Обеспечение безотказной работы деталей машин с использованием новой системы переменных допусков
Автор: Денисов Вячеслав Александрович, Соломашкин Алексей Алексеевич
Журнал: Инженерные технологии и системы @vestnik-mrsu
Рубрика: Процессы и машины агроинженерных систем
Статья в выпуске: 1, 2020 года.
Бесплатный доступ
Введение. Статья посвящена описанию алгоритма определения системы допусков, основанного на использовании переменного допуска, обеспечивающего безотказную работу деталей на участке. Приведена блок-схема программы по определению переменного допуска. Установлены блоки исходной информации: ломанные и гладкие кривые контролируемого параметра; гистограмма и график распределения ресурса и определения активного участка контроля; блоки построения графиков «предельных веерных кривых изнашивания» и системы допусков для объектов исследования двух типов, в данном случае для универсального топливного насоса (УТН-5) и четырехсекционного малогабаритного топливного насоса с механическим регулятором. Предложены два способа определения системы допусков. В первом варианте графически - путем построения «предельных веерных кривых изнашивания» и определения допусков по значению ординат в контрольных точках. Во втором варианте - аналитически. Разработана формула, заменяющая графический вариант определения системы допусков. Материалы и методы. В качестве объекта исследования были выбраны два типовых насоса высокого давления. Для этих насосов были известны нормативные значения, то есть номинальное и предельное значения параметров, определены графики проведения проверок и уравнения кривых изнашивания. Устанавливались зависимости, описывающие кривые изнашивания плунжерных пар насосов, строились гистограмма и график определения ресурса насосов, определялся активный участок контроля при заданном коэффициенте вероятности безотказной работы, а также вычислялись и объединялись в систему допуска значения, вычисленные для различной наработки насоса. Результаты исследования. В результате исследования получены системы допусков для топливного насоса высокого давления двух типов, определены показатели надежности для одного из них. Разработан алгоритм определения системы допусков как графически, так и аналитически по специально разработанной формуле. Обсуждение и заключение. Исследование позволяет утверждать возможность использования переменного допуска, как основы для определения системы допусков и показателей надежности объекта диагностирования.
Система допусков, постоянный допуск, переменный допуск, показатели надежности, вероятность отказа, средний срок службы
Короткий адрес: https://sciup.org/147220649
IDR: 147220649 | DOI: 10.15507/2658-4123.030.202001.076-091
Текст научной статьи Обеспечение безотказной работы деталей машин с использованием новой системы переменных допусков
Допуски (в отличие от допусков и посадок по ГОСТу 25347-821) при техническом обслуживании и ремонте (ТОР) являются составной частью диагностической системы, ее конечной частью, завершающим этапом в определении исправности деталей машин. Основные положения, классификация, номенклатура диагностических параметров, встроенные системы диагностирования и многое другое отражены
[ETS]
в существующих ГОСТах по данной тематике2.
Система допусков - это ограничения, накладываемые на параметры технического состояния (ПТС) деталей машин, находящихся в эксплуатации3 [1].
Если в результате диагностирования, значение контролируемого параметра превысило установленное заранее допускаемое значение (допуск), то считается, что такая деталь «вышла за допуск» и она признается неисправной. Если же диагностируемая деталь не превысила эту отметку, то она считается исправной и работоспособной [2-5]. Актуальность работы состоит в том, что правильно подобранный допуск позволяет оценить исправность детали, ее потребность в замене и срок ее службы.
Рассмотрим это на примере диагностирования топливного насоса высокого давления (ТНВД). В качестве диагностического параметра, характеризующего исправность и работоспособность ТНВД, выбрана его цикловая подача q , полученная на его пусковых оборотах, то есть пусковая цикловая подача, измеряемая в мм3/цикл. Для этого параметра известна величина номинального значения U ном, величина предельного значения U пр (устанавливается в соответствии с ОСТ4 и РТМ5), а также периодичность проверки при техническом обслуживании № 3 - через 1000 мото-часов. Вместе с этим
Том 30, № 1. 2020 существуют устройства для контроля цикловой подачи насосов, стенды для диагностики и ремонта ТНВД.
Поскольку диагностирование проводится по графику Tk = { tk i }, например, периодически через определенную межконтрольную наработку tm , то значение допуска U доп - D устанавливается таким, чтобы деталь после i -й проверки ( tk i ) при наработке tk i могла без отказа доработать до следующей проверки ( i +1), при наработке tk i+ 1 , то есть через межконтрольную наработку tm (рис. 1).
Обычно такой процесс описывается кривой изнашивания диагностируемой детали. Если значение контролируемого параметра изменяется, например, по степенной зависимости U ( t ) = v^t a , то U пр ( t ) = Vftk 2 a и U доп ( t ) = v •tk 1 a . Тогда допуск D = U пр ( tk 2 ) • ( tk 2 / tk 1 ) a или D = = U пр ( tk 2) • (( tk 1 +tm ) / tk 1 ) a , где a - показатель степени степенной функции изнашивания; vi – скорость изнашивания, ед. скорости.
Кроме степенной можно использовать и другие элементарные функции и их комбинации. Пример приведен в работе А. А. Соломашкина [6]. Здесь находим анализ существующих и перспективных функций, которые могут использоваться в качестве кривых изнашивания. Для выбора наиболее информативных использовали два критерия: коэффициент достоверности аппроксимации и среднеквадрати-
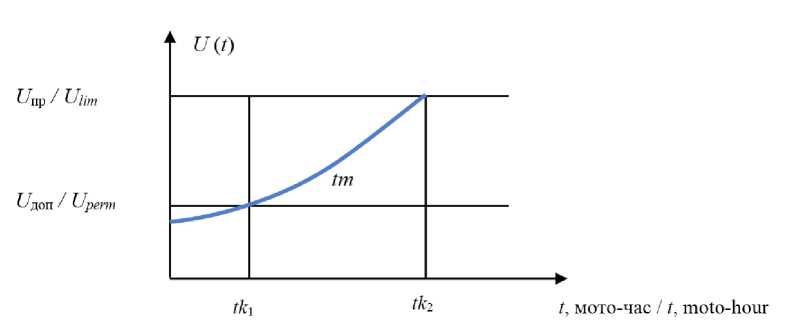
Р и c. 1. Изменение контролируемого параметра на участке tk 1 … tk 2:
U ( t ) - изменение параметра U ( t ) за время t , мото-час; U п и U оп - предельное и допускаемое значение параметра, ед. изм.; t – наработка, мото-час; tm – межконтрольная наработка, мото-час; tk 1 и tk 2 – наработка, мото-час
F i g. 1. Change of a controlled parameter on the section tk 1 ... tk 2:
U(t) - parameter change U(t) in time t, moto-hour; Ulim and Uperm - limit and permissible value of the parameter, units of measurement; t – operating time, moto-hour; tm – mikontara life, moto-hour; tk1 и tk2 – operating time, moto-hour ческое отклонение. Дополнительным условием была монотонность кривой, то есть отсутствие каких бы то ни было экстремумов, так как это не приемлемо для процесса изнашивания, износ идет только в одну сторону.
В итоге были получены следующие результаты. На первом месте - парабола, на втором – степенная функция и на третьем – экспонента. Исторически сложилось так, что чаще всего используется степенная функция, предложенная В. М. Михлиным6.
Обзор литературы
Применение допусков при диагностировании подробно изложено в исследованиях разработчиков по данной теме [1–3].
Основным специалистом по допускам для сельскохозяйственных машин является ФГБНУ «Федеральный научный агроинженерный центр ВИМ».
Здесь разрабатываются методы и средства диагностирования машин, а также стратегии технического обслуживания и ремонта машин, используя разработанные допуски.
В 2018 г. были разработаны два основных стандарта организаций (СТО) по системе допусков: СТО ВИМСТАНДАРТ 005-20187 и СТО ВИМСТАНДАРТ 004-20188.
Первый СТО декларирует алгоритм получения допуска и формулу, его заменяющую. Здесь допуск переменный, учитывающий скорость изнашивания каждой конкретной детали в отдельности. Это позволяет выбраковывать те детали, у которых текущее значение контролируемого параметра превышает допускаемое значение (допуск). Такие детали находятся «за допуском». Они неисправны, и их следует заменить. Если же допуск не превышен, то деталь
«в допуске», она исправна, и ее оставляют в эксплуатации. При этом замене подлежат детали с большой скоростью изнашивания. Они первыми достигают предельного значения, отказывают и первыми подлежат выбраковке. Детали с малой скоростью изнашивания, то есть медленно изнашивающиеся, заменяются в последнюю очередь, дорабатывают до предела и имеют самый большой срок службы. Такой селективный отбор позволяет формировать потоки отказов деталей машин с различной скоростью изнашивания. Это позволяет оптимизировать процесс восстановления замененных деталей по степени их износа. Все процедуры селективного отбора объединены в один общий алгоритм выбраковки с переменным допуском, «реагирующий» на скорость изнашивания. Селективный подбор осуществляется по скорости изнашивания.
Здесь используется переменный допуск взамен постоянного, который не различает скорость изнашивания деталей. Постоянный допуск плохо контролирует отказы деталей с большой скоростью изнашивания и незаслуженно выбраковывает детали с малой скоростью изнашивания, лишая их возможности полностью использовать свой ресурс, то есть доработать до отказа.
Алгоритм выбраковки деталей позволяет заменить одной формулой все процедуры выбраковки деталей и получить значение допуска для деталей с различной скоростью изнашивания.
Второй СТО предназначен для получения основных показателей надежности, то есть вычисления вероятности отказа и среднего срока службы, использует допускаемые значения параметра, полученные в первом СТО. Это хорошее приложение к первому СТО. Вместе они составляют единое целое для решения задачи надежности сельскохозяйственных машин.
Примеры стратегий, существующих и перспективных систем допусков, приведены в некоторых публикациях [7; 8].
Вместе с ФГБНУ «ГОСНИТИ» похожие работы проводят специалисты ФГБОУ ВО «МГУ им. Н. П. Огарёва». В анализе методов оптимизации допускаемых отклонений параметров они ссылаются на методику определения допусков, разработанную В. М. Михлиным, Ю. Н. Артемьевым9 [9], В. Н. Дорогим [2; 3], а также работы таких специалистов, как Л. К. Челпан10, А. А. Соломашкин [10;11] и других.
Материалы и методы
Для вычисления допуска D разработана компьютерная программа, позволяющая по исходным данным определить этот допуск. Блок-схема программы приведена ниже на рисунке 2. Для примера в качестве объекта были выбраны два ТНВД. Один универсальный топливный насос типа УТН-5, а второй – четырехсекционный малогабаритный топливный насос с механическим регулятором (4МТНМ). ТНВД является объектом, неисправность которого приводит к потере мощности дизеля, перерасходу топлива и плохой экологии в том месте, где работает насос.
Блок 1 – блок начальной, исходной информации. В качестве исходной информации была выбрана пусковая цикловая подача насоса.
Значение пусковой цикловой подачи плунжерных пар насоса q можно получить, например, путем проведения стендовых, ускоренных износных испытаний на специальных стендах.
Нормативные параметры насоса
Номинальное значение пусковой цикловой подачи насоса U ном = = 140 мм3/цикл. Предельное значение пусковой цикловой подачи насоса
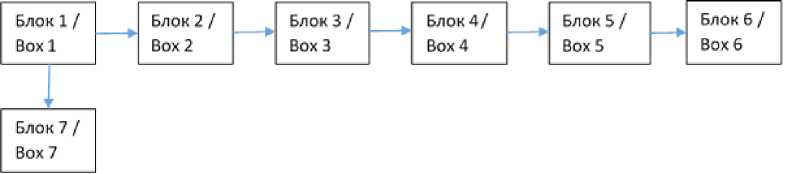
Р и с. 2. Блок-схема исследований
F i g. 2. Block diagram of research
U пр = 110 мм3/цикл. Время испытаний t i = (0, 4, 8, 12, 16, 20, 24), стендо-час. Коэффициент ускорения испытаний Ku = 100. Результаты таких испытаний для насоса УТН-5 приведены в виде массива q (8 x 7) на рисунке 3.
В блоке 2 точечные значения контролируемого параметра преобразуются в график на рисунке 4.
Далее в блоке 3 ломаные кривые аппроксимируются гладкой степенной функцией, строится соответствующий график (рис. 5) и определяется среднее значение коэффициента a – показателя степени, степенной функции каждой плунжерной пары насоса. Здесь же устанавливается предельное значение параметра U пр = 110 мм3/цикл.
В блоке 4 определяются локальные ресурсы плунжерных пар и строится гистограмма и график закона распределения ресурса насоса.
Значения локальных ресурсов каждой плунжерной пары составляют: Res i = 1 943, 2 983, 2 440, 2 441, 1 138, 1 631, 2 127, 3 877. Вид графика закона распределения ресурса насоса приведен ниже в (1).
Res( t ) =
V 2-п-о
• exp
-1 2а 1
• ( t - ц )2
. (1)
График гистограммы и закона распределения ресурса приведен ниже, на рисунке 6. Здесь Т ср = 2 322 мото-часов,
122,7 132,3 127,9 125,1 q = 185,9 192,,3 173,7 128,7 |
115,0 105,5 95,3 89,2 85,1 77,8 126,8 122,5 117,1 111,7 105,2 102,0 121,8 115,1 108,5 102,0 96,7 90,0 118,4 117,4 106, 2 100,1 96,1 86,2 175,5 156,6 145,6 135,5 123,0 117,6 177,3 173, 2 164,2 152,6 144,1 136,7 166,9 160,1 155, 2 145,2 135,1 130,7 120, 2 115,4 113,3 108,0 103,6 101,1 |
Р и с. 3. Исходные данные насоса УТН-5 – пусковая цикловая подача плунжерных пар: q – пусковая цикловая подача плунжерных пар насоса, мм3/цикл
F i g. 3. Input data of UTN-5 pump – starting injection plunger: q – starting injection quantity plunger pump, mm3/cycle
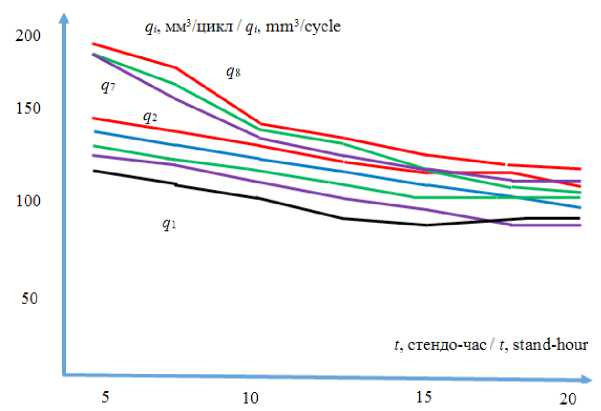
Р и с. 4. Значения контролируемого параметра пусковой цикловой подачи плунжерных пар насоса. Ломанные кривые: q 1… q 8 – пусковая цикловая подача насоса, мм3/цикл; t – наработка, стендо-час
F i g. 4. The values of the controlled parameter starting cycle flow of the pump plunger pairs. Broken curves: q 1… q 8 – starting cycle pump flow, mm3/cycle; t – time, stand-hour
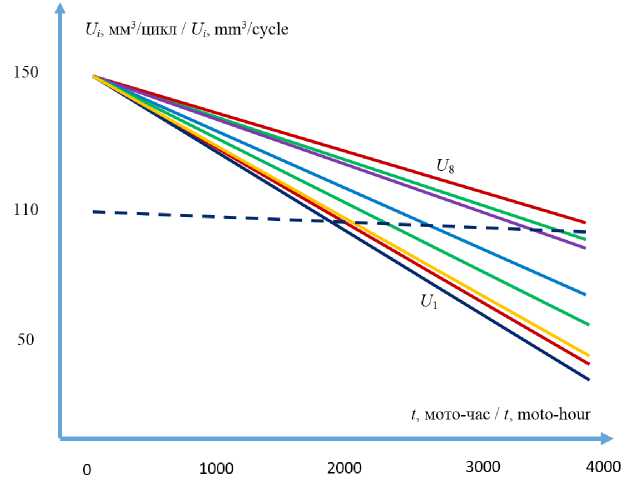
Р и с. 5. Кривыe изнашивания насоса и предельное значение пусковой цикловой подачи плунжерных пар насоса. Гладкие кривые: U 1… U 8 – пусковая цикловая подача насоса, мм3/цикл; t – наработка, мото-час; 110 – предельное значение подачи, мм3/цикл
F i g. 5. The wear curves of the pump and the limit value of the starting cycle flow of the pump plunger pairs. Smooth curves: U 1… U 8 – starting cycle pump flow, mm3/cycle; t – operating time, moto-hour; 110 – limit value of flow, mm3/cycle
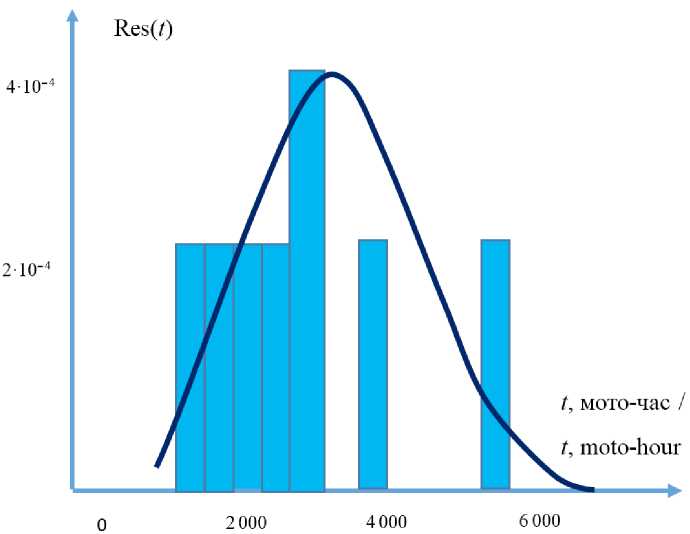
Р и с. 6. Гистограмма и закон распределения ресурса насоса: Res( t ) - ресурс насоса; t - наработка насоса, мото-час
F i g. 6. Histogram and distribution of the pump resource: Res( t ) - pump resource; t - pump operating time, moto-hour
среднее квадратическое отклонение ресурса σ = 840 мото-часов.
Далее идут блоки определения допусков. В Блоке 5 проводится определение активного участка контроля (АУК) и графика будущих проверок Тк .
АУК устанавливается при условии определения активного участка контроля с известным значением B . Здесь B – это коэффициент доверительной безотказности работы объекта контроля – насоса. Для машиностроения B = 95 %, то есть на зону АУК приходится примерно 95 % всех отказов насоса из закона распределения его ресурса.
Так как 95 % составляет ширину наработки в 2о слева и справа от середины графика ресурса, то левая граница АУК будет – t_нач = Тср – 2·σ, а правая – t_кон = Тср + 2·σ. Следовательно, начало участка АУК будет – t_нач = Тср – 2·σ = = 2 333 - 2 • 840 = 642 мото-часа, а ко- нец участка АУК – 4 002 мото-часа. Таким образом, весь активный участок контроля АУК, на который приходится 95 % отказов насоса, будет выглядеть так, как на рисунке 7.
Далее, в Блоке 6 задают график проведения проверок насоса Tk и определяют «предельные веерные кривые изнашивания» его плунжерных пар. Сначала определяют коэффициент скорости v 1, а затем уравнения этих «предельных веерных кривых изнашивания». Зная значения этих кривых, определяют систему допусков (несколько допусков) как значения кривых в соседних точках этих кривых, полученных для значений, соответствующих графику проведения проверок Tk . Для наглядности строят график «веерных кривых» и на этом графике определяют значения допусков (рис. 8). Пример таких вычислений приведен ниже.
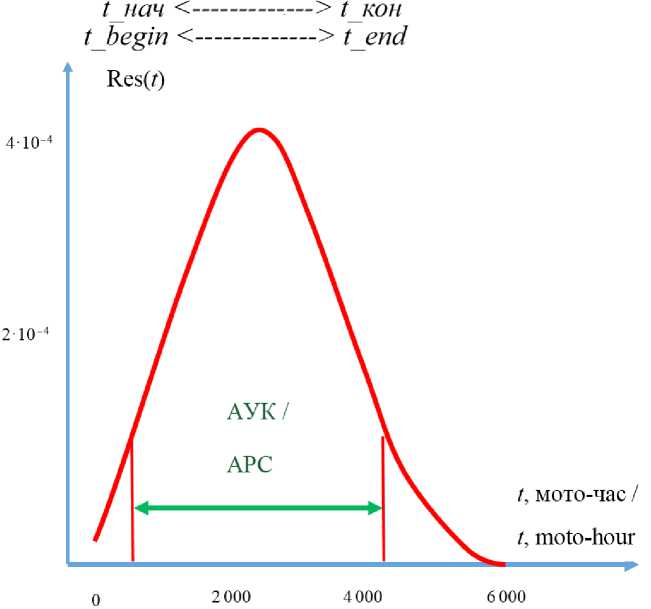
Р и с. 7. Активный участок контроля АУК: Res( t ) – ресурс насоса; t_нач и t_кон – начало и конец АУК, мото-час; t – наработка, мото-час
F i g. 7. Active phase of control APC: Res( t ) – pump resource; t_begin and t_end – start and finish of the APC, moto-hour; t – operating time, moto-hour
Определение «предельных веерных кривых изнашивания» и допусков (2…6). Из графика видно, что:
veer0 (t0) = v10 · t0a + Uном veer0 (Tk_10) = 110,(2)
veer1 (t1) = v11 · t1a + Uном veer1 (Tk_10) = 124,406,(3)
veer2 (t2) = v12 · t2a + Uном veer2 (Tk_11) = 119,541,(4)
veer3 (t3) = v13 · t3a + Uном veer3 (Tk_13) = 117,135,(5)
veer4 (t4) = v14 · t4a + Uном veer4 (Tk_14) = 115,698.(6)
Результаты исследования
Допуски, полученные графически, приведены на рисунке 8 (7…10).
D 1 = veer1 ( Tk _10) D 2 = veer2 ( Tk _11) D 3 = veer3 ( Tk _12) D 4 = veer4 ( Tk _13)
D 1 = 124,406, (7)
D 2 = 119,541, (8)
D 3 = 117,135, (9)
D 4 = 115,698. (10)
Указанный алгоритм содержит 6 связанных между собой блоков. Это следующие блоки: начальный блок и блок с исходной информацией. Здесь точечную информацию преобразуют в графическую. Далее, по этим данным строятся гистограмма и график закона распределения ресурса диагностируе-
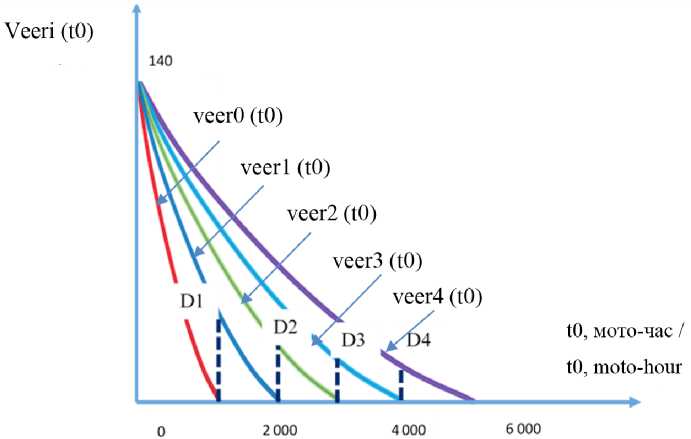
Р и с. 8. График «предельных веерных кривых изнашивания» плунжерных пар насоса и системы допусков, полученные графически D1, D2, D3 и D4: veerO (tO) ... veer4 (tO) - «предельные веерные кривые изнашивания» плунжерных пар насоса, мм3/цикл; система допусков
D 1...D4, мм3/цикл; tO - наработка, мото-час
F i g. 8. Graph of limit fan wear curves of pump plunger pairs and tolerance systems obtained graphically D1, D2, D3 and D4: veer0 (t0) … veer4 (t0) – limit fan curves of the pump’s plunger vapors, mm3/cycle; D1...D4 – tolerance system, mm3/cycle; t0 – work, moto-hour мого объекта. Затем формируется активный участок контроля, на который приходится заданный процент отказов. Далее, на этом участке задается график проведения проверок, строятся нужные (предельные веерные) кривые, и с их помощью графически определяются кривые изнашивания и допуска. В итоге с помощью 6 блоков, содержащих различную информацию, графически определяются допуски.
Блок 7. Для получения этих допусков другим аналитическим способом разработана формула, определяющая эти же допуски аналитически, то есть по формуле, приведенной ниже.
Допуски, полученные по прилагаемой формуле, представляют группу допусков (систему допусков, полученных по формуле 11), заменяя целый алгоритм, состоящий из нескольких (в дан- ном случае шести), связанных между собой различных блоков11.
D ( i ) = U ном +
+ ( U пр U ном ) "
tm 0 + ( i - 1) " tm "I alfa
tm 0 + i " tm
. (11)
Результаты, полученные аналитически (12):
D (1) = 127,637 D (2) = 120,852
D (3) = 117,843 D (4) = 116,141. (12)
Результаты, полученные графически (13):
D (1) = 127,637 D (2) = 119,541
D (3) = 117,135 D (4) = 115,698. (13)
Результаты, полученные аналитически, отличаются от результатов, полученных графически, незначительно, на несколько процентов.
Получив систему допусков для этого насоса, можно определить его основные показатели надежности, такие
Том 30, № 1. 2020
как вероятность отказа Q и средний срок службы Т ср . Результаты расчета приведены в таблице 1.
Локальные и интегральные показатели надежности насоса q , t и Q 1 , T cp1 , полученны по методике, изложенной в СТО ВИМСТАНДАРТ 004-201812.
Т а б л и ц а 1
T a b l e 1
Расчеты показателей надежности для переменного допуска Calculations of reliability metrics for variable tolerance
Показатели надежности / Reliability indicators |
Формула для вычисления / Formula for calculating |
Результат / Result |
Вероятность отказа / Probability of failure |
tm 0 q отк1 = J Res( t ) dt 0 |
0,020 |
Вероятность замены / Probability of replacement |
Tk _1 4 q 33M1 = J Res( t ) dt 0 |
0,977 |
Фактическая вероятность отказа / Actual probability of failure |
Q ф1 = q отк1 |
0,020 |
Общая вероятность отказа / Total probability of failure |
Q 1 q отк1 q зам1 |
0,996 |
Срок службы отказавших деталей, мото-час / Service life of failed parts, moto-hour |
tm 0 t otk1 = J t Res( t ) dt 0 |
8,194 |
Срок службы предварительно замененных деталей, мото-час / Service life of pre-replaced parts, moto-hour |
Tk _11 1 3aMi = Tk _10 • J Res ( t ) dt + Tk _10
Tk _11
Tk _12
Tk _13 |
1 821 |
Фактический срок службы, мото-час / Actual service life, moto-hour |
ф1 отк1 зам1 |
1 829 |
Средний срок службы, мото-час / Average service life, moto-hour |
T ср |
2 322 |
Коэффициент вероятности отказа / Failure probability factor |
kQ = Q ^1 Q 1 Q 1 |
0,020 |
Коэффициент срока службы / Service life factor |
kT 1 = T b1 T cp |
0,788 |
Здесь расчеты приведены для переменного допуска.
Расчеты в таблице показывают, что для этого насоса при среднем сроке службы 2 322 мото-часов фактический срок службы равен 1 829 мото-часов, или 78,8 % от среднего, а вероятность отказа составляет 0,02, что является весьма незначительным для данного экземпляра.
Для сравнения результатов расчета дополнительно приведены исследования по определению системы допусков для другого типа ТНВД – 4МТНМ. Результаты приведены ниже.
Исходные данные насоса 4МТНМ:
T cp = 9450 σ = 500. (14)
U ном= 173 U пр = 135 tm 0 = 7 800 tm = 500 a = 1,822. (15)
Определение допускаемых значений параметра Di для данного графика проверок (16; 17). Допускаемые значе- ния параметра Di (18; 19), полученные графически (рис. 9):
D 1 = 139,043 D 2 = 138,819
D 3 = 138,618 D 4 = 138,438. (16)
D 5 = 138,274 D 6 = 138,126
D 7 = 137,990 D 8 = 137,833. (17)
Допускаемые значения параметра Di , полученные по приведенной формуле (11), указаны ниже в (18; 19):
D (1) = 139,043 D (2) = 138,819
D (3) = 138,618 D (4) = 138,438. (18)
D (5) = 138,274 D (6) = 138,126
D (7) = 137,990 D (8) = 137,866. (19)
На рисунке 9 приведены «предельные веерные кривые изнашивания» плунжерных пар насоса ТНВД – 4МТНМ, мм3/цикл, (типа 2…6), а также
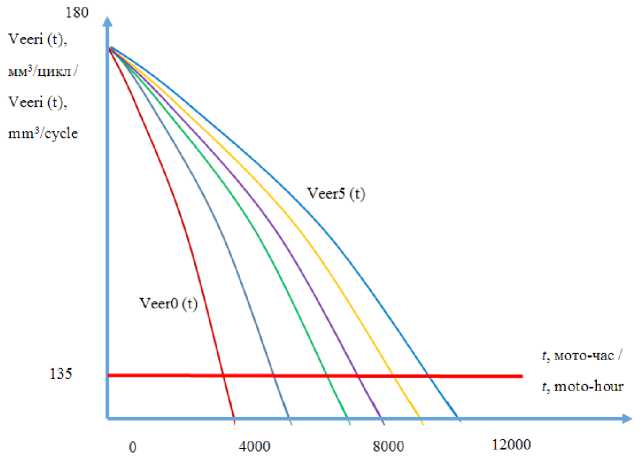
Р и с. 9. «Предельные веерные кривые изнашивания» плунжерных пар насоса ТНВД – 4МТНМ, мм3/цикл; 135 – предельное значение цикловой подачи, мм3/цикл
F i g. 9. “Limiting fan curves of wear” of TNVD pump plunge pairs – 4МТНМ, mm3/cycle;
135 – cycle limit, mm3/cycle
предельное значение цикловой подачи – 135 мм3/цикл.
На рисунке 10 показан способ определения допускаемых значений параметра D 1 (139,0 мм3/цикл) и D 5 (138,2 мм3/цикл).
Анализируя формулы (16; 17) и (18; 19), можно сделать вывод о том, что чем меньше коэффициент вариации ресурса, чем дальше график закона распределения ресурса находится от начала координат, тем меньше отличия между значениями допусков, полученных графически и аналитически. Дополнительно для указанного случая, когда скорость изнашивания деталей остается примерно постоянной, допуски можно определять, используя постоянную допуска D = 138 (для описанного случая).
Обсуждение и заключение
Допуски в ТОР являются составной частью диагностической системы, ее заключительной частью, завершающим этапом в определении исправности деталей машин. Это ограничения, накладываемые на изменения паспорта транспортного средства (ПТС) деталей машин, находящихся в эксплуатации. Если эти ограничения превышают нормативные допуски, то вероятность отказа детали машины очень высокая, то есть за допуском, но меньше предельной, такую деталь следует заменить, так как она не доработает до следующей межконтрольной проверки. Она считается неисправной.
В качестве допуска используются либо значения, полученные в алгоритме определения системы допусков, либо специально разработанная функция, заменяющая его и определяющая значения допуска при заданной наработке детали.
Итак, если в результате диагностирования значение контролируемого параметра превысило установленный заранее допуск, то считается, что такая деталь «вышла за допуск» и является неисправной. И наоборот, если значение контролируемого параметра
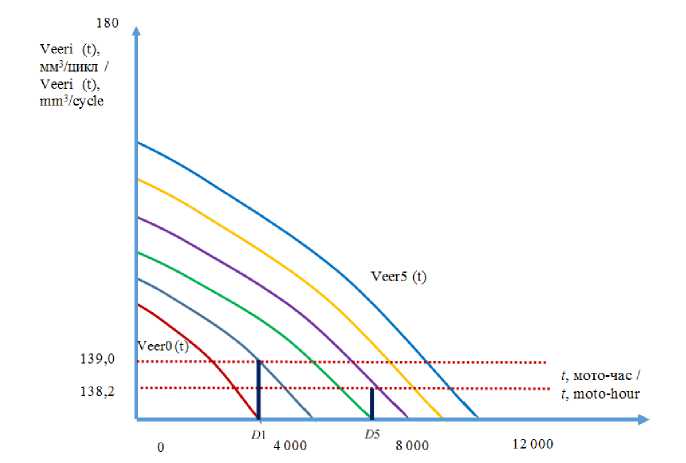
Р и с. 10. Система допусков для насоса 4МТНМ: Veeri (t) - «предельные веерные кривые изнашивания» плунжерных пар насоса ТНВД – 4МТНМ, мм3/цикл;
D 1, D 5 – допускаемые значения
F i g. 10. The system of tolerances for 4МТНМ pump: Veeri (t) – “limit fan curves of wear” of the TNVD pump plungers – 4МТНМ, mm3/cycle; D 1; D 5 – value allowed
«в допуске», то есть оно не превысило допуск, то такая деталь считается исправной и работоспособной.
В состав этой системы допусков входят: номинальное U ном , допускаемое D доп и предельное значение U пр контролируемого параметра, а также график проведения проверок ПТС - Tki = {tki} и уравнение кривой изнашивания, например, U ( t ) = A U + vt , где U ( t ) - ресурсный параметр (износ); A U - показатель приработки; t - наработка; v - скорость изнашивания; a - показатель степени степенной кривой изнашивания.
Такая система наиболее эффективна при ресурсном диагностировании. Она позволяет оценить исправность и срок службы деталей машины за весь срок ее эксплуатации. Система считается ресурсосберегающей, так как при ее использовании резко сокращается число отказов в эксплуатации. Способ задания и использования такой ресурсосберегающей системы допусков представлен в существующих методиках.
Приведены примеры алгоритма и компьютерных программ применительно к двум ТНВД. Результаты вычисления системы допусков, полученные при помощи алгоритма и разработанной функциии, отличаются незначительно, на 2…3 %, что свидетельствует о минимальной погрешности определения системы допусков.
Поступила 10.07.2019; принята к публикации 15.10.2019; опубликована онлайн 31.03.2020
Об авторах:
Все авторы прочитали и одобрили окончательный вариант рукописи.
Список литературы Обеспечение безотказной работы деталей машин с использованием новой системы переменных допусков
- Михлин, В. М. Метод определения допускаемых износов деталей, обеспечивающий повышение их безотказности / В. М. Михлин, В. Н. Дорогой // Вестник машиностроения. - 2008. -№ 7. - С. 11-14. URL: https://www.mashin.ru/files/ve708.pdf (дата обращения: 19.02.2020)
- Дорогой, В. Н. Новая методика определения допускаемых износов деталей и соединений машин / В. Н. Дорогой // Машинно-технологическая станция - МТС. - 2008. - № 3. - С. 5-10.
- Дорогой, В. Н. Алгоритм ресурсосберегающей методики определения и оценки допускаемых износов / В. Н. Дорогой, В. М. Михлин // Труды ГОСНИТИ. - 2008. - Т. 102. - С. 191-194.
- Зиченков, М. Ч. Новый подход к созданию легких и надежных силовых композитных авиаконструкций / М. Ч. Зиченков, И. О. Кондаков, А. Н. Шаныгин // Научный вестник МГТУ ГА. -2016. - Т. 19, № 6. - С.127-136. URL: https://avia.mstuca.ru/jour/article/view/994 (дата обращения: 19.02.2020) - Рез. англ.
- Мартышкин, А. П. Анализ обоснования предельных параметров элементов машин и получение практической формулы определения предельных отклонений параметров с заданной безотказностью / А. П. Мартышкин, С. Е. Маскайкина, Н. И. Полуешина [и др.] // Интернет-журнал "Науковедение". - 2015. - Т. 7, № 2. - С. 109. URL: https://naukovedenie.ru/PDF/33TVN215.pdf (дата обращения: 19.02.2020) - Рез. англ.
- Соломашкин, А. А. Выбор аппроксимирующей функции для описания кривой изнашивания деталей машин / А. А. Соломашкин // Международный научный журнал. - 2011. - № 4. -С. 104-108. - Рез. англ.
- Казакова, В. А. Стандарты организаций - стимулятор инновационного развития АПК / В. А. Казакова, В. А. Шинкевич // Стандарты и качество. - 2019. - № 6. - С. 52-54.
- Кокорева, Е. Б. Повышение эффективности использования сельскохозяйственной техники / Е. Б. Кокорева // Бюллетень науки и практики. - 2018. - Т. 4, № 2. - С. 320-325.
- Артемьев, Ю. Н. Методика расчета допускаемых при ремонте размеров и натягов тракторных двигателей и сопряжений / Ю. Н. Артемьев // Труды ГОСНИТИ. - 1994. - Т. 4. - С. 3-20.
- Соломашкин, А. А. Стратегии технического обслуживания и ремонта машин / А. А. Со-ломашкин // Труды ГОСНИТИ. - 2017. - Т. 128. - С. 145-151. URL: http://vimtsm.ru/wp-content/ uploads/2019/03/128_2017.pdf (дата обращения: 19.02.2020) - Рез. англ.
- Черноиванов, В. И. Алгоритм сравнения двух систем допусков / В. И. Черноиванов, В. А. Денисов, А. А. Соломашкин // Сельскохозяйственная техника: обслуживание и ремонт. -2019. - № 2. - С. 49-54. URL: https://panor.ru/articles/algoritm-sravneniya-dvukh-sistem-dopus-kov/2956.html (дата обращения: 19.02.2020) - Рез. англ.