ = Ca2++Mg2++2Н 2 CO 3 |
-82,12 |
14,39 |
7 |
CaCO 3 + 2H 2 О = Ca(ОН) 2 +CO 3 2- + 2H+ |
179,51 |
-31,47 |
8 |
MgCO 3 + 2H 2 О = Mg(ОН) 2 +CO 3 2- + 2H+ |
125,49 |
-22,00 |
9 |
Mg2++2H 2 О = Mg(ОН) 2 + 2H+ |
99,12 |
-17,37 |
10 |
CaMg(CO 3 ) 2 +4H 2 О=Ca(ОН) 2 +Mg(ОН) 2 +2CO 3 2-+4H+ |
338,98 |
-59,42 |
11 |
MgCO 3 ∙Mg(OH) 2 ∙3H 2 O + 3H+ = 2Mg2++ НCO 3 - + 5Н 2 О |
-96,75 |
16,96 |
12 |
MgCO 3 ∙Mg(OH) 2 ∙3H 2 O + НCO 3 -+ H+= 2MgCO 3 + 5Н 2 О |
-41,49 |
7,27 |
13 |
MgCO 3 ∙Mg(OH) 2 ∙3H 2 O = 2 Mg(ОН) 2 + НCO 3 - +H++ Н 2 О |
101,49 |
-17,79 |
14 |
FeCO 3 + 2H+ = Fe2++H 2 CO 3 |
-43,7 |
7,66 |
15 |
FeCO 3 + H+ = Fe2++HCO 3 - |
-7,32 |
1,28 |
16 |
FeCO 3 + 2H 2 О = Fe(OH) 2 +HCO 3 - + H+ |
73,44 |
-12,87 |
17 |
FeCO 3 + 2H 2 О = Fe(OH) 2 +CO 3 2- + 2H+ |
132,44 |
-23,22 |
18 |
Fe2++ 2H 2 О = Fe(OH) 2 + 2H+ |
80,76 |
-14,16 |
В природе встречаются две основные кристаллические модификации карбоната кальция: кальцит и арагонит [3]. Как правило, карбонат кальция из природных вод при наличие пресыщения кристаллизуется в форме кальцита.
При выборе реакций с участием ионов магния принимались во внимание известные данные о том, что в водном растворе магния карбонат гидролизуется, поэтому при в растворе образуются основные карбонаты состава x MgCO 3 . y Mg(OH) 2 . z H 2 O [6].
При взаимодействии MgCO 3 с карбонатами щелочных и щелочноземельных металлов могут образовываться труднорастворимые двойные карбонаты, например MgCa(CO 3 ) 2 (доломит) [3].
Ионы двухвалентного железа в нейтральной и слабощелочной среде связываются в карбонат железа – FeCO 3 (сидерит). При повышении рН среды образуется гидроокись железа - Fe(OH) 2 , медленно превращающаяся в результате кристаллизации в оксид железа FeO. При окислении железа до Fe3+ очень быстро образуется гидроксид железа, который медленно переходит в оксид железа Fe2O3 [3].
После расчета констант равновесия рассматриваемых реакций проводились преобразования выражений для константы в расчетное уравнение, связывающие концентрации ионов угольной кислоты с концентрациями прочих ионных компонетов жидкой фазы пульпы.
В табл. 3 представлены конечные уравнения, связывающие рН и концентрацию одной из форм угольной кислоты (молекулярной, бикарбонатной и карбонатной) в жидкой фазе пульпы в граничных условиях образования – растворения осадков по модельным химическим реакциям.
Таблица 3.
Преобразованные уравнения для реакций с участием карбонатных и гидроксидных породообразующих минералов [Ca2+] = 2150 мг/л ( 5*10-2 моль/л); [Mg2+] = 460 мг/л ( 2*10-3 моль/л); [Fe2+] = 5,3 мг/л (10-4 моль/л)
№ |
Переход |
Расчетное уравнение |
1 |
CaCO 3 / Ca2+, НCO 3 - |
lg [НCO 3 -] = 3,18 - рН |
2 |
MgCO 3 / Mg2+, НCO 3 - |
lg [НCO 3 -] = 7,42 - рН |
3 |
CaMg(CO 3 ) 2 / Ca2++ Mg2+, НCO 3 - |
lg [НCO 3 -] = 2,32 - pH |
4 |
CaCO 3 / Ca2+, Н 2 CO 3 |
lg [Н 2 CO 3 ] = 9,55- 2pH |
5 |
MgCO 3 / Mg2+, Н 2 CO 3 |
lg [Н 2 CO 3 ] = 13,8 - 2pH |
6 |
CaMg(CO 3 ) 2 / Ca2++Mg2+, Н 2 CO 3 |
lg [Н 2 CO 3 ] = 8,7 – 2pH |
7 |
CaCO 3 / Ca(ОН) 2 , CO 3 2- |
lg [CO 3 2-] = -31,47 + 2pH |
8 |
MgCO 3 / Mg(ОН) 2 , CO 3 2- |
lg [CO 3 2-] = -21,4 + 2pH |
9 |
Mg2+/ Mg(ОН) 2 |
pH= 9,63 |
10 |
CaMg(CO 3 ) 2 /Ca(ОН) 2 +Mg(ОН) 2 , CO 3 2- |
lg [CO 3 2-] = -29,71+ 2pH |
11 |
MgCO 3 ∙Mg(OH) 2 ∙3H 2 O / Mg2+, НCO 3 - |
lg [НCO 3 -] = 20,56 - 3рН |
12 |
MgCO 3 ∙Mg(OH) 2 ∙3H 2 O / MgCO 3 , НCO 3 - |
lg [НCO 3 -] = - 7,27 + pH |
13 |
MgCO 3 ∙Mg(OH) 2 ∙3H 2 O / Mg(ОН) 2 , НCO 3 - |
lg [НCO 3 -] = - 17,79 + pH |
14 |
FeCO 3 / Fe2+ , H 2 CO 3 |
lg [Н 2 CO 3 -] = 11,66 - 2pH |
15 |
FeCO 3 / Fe2+ , HCO 3 - |
lg [НCO 3 -] = 5,28 – pH |
16 |
FeCO 3 / Fe(OH) 2 , HCO 3 - |
lg [НCO 3 -] = -12,87+ pH |
17 |
FeCO 3 / Fe(OH) 2 , CO 3 2- |
lg [CO 3 2-] = -23,22+ 2pH |
18 |
Fe2+ / Fe(OH) 2 |
pH= 8,88 |
При расчетах в уравнения подставлялись концентрации ионов в соответствии с результатами анализа ионно-молекулярного состава жидкой фазы пульпы и оборотной воды. При построении диаграмм термодинамической стабильности учитывались переходы между различными формами угольной кислоты и принималось, что вся угольная кислота представлена преобладающей формой: при рН менее 6,36 - Н2CO3; при рН от 6,36 до 10,34 - НCO3-; при рН более 10,34 - CO32-.
Диаграммы на рис. 1-5 построены для стандартных условий (Т = 250С). Результаты расчетов применимы для относительно узкого интервала температур – от 15 до 350С. Для повышенных температур, характерных при применении тепловой обработки, термодинамические константы веществ и, в частности, их энергии образования изменяются. Это приводит и к изменению значений констант реакций, в т.ч. констант равновесия рассматриваемых химических реакций.
Анализ результатов расчетов показал следующее. Оборотная вода и жидкая фаза пульпы пересыщена по ионам кальция и карбоната. Образование карбоната кальция возможно как в операции измельчения, так и пенной сепарации (рис. 1, обл. 1, 2). Об этом свидетельствует расположение областей 1 и 2 в заметном удалении от границы межфазного перехода.
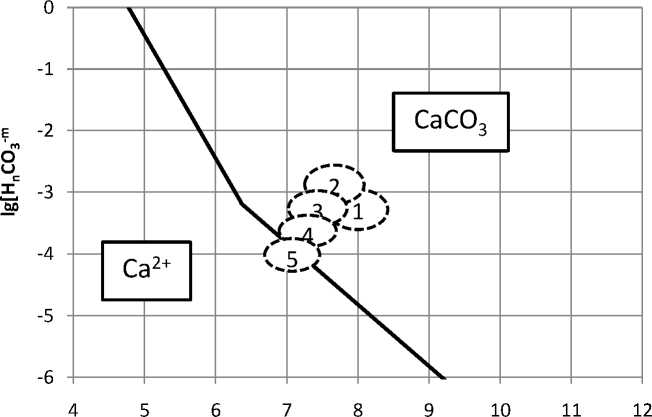
рН среды
Рис. 1. Диаграмма термодинамической стабильности кальцита в жидкой фазе основных технологических переделов: 1 – в операции самоизмельчения; 2 – в операции пенной сепарации; 3 – там же при использовании обработанной оборотной воды; 4 - там же при использовании тепловой обработки; 5 - там же при совместном использовании электрохимической и тепловой обработки
Это означает, что процесс образования карбоната кальция может протекать в течение всего технологического процесса. Поскольку применение электрохимически кондиционированной воды (после бездиафрагменной обработки) ведет к снижению концентраций кальция и бикарбонат-иона (на 30-40%) водная фаза становится менее пересыщенной по отношению к образованию карбоната кальция. Однако, как видно из рис.1 (область 3), такого снижения концентраций недостаточно для предотвращения процесса осадкообразования с образованием карбоната кальция. Более эффективно применение тепловой обработки, вызывающей существенное (в два и более раз) снижение концентрации карбонатных ионов. Область соотношений концентраций ионов бикарбоната и водородных ионов (рН) лежит на границе устойчивости карбоната кальция. Перспективным путем решения задачи предотвращения или снижения интенсивности осадкообразования является сочетание тепловой и электрохимической обработки. Как видно из рис. 1 (обл. 5), именно в этом случае достигается достижение условий, когда жидкая фаза становится «коррозионно-активной» по отношению к карбонатам кальция.
Результаты расчетов (рис. 2) показывают, что во всех рассмотренных продуктах и условиях образование в жидкой фазе карбоната магния (магнезита или гидрокарбоната магния) невозможно. Аналогичным образом невозможно и образование гидроокиси магния.
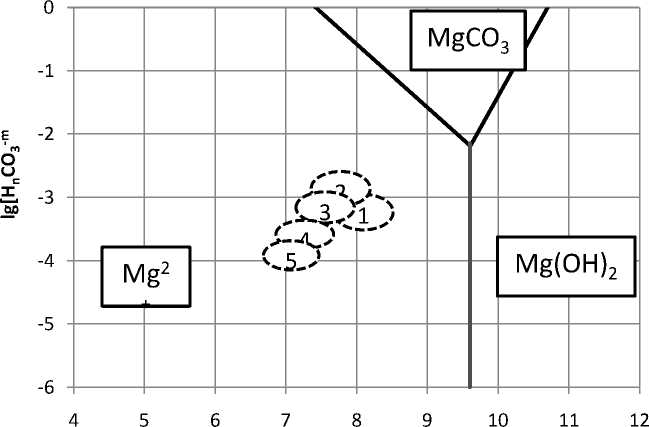
рН среды
Рис. 2. Диаграмма термодинамической стабильности магнезита в жидкой фазе основных технологических переделов: 1 – в операции самоизмельчения; 2 – в операции пенной сепарации; 3 – там же при использовании обработанной оборотной воды; 4 - там же при использовании тепловой обработки; 5 - там же при совместном использовании электрохимической и тепловой обработки
Несколько иначе обстоит дело с образованием основных карбонатов магния. Результаты расчетов показывают, что образование тригидрогидроксокарбоната магния MgCO3Mg(OH)2H2O возможно в основных технологических операциях и может быть предотвращено применением тепловой обработки (обл. 4) или электрохимической и тепловой обработки (обл. 5).
сочетанием

Рис. 3. Диаграмма термодинамической стабильности тригидрогидроксо-карбоната магния в жидкой фазе основных технологических переделов: 1 -в операции самоизмельчения; 2 - в операции пенной сепарации; 3 - там же при использовании обработанной оборотной воды; 4 - там же при использовании тепловой обработки; 5 - там же при совместном использовании электрохимической и тепловой обработки
Значительно более устойчивыми являются смешанные карбонаты кальция и магния, например, доломит. Анализ диаграммы на рис.4 показывает, что образование доломита возможно в жидкой фазе при всех рассматриваемых условиях. Разложение доломита возможно только в результате кислотной обработки при рН менее 5,5 - 6. Такие условия вполне могут быть достигнуты при использовании анолита [7]. Однако необходимо учитывать, что в анолите может происходить накапливание бикарбонатных ионов, которые будут интенсифицировать образование доломита.
Анализ диаграмм показывает, что в любом случае условием интенсификации разложения карбонатных и гидроксидокарбонатных осадков является снижение концентрации бикарбонатных ионов и смещение рН в кислую область. Как было отмечено выше влияние тепловой обработки на растворение минеральных пленок неоднозначно. С одной стороны - повышение температуры ведет к снижению ПР карбонатов и гидроксидокарбонатов кальция и магния, а с другой стороны - ведет к снижению растворимости углекислоты и, соответственно, концентрации - бикарбонатных ионов, и далее - растворению минералов.
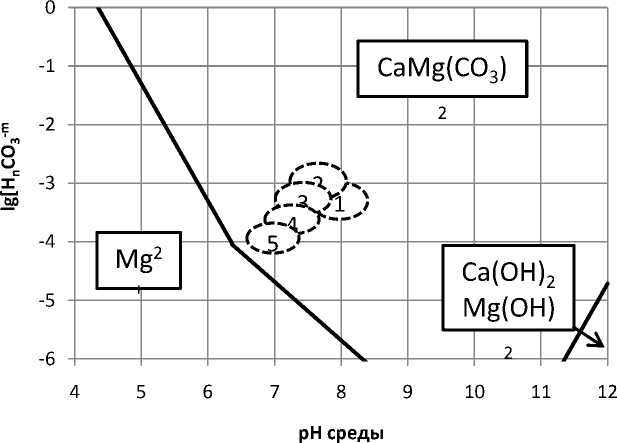
Рис. 4. Диаграмма термодинамической стабильности доломита в жидкой фазе основных технологических переделов: 1 – в операции самоизмельчения; 2 – в операции пенной сепарации; 3 – там же при использовании обработанной оборотной воды; 4 - там же при использовании тепловой обработки; 5 - там же при совместном использовании электрохимической и тепловой обработки
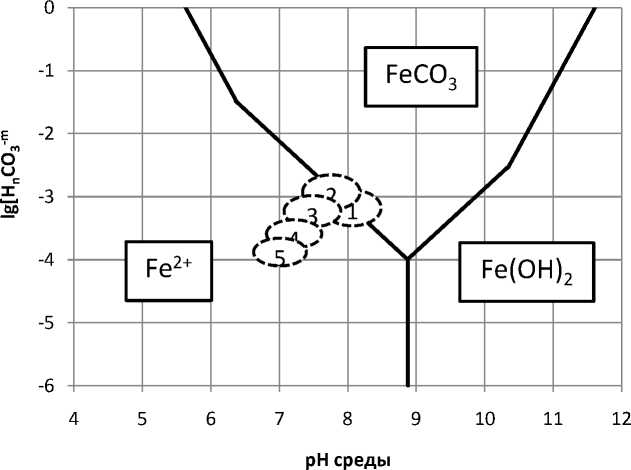
Рис. 5. Диаграмма термодинамической стабильности сидерита в жидкой фазе основных технологических переделов: 1 – в операции самоизмельчения; 2 – в операции пенной сепарации; 3 – там же при использовании обработанной оборотной воды; 4 - там же при использовании тепловой обработки
Важным этапом является выбор «модельного» минерала, условия образования – растворения которого отвечали бы аналогичным процессам с участием других минералов. Сопоставление полученных результатов показывает, что таким минералом может быть кальцит. Действительно, условия растворения кальцита будут одновременно условиями растворения гидроксидокарбонатов магния и карбоната железа. Условия образования-растворения доломита не выбраны к качестве граничных, поскольку доломит образуется при длительных процессах осадкообразования, когда возможна перестройка кристаллических решеток самостоятельных карбонатов кальция и магния.
Термодинамическая оценка устойчивости карбонатных соединений проводилась применительно к кальциту и заключалась в установлении соотношений между ионно-молекулярными компонентами жидкой фазы в условиях равновесия реакций образования – растворения с образованием ионов кальция, молекул и анионов угольной кислоты.
Расчетные значения констант диссоциации угольной кислоты Значения констант К д1, К д2 и L CaСO3 при проведении расчетов для различных температур были взяты из работы [3] и приведены на рис. 6 а, б.

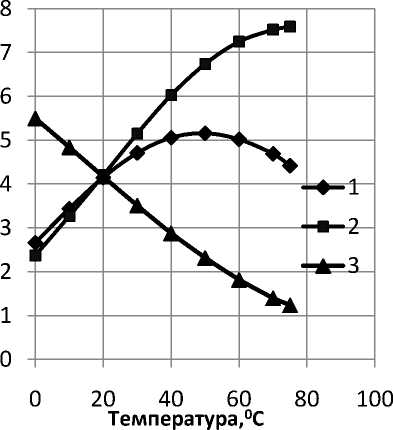
б га
Рис.6. Зависимости констант диссоциации угольной кислоты по первой (1) и второй ступени (2) и константы L CaСO3 (3) от температуры в обычных (а) и логарифмических (б) координатах
-6
-7
-8
-9
-12
зГ-11 ею ею
-10 х ею
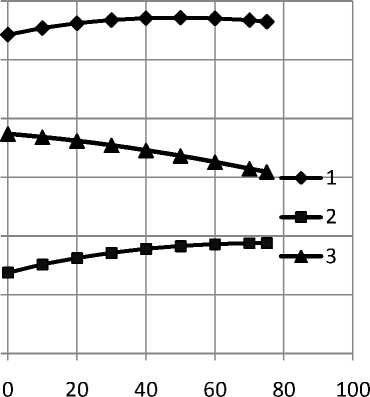
Температура, оС
Концентрация карбонатных ионов в равновесии с молекулярной формой угольной кислоты, описываемого уравнением реакции
Н 2 CO 3 = CO 3 2-+ 2H+ ,
может быть рассчитана по уравнению lg[CO3-] + 2lg[H+] - lg[Н2CO3] = lgКд1 +lgКд2,(3)
где lgКд1, lgКд2 - константы диссоциации угольной кислоты по 1-й 2-й ступени.
После преобразования получим:
lg[CO3-] = lgКд1+ lgКд2 +lg[Н2CO3] + 2pH.(4)
Для уравнения растворения кальцита по реакции
CaCO3 = Ca2++CO32-(5)
уравнение связи имеет следующий вид:
lg [CO3-] = lgLCaCO3- lg[Ca2+](6)
Приравнивая правые части расчетных уравнений 4 и 6 получим:
lgКд1 + lgКд2+ lg[Н2CO3] + 2pH = lgLCaCO3- lg[Ca2+].(7)
Исходя из этого соотношения можно получить уравнение:
lg[Н2CO3] + lg[Ca2+] + 2рН = lgLCaCO3- lgКд1- lgКд2.(8)
Данное уравнение определяет соотношение между ионномолекулярными компонентами жидкой фазы в условиях равновесия и позволяет рассчитать равновесную концентрацию одного из компонентов, например рН в граничных условиях устойчивости кальцита:
рН = ( lgL CaCO3 - lgК д1 - lgК д2 - lg[Н 2 CO 3 ] - lg[Ca2+])/2. (9)
Если концентрация рН будет больше расчетного (в более щелочной среде) – минерал устойчив. Если меньше – минерал будет растворяться.
Для стандартных условий с учетом фактических значений констант на рис.6 уравнение 9 примет вид:
рН = 4,17 – 0,5lg[Н 2 CO 3 ] – 0,5lg[Ca2+]. (10)
Для повышенной температуры (700С), с учетом данных на рис. 6, уравнение 9 примет вид:
рН = 3,8 – 0,5lg[Н 2 CO 3 ] – 0,5lg[Ca2+]. (11)
Проверка уравнений 10 и 11 проводилась в результате эксперимента, предусматривающего регулирование рН раствора с заданным ионным составом с использованием визуальной фиксации наличия взвеси осадка или отложений осадка на стенках реактора при изменении рН раствора с заданным исходным составом.
Были проведены две серии опытов. В первой серии (табл.3) моделировалась слабоконцентрированная оборотная вода, получаемая смешиванием оборотной и природной воды. Во второй серии опытов -высокоминерализованная техническая вода Мирнинского ГОКа. Концентрация молекулярной формы угольной кислоты приравнивалась предельной растворимости СО2 при заданной температуре (700С) и парциальном давлении в воздухе 3*10-4 ат, равной 4 мг/л (7*10-5 моль/л) [3].
Подстановка фактических концентраций в уравнения позволила рассчитать граничные рН осадкообразования (табл. 4). Сопоставление расчетных данных с фактическим рН осадкообразования показывает, что разработанная модель хорошо описывает экспериментальные данные.
Таблица 4.
Расчетные и экспериментальные рН осадкообразования карбоната кальция
Условия эксперимента |
[Ca2+], мг/л |
Т0С |
Предельное [Н 2 CO 3 ], мг/л |
рН осадкообразования |
|
Расчетное |
Экспериментальное |
||||
1. Слабоконцентрированный раствор |
430 |
25 |
30 |
6,83 |
7,1 |
70 |
4 |
7,27 |
7,5 |
||
2. Сильноконцентрированный раствор |
2150 |
25 |
30 |
6,48 |
6,7 |
70 |
4 |
6,92 |
7,2 |
Обнаруживаемое отклонение экспериментально измеренной величины рН осадкообразования от расчетного носит систематический характер и обусловлено необходимостью определенного пресыщения раствора взаимодействующими ионами для протекания процессов фазообразования [3].
С учетом этого факта необходимо учитывать, какой процесс моделируется: процесс осаждения или процесс растворения. Очевидно, что в случае расчета рН осадкообразования целесообразно вводить поправочный коэффициент (0,3 по рН), увеличив свободный член в уравнениях 10 и 11. Для обычной температуры (250С):
рН ос = 4,27 – 0,5lg[Н 2 CO 3 ] – 0,5lg[Ca2+], (12)
для повышенной температуры (700С), с учетом данных на рис. 6, уравнение 11 примет вид:
рН ос = 4,1 – 0,5lg[Н 2 CO 3 ] – 0,5lg[Ca2+]. (13)
В практическом плане уравнения 10 и 11 может быть реализованы и для расчета граничных условий протекания процесса электрохимической очистки алмазов от карбонатных пленок с целью восстановления их флотируемости. В случае применения подкисленных продуктов диафрагменной обработки оборотной воды достигается смещение рН в кислую область и обеспечивается повышение гидрофобности и эффективности флотации исходно гидрофильных алмазов.
Анализ результатов проведенных экспериментов показывает, что удаление пленок и карбоната кальция имеет место при рН близких к расчетным. Как и в предыдущем случае, имеет место отклонение экспериментально измеренной величины рН растворения осадка от расчетного, которое также носит систематический характер и обусловлено необходимостью поддержания пониженных относительно расчетных концентраций переходящих в раствор ионов для интенсивного протекания процессов растворения.
Таблица 5.
Расчетные и экспериментальные рН растворения карбоната кальция
Условия эксперимента |
[Ca2+], мг/л |
Т0С |
Предельное [Н 2 CO 3 ], мг/л |
рН растворения осадка |
|
Расчетное |
Экспериментальное |
||||
1. Слабоконцентрированный раствор |
430 |
25 |
30 |
6,83 |
6,4 |
70 |
4 |
7,27 |
6,8 |
||
2. Сильноконцентрированный раствор |
2150 |
25 |
30 |
6,48 |
6,0 |
70 |
4 |
6,92 |
6,5 |
Очевидно, что в случае расчета рН растворения осадка целесообразно вводить поправочный коэффициент (0,4 по рН), уменьшив свободный член в уравнениях 10 и 11. Для обычной температуры (250С):
рН = 3,77 – 0,5lg[Н 2 CO 3 ] – 0,5lg[Ca2+], (14)
и для повышенной температуры (700С):
рН = 3,9 – 0,5lg[Н 2 CO 3 ] – 0,5lg[Ca2+]. (15)
Проведенный анализ показал, что фактическое рН водной фазы в операциях рудоподготовки и обогащения алмазосодержащих кимберлитов (7,8 – 8,2) превышает рН осадкообразования (6,7 – 7,1)и лежит в области «карбонатизации», т.е. интенсивного образования осадков карбонатных и гидроксидокарбонатных минералов (рН. Что вполне соответствует результатам вышеизложенного термодинамического анализа.
Аналогичным образом, сравнение фактического рН жидкой фазы пульпы в операции термического кондиционирования питания пенной сепарации (6,8-7,2) соответствует граничному рН растворения – осаждения карбонатов кальция (6,9 – 7,3), что объясняет сохранение гидрофобности алмазов после операции термического кондиционирования. Применение электрохимически обработанной оборотной воды позволяет еще более сместить рН жидкой фазы в кислую область и достичь условий растворения карбонатных пленок с поверхности алмаза непосредственно в ходе технологического процесса пенной сепарации.
Таким образом, после произведенной корректировки уравнения 12, 13, 14, 15 могут быть использованы для оперативной оценки склонности к осадкообразованию жидкой фазы оборотных вод и жидкой фазы пульпы, а также при выборе условий растворения карбонатных пленок в процессах комбинированного теплового и электрохимического кондиционирования пульпы и оборотной воды при флотационном обогащении алмазосодержащего сырья.
пенная сепарация, алмазосодержащее сырье, карбонатные пленки, оборотная вода, термохимические расчеты, диаграммы устойчивости foam separation, diamond-bearing raw materials, carbonaceous film, recycled water, thermochemical calculations, the stability diagram
Список литературы Научное обоснование применения тепловой и электрохимической обработки для повышения эффективности пенной сепарации алмазосодержащих руд
- Куренков И.И. О свойствах поверхности алмаза в связи с извлечением из руд/Труды Института горного дела им. А.А. Скочинского. -М.: Изд. АН СССР, 1957. -т. IV. -С. 241-251.
- Чантурия В.А., Трофимова Э.А., Диков Ю.П., Двойченкова Г.П., Богачев В.И., Зуев А.А. Связь поверхностных и технологических свойств алмазов при обогащении кимберлитов//Горный журнал, 1998. -№ 11-12. -С. 52 -56.
- Гаррелс Ч., Крайст Г. Растворы, минералы, равновесия. -М.: Мир, 1967. -407 с.
- Наумов Г.Б., Руженко Б.Н., Ходаковский И.Л. Справочник термодинамических величин. -М.: Атомиздат, 1971. -240 с.
- Краткий справочник физико-химических величин. -Под редакцией Мищенко К.П. и Равделя А.А. -Л.: Химия, 1974. -200 с.
- Риббе П.Х. Карбонаты. Минералогия и химия: Пер. с англ. Под ред. Р.Дж. Ридера. -М.: Мир, 1987. -494 с.
- Морозов В.В., Лесовик М., Авдохин В.М. Развитие методов аналитического контроля ионного состава пульпы и оборотных вод при автоматическом регулировании замкнутых циклов обогащения полиметаллических руд//Горный информационно-аналитический бюллетень,1999. -№8. -С. 14-16.