Новые способы производства многослойных минераловатных изделий
Автор: Коваль Григорий Иванович, Каримова Татьяна Григорьевна
Рубрика: Строительные материалы и изделия
Статья в выпуске: 1 т.13, 2013 года.
Бесплатный доступ
В статье дано описание запатентованных новых способов производства многослойных минераловатных изделий, в том числе с комбинированной структурой.
Многослойные минераловатные изделия, способы производства
Короткий адрес: https://sciup.org/147154333
IDR: 147154333
Текст научной статьи Новые способы производства многослойных минераловатных изделий
К качественным характеристикам минераловатных изделий в зависимости от их марки относятся сжимаемость, прочность на сжатие при 10 % деформации, растяжение и отрыв слоев, сдвиг/срез.
Одним из эффективных способов повышения указанных характеристик минераловатных изделий, наряду с увеличением длины волокон, уменьшением их диаметра, количества и качества связующего, условиями его распределения и полимеризации [1], приданием разной ориентации волокон, является выполнение их из нескольких слоев [2, 3]. Слои могут иметь разную плотность и структуру, между слоями могут укладываться армирующие материалы в виде металлических и синтетических сеток, тканей и т. п., на наружные поверхности могут накладываться упрочняющие и изоляционные слои [3, 4].
Для получения многослойных минераловатных изделий в технической и патентной литературе, а также в различных рекламных материалах предложено несколько характерных технических решений, включающих резку ковра на слои, гофрирование одного из слоев, уплотнение других слоев, последующее наложение их друг на друга и полимеризацию [2, 5].
С целью уточнения и конкретизации технологических режимов получения многослойных ми- нераловатных изделий, совершенствования технологических приемов и дальнейшего развития технологии их производства предложен ряд новых способов производства многослойных минераловатных изделий, в том числе с комбинированной структурой.
Для получения двухслойных минераловатных плит с заданными показателями плотности слоев ρ 1 и ρ 3 (рис. 1) при непрерывном режиме производства с постоянной скорость V перемещения первичного ковра и готовой двуслойной минераловатной плиты предложены новые технологические режимы [6].
Для выполнения этих режимов осуществляется предварительная резка тросиком или пилой 2 первичного ковра толщиной h с плотностью ρ, полученного в камере 1, на слои толщиной h 1 и h 2 . Плотность отрезаемого нижнего слоя первичного ковра ρ 1 равна плотности первичного ковра ρ. Толщина нижнего слоя первичного ковра h1 равна толщине нижнего слоя готовой плиты. Толщину верхнего слоя h2 первичного ковра определяют соотношением h 2 =h 3 ·ρ 3 /ρ 1 , обеспечивающим равенство скоростей нижнего слоя толщиной h1, а также верхнего слоя до h 2 и после h 3 уплотнения его до плотности ρ3 дополнительными формирующими роликами 3. Толщина первичного ковра определяется из условия h=h1+ h3·ρ3/ρ1.
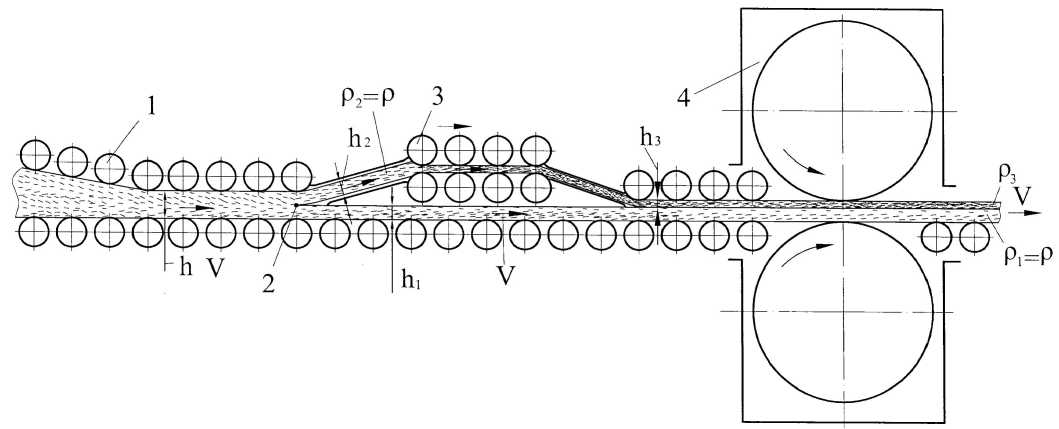
Рис. 1. Технологическая схема производства полиплотностных минераловатных изделий
После выхода из формирующих роликов 3 верхний слой ковра укладывается на нижний и их совместно перемещают для тепловой обработки в камере 4, на выходе из которой получается двухслойная минераловатная плита с заданными характеристиками.
С применением приведенных технологических режимов могут быть получены плиты с большим числом слоев, например, трехслойные плиты. Первые два слоя плиты получают аналогично двухслойному варианту, а третий слой, располагаемый, например, ниже нижнего слоя плиты, получают при технологических режимах, аналогичных получению верхнего слою плиты.
Для конкретизации технологических режимов производства многослойных минераловатных изделий с комбинированной структурой [2, 5], обеспечения технологичности их изготовления путем устранения разницы длин слоев в ковре, повышения их качества за счет обеспечения надежной связки слоев разработан способ [7], при котором перед продольной резкой ковра на слои известными средствами [2] осуществляют его гофрирование путем периодического встречного вмятия с образованием перемычек между гофрами.
На рис. 2–4 показана технология получения указанных изделий. Минераловатный ковер 1
с расположением волокон вдоль ковра со связующим (см. рис. 2) из камеры волокноосаждения (на рисунке не показано) передается на транспортер 2 и поступает к паре гофрировочных валков 3, где осуществляется гофрирование ковра 1 с получением на нем встречных вмятин с перемычками между гофрами. Далее гофрированный ковер поступает к двухстороннему ленточному транспортеру 5, скорость перемещения ленты которого меньше скорости подачи гофрированного ковра 4 от гоф-рировочных валков 3. За счет этого на гофрированный ковер 4 действует продольное осевое усилие Т, благодаря чему гофры соединяются, образуя комбинированный минераловатный ковер 6. Далее ковер устройством для продольной резки 7 режется на два слоя 8 и 9.
Направляющими роликами 10, 11 (см. рис. 3) слои 8, 9 поворачиваются вокруг своей продольной оси на угол 180 град. За счет этого точки А и Б слоев оказываются в положениях А 1 и Б 1 . На рис. 3 направляющие ролики 10, 11 показаны условно смещенными вдоль оси слоев. Одновременно слои ковра 8 и 9 меняют направление перемещения на угол 180>α>0 град. по отношению к направлению перемещения первичного ковра 1.
В дальнейшем, проходя через двухсторонний транспортер 12 (рис. 4) слои 8, 9 накладываются
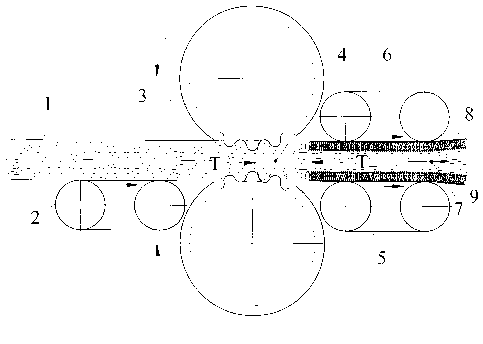
Рис. 2. Схема двухстороннего гофрирования минераловатного ковра
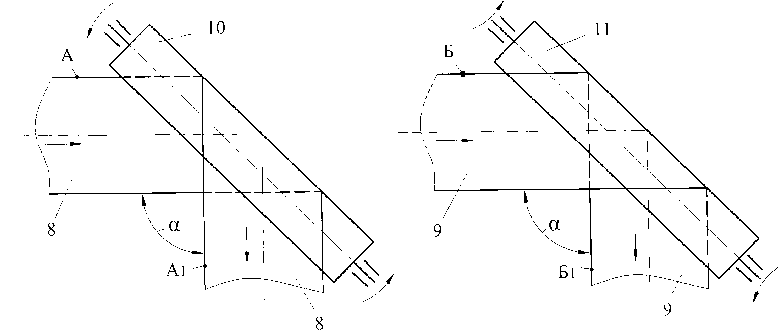
Рис. 3. Схема поворота слоев ковра вокруг их продольной оси на 180 град. c изменением направления их перемещения
друг на друга, соединяются и передаются в камеру тепловой обработки 14 и готовая многослойная минераловатная с комбинированной структурой выдается из нее транспортером 15.
Недостатком технологии получения многослойных минераловатных изделий при применении резки первичного ковра на слои являются требование точной настройки положения режущего инструмента для получения слоев требуемой толщины, необходимость применения сложной и громоздкой технологии передачи полос неограниченной длины из положения нахождения в одной плоскости в положение укладки в стопу.
Существенно упрощает технологию получения многослойных минераловатных изделий применение способа [8], при котором минераловатный ковер 1 (см. рис. 5) шириной В со связующим из камеры волокноосаждения передается на перемещающийся транспортер и поступает к механизму продольной резки 2, с помощью которого из мине- раловатного ковра получаются, например, три полосы 3, 4, 5 шириной b. Далее полосы поступают на дальнейшую обработку, где, например, осуществляется изменение их толщины и плотности (на рисунке не показано). Затем с помощью направляющих роликов 6, 7, 8 полосы 3, 4, 5 поворачивают вокруг их продольной оси на угол 180 град. с одновременным изменением направления перемещения на угол 180>α>0 град. Благодаря этому обеспечивается установка полос 3', 4', 5' друг над другом. Далее полосы 3', 4', 5' синхронно перемещают, укладывают друг на друга и подают в камеру тепловой обработки, на агрегаты продольной и поперечной резки для получения минераловатных изделий в виде полос и плит (на рисунке не показано).
Предложен также другой технологический вариант [9] решения задачи получения многослойных минераловатных изделий с применением резки первичного ковра на более узкие полосы и их укладки друг на друга после соответствующего
8'
Рис. 4. Процесс получения двухслойных минераловатных изделий с комбинированной структурой при двухстороннем гофрировании слоев
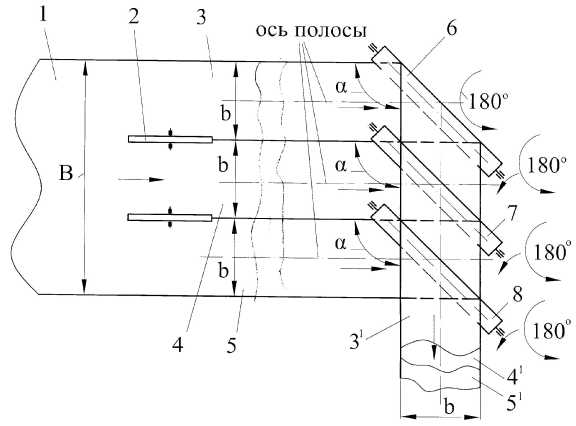
Рис. 5. Схема получения трехслойного минераловатного изделия с изменением направления перемещения и поворотом слоев на 180 град.
изменения их толщины и плотности. Отличительной особенностью этого способа является то, что перед укладкой друг на друга (n-1) полосу дважды поворачивают вокруг их продольных осей на угол 180 град., при этом после каждого поворота направления перемещения указанных полос в плоскости ковра изменяют на угол 180>α> 0 град., где n – число слоев. На рис. 6 показан процесс получения трехслойного ковра. Минераловатный ковер 1 шириной В со связующим из камеры волокно-осаждения передается на перемещающийся транспортер (на рисунке не показано) и поступает к механизму продольной резки 2, с помощью которого из минераловатного ковра получаются три полосы 3, 4, 5 шириной b. Далее полосы поступают на дальнейшую обработку, где, например, осуществляется изменение их толщины и плотности. Затем с помощью направляющих роликов 6, 8 полосы 3 и 5 поворачивают вокруг их продольной оси на угол 180 град. с одновременным изменением направления перемещения полосы 3 на угол α1=135 град., а полосы 5 на угол α2=90 град. Полоса 4 при этом перемещается без изменения направления пере- мещения. При дальнейшем перемещении полосы 3 и 5 еще раз поворачивают вокруг их продольной оси на угол 180 град. и изменяют направления перемещения полосы 3 на угол α1=135 град., а полосы 5 на угол α2=90 град. Благодаря этому обеспечивается установка полос 3 и 5 над полосой 4. Далее полосы 3', 4', 5' синхронно перемещают, укладывают друг на друга и подают в камеру тепловой обработки, на агрегаты продольной и поперечной резки для получения минераловатных изделий в виде полос и плит (на рисунке не показано).
Описанные технологии обеспечивают компоновку многослойного ковра с минимальным количеством технологических операций в одной компактной непрерывной технологической линии.
На дальнейшее совершенствование и устранение недостатков известных технологий получения многослойных минераловатных изделий с комбинированной структурой направлено применение технического решения [10], согласно которому минераловатный ковер 1 (рис. 7) с расположением волокон вдоль ковра со связующим из камеры волокноосаждения передается на транс-
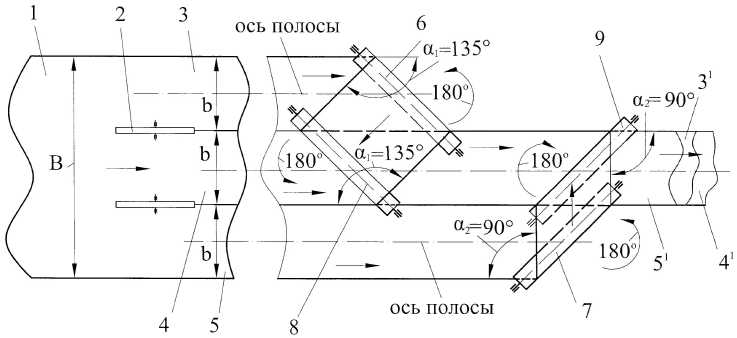
Рис. 6. Схема получения трехслойного минераловатного изделия при продольном перемещении слоев
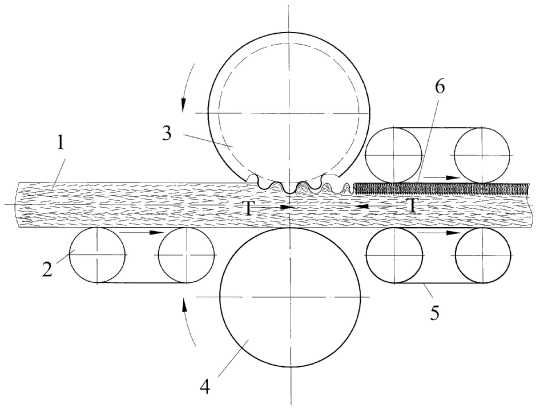
Рис. 7. Схема одностороннего гофрирования минераловатного ковра
портер 2. Затем он поступает к паре гофрировоч-ных валков 3, 4, один из которых 4 имеет гладкую поверхность, а другой 3 имеет поверхность с эвольвентными зубьями, расположенными под прямым или острым углом к направлению перемещения минераловатного ковра. Гофрировоч-ный валок 3 осуществляет гофрирование ковра 1 с получением на нем вмятин и выпуклостей в виде зубчатой рейки (рис. 8) с прямым или косым зубом. Гофрированный с одной стороны минераловатный ковер 1 поступает к двухстороннему ленточному транспортеру 5, скорость перемещения ленты которого меньше скорости подачи гофрированного ковра от гофрировочных валков 3, 4. За счет этого на гофрированный ковер действует продольное осевое усилие Т. Благодаря чему гофры соединяются, образуя комбинированный минераловатный ковер 6. Далее ковер 6, имеющий ширину В, механизмом продольной резки 7 режется на две равные части 8, 9, каждая из которых имеет ширину b. Направляющими роликами 10, 11 части ковра соответственно 9 и 8 поворачивают вокруг продольных осей соответствующих частей ковра на угол 180 град. с одновременным изменением направления перемещения части ковра 9 на угол 180>α> 0 град., а части ковра 8 – на угол угол 360>γ> 180 град. Затем часть ковра 8 с помощью направляющего ролика 12 дополнительно поворачивают вокруг ее продольной оси на угол 180 град. с изменением направления перемещения на угол (γ+α) град. в обратную по отношению к первоначальному повороту части ковра 8 сторону на угол γ. В рассматриваемом варианте технологии угол α = 60 град., угол γ =90 град.
Благодаря таким технологическим операциям части ковра 8, 9 переворачиваются и оказываются в положении, при котором гофрированные поверхности накладываются друг на друга. При этом часть ковра 8 направляют под часть ковра 9.
При осуществлении гофрирования ковра под острым углом, например, β = 60 град. к направлению его перемещения (рис. 8) после укладки друг на друга частей ковра 8, гофры одной части ковра располагаются по отношению к гофрам другой части ковра под углом 180 град –2β = 60 град. Учитывая, что в результате гофрирования под углом β=60 град. и компоновки гофр, волокна частей ковра ориентируются под углом 90–β = 30 град. в разные стороны к плоскости ковра, создавая «арочную, сотовую» структуру.
В дальнейшем, проходя через двухсторонний транспортер 13 (см. рис. 4) части ковра 8, 9 соединяются и передаются в камеру тепловой обработки 14. После камеры тепловой обработки 14 получается многослойная минераловатная полоса с комбинированной структурой, обладающая высокими механическими свойствами ни изгиб, сжатие и растяжение в разных направлениях. В средней части полосы находятся волокна с вертикально слоистой структурой, а по периферии – волокна с горизонтально-слоистой структурой. Линия раздела частей ковра расположена в середине его высоты. Такое положение линии разъема обеспечивает высокую прочность соединения, так как при изгибе готовой минераловатной полосы и плиты место соединения располагается в нейтральном сечении, где отсутствуют напряжения растяжения и сжатия. Это исключает расслоение минераловатной полосы и плиты.
Таким образом, на основе анализа информации о применяемых на практике технологиях производства минераловатных изделий, а также известных предложений по перспективным техническим решениям в данной области техники и технологии разработан комплекс новых способов, которые могут быть эффективно использованы в практике минераловатного производства.
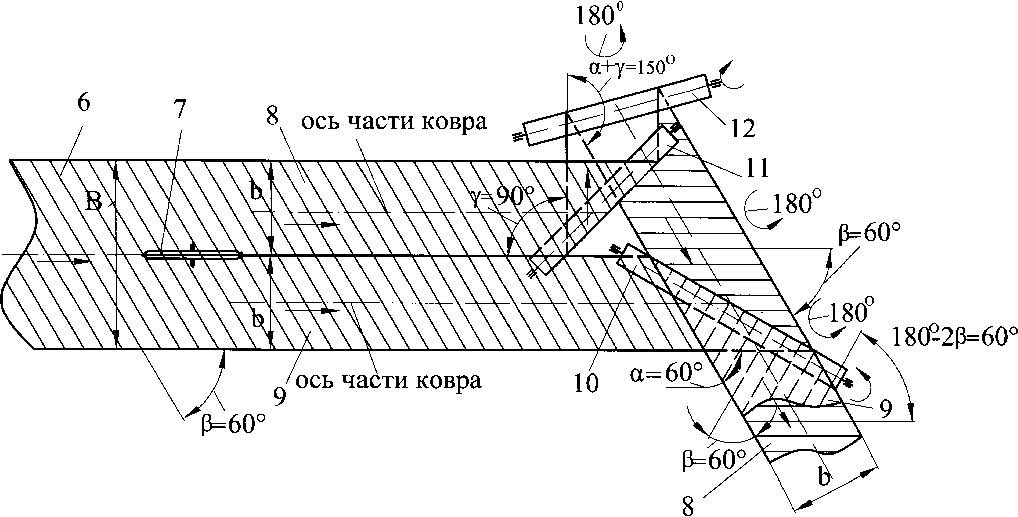
Рис. 8. Процесс укладки слоев, гофрированных под острым углом к направлению их перемещения
Список литературы Новые способы производства многослойных минераловатных изделий
- Горлов, Ю.Л. Технология теплоизоляционных и акустических материалов и изделий: учебник для вузов по спец. «Производство строительных изделий и конструкций»/Ю.Л. Горлов. -М.: Высш. шк., 1989. -384 с.
- Тобольский, Г.Ф. Минераловатные утеплители и их применение в условиях сурового климата/Г.Ф. Тобольский, Ю.Л. Бобров. -Л.: Стройиздат, Ленинградское отделение, 1981. -176 с.
- Сухарев, М.Ф. Производство теплоизоляционных материалов/М.Ф. Сухарев, И.Л. Майзель, В. Г. Сандлер. -М.: Высшая школа, 1981. -231 с.
- Бобров, Ю.Л. Долговечность теплоизоляционных минераловатных материалов/Ю.Л. Бобров -М.: Стройиздат, 1987. -168 с.
- Пат. 2152489 Российская Федерация, МПК7 Е04В1/78, В65В27/12, Д04Н1/70, Е04С2/16, В32В1/08, В28В1/52. Способ изготовления отвержденного нетканного полотна из минерального волокна и устройство для его осуществления/Л.Й. Нергор, К. Брандт, И. Кринланд. -№ 96117383/03; заявл. 27.01.1995; опубл. 10.07.2000. -40 с.
- Пат. 2362672 Российская Федерация, МПК7 Е04В1/74, В28В1/52, Способ производства минераловатных плит/Г.И. Коваль, В.Г. Дремин, Т.Г. Каримова. -№ 2008101235/03; заявл. 09.01.2008; опубл. 27.07.2009. -6 с.
- Пат. 23512457 Российская Федерация, МПК7 Е04В1/74, В28В1/52, Способ производства минераловатных изделий/Г.И. Коваль, Т.Г. Каримова. -№ 2008100834/03; заявл. 09.01.2008; опубл. 20.04.2009. -7с.
- Пат. 2364503 Российская Федерация, МПК7 Е04В1/74, В28В1/52, Способ производства многослойных минераловатных изделий/Г.И. Коваль, Т.Г. Каримова. -№ 2008104273/03; заявл. 04.02.2008; опубл. 20.08.2009. -5 с.
- Пат. 2356729 Российская Федерация, МПК7 Е04В1/74, В28В1/52, Способ производства многослойных минераловатных изделий/Г.И. Коваль, Т.Г. Каримова. -№ 2008104270/03; заявл. 04.02.2008; опубл. 27.04.2009. -5 с.
- Пат. 2353513 Российская Федерация, МПК7 Е04В1/74, В28В1/52, Способ производства минераловатных изделий с комбинированной структурой/Г.И. Коваль, Т.Г. Каримова. -№ 2008104269/03; заявл. 04.02.2008; опубл. 27.05.2009. -8 с.