Оценка эрозионной стойкости упрочненных металлических сплавов в условиях каплеударного воздействия
Автор: Кудряков Олег Вячеславович, Варавка Валерий Николаевич, Забияка Игорь Юрьевич, Бронникова Наталья Ивановна
Журнал: Вестник Донского государственного технического университета @vestnik-donstu
Рубрика: Машиностроение и машиноведение
Статья в выпуске: 1 т.18, 2018 года.
Бесплатный доступ
Введение. Статья посвящена изучению явления каплеударной эрозии, которая развивается в металлических материалах при частотах капельных соударений 50…200 с-1 и скоростях 150…600 м/с. Исследована возможность сравнительной оценки сопротивления износу материалов различных структурных классов с различным уровнем механических свойств. Основной целью работы было создание расчетно-аналитической модели эрозионного износа упрочненных материалов. Параллельно решалась задача критериальной оценки материалов, с помощью которой можно было бы отнести их к пластичным или упрочненным, после чего использовать соответствующую модель механики усталостного разрушения. Материалы и методы. Для расчетно-аналитических оценок эрозионной стойкости материалов использованы известные зависимости механики разрушения и теории усталости Пэриса-Эрдогана. Параметры расчетных выражений получены на базе результатов стендовых эрозионных испытаний и данных растровой электронной микроскопии образцов стали 20Х13 с мартенситной структурой. Результаты исследования. В качестве классификационного критерия пластичных и прочных материалов предложено использовать их диаграммы предельных состояний. В частности, на основе такой диаграммы упрочненных материалов могут быть определены значения начального и критического размера хрупкой трещины, которые используются в основной модели для расчета эрозионной стойкости материала. На базе уравнения Пэриса усталостной теории Пэриса-Эрдогана разработана и научно обоснована расчетно-аналитическая модель для оценки эрозионной стойкости упрочненных материалов, деградация поверхности которых происходит по механизму зарождения и развития трещин скольного типа. Представлены данные расчетов для образцов мартенситной стали 20Х13 с использованием экспериментально полученных параметров уравнения Пэриса. Обсуждение и заключения. Полученные результаты актуальны для выбора, оптимизации или разработки эрозионно-стойких материалов для высокоскоростных лопастей парогазотурбинного и компрессорного оборудования, работающих в условиях образования капельного конденсата.
Каплеударная эрозия, усталостное разрушение, мартенситная сталь
Короткий адрес: https://sciup.org/142214933
IDR: 142214933 | DOI: 10.23947/1992-5980-2018-18-1-6-15
Текст научной статьи Оценка эрозионной стойкости упрочненных металлических сплавов в условиях каплеударного воздействия
Введение. Единичный удар водяной капли по металлической поверхности выглядит довольно безобидным и не может причинить ей большого вреда. Однако при длительном циклическом воздействии капель с частотой соударений 50…200 с - 1 и скоростью 150…600 м/с происходит стремительное эрозионное разрушение металла . На практике условия каплеударной эрозии формируются при наличии конденсата в парогазовых средах, что приводит к прогрессирующему износу лопастей парогазотурбинного и компрессорного оборудования. Несмотря на актуальность проблемы и её активное изучение [ 1 – 5 ], к настоящему времени физическая природа инициации износа при ударно - капельном воздействии до конца не ясна. Сложность анализа обусловлена тем, что каплеударное воздействие включает несколько составляющих: механическую (усталостную), кавитационную (гидродинамическую и пузырьковую) и коррозионную [ 6 – 10].
Кинетика эрозионного износа включает несколько стадий [ 11, 12 ]. Первая из них, инкубационная, характерна тем, что признаков разрушения и потери массы металла на этой стадии ещё нет. Поэтому длительность инкубационного периода обычно принимается в качестве антиэрозионного свойства материала в условиях каплеударного воздействия.
В ряде работ [ 8, 13 – 17] авторами исследованы особенности этого явления в таких пластичных металлических материалах, как однофазные титановые сплавы, сталь с аустенитной или сорбитной структурой. Начало изнашивания в этом случае определяется развитием подповерхностной усталостной пористости (рис. 1, a ), возникающей в металле в зоне соударения по механизму перколяции [ 18, 19] с последующим слиянием пор и формированием первичных поверхностных эрозионных кратеров износа (рис. 1, b ). В этом случае кратеры имеют характерную морфологию с весьма разветвленной поверхностью .
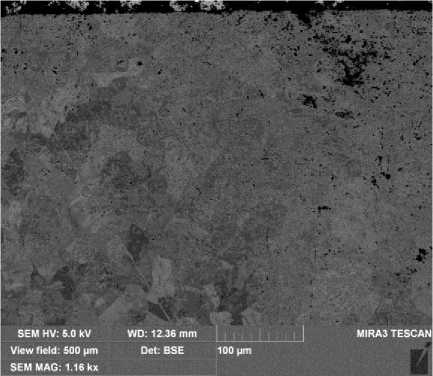
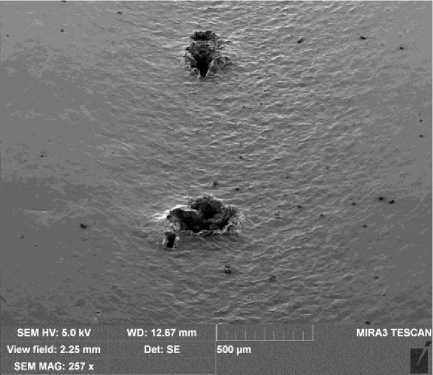
-
а ) b)
Рис. 1. Зарождение износа при каплеударной эрозии образцов аустенитной стали 08Х18Н10Т (РЭМ): а — формирование усталостной пористости в месте соударения (сечение образца по глубине); b — образование первых эрозионных кратеров (эрозионная дорожка на поверхности образца)
Fig. 1. Origin of wear under drip erosion of samples of austenic steel 08Cr18Ni10Ti (SEM): a – formation of fatigue porosity at collision site (cross section of the sample in depth); b – formation of the first erosion craters (erosion track on the sample surface)
Машиностроение и машиноведение
Морфологические особенности такого износа и его расчетно - аналитическая модель, разработанная на принципах усталостной теории Гудмена, наиболее полно представлены в работе [8]. В упрочненных же металлических материалах механизм перколяции не может быть реализован, так как размер зон пластичности слишком мал. В этом случае усталостная пористость не образуется, а морфология первичных кратеров износа определяется механизмом зарождения, роста и ветвления хрупких (скольного типа) усталостных трещин. Отличительными признаками такого механизма зарождения эрозионных кратеров являются сравнительно гладкая (фасеточная) поверхность их стенок (рис. 2, а) и наличие трещин в поперечном сечении кратеров (рис. 2, b).
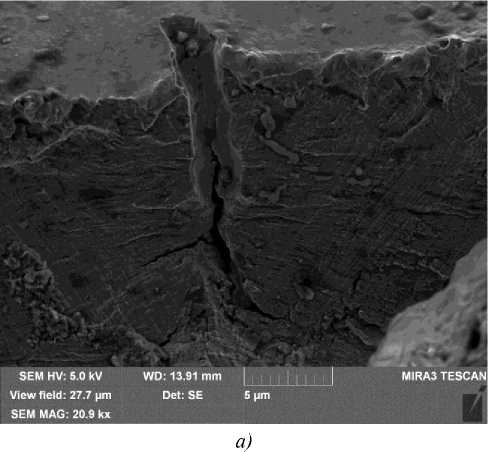
Рис. 2. Эрозионные кратеры на поверхности образца мартенситной стали 20Х13 (РЭМ)): а — стенка первичного кратера с ветвящейся острой трещиной;
b — поперечное сечение кратера с усталостными трещинами
Fig. 2. Erosion craters on the surface of sample of martensitic steel 20Cr13 (SEM)): a – wall of primary crater with sharp branching crack;
b – cross section of crater with fatigue cracks
Исходя из анализа вышеупомянутых экспериментальных данных была сформулирована цель настоящей работы — нахождение закономерностей и создание расчетно - аналитической модели эрозионного износа рассматриваемых материалов. Параллельно решалась задача критериальной оценки материалов, с помощью которой можно было бы отнести их к пластичным или прочным и использовать соответствующую модель механики усталостного разрушения.
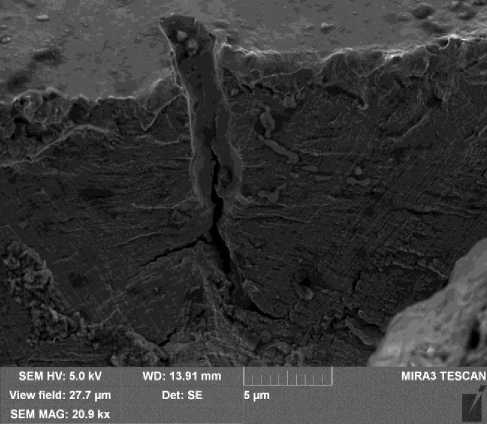
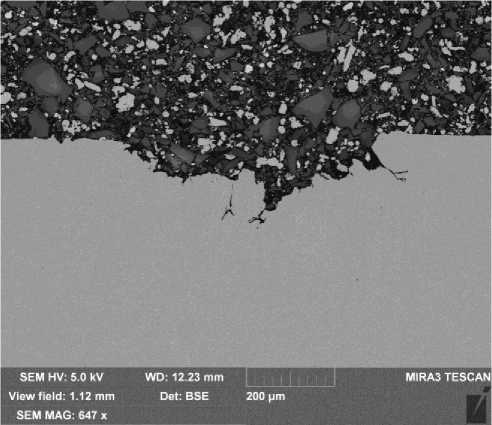
b)
Использование диаграмм предельных состояний материала в расчетной модели. Анализ базы экспериментальных данных, полученных в результате стендовых эрозионных испытаний образцов сталей с различной структурой, позволяет рекомендовать их диаграммы предельных состояний в качестве классификационного критерия пластичных и прочных материалов. В механике разрушения диаграмма предельных состояний определяет зоны хрупкого и вязкого разрушения материала. Общий вид такой диаграммы представлен на рис. 3 , где продемонстрировано предельное состояние по временному сопротивлению σ В в соответствии с теорией пластичности (наклонная прямая 1) и предельные состояния в соответствии с линейной механикой разрушения (кривые 2 и 3). Диаграмма на рис. 3 нуждается в некоторых комментариях, поскольку, применительно к исследуемой нами проблеме, отличается от своих классических предшественников.
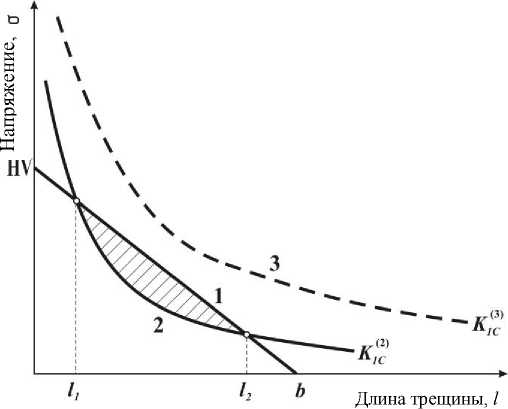
Рис. 3. Общий вид диаграммы предельных состояний с линиями предельных (1) и критических (2, 3) напряжений
Fig. 3. General form of limiting states diagram with lines of limiting (1) and critical (2, 3) stresses
В фундаментальной работе [2 0, C. 23] доказано, что для различных видов нагружения как при пластическом, так и при хрупком разрушении трещиностойкость К 1С определяется временным сопротивлением (пределом прочности) материала а В и конструктивным размером образца b (например, толщиной или шириной пластины):
откуда b = —2— , а в
где К 1С — критический коэффициент концентрации напряжений для трещины скольного типа (хрупкая трещина типа I).
Выражение (1) универсально, поскольку выведено для наиболее общих и простых случаев — неограниченного полупространства по глубине материала и неограниченной плоскости поверхности образца. Оно справедливо как для случая поверхностной трещины, распространяющейся в глубину, когда ограничивающим размером является толщина образца, так и для центральной (внутренней) трещины, растущей вдоль своей оси, когда ограничивающим размером b является ширина образца.
С учетом выражения (1) линия предельного состояния 1 на рис. 3 определяется как:
а в Y
2 ■ K i c )
а p ( l ) = HV ■ 1 -
В выражении (2) учтено, что рассматриваемые процессы каплеударного воздействия локализованы на поверхности материала. Все возникающие при этом трещины являются поверхностными (т. е. направлены в глубину образца либо от его поверхности, как на рис. 2, а, либо от поверхности кратера, как на рис. 2, b ). Когда трещина достигает некоторого определенного макроразмера (например, l 2 или b ), все процессы, определяющие её продвижение, локализованы в вершине трещины . В этом случае эти процессы происходят на некоторой глубине от поверхности и использование в расчетах такой макроскопической (т. е. объемной) характеристики, как а В в выражениях (1) и (2), с физической точки зрения оправдано. Когда же рассматривается процесс поверхностного зарождения трещины (например, l 1 ) , необходимо учитывать поверхностные эффекты (например, поверхностное натяжение или силы отображения, действующие на дислокации), которые требуют дополнительной работы зарождения по сравнению с работой зарождения трещины в объеме материала. В этом случае предельное состояние материала должно характеризоваться более высоким уровнем напряжения, чем а В . Такой более высокий уровень напряжений на диаграмме предельных состояний для поверхностной трещины задан в
Машиностроение и машиноведение
выражении (2) и на рис. 3 для линии 1 при l =0 значением твердости HV , что соответствует физическому смыслу твердости как поверхностного свойства.
Линии критических напряжений (кривые 2 и 3 на рис. 3) представляют собой степенные функции :
σ k ( l ) =
K 1 C
Y ⋅ π⋅ l
Высоким значениям К1С соответствует кривая 3, причем хрупкое состояние в этом случае не достигается, так как линии предельных состояний 1 и 3 не пересекаются. На диаграмме предельных состояний аустенит- ной стали 08Х18Н10Т линии не пересекаются, что говорит об отсутствии трещин и позволяет отнести её к пла- стичным материалам с перколяционным механизмам усталостного разрушения в условиях каплеударного изно- са.
Область трещин
l
1
-
l
2
соответствует хрупкому состоянию при
К
1С
, отвечающему кривой 2. Из рис
. 3
видно, что при уменьшении
К
1С
, а также с возрастанием значений
HV
или
b
(при фиксированном
К
1С
) заштрихованная область хрупкого состояния
l
1
-
l
2
увеличивается. Точки пересечения графиков на рис.
3
по своей физической сущности представляют собой начальный
l
1
≡
l
0
и критический
l
2
≡
l
С
размеры трещины. При
l
Расчетно-аналитическая модель для оценки эрозионной стойкости упрочненных металлических сплавов. В интервале между l 0 и l C скорость роста трещины (в расчете на один цикл нагружения, т. е. на один удар капли) может быть определена на основе теории усталости Пэриса - Эрдогана [ 22] с помощью уравнения Пэриса:
dl = A Δ Km (4)
dN
В свою очередь величина Δ К определяется выражением:
Δ K = K max - K min = Δσ π l (5)
с учетом следующих условий:
K max = σ max π l и K min = σ min π l для σ min > 0 и K min = 0 для σ min ≤ 0
Здесь К — коэффициент концентрации напряжений для соответствующих максимального σ max и минимального σ min напряжений единичного цикла.
Для использования методического аппарата теории Пэриса - Эрдогана необходимо экспериментальное определение параметров уравнения Пэриса m и А , которые являются эмпирическими константами материала. Так, например, выполненные авторами стендовые испытания образцов стали 20Х13 с мартенситной структурой для условий каплеударной эрозии дают значения параметров уравнения Пэриса: m = 2,5 и А = 3,403·10 - 9 м/цикл.
В работе [ 8] доказано, что при соударении жидкой капли с металлической поверхностью напряжение σ распределяется по поверхности во времени τ в соответствии графиком на рис. 4 . Величина σ выражена в относительных единицах ρ 0 ·с 0 · V 0 , называемых приближением гидравлического удара. Время τ также имеет относительную шкалу, где ρ 0 — плотность жидкости, с 0 — скорость звука в жидкости при нормальных условиях, V 0 — скорость соударения, R 0 — радиус капли.
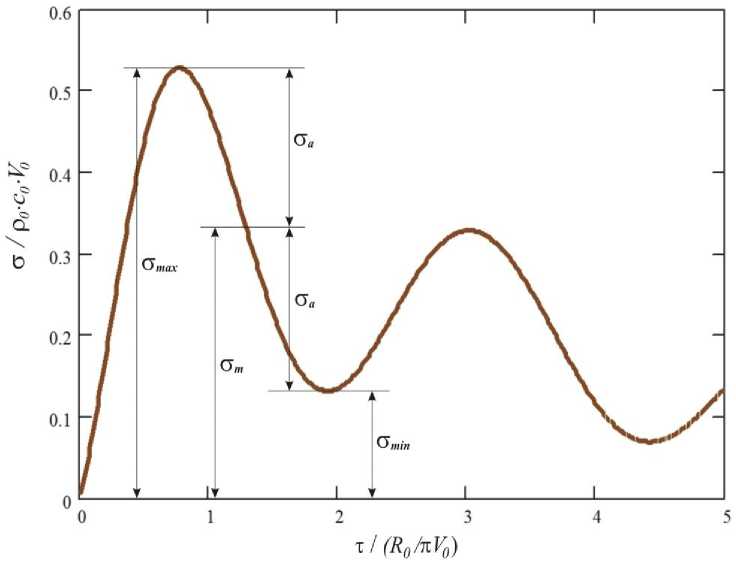
Рис. 4. Расчетные параметры цикла нагружения при капельном соударении
Fig. 4. Calculated parameters of loading cycle in case of drop collision
На рис. 4 отмечены величины напряжений, принятые в теории усталости, в частности в теории Пэриса - Эрдогана (максимальное σ max , минимальное σ min , среднее σ m и т. д.). Однако они требуют уточнения для использования в уравнении Пэриса ( 4 ). На рис. 4 представлено распределение напряжений для однократного соударения, а уравнение Пэриса используется для многоциклового нагружения. При однократном соударении с увеличением времени σ min → 0, поэтому единичный цикл нагружения становится отнулевым. При этом время между соударениями, попадающими в одну точку, превышает время единичного соударения в несколько раз. При отнулевом цикле нагружения в формуле ( 5 ) в соответствии с рис. 4 следует принимать:
Δ σ = σ max = 0,528· ρ 0 ·с 0 · V 0 . (6)
Решением уравнения Пэриса (4) для условий каплеударной эрозии может быть найдено допустимое количество циклов (капельных соударений) NC, определяющее продолжительность инкубационного периода эрозионного износа данного материала:
NClC
N C = ∫ dN =∫ 0 l 0
da
A ⋅ ( ∆ K ) m
Строго говоря, полученное интегрированием значение N C не является величиной инкубационного периода каплеударной эрозии m 0 , поскольку не учитывает количество циклов N 3 , необходимых для образования трещины размером l 0 . Поэтому для прикладного использования выражения ( 7 ) необходимы корреляции величины N C с данными стендовых испытаний с учетом того, что m 0 = N 3 + N C .
Машиностроение и машиноведение
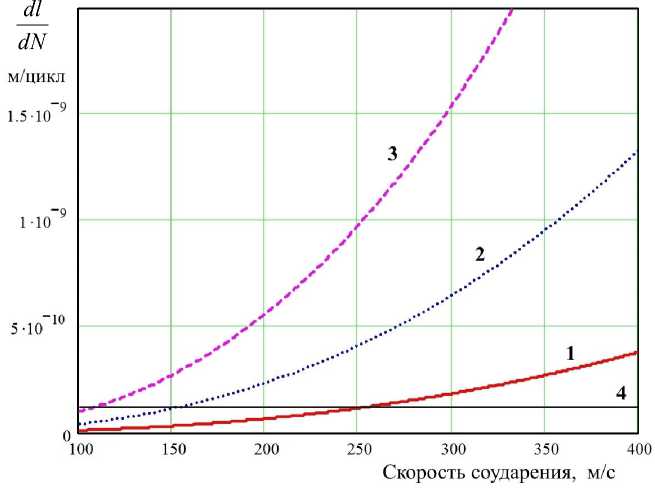
Рис. 5. Зависимость скорости роста трещины в стали 20Х13 с мартенситной структурой от скорости капельного соударения при различных значениях начальной длины трещины: 1 — 0,55 мкм; 2 — 1,5 мкм; 3 — 3,0 мкм;
4 — пороговое значение роста острой трещины
Fig. 5. Dependence of crack growth rate in 20Cr13 steel with martensitic structure on drip collision rate for different values of initial crack length: 1 – 0.55 μm; 2 – 1.5 μm; 3 – 3.0 μm; 4 – threshold value of sharp crack growth
Не вдаваясь в детали данной корреляции, которые выполнены при разработке расчетно - аналитической модели, приведем результат использования теории Пэриса - Эрдогана (4)+(5)+(7) с учетом особенностей каплеударного механизма эрозии (6) на примере стали 20Х13 с мартенситной структурой, представленный на рис. 5. Зависимости на рис. 5 можно рассматривать в качестве прикладного критерия эрозионного разрушения , показывающего минимальное значение скорости соударения, при котором инициируется износ в стали. Если график функции на рис. 5 находится ниже линии порогового значения, то расстояние, на которое трещина продвигается за один цикл нагружения, лежит в области упругих деформаций и упруго релаксирует после снятия нагрузки. В этом случае трещина расти не будет. Так, например, из рис. 5 следует, что, если в мартенсите стали 20Х13 уже есть трещины длиной l 0 = 1,5 мкм (линия 2), то они будут развиваться при скоростях соударения V 0 , превышающих 150 м/с.
Обсуждения и заключение. Представленная расчетно - аналитическая модель формирования износа при каплеударной эрозии упрочненных материалов включает две фактически независимых части. В первой из них путем построения диаграммы предельных состояний материала определяются начальный l 0 и критический l C размеры трещин, которые зависят исключительно от структуры и механических свойств материала ( HV, σ B , K 1C ). Во второй части на основе уравнения Пэриса из усталостной теории Пэриса - Эрдогана рассчитывается предельное количество циклов нагружения (число ударов капель, попадающих в одну точку), которое материал может выдержать до начала формирования износа, соответствующего значению l C . При этом параметры уравнения Пэриса для исследуемого материала должны быть определены из эксперимента. Для приблизительной сравнительной оценки допустимо использовать известные типичные значения параметров, которые приводятся в научной литературе, однако, далеко не все типы материалов изучены с точки зрения использования для них уравнения Пэриса. Поэтому сравнение материалов и использование для них типичных значений (не только параметров уравнения Пэриса) следует проводить с обязательным учетом структурных особенностей.
Предложенный в работе расчетный критерий в виде минимальной скорости соударений , при которой инициируется эрозионный каплеударный износ, можно рассматривать как универсальный для любого материала. Аналогичный критерий был апробирован авторами в работе [8] на основе усталостной модели Гудмена для пластичных материалов, в настоящей же работе он использован для упрочненных материалов и рассчитан на базе модели Пэриса-Эрдогана. Это обеспечивает единое измерительное пространство для материалов, деградация поверхности которых при каплеударной эрозии происходит по принципиально различным механизмам — путем развития хрупких трещин в упрочненных материалах (например, в мартенситной стали 20Х13, рассмотренной в настоящей работе) и путем образования усталостной пористости по механизму перколяции в пластичных V0min. материалах (например, в аустенитной стали 08Х18Н10Т, рассмотренной в работе [8]).
Список литературы Оценка эрозионной стойкости упрочненных металлических сплавов в условиях каплеударного воздействия
- Hattori, S., and Takinami, M. Comparison of cavitation erosion rate with liquid impingement erosion rate//Wear. -2010. -Vol.269. -pp. 310-316.
- Рыженков, В. А. Современное состояние и способы решения проблемы эрозионного износа лопаток влажно-паровых ступеней турбин/В. А. Рыженков, А. И. Лебедева, Ал. Ф. Медников//Теплоэнергетика. -2011. -№ 9. -С. 9-13.
- Tobin, E.F., Young, T.M., Raps, D., and Rohr, O. Comparison of liquid impingement results from whirling arm and water-jet rain erosion test facilities//Wear. -2011. -Vol. 271. -pp. 2625-2631.
- Sandeep, Soni. Analysis of liquid droplet erosion for steam turbine blades of composite material//Int. J. Mech. Eng. & Rob. Res. -2012. -Vol. 1, no. 3. -pp. 214-226.
- Kamkar, N., Bridier, F., Bocher, P., and Jedrzejowski, P. Water droplet erosion mechanism in rolled Ti-6Al-4V//Wear of Materials. -2013. -Vol.301, iss.1-2. -pp. 442-448.
- Чижов, А. В. Высокоскоростной удар капли о преграду/А. В. Чижов, А. А. Шмидт//Журнал технической физики. -2000. -Т. 70, вып. 12. -С. 18-26.
- Haller K.K., Ventikos Y., Poulikakos D., Monkewitz P. Computational study of High-speed liquid droplet impact//Journal of Applied Physics. -2002. -Vol. 92, №5. Р.2821-2828.
- Варавка, В. Н. Закономерности износа стали при воздействии дискретного водно-капельного потока. Часть 1: Начальная стадия каплеударной эрозии/В. Н. Варавка, О. В. Кудряков//Трение и износ. -2015. -Т. 36, № 1. -С. 89-99.
- Варавка, В. Н. Закономерности износа стали при воздействии дискретного водно-капельного потока. Часть 2: Стадия развитой каплеударной эрозии/В. Н. Варавка, О. В. Кудряков//Трение и износ. -2015. -Т. 36, № 2. -С. 201-212.
- Кудряков, О. В. К проблеме водородного охрупчивания стали при каплеударной эрозии/О. В. Кудряков //Вестник Дон. гос. техн. ун-та. -2017. -Т. 17, № 2 (89). -С. 56-69.
- Варавка, В. Н. Закономерности и параметры каплеударной эрозии титановых сплавов/В. Н. Варавка //Известия вузов. Северо-Кавказский регион. Технические науки. -2011. -№ 6. -С. 92-98.
- Кинетика зарождения и развития процесса эрозионного разрушения поверхности сталей при каплеударном воздействии/В. А. Рыженков //Надежность и безопасность энергетики. -2012. -№1 (16). -С. 67-71.
- Варавка, В. Н. Прочность и механизмы разрушения высокопластичных материалов при воздействии дискретного водно-капельного потока/В. Н. Варавка, О. В. Кудряков//Вестник Дон. гос. техн. ун-та. -2011. -Т. 11, № 8 (59), вып. 2. -С. 1376-1384.
- Кудряков, О. В. Механизмы формирования эрозионного износа металлических материалов при высокоскоростных капельных соударениях: Ч. 1/О. В. Кудряков, В. Н. Варавка//Материаловедение. -2012. -№ 5. -С. 36-43.
- Кудряков, О. В. Механизмы формирования эрозионного износа металлических материалов при высокоскоростных капельных соударениях: Ч. 2/О. В. Кудряков, В. Н. Варавка//Материаловедение. -2012. -№ 6. -С. 14-19.
- Варавка, В. Н. Особенности разрушения металлических сплавов в условиях устойчивой каплеударной эрозии/В. Н. Варавка, О. В. Кудряков//Известия вузов. Северо-Кавказский регион. Технические науки. -2012. -№ 3. -С. 45-50.
- Кудряков, О. В. Мониторинг начальных стадий эрозионного износа ионно-плазменных покрытий при каплеударном воздействии/О. В. Кудряков, В. Н. Варавка//Упрочняющие технологии и покрытия. -2012. -№ 10. -С. 40-47.
- Штремель, М. А. Прочность сплавов. Ч.2. Деформация/М. А. Штремель. -Москва: МИСиС, 1997. -527 с.
- Эшби, М. Конструкционные материалы. Полный курс/М. Эшби, Д. Джонс. -Долгопрудный: Издательский Дом «Интеллект», 2010. -672 с.
- Механика разрушения и прочность материалов/Под общ. ред. В. В. Панасюка. -Киев: Наукова Думка, 1988. -436 с.
- Справочник по коэффициентам интенсивности напряжений/Ю. Ито, Ю. Мураками . -Москва: Мир, 1990. -448 с.
- Paris P. A critical analysis of crack propagation laws /P. Paris and F. Erdogan//Trans. ASME, J. Basic Engng. -1963. -Vol. 15. -P. 528 -534.