Обоснование применения высокотемпературной механообработки для клина тягового хомута из стали 38ХС
Автор: Аникина В.И., Ковалева А.А., Таскин В.Ю.
Журнал: Журнал Сибирского федерального университета. Серия: Техника и технологии @technologies-sfu
Статья в выпуске: 7 т.5, 2012 года.
Бесплатный доступ
В статье обоснована ресурсосберегающая высокотемпературная термическая обработка легированной конструкционной стали 38ХС, совмещенная с процессом штамповки, производящаяся в двух средах вода–воздух, вместо применяемой стандартной закалки и последующего высокого отпуска.
Сталь 38хс, steel 38хс, закалка, высокотемпературная механообработка (втмо)
Короткий адрес: https://sciup.org/146114708
IDR: 146114708
Текст научной статьи Обоснование применения высокотемпературной механообработки для клина тягового хомута из стали 38ХС
Клин тягового хомута, изготовляемый из стали 38ХС для получения потребительских свойств, обычно подвергается окончательной термической обработке, заключающейся в закалке и последующем высоком отпуске.
Для снижения себестоимости продукции и в то же время повышения прочностных характеристик деталей из стали 38 ХС исследовали возможность проведения их термической обработки непосредственно в потоке обработки давлением. Температуру горячей обработки давлением (ковки) использовали как температуру закалки. Охлаждающей средой при закалке служила проточная вода комнатной температуры, которая в обычных условиях закалки вызывает трещинообразование и не используется при закалке деталей из этой стали.
Закалку стали 38ХС проводили в двух средах (вода–воздух) с температуры горячей обработки давлением после обрезки облоя. В качестве закалочной жидкости применяли воду, охлаждение в которой до комнатной температуры обычно вызывает трещинообразование. Длительность выдержки в воде ограничивали временем, достаточным для понижения температуры поверхности изделия до точки начала мартенситного превращения. Время охлаждения в воде, обеспечивающее оптимальное поле температур по сечению изделия, рассчитывали по программе, разработанной В.С. Биронтом на кафедре металловедения и термической обработки металлов СФУ.
Дальнейшее охлаждение изделий на спокойном воздухе вызывало отогрев поверхностных слоев за счет отвода тепла сердцевины, снижая температурный градиент по сечению, что обеспечивало уменьшение внутренних остаточных напряжений.
Максимальный эффект от применения закалки в двух средах (вода–воздух) по получению высоких прочностных свойств при достаточном уровне ударной вязкости может быть только при совмещении горячей обработки давлением с закалкой и оптимизацией режима первого этапа охлаждения (в воде).
По промышленной технологии охлаждение при закалке и отпуске стали 38ХС проводят в масло. Ускоренное охлаждение (в воде) не рекомендуют из-за опасности трещинообразования, которое отсутствует при недопускании сквозного охлаждения.
Закалка в воде приводит к получению мартенситной структуры по всему сечению детали, которая после отпуска представляет грубые иглы сильно травящегося сорбита. Это снижает пластические и прочностные свойства.
Ограничение длительности охлаждения при закалке в воде дает возможность протеканию мартенситного превращения только на поверхности изделия, при этом оставляет сердцевину горячей. Дальнейшее охлаждение на воздухе позволило всему изделию равномерно охлаждаться в области бейнитного превращения. При этом тепло постепенно перераспределялось от сердцевины к поверхности (табл.).
Результаты испытаний позволяют сделать вывод о том, что механические свойства экспериментальных образцов после закалки в воду и охлаждения в ней от 30 с до 3 мин удовлетворяют ТУ завода.
Проведение отпуска по стандартной технологии приводит к равномерному распределению структурных составляющих по объему детали и дает стабильные механические свойства.
Связь между строением излома и условиями деформации и разрушения позволяет судить о качестве материала.
Фрактографический анализ изломов проводили на электронном микроскопе на образцах стали 38ХС, прошедших заводскую термическую обработку и термомеханическую, совмещающую термическую обработку непосредственно в потоке обработки давлением.
Анализ рельефа разрушения образцов, прошедших заводскую обработку, показал, что излом имеет неоднородное строение (квазивязкое), то есть наблюдаются участки с вязким строением и участки хрупкие, разрушение которых осуществлялось сколом (рис. 1).
Деформированные растяжением образцы имели радиальные трещины, идущие в основном вдоль расположения карбидной фазы (рис. 2).
При испытании на ударную вязкость удельная работа разрушения более высокая. На таких образцах после заводской термической обработки наблюдали больше участков вязкой составляющей, хотя обнаружен смешанный характер разрушения (шестоватое строение по периферии и кристаллическое в центральной части), что показано на рис. 2 а .
Разрушение в основном происходит вокруг крупных включений карбидов или по границам зерен. Это видно на фрактограмме, где обнаружены ямки, в которых, вероятно, залегали карбиды (рис. 3).
Для идентификации характера разрушения изучали различные участки образцов при малых (х 80) и больших (х 1000, х 40000) увеличениях.
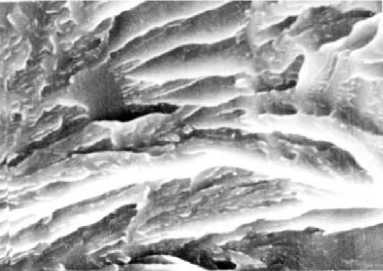
а
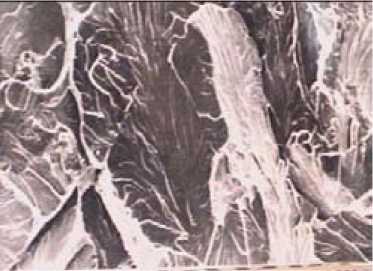
б
Рис. 1. Фрактограмма образцов, прошедших термическую обработку по заводской технологии: а – ×80, б – ×1000
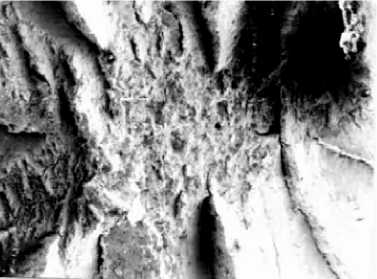
а
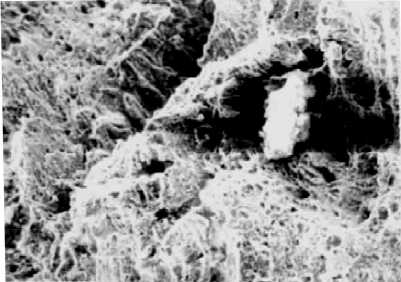
б
Рис. 2. Фрактограммы образцов, прошедших термическую обработку по заводской технологии: а – испытание на растяжение ×8, б – испытание на ударную вязкость ×80
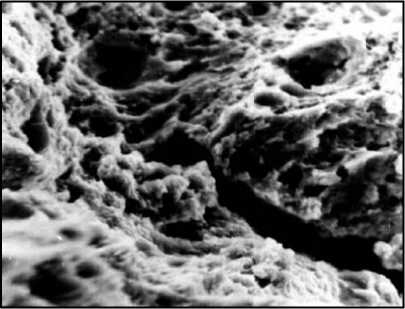
Рис. 3. Фрактограмма образцов, прошедших термическую обработку по заводской технологии ×140
На образцах, прошедших заводской режим обработки (ковка от 1000 °С, закалка и отпуск), больше участков хрупкого внутризеренного разрушения.
На рис. 1 а, б видны фасетки скола и ручьистый узор, образующийся в результате разрушения перемычек между фасетками и представляющий собой систему сходящих ступенек скола, возникающую в плоскости скола и расположенную под углом к направлению растягивающих напряжений. Эти ступеньки могли образоваться при слиянии параллельных трещин, распространяющихся в разных плоскостях, при пересечении с растущей трещиной, границами кручения или винтовых дислокаций (рис. 1).
Основным микроструктурным элементом поверхности вязкого излома являлись ямки (чашеобразные углубления параболической формы). Ямочный рельеф характеризуется следами локальной деформации, складками, гребнями (рис. 3).
На рис. 4 видно, что хрупкий скол можно наблюдать по виду хрупкой составляющей. Этот вид разрушения называют транскристаллитным, или квазисколом. Такой характер разрушения имеет высококремнистый феррит.
Кроме вязких и хрупких составляющих на фрактограммах видны карбиды и места их расположения. Карбиды имеют различную форму: удлиненные карбиды цементитного типа, карбиды ограненной формы, предположительно хромистые (рис. 5, 6).
В изломах образцов, обработанных по заводской технологии, карбиды крупные, неравномерно расположенные по сечению. В изломах образцов, обработанных по предлагаемому режиму, расположение карбидов более равномерное по сечению, карбиды имеют яйцевидную овальную форму и небольшой размер. В основном они располагаются по границам зерен (рис. 6 а, б ).
Фрактограммы, представленные на рис. 6, показывают дробление цементитных пластин, которые способствуют повышению вязкости стали. Это же показывают и исследования механических свойств (табл.).
Дробление хромистых карбидов наблюдалось при всех исследуемых режимах ВТМО, а это является определяющим в повышении ударной вязкости.
Фрактографический анализ подтвердил возможность применения технологии ВТМО для стали 38ХС.
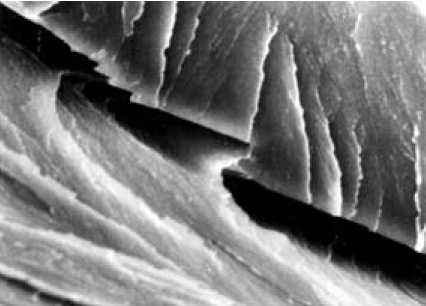
Рис. 4. Фрактограмма излома, прошедших ВТМО, ×960
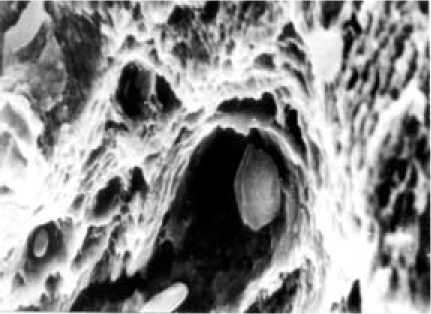
Рис. 5. Фрактограмма излома, прошедших ВТМО, ×950
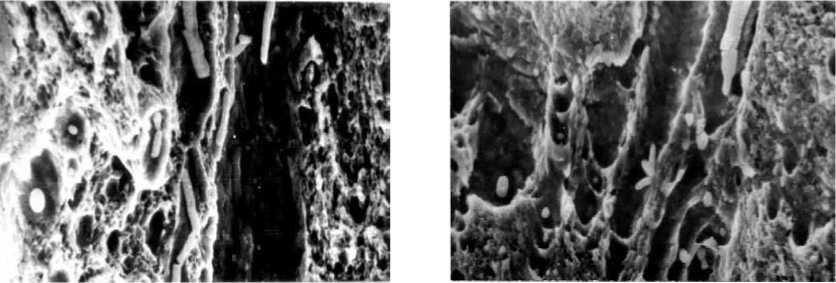
а
б
Рис. 6. Фрактограмма излома, прошедших ВТМО: а – ×400, б – ×600
Таблица. Результаты механических испытаний образцов, прошедших закалку с температуры обрезки облоя фиксированное время в воду и последующий высокий отпуск
№ п/п |
Время охлаждения, с |
Твердость НВ |
σв, МПа |
σт, МПа |
δ, % |
Ψ, % |
КСU, кДж/м2 |
1 |
180 |
255 |
905 |
764 |
21,5 |
55,5 |
1488 |
2 |
300 |
278 |
900 |
730 |
20,5 |
53,7 |
1676 |
3 |
180 |
255 |
888 |
741 |
16,0 |
50,9 |
806 |
4 |
— 60 |
285 |
911 |
741 |
18,0 |
53,7 |
1481 |
5 |
120 |
272 |
894 |
730 |
18,5 |
57,2 |
1413 |
6 |
30 |
— 282 |
905 |
707 |
16,0 |
54,6 |
1488 |
7 |
20 |
266 |
883 |
668 |
17,0 |
55,5 |
649 |
8 |
25 |
270 |
883 |
679 |
18,5 |
55,5 |
1431 |
9 |
20 |
266 |
871 |
656 |
17,5 |
56,4 |
850 |
10 |
10 |
239 |
922 |
679 |
14,5 |
37,2 |
838 |
Закалка в двух средах (вода–воздух) дала положительные результаты на сталях 40Х и 18ХГТ. Стандартный режим термообработки данных сталей предусматривал, как и сталь 38ХС, закалку в масло и последующий отпуск в масло.
Сбережение ресурсов от внедрения предлагаемой технологии достигается устранением из производственного процесса операции закалки в закалочной печи и замены охлаждающей среды – масла на воду.