Обработка поверхности армирующего наполнителя из углеволокна для повышения адгезии с бутадиеновым эластомером
Автор: Копырин М. М., Марков А. Е., Дьяконов А. А., Туисов А. Г., Лебедев М. П., Кычкин А. А., Охлопкова А. А., Лазарева Н. Н., Данилова С. Н.
Журнал: Журнал Сибирского федерального университета. Серия: Техника и технологии @technologies-sfu
Рубрика: Исследования. Проектирование. Опыт эксплуатации
Статья в выпуске: 4 т.16, 2023 года.
Бесплатный доступ
В работе приводятся результаты исследования увеличения адгезионного взаимодействия бутадиенового эластомера с армирующей тканью на основе углеволокна. Повышения адгезии эластомера с углеволокном добивались путем поверхностной обработки армирующей ткани, растворенной резиновой смесью в толуоле и клеем Хемосил. В результате исследования высокомодульных материалов на расслоение эластомера от углеволокна наблюдается повышение прочности адгезии. При обработке хемосилом армирующей ткани разрушение происходит по эластомеру, прочность соединения с углеволокном превышает когезионную прочность эластомера. Увеличение адгезии между армирующим наполнителем и бутадиеновой матрицей приводит к изменению упругопрочностных свойств полученных высокомодульных материалов, происходит увеличение прочности при разрыве, твердости, снижение относительного удлинения и абразивостойкости. Методом электронной микроскопии установлено, что поверхностная обработка углеткани приводит к образованию плотного контакта с эластомерной матрицей. При помощи термомеханического анализа показано, что данные материалы могут эксплуатироваться при отрицательных температурах.
Эластомер, углеволокно, высокомодульный материал, адгезия, композитный эластомер, поверхностная обработка
Короткий адрес: https://sciup.org/146282620
IDR: 146282620
Текст научной статьи Обработка поверхности армирующего наполнителя из углеволокна для повышения адгезии с бутадиеновым эластомером
Активное развитие различных областей промышленности ставит новые задачи по разработке функциональных и конструктивных материалов, которые обладают высокими эксплуатационными показателями. Одним из направлений материаловедения является создание высокопрочных полимерных композитов с заданными свойствами за счет комбинирования разных материалов. При этом актуальной задачей при разработке таких композитов является повышение адгезии между материалами, отличающимися по своему химическому составу и свойствам, так как высокая прочность соединения между материалами в изделии отвечает за надежность при его эксплуатации.
В настоящее время за счет армирования волокнами различных полимерных матриц разрабатываются высокомодульные материалы, обладающие наибольшей прочностью в сочетании с высоким сопротивлением к деформации [1, 2]. Применение композиционных материалов в климатических условиях Арктики и Субарктики достигается за счет использования материалов, отвечающих условиям эксплуатации. Например, основным ингредиентом, который отвечает за морозостойкость в резиновых смесях, является каучук [3], при этом наиболее высокой морозостойкостью обладают эластомеры на основе бутадиеновых каучуков [4]. В качестве армирующих наполнителей для разработки высокопрочных композитных эластомеров можно применять высокомодульные волокна из базальто-, стекло- и углеволокна с широким интервалом рабочих температур [5–8]. Данные материалы обладают высокими прочностными свойствами [9, 10] и химической инертностью [11–13]. Эти наполнители в основном применяются в эпоксидных матрицах [14, 15].
С введением армирующих наполнителей в полимерную матрицу встает вопрос повышения сцепления между ними. Как показал литературный анализ [16–18], наиболее распространенным и доступным методом является нанесение или смачивание поверхности волокна (поверхностная обработка). Например, в работе [17] использовались методы химического травления волокон для улучшения адгезии стекловолокна с полимерной матрицей. В исследовании [18] авторы достигли повышения адгезии между стекловолокном и стирол-бутадиен-винил-пиридным эластомером за счет предварительной пропитки стекловолокна раствором, содержащим ɣ-аминопропилтриэтоксисилан, глицерин и воду. В работе [16] авторы модифицировали поверхность волокна плазмохимическим методом.
Целью данной работы является повышение адгезии между армирующей тканью на основе углеволокна с бутадиеновым эластомером, изучение их физико-механических свойств и структуры.
Материалы и методы исследования
Для повышения адгезионного взаимодействия между тканью из углеволокна и морозостойкого эластомера проводилась предварительная обработка поверхности ткани двумя способами с последующей совместной вулканизацией. Первый способ включает в себя обработку поверхности армирующей ткани растворенной смесью резины (РС) в толуоле, вследствие чего происходит проникновение РС вглубь ткани и его застывание. Второй способ включает в себя обработку поверхности ткани праймером и адгезивом Хемосил.
Объектами исследования являются высокомодульные эластомерные композиты, армированные тканью из углеволокна. В качестве эластомерной матрицы взяли стандартную резино- – 452 –
Таблица 1. Рецептура резиновой смеси на основе каучука СКД-В и время введения ингредиентов
Table 1. Recipe and time of introduction of ingredients of rubber mixture based on SKD-V rubber
Смешение ингредиентов резиновой смеси производили в лабораторных вальцах открытого типа PL-2200 (Brabender, Германия): каучук и стеариновую кислоту вводили в начале процесса, на 2-ой мин вводили технический углерод, на 5-ой мин – оксид цинка, на 10-ой – добавляли сульфенамид Ц, на 12-ой мин – серу. Общее время смешения ингредиентов резиновой смеси составило 20 мин.
В качестве армирующего слоя применяли углеткань (УТ) марки 2/2–1000–12К-400 (Препрег-СКМ, Россия) (ТУ 1916–038–38276489–2016) с плотностью 407 г/м2 и саржевым переплетением 2/2. УТ 2/2–1000–12К-400 характеризуется высокой термостойкостью до 1500 °C, небольшим удельным весом и устойчивостью к воздействию вибрации.
Образцы композитных эластомеров были изготовлены методом послойной укладки: резиновая смесь – армирующий слой ткани – резиновая смесь. На рис. 1 представлена фотография образца, на котором видна послойная укладка.
Вулканизацию опытных высокомодульных эластомерных образцов проводили на гидравлическом прессе ПКМВ-100 (Импульс, Россия) при температуре 155 оС в течение 20 мин под давлением 10 МПа.
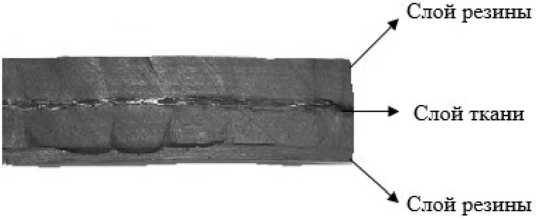
Рис. 1. Фотография образца с послойной укладкой: резина-ткань-резина
Fig. 1. Photo of sample with layering: rubber-fabric-rubber
Упругопрочностные свойства армированных эластомеров определяли на испытательной машине Autograph (Shimadzu, Япония) при комнатной температуре в соответствии со стандартом ISO 37–2020. Растяжение образцов производили со скоростью 500 мм/мин до разрыва, в процессе растяжения измеряются силы при заданных удлинениях в момент разрыва, а также удлинение образца в момент разрыва. Определение твердости эластомерных образцов осуществляли по стандарту ISO 7619–1–2009. Абразивостойкость образцов определяли по массовому истиранию об абразивную поверхность наждачной бумаги зернистостью N 150 при скольжении на машине МИ-2 (Метротекс, Россия), в соответствии со стандартом ISO 4649–85. Адгезию между слоями при расслоении определяли на испытательной машине «Autograph» (Shimadzu, Япония), позволяющей сохранять направление приложенной нагрузки (растягивающего усилия) перпендикулярно к твердой полимерной подложке. Исследование проведено при комнатной температуре и скорости перемещения захватов 50 мм/мин. Исследование надмолекулярной структуры материалов проводилось при помощи растрового электронного микроскопа JSM-7800F (JEOL, Япония). Определение термомеханических кривых высокомодульных эластомеров проводилось на термомеханическом анализаторе ТМА-60 (Shimadzu, Япония). Температурный диапазон исследования варьировался от минус 100 до плюс 100 оС. Скорость нагрева образцов составляла 10 оС/мин при нагрузке индентора 50Н.
Результаты и обсуждения
На рис. 2 приведены результаты испытания относительного удлинения и предела прочности исходного эластомера, эластомера с УТ (СКД-В УТ), эластомера с УТ, обработанной РС (СКД-В УТ/РС), и эластомера с УТ, обработанной Хемосилом (СКД-В УТ/Хемосил).
Введение в эластомерную матрицу слоя армирующей УТ приводит к значительному уменьшению показателей относительного удлинения при разрыве по сравнению с исходным эластомером. Из диаграммы (рис. 2а) видно, что низкие деформационные свойства армированных образцов напрямую связаны с высоким сопротивлением к растяжению УТ. Поверхностное модифицирование армирующих тканей снижает относительное удлинение за счет образования
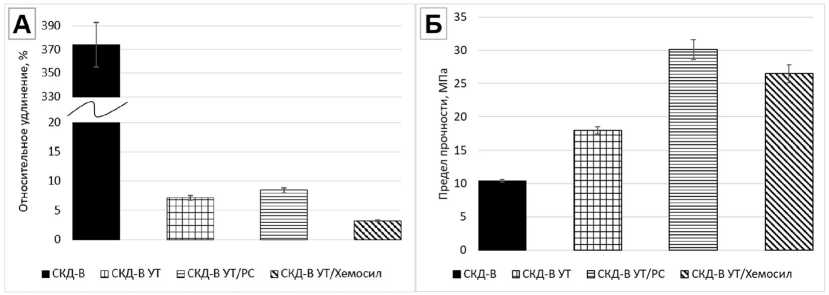
Рис. 2. Диаграммы относительного удлинения (а) и предела прочности (б) эластомеров на основе каучука СКД-В и УТ с растворенной смесью и с Хемосилом
Fig. 2. Relative elongation (a) and tensile strength (б) diagrams of elastomers based on SKD-V rubber and CF, with dissolved compound (DC) and with Chemosil более плотного соединения между эластомерной матрицей и волокнами. Наибольшее снижение деформационных свойств наблюдается у образца, обработанного Хемосилом.
По результатам исследования прочностных свойств (рис. 2б) наблюдается существенное увеличение при введении армирующих слоев тканей в эластомер. Добавление армирующей ткани без поверхностной обработки в эластомерную матрицу значительно повышает прочностные показатели. Модифицирование поверхности волокон растворенной смесью и Хемосилом приводит к дальнейшему росту прочности эластомеров благодаря повышению адгезии между армирующим наполнителем и матрицей. Наибольшей прочностью обладает образец с УТ, обработанной РС – 30,1 МПа, что в 3,8 раза больше прочности исходной резины. При сравнении обработанных образцов видно, что наиболее высокий показатель прочности наблюдается у образцов с поверхностной обработкой РС. Предположительно, такое увеличение можно объяснить тем, что резиновая смесь во время вулканизации проникает в свободное пространство между пучками волокон УТ и взаимодействует с РС. При этом незначительное снижение прочности образцов с обработкой ткани Хемосилом, по сравнению с образцом с обработанной тканью РС, может быть связано с частичным растворением замасливателя на поверхности волокна при нанесении.
Повышение сопротивления к сдвиговым деформациям, выраженное в уменьшении относительного удлинения, и повышение предела прочности придают высокомодульные свойства композитным образцам.
Для объяснения причин изменения упругопрочностных показателей армированных эластомеров провели исследование надмолекулярной структуры образцов. На рис. 3 представлены микрофотографии сколов образцов на межфазной границе взаимодействия армирующих наполнителей с эластомерной матрицей.
На микрофотографии (рис. 3б) видно, что на месте контакта эластомерной матрицы с армирующей тканью без поверхностной обработки взаимодействия не наблюдается. Отсутствие адгезии между эластомерной матрицей и наполнителями отражается на прочностных свойствах при растяжении, что объясняет наименьшие показатели среди армированных образцов. На рис. 3в, г приведены микроструктуры образцов с УТ после поверхностной обработки РС и Хемосилом, где показан хороший контакт эластомера с армирующей тканью. Анализ предела прочности армированных образцов (рис. 2б) с микроструктурой образцов на фазовой границе взаимодействия напрямую коррелирует.
На рис. 4 приведены диаграммы твердости по Шору А (а) и износостойкости (б) исходного и армированных эластомеров.
Из диаграммы твердости по Шору А (рис. 4а) видно, что введение армирующей ткани в эластомерную матрицу не влияет на показатели твердости. Изменения варьируются в 1 единицу, что входит в интервал погрешности. После обработки ткани растворенной смесью показатель твердости повысился в среднем на 5 единиц у образцов СКД-В УТ/РС по сравнению с исходной резиной. Это объясняется тем, что растворенная резиновая смесь заполнила свободное пространство между волокнами ткани. Значительное повышение твердости наблюдается у образцов с УТ, обработанной Хемосилом. Твердость повысилась в среднем на 12 %, что обусловлено получением жесткого каркаса клеящих слоев Хемосила после вулканизации.
На рис. 4б приведена диаграмма результатов испытания на износостойкость, где образцы с армирующими тканями подверглись большему истиранию по сравнению с исходной резиной, – 455 –
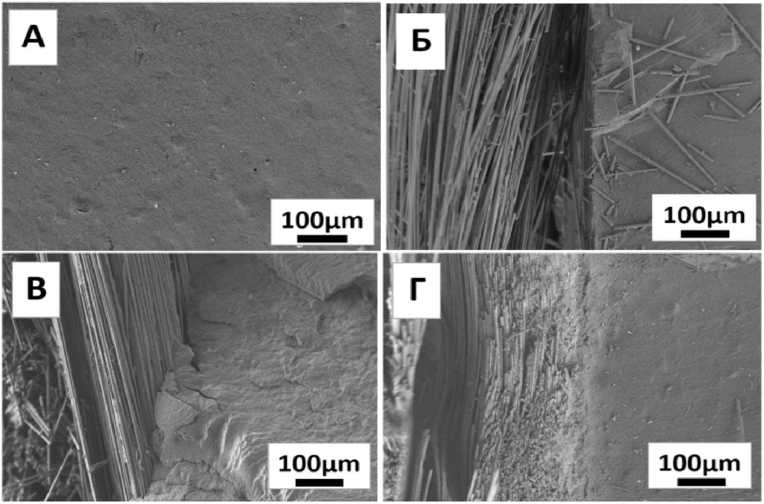
Рис. 3. Микрофотографии сколов образцов: a) СКД-В; б) СКД-В УТ; в) СКД-В УТ/РС; г) СКД-В УТ/ Хемосил
Fig. 3. Microphotographs of cleavage samples: a) SKD-V; б) SKD-V CF; в) SKD-V CF/DC; г) SKD-V CF/Che-mosil
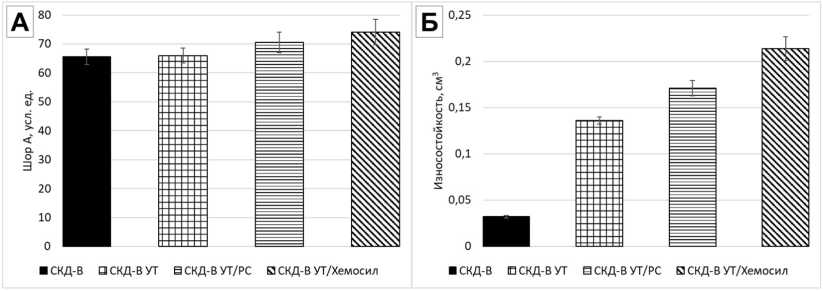
Рис. 4. Диаграммы твердости по Шору А (а) и износостойкости (б) эластомеров на основе каучука СКД-В и УТ с растворенной смесью и с Хемосилом
Fig. 4. Shore A hardness diagrams (a) and wear resistance diagrams (б) of elastomers based on SKD-V and CF rubber, with dissolved compound (DC) and with Chemosil истирание армированных образцов увеличилось в ~4,2–6,7 раза. Это может объясняться тем, что ткани при абразивном истирании о крупные частицы подвергаются разрушению и разрыву волокон. Предположительно, увеличение объема истирания после поверхностной обработки армирующих тканей растворенной смесью и Хемосилом происходит за счет увеличения адгезии между наполнителем и эластомером, вследствие чего происходит отрыв волокна вместе с резиной.
Результаты испытания на расслоение эластомерных образцов, армированных УТ, показаны в табл. 2.
Таблица 2. Показатели адгезии образцов на основе эластомера СКД-В и УТ с растворенной смесью и с Хемосилом
Table 2. Values of adhesion parameters of samples based on SKD-V and CF elastomer, with dissolved compaund and with Chemosil
Образец |
Н/мм |
СКД-В |
8,58 |
СКД-В УТ |
0,91 |
СКД-В УТ/РС |
2,61 |
СКД-В УТ/Хемосил |
9,31 |
Из табл. 2 видно, что адгезия между эластомерной матрицей и армирующей тканью у образца СКД-В УТ имеет низкое значение из-за отсутствия взаимодействия на границе раздела фаз, вследствие инертности эластомера с УТ. Поверхностная обработка УТ растворенной смесью увеличивает адгезию в ~3 раза по сравнению с образцом без обработки. РС проникает в свободные пространства между волокнами УТ, что приводит к плотному сцеплению с эластомерной матрицей с двух сторон во время вулканизации. Когезионная прочность при расслоении эластомера на основе СКД-В составила 8,58 Н/мм. В процессе испытания на расслоение образца СКД-В УТ/Хемосил разрушение имело когезионный характер и происходило по эластомеру, что свидетельствует об образовании прочного адгезионного соединения между матрицей и УТ, превышающего когезионную прочность эластомера. Адгезия образца СКД-В УТ/Хемосил увеличилась в ~10 раз по сравнению с образцом без обработки. Такое увеличение прочности соединения предположительно объясняется плотным каркасом на поверхности ткани и образованием новых химических связей на границе взаимодействия материалов.
На рис. 5 представлены микрофотографии армированных образцов после испытания на расслоение, исследуемая область была со стороны эластомера.
На микрофотографиях (рис. 5а) образцов с исходной армирующей тканью наблюдаются оторванные обломки волокон после испытания на расслоение. Отслоение необработанных

Рис. 5. Микрофотографии образцов после испытания на расслоение: a) СКД-В УТ; б) СКД-В УТ/РС; в) СКД-В УТ/Хемосил
Fig. 5. Microphotographs of specimens after delamination testing: a) SKD-V CF; б) SKD-V CF/DC; в) SKD-V CF/Chemosil
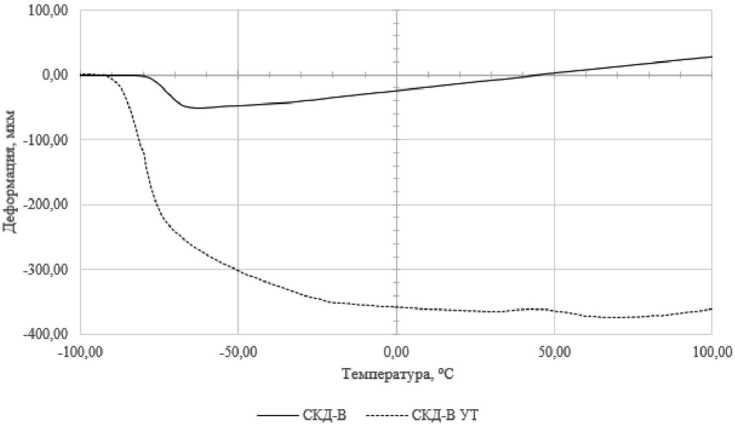
Рис. 6. Кривые термомеханического анализа СКД-В и СКД-В УТ
Fig. 6. Thermomechanical analysis curves for SKD-V and SKD-V CF волокон от эластомерной матрицы свидетельствует о слабом адгезивном взаимодействии, что подтверждается результатами исследования прочности соединения. На участке расслоения образцов ткани с обработанной поверхностью РС (рис. 5б) наблюдаются более плотно вдавленные волокна ткани в массив эластомерной матрицы. Плотное соединение волокон с матрицей произошло вследствие полного обволакивания волокон РС. Поверхностная обработка армирующих тканей Хемосилом приводит к увеличению адгезии матрицы с волокнами, вследствие чего происходит когезионное разрушение эластомера. Это объясняется тем, что во время поверхностной обработки Хемосилом он проник между волокнами, тем самым создавая прочный каркас и соединение между материалами в процессе вулканизации. Наибольшую прочность при испытании на расслоение показал образец СКД-В УТ/Хемосил. На поверхности образца (рис. 5в) не наблюдаются УТ и следы ее отрыва, что является следствием когезионного разрушения эластомера. Во время испытания армированных образцов, обработанных Хемосилом на расслоение, разрушение происходит по резине, что указывает об образовании адгезионного соединения между материалами, которое превышает когезионную прочность эластомера.
На рис. 6 приведены кривые термомеханического анализа (ТМА) эластомерной матрицы и образца на основе эластомерной матрицы с армированной углетканью.
На графике ТМА наблюдаются кривые зависимости изменения линейного размера в зависимости от увеличения температуры. Начало изменения линейного размера для эластомера СКД-В проявляется в диапазоне температур от минус 81,3 до минус 75,9 °C, что связано с сегментальной подвижностью макромолекул каучука. У образца СКД-В УТ подвижность начинает проявляется в диапазоне температур от минус 92,4 до минус 85,7 °C. Предположительно, начало изменения термомеханических кривых армированного эластомера при более низких температурах определяется проявлением подвижности армирующего наполнителя.
Заключение
На основании результатов исследования свойств высокомодульных материалов установлено, что поверхностная обработка углеткани является эффективным способом для увеличения прочности соединения между углеволокном и эластомером. При поверхностной обработке углеткани клеем Хемосил происходит повышение адгезии между наполнителем и матрицей, которая превышает когезионную прочность эластомера. Также поверхностная обработка ткани растворенной смесью и клеем Хемосил приводит к повышению прочностных свойств, твердости, к снижению относительного удлинения и износостойкости. При исследовании микроструктуры границы взаимодействия образцов с поверхностной обработкой наблюдается плотный контакт углеволокон с эластомерной матрицей. Методом термомеханического анализа установлено, что температурный диапазон применения зависит от используемой матрицы и наполнителя.