Оценка эффективности гидрогеологической и окружающей среды при подземном блочном выщелачивании металлов из руд
Автор: Ляшенко В.И., Голик В.И., Клюев Р.В.
Журнал: Горные науки и технологии @gornye-nauki-tekhnologii
Рубрика: Разработка месторождений полезных ископаемых
Статья в выпуске: 1 т.7, 2022 года.
Бесплатный доступ
Одним из самых проблемных мест подземного блочного выщелачивания (ПБВ) металлов из руд является возможность загрязнения водной и воздушной среды в зоне их влияния. Поэтому доказательство возможности минимизации последствий ПБВ металлов из руд путем управления технологическими процессами в рамках реализации природо- и ресурсосберегающих технологий актуально. Цель исследования - обоснование эффективности подземной разработки рудных месторождений традиционными и комбинированными технологиями с выщелачиванием металлов из скальных некондиционных и забалансовых руд. Это обеспечит повышение сырьевой базы добычи металлов из забалансовых руд и улучшит охрану недр, гидрогеологической и окружающей среды. Отличительной особенностью ПБВ (подземного участка по выщелачиванию металлов из замагазинированных руд) является то, что выщелачивающие растворы подают из сорбционной колонны, размещенной в горных выработках горизонта орошения в непосредственной близости от эксплуатационного блока. Выдачу продуктивных растворов в виде смолы осуществляют из сорбционной колонны, размещенной в горных выработках горизонта орошения, в вагонетках на дневную поверхность и далее в цистернах на гидрометаллургический завод. Исследованию подвергается пока еще редкий опыт обоснования эффективности и экологической безопасности ПБВ металлов из забалансовых и некондиционных скальных руд в установках, смонтированных в горных выработках, на основании мониторинга и оценки охраны недр, гидрогеологической и окружающей среды. Выявлено усредненное значение концентрации урана по горизонтам: 210 м - 3,6 мг/л; 225 м - 3,58 мг/л; 280 м - 0,91 мг/л. При этом загрязнения подземных шахтных вод не обнаружено. Уровень аэрозолей серной кислоты и продуктов распада радона не превышал значений предельно-допустимой концентрации. Рекомендовано охрану гидрогеологической среды производить заиливанием глинистым раствором днища камеры по сбору продуктивных растворов, сооружать полуактивные водопроницаемые химически активные барьеры. Указанная технология ПБВ внедрена при отработке опытного блока 5-86 и рекомендована для блоков 5-84-86 и 5-88-90 Мичуринского месторождения ГП «ВостГОК», Украина, а также при разработке рудных месторождений Российской Федерации, Республики Казахстан.
Рудные месторождения, подземное блочное выщелачивание, установки, горные выработки, мониторинг, гидрогеологическая и окружающая среда, эффективность
Короткий адрес: https://sciup.org/140293741
IDR: 140293741
Текст научной статьи Оценка эффективности гидрогеологической и окружающей среды при подземном блочном выщелачивании металлов из руд
С увеличением объемов подземной добычи руд растет объем отходов на поверхности и в подземных выработках, что повышает темпы загрязнения окружающей среды [1, 2]. Многие участки эксплуатируемых месторождений представляют собой раздробленную горную массу, являющуюся базой для неуправляемого процесса природного выщелачивания [3, 4]. Поэтому доказательство возможности минимизации последствий природного выщелачивания путем управления технологическими процессами в рамках реализации ресурсосберегающих технологий актуально [5, 6]. Ниже приведены основные научные и практические результаты исследований комбинированных технологий разработки рудных месторождений, относящихся как к технологиям обогащения и гидрометаллургии, https://mst.misis.ru/
2022;7(1):5–17
так и технологиям подземной добычи (физико-химическим геотехнологиям) полезных ископаемых [7, 8]. Данная работа является продолжением исследований с участием авторов, основные научные и практические результаты которых наиболее полно приведены в работах [9, 10].
Цель исследования - обоснование эффективности подземной разработки рудных месторождений традиционными и комбинированными технологиями с выщелачиванием металлов из скальных некондиционных и забалансовых руд. Это обеспечит повышение сырьевой базы добычи металлов из забалансовых руд и улучшит охрану недр, гидрогеологической и окружающей среды.
Для достижения поставленной цели необходимо решить следующие задачи.
-
1. Проанализировать факторы, влияющие на эффективность и экологическую безопасность подземной разработки рудных месторождений с выщелачиванием металлов.
-
2. Выявить условия и источники возможного загрязнения водной и воздушной среды в зоне влияния подземного блочного выщелачивания металлов из руд.
-
3. Разработать мероприятия для снижения отрицательного влияния на окружающую среду подземного блочного выщелачивания металлов из руд.
-
4. Рекомендовать перспективные исследования, влияющие на повышение эффективности и экологической безопасности подземного блочного выщелачивания металлов из руд.
Методы исследований
Для обобщения, критического анализа и прогнозирования научных достижений в области технологии и технических средств подземной добычи руд, подземной геотехнологии, взрывного разрушения твердых сред использованы методы механики сплошных сред, математической статистики и исследования волновых процессов по стандартным и новым методикам.
Обсуждение результатов
Технологический аудит подземного блочного выщелачивания металлов из руд Известные способы извлечения металлов из рудного сырья не являются безотходными, так как для полной утилизации хвостов нужно будет затратить еще больше средств и энергии. Не улучшаются и экологические последствия, так как вторичные хвосты в процессе хранения и переработки активизируются и мигрируют в окружающую среду. Значительная экономическая эффективность отличает новую технологию от известных тем, что нет необходимости её извлечения на поверхность [11, 12].
На Гумешевском месторождении подземное блоковое выщелачивание руд осуществляется с 2005 г. На рудниках «Приаргунского производственного горно-химического объединения» (г. Краснокаменск, Российская Федерация) применяют системы разработки с выщелачиванием металла из магазинированных в камере руд в промышленных масштабах. Геотехноло-гические способы получения металлов в РСО–Алания известны со второй половины прошлого века [13, 14].
Влияние природного выщелачивания руд на экологию исследуется на практике предприятий Северного Кавказа, где содержание продуктов природного выщелачивания руд на 2–3 порядка превышает санитарные нормы. В частности, река Баксан (Кабардино-Балкария) на участке Тырныаузского месторождения принимает стоки вольфрамово-молибденового комбината, содержащие вольфрам и молибден. В Алагирском районе Республики Северная Осетия–Алания на участке Садонских месторождений река Ардон загрязняется медью, свинцом и цинком [15, 16].
Альтернативой традиционным технологиям разработки указанных месторождений может быть технология с переводом полезного компонента из руды в раствор. Руда магазинируется в блоках. Просочившись через толщу руды, продуктивный раствор реагентов собирается в днище, откуда направляется на переработку (рис. 1).
Откаточный горизонт
Оросительные скважины
Дренажные скважины
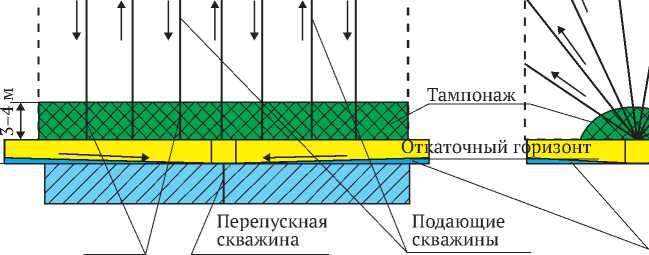
Тампонаж
Подающие скважины
Перепускная скважина ткаточный горизонт j
Гидроизоляция
Рис. 1. Подготовка рудных тел к выщелачиванию без дробления руды
2022;7(1):5–17
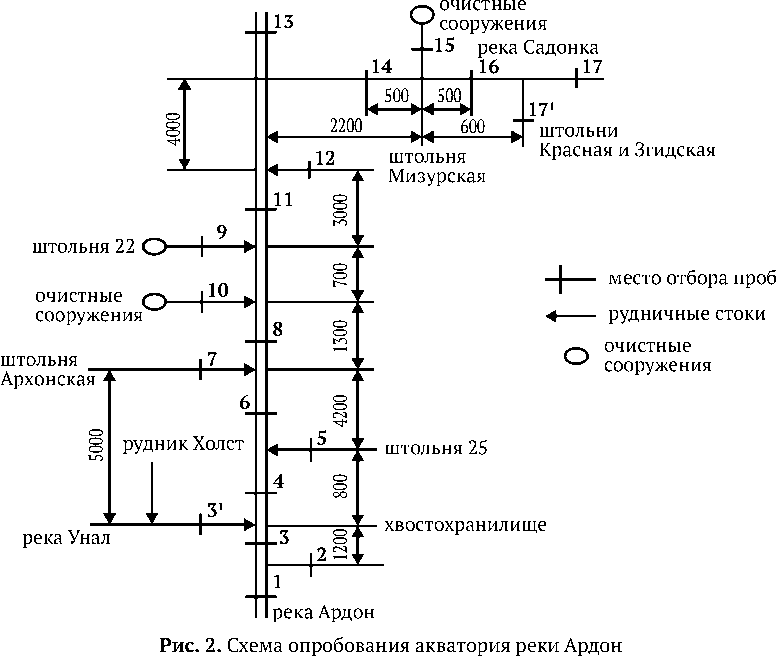
На Какадурском месторождении (Северная Осетия) при подземном блоковом выщелачивании руд с содержанием свинца 0,99 %, цинка 0,71 % отрабатывали не отдельный участок некондиционных для традиционной технологии запасов, а всего месторождения. Профессор И. А. Остроушко доказал его целесообразность и добился реализации. Новая технология выщелачивания минералов в дезинтеграторе основана на том, что при скорости удара 250 м/с их технологические свойства изменяются. При переработке хвостов обогащения Садонских руд в дезинтеграторе извлечено 22% свинца и 76% цинка от их исходного количества в первичных хвостах. Путем многократной переработки содержание доводится до требуемого уровня [17, 18]. Количество металлов в растворах природного выщелачивания корреспондирует с содержанием ускорителей процесса – железосодержащих минералов, и замедлителей – кальция и магния. Для оценки особенностей рудничных стоков в реке Ардон были исследованы пробы воды (рис. 2).
Объединение возможностей предприятий, например, свинцово-цинкового комбината и ОАО «Кав-доломит» (РСО–Алания, Российская Федерация) имеет природоохранную значимость, так как заполнение выработанного пространства закладочной смесью на основе вяжущих из доломита уменьшит потери руд при отбойке. Для получения вяжущей фракции доломита применяют мельницы, в которых удельная поверхность доломитов увеличивается до 3000 см2/г, что повышает активность вяжущих добавок на 20–30 % [19, 20]. Одним из лучших способов снижения количе- ства отходов радиоактивных веществ на поверхности земли, сокращения объемов закладки и увеличения производительности предприятия в процессе выпуска продукции является добыча подземным блочным выщелачиванием металлов из отбитых руд (рис. 3).
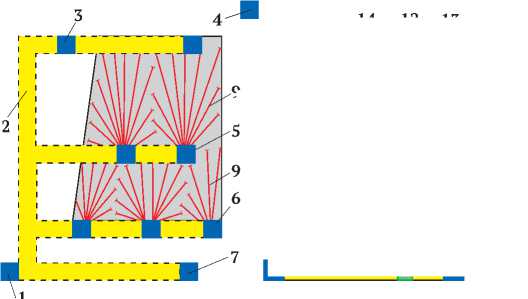
а
Рис. 3. Технология подземного блочного выщелачивания металлов из отбитых руд: а и б – разбуривание и выщелачивание замаганизированных руд в блоке:
1 – штрек; 2 – восстающий; 3 – штрек для орошения;
4 – штрек; 5 – буровые штреки; 6 – дренажно-буровые штреки; 7 – дренажный штрек; 8 – дренажные скважины; 9 – промежуточный горизонт орошения;
10 – промежуточный горизонт орошения; 11 – штрек для орошения; 12 – верхняя подсечка; 13 – костровая крепь; 14 – оросительная система
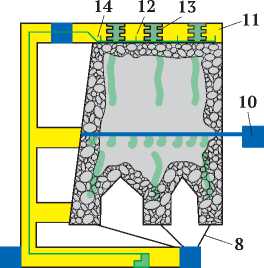
б
2022;7(1):5–17
Технология выщелачивания металла из скальных руд в установках, размещенных в горных выработках, иллюстрируется рис. 4.
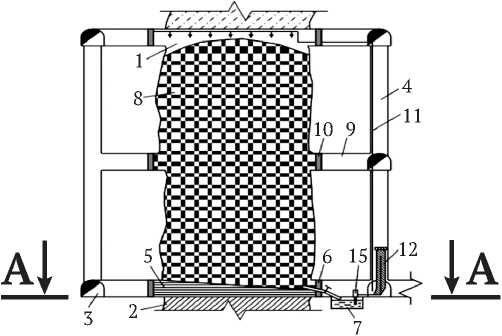
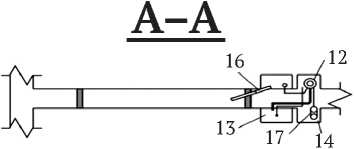
Рис. 4. Технологическая схема выщелачивания металла из скальных руд в подземных установках:
1 – камера; 2 – рудное тело; 3 , 4 – горизонтальные и вертикальные выработки; 5 – изоляционный материал;
6 – изоляционная перемычка; 7 – емкость;
8 – магазинированная руда; 9 – выработка;
10 – изолирующая перемычка; 11 – трубопровод;
12 – аппараты для сорбционной переработки продуктивных растворов; 13 – емкость для приготовления выщелачивающего раствора; 14 – ниши; 15 – насосы;
16 – труба; 17 – аппарат десорбции металла
Рудное тело 2 разделяют на эксплуатационные блоки, проходят горноподготовительные и нарезные выработки. Бурение проводится скважинами диаметром 50–85 мм из подэтажных выработок 9 . Частичный выпуск замагазинированной руды 8 осуществляют на откаточный горизонт. В верхней части камеры 1 монтируют оросительную систему, состоящую из труб 11 и форсунок, а в нижней оборудуют выработки 7 для сбора продуктивных растворов [21, 22].
Аппаратурная схема промышленного освоения технологии ПБВ представлена на рис. 5. Она включает: железнодорожную цистерну; насосы типа F430 PP – 50/38; Х 80–50–250 Е; ПР63; АХ 125–100–400Е и Х50–32–125; емкость для низкосортной кислоты; сливное устройство; автоцистерну и емкость для смолы; погружной насос типа F-706 PP-185; зумпфы для растворов продуктивных, нейтрализации и выщелачивающих; гидроподьемник; емкости объемом 0,4 и 0,8 м3; сорбционную колонну типа СНК; трубопровод; эжектор; свободную емкость; емкости для подкисления и нейтрализации; таль ручную грузоподъемностью до 1 т.
Выщелачивающий и продуктивный растворы перекачивают из нижележащего на вышележащий горизонт без выдачи их на дневную поверхность. На днев- ную поверхность продукцию выдают в виде смолы для дальнейшей переработки на ГМЗ. По сути в шахте сооружают подземный участок по выщелачиванию металлов из скальных руд в блоках ПБВ с переработкой растворов в установках, размещенных в подземных выработках. Авторы указывают на то, что данный метод позволяет существенно сократить операции, применяющиеся в традиционной системе добычи [23, 24] (кроме таких, как: создание компенсационного пространства, выпуск и доставка до 30 % замагази-нированной руды из камеры ПБВ и др.).
Мониторинг гидрогеологической и окружающей среды
Система мониторинга окружающей среды включает в себя трехступенчатый контроль и позволяет решать следующие задачи: осуществлять контроль за состоянием шахтных вод; определять зоны загрязнения шахтного воздуха; обнаруживать аварийное загрязнение окружающей среды; обеспечивать органы управления предпиятия.
Результаты исследований
Для наблюдения за возможной миграцией из камеры блока и зумпфа в направлении основания блока пробурено шесть восстающих наблюдательных скважин (рис. 6). Первый уровень мониторинга состояния водной среды проводился ежемесячно по величине водородного показателя рН шахтной воды в наблюдательных скважинах обслуживающим персоналом опытного блока.
В процессе эксперимента произведено 18630 замеров величины рН воды. Наблюдательные скважины за время эксперимента оставались сухими. Показатель рН воды практически соответствовал нейтральному значению 6,5–7,5 и только в 5 случаях значения рН составили 1,5–2,0, что объясняется прорывами трубопроводов, износом запорной арматуры. Ореол растекания технологических растворов был локальным и нейтрализован известковым молоком.
Второй уровень мониторинга водной среды проводился по следующим параметрам: содержание урана; щелочность; водородный показатель (рН). За время отработки блока отобрано 882 проб шахтной воды. В табл. 1 представлены результаты мониторинга, усредненные по кварталам. По выполненным анализам усредненное значение концентрации урана равно: горизонт 210 м – 3,6 мг/л; горизонт 225 м – 3,58 мг/л; горизонт 280 м – 0,91 мг/л. Величина рН соответствовала нейтральному значению. Данные наблюдений свидетельствуют о том, что отрицательного влияния опытного блока на качество шахтной воды не обнаружено, при этом наблюдательные скважины оставались полностью сухими [25, 26].
Третий уровень предусматривал также мониторинг воздушной среды. Ежемесячно выполнялся полный химический анализ проб шахтной воды на кальций, магний, натрий, калий, железо общее, карбонаты, бикарбонаты, сульфаты, хлориды, нитраты, нитриты, аммоний сухой остаток, уран, а также ежеквартально – радиохимический анализ на радий–226, торий–230, полоний–210, свинец–210, уран (табл. 1).
2022;7(1):5–17
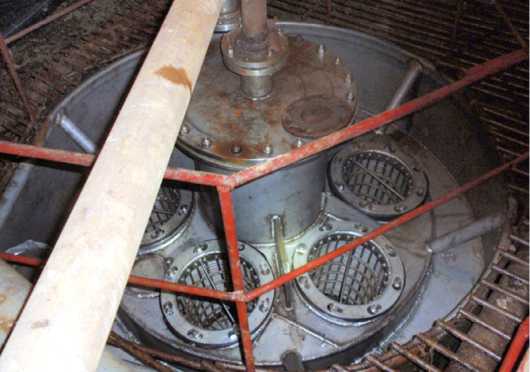
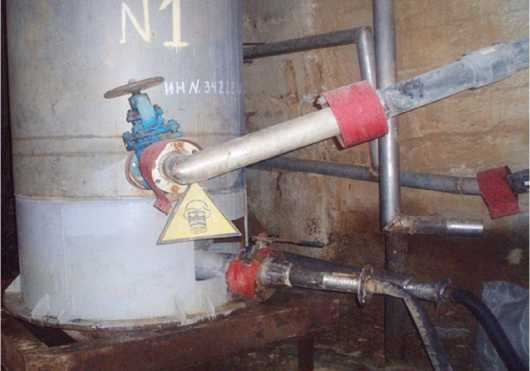
a
б
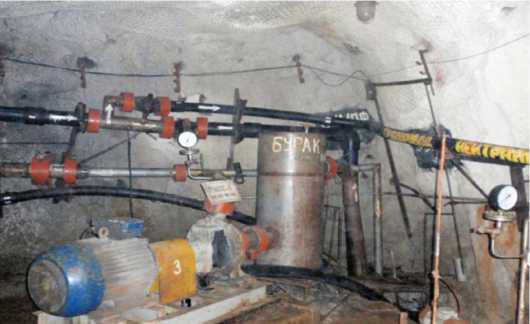
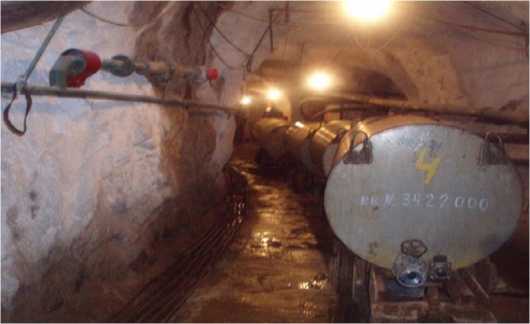
в
г
Рис. 5. Технологическое оборудование для ПБВ на Ингульской шахте ГП «ВостГОК» (фото): а и б – сорбционные колонны типа СНК; в – насосная с ёмкостью 0,4 м3 и насосом АХ; г – состав ёмкостей с ионнообменной смолой и разбавленной серной кислотой
Сорбционная колонна

Гор. 210 I___г
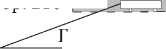
Горизонт орошения
Магистральный трубопровод
Оросители
Вс. Х 59 оси
Контур рудного тела
Гор. 225
Гор. 240
Рс. 59
Гор. 280
Гор. 250
Гор. 255
Емкость приема сорбента
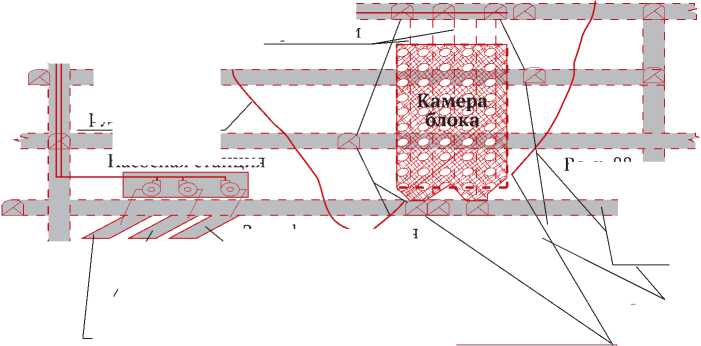
Насосная станция
Горизонт улавливания
Скважины наблюдения
Зумпф растворов нейтролизации
Рис. 6. Технологическая схема подготовки блока к выщелачиванию:
Рс.59 – рудоспуск 59-й оси; Вс. Х 59, Вс. Х 88 – вентиляционно-ходовой восстающий 59-й и 88-й оси соответственно
Зумпф улавливания прод. растворов Зумпф приготовления и дозакисления прод. растворов
Вс. х. 88
2022;7(1):5–17
Таблица 1
Результаты мониторинга третьего уровня по шахтной воде
Наименование |
Место отбора проб |
Контролируемые параметры |
||
щелочность, мг экв/л |
рН |
уран, мг/л |
||
П – 1 П – 2 |
2,70 |
7,8 |
6,7 |
|
До эксперимента |
П – 3 П – 4 |
0,50 |
7,8 |
0,64 |
П – 5 П – 6 |
5,75 |
7,9 |
1,32 |
|
Усредненное |
П – 1 П – 2 |
2,60 |
7,3 |
3,60 |
значение за три |
П – 3 П – 4 |
3,21 |
7,5 |
3,58 |
года эксперимента |
П – 5 П – 6 |
5,37 |
7,7 |
0,91 |
За время ведения опыта было отобрано и проанализировано на полный химический анализ 210 проб шахтной воды и 60 проб на радиохимический анализ. Результаты химического и радиохимического состава шахтной воды, а также шахтной воды непосредственно перед установкой очистки шахтных вод на горизонте 2010 м приведены в табл. 2.
Таблица 2
Результаты мониторинга третьего уровня по шахтной воде
Объект исследования и определяемый компонент |
Шахтная вода |
Среднее значение |
||
до опыта |
во время опыта |
после опыта |
||
Уран, мг/л |
90 |
6,7 |
6,2 |
4,4 |
Ra - 226 x 10-11, Ки/л |
20 |
8,37 |
6,24 |
6,7 |
Th - 230 x 10-11, Ки/л |
20 |
3,03 |
2,46 |
2,2 |
Pb - 210 x 10-11, Ки/л |
20 |
32,05 |
9,53 |
10,4 |
Po - 210 x 10-11,Ки/л |
20 |
2,5 |
1,18 |
2,8 |
SO2-4, мг/л |
70 |
614 |
659 |
691 |
CI, мг/л |
70 |
172 |
166 |
142 |
PH, ед. |
70 |
7,6 |
7,7 |
8,2 |
Ca2f, мг/л |
70 |
145 |
133 |
124 |
Md2f, мг/л |
70 |
41,3 |
62,8 |
52 |
Naf, мг/л |
70 |
235 |
229 |
220 |
Kf, мг/л |
70 |
15,5 |
13,2 |
12 |
Fe общ , мг/л |
70 |
0,05 |
0,05 |
0,05 |
NH 4 , мг/л |
70 |
1,1 |
0,15 |
0,1 |
NO 3 , мг/л |
70 |
40 |
15 |
9 |
NO2, мг/л |
70 |
26 |
0,2 |
0,1 |
HCO 3 , мг/л |
70 |
92 |
157 |
132 |
Сухой остаток, мг/л |
70 |
1588 |
1560 |
1366 |
Результаты химического состава шахтной воды показывают, что до момента закисления блока химический состав шахтной воды значительно различается как по времени отбора, так и по месту отбора проб. Так, например, концентрация сульфат-иона колеблется от 403,0 до 998,0 мг/л, содержание урана от 0,35 до 7,30 мг/л. Сравнивая результаты анализов пород, можно сделать вывод о том, что средняя концентрация сульфат-, хлор-иона урана, рН, сухого остатка в пробах, отобранных в ходе проведения эксперимента по ПБВ, не превышала значений в пробах, отобранных до начала закисления отбитой руды.
Существенных изменений состава и концентраций элементов шахтной воды, сбрасываемой в реку Ингул, за период работы блоков ПБВ 5-86; 5-84-86; 5-88-90 не произошло. Один раз в месяц проводился отбор проб на следующие параметры: аэрозоли серной кислоты; содержание радона; мощность экспозиционной дозы гамма-излучения. С начала эксплуатации только блока 5–86 произведено 576 замеров. Анализ результатов, представленных в табл. 3, свидетельствует, что определяемые показатели не превышали показателей проб, отобранных до опыта [27, 28].
Таблица 3
Результаты мониторинга третьего уровня по воздушной среде |
||||
Объект исследования и определяемый компонент |
Воздушная среда |
Среднее значение |
||
до опыта |
во время опыта |
после опыта |
||
Горизонт 210 м |
||||
Аэрозоли серной кислоты, мг/м3 |
640 |
– |
0,5 |
– |
Радон, Бк/м3 |
64 |
580 |
645 |
110 |
МЭД, мкР/ч |
64 |
146 |
206 |
227 |
Горизонт 240 м |
||||
Аэрозоли серной кислоты, мг/м3 |
128 |
– |
0,26 |
– |
Радон, Бк/м3 |
128 |
513 |
490 |
439 |
МЭД, мкР/ч |
128 |
454 |
331 |
312 |
Оценка полученных результатов
Первоначальные результаты работы показали существенную зависимость эффективности процесса выщелачивания (по временному фактору) от рабочего объёма зумпфа продуктивных растворов. Наиболее оптимальным, как выяснилось, является объем в 70–80 м3, а проектный был 20 м3. Первоначальный опыт эксплуатации выявил такой отрицательный фактор, как наличие значительного количества песка и мусора в отрегенерированной смоле на ГМЗ. Впоследствии было принято решение по монтажу на ГМЗ автономного узла регенерации смолы для опытных участков ПБВ [29, 30].
При отработке блока 5–86 в соответствии с выданными рекомендациями максимально использовались ранее пройденные выработки. Такой же подход был использован при подготовке к ПБВ опытно-экспериментальных блоков на Мичуринском месторождении 5–84–86 и 5–88–90, а также промышленно-экспериментального блока 1–75–79. Проведен необходимый объем восстановительно-ремонтных работ ранее пройденных выработок. Вместе с тем требуют особого внимания вопросы устойчивости выработок горизонта орошения, расположенного в районе интенсивного влияния отработанных блоков. Рудный массив в этаже 197–210 м ослаблен существующими до подготовки блоков к ПБВ нарезными и очистными выработками, а также сетью скважин создаваемой системы орошения. В этих выработках был организован систематический контроль за их устойчивостью и характером напряженно-деформированного состояния https://mst.misis.ru/
2022;7(1):5–17
приконтурного массива (геомеханический и сейсмический мониторинги). Результаты промышленного эксперимента по ПБВ показывают, что в рамках существующей на ГП «ВостГОК» системы подготовки запасов к отработке, с изменением только параметров буровзрывных работ удалось получить в опытном блоке руду оптимального гранулометрического состава. За время эксперимента в раствор переведено около 54 % запасов металла в блоке при расходе кислоты 36 % от проектного. Таким образом, добыча и переработка руд с применением традиционных технологий в современных экономических условиях нецелесообразна при содержании металла в добытой рядовой руде менее 0,070 у.е. (табл. 4).
Таблица 4
Основные показатели блочного выщелачивания металла
Наименование |
Показатели |
Объем выщелачиваемой руды, тыс. т |
8,248 |
Содержание металла, усл. ед. |
0,065 |
Израсходовано кислоты H 2 SO 4 , т |
231,1 |
Удельный расход кислоты, кг/т |
28,0 |
Расход кислоты на закисление, т |
27,8 |
Удельный расход окислителя, кг/т |
3,3 |
Время закисления, сутки |
40 |
Количество растворов, поданных на орошение, м3 |
66106 |
Плотность орошения, л/м2х ч |
9,6 |
Отношение «Ж:Т», ед. |
8:1 |
Время орошения, сут |
166 |
Продолжительность сорбции, сут |
398 |
Объем растворов на сорбцию, м3 |
25756 |
Характеристика продуктивных растворов: а) концентрация металла, средняя, мг/л б) кислотность, средняя, г/л |
220 13,5 |
Характеристика орошающих растворов: концентрация Fe+3 /Fe+2, г/л минерализация (сухой остаток), г/л |
1,9/0,38 43,2 |
Объем насыщенного анионита металлом, м3 |
101,3 |
Средняя емкость насыщенного сорбита, кг/м3 |
27,3 |
Остаточная емкость отрегенерированного сорбента по металлу, кг/м3 |
0,66 |
Промывка «хвостов» в блоке: продолжительность, сут |
65 |
Объем промывных вод, м3 |
5775 |
Удельный расход воды на промывку, м3/т |
0,7 |
Феномен природного выщелачивания является следствием недостаточного уровня применяемых технологий разработки. Механизм процессов природного выщелачивания металлов адекватен, что открывает возможности управления ими. Радикальным способом минимизации последствий природного выщелачивания является полная утилизация металлосодержащего сырья. Концепция природоохранности пользования недрами предусматривает замену неуправляемого природного выщелачивания технологическим выщелачиванием в контролируемом рабочем пространстве. Уровень знаний о теории и практике извлечения металлов из металлических руд месторождений позволяет использовать технологии с выщелачиванием для восстановления былого потенциала горнодобывающих отраслей [31, 32].
Эффективность
Максимальная эффективность комбинированной технологии разработки с выщелачиванием металлов из руд обеспечивается за счет увеличения извлечения полезных компонентов из недр:
M ′ ≥ ε n -ε TM , (1) ε n -ε2ε3
где M – количество полезного компонента в недрах; M′ – количество полезного компонента, выдаваемого из недр; ε n – извлечение металлов из руд технологиями с выщелачиванием; ε T – извлечение металлов из недр при его отработке традиционной системой (ТС):
M m
ε T = M ε1ε2ε3, (2)
где Mm – количество металлов ТС; ε 1 – извлечение металлов из недр ТС; ε 2 – извлечение металлов в концентрат; ε 3 – извлечение полезного компонента из концентрата в готовый продукт.
Прибыль от вовлечения некондиционных по содержанию полезных компонентов запасов в производство за счет увеличения объемов добычи, прироста продукции и повышения отдачи капитала для комбинированных технологий выщелачивания определяется согласно математической модели вида:
Profit V
( C ore
b ext
b b sel
C enr C met ) V b +
comb
+ ( C ore
-
comb C ext
-
C
comb
enr
-
comb
C met ) D 0
■ V Srnb ’
Преимущества блочного выщелачивания
Отсутствуют затраты на отдельные операции по сравнению с традиционной технологией добычи и переработки руды, а именно:
– при добыче: вторичное дробление и выпуск руды; внутришахтные перевозки руды; выдача руды на поверхность; дробление и обогащение руды; закладка выработанного пространства; погрузка в железодорожные вагоны и перевозка руды на ГМЗ;
– при переработке на ГМЗ: перегрузка руды; измельчение руды; выщелачивание; сорбция; регенерация смолы; складирование хвостов.
где Profit – годовая прибыль от комбинирования технологий, ден. ед.; C o b re , C o c r o e mb – соответственно стоимость реализации металлов из балансовых и комбинированных запасов руд, ден. ед. / т; C e b xt , C e b nr , C m b et – соответственно затраты на добычу, обогащение и металлургический передел балансовых руд, ден. ед. / т; C e c x o t mb , C e c n o r mb , C m co e m t b – соответственно затраты на добычу, обогащение и металлургический передел комбинированных запасов руд, ден. ед. / т; V b sel , V c s o e m l b – соответственно объем селективно добытых балансовых и комбинированных руд, т; n – номенклатура извлекаемых металлов; D 0 – суммарный ущерб (экономические последствия), наносимый (–) окружаю-
2022;7(1):5–17
щей среде или предотвращаемый (+) с учетом затрат на хранение загрязняющих веществ и защиту населения, проживающего в зоне влияния горных объектов, ден. ед.
Таким образом, внедрение в промышленных масштабах ПБВ значительно улучшит экономические показатели производства, что позволило бы через модернизацию основных фондов, техническое перевооружение производства, вовлечь в отработку запасы бедных, а также некондиционных руд и продлить таким образом сроки существования действующих шахт. В результате проведенных исследований установлено, что горно-химические технологии могут быть использованы для разработки бедных и некондиционных руд месторождений и таким образом повысить их рентабельность. Кроме того, за счет привлечения в производство некондиционных руд сырьевая база добычи металлов на действующих шахтах может быть увеличена в 1,4–1,6 раза. Установлено, что эффективность различных вариантов технологии выщелачивания металла из руд определяется полнотой его извлечения. Накопленный в мировой практике опыт свидетельствует, что при прочих равных условиях, таких как характер минерализации, структура, пористость руды, коэффициент диффузии, температура, концентрация рабочих растворов и т.п., полнота выщелачивания непосредственно зависит от качества дробления руды и равномерности ее распределения по плотности в зама-газинированном состоянии. Доказана возможность выщелачивания металла из рудных месторождений и установлена зависимость извлечения металла от среднего линейного размера раздробленной взрывом рудной массы [33, 34].
Перспективные исследования
Для обеспечения охраны гидрогеологической среды необходимо осуществлять заиливание глинистым раствором днища камеры по сбору продуктив-них растворов, а также сооружать полуактивные водопроницаемые химически активные барьеры (ВХАБ) и применять биологические технологии при ПБВ. Основными преимуществами использования железооксидных композитов на основе природных глинистых минералов для очистки воды от загрязнения соединениями урана являются их экологичность, дешевизна, доступность и технологичность. Это должно обеспечивать снижение степени загрязненности металлами грунтовых и поверхностных вод, почв и отложений, включая главный Мичуринский разлом (г. Кропив-
ницкий, Украина). Необходимо также продолжить исследования, направленные на разработку таких технологий, которые удовлетворяли бы как экономическим, так и экологическим требованиям [35, 36].
Заключение
На основании полученных научных и практических результатов при комбинированном выщелачивании металлов из забалансовых и некондиционных руд для их последующего обогащения на гидрометаллургическом заводе авторами сделаны следующие выводы.
-
1. Отмечено, что за время опытно-промышленного эксперимента выщелачивания металлов из руд эксплуатационного блока 5–86 Мичуринского месторождения (Украина) наблюдение осуществлялось на трех горизонтах: 210, 225 и 280 м. В процессе эксперимента величина показателя рН воды соответствовала нейтральному значению 6,5–7,5 и только в 5 случаях его значения составили 1,5–2,0. Это объясняется прорывами трубопроводов, износом запорной арматуры. Ореол растекания технологических растворов был локальным и нейтрализован известковым молоком.
-
2. На основании экологического мониторинга и результатов анализа усредненное значение концентрации урана составляло: горизонт 210 м – 3,6 мг/л; горизонт 225 м – 3,58 мг/л; горизонт 280 м – 0,91 мг/л. Загрязнения подземных шахтных вод не обнаружено. Уровень аэрозолей серной кислоты и продуктов распада радона не превышал значений предельно-допустимой концентрации.
-
3. Рекомендовано для нейтрализации и промывки отработанной рудной массы обрабатывать ее раствором извести и шахтной водой через скважины для подачи выщелачивающих растворов (оросительная система). Охрану гидрогеологической среды осуществлять путем заиливания глинистым раствором днища камеры по сбору продуктивных растворов. Организовать мониторинг подземных вод через наблюдательные скважины, пробуренные в днище эксплуатационного блока и к контактам с рудным телом, а также зонами трещиноватости и гидрогеологического разрыва пород.
-
4. Показано, что природное выщелачивание металлов из рудного сырья является следствием недостаточного уровня применяемых технологий разработки и может быть минимизировано. Это обеспечит повышение экономической эффективности, рациональное использование недр, охрану гидрогеологической и окружающей среды, а также увеличит сырьевую базу добычи металлов в 1,4–1,6 раза.
2022;7(1):5–17
%D0%9C%D0%93%D0%A2%D0%A3%20%D0%B7%D0%B0%202009%20%D0%B3%D0%BE%D0%B4,%20 %D0%9D%D0%BE%D0%BC%D0%B5%D1%80%203.pdf
2022;7(1):5–17
2022;7(1):5–17
2022;7(1):5–17
Список литературы Оценка эффективности гидрогеологической и окружающей среды при подземном блочном выщелачивании металлов из руд
- Мосинец В. Н., Лобанов Д. П., Тедеев М. Н. и др. Строительство и эксплуатация рудников подземного выщелачивания. Монография. Под общ. ред. В. Н. Мосинца. М.: Недра; 1987. 304 с.
- Чернов А. П. (ред.). Добыча и переработка урановых руд в Украине. Киев: АДЕФ–Украина; 2001. 238 с.
- Ляшенко В. И., Голик В. И., Козырев Е. Н. Комбинированные технологии добычи полезных ископаемых с подземным выщелачиванием. Горный журнал. 2008;(12):37–40.
- Дзапаров В. Х. Угроза безопасности жизнедеятельности региона РСО-Алания. Вестник Магнитогорского государственного технического университета им. Г. И. Носова. 2009;(3):75–76. URL: http://vestnik.magtu.ru/content/%D0%92%D0%B5%D1%81%D1%82%D0%BD%D0%B8%D0%BA%20%D0%9C%D0%93%D0%A2%D0%A3%20%D0%B7%D0%B0%202009%20%D0%B3%D0%BE%D0%B4,%20%D0%9D%D0%BE%D0%BC%D0%B5%D1%80%203.pdf
- Аренс В. Ж., Бабичев Н. И., Башкатов А. Д. и др. Скважинная гидродобыча полезных ископаемых. 2-е изд. М.: Горная книга; 2011. 295 с.
- Ляшенко В. И., Кислый П. А., Дятчин В. З. Радиометрическая предконцентрация урановых руд. Обогащение руд. 2015;(1):3–9.
- Ляшенко В. И., Хоменко О. Е., Голик В. И. Развитие природоохранных и ресурсосберегающих технологий подземной добычи руд в энергонарушенных массивах. Горные науки и технологии. 2020;5(2):104–118. https://doi.org/10.17073/2500-0632-2020-2-104-118
- Ghorbani Y., Franzidis J.-P., Petersen J. Heap leaching technology – current state, innovations, and future directions: a review. Mineral Processing and Extractive Metallurgy Review. 2016;37(2):73–119. https://doi.org/10.1080/08827508.2015.1115990
- Oxley A., Smith M. E., Caceres O. Why heap leach nickel laterites. Minerals Engeneering. 2016;88:53–60. https://doi.org/10.1016/j.mineng.2015.09.018
- Vrancken C., Longhurst P. J., Wagland S. T. Critical review of real-time methods for solid waste characterisation: Informing material recovery and fuel production. Waste Management. 2017;61:40–57. https://doi.org/10.1016/j.wasman.2017.01.019
- Li J., Li D., Xu Z., Liao C., Liu Y., Zhong B. Selective leaching of valuable metals from laterite nickel ore with ammonium chloridehydrochloric acid solution. Journal of Cleaner Production. 2018;179:24–30. https://doi.org/10.1016/j.jclepro.2018.01.085
- Габараев О. З., Дмитрак Ю. В., Дребенштедт К., Савелков В. И. Закономерности взаимодействия разрушенных геоматериалов и рудовмещающего массива при отработке подработанных вкрапленных руд. Устойчивое развитие горных территорий. 2017;9(4):406–413. https://doi.org/10.21177/1998-4502-2017-9-4-406-413
- Комащенко В. И. Эколого-экономическая целесообразность утилизации горнопромышленных отходов с целью их переработки. Известия Тульского государственного университета. Науки о Земле. 2015;(4):23–30. URL: https://tidings.tsu.tula.ru/tidings/pdf/web/file/tsu_izv_earth_science_2015_04.pdf
- Burdzieva O. G., Zaalishvili V. B., Beriev O. G., Kanukov A. S., Maysuradze M. V. Mining impact on environment on the North Ossetian territory. International Journal of GEOMATE. 2016;10(1):1693–1697. URL: https://geomatejournal.com/geomate/article/view/2012/1888
- Карамушка В. П., Камнев Е. Н., Кузин Р. З. Рекультивация объектов добычи и переработки урановых руд. М.: Издательство «Горная книга»; 2014. 183 с.
- Kachurin N., Kоmashchenko V., Morkun V. Environmental monitoring atmosphere of mining territories. Metallurgical and Mining Industry. 2015;(6):595–597. URL: https://www.metaljournal.com.ua/assets/Journal/MMI-6/083-Nikolai-Kachurin.pdf
- Святецкий В. С., Солодов И. Н. Стратегия технологического развития уранодобывающей отрасли России. Горный журнал. 2015;(7):68–77. https://doi.org/10.17580/gzh.2015.07.10
- Каплунов Д. Р., Юков В. А., Лавенков В. С. Сопоставление блокового и скважинного выщелачивания для подземной добычи медных руд. Горный информационно-аналитический бюллетень. 2017;(3):7–14. URL: https://giab-online.ru/files/Data/2017/3/7_14_3_2017.pdf
- Морозов А. А., Яковлев М. В. Вовлечение в переработку забалансовых урановых руд, образовавшихся при освоении месторождений Стрельцовского рудного поля. Горный информационно-аналитический бюллетень. 2016;(12):174–181. URL: https://giab-online.ru/files/Data/2016/12/174_181_12_2016.pdf
- Рыльникова М. В., Радченко Д. Н. Методологические аспекты проектирования системы управления минерально-сырьевыми потоками в полном цикле комплексного освоения рудных месторождений. Рациональное освоение недр. 2016;(3):36–41.
- Chen T., Lei C., Yan B., Xiao X. Metal recovery from the copper sulfide tailing with leaching and fractional precipitation technology. Hydrometallurgy. 2014;147–148:178–182. https://doi.org/10.1016/j.hydromet.2014.05.018
- Ghorbani Y., Franzidis J.-P., Petersen J. Heap leaching technology – Current state, innovations, and future directions: a review. Mineral Processing and Extractive Metallurgy Review. 2016;37(2):73–119. https://doi.org/10.1080/08827508.2015.1115990
- Копбаева М. П., Панова Е. Н., Принзин Н. А., Карманов Е. М. Оптимизация технологии пероксидного осаждения урана. Горный журнал. 2016;(5):90–94. https://doi.org/10.17580/gzh.2016.05.13
- Солодов И. Н., Камнев Е. Н. (ред.). Геотехнология урана (российский опыт). М.: КДУ; 2017. 576 с.
- Святецкий В. С., Полонянкина С. В., Ермаков А. Г. Уранодобывающая отрасль России: состояние и перспективы развития. Разведка и охрана недр. 2017;(11):22–26.
- Машковцев Г. А., Мигута А. К., Щеточкин В. Н. Сырьевая база урана. Проблемы развития и освоения. Минеральные ресурсы России. Экономика и управление. 2017;(3):67–78.
- Балихин А. В. Минерально-сырьевая база урана: современное состояние и перспективы развития. Обзор. Комплексное использование минерального сырья. 2019;(1):36–50. https://doi.org/10.31643/2019/6445.05
- Sinclair L., Thompson J. In situ leaching of copper: Challenges and future prospects. Hydrometallurgy. 2015;157:306–324. https://doi.org/10.1016/j.hydromet.2015.08.022
- Aben E., Markenbayev Zh., Khairullaev N., et al. Study of change in the leaching solution activity after treatment with a cavitator. Mining of Mineral Deposits. 2019;13(4):114–120. https://doi.org/10.33271/mining13.04.114
- Malanchuk Z., Korniienko V., Malanchuk Ye., et al. Modeling the formation of high metal concentration zones in man-made deposits. Mining of Mineral Deposits. 2018;12(2):76–84. https://doi.org/10.15407/mining12.02.076
- Stupnik M., Kalinichenko O., Kalinichenko V., et al. Choice and substantiation of stable crown shapes in deep-level iron ore mining. Mining of Mineral Deposits. 2018;12(4):56–62. https://doi.org/10.15407/mining12.04.056
- 32 Овсейчук В. А., Зозуля А. М. Совершенствование процесса блочного подземного выщелачивания в условиях Стрельцовского рудного поля. Горный информационно-аналитический бюллетень. 2021;(3–1):26–33. https://doi.org/10.25018/0236_1493_2021_31_0_26
- Kovalchuk I., Tobilko V., Kholodko Yu., Zahorodniuk N., Kornilovych B. Purification of mineralized waters from U(VI) compounds using bentonite/iron oxide composites. Technology audit and production reserves. 2020;3(3):12–18. https://doi.org/10.15587/2706-5448.2020.205146
- Антонинова Н. Ю., Собенин А. В., Шубина Л. А. Оценка возможности использования промышленных отходов при формировании геохимических барьеров. Горный информационно-аналитический бюллетень. 2020;(12):78–88. https://doi.org/10.25018/0236-1493-2020-12-0-78-88
- Камнев Е. Н., Карамушка В. П., Селезнев А. В. и др. Экологические проблемы и их решение при закрытии урановых производств (на примере России, СНГ и Германии). Горный информационно-аналитический бюллетень. 2020;(5):26–39. https://doi.org/10.25018/0236-1493-2020-5-0-26-39
- Подрезов Д. Р. Задачи совершенствования управления и повышения эффективности функционирования технологических блоков рудника подземного скважинного выщелачивания урана. Горные науки и технологии. 2020;5(2):131–153. https://doi.org/10.17073/2500-0632-2020-2-131-153