Об одном методе снижения износа сколом пар трения, работающих при низких климатических температурах
Автор: Лебедев М.П., Семенов Я.С., Портнягин С.П., Савинова А.В.
Журнал: Известия Самарского научного центра Российской академии наук @izvestiya-ssc
Рубрика: Машиностроение
Статья в выпуске: 1-2 т.12, 2010 года.
Бесплатный доступ
Покрытия, нанесенные стандартной технологией восстановления деталей, основанные на газоплазменном напылении, обычно подвержены износу сколом по двум основным причинам: из-за низкого качества обработки поверхности подложки; из-за высокой хрупкости наносимого покрытия. Особенно это проявляется при низких температурах. Нами предложена технология, устраняющая вышеназванные недостатки. Лазерное оплавление повышает сцепление покрытия с подложкой, снижая значение чистоты обработки подложки и, вместе с тем, легируя переходный слой смешиванием, и устраняет износ по первой причине. Используемые порошковые материалы Ni- Сr-В-Si, Fe-С-Сr-V, нержавеющая сталь Х18Н9Т содержат Ni, Cr, V, которые понижают критическую температуру вязкохрупкого перехода и должны снижать хрупкий износ сколом по второй причине. Полученные результаты показывают, что примененная технология нанесения покрытия и исследованные порошковые материалы вызывают снижение износа при испытаниях на трение по схеме «диск по диску» с проскальзыванием и нагружением при температуре окружающего воздуха (−15Со). При этом не наблюдается откол от подложки и хрупкий износ сколом.
Пары трения, износ сколом, пониженные температуры, порошковые материалы, технология лазерного оплавления
Короткий адрес: https://sciup.org/148198956
IDR: 148198956
Текст научной статьи Об одном методе снижения износа сколом пар трения, работающих при низких климатических температурах
Большинство материалов в различных узлах машин и механизмов работают при трении в экстремальных условиях. В парах трения, как правило, возникают высокие контактные напряжения и их концентрации, большие скорости нагружения, значительные пластические деформации и, как следствие, износ сопряженных поверхностей. При этом механические, физические, химические и другие проявления трения определяют в основном работоспособность, ресурс, экономичность, безопасность и эксплутационные характеристики машин, механизмов и горнодобывающих агрегатов. Роль вышеназванных проявлений трения существенно возрастает, если силовые воздействия имеют вид циклического или ударного нагружения, а температура эксплуатации понижается. Именно в таких условиях работает подавляющее большинство строительной, горнодобывающей и
Лебедев Михаил Петрович, доктор технических наук, заместитель директора
Портнягин Сергей Павлович, доцент
Савинова Анастасия Васильевна, студентка другой техники, особенно в условиях Крайнего Севера, где период низких климатических температур составляет значительное время и возникает так называемый «пусковой период» - период времени от старта пар трения при низких температурах до температуры рабочего состояния. Изнашивание в этих условиях характеризуется сколом, как разновидностью хрупкого изнашивания, что связано с повышенной хрупкостью материала при понижении температуры. Поэтому в работе [1] рекомендовано использовать в качестве легирующих элементов для материалов на основе железа элементы с заполненными np-, nd-и nf-электронными оболочками или элементами с большой длиной химической связи.
Цель работы – разработать технологию снижения изнашивания сколом в «пусковой период» при низких температурах.
Методика исследований. При плазменном напылении металлов из-за неполного проплавления их частиц смешивание легирующих элементов с подложкой и в покрытии происходит неравномерно . При получении износостойких материалов легированных элементами с большой длиной химической связи или с заполненными np- nd- nf-электронными оболочками для работы в «пусковой период» можно использовать лазерную технологию [2]. Основные методы и технологии при нанесении легирующих элементов на основу – это плазменное напыление порошков с легирующими элементами и последующим их лазерной обработкой (ЛО).
Методика получения износостойких материалов. Для получения образцов плазменных покрытий и последующей лазерной обработкой были выбраны порошок системы Ni-Сr-В-Si (ПГСР-4), (используется для восстановлений деталей техники), а также порошки системы Fe-С-Сr-V ( ХВС ), системы Ni-Аl и порошок нержавеющей стали Х18Н9Т. Известно [3-5], что Ni , Cr , V понижают критическую температуру вязкохрупкого перехода (хладноломкости) материала, поэтому применение порошков содержащих эти металлы представляется целесообразным. В качестве подложки использовали образцы из стали 3сп - в виде прямоугольной пластины размером 50х35х10 мм, разделенной предварительно на 6 частей пропилами для того, чтобы не повредить покрытия при последующей механической обработке. Исходные порошки обладали дисперсностью 60…100 мкм.
Лазерную обработку проводили СО 2 -лазером ЛОК-ЗМ, генерирующим в непрерывном режиме на воздухе излучение с длиной волны λ=10,6 мкм. Потери по мощности лазерного луча от каждой отражающей поверхности составляют 17%. Мощность лазерного излучения измеряли непосредственно на выходе лазерной установки. Оплавление поверхности осуществлялось движением лазерного луча по винтовой линии с постоянным шагом, обеспечивающим непрерывность обработки поверхности. Мощность лазерного излучения составляла 1,0 ^ 1,9 кВт. По методике, описанной в работе [ 6 ] , была проведена оценка влияния удельной энергии лазерного излучения W на глубину оплавления плазменных покрытий для разных материалов.
При небольших значениях удельной энергии (<15 Дж/мм2) оплавления основы не происходит, а проплавляется только покрытие; на поверхности которого наблюдаются поры. Увеличение удельной энергии приводит к расплавлению металла подложки, происходит процесс легирования ее поверхности, изменяется химический состав и, соответственно, свойства формирующегося слоя. Глубина проплавления подложки зависит от материала покрытия и его толщины.
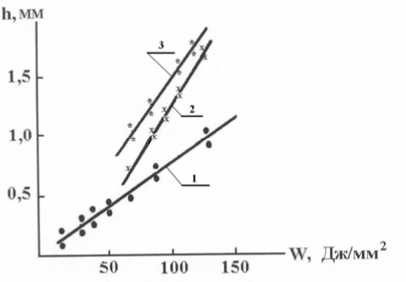
Рис. 1. Влияние удельной энергии лазерного излучения на глубину оплавления (h = 0,3-0,4 мм). 1 – ПГСР-4; 2 – ХВС; 3 – Х18Н9Т
При ЛО напыленного слоя и части металлической подложки происходит их смешивание с последующим легированием. При этом коэффициент перемешивания включает параметры обработки – мощность излучения и скорость перемещения луча, отражающие объем или площадь расплава, а также толщину расплавленного слоя. Толщина предварительно наносимых слоев легирующих элементов составляла 0,2 ^ 0,7 мм. Коэффициент K перемешивания определялся на поперечных шлифах по результатам 3-7 измерений в различных частях при зафиксированной начальной толщине слоя легирующих элементов. Зависимость коэффициента перемешивания от удельной энергии достаточно хорошо описывается линейной зависимостью [ 7 ] . Коэффициента перемешивания вычисляли по формуле K=0,05+5,67W [8] (рис. 2.).
W = P т =
F
4 P V ч, 3.14 dn
где F =π d2 n /4, τ = d n / V, P – мощность лазерного излучения; d n – диаметр лазерного луча; V – скорость перемещения лазерного луча; τ – время перемещения луча лазера на расстояние, равное диаметру луча.
Анализ зависимости глубины оплавления обработанных поверхностей от удельной энергии излучения показал (рис. 1), что для всех исследованных материалов с ростом удельной энергии глубина оплавления увеличивается.
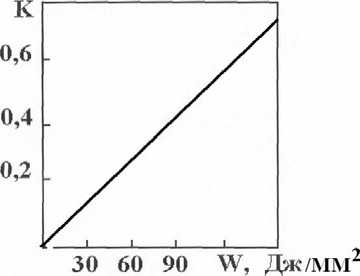
Рис. 2. Влияние удельной энергии лазерного излучения на коэффициент перемешивания (ПГСР-4)
Анализ методами стереометрической металлографии показал, что при увеличении удельной энергии лазерного излучения коэффициент перемешивания возрастает. Кроме того, при изменении коэффициента перемешивания содержание упрочняющих фаз для исследованных составов меняется в пределах от 20 до 35% (рис. 3.). Упрочняющие фазы имеют различную морфологию и могут иметь как округлую, так и овальную формы, в некоторых случаях они образуют сплошную сетчатую
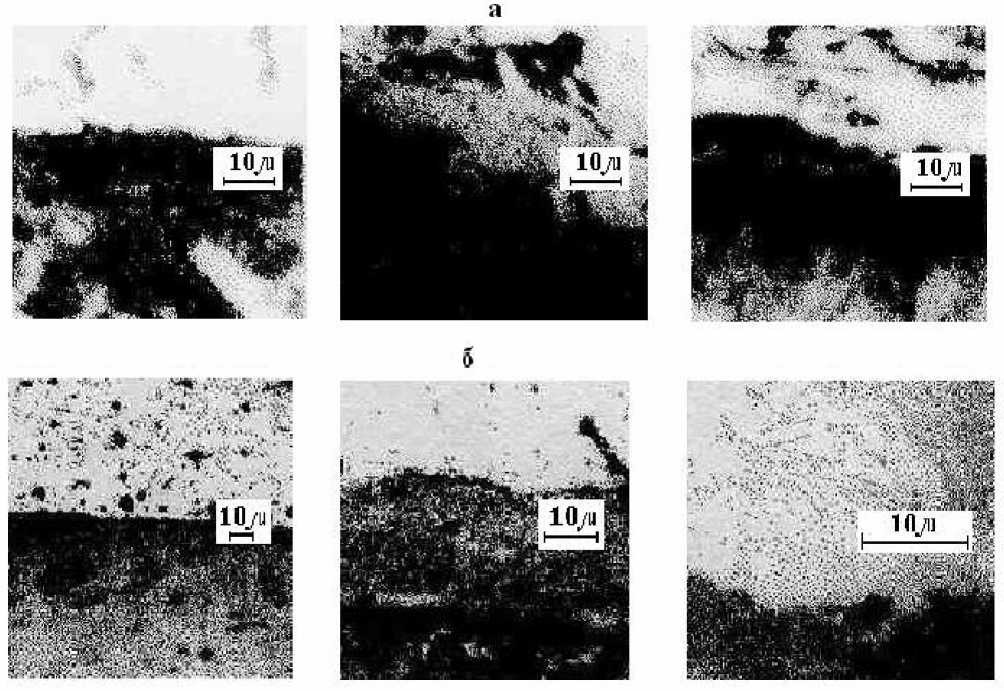
Рис. 3. Микроструктура материала в зоне оплавления:
а – напыленного слоя разной толщины (а – 0,2 мм; 0,5 мм; 1,0 мм); б – оплавленного слоя (не травленный шлиф; диффузионный слой в подложке; диффузионный слой в напыленном покрытии)
Были проведены испытания образцов с различными напыленными покрытиями на контактную износостойкость по схеме «диск по диску» с проскальзыванием и нагружением при температуре окружающего воздуха (-15Со) [8]. Перед испытаниями проводили приработку образцов на установке СМЦ-2 до исчезновения следов шлифования. В качестве контртела использовали ролик из инструментальной стали У8А ГОСТ-1435-74 (65 HRC). Через каждые 105 циклов испытаний (≈ 5,5 ч) измеряли износ покрытий с точностью ±2 мкм на микроскопе УИМ-23. Испытания на скол покрытие-подложка проводилась следующим образом: контртело разгонялось до рабочей скорости, затем приводилось в соприкосновение с структуру по границам кристаллитов, формируя, как бы упрочняющий каркас, что характерно для легированных слоев, получаемых с использованием шликерных покрытий. Таким образом, изменение коэффициента перемешивания приводит к изменению содержания упрочняющих фаз, их дисперсности, морфологическим изменениям структуры, что обусловливает свойства получаемых упрочненных поверхностных слоев.
покрытием: откола покрытия при температуре испытания (-15оС) не наблюдалось, также как и при положительных температурах. Видно (рис. 4), что лазерное оплавление, а также введение химических элементов Ni , Cr , V резко снижают износ, а также износ отколом покрытия от подложки. В качестве примера приведена зависимость износа покрытия от числа циклов для ПГСР-4.
Выводы: на основании результатов проведенных испытаний можно сделать вывод, что примененная технология нанесения покрытия и примененные порошковые материалы Ni-Сr-В-Si, Fe-С-Сr-V , нержавеющая сталь Х18Н9Т снижают износ пар трения.
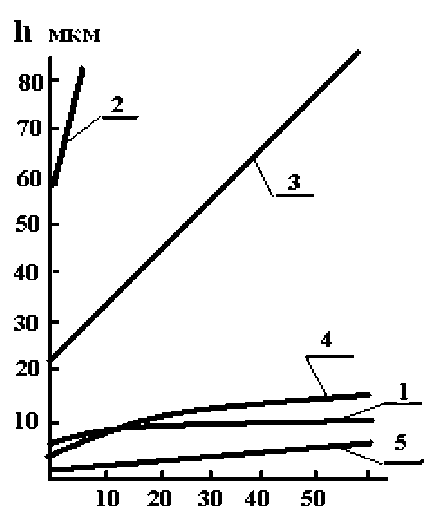
Рис. 4. Зависимость износа покрытия от числа циклов для ПГСР-4 с оплавлением: h – толщина покрытия
Список литературы Об одном методе снижения износа сколом пар трения, работающих при низких климатических температурах
- Бузник, В.М. О «пусковом периоде» пар трений в условиях Крайнего Севера/В.М. Бузник, Я.С. Семенов, М.П. Лебедев//Трение и износ. -2005, (26). -№2. -С. 191-196.
- Григорьянц, А.Г. Основы лазерной обработки материалов. -М.: Машиностроение, 1989. -304 с.
- Ларионов, В.П. Механизм влияния легирующих элементов и температуры на вязкохрупкий переход бинарных сплавов железа/В.П. Ларионов, Я.С. Семенов//Докл. РАН. -1994, (335). -№1. -С. 54-57.
- Ларионов, В.П. Физические основы вязкохрупкого перехода низколегированных сталей и сплавов железа/В.П. Ларионов, Я.С. Семенов. -Новосибирск: Наука, 1992. -172 с.
- Семенов, Я.С. Влияние напряженного состояния на вязкохрупкое разрушение/Я.С. Семенов, С.Г. Касьянов//Технология и свойства материалов техники Севера. -Якутск, 1990. -С.44-50.
- Крылов, К.И. Применение лазеров в машиностроении и приборостроении/К.И. Крылов, В.Т. Прокопенко, А.С. Митрофанов. -Л.: Машиностроение. -1978.
- Калин, Б.Е. Повышение стойкости к распылению Be, Fe, Cu путем одновременного легирования их поверхностными атомами Al и Ti/Б.Е. Калин, Н.В. Волков, С.В. Олейников//Физика и химия обработки материалов. -2004. -№2. -С. 12-15.
- Лебедев, М.П. Нагружающее устройство к машине для испытаний на трение и износ/М.П. Лебедев, В.В. Кончиц, Ю.Е. Кирпиченко//Патент №97105344/28 от 28.01.98