Новые полирующие и шлифующие материалы для литейного производства на основе наноструктурированного минерального сырья Красноярского края
Автор: Степанова Т.Н., Мамина Л.И., Баранов В.Н., Безруких А.И., Костин И.В.
Журнал: Журнал Сибирского федерального университета. Серия: Техника и технологии @technologies-sfu
Статья в выпуске: 7 т.5, 2012 года.
Бесплатный доступ
Показана возможность применения в составах чистящих, шлифующих и полирующих композиций природных материалов Красноярского края (оксида кремния, оксида магния и оксида алюминия) в исходном и активированном состояниях.
Оксид кремния, оксид магния и оксид алюминия, механоактивация, чистящие композиции, шлифующие и полирующие композиции
Короткий адрес: https://sciup.org/146114711
IDR: 146114711
Текст научной статьи Новые полирующие и шлифующие материалы для литейного производства на основе наноструктурированного минерального сырья Красноярского края
Готовые отливки, выполненные литьем, имеют шероховатую поверхность, поэтому для окончательной доводки их поверхность шлифуют и полируют. Полирующие материалы оказывают на обрабатываемую поверхность помимо механического еще и химическое воздействие. Входящие в состав паст специальные добавки, реагируя с материалом, ускоряют их обработку. В шлифующих и полирующих порошках и пастах широко применяют в качестве абразивного материала оксид хрома, природный корунд, электрокорунд, имеющие высокую твердость (7-10 по шкале Мооса).
В данной работе были продолжены исследования по использованию в составах шлифующих и полирующих композиций природных материалов Красноярского края в исходном и активированном состояниях [1, 2]. Исследуемые материалы на основе оксида алюминия, оксида магния, оксида кремния имеют твердость по шкале Мооса 9; 5,5 и 7 соответственно. Геометрические параметры исходных материалов приведены на рис. 1.
Из представленных данных видно, что максимальный размер частиц и, следовательно, минимальная внешняя удельная поверхность у оксида алюминия, а оксид магния обладает максимальной дисперсностью.
Для наноструктурирования и активации частиц материалов их обрабатывали в планетарноцентробежной мельнице АГО-2 в течение 20-60 мин. В материалах изменяются параметры кристаллической решетки входящих минералов, повышая в итоге реакционную способность
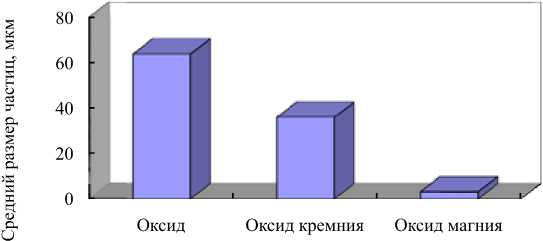
алюминия
Нап о лнитель
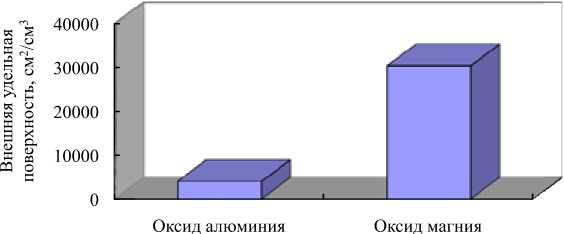
Наполнитель
б
Рис. 1. Геометрические параметры наполнителей: а – средний размер частиц; б – внешняя удельная поверхность дисперсных порошков. Увеличение размера частиц и снижение удельной поверхности после обработки связано с накоплением энергии в массе материала и агрегацией частиц. При длительной обработке происходит релаксация «закаченной» энергии в результате диспергации материала. Исследования структуры материалов показали, что в ходе обработки существенно изменяется форма частиц: в исходном состоянии материалы имеют осколочные частицы, в обработанном – сферическую форму.
В работе исследовали коэффициент трения наполнителей в масле. Результаты исследований приведены на рис. 2, 3 и в табл. 1, 2. Из представленных данных видно, что с увеличением времени активации коэффициент трения снижается для всех исследуемых материалов.
Из выпускаемых материалов этого класса наибольшее распространение на сегодняшний день получила паста ГОИ. К основным недостаткам этой пасты можно отнести ее высокую токсичность и стоимость. Поэтому ведутся поиски материалов для разработки новых составов, не содержащих хрома. В качестве наполнителей были опробованы наноструктурированные оксиды алюминия, магния и кремния, содержащие различные доли нанофракции и степень аморфизации.
Типы и качество наполнителей, используемых в составах, содержащих важную антифрикционную композицию, даны в табл. 3.
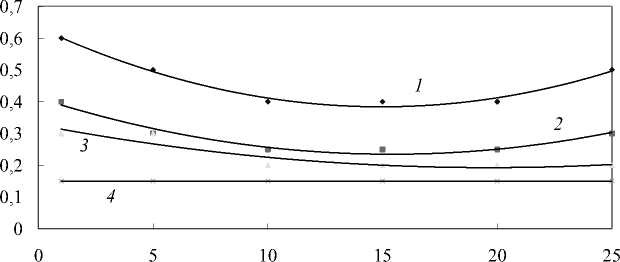
Время испытаний, мин
Рис. 2. Коэффициент трения (оксид кремния + масло). Время активации, мин: 1 – 0; 2 – 20; 3 – 40; 4 – 60
0,4
0,35
0,3
0,25
0,2
0,15
0,1
0,05
1 2 |
' ■ т |
3=4 |
Время испытаний, мин
Рис. 3. Коэффициент трения (оксид алюминия + масло). Время активации, мин: 1 – 0; 2 – 20; 3 – 40; 4 – 60
Таблица 1. Зависимость коэффициента трения от времени активации оксида кремния
Время активации оксида кремния, мин/коэффициент трения
0 |
К тр |
20 |
К тр |
40 |
К тр |
60 |
К тр |
1 |
0,6 |
1 |
0,4 |
1 |
0,3 |
1 |
0,15 |
5 |
0,5 |
5 |
0,3 |
5 |
0,3 |
5 |
0,15 |
10 |
0,4 |
10 |
0,25 |
10 |
0,2 |
10 |
0,15 |
15 |
0,4 |
15 |
0,25 |
15 |
0,2 |
15 |
0,15 |
20 |
0,4 |
20 |
0,25 |
20 |
0,2 |
20 |
0,15 |
25 |
0,5 |
25 |
0,3 |
25 |
0,2 |
25 |
0,15 |
Таблица 2. Зависимость коэффициента трения от времени активации оксида алюминия
Время активации оксида алюминия, мин
0 |
К тр |
20 |
К тр |
40 |
К тр |
60 |
К тр |
1 |
0,37 |
1 |
0,27 |
1 |
0,2135 |
1 |
0,219 |
5 |
0,37 |
5 |
0,276 |
5 |
0,2135 |
5 |
0,215 |
10 |
0,37 |
10 |
0,27 |
10 |
0,215 |
10 |
0,215 |
15 |
0,37 |
15 |
0,27 |
15 |
0,215 |
15 |
0,215 |
Таблица 3. Наполнители для наноструктурированных абразивных составов
Номер состава |
Наполнитель |
Время активации, мин |
1 |
Оксид алюминия |
0 |
2 |
20 |
|
3 |
40 |
|
4 |
60 |
|
5 |
Оксид кремния |
0 |
6 |
20 |
|
7 |
40 |
|
8 |
60 |
|
9 |
Оксид магния |
0 |
10 |
20 |
|
11 |
40 |
|
12 |
60 |
Составы опробованы в качестве чистящих, шлифующих, полирующих.
Качество очищаемой поверхности после процесса очистки оценивали по пятибалльной шкале: 1 – очень неудовлетворительное, 2 – неудовлетворительное, 3 – среднее, 4 – хорошее, 5 – отличное.
Результаты экспериментов приведены в табл. 4.
Из представленных данных видно, что для очистки поверхностей лучше использовать пасту на основе исходных материалов. Уменьшение среднего размера частиц наполнителя не приводит к улучшению процесса очистки. Из исследуемых материалов наилучшим образом сработал оксид кремния. Оксид магния, обладающий наименьшим размером частиц, не способен обеспечить поверхности необходимое качество очистки. В то же время у оксида алюминия частицы имеют достаточно большой размер частиц, что и приводит к появлению на поверхности большого количества рисок, царапин, что нежелательно.
Для оценки эффективности использования предложенных составов в качестве шлифовальных и полировальных паст была разработана шкала, представленная в табл. 5.
Качество отшлифованной и отполированной поверхности показано в табл. 6.
Таблица 4. Степень очистки поверхности разработанными пастами
Номер состава (см. таблицу 3) |
Наполнитель |
Время активации, мин |
Качество очищаемой поверхности |
1 |
Оксид алюминия |
0 |
4 |
2 |
20 |
3 |
|
3 |
40 |
3 |
|
4 |
60 |
3 |
|
5 |
Оксид кремния |
0 |
5 |
6 |
20 |
4 |
|
7 |
40 |
3 |
|
8 |
60 |
3 |
|
9 |
Оксид магния |
0 |
3 |
10 |
20 — |
2 |
|
11 |
40 |
— 2 |
|
12 |
60 |
Таблица 5. Шкала для оценки качества шлифуемой и полируемой поверхности
Балл |
Критерий оценки |
Условное изображение |
1 |
Темный цвет, ярко выраженные риски |
|
2 |
Темный цвет, риски явно не выражены |
|
3 |
Светлый цвет, риски явно не выражены |
|
4 |
Светлый цвет, рисок нет |
|
5 |
Идеально блестящая поверхность, рисок нет |
Так, в шлифовальных составах наилучшим образом зарекомендовали наполнители, активированные в течение 20 мин, а для полировальных – в течение 40 мин. Увеличение времени активации нецелесообразно из-за начинающейся агрегации и твердофазного спекания частиц.
По полученным данным для разработанных составов можно сделать рекомендации, приведенные в табл. 7.
Лабораторные испытания показали эффективность замены пасты ГОИ на разработанные составы чистящих, шлифующих и полирующих материалов на основе природных материалов Красноярского края.
Таблица 6. Качество отшлифованной и отполированной поверхностей
Номер состава |
Наполнитель |
Время активации, мин |
Качество поверхности |
|
шлифуемой |
полируемой |
|||
1 |
Оксид алюминия |
0 |
4 |
3 |
2 |
20 |
5 |
4 |
|
3 |
40 |
3 |
5 |
|
4 |
60 |
3 |
3 |
|
5 |
Оксид кремния |
0 |
3 |
2 |
6 |
20 |
4 |
3 |
|
7 |
40 |
2 |
4 |
|
8 |
60 |
2 |
4 |
|
9 |
Оксид магния |
0 |
2 |
1 |
10 |
20 |
4 |
2 |
|
11 |
40 |
2 |
4 |
|
12 |
60 |
2 |
3 |
Таблица 7. Рекомендации по использованию предложенных составов
Время активации наполнителя, мин |
Область использования |
0 |
Чистящие |
20 |
Шлифующие |
40 |
Полирующие |