Оценка динамической устойчивости в мониторинговой системе управления технико-экономической эффективностью дорожных машин
Автор: Мандровский Константин Петрович
Журнал: Вестник Донского государственного технического университета @vestnik-donstu
Рубрика: Машиностроение и машиноведение
Статья в выпуске: 2 (85) т.16, 2016 года.
Бесплатный доступ
Целью данного исследования является рассмотрение предпосылок к сокращению времени транспортных перемещений дорожно-строительных машин. На основе полученных сведений могут быть сформированы соответствующие рекомендации, используемые в мониторинговой системе управления эффективностью и техническом аудите. Отмечены недостатки существующих мониторинговых систем. Показано, что их применение для повышения технико-экономической эффективности дорожных машин не позволяет достичь контролируемых результатов. Технико-экономический эффект целесообразно оценивать по критерию себестоимости единицы продукции с учетом затрат на владение. Для расчета такого критерия необходима исходная информация, которую можно получить путем мониторинга. При минимуме критерия имеет место ограничение по времени выполнения и по качеству работы. Рассмотрена возможность реализации ограничения по времени выполнения работы, которое во многом зависит от времени транспортных операций машин. Транспортные операции, в свою очередь, определяются уровнем устойчивости. Поэтому для разработки рекомендаций по сокращению времени транспортных операций необходима оценка устойчивости с помощью специальных расчетов формул. Рассмотрены разные варианты расчета, выбран вариант составления дифференциальных уравнений раскачивания. Отмечено, что лучше всего рабочий процесс описывается грузовыми диаграммами, поэтому именно их необходимо строить на базе дифференциальных уравнений. Рассмотрен пример построения грузовых диаграмм для ковшевого фронтального погрузчика. Дано описание использования грузовых диаграмм для составления рекомендаций по сокращению времени транспортных перемещений
Система мониторинга, эффективность, устойчивость, время транспортного перемещения, технический аудит, критерий эффективности
Короткий адрес: https://sciup.org/14250211
IDR: 14250211 | DOI: 10.12737/19694
Текст научной статьи Оценка динамической устойчивости в мониторинговой системе управления технико-экономической эффективностью дорожных машин
Введение. Анализ существующих систем мониторинга эффективности дорожных машин выявил факт регистрации технических показателей без учета экономических данных [1]. Нет сведений о наличии аналитического центра, в котором могли бы производиться расчеты по специализированным методикам. Таким образом, существующие мониторинговые системы не обладают функционалом количественной оценки технико-экономической эффективности, что препятствует оценке вводимых мероприятий. В частности, невозможно оценить чувствительность систем машин по показателям экономии денежных средств к вводимым управляющим воздействиям.
Для заданных условий эксплуатации наилучшей будет машина, при помощи которой можно выполнить задачу с наименьшими затратами (показатель 1) за приемлемые сроки (показатель 2) при приемлемом качестве (показатель 3). Каждый из трех перечисленных показателей можно использовать в качестве критерия. Однако недостаточность исходной информации создает известные проблемы при использовании этого критерия. Поэтому величину затрат целесообразно оценивать в соизмерении с работой при помощи удельной величины — себестоимости единицы продукции с учетом затрат на владение (СЕПВ). Такой подход позволяет использовать результаты оценки при выполнении технического аудита в качестве инструмента для выявления направлений развития эксплуатационного предприятия или производства (см., например, [2–5]).
Все три показателя не могут одновременно достичь экстремума, поэтому часть из них целесообразно ограничить. Из перечисленных трех показателей только один (СЕПВ) позволяет оценивать прибыль — наиболее значимый фактор при определении эффективности. Соответственно, в качестве целевой функции целесообразно выбрать минимизацию СЕПВ.
Итак, при мониторинге технико-экономической эффективности дорожных машин будут учитываться в качестве основных:
— целевая функция — минимум СЕПВ,
-
— ограничение — показатель (параметр) времени выполнения работы,
-
— ограничение — показатель (параметр) качества работы.
Исследовательская часть. Рассмотрим, как можно реализовать ограничение по времени выполнения работы, оказывающее прямое влияние на производительность машины. При этом время выполнения работы во многом зависит от времени транспортных операций машин. Рекомендации о коррекции времени транспортных перемещений формируются с учетом оценки устойчивости машин, для чего используются расчетные зависимости, составляемые на базе расчетных схем.
Перемещение дорожных машин при выполнении рабочих операций приводит к изменению нагрузок на опорные конструкции, что обусловлено перераспределением статических сил и возникновением динамических нагрузок.
Нулевое значение нагрузки на опорной конструкции способствует раскачиванию машины вокруг оси, называемой ребром опрокидывания. При раскачивании возникает опасность «перехода» равнодействующей сил тяжести за ребро опрокидывания. В данном случае опрокидывание неизбежно, даже если действие динамических сил прекращается. Для предупреждения подобных ситуаций необходимы расчеты на устойчивость.
Существуют различные методы определения коэффициента устойчивости. Как правило, при расчетах принимаются во внимание нагрузки от сил тяжести и динамические силы (с помощью коэффициента запаса). Таким образом, можно оценить устойчивость машины на базе диагностических показателей — коэффициентов устойчивости, не предусматривающих возможность учета закона раскачивания.
В последние десятилетия появились компьютерные приложения, позволяющие оценить динамическую устойчивость. Для этого составляется графическая модель и описывающие ее поведение алгебраические и дифференциальные уравнения [6, 7]. Однако они не могут быть интегрированы в аналитический центр мониторинговой системы управления эффективностью без специальных изменений.
В научных работах по исследованию динамики машин и механизмов [8–10] не рассматриваются задачи оценки устойчивости. В работах [11–13] рассмотрены вопросы оценки и повышения устойчивости машин, но их методики направлены на конкретный вид машины, что сужает область использования.
Таким образом, можно обоснованно утверждать, что существует потребность в создании математических моделей, пригодных для введения в программное обеспечение аналитического центра управления эффективностью техники.
Сложность и детализация расчета при моделировании динамики движений элементов рабочего оборудования машин в процессе потери устойчивости зависят от условий исследования [14]:
-
— с определением законов движений всех подвижных элементов (звеньев) рассматриваемой расчетной схемы;
-
— с определением закона движения только опорно-ходового устройства.
В первом случае необходимо составление и решение дифференциального уравнения. Очевидно, что с увеличением числа дифференциальных уравнений возрастает сложность математической модели. Таким образом, второе направление представляется значительно более простым в реализации. В данном случае необходимо задать законы движения по степеням свободы схемы, для которых дифференциальное уравнение не составляется. Однако в общем случае закон движения не известен, задать его можно только укрупненно — соответственно, результаты такого анализа будут менее точными и дадут меньше информации.
Итак, при определении законов движений всех элементов необходимо составить систему дифференциальных уравнений и обеспечить ее решение. Для описания движений машины в одной плоскости нужно составить многозвенный механизм (рис. 1).
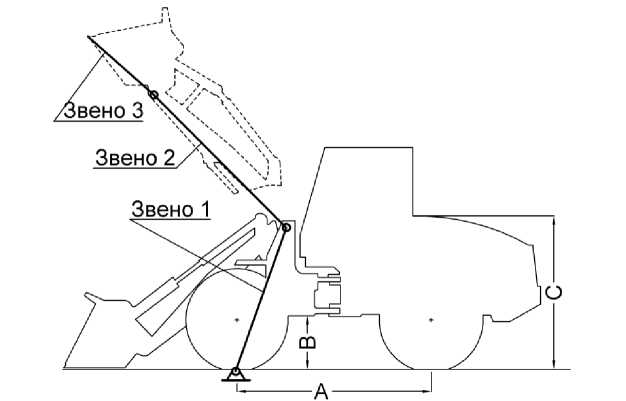
Рис. 1. Схема пневмоколесного фронтального погрузчика с ковшевым рабочим оборудованием
В общем случае схема может состоять из произвольного количества звеньев. Если начать нумерацию звеньев моделирующей схемы (многозвенника) с опорно-ходового устройства, то последнее будет носить номер звена 1 (рис. 1). Соответственно, звенья 2, 3, 4 и т. д. будут моделировать рабочее оборудование. Иными словами, если говорить о фронтальном погрузчике, то звеном 2 будет конструкция подъема ковша, звеном 3 — сам ковш. Звено 1 начинает поворот только при потере устойчивости — раскачивании. У некоторых машин звенья рабочего оборудования (например, рукоять экскаватора-погрузчика) имеют переменную длину.
Звенья можно принять недеформируемыми, поскольку деформируемость не оказывает влияния на устойчивость. Для использования существующих формул необходимо обозначить центры тяжести звеньев и координаты шарниров (рис. 2).
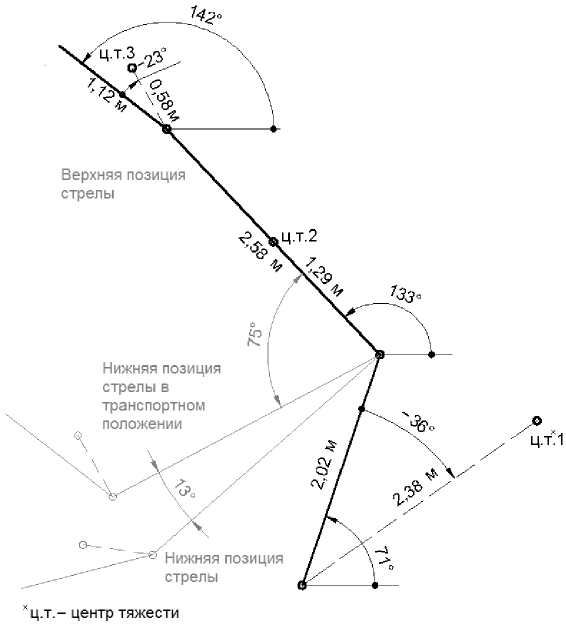
Рис. 2. Параметры моделирующего многозвенника
Машиностроение и машиноведение
В общем случае при составлении динамической расчетной схемы можно предусмотреть возможность изменения длины звена и угловой позиции между последующим и предыдущим звеном. Изменение длины звена происходит с небольшими скоростями и не должно оказывать существенного влияния на устойчивость, поэтому данный фактор можно не вводить в схему. Целесообразно обеспечить возможность поступательного движения всей схемы целиком, моделирующего перемещение шасси. Для упрощения расчетной схемы закон движения можно задать, не составляя дифференциальное уравнение.
Наихудшей рабочей ситуацией является опрокидывание машины. Для расчетной схемы соответствующие условия можно назвать расчетными случаями. Например, для схемы экскаватора таким расчетным случаем будет единовременное торможение стрелы, рукояти и ковша при движении вниз.
Оператор выбирает момент торможения таким образом, чтобы остановка рабочего оборудования произошла по прохождении некоторого пути. Путь характеризуется углом поворота звена и преодолевается за время, которое удобно использовать в качестве характеристики торможения при составлении расчетной схемы. Иными словами, если в реальности оператор контролирует путь торможения, то в расчетной схеме для упрощения зависимостей момент торможения задается в виде конкретной численной величины.
Плечо действия силы от гидроцилиндра относительно оси шарнира в процессе изменения угловой позиции шарнира переменно, поэтому даже при постоянном усилии на гидроцилиндре момент будет меняться в зависимости от угловой позиции. Если пренебречь этим фактом, то момент торможения можно принять постоянным.
На основании изложенного процесс торможения будет характеризоваться постоянной величиной момента торможения, действующего на протяжении некоторого времени торможения. Причем момент торможения является исходной информацией, а время торможения — результатом расчета. При остановке звена его неподвижность обеспечивается соответствующим моментом. Момент торможения конкретных величин прикладывается во всех шарнирах, где присутствуют гидроцилиндры, поэтому в расчетной схеме в общем случае действуют несколько тормозных моментов на протяжении соответствующих отрезков времени.
Опрокидывание можно считать неизбежным, если раскачивание звена 1 (опорно-ходовое устройство) не меняет направления по окончании действия сил инерции. В расчетной схеме действие сил инерции оканчивается с завершением действия последнего из моментов торможения. Если после этого звено 1 меняет направление вращения, то линия действия равнодействующей сил тяжести еще не перешла оси раскачивания и произойдет возврат в исходную позицию. Для решения задачи следует получить зависимость угловых координат всех шарниров схемы от времени, для чего необходимо иметь данные о балансе сил.
На звено схемы действуют [14]:
-
— силы инерции: центробежные, касательные и Кориолисовы — от собственного поворота звена и от поворота предшествующих звеньев;
-
— силы тяжести;
-
— моменты торможения.
Центробежная сила присутствует всегда при наличии вращения и не меняет направления относительно его радиуса. Касательная сила инерции перпендикулярна радиусу вращения, присутствует только при ускорен-ном/замедленном вращении и может менять направление относительно радиуса. Сила Кориолиса присутствует при вращении в случае изменения длины радиуса вращения и может менять направление относительно радиуса. При сравнительно небольших угловых скоростях (именно такие характерны для рабочего оборудования дорожных машин) силы Кориолиса не достигают больших величин, поэтому их влияние в данном случае не учитывается.
Итак, описанная выше расчетная схема предполагает составление математических моделей и учет законов движения в шарнирах. Она реализуется в несколько этапов. Для каждого из звеньев определяются:
-
— численные значения моментов — отдельно для каждой действующей силы;
-
— направления действия моментов для каждой силы;
-
— действующие суммарные моменты;
-
— угловые ускорения, угловые скорости и угловые координаты.
В процессе реализации этих этапов получены математические модели произвольной плоской многозвенной схемы, позволяющей производить оценку устойчивости машин с рабочим оборудованием манипуляторного типа при наличии рабочих движений в одной плоскости [14–15].
В качестве примера реализации описанной расчетной схемы и математических моделей рассмотрим устойчивость фронтального ковшевого погрузчика массой 7770 кг с характеристиками: А = 2,6 м, В = 0,62 м, С = 2,08 м (рис. 1) [15]
В проспекте отсутствуют данные о позициях центров тяжести и массах отдельных элементов. Принятые в связи с этим допущения делают расчетную схему соответствующей оригиналу лишь с некоторой степенью точности.
— Центр тяжести базового шасси расположен на расстоянии 0,75А от оси переднего колеса по горизонтали и на расстоянии (В + С) / 2 по вертикали. Здесь А — колесная база, В — дорожный просвет, C — высота по капоту (рис. 1).
— Центр тяжести стрелы находится на половине расстояния от оси вращения стрелы до оси вращения ковша.
— Масса рабочего оборудования (стрела и ковш) составляет 15 % от общей массы машины.
На основании допущений масса машины без рабочего оборудования равна 85 % от общей массы. Масса рабочего оборудования (стрелы и захвата) равна 15 % от общей массы. В таком случае для погрузчика:
— масса машины без рабочего оборудования (звено 1, рис. 1, 2) составит 7770 · 0,85 = 6604,5 кг;
— масса рабочего оборудования (звено 2) составит 7770 · 0,15 = 1165,5 кг.
Ковш при вращении стрелы занимает горизонтальную позицию, т. е. может вращаться относительно стрелы, составляя тем самым отдельное звено. В данном случае имеет место 3-звенная схема (рис. 1), состоящая из шасси (звено 1), стрелы (звено 2) и ковша (звено 3). Характеристики данной схемы представлены на рис. 2.
С позиции благоприятности условий для опрокидывания можно выделить следующие расчетные случаи (табл. 1):
-
1) машина неподвижна, стрела с грузом опускается и затормаживается;
-
2) машина замедляется, стрела с грузом опускается и затормаживается;
-
3) машина разгоняется, стрела с грузом опускается и затормаживается.
Таблица 1
Характеристики расчетной схемы к построению грузовых диаграмм для трех расчетных случаев
№ строки |
Учитываемые факторы |
№ расчетного случая |
||
1 |
2 |
3 |
||
Длина звена (м) |
||||
1 |
1 |
2,02 |
||
2 |
2 |
2,58 |
||
3 |
3 |
1,12 |
||
Начальная угловая координата звена (град) |
||||
4 |
1 |
71 |
||
5 |
2 |
133 |
||
6 |
3 |
142 |
||
Радиус центра тяжести звена (м) |
||||
7 |
1 |
2,38 |
||
8 |
2 |
1,29 |
||
9 |
3 |
0,58 |
||
Угловая координата центра тяжести звена (град) |
||||
10 |
1 |
–36 |
||
11 |
2 |
0 |
||
12 |
3 |
–23 |
||
Масса звена (кг) |
||||
13 |
1 |
6604,5 |
||
14 |
2 |
1165,5 |
||
15 |
3 |
Искомая величина |
||
Начальный момент торможения на звене (Н·м) |
||||
16 |
1 |
– |
– |
– |
17 |
2 |
208121,5 |
||
Начальная угловая скорость звена (рад/сек) |
||||
18 |
1 |
0 |
||
19 |
2 |
0,2 |
||
20 |
Угол уклона (град) |
0 |
||
21 |
Ускорение поступательного движения (м/сек 2 ) |
0 |
2 |
–2 |
22 |
Продолжительность действия ускорения (сек) |
0 |
0,5 |
0,5 |
Машиностроение и машиноведение
Третий расчетный случай не так опасен, как второй, введен только для возможности подтверждения адекватности используемой расчетной схемы и математических моделей.
Момент торможения на стреле принят таким (строка 17 табл. 1), чтобы дать остановку за время, меньшее 1
секунды.
Одним из наилучших вариантов описания возможностей прямого функционального назначения для рассматриваемого типа машин является грузовая диаграмма (рис. 3). Рабочее оборудование не имеет возможности удлинения, поэтому грузовая диаграмма представлена одной кривой, каждой угловой позиции стрелы в зависимости от расчетно- го случая соответствует своя грузоподъемность.
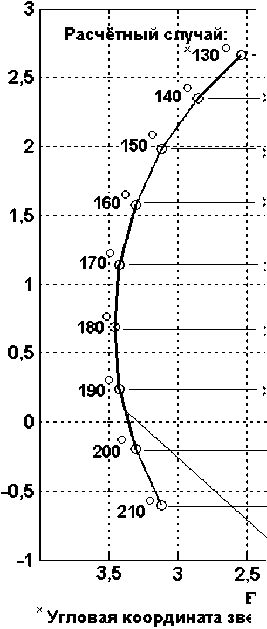
---более 4000
>4000: 3800
3 кг
>4000
>40OT:’360ff:’>40U0:
>4000: 3600
>4000: 3600
>4000: 3600
>4000; 3800
более 4000
более 4000
>4000
>4000
>4000
кг
>4000; ;
Ось вращения стрелы __---~~-~
кг
Траектория режущей кромки ковша
1,5
0,5 0
Вылет ковша, м ена2-стрелы
Рис. 3. Грузовая диаграмма ковшевого погрузчика для расчетных случаев 1–3
Максимальная грузоподъемность рассматриваемой машины принята равной 4000 кг. Как видно из диаграммы, максимальная грузоподъемность для рассматриваемых случаев определяется не устойчивостью, а, скорее, прочностными возможностями рабочего оборудования. Только для расчетного случая 2 (замедленное движение шасси) максимальная грузоподъемность меньше 4000 кг.
Процессы торможения протекают в короткие отрезки времени (менее 1 сек), что зависит от момента торможения на стреле (строка 17 табл. 1) и определено продолжительностью действия ускорения поступательного движения (строка 22 табл. 1). Именно для этих мгновений справедливы грузовые диаграммы на рис. 3. В остальное время грузоподъемность из условий устойчивости будет только выше.
Обсуждение и результаты. Результаты расчетов позволяют выявить предельные ускорения движения стрелы и шасси. Таким образом, можно определить предельные кинематические характеристики движения рабочих органов машины с учетом принципиальной возможности выполнения поставленной задачи из условий устойчивости и прочности рабочего оборудования. Далее необходимо на базе предельных кинематических характеристик движения назначить величины повышения аналогичных характеристик для остальных элементов рабочего цикла, занимающих большую часть времени работы машины. Такое повышение возможно в рамках систем автоматизированного управления, что определяет их актуальность, т. к. деятельность оператора не влияет на соответствующие показатели.
Информацию о возможности повышения кинематических характеристик следует передать по каналу обратной связи мониторинговой системы управления эффективностью.
Выводы.
-
1. В качестве критерия эффективности в мониторинговой системе можно использовать себестоимость единицы продукции с учетом затрат на владение с ограничениями по показателю (параметру) времени выполнения работ и показателю (параметру) качества работы.
-
2. Для машин с оборудованием манипуляторного типа время выполнения работы во многом зависит от кинематических характеристик транспортных операций, ограниченных устойчивостью против опрокидывания.
-
3. Для оценки устойчивости нужны математические модели, составляемые на базе расчетных схем с определением: законов движений всех подвижных элементов (звеньев) рассматриваемой расчетной схемы и закона движения только для опорно-ходового устройства.
-
4. Из результатов расчетов для режимов торможения при совершении транспортных операций выявляются предельные ускорения движения оборудования и шасси, на базе которых можно назначить величины повышения кинематических характеристик для остальных элементов транспортных операций.
-
5. Информацию о возможности повышения кинематических характеристик (в системе автоматизированного управления рабочим оборудованием машин) необходимо передать по каналу обратной связи мониторинговой системы управления эффективностью.
Список литературы Оценка динамической устойчивости в мониторинговой системе управления технико-экономической эффективностью дорожных машин
- Мандровский, К. П. Системы мониторинга дорожно-строительных, транспортных машин и дорожных покрытий/К. П. Мандровский//Интерстроймех-2015: мат-лы междунар. науч.-техн. конф. -Казань, 2015. -С. 310-315.
- Hiwase, P.-D. The Role of Technical Audit in Environmental Impact Assessment/P.-D. Hiwase, N.-S. Raman, H.-V. Hajare//International Journal of Innovative Research in Science, Engineering and Technology. -2013. -Vol. 2 (3). -P. 664-669.
- Srivastava S. B. Technical Audit -A Throughfare of System Perfection/S. B. Srivastava//International Journal of Scientific & Engineering Research. -2012. -Vol. 3 (1). -P. 98-110.
- Вокина, Е. Б. Основы промышленного и технического аудита/Е. Б. Вокина//Вестник транспорта Поволжья. -2011. -№ 5 (29). -С. 21-27.
- Палкин, С. В. Технический аудит в системе менеджмента/С. В. Палкин//Железнодорожный транспорт. -2009. -№ 4. -С. 38-42.
- EULER. Программный комплекс автоматизированного динамического анализа многокомпонентных механических систем /ЗАО «Автомеханика». -Режим доступа: http://www.euler.ru/(дата обращения: 28.07.15).
- Simulink. Графическая среда имитационного моделирования /Softline. -Режим доступа: http://matlab.ru/products/simulink (дата обращения: 28.07.15).
- Алексеева, Т. А. Математическое моделирование случайных дорожных возмущений при исследовании динамики мобильных машин/Т. А. Алексеева//Науч.-техн. ведомости Санкт-Петербург гос. политехн. ун-та. Физ.-мат. науки. -2015. -№ 2 (218). -С. 118-122.
- Жулай, В. А. Динамика дефектных карданных передач строительных и дорожных машин/В. А. Жулай, В. А. Козлов, А. Н. Щиенко//Изв. высш. учеб. заведений. Строительство. -2008. -№ 1. -С. 72-78.
- Ли, С. В. Динамика многороторных рабочих органов строительно-дорожных машин/С. В. Ли, Г. М. Ахметов, М. Н. Есенгалиев//Труды университета/Карагандинский гос. техн. ун-т. -2007. -№ 3. -С. 67-68.
- Плиев, С. Х. Расчет двухосной колесной машины на устойчивость против опрокидывания/С. Х. Плиев//Изв. Горского гос. аграрн. ун-та. -2015. -Т. 52, № 1. -С. 124-127.
- Прохорова, Е. В. Методика оценки устойчивости экскаватора, оборудованного быстросоединительным устройством/Е. В. Прохорова//Инновационные материалы, технологии и оборудование для строительства современных транспортных сооружений: междунар. науч.-практ. конф./Белгородский гос. техн. ун-т им. В. Г. Шухова. -Белгород, 2013. -Т. II. -С. 180-185.
- Плиев, С. Х. Расчет статической и динамической устойчивости трициклов/С. Х. Плиев, Т. Т. Агузаров//Изв. Горского гос. аграрн. ун-та. -2014. -Т. 51, № 4. -С. 216-225.
- Мандровский, К. П. Динамика и математическое моделирование движений машин при оценке устойчивости/К. П. Мандровский. -Москва: МАДИ, 2012. -72 с.
- Мандровский, К. П. Моделирование и оценка устойчивости самоходных машин/К. П. Мандровский. -Saarbrucken: LAP LAMBERT Academic Publishing, 2012. -85 c.