Обоснование толщины покрытия при напылении биметаллического подшипника скольжения
Автор: Коренев В.Н., Родичев А.Ю., Семенов А.В., Павликов П.В.
Журнал: Агротехника и энергообеспечение @agrotech-orel
Статья в выпуске: 1 (1), 2014 года.
Бесплатный доступ
Затраты времени и себестоимость получения газотермических покрытий пропорциональны их толщине, необходимо определить ее оптимальное значение, удовлетворяющее требованиям, предъявляемым к покрытию, при минимальных затратах на ее получение. Наиболее эффективно задача обоснования толщины покрытий, наносимых с помощью газопламенного напыления на деталях, может быть решена с помощью расчетно-аналитического метода.
Газотермическое покрытие, газопламенное напыление, обоснование, толщина, расчетно-аналитический метод
Короткий адрес: https://sciup.org/14769977
IDR: 14769977
Текст научной статьи Обоснование толщины покрытия при напылении биметаллического подшипника скольжения
The time consumption and the prime cost of producing gasthermal coverings are proportional to their thickness; it is necessary to determinate its optimum value that meets the requirements, placed to the covering at the minimum costs for its production. Most effective way of solving the problem of justification of coverings thickness applied by means of flame spraying on details is to use the calculating-analytical method.
Задний мост автогрейдера и задняя подвеска автомобилей КамАЗ, ЗИЛ-130Г, КрАЗ, имеет разное конструктивное решение балансирного устройства, в состав которого входят втулки (подшипники скольжения), изготовленные из антифрикционного материала, работающие в условиях абразивного изнашивания. Эти подшипники лимитируют ресурс заднего моста автогрейдера (задней подвески автомобилей) и требуют восстановления либо замены новыми - ремонтного размера.
При проведении капитального ремонта автомобилей требуется ремонт задней подвески, а анализ износного состояния подшипников скольжения показал, что внутренняя цилиндрическая поверхность бронзовых втулок выходит за пределы размеров допустимых при ремонте. Геометрические параметры и материал подшипников скольжения автомобилей и автогрейдера представлены в таблице.
Таблица - Геометрические параметры и материал подшипников скольжения задней подвески автомобильной и строительно-дорожной техники
Тип и марка транспортного средства |
Основные размеры подшипников скольжения D×d×L, мм |
Материал подшипников скольжения |
КамАЗ |
100×89×80 |
Бронза |
КрАЗ |
120×108×80 |
Бронза |
ЗИЛ-130Г |
100×89×80 |
Бронза |
Автогрейдер |
240×220×120 |
Бронза |
Тип и марка транспортного средства |
Основные размеры подшипников скольжения D×d×L, мм |
Материал подшипников скольжения |
210×190×120 |
Анализ существующих материалов и технологий изготовления и восстановления подшипников скольжения позволяет остановить свой выбор на технологии восстановления подшипника скольжения из цельной бронзы путем постановки дополнительной детали ремонтного размера [1]. Причем дополнительную деталь ремонтного размера изготавливают биметаллической. Для изготовления биметаллического подшипника скольжения автомобиля КамАЗ сначала изготавливают стальную втулку с наружным диаметром равным номинальному диаметру бронзовой втулки, внутренним диаметром большим номинального на 1,5…3 мм, для нанесения на внутренний диаметр стальной втулки антифрикционного слоя толщиной 0,75…1,5 мм.[2]
Для изготовления биметаллической втулки используем заготовку Труба 114 х 20 ГОСТ 8732 - 78 , длина L =84 мм.
В 20 ГОСТ 8731 - 74
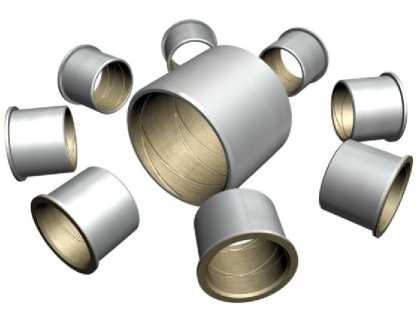
Рисунок 1 – Биметаллические подшипники скольжения башмака балансирного устройства автомобильной и строительнодорожной техники.
Поскольку затраты времени и себестоимость получения газотермических покрытий пропорциональны их толщине, необходимо определить ее оптимальное значение, удовлетворяющее требованиям, предъявляемым к покрытию, при минимальных затратах на ее получение. Наиболее эффективно задача обоснования толщины покрытий на деталях может быть решена с помощью расчетно-аналитического метода.
Толщина покрытия - понятие, относящееся к определенной обрабатываемой поверхности, измеряют ее по нормали к этой поверхности. Колебание размеров, получаемых на каждой ступени обработки, обуславливает изменение толщины покрытия. Различают следующие возможные значения толщины покрытия, подвергнутого размерной обработке: номинальная толщина, наиболее возможная толщина, наименьшая возможная толщина и средняя толщина.
Выбранная система отсчета толщины покрытия должна удовлетворять следующим требованиям: объективно учитывать закономерности изменения толщины покрытия на различных стадиях обработки поверхностей детали, соответствовать системе допусков и посадок и теории размерных цепей. Этим требованиям отвечает система, в которой за начало отсчета принято номинальное значение размера. Построим на основе такой системы отсчета схемы размерных связей между операционными размерами, припусками и допусками на обработку для охватывающей поверхности. [3]
Проведем расчет выражений, полученных в результате решения размерных цепей. За основу расчета выбираем подшипник скольжения из бронзы автомобиля КамАЗ (фото 1) наружным диаметром Ø100мм и внутренним диаметром Ø88мм с буртиком 0111мм.
Минимальная толщина обрабатываемого покрытия
t
п . мин .
tn
дет
Ф
t - минимальный размер толщины обрабатываемого п. мин.
покрытия;
t - номинальное значение толщины обрабатываемого покрытия;
Здет - допуск на размер детали;
Ф
- фактор формы для цилиндрических поверхностей
Ф = 2
f S 0’22
t = 1,5 — = 1,39 мм п. мин.
Допуск на толщину обрабатываемого покрытия
^п =
Г s’ л
•^
V Ф 7
+ 5 дет ,
5 - допуск на толщину обрабатываемого покрытия;
5заг - величина допуска на размер заготовки
5' = | 087 1 + 0,22 = 0,655 мм п V 2
Максимальная толщина обрабатываемого покрытия t = t + загаг-
-
п. макс п^^
t - максимальный размер толщины обрабатываемого п. макс покрытия;
t =1,5 + 087 = 1,935 мм п. макс , 2,
Номинальная толщина обрабатываемого покрытия t = (Азаг — Адет ) ,(3)
пФ
-
t - номинальная толщина обработанного покрытия;
Адет — размер готовой детали
Азаг - размер исходной заготовки перед нанесением покрытия
(91 — 88)1 < tп = = 1,5 мм
Допуск на размер заготовки с покрытием
5" = 5' + Ф5(4)
заг загп
-
5Заг - допуск на размер заготовки с напыленным покрытием
-
5 - допуск на толщину напыленного покрытия
5'" аг = 0,87 + 2 • 0,1 = 1,07
Номинальный припуск на обработку покрытия 7=7 + Л"
Z о Z омин + 5 заг ,
Z - припуск на обработку покрытия
Z о = Z омин + 5 заг + Ф5 п ,
Z - минимальный общий припуск на обработку
покрытия
Zo = 0,4 + 1,07 = 1,47 мм
Максимальный припуск на обработку покрытия
Z = Z + 5 ,
омакс о дет
Z омакс Z омин + 5 заг + Ф5 п + 5 дет ,
Z - максимальный общий припуск на обработку
покрытия
Zомакс = 1,47 + 0,22 = 1,69 мм
Максимальная толщина напыленных покрытий
Т = t + Z ° ,
п. макс п ^^ ,
Т - максимальная толщина наносимого покрытия
п . макс
1.47
Т п.макс = 1,5 + = 2,235 ммМинимальная толщина напыленных покрытий
Т = Т „
п . мин п . макс
— 5 п ,
Т - минимальная толщина наносимого покрытия п.мин
Т„„= 2,235 — 0,1 = 2,135 мм
Номинальный размер заготовки с напыленным покрытием
A 3аг = А з аг
—
ФТ , п.макс ,
A " - номинальный размер заготовки с покрытием
A"аг = 91 — 2 • 2,235 = 86,53 мм
Максимальный размер заготовки с напыленным покрытием
"
заг . макс заг заг ,
A - максимальный размер заготовки с покрытием заг. макс
= А заг . макс заг
-ФТ + 5 " , п . макс заг ,
A"заг м = 6 86,53 + 1,07 = 87,6 мм заг . макс
Минимальный размер заготовки с напыленным покрытием
It II . I
-ФТ п. макс ,
= А = А заг . мин заг заг
А" - минимальный размер заготовки с покрытием заг. мин
" = А'
заг . мин заг
- Фtп
— Ф5п,
Аз аг. мин = Аз аг = 91 - 2'2,235 = 86,53
мм
Средняя толщина покрытий
t п. ср
t +1
п . макс п . мин
2
,
t - средняя толщина покрытий
t п.ср
1,935 +1,39
2
= 1,6625 мм
В результате проведенных расчетов четырех возможных вариантов расположения наслаиваемых покрытий на обрабатываемой поверхности, получаемых в результате совмещения минимальных и максимальных размеров заготовки, подготовленной к нанесению покрытия, были определены: максимальный, номинальный и минимальный размер заготовки с напыленным покрытием; максимальная, минимальная и средняя толщина напыленного покрытия (рис. 2).
Вывод. Проведенные расчеты и построенная схема максимальных, номинальных и минимальных размеров заготовки с напыленным покрытием дает возможность для разработки технологии изготовления биметаллического подшипника с оптимальными параметрами, удовлетворяющими требованиям, предъявляемым к покрытию, при минимальных затратах на ее получение.
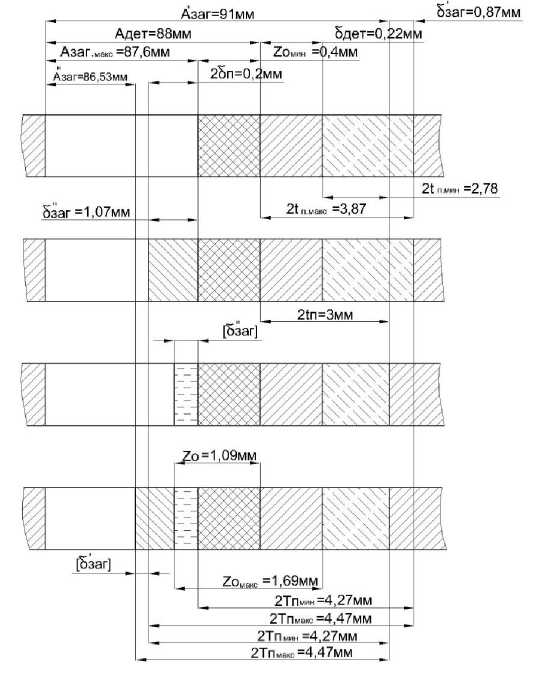
Рисунок 2 - Схема максимальных, номинальных и минимальных размеров заготовки с напыленным покрытием.
Список литературы Обоснование толщины покрытия при напылении биметаллического подшипника скольжения
- Пат. №2424888 Российская Федерация, МПК7 B23P6/00 Способ восстановления подшипника скольжения. /Коренев В. Н., Хромов В. Н., Родичев А. Ю. опубл. 27.07.11 г. Бюл. №21
- Пат. №2416744 Российская Федерация, МПК7 F16C 33/00 Способ изготовления подшипника скольжения. /Родичев А. Ю., Хромов В. Н., Коренев В. Н., Барабаш В. В. опубл. 20.04.11 г. Бюл. №36
- Хасуй, А. Наплавка и напыление /А.Хасуй, О Моригаки. -М.: Машиностроение, 1985. -240с., ил. УДК 546.57