Оценка износостойкости монолитных подошв обуви из термоэластопластов
Автор: Буркин А.Н., Нейфельд М.А.
Журнал: Вестник Витебского государственного технологического университета @vestnik-vstu
Рубрика: Технология материалов и изделий текстильной и легкой промышленности
Статья в выпуске: 4 (50), 2024 года.
Бесплатный доступ
Износостойкость подошв является одним из важнейших эксплуатационных свойств обуви. На это свойство оказывает влияние ряд факторов: сырьевые материалы, параметры технологического процесса производства подошв, условия хранения и эксплуатации обуви и т. д. Каждый фактор в отдельности и их сочетание приводят к изменениям характеристик готового изделия, что вызывает необходимость оценки износостойкости обуви или деталей низа обуви. В статье была рассмотрена проблематика испытания современных подошв с глубоким рифлением протектора, на примере тэрмоэластопластов (ТЭП). Целью исследования являлась разработка методики исследования современных подошвенных материалов, имеющих рифления различной глубины, по показателю сопротивление истиранию при скольжении. Методы исследования - стандартные методики оценки физико - механических полимерных подошвенных материалов. В результате работы предложена усовершенствованная методика испытания по показателю сопротивление истиранию, которая включает в себя новый подход к подготовке образцов, позволяющий проводить испытания подошв с глубоким рифлением, и рекомендации по процедуре испытания, а именно смена положения образцов через каждые 2,5 минуты. Разработанная методика легко воспроизводима в лабораторных условиях и не противоречит стандартной методике.
Подошвы, свойства, методика, современный ассортимент, оценка износостойкости, прибор ми-2
Короткий адрес: https://sciup.org/142244110
IDR: 142244110 | DOI: 10.24412/2079-7958-2024-4-37-48
Текст научной статьи Оценка износостойкости монолитных подошв обуви из термоэластопластов
УДК 685.34.073.22 DOI:
Защита стоп, обеспечение безопасности и комфорта ношения обуви наиболее актуальная задача проектирования и производства современной обуви. Она обеспечивает повышение производительности во время различных видов деятельности. Касаемо безопасности и производительности труда, важно, чтобы обувь обеспечивала эффективное сцепление с грунтом в любой ситуации (In-Ju Kim, 2016).
Целью исследования являлась разработка методики исследования современных подошвенных материалов, имеющих рифления различной глубины, по показателю сопротивление истиранию при скольжении.
Износ подошв, подмёток, каблуков или набоек обуви проявляется в уменьшении их толщины. Изнашивание в этом случае сводится к последовательному механическому разрушению поверхностных слоёв вследствие относительного перемещения подошв по опорной поверхности. Главным фактором, непосредственно обуславливающим износ, является контакт низа обуви с опорной поверхностью.
Оценка комфорта – это важный критерий в разработке любого товара, особенно товара, который характеризуется многократным и длительным использованием, например, обувь. А одним из важнейших компонентов обуви является подошва, дизайн которой основан на многих факторов, таких как размер и форма (Pasquale Franciosa, Salvatore Gerbino, Antonio Lanzotti and Luca Silvestri, 2013).
Толщина подошвы определяет оригинальность обувной пары. Утолщённая подошва соответствует повседневной обуви, спортивному стилю или креативному образу. В последнее время среди молодых людей грубая обувь на объёмной подошве пользуется невероятным успехом (Е. Ванга, 2021). Обувь с так называемой «тракторной» подошвой впервые появилась в 70-е годы, когда популярность приобрели всевозможные неформальные молодёжные направления и течения. Оставили они свой отпечаток не только в культуре, но и в истории моды в виде таких новаторских на то время идей, как туфли и сапоги на толстой, внешне нарочито грубой, риф- леной платформе1. Такая подошва – это один из модных трендов, который не теряет популярности уже несколько лет, свою популярность она получила в 2015 году и согласно интернет-источникам2, является трендом сезона 2024/2025.
Непременным атрибутом такой подошвы является рифление. Оно может имитировать рельеф протекторов шин и иметь фигурные очертания, такие как зубцы, волны и др. Эти элементы могут быть массивными или мелкими, грубыми или изящными3. Расположение элементов на ходовой части подошв не регламентируется никакими стандартами. Приоритет при разработке рельефа отдаётся дизайнерским решениям и, как правило, выполняется без учёта фрикционного взаимодействия подошв с опорной поверхностью (В.А. Харина, 2022).
Условно, по высоте рифления, подошвы можно разделить на следующие группы (А.В. Подкопаева, Ю.С. Конарева, 2019):
-
– высокое (8–9 мм) правильно подобранное расположение рифов может обеспечить хорошее сцепление с загрязнённой поверхностью;
-
– среднее (4–7 мм) подходит для твёрдых грунтов, камней, лесных и горных троп в сухую погоду;
-
– низкое (1–3 мм) используется при носке обуви по жёстким твёрдым поверхностям и плохо держит сцепление на грязной поверхности;
-
– нулевое рифление представляет собой ложбинки между разными секциями подошв.
Несмотря на большое разнообразие материалов, и конструктивных особенностей (фасонов) обуви, её идентификационные признаки могут быть сведены в единую классификацию: групповые и индивидуальные признаки.
К групповым признакам относят: конструкцию подошвы, фасон подошвы, фасон каблука, размер низа обуви и её частей, форму подошвы и её частей, общую характеристику поверхности подошвы и её частей и др.
К индивидуальным признакам, возникающим при изготовлении обуви, относят: дефекты, обусловленные случайными причинами, их форму и положение относительно срезов и деталей рельефных рисунков подошв (А.А. Байбарин, О.Ю. Локтионова, 2017).
Материал и средства исследований
Термоэластопласты обладают большой популярностью при производстве обуви. На крупнейших предприятиях Республики Беларусь около 50–60 % обуви производятся на подошвах из ТЭП (М. А. Козлова, А.Н. Радюк, К.О. Бужинская, 2022).
Образцы современных подошв мужского и женского ассортимента из монолитных термоэластопластов, применяемых на обувных предприятиях, представлены на рисунке 1. На рисунке также представлены схематичные
-•
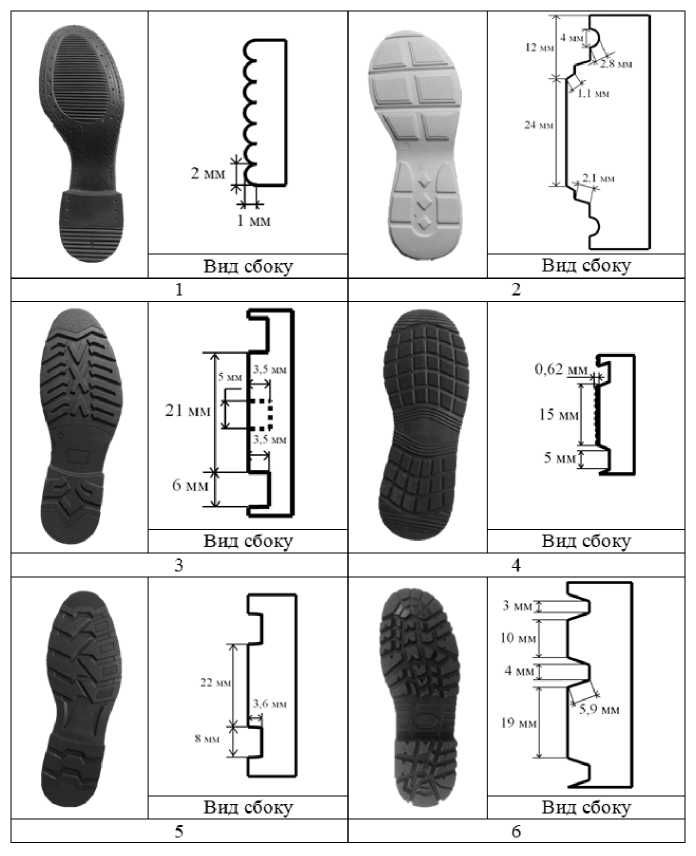
Рисунок 1 – Современный ассортимент подошв Figure 1 – Current assortment of soles
фрагменты вида сбоку рифления пучковой зоны подошв с размерами.
Данные подошвы использовали при производстве обуви осенне-весеннего сезона 2023/2024, образцы 1, 2 для женского ассортимента, 3–6 – для мужского. Они отличаются друг от друга, имеют разную глубину рифления. Образцы 1 – коричневого цвета; 2 – бело-бежевого; 4 – черно-белого; 3, 5, 6 – чёрного цвета.
В данный момент нет рекомендаций в технических нормативных правовых актах (ТНПА), которые бы учитывали ассортиментное разнообразие подошвенных материалов по такому признаку, как состав, поэтому стандарты на методы испытаний и требования по физико-механическим испытаниям берутся на резины для низа обуви, как на наиболее близкого аналога.
Для испытаний были отобраны по 6 пар подошв и определены их физические свойства, представленные в таблице 1. Выбор данных свойств обусловлено тем, что они могут измеряться неразрушающим методом. По определённым показателям плотности можно с уверенностью сказать, что испытуемые образцы имеют монолитную структуру.
Согласно литературным источникам свойства монолитных тэрмоэлстопластов находятся в пределах 0,9–1,1 г/см3 по показателю плотность, по твёрдости в пределах 50–75 усл.ед.
Испытания подошв проводили по ГОСТ 7926-75 «Резина для низа обуви. Методы испытаний», который устанавливает методы испытаний для подошвенных пластин и деталей низа обуви. В текстовой части стандарта не учитывается современное разнообразие подошв, с точки зрения глубины рифления и устанавливает схему вырубки образцов для проведения физико-механических испытаний гладких и мелкоузорчатых (мелко рельеф- ных) деталей для низа обуви.
Так для испытания подошв по показателю сопротивление истиранию стандарт устанавливает вырубку образцов из носочной и пяточной части в определённых местах (рисунок 2).
Основной проблемой испытания подошв можно считать то, что полимерные образцы, представленные для испытания на трение, не всегда имеют гладкую поверхность и однородную толщину или могут не подходить для испытания на заявленном оборудовании (D.I. James, R. Mohsen, 1982).
Сравнив рисунок 1 и 2 отметим, что далеко не все образцы можно раскроить по данной схеме, ввиду их сложного рельефного строения подошвы, учитывая то, что габаритные размеры образцов 28 на 20 мм.
Испытание по показателю сопротивление истиранию проводят по ГОСТ 426-77 «Резина. Метод определения сопротивления истиранию при скольжении». Сущность метода заключается в истирании образцов, прижатых к абразивной поверхности вращающегося диска, при постоянной нормальной силе и последующем определении показателей сопротивления истиранию (А.Н. Радюк, Е.А. Колальчук, А.Н. Буркин, 2022).
Для данного метода используются образцы Т-образной формы. В связи с тем, что образцы подобной конфигурации затруднительно вырезать, а из некоторых подошв и невозможно в виду: сложного рифления с ходовой и внутренней части подошв; малой общей толщины подошвы и др. Указанное выше привело к разработке нового подхода подготовки образцов к испытанию. Формованные подошвы имеют разную толщину на отдельных участках. В частности, в подошве для клеевого метода крепления толщина в передней части должна быть не менее 4,0–4,5 мм, геленочной части – 3,5 мм. Согласно
Таблица 1 – Физические свойства образцов подошв
Table 1 – Physical properties of the soles samples
№ образца |
Плотность г/см3 |
Твёрдость, усл.ед. |
1 |
0,98–0,99 |
70–74 |
2 |
1,24–1,25 |
58–63 |
3 |
1,15–1,16 |
61–67 |
4 |
1,10–1,12 |
61–66 |
5 |
1,05–1,06 |
64–67 |
6 |
1,08–1,09 |
72–77 |

Рисунок 2 – Места для вырубки образцов Figure 2 – Places for cutting samples источнику (В.Х. Лиокумович, 1975) при наличии рисунка на ходовой стороне толщина подошвы может быть уменьшена, требованиям к высоте (толщине) рифления не представлены. Следовательно, имея рельеф высотой 2 мм, мы можем уменьшить толщину подошвы. Представления о процессе носки и влияния атмосферных условий говорят о том, что нельзя уменьшать основную толщину. Рельеф, размером 2 мм, достаточно быстро износится в зонах повышенной нагрузки (в пучковой и пяточной части), а оставшаяся общая толщина примет на себя основную нагрузку, приводя к повышенному риску прокола и попадания влаги во внутреннее пространство обуви и ещё большему уменьшению толщины подошвы. Данные факторы приведут к разрушению обуви, как с внутренней части (попадающая влага), так и с наружной части (сквозное протирание подошвы).
Особенность подготовки заключается в следующих этапах:
-
1. Вырубка образцов из подошв. Для этого использовался штанцевый резак или обувной нож для выкройки образца 20x20 мм из мест ходовой поверхности подошв, где это возможно (кроме геленочной части). Из каждой полупары вырубалось по три образца, согласно местам раскройки предлагаемой рисунком 2, симметрично вырезанным образцам из одной полупары, вырубались образцы из другой. Толщина испытуемых образцов была разной для каждой зоны (таблица 2). В этой и последующих таблицах приводятся средние значения показателей. Объём выборки составлял 12 образцов для каждого вида подошв.
-
2. Подшлифовка полученных образцов для последующего склеивания. Данная операция необходима для получения равномерной шероховатой внутренней поверхности образца. Целесообразно оставить рабочую толщину образца не менее 5 мм. Подшлифовку можно проводить вручную, на испытательном оборудовании
-
3. Вырубка и подготовка подложки для образца. Для этого использовался обувной стелечный картон толщиной от 1 до 2 мм и с помощью обувного ножа или ножниц вырезают образец 28x20 мм. В случае, если рабочая толщина меньше 5 мм, необходимо подобрать картонную подложку необходимой толщины размером 20x20 мм.
-
4. Склейка образцов. Если рабочая толщина образца менее 5 мм, первоначально склеивают образец с картоном 20x20 мм, подходящей толщины, используя клей полиуретановый и кисть с натуральной щетиной. Если толщина 5 и более миллиметров, то образец подшлифованной стороной приклеивают на картон размером 28 на 20 мм. Полученные образцы склеивают. Испытания образцов проводятся через сутки. Полученные варианты образцов представлены на рисунке 3.
б (b)
в (c)
Рисунок 3 – Схемы образцов для испытания:
а – по ГОСТ 426-77; б – с рабочей толщиной менее 5 мм; в – с рабочей толщиной 5 и более мм;
1 – испытуемый образец; 2 – стелечный картон
Figure 3 – Diagrams of samples for testing:
a – according to GOST 426-77; b – with a working thickness of less than 5 mm;
c – with a working thickness of 5 mm or more; 1 – the test sample; 2 – shelving cardboard
-
5. Кондиционирование образцов проводится по ГОСТ 12423-2013 «Пластмассы. Условия кондиционирования и испытания образцов (проб)» при следующих условиях: температура воздуха – 23 °С, относительная влажность – 50 %.
Таблица 2 – Толщина испытуемых образцов
Table 2 – Thickness of the test samples
№ образца |
Толщина, мм |
Зона выкройки |
№ образца |
Толщина, мм |
Зона выкройки |
1 |
4,4 |
Носок |
4 |
4,4 |
Пятка |
4,7 |
Носок |
4,4 |
Пятка |
||
6,5 |
Пятка |
6,0 |
Носок |
||
2 |
4,7 |
Пятка |
5 |
3,8 |
Носок |
4,5 |
Носок |
3,9 |
Носок |
||
4,8 |
Пятка |
5,2 |
Пятка |
||
3 |
4,3 |
Носок |
6 |
9,3 |
Носок |
4,1 |
Носок |
8,7 |
Пятка |
||
5,3 |
Пятка |
9,0 |
Пятка |
Зоны выкройки в образцах не однообразны, это связано с разнообразием рельефа каждого конкретного образца.
Как видно из таблицы в большинстве случаев толщина носочной части меньше толщины пяточной части. Это связано с тем, что при ходьбе на пятку приходится наибольшая нагрузка. Для повышения износостойкости пяточной части и минимизации скольжения на ходовой стороне подошвы должен быть рисунок (рельеф). Исключениями являются образец 4, за счёт высокого рифления носочной части и образец 6, где толщина на всей длине практически одинаковая.
(с помощью специального приспособления с ячейками для размещения образцов) или наждачном круге.
Полученные образцы взвешивают. Необходимо отслеживать относительную влажность лабораторного помещения, так как её изменение может исказить результаты испытания: массу образцов. Влажность никак не повлияет на полимерный материал, но резкое изменение влажности окружающей среды, может повлиять на массу картонов, используемых при испытании.
Согласно ГОСТ 426-77 допускается дублирование образцов. Истираемая часть образцов должна выступать из рамок-держателя на (3,5±0,5) мм. Количество испытуемых образцов должно быть не менее шести (три пары).
Испытания по показателю сопротивление истиранию при скольжении в странах СНГ в основном проводят на приборе МИ-2, схема прибора представлена на рисунке 4. Только для данного метода имеются нормируемые значения по износу полимеров, установленные в ГОСТ 10124-76 «Пластины и детали резиновые непористые для низа обуви» и которые составляют не менее 2,5 Дж/мм3.
На приборе МИ-2 два образца 5, закреплённые на рычаге 2, прижимаются к шлифовальному полотну 4, прикрепленному к вращающемуся диску 3. Рычаг имеет ось 2, помещённую в полном валу диска 3. К шлифовальному полотну образцы прижимаются силой, создаваемой грузом 1, соединенным гибкой тягой с осью 2. На рычаге 6 подвешивается груз 7, уравновешивающий силу трения и удерживающий рычаг в горизонтальном положении (Б.Я. Краснов, 1988).
Согласно ГОСТ 426-77 материалом, истирающим резину, должна быть шлифовальная шкурка по ГОСТ 344 марки П2 44А КМ-1 с истирающей способностью 45–80 м3/ТДж (160–300 см3/кВт∙ч). Согласно переводу зернистости шлифовального полотна по ГОСТ Р 52381-2005 «Материалы абразивные. Зернистость и зерновой состав шлифовальных порошков. Контроль зернового состава» – современное обозначение необходимого шлифовального полотна Р 180. В связи с тем, что данная шлифовальная шкурка достаточно гибкая, во избежание её заломов во время испытания, было принято решение с помощью двухсторонней липкой ленты приклеивать на плотный картонный диск.
Испытания проводили при температуре помещения (23±2) °С.
Шлифовальную шкурку закрепляют на диске прибора. Помещают два образца в рамки держатели и прикладывают к ним нормальную силу, равную 26 Н. Необходимо провести стабилизацию шкурки не менее
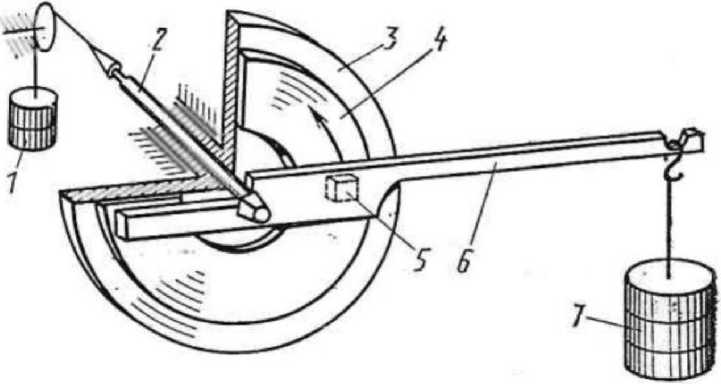
Рисунок 4 – Схема прибора МИ-2
Figure 4 – Diagram of the MI-2 device
15 минут и провести притирку образцов до появления износа на всей поверхности их контакта. Согласно ГОСТ 426-77 допускается совмещение процессов стабилизации шлифовальной шкурки и притирки образцов.
Притёртые образцы освобождают из рамок-держателей, очищают от бахромки и пыли и взвешивают на аналитических весах с погрешностью ±0,01 или ±0,001 г.
Притёртые образцы закрепляют в рамках-держателях и прикладывают к ним нормальную силу, равную 26 Н.
Результатом испытания является расчёт показателя сопротивление истиранию Дж/мм3 по формуле:
р=^-к, (1)
где A – работа трения в Дж; K – коэффициент, учитывающий истирающую способность шлифовальной шкурки; ∆ V – убыль объёма резины в мм3, рассчитываемая по формуле:
ДУ = 1Q9 Cmi ~ m2) "' P
,
где m1 – масса двух образцов до испытания, кг; m2 – масса двух образцов после испытания, кг; ρ – плотность образца, кг/м3.
Согласно методике, изложенной выше, испытание образцов проводят непрерывно в течение 5 минут, закреплённых в держателях в том же положении, что и при притирке образцов. При таких испытаниях абразивные частицы, двигаясь по одной траектории, прорезают образец в одних и тех же местах, оставляя дугообразные полосы на образцах. Для более равномерного износа предложено через каждые 2,5 минуты менять образцы местами в рамках-держателях, тем самым изменяя и последующую траекторию резанья материала абразивом. Характер износа после 2,5 минут и после 5 минут представлен на рисунке 5.
Это позволит минимизировать возможную неравномерность испытания образцов, при котором абразивные частицы хаотично взаимодействуют с поверхностью подошв.
Результаты исследований
По представленной методике были проведены испытания, с измерением массы (в граммах) и толщины (в мм) полимерного образца каждые 2,5 минуты, предполагая, что в процессе испытаний изменяется только масса ТЭП. Результаты измерений представлены в таблице 3.
В результате статистической обработки экспериментальных данных установлена линейная зависимость
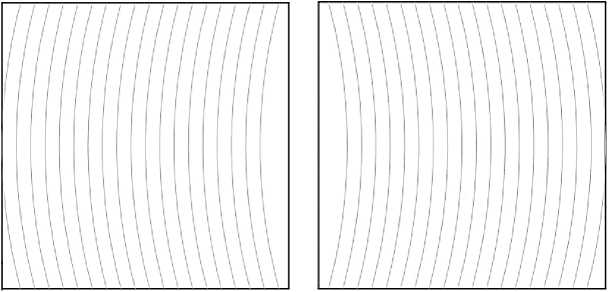
а б (b)
Рисунок 5 – Характер износа образцов:
а – образец с левой стороны после 2,5 минуты; б – образец с правой стороны после 2,5 минуты; в – образцы после 5 минут испытания
Figure 5 – The wear pattern of the samples:
a – the sample on the left side after 2,5 minutes; b – the sample on the right side after 2,5 minutes;
c – the samples after 5 minutes of testing
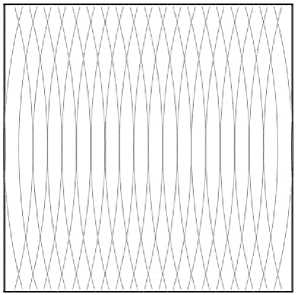
в (c)
с коэффициентами достоверности аппроксимации по массе 0,97–0,99, по толщине – 0,98–0,99. Обобщённые результаты испытания приведены в таблице 4.
Сопротивление истиранию подошв обуви зависит от геометрических параметров подошвы (A. Ishizako, T. Nishi, T. Yamaguchi, 2024), таких как направление, ширина, глубина канавок протектора (Mark G. Blanchette, and Christopher M. Powers, 2015), соотношение длины и ширины блоков протектора, видимая площадь контакта и твёрдость блоков протектора, топография поверхности (T.Yamaguchi, T. Umetsu, Y. Ishizuka, K. Kasuga, T. Ito, Ishizawa S. and K. Hokkirigawa, 2012).
Анализ результатов
Во время испытания в течение 15 минут разрыв поверхности образцов не наблюдался. Все полученные данные удовлетворяют требованиям стандарта ГОСТ 10124-76 «Пластины и детали резиновые непористые для низа обуви».
Таблица 3 – Кинетика износа во время испытания
Table 3 – Kinetics of wear during the test
№ образца |
Начальные значения |
Время, минуты |
||||||||
2,5 |
5 |
7,5 |
10 |
12,5 |
15 |
17,5 |
20 |
|||
1 |
масса, г |
3,23 |
3,05 |
2,85 |
2,65 |
2,46 |
2,44 |
2,10 |
- |
- |
толщина, мм |
5,2 |
4,6 |
4,1 |
3,6 |
3,1 |
2,5 |
2,1 |
- |
- |
|
2 |
масса, г |
3,33 |
3,15 |
2,95 |
2,78 |
2,60 |
2,44 |
2,26 |
- |
- |
толщина, мм |
4,4 |
4,0 |
3,6 |
3,3 |
2,8 |
2,5 |
2,1 |
- |
- |
|
3 |
масса, г |
3,36 |
3,19 |
3,00 |
2,83 |
2,66 |
2,49 |
2,32 |
2,21 |
- |
толщина, мм |
4,5 |
4,0 |
3,6 |
3,2 |
2,9 |
2,5 |
2,1 |
1,8 |
- |
|
4 |
масса, г |
3,06 |
2,85 |
2,69 |
2,50 |
2,36 |
2,17 |
2,03 |
1,88 |
- |
толщина, мм |
4,9 |
4,2 |
3,7 |
3,2 |
2,8 |
2,5 |
2,1 |
1,7 |
- |
|
5 |
масса, г |
3,03 |
2,88 |
2,75 |
2,58 |
2,45 |
2,28 |
2,14 |
2,02 |
- |
толщина, мм |
4,2 |
3,8 |
3,5 |
3,1 |
2,7 |
2,4 |
2,0 |
1,6 |
- |
|
6 |
масса, г |
4,21 |
4,02 |
3,74 |
3,68 |
3,50 |
3,31 |
3,14 |
2,96 |
2,78 |
толщина, мм |
9,1 |
8,4 |
7,9 |
7,3 |
6,8 |
6,3 |
5,9 |
5,5 |
4,9 |
Примечание: знак «-» обозначает разрушение одного образца из массива.
Таблица 4 – Результаты испытания по показателю сопротивление истиранию
Table 4 – Test results for abrasion resistance
Номер образца |
Масса после притирки образцов, г |
Масса после 5 минут испытания, г |
Разность масс, г |
Убыль объёма, мм3 |
Сопротивление истиранию, Дж/мм3 |
1 |
2,85 |
2,10 |
0,75 |
762 |
2,86 |
2 |
2,95 |
2,26 |
0,69 |
554 |
3,88 |
3 |
3,00 |
2,32 |
0,68 |
587 |
3,63 |
4 |
2,69 |
2,03 |
0,66 |
594 |
3,62 |
5 |
2,75 |
2,14 |
0,61 |
585 |
3,68 |
6 |
3,86 |
3,14 |
0,73 |
672 |
3,19 |
В некоторых литературных источниках представлены зависимости износостойкости резины от физических свойств (Н.Д. Закатова, Е.Я. Михеева, 1966). В таблице 5 приведена сводная таблица значений по следующим показателям: плотность, твёрдость, сопротивление истиранию. Проведена сортировка таблицы по показателю сопротивление истиранию от минимума к максимуму.
Как видно из таблицы, имеется зависимость (коэффициент корреляции 0,67) между показателями твёрдость и сопротивление истиранию, а между показателями сопротивление истиранию и плотностью такой взаимосвязи нет (коэффициент корреляции 0,03). Можно заметить, что образцы с малой плотностью и высокой твёрдостью имеют низкое сопротивление истиранию по сравнению с другими образцами и наоборот, образец с самой высокой плотностью и самими низкими показателями по твёрдости имеют более высокое значение по показателю сопротивление истиранию. В источнике (Н.Д. Закатова, Е.Я. Михеева, 1966) отмечено, что при одинаковой устойчивости к истиранию, резины с большей твёрдостью менее устойчивы к износу в эксплуатации.
Учитывая то, что в структуре ТЭП имеется эластомерная составляющая это позволит в дальнейшем оценивать её вклад при исследовании и прогнозировании ресурса подошв по схеме: «состав – свойства».
Выводы
Разработанная усовершенствованная методика позволяет испытывать современный ассортимент подошв, имеющих сложный и разнообразный рельеф. Проведена апробация данной методики и представлены данные, которые удовлетворяют и не противоречат требованию стандартов. По полученным результатам было установлено, что износ подошвенных материалов из ТЭП монолитной структуры подчиняется линейному закону.
В дальнейшем рекомендуется уменьшить размер образца, с изменением его конфигурации (например, круглые образцы диаметром 16 и 10 мм), что позволило бы более рационально использовать поверхность подошвы для испытаний. Рекомендуем также включать данные притирания в основное испытание, тем самым имитируя износ, протекающий при естественной носке обуви.
Таблица 5 – Сводная таблица
Table 5 – Summary table
Номер образца |
Плотность, г/см3 |
Твёрдость, усл. ед. |
Сопротивление истиранию, Дж/мм3 |
1 |
0,98–0,99 |
70–74 |
2,86 |
6 |
1,24–1,25 |
72–77 |
3,19 |
4 |
1,15–1,16 |
61–66 |
3,62 |
3 |
1,10–1,12 |
61–67 |
3,63 |
5 |
1,05–1,06 |
64–67 |
3,68 |
2 |
1,08–1,09 |
58–63 |
3,88 |