Оценка периода зарождения усталостной трещины от рисок после механической обработки
Автор: Питухин Александр Васильевич
Журнал: Ученые записки Петрозаводского государственного университета @uchzap-petrsu
Рубрика: Технические науки
Статья в выпуске: 1 (90), 2008 года.
Бесплатный доступ
Приведены зависимости для определения числа циклов, после которого усталостная трещина начнет свое развитие из микродефекта при воздействии циклических напряжений, заданных в виде блока и в виде плотности распределения размахов. Рассмотрен случай наличия на поверхности детали рисок после механической обработки и предложены зависимости для определения периода зарождения усталостной трещины в зависимости от параметров шероховатости поверхности.
Период зарождения усталостной трещины, риски от механической обработки, параметр шероховатости поверхности
Короткий адрес: https://sciup.org/14749356
IDR: 14749356
Текст научной статьи Оценка периода зарождения усталостной трещины от рисок после механической обработки
Под действием переменных напряжений в материалах происходит процесс постепенного накопления повреждений, приводящий к образованию трещин, их развитию и разрушению. Различают малоцикловое и многоцикловое разрушения. При малоцикловой усталости имеет место образование петель гистерезиса, поскольку циклическое деформирование происходит в упругопластической области. Число циклов до разрушения обычно не превосходит 105. Элементы конструкций во многих областях машиностроения проектируются на значительно большую циклическую долговечность. Это изделия станкостроительной и автотракторной промышленности, нефтехимического и бумагоделательного машиностроения, подъемно-транспортного и лесного машиностроения, судостроения и многих других отраслей. В связи с вышесказанным мы в дальнейшем будем рассматривать только многоцикловую усталость.
Процесс накопления повреждений делят на несколько стадий: создание характерной микро- структуры и изменение механических свойств, зарождение микротрещин в пределах устойчивых полос скольжения, распространение микротрещин и развитие их в макротрещины, образование магистральной трещины, окончательное разрушение. В расчетной практике обычно ограничиваются двумя укрупненными стадиями: стадией рассеянных повреждений и стадией развития усталостной трещины.
Продолжительность стадий зависит от материала, наличия концентраторов напряжений, размеров дефектов, степени стеснения деформаций, уровня нагруженности. В зонах местных напряжений в условиях стеснения пластических деформаций продолжительность стадии роста магистральной трещины может существенно превышать продолжительность стадии рассеянных повреждений. Так, по данным В. С. Ивановой с соавт. [1], микроскопические трещины наблюдаются уже после 0,1 числа циклов нагружения до разрушения. Относительное время развития микротрещины для образцов с концентраторами достигает 0,2…0,5 и более от общей долговечности.
В настоящее время предложено достаточно много как структурных, так и феноменологических моделей первой и второй стадии усталостного разрушения. Феноменологические (полу-эмпирические) модели основаны на обобщении результатов наблюдений и не ставят целью объяснение или полное описание существа явлений. Структурные модели позволяют описать и объяснить явления исходя из внутренней структуры рассматриваемых объектов. Используются энергетический, деформационный и силовой подходы. Силовые модели нашли наиболее широкое распространение. Заслуживают внимания кинетические уравнения повреждений силового типа и расчеты на их основе, предложенные П. А. Павловым в работе [2]. В. В. Болотиным [3] рекомендуется определять число циклов зарождения N 3 , после которого трещина начнет свое развитие при воздействии циклических напряжений постоянного размаха по формуле:
N C
N3 = -------------—, zAct > ст, (1)
[(xAct - CTth)/ ov ] m3
где N С - постоянная времени;
X - коэффициент концентрации напряжений от микродефектов;
ct^, о th, m з - константы материала (при заданных условиях внешней среды). Константа ctv характеризует сопротивление материала накоплению микроповреждений;
CT th - порог этого сопротивления;
A ct
A CT = СТ max
напряжений
- размах
СТ min ;
цикле;
стmax, ст min - максимальное и минимальное напряжения в цикле нагружения.
Определение периода зарождения усталостной трещины из различных концентраторов напряжений для получения расчетных оценок показателей надежности является важной задачей, так как в большинстве случаев трещина образуется именно на дефектах, являющихся концентраторами напряжений.
Формула (1) определяет число циклов, после которого трещина начнет свое развитие из микродефекта при воздействии циклических напряжений постоянного размаха A ct . При задании нагрузки в виде блока при предположении о справедливости гипотезы линейного суммирования усталостных повреждений и условия начала роста трещины
m у П = 1, у Ni используя зависимость (1), получим
N з = П б
N c CT m3
ZnXtCT- ст. ) m3
i = 1
Инкубационный период, выраженный в единицах наработки, определится по аналогии с (2) как
N c CT Im 3
Т з = Т б
m
У n(xACTi- CTth) m3
i = 1
Наработка до отказа с учетом двух стадий развития усталостной трещины запишется в виде:
T = Т з + T p ; N = N 3 + N p . (4)
Число циклов N p , называемое остаточным ресурсом, определяет период распространения усталостной трещины, или живучесть.
В случае задания нагруженности в виде плотности распределения размахов действующих напряжений не представляет трудности на основе формулы (2) получить зависимость:
____________NcCT1m3____________
CT j f ( A ct )( xAct - CT th ) m3 d A ct
CT th
Определим период зарождения трещины от рисок после механической обработки. Для этого необходимо найти выражение для коэффициента концентрации напряжений x , вызванных этими рисками. В работе В. А. Пальмова с соавторами [4] решена задача теории упругости о напряженном состоянии тела со случайной шероховатой поверхностью. Решение для коэффициента концентрации при растяжении полуплоскости с синусоидальной границей, образованной системой периодически повторяющихся выступов и впадин, получено в виде:
A
X = 1 + 4nT, где A - высота выступов;
T - шаг.
В той же работе [4] рекомендуется для практических расчетов более грубая оценка коэффициента концентрации, которая хорошо согласуется с экспериментальными данными по усталости стальных образцов:
X = 1 + 4 п /2 ^a . (6)
В рабочих чертежах на детали и элементы конструкций оговариваются параметры шероховатости поверхности и проставляется предельно допустимая высота неровностей профиля по десяти точкам R z или среднеарифметическое значение отклонения профиля от средней линии R a . Поэтому выразим коэффициент концентрации через R z . R z определяется как среднее расстояние между пятью высшими и пятью низшими точками профиля в пределах базовой длины l б [5]. ГОСТ 2789-73 распространяется на шероховатость поверхностей с интервалами R z =1600-0,025 мкм; R a =100…0,008 мкм;
l б =25…0,01 мм. Причем для точения, строгания и фрезерования можно принять R max = 6 R a ;
Таблица 1
Расчетные коэффициенты концентрации напряжений для обработанных поверхностей
Класс шероховатости |
R z , мкм |
X |
4 |
от 40 до 20 |
от 3,22 до 2,11 |
5 |
от 20 до 10 |
от 2,11 до 1,56 |
6 |
от 10 до 6,3 |
от 1,56 до 1,35 |
7 |
от 6,3 до 3,2 |
от 1,35 до 1,18 |
8 |
от 3,2 до 1,6 |
от 1,18 до 1,09 |
R z = 5 R a [6]. Здесь R max - наибольшая высота неровностей профиля. Полагая профиль шероховатостей синусоидальным со случайным значением амплитуды R z 2 и постоянным шагом l б 5, получим
X = 1 + 44,4 Rz- . (7) l б
Здесь R z входит в мм.
В таблице 1 приведены значения коэффициентов концентрации напряжений, подсчитанные по зависимости (7) при l б =0,8 мм. Они достаточно хорошо совпадают с результатами, приведенными в работе [4, с. 292, 293], где рекомендуется для 5-го класса шероховатости при обработке шлифованием коэффициент концентрации 2,44, а для восьмого класса - 1,44.
Используя (3) с учетом (7), получим зависимость для определения периода зарождения трещины от рисок механической обработки:
Т з = Т б •
N o т з
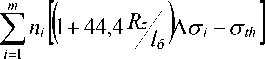
Оценивание статистических характеристик наработки до отказа в этом случае осуществляем в следующем порядке.
-
1. Задаем число испытаний N 1 , внешнюю нагрузку и другие необходимые данные.
-
2. Моделируем на ЭВМ по соответствующим законам распределения случайную реализацию вектора начальных параметров.
-
3. Располагаем уровни нагрузки в блоке нагружения в случайном порядке.
-
4. Подсчитываем период зарождения TЌ по зависимости (8).
-
5. Подсчитываем по рекуррентным формулам (4.47) и (4.50), полученным в работе [7], текущие значения длины трещины и коэффициента интенсивности напряжений (КИН), сравнивая его с предельным значением K fc (или K IC ).
-
6. Вычисления на 5-м шаге осуществляем до выполнения условия A K I > A K f c v 1 > lc, после чего определяем остаточный ресурс T p .
-
7. Определяем наработку до отказа Т = Т з + Т р .
-
8. Повторяем вычисления по пунктам 2-6 N 1 раз для получения последовательности (выборки) { Т } объемом N 1 .
-
9. Обработка выборки с использованием программ статистической обработки из математического обеспечения ЭВМ для оценивания средней наработки до отказа T , среднего квадратического отклонения ст ? , вероятности безотказной работы.
Полагаем 1 0 = R max/ 2 = R /2 .
При использовании аналитических зависимостей (4.40), (4.41), (4.44) и (4.45) из работы [7] для оценки длительности периода распространения усталостной трещины вместо пунктов 5 и 6 приведенного алгоритма следует применить какую-либо из вышеуказанных аналитических зависимостей.
Предложенной моделью можно пользоваться и при наличии других микродефектов. В этом случае необходимо в зависимости от них определять коэффициент концентрации х и использовать формулу (2).
Разработанные методы рекомендуется использовать при оптимальном проектировании, для задач технической диагностики, а также непосредственно в расчетах. Кроме того, они могут входить как составная часть в пакеты САПР, в экспертные системы.
Список литературы Оценка периода зарождения усталостной трещины от рисок после механической обработки
- Иванова В. С., Терентьев В. Ф. Природа усталости металлов. М.: Металлургия, 1975. 455 с.
- Павлов П. А. Основы инженерных расчетов элементов машин на усталость и длительную прочность. Л.: Машиностроение, 1988. 252 с.
- Болотин В. В. Механика зарождения и начального развития усталостных трещин//Физико-химическая механика материалов. 1986. № 1. С. 18-23.
- Хусу А. П., Витемберг Ю. Р., Пальмов В. А. Шероховатость поверхностей. Теоретико-вероятностный подход/М.: Наука, 1975. 344 с.
- Комбалов В. С. Оценка триботехнических свойств контактирующих поверхностей. М.: Наука, 1983. 136 с.
- Справочник технолога-машиностроителя: В 2 т./Под ред. А. Г. Косиловой и Р. К. Мещерякова. 4-е изд., перераб. и доп. М.: Машиностроение, 1986. Т.1. 655 с.
- Питухин А. В. Вероятностно-статистические методы механики разрушения и теории катастроф в инженерном проектировании. Петрозаводск: Изд-во ПетрГУ, 1998. 304 с.