Новая технология переработки кислых золошлаковых отходов ТЭЦ в силикатный кирпич
Автор: Гильмияров Данил Игоревич, Михайленко Андрей Андреевич, Овчаренко Геннадий Иванович
Рубрика: Строительные материалы и изделия
Статья в выпуске: 1 т.14, 2014 года.
Бесплатный доступ
Предложена новая технология переработки кислых золошлаковых отходов ТЭЦ с высоким содержанием ококсованного угля в качественное минеральное сырье. Технологическая схема включает дожигание предварительно гранулированных отходов в котлах кипящего слоя с получением дополнительного тепла, качественного минерального сырья и силикатного кирпича на его основе.
Зола, золошлаковые отходы, ококсованный уголь, грануляция, обработкав котлах кипящего слоя
Короткий адрес: https://sciup.org/147154367
IDR: 147154367
Текст научной статьи Новая технология переработки кислых золошлаковых отходов ТЭЦ в силикатный кирпич
Использование зол и золошлаковых отходов (ЗШО) ТЭЦ во многих странах мира превышает 40–60 % от их выхода. В России объем перерабатываемых золошлаковых материалов не превышает 10 %. Причины такого положения дел в России – многочисленны. Одна из главных заключается в широком распространении ТЭЦ малой и средней мощности с системой улавливания золы в скрубберах (мокрые циклоны), после которых можно отбирать из систем гидрозолоудаления (ГЗУ) либо золошлаковую пульпу с коэффициентом разбавления водой до 100, либо золошлаковую смесь из отвала с влажностью более 40 %.
Другая основная причина заключается в большом содержании недогоревшего угля (механический недожог или потери при прокаливании) в таких ЗШО, доля которого достигает 30 % от общей массы, в среднем составляя 15–20 %. Применение такого рода сырья проблематично из-за высокого содержания органики. Если рассматривать данную проблематику с экономической точки зрения, то ТЭЦ несут огромные издержки по удалению, хранению данного вида отходов, а также «экологическим» выплатам и т. п. Только на воду для ГЗУ средняя ТЭЦ затрачивает более 100 млн руб. в год. Оборотное водоснабжение у таких ТЭЦ, как правило, отсутствует. С учетом развивающихся рыночных отношений это крайне нецелесообразно и поэтому использование ЗШО ТЭЦ в России сегодня становится все более актуальной задачей.
Цель настоящей работы – предложить технологическую схему переработки золошлаковых отходов, обеспечивающую снижение издержек ТЭЦ и получение качественного минерального сырья для производства силикатного кирпича.
Оценку состава и свойств ЗШО осуществляли для отходов ТЭЦ Барнаула, Бийска, Рубцовска, сжигающих кузнецкий каменный уголь марки СС и в целом характеризующих сложившуюся ситуацию в Сибири. В золоотвале Барнаульской ТЭЦ-2 находятся отходы с потерями при прокаливании (ППП) от 3,8 до 26,9 % со среднегодовым количеством мехнедожога в 19,5 % по отчёту ТЭЦ-2 за 2009 г. (см. таблицу). Аналогичная картина наблюдается и
Химический состав использованных зол и золошлаков ТЭЦ-2
Наименование материала |
Потери при прокаливании (ППП) |
SiO 2 |
Al2O 3 |
Fe 2 O 3 |
CaO |
MgO |
SO 3 |
Сумма |
1.ЗШО ТЭЦ-2 проба 1 |
3,83 |
43,15 |
12,86 |
32,10 |
5,55 |
2,31 |
0,09 |
99,89 |
2. ЗШО ТЭЦ-2 проба 2 |
26,87 |
44,43 |
18,38 |
1,81 |
4,64 |
1,29 |
0,57 |
96,87 |
3. ЗШО ТЭЦ-2 проба 2 после прокаливания |
– |
54,38 |
26,28 |
6,87 |
5,16 |
1,36 |
0,57 |
95,16 |
4. ЗШО ТЭЦ-2 проба 3 |
25,12 |
46,28 |
18,97 |
1,18 |
2,94 |
0,73 |
0,41 |
95,63 |
5. ЗШО ТЭЦ-2 проба 3 после прокаливания |
– |
58,07 |
26,89 |
6,71 |
4,25 |
0,27 |
0,16 |
96,35 |
6. КУЗ ТЭЦ-2 |
8,32 |
56,10 |
21,16 |
6,06 |
4,38 |
0,90 |
0,98 |
97,90 |
7. Шлак ТЭЦ-2 |
0,30 |
62,12 |
23,21 |
9,28 |
3,53 |
1,06 |
0,30 |
99,80 |
Примечание. КУЗ – каменноугольная зола, отобранная после скруббера.
Гильмияров Д.И., Михайленко А.А., Овчаренко Г.И.
для ТЭЦ Бийска и Рубцовска. Количество шлаковой составляющей в этих отходах не превышает 5 % и это не влияет на содержание ППП в материале.
Оценка влияния мехнедожога на характеристики минерального сырья производилась по свойствам полученного силикатного кирпича. Зольная составляющая разбавлялась молотым шлаком ТЭЦ-2 для получения кислого компонента с разным содержанием ППП. Использование ЗШО с содержанием ококсованного угля уже в 5 % приводит к падению прочности в 2 раза в сравнении с сырьем без ППП, а при 25 % – в 10 раз (рис. 1).
Таким образом, было принято решение о дожигании ЗШО при температуре котла кипящего слоя в 800 °С до полного выгорания ококсованно-го угля, а также помола полученного минерального сырья после обжига.
Как видно из рис. 2, прокаливание и помол благоприятно влияют на прочностные характери- стики полученного материала. Также были проведены испытания на морозостойкость полученного материала. Из рис. 3 видно, что уже при 50 % затрат энергии на помол прочность составов повышается практически в 2 раза. При этом даже после 35 циклов морозостойкости не отмечается снижения прочности.
Для того, чтобы передел прокаливания не был затратным, нами рассмотрен вариант дожигания золошлаков ТЭЦ в котлах кипящего слоя с получением дополнительной тепловой энергии, которую можно вернуть на ТЭЦ, либо использовать в технологии получения строительных материалов.
Для устойчивой работы котла необходима калорийность отхода в пределах 1,5–1,8 ккал/кг (6,3– 7,5 кДж/кг) и формирование его в виде гранул до 5– 7 мм в диаметре. Часто в ЗШО содержание ППП достаточно для устойчивой работы котла. В случае низкого содержания мехнедожога в отходе, в схеме
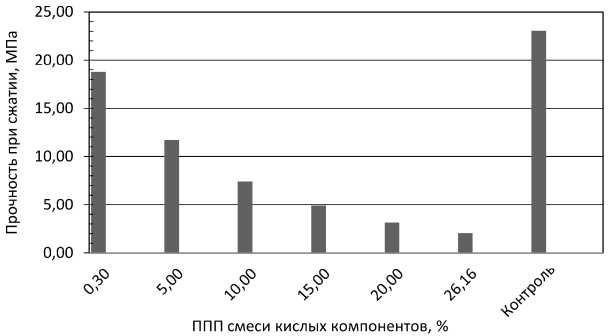
Рис. 1. Зависимость прочности при сжатии составов от ППП кислого компонента
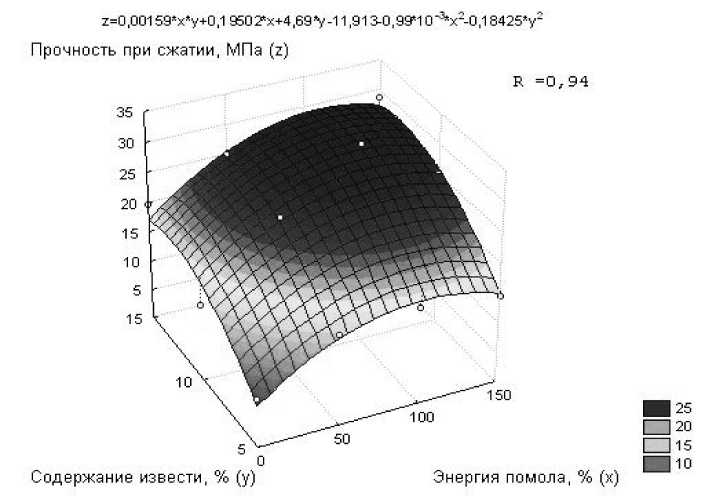
Рис. 2. Зависимость прочности составов из прокаленной пробы ЗШО с начальным содержанием ППП = 26,87 % от энергии помола сырья и содержания извести (за 100 % приняты затраты энергии на помол смеси клинкера и гипса до тонкости выпускаемого заводом цемента)
Строительные материалы и изделия
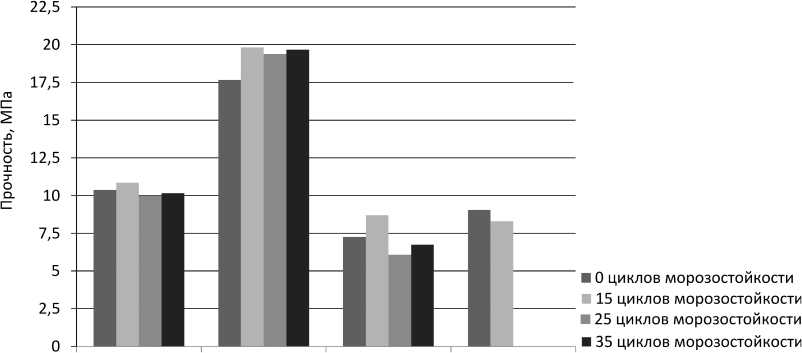
ЗШ0(1 ЗШО(50%ЭП, ЗШО (2 проба) ЗШО(50%ЭП, проба)+15И+5Г 1проба)+10И+5Г +10И+5Г 2проба)+10И+5Г
Рис. 3. Зависимость прочности составов с разными содержанием извести и энергией помола (ЭП) циклов морозостойкости
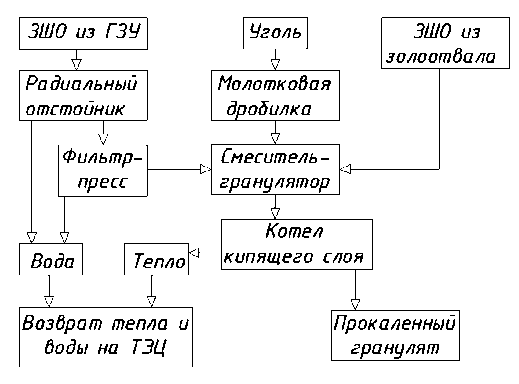
Рис. 4. Технологическая схема переработки кислых золошлаковых отходов ТЭЦ в качественное минеральное сырьё
предусматривается дополнительное введение молотого угля в пределах 10–15 %. Особенность работы котла кипящего слоя заключается в том, что в нем температура горения не превышает 800 °С и топливо выгорает до содержания не более 0,5 %.
Для работы кипящего слоя необходимо гранулировать ЗШО. Сами по себе отходы плохо поддаются грануляции из-за отсутствия связующего компонента, и во время прокаливания гранулы будут разрушаться. Нами исследовался ряд связок для грануляции ЗШО. Лучшие результаты были получены с применением извести. Рекомендуемое количество составляет порядка 9 %. При этом такое же количество извести необходимо для получения силикатного кирпича с хорошими физикомеханическими характеристиками. Также для грануляции возможно применение глины и жидкого стекла [1]. Полученный прокаленный гранулят имеет приятный бежевый цвет. Таким образом, была предложена технологическая схема (рис. 4).
Выводы
-
1. Предложена технологическая схема по переработке золошлаковых отходов ТЭЦ из ГЗУ и золоотвалов с их обезвоживанием и дожиганием мехнедожега в котлах кипящего слоя, а также их эффективным дальнейшим использованием в качестве сырья для производства стройматериалов.
-
2. Переработка кислых зол и золошлаков на силикатный кирпич требует обязательного их дожигания и помола. Это позволяет получить стеновой материал с высокими строительно-техническими характеристиками.
Список литературы Новая технология переработки кислых золошлаковых отходов ТЭЦ в силикатный кирпич
- Фок, Н.А. Исследование различных видов связок на процесс грануляции золошлаков/Н.А. Фок, Д.И. Гильмияров, А.А. Михайленко//Ползуновский вестник. -2012. -№ 1/2. -С. 109-113.