О задаче Стефана и расчетах затвердевания отливок
Автор: Васенин Валерий Иванович
Журнал: Известия Самарского научного центра Российской академии наук @izvestiya-ssc
Рубрика: Современные технологии в промышленности, строительстве и на транспорте
Статья в выпуске: 4-5 т.14, 2012 года.
Бесплатный доступ
Проанализированы формулы И. Стефана и других авторов для расчета затвердевания отливок.
Отливка, форма, затвердевание, тепловой баланс
Короткий адрес: https://sciup.org/148201360
IDR: 148201360
Текст научной статьи О задаче Стефана и расчетах затвердевания отливок
Для затвердевшей части отливки, т. е. для т > 0 и 0 < x < ^
д θ д 2θ
—2 = a 2— 2- д τ дx 2
.
Здесь a 1 и a 2 – коэффициенты температуропроводности жидкого и твердого метала, м2/с.
Граничные условия:
-
а) для x = 0 и т > 0 9 1 (0, т ) = 9 п ;
-
б) для x = да и т > 0 9 1 ( да , т ) = 9 ж ;
-
в) на фронте затвердевания для x = £ и т > 0 0 i& т ) = 6 2& т ) = 9 кр .
Займемся потоками тепла на фронте затвердевания, где x = ξ. В объеме металла толщиной d^ есть три потока тепла (в Вт/м2): q 1 -поток тепла от жидкого металла к фронту затвердевания; q 2 – поток тепла от фронта затвердевания к поверхности охлаждения; q L – поток тепла, выделяющегося (или поглощающегося) при затвердевании (расплавлении) слоя толщиной d^. Знаки q 1, q 2 и q L зависят от величины перегрева жидкого металла и интенсивности теплоотвода на поверхности охлаждения. Предположим, что идет затвердевание металла. Тепло передается от более нагретых участков тела к менее нагретым, поэтому потоки тепла q 1 и q 2 противоположны направлениям градиентов температур (и положительному направлению оси x ) и запишутся так:
д θ 1 д θ 2
q 1 = - Л 1 q 2 = - Л 2
дx дx
,,
(3), (4)
где X 1 и Х 2 - коэффициенты теплопроводности жидкого и твердого металла, Вт/м - град. Раз мы условились, что идет затвердевание, то этот процесс происходит с выделением тепла и q L имеет знак «+»:
dξ qL = + L р2 , dτ
,
где L – удельная теплота кристаллизации, Дж/кг; р 2 - плотность твердого металла, кг/м3. Температуру объема металла толщиной d ξ можно считать постоянной и равной температуре кристаллизации 0 кр . Поэтому сумма источников и стоков тепла равна 0:
6 1 — 6 ж - ( 6 ж
09 =0 +(0
2 п кр
-
e кр )
1 - erf ( x /2 T a j ) 1 - erf ( x /2 Ja )
- 6 п )
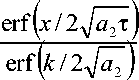
q i + q 2 + Q l = 0- (6)
Подставив значения входящих в (6) величин и сделав преобразования, получим:
где erf – функция ошибок Гаусса; k – коэффициент затвердевания, м/с1/2. Дифференцируя (10) и (11) по x , имеем:
д θ д θ d ξ
X, — 2 + X. — 1 = L р . —
2 дx 1 дx 2 d τ
.
д 6 1 _ (e ж - 6 ) exp (- x21 4 a i ) dx [ 1 - erf ( x / 2 .Ja )]V ai пт
Общепринятой является запись в таком виде (так называемое условие Стефана):
дθ2 дθ1
X< X/]
дx дx dτ .(
Хотя непонятно, как получено это выражение. Если из потока тепла q 2 вычесть q 1 и приравнять q L , то получится
-
дθ дθ
-
- X, — 2 + X. — 1 — L р , —
дx дx dτ ,( а не соотношение (8). По-видимому, значения q1 и q2 были взяты со знаком «+», из q1 вычли q2 и приравняли qL. Все дело в этом знаке «+» перед вторым членом выражения (7), а не «–», как у И. Стефана, Ф. Ноймана и других. Дальнейший ход решения известен. Наиболее подробно, без пропусков простых преобразований он изложен в книге [2]. Достаточно хорошо рассмотрена тема в книгах [11-13]. Правда, во всех этих четырех книгах используется зависимость (8), а не (7). Посмотрим, к чему приведет неверная запись тепловых потоков на фронте затвердевания. После ряда преобразований имеем такие соотношения для текущих температур жидкой и твердой фаз:
д 6 2 = ( 6 кр - 6 п ) exP (- x 7 4 a 2 ) dx erf ( x / 27 0"а пт
Толщина затвердевшей корочки изменяется во времени так:
^ — x 4т а производная dξ k dτ 2 τ
Коэффициент аккумуляции тепла жидкого металла

твердого металла b2
— 2 /

Подставляя (12), (13), (15) в (7) и учитывая (16) и (17), окончательно имеем:
b2 (6 кр - 6 п ) _ b1(6 ж - 6 кр )________ УЛ exp (x2/ 4a2 )erf (kj 2^2) exp (x2/ 4a, )[1 - erf (x/ 277)] 2 2
В статьях и книгах [2-13] итоговая зависимость отличается от (18) знаком «+» перед вторым членом этого выражения. Назовем формулу этих книг и статей как (18St). Знак «+» меняется на «–» в (7), а «–» на «+» в (8) из-за того, что правая часть выражения (12) имеет знак «–» и после подстановки в (7) или (8) происходит смена знака перед вторым членом уравнений (18) и (18St). Выясним, к чему приведет замена знака с
«–» на «+» в формуле (18St) по сравнению с (18). Для этого проведем расчеты затвердевания по выражениям (18) и (18St). На примере чугунной отливки – неограниченной плиты толщиной 2 X = 30 - 10-3 м. Значения коэффициентов возьмем из книги [14]: Х 1 =18,6 Вт/м - град; Х 2 =36,2 Вт/м - град; c 1 838 Дж/кг - град; c 2 =753 Дж/кг - град; р 1 =6950 кг/м3; р 2=7200 кг/м3; L =215 000 Дж/кг; 0 ж =1280 ° С; 0 кр =1180 ° С; a i =31,9 - 10-7 м2/с;
a 2 =66,7-10^ м2/с; b 1 =10400, b 2 =14000, Ь ф =1380 Вт - с1/2/м2 - град. Нужно задаться температурой поверхности металла. Для граничных условий 1го рода рассчитаем ее по следующему соотношению [11]:
θ
п
= 6
кр
Ь 2 Ь ф
1 + b 2 / Ь ф
Получаем 0 п =1074 ° C, или Т п =1094 ° С. Хотя формы, конечно, нет. Просто поддерживается на поверхности отливки такая температура,
соответствующая затвердеванию отливки в песчаной форме, но при отсутствии формы. 0 п нельзя принимать равной 0 кр : будет мал отвод тепла от отливки. Результаты расчетов приведены в таблице. Величину коэффициента затвердевания изменяли от 0,500 - 10-3 до 5,000 - 10-3 м/с1 / 2. Обозначения в табл. 1 такие: A , B и C – это первый, второй и третий члены выражений (18) и (18St), A + В – суммирование по (18St), A – B – вычитание по (18). A , B , A + B , A – B и C измеряются в Вт - с1/2/м2 и должны быть умножены на 10 6 .
Таблица 1. Влияние коэффициента затвердевания на отвод тепла от отливки
k •IO3, м/с1 / 2 |
A |
B |
A + B |
A - B |
C |
0,500 |
12,754 |
1,211 |
13,965 |
11,543 |
0,662 |
0,800 |
7,893 |
1,317 |
9,210 |
6,576 |
1,059 |
1,000 |
6,250 |
1,390 |
7,640 |
4,860 |
1,324 |
1,301 * |
4,727 |
3,006 |
7,733 |
1,721 |
1,722 |
1,500 |
4,043 |
1,579 |
5,622 |
2,464 |
1,986 |
1,605 |
3,747 |
1,619 |
5,366 |
2,128 |
2,125 |
2,000 |
2,900 |
1,775 |
4,675 |
1,125 |
2,647 |
2,084 ** |
2,759 |
2,759 |
|||
2,500 |
2,190 |
1,939 |
4,129 |
0,251 |
3,310 |
2,950 |
1,742 |
2,167 |
3,909 |
–0,425 |
3,906 |
3,000 |
1,694 |
2,182 |
3,876 |
–0,488 |
3,972 |
4,000 |
1,059 |
2,619 |
3,678 |
–1,560 |
5,300 |
5,000 |
0,663 |
3,071 |
3,734 |
–2,408 |
6,620 |
5,260 * |
0,584 |
6,378 |
6,962 |
–5,793 |
6,964 |
Примечание: * - перегрев чугуна θ ж – θ кр = 200ºC; ** - перегрев чугуна θ ж – θ к р = 0ºС
Начнем с решения уравнений (18) и (18St). В книгах [2, 3, 11-13] утверждается, что выражение (18St) очень сложно и его нужно решать графически. На самом деле (18) и (18St) решаются элементарно, нужно задаться несколько раз (5-7 раз) значением k , вычислить значения A + B и A – B и добиться, чтобы отличие этой суммы или разности от C не превышало заданной величины.
Теперь об обещанном доказательстве ошибочности выражения (18St). При нулевом перегреве, то есть при равенстве 0 вторых членов уравнений (18) и (18St) коэффициент затвердевания равен 2,084 - 10-3 м/с1 / 2 по обеим формулам (см. табл. 1). При перегреве 100 и 200 ° C этот коэффициент получается равным 1,605 - 10-3 и 1,301 - 10-3 по зависимости (18), 2,950 - 10-3 и 5,260 - 10-3 м/с1 / 2 - по (18St). То есть с увеличением перегрева коэффициент затвердевания (и скорость затвердевания) по соотношению (18St) растет (?!), а не уменьшается, как это должно быть и как получается по (18).
Как видно, уравнения (18) и (18St) имеют решения . Замена «+» на «–», т. е. переход от (18St) к (18) ведет к важному результату:
значительно уменьшается расхождение между теоретическими и экспериментальными значениями коэффициента затвердевания. В данном примере теоретическое значение k при переходе от (18St) к (18) уменьшилось с 2,950-10-3 до 1,605-10-3 при экспериментальном его значении * 0,8-10-3 м/с1/2 [15]. Разница между теоретическим и экспериментальным значениями k стала равной 2, а не 3,7. Хотя время затвердевания будет больше теоретического в соответствии с (14) в 22 = 4 раза по (18) и в 3,72=13,7 раза по (18St). Разница в 4 раза (для данного конкретного случая затвердевания чугуна в песчаной форме при ГУ1), конечно, существенная, но все же это не 13,7 раза, как получается при расчете по (18St). Хотя и была принята температура поверхности отливки, какой она была бы при затвердевании чугунной отливки в песчаной форме при идеальном контакте, и, следовательно, завышенном теплоотводе по сравнению с реальными условиями литья. При ГУ1 термическое сопротивление отводу тепла от стенки отливки равно нулю, а поверхность отливки мгновенно принимает температуру окружающей среды, то есть 0п. Лимитирующим звеном в процессе охлаждения является внутренний теплообмен – отвод тепла твердым металлом. Это внутренняя задача. На практике ГУ1 осуществляют при очень высокой интенсивности внешнего теплообмена, например, при закалке изделий в жидкостях, температура кипения которых ниже температуры нагрева изделий под закалку. При этом температура поверхности остается постоянной и равной температуре кипения жидкости [16]. Например, при закалке данной чугунной отливки при 0п = 80°С рассчитанный по (18) коэффициент затвердевания составляет 4,572-10-3 м/с1/2. При ГУ1 нет проблем с отводом тепла с поверхности отливки: все тепло «убирается» каким-то образом. Но при литье теплоотвод с поверхности отливки ограничивается не подводом тепла из центра отливки к ее поверхности, а от поверхности отливки внутрь формы. Это задача внешняя, теплоотвод определяется отводом тепла формой, а у песчаной формы коэффициент аккумуляции тепла на порядок ниже коэффициента аккумуляции тепла отливки. Теплоотвод от отливки гораздо ниже, чем при ГУ1, когда мы задались 0п из расчета температуры идеального контакта отливки и песчаной формы. Расхождения между теоретическими и экспериментальными значениями k объясняются не тем, что 0п меняется во времени (этим можно пренебречь за время затвердевания отливки), или изменением свойств металла и формы. bф определяется при заливке в заданную форму по времени затвердевания при минимальном перегреве. Изменение свойств металла невелико, по крайней мере, никак не объясняет 4-кратное замедление времени затвердевания по сравнению с теоретическим. Дело в изменении задачи с внутренней на внешнюю из-за резкого замедления отвода тепла с поверхности отливки.
Как же выйти из этого положения? Нам нужно сохранить 0 п = 0 по = 0 пф , где 0 по и 0 пф -температура поверхности отливки и температура поверхности формы. Иначе невозможно получить решение в замкнутом виде, т. е. в виде интегралов от элементарных и специальных функций. И в то же время задать равенство тепловых потоков из отливки и в форму:
д θ 2 д θ ф
— ^7 --- = -Кд --- дx дx
.
То есть используются одновременно ГУ1 и ГУ4. Конечно, в случае идеального контакта отливки и формы равенство (20) выполняется. И в работах С. Шварца [17, 18] было получено выражение, учитывающее литейную форму, отличающееся от (18St) только первым членом и появлением знака «–» между первым и вторым членами.
Обозначим формулу С. Шварца как (18S) и приведем только часть ее:
b2θкр exp (k2/ 4a2 )[b2/ Ьф + erfk 2 ja)] (18S)
Сначала займемся знаком «–». На самом деле должен быть «+» из-за того, что после подстановки (12) в (8) два «минуса» дадут «плюс». Расчет по (18S) при прежних условиях дает £=0,342-10-3 м/с1/2, что в 2,34 раза ниже экспериментального значения k, а время затвердевания, следовательно, будет в 2,342 = 5,48 раза больше опытного. Таким образом, формула (18) дает значения k, в 2 раза большие, (18S) – в 2,34 раза меньшие экспериментальных. А по (18St), как уже говорилось, расчетные значения k в 3,7 раза больше опытных. Однако положение еще хуже, чем оно может показаться из сказанного. Дело в том, что при наличии формы резко замедляется отвод тепла от твердой корочки металла, а формулы (7) и (20) не отражают этого, а (18S) учитывает это не полностью. По (7) и (20) для твер-дθ дой корочки поток тела q2 = -к2 —2, но ведь дx форма отводит тепла гораздо меньше. Известно, что величина потока тепла в форму при постоянной температуре на ее поверхности определяется так [11, 19]:
Ч ф =
—
b ф θ

Мы можем убрать форму, но считать, что тепло от твердой корочки уходит в форму в виде потока q ф . Понятно, что выражение (20) верно, но в (7) стоит q 2 – сколько может отвести тепла твердая корочка. А ведь форма «возьмет» тепла значительно меньше. Нужно ориентироваться на q ф . Теплоотвод лимитируется формой, а не твердой корочкой металла. Поэтому (6) следует записать в таком виде:
qi + Яф + Ql = 0
, а (7) будет выглядеть так:
д θ2 b ф θ п d ξ
К^ 1 L р9
дx πτ dτ
Однако уравнение (23) может быть решено только численными методами и должно стать предметом отдельного исследования. А пока сказать что-нибудь об этом решении невозможно.
Из зависимости (18) можно сделать следующее важное заключение. Приравняем второй член этого уравнения нулю, а теплоту перегрева
добавим к теплоте кристаллизации в правой части:
. b2(еV9,п) „=р2k[L+c (е. -екр)]
exp (к 2/ 4 a ) erf ( к / 2 .^а ) 2
При перегреве в 100 ° С к будет равен 1,605 - 10-3 и 1,790 - 10-3 м/с1 / 2 соответственно по (18) и (24), а перегрев в 200 ° С дает 1,301 - 10-3 и 1,602 - 10-3 м/с1/2. То есть включение теплоты перегрева в теплоту кристаллизации приводит к увеличению коэффициента затвердевания на 11,5 и 23,1% по сравнению с его учетом во втором члене уравнения (18). А время затвердевания отливки будет соответственно в 1,24 и 1,52 раза меньше – весьма значительные величины. Надо сказать, что, что уравнение Стефана получено для полубес-конечного тела. И использование этой зависимости для тел конечных размеров дает завышенную величину времени затвердевания отливки.
Рассмотрев работы И. Стефана и С. Шварца по затвердеванию, сделаем обзор существующему положению дел. Все последующие работы сводятся к двум формулам для определения времени затвердевания отливки. Первая из них записывается так:
т затв
П ХX [ c l Р 1 ( е ж - е кр )+ L р 2 | 2Ь ф е п
По второй подсчитывается текущая температура отливки [20], задаваясь которой находят время достижения отливкой этой температуры:
е = е [ 1 - erf ( toVT ) ] exp ( го2т )
, где начальная температура отливки
е н = е кр +
с (еж - е„)+l
1 ж кр
c 2
,
а коэффициент
го =
b ф
с ρ X
В (27) теплота кристаллизации суммируется с теплотой перегрева, переводится в температуру и прибавляется к температуре кристаллизации. Как уже говорилось, судя по (18) и (24), простое сложение теплоты перегрева и теплоты кристаллизации приводит к завышению коэффициента затвердевания, что, конечно, скажется
и на (25). По-видимому, это относится и к (26). Включение теплоты перегрева в теплоту кристаллизации первым произвел С. Сайто в 1921 г. [21]. Затем формула (25) с незначительными отличиями приводится в статье Н. Хворинова [22] и используется во многих статьях и книгах, в т. ч. во всех книгах А.И. Вейника и Г.Ф. Баландина. Не занимаясь обсуждением этих отличий, отметим только, что в знаменателе (25) должна быть 0 п , а не 0 кр . Анализ зависимостей (25) и (26) проведен в статье [23].
Расчет времени затвердевания отливки по (25) и (26) дает близкие результаты. Так, т затв по (25) для чугунной отливки с 2X = 30 - 10-3 м равно 317 с, по (26) – 296 с. И какая из этих формул точнее, может рассудить только эксперимент. Но зависимость (26), в отличие от (25), не требует постоянства коэффициента затвердевания и пропорциональности толщины намерзшей корочки корню квадратному из времени (не используется «закон квадратного корня»), не нужно принимать 0 п = const. Температура контакта отливки с формой непрерывно меняется. И, что очень важно, выражение (26), в отличие от (25), может быть использовано для расчетов охлаждения отливки в форме до заданной температуры – температуры выбивки. Причем в литературе нет формул, по которым можно было бы рассчитать охлаждение отливки до нужной температуры, так как имеющиеся зависимости неудовлетворительны по своему математическому обоснованию. По (26) время охлаждения чугунной отливки с 2 X = 30 - 10-3 м до 500 ° С составляет 9660 с, по экспериментальным данным оно равно 9000 с.
Учитывая, что формула (25) за 91 год не претерпела существенных изменений, на первый план выходит зависимость (26), которая к тому же дает расчет времени охлаждения отливки до заданной температуры. Выражение (26) получается путем строгого решения дифференциального уравнения теплопроводности Фурье для формы. По-видимому, дальнейшие усилия исследователей должны быть направлены на определение граничных условий на фронте затвердевания и на поверхности контакта отливки с формой, анализе и усовершенствовании формулы (18) и получению решений по типу (26).
Список литературы О задаче Стефана и расчетах затвердевания отливок
- Lame, G. Memoire sur la solidification par refroidissement d’un globe liquide/G. Lame, B.P. Clapeyron//Annales de Chimie et de Physique. 1831. Vol. 47. P. 250-256.
- Гребер, Г. Основы учения о теплообмене/Г. Гребер, С. Эрк, У. Григулль. -М.: Изд-во иностранной литературы, 1958. 568 с.
- Раддл, Р.У. Затвердевание отливок. -М.: Машгиз, 1960. 392 с.
- Stefan, J. Űber einige Probleme der Theorie der Wärmeleitung//Sitzungsberichte der kaiserliche Akademie der Wissenschaften in Wien. Mathematisch-naturwissenschaftliche Klasse. 1889. Bd. XCVIII. Abth. IIa. S. 473-484.
- Stefan, J. Űber die Theorie der Eisbildung, insbesondere űber die Eisbildung in Polarmeere//Sitzungsberichte der kaiserliche Akademie der Wissenschaften in Wien. Mathematisch-naturwissenschaftliche Klasse. 1889. Bd. XCVIII. Abth. IIa. S. 965-983.
- Рубинштейн, Л.И. Проблема Стефана. -Рига: Звайзгне, 1967. 458 с.
- Авдонин, Н.А. Математическое описание процессов кристаллизации. -Рига: Зинатне, 1980. 180 с.
- Мейрманов, А.М. Задача Стефана. -Новосибирск: Наука (Сибирское отделение), 1986. 240 с.
- Шахов, Е.М. О задаче Стефана//История физико-математических наук. Том 34. -М.: Изд-во АН СССР, 1960. С. 512-526.
- Данилюк, И.И. О задаче Стефана//Успехи математических наук. 1985. Т. 40. № 5. С. 133-185.
- Лыков, А.В. Теория теплопроводности. -М.: Высшая школа, 1967. 600 с.
- Тихонов, А.Н. Уравнения математической физики/А.Н. Тихонов, А.А. Самарский. -М.: Изд-во МГУ; Изд-во «Наука», 2004. 798 с.
- Мастрюков, Б.С. Теплофизика металлургических процессов/Б.С. Мастрюков, Г.С. Сборщиков. -М.: Металлургия, 1993. 320 с.
- Баландин, Г.Ф. Теория формирования отливки. -М.: МГТУ им. Н.Э. Баумана, 1998. 360 с.
- Гуляев, Б.Б. Теория литейных процессов. -Л.: Машиностроение, 1976. 216 с.
- Теплотехника металлургического производства. Том I. Теоретические основы. -М.: МИСИС, 2002. 608 с.
- Schwarz, C. Die rechnerische Behandlung der Abkűhlungs-und Erstarrungsvorgänge bei flűssigem Metall//Archiv fűr das Eisenhűttenwesen. 1931. Bd. 5. Hf. 3. S. 139-148; Hf. 4. S. 177-191.
- Schwarz, C. Zur rechnerischen Behandlung der Erstarrungsvorgänge beim Giessen von Metallen//Zeitschrift fűr angewandte Mathematik und Mechanik. 1933. Bd. 13. Hf. 3. S. 202-223.
- Анастасиади, Г.П. Автомодельность температурного поля песчаной формы//Тепловые процессы в отливках и формах/Г.П. Анастасиади, В.М. Голод. -М.: Наука, 1972. С. 82-90.
- Корнилов, А.А. Теоретические основы остывания отливок в неметаллической форме/А.А. Корнилов, В.Д. Репкин, В.Д. Орешкин, Г.В. Куртуков//Затвердевание и охлаждение отливок. -Новосибирск: Изд-во СО АН СССР, 1961. С. 5-20.
- Saito, S.//Science Reports of the Tohoku Imperial University. 1921. Vol. 10. P. 305-311.
- Chworinoff, N. Theorie der Erstarrung von Gubstűcken//Die Giesserei. 1940. Bd. 27. Hf. 10. S. 177-186; Hf. 11. S. 201-208; Hf. 12. S. 222-225.
- Васенин, В.И. Расчет затвердевания и охлаждения отливки в песчаной форме//Вестник ПГТУ. Машиностроение, материаловедение. 2007. № 3. С. 34-45.