Оценка триботехнических свойств консолидированных материалов, полученных методом электроискровой обработки
Автор: Величко Сергей Анатольевич, Мартынов Алексей Владимирович, Мартынова Елена Геннадьевна
Журнал: Инженерные технологии и системы @vestnik-mrsu
Рубрика: Технологии, машины и оборудование
Статья в выпуске: 1, 2023 года.
Бесплатный доступ
Введение. К сельскохозяйственной отрасли глубокой переработки сырья с ориентацией на конечного потребителя относится хлебопекарная промышленность. При производстве хлебобулочных изделий одну из операций технологического процесса выполняют тестоделительные машины вакуумно-поршневого типа, срок службы которых на 30-40 % ниже нормативного. Наиболее перспективным для восстановления изношенных деталей механизма всасывания является метод электроискровой обработки. При выборе материалов электрода важно, чтобы они обладали не только низкой эрозионной стойкостью, но и высокими триботехническими свойствами. Цель статьи. Выбрать электроискровые покрытия, снижающие изнашивание рабочих поверхностей деталей механизма всасывания при ремонте тестоделительных машин вакуумно-поршневого типа. Материалы и методы. Определение свойств электроискровых покрытий проводилось методами неразрушающего контроля с использованием современного научно-исследовательского оборудования, а обработка результатов с использованием программы «Компас-3D». Результаты исследования. Получены значения физических, механических, фрикционных и триботехнических свойств электроискровых покрытий из бронзы БрОС10-10 и сплава X15H60. Суммарная интенсивность изнашивания для покрытия из бронзы БрОС10-10 составила 8,3 ∙ 10-12, а для сплава Х15Н60 15 ∙ 10-12. Обсуждение и заключение. Суммарная интенсивность изнашивания на машине трения у образцов с покрытием из бронзы БрОС10-10 ниже, чем у базовой пары трения, в 1,4 раза, а у образцов с покрытием из сплава X15H60 выше в 1,26 раза. Добавление твердосмазочного покрытия MODENGY на покрытие из сплава X15H60 способствует снижению его истирающей способности в 3 раза, а суммарной интенсивности изнашивания - в 1,34 раза относительно базовой пары трения. Расчетно-экспериментальный метод показал низкую интенсивность изнашивания электроискровых покрытий из бронзы БрОС10-10 и сплава X15H60 по отношению к материалу деталей механизма всасывания тестоделительных машин вакуумно-поршневого типа.
Тестоделительная машина вакуумно-поршневого типа, электроискровая обработка, интенсивность изнашивания, разрушающее напряжение, модуль упругости, фрикционные параметры
Короткий адрес: https://sciup.org/147240169
IDR: 147240169 | DOI: 10.15507/2658-4123.033.202301.079-099
Текст научной статьи Оценка триботехнических свойств консолидированных материалов, полученных методом электроискровой обработки
Пищевая индустрия занимается переработкой сельскохозяйственной продукции с ориентацией или на источники сырья, или на конечного потребителя.
Хлебопекарная промышленность относится к сельскохозяйственной отрасли глубокой переработки сырья и обеспечивает население страны продуктами первой необходимости: хлебом,
Vol. 33, no. 1. 2023 хлебобулочными и бараночными изделиями.
При производстве хлебобулочных изделий наиболее важным является получение заготовок теста одинаковой массы. Эту операцию выполняют тестоделительные машины1. Широкое применение в хлебопекарной промышленности по способу нагнетания теста находят тестоделительные машины вакуумно-поршневого типа, достоинством которых является точное деление тестовых заготовок массой от 50 г из ржаной и пшеничной муки. Они бережно относятся к тесту, не травмируют клейковину. К одной из таких машин, широко используемых на территории России и стран СНГ, относится ТД-4 фирмы ЗАО НПП «Восход» (рис. 1) [1].
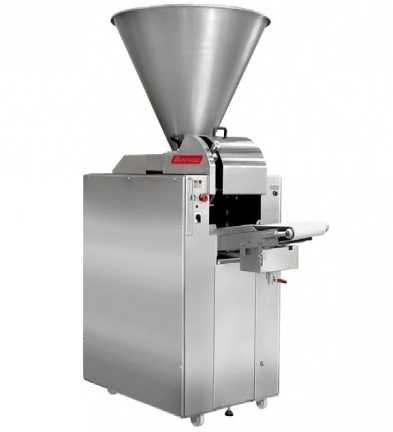
Р и с. 1. Общий вид тестоделительной машины ТД-4
F i g. 1. General view of the TD-4 dough divider
I I s)
Cрок службы тестоделительных машин при соблюдении всех регламентов эксплуатации, указанных в технической документации, составляет более 10 лет [1]. Однако в реальных условиях эксплуатации срок службы не превышает 6–7 лет [1; 2].
Работоспособность тестоделительных машин вакуумно-поршневого типа определяет механизм всасывания делительного устройства, при износе деталей которого происходит потеря вакуума и, как следствие, нарушается точность развесовки теста.
В настоящее время ремонт тестоделительных машин осуществляется полной заменой узла механизма всасывания на новый, изготовленный под заказ заводом-изготовителем. Себестоимость такого ремонта достигает 30–40 % от стоимости новой машины, а срок окупаемости составляет 3–4 года в зависимости от номенклатуры хлебобулочных изделий и режима работы оборудования [3; 4].
Анализ методов восстановления деталей показал, что наиболее перспективным для восстановления деталей является метод электроискровой обработки (ЭИО). Из таблицы 1 видно, что источники энергии для формирования электрической искры в газовой среде обладают лучшими энергетическими характеристиками2 [5; 6].
Сравнение гальванических методов и электроискровой обработки по техникоэкономическому критерию показал, что во втором случае комплексный показатель оценки ниже в 5,1 раза3 [5].
Т а б л и ц а 1
T a b l e 1
Энергетические характеристики термических источников энергии, применяемых для восстановления параметров изношенных деталей
Energy characteristics of thermal energy sources used to restore the parameters of worn parts
Сущность метода электроискровой обработки состоит в том, что под воздействием электрического импульсного разряда в газовой среде происходит преимущественно эрозия материала анода и перенос продуктов эрозии на катод.
В отличие от технологий, где источник тепла и рабочий материал формируются отдельно, электрическая искра как технологический инструмент осуществляет разрушение электрода и формирование на поверхности детали покрытия с измененным поверхностным слоем (ИПС) [7; 8].
В результате высокой мощности энергии в пятне нагрева импульсного действия и перемещения материала в ИПС, в зависимости от выбранных электродных материалов и принятых 82
режимов в широком диапазоне, изменяются физико-механические свойства рабочих поверхностей деталей, что в конечном итоге позволяет формировать покрытия с высокими триботехническими свойствами.
Прогнозирование высоких триботехнических свойств электроискровых покрытий объясняется не только структурными изменениями, но и особенностями параметров топографии. Их текстура имеет специфический рельеф в виде замкнутых впадин, так называемых масляных карманов (МК). Наличие МК способствует удержанию объема смазки, улучшающего диссипативные характеристики поверхности трения, что способствует снижению интенсивности изнашивания наносимого металлопо-крытия4 [9].
Цель исследования – выбор электроискровых покрытий, обеспечивающих снижение интенсивности изнашивания рабочих поверхностей деталей механизма всасывания при ремонте тестоделительных машин вакуумно-поршневого типа.
Обзор литературы
На этапе выбора материала электрода для восстановления и обеспечения высоких триботехнических свойств, при разработке технологического процесса, применяется расчетно-экспериментальной метод, позволяющий определить соотношение интенсивностей изнашивания создаваемых покрытий с базовыми образцами.
Исследования показали, что расчетная интенсивность изнашивания при упругом контакте пар трения будет определяться по формуле:
I = K 2 • a • K v
i + -y^
• p 2 v + 1 x
2vty vty x E2 v+1 • A2 v+1 •

t y
где K – коэффициент, равный
-
-1--1- -1-
- K2 = 0,5 y 2v • 22v • K1; K 1 - коэффициент, зависящий от геометрии и высоты единичных неровностей на поверхностях твердых тел; α – коэффициент перекрытия, равный α = Aa / Ar (Aa – номинальная площадь контакта, Ar – фактическая площадь контакта); Ktv – поправочный коэффициент числа циклов до отделения частицы износа; ty – показатель кривой фрикционной усталости при упругом контакте; v – параметр формы опорной кривой; E – модуль упругости покрытия (модуль Юнга), кгс/см2;
p – эксплуатационная нагрузка в паре трения, кгс/см2; ∆ – комплексная шероховатость поверхности; k – коэффициент, характеризующий напряженное состояние на контакте; σ0 – разрушающее напряжение при однократном растяжении (σ0 = σ2), кгс/см2. Более подробно эти данные представлены в работе Е. Г. Мар-тыновой5.
Во время работы тестоделительной машины происходит приработка деталей механизма всасывания друг к другу. При этом на поверхностях деталей устанавливается равновесная шероховатость, из-за чего влияние параметров микрогеометрии становится минимальным [10–12].
Тогда для приработанных поверхностей молекулярная составляющая коэффициента трения f М будет определяется по формуле:
-
f . - 1,4. P°^5t + ^ , (2) E
где τ0 (кгс/см2) и β – фрикционные параметры покрытия; α Г – коэффициент гистерезисных потерь. Для нанесенного покрытия из сплавов Х15Н60 и бронзы БрОС10-10, α Г= 0,04 [13].
Из выражения (2) следует, что коэффициент трения f М для приработанных поверхностей практически не зависит от давления в паре трения и их микрогеометрических характеристик.
Устанавливающаяся после приработки пар трения равновесная шероховатость поверхностей определяется по выражению [13]:
5/4
1510
A E3/4 • p1/2 • a3/4.
Тогда формула расчета интенсивности изнашивания пар трения (1), имеющих упругий контакт в случае контактирования приработанных поверхностей, с учетом выражения (3), запишется:
’
I = K • 15 5 • a • K. • p x 2 tv ty ty xE2 • T0'2 • — •[ f' I . (4) a r' I ° 0 )
Таким образом, при упругом виде контактного взаимодействия приработанных поверхностей на интенсивность изнашивания влияют механические, физические и фрикционные свойства поверхности изнашивающейся детали и молекулярная составляющая коэффициента трения.
В настоящее время в научной литературе имеется ограниченное количество публикаций, описывающих результаты экспериментальных исследований механических, физических и фрикционных свойств консолидированных материалов, полученных методом электроискровой обработки. Недостаточная изученность свойств покрытий объясняется низким уровнем апробации методик неразрушающего контроля применительно к электроискровым покрытиям.
В последние годы получен ряд ответов на вопросы трибологического материаловедения в области изучения свойств электроискровых металлопокрытий.
Представлены результаты исследования разрушающего напряжения при однократном растяжении σ 0. Для этого по остаточному отпечатку, равному 1 мм, на глубине 0,1 мм от шарикового наконечника диаметром 2,5 мм фиксировалось
Том 33, № 1. 2023
значение максимальной нагрузки. Затем по экспериментальным зависимостям находилось значение σ 0. Расхождение результатов эталонных образцов по данной методике составило не более 5 %6.
Результаты оценки модуля упругости покрытия из сплава Х20Н80 методом инструментального индентирования, основанного на построении диаграммы зависимости нагрузки, приложенной к индентору от глубины его проникновения во время нагружения и разоружения, представлены в ряде работ7 [9]. Расхождение результатов эталонных образцов и покрытий из сплава Х20Н80 по данной методике составило не более 7 %.
Таким образом, можно отметить, что имеющиеся и хорошо апробированные методы и средства измерения позволяют с высокой степенью достоверности определять физико-механические и фрикционные свойства электроискровых покрытий [14; 15].
Материалы и методы
Для расчета интенсивности изнашивания электроискровых покрытий по формуле (4) необходимо определить физические, механические и фрикционные свойства.
Для расчета интенсивности изнашивания электроискровых покрытий по формуле (4) наносимых на рабочие поверхности деталей ресурсоопределяющего узла механизма всасывания необходимо определить физические, механические и фрикционные свойства [16; 17].
Расчет интенсивности изнашивания покрытий проведен при наибольшей эксплуатационной нагрузке, действующей на детали сопряжения «поршень – камера», равной 3,2 МПа.
Для проведения исследований по определению составляющих параметров на поверхность образцов, изготовленных из сплава ЧН19Х3Ш, были нанесены покрытия из хромоникелевого сплава марки Х15Н60 и оловянисто-свинцови-стой бронзы марки БрОС10-10 методом электроискровой обработки на установке «БИГ-5» (фирма SCINTI, Молдова) в ручном режиме с количеством энергии 300 Дж, частотой импульсов 50 Гц, а также удельным временем обработки 27 с/см2. Полученная толщина покрытия достаточна для компенсации износов поверхностей деталей механизма всасывания.
Параметр шероховатости Rα на участках основного профиля исследуемого электроискрового покрытия после механической обработки составляет не более 0,2 мкм по ГОСТ 2789-73.
Принятое количество образцов для каждого эксперимента при доверительной вероятности α 0 = 0,9, относительной ошибке δ = 10 % и ожидаемом коэффициенте вариации V = 0,1 принято равным 8 шт. [16].
Для определения разрушающего напряжения при однократном растяжении (4) σ0 были изготовлены образцы размером 15×15×10 мм. В поверхность испытуемого образца на глубину 0,1 мм вдавливается шариковый наконечник диаметром 2,5 мм до получения остаточного отпечатка диаметром 1 мм9 [17]. При этом фиксируется максимальное значение нагрузки Pmax.
Затем рассчитывается максимальная твердость Н max по уравнению:
Н
max
1,32 Р max ,
где Р max – максимальная нагрузка, Н.
По экспериментальной зависимости, представленной в другой работе10, между максимальной твердостью H mах и пределом прочности исследуемых покрытий σ в находится значение σ в.
Для измерения диаметра отпечатков d в двух взаимно перпендикулярных направлениях с точностью измерений ±0,02 мм использовался анализатор Siams 700, установленный на базу оптического микроскопа Olympus GX51. Повторность измерений на каждом образце составляла 5 вдавливаний.
Измерение модуля упругости покрытий проводится методом инструментального индентирования, основанного на построении диаграммы зависимости нагрузки, приложенной к индентору от глубины его проникновения, во время нагружения и разгружения11 [18; 19]. Общий вид диаграммы представлен на рисунке 3.
Для получения кривых 1 и 2 (рис. 3) в качестве нагрузочно-разгрузочного устройства используется машина Hegewald & Peschke Inspekt table 50 кН (рис. 4). Для эксперимента были изготовлены образцы размером 15×15×10 мм.
-
9 Оценка относительного удлинения покрытий…
-
10 Совершенствование методики определения модуля упругости…
a)
b)
Р и с. 2. Испытательная машина Hegewald & Peschke: a) общий вид; b) интерфейс машины F i g. 2. Hegewald & Peschke testing machine: a) general view; b) machine interface
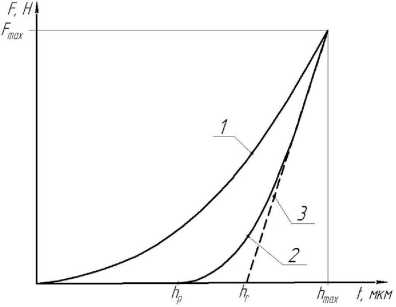
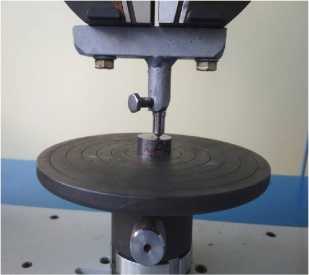
Р и с. 3. Зависимость нагрузки от глубины индентирования: 1 – кривая нагружения; 2 – кривая разгружения;
-
3 – касательная к кривой разгружения 2 ; hr – точка пересечения касательной 3 с осью перемещения; hp – точка пересечения кривой разгружения 2 с осью перемещения;
h max – максимальная глубина внедрения индентора
F i g. 3. Dependence of load on the indentation depth: 1 ‒ loading curve; 2 ‒ unloading curve; 3 ‒ tangent to the unloading curve 2 ; hr ‒ point of intersection of tangent 3 with the axis of movement; hp ‒ point of intersection of the unloading curve 2 with the axis of p movement; h max ‒ maximum depth of indentor introduction
К подвижной (верхней) траверсе крепилось приспособление, в которое устанавливался алмазный индентор Виккерса, а на неподвижную (нижнюю) траверсу устанавливался испытуемый образец (рис. 4)12 [18; 19].
При вдавливании алмазного индентора в поверхность образца фиксируется максимальное значение заданной нагрузки F max. Зависимость приложенной нагрузки к индентору от глубины его проникновения в поверхность испытуемого образца (линия 1 рис. 3) появляется автоматически на мониторе испытательной машины. При измерениях индентор внедряется в испытуемую поверхность образца на минимальную глубину 50 мкм. Затем после выдержки индентора под нагрузкой в течение 15 с осуществляется полная разгрузка образца с получением графической зависимости (линия 2 рис. 3). По полученной линии 2 графически строится касательная линия 3 при нагрузке F max.
По данным литературных источни-ков13 [20], модуль упругости при инден-тировании EIT равен
Ap – площадь поперечного сечения поверхности в контакте (для индентора Виккерса A p = 4, 950 h c , мкм2); hc – глубина внедрения наконечника в испытуемый образец.
Величина hc вычисляется по формуле:
hc = hmax - e (hmax " hr ), (8)
где h max – глубина, соответствующая максимальной нагрузке F max (рис. 3), мкм; ε – поправочный коэффициент (для индентора Виккерса ε = 3/4); hr – точка пересечения касательной 3 с осью t , мкм (рис. 3).
Для определения податливости C (7) используется выражение:
C dw dhc
" dF ” dF ’
E IT
1 "V. )2
1 1 "V, )2, —
E r E i
где vs – коэффициент Пуассона испытуемого материала; vi – коэффициент Пуассона индентора (для алмазного индентора νi = 0,07); Ei – модуль упругости индентора (для алмазного индентора Ei =11,4 ∙ 105 Н/мм2); Er – приведенный модуль упругости в области индентиро-вания, Н/мм2.
Модуль упругости Er в области ин-дентирования равен
Л
Er= 2CjAp ’
где C – податливость в контакте индентора с испытуемым образцом;
где w – тангенс угла наклона линии dF начала разгружения (определяется по
касательной линии 3 , рис. 3); c dF
– по-
датливость прибора, равная величине
обратной его жесткости14 [20].
то податливость рамы, определяемая по формуле (9), будет равна 80,6 ∙ 10–7 мм/Н. При изменении конструкции верхней траверсы машины (рис. 4) общая жесткость снизилась, а податливость увеличилась до значения 26,7∙ 10–6 мм/Н.
Определение фрикционных параметров τ 0 и β взаимодействия двух твердых тел осуществляется по ГОСТ 27640-88.
Для их определения используется способ, заключающийся в относительном движении деформированных поверхностных слоев с пренебрежимо малой величиной сопротивления.
-
13 Sosnovskiy L. A., Makhutov N. A., Troshchenko V. T. Evolution of Ideas on Fatigue of Metals by Volume Loading and Friction // VI Междунар. симпозиум по трибофатике МСТФ 2010. Минск, 2010. С. 77–84. URL: https://www.elibrary.ru/item.asp?id=41104417 (дата обращения: 01.05.2021).
-
14 Там же.
Это достигается, если индентор 1 (рис. 5), изготовленный в виде сферы, сдавливать между двумя плоскопараллельными образцами 2 и 3 нормальной силой P . После приложения силы индентор необходимо вращать15 [20].
Особенностью устройства является создание точной нагрузки на образцы с погрешностью ±0,5 % в диапазоне от 1 до 50 000 Н, а также измерение момента трения с погрешностью ±5 % в интервале от 0,1 до 20 Н·м. Все результаты по значениям нагрузки и моменту трения автоматически передаются на ПК сбора данных.
Том 33, № 1. 2023
Вращающийся образец выполнен из стали ШХ15 диаметром 15 мм, а плоские контробразцы – размером 15×15×10 мм.
При проведении испытаний образец устанавливается относительно края контробразца на расстоянии не менее 10 мм.
Затем к верхнему контробразцу в два этапа прикладывается нагрузка. На первом этапе нагрузка должна быть такой, чтобы остались отпечатки диаметром 1–2 мм на контробразцах.
После выдержки образцов и контробразцов этой нагрузке в течение 3–6 с проводится вращение образца с частотой 2 об/мин. При повороте на 30–60° и до углового перемещения на 90° непрерывно регистрируется значение момента сил трения m . После этого нагрузка снимается, а образец и контробразцы смещаются друг относительно друга на расстояние не менее 15 мм до другого
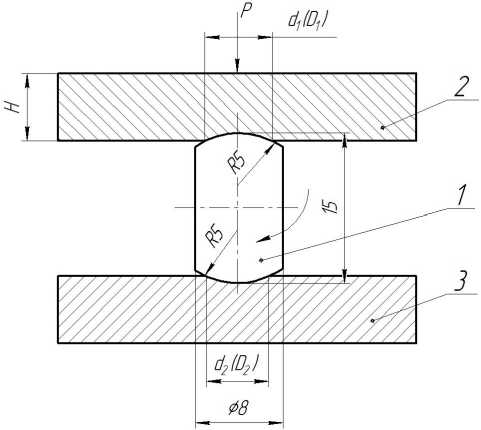
Р и с. 5. Схема определения фрикционных параметров τ 0 и β : 1 – вращающийся образец; 2, 3 – плоские контробразцы; d 1, d 2 – диаметры отпечатков верхнего контробразца; D 1, D 2 – диаметры отпечатков нижнего контробразца
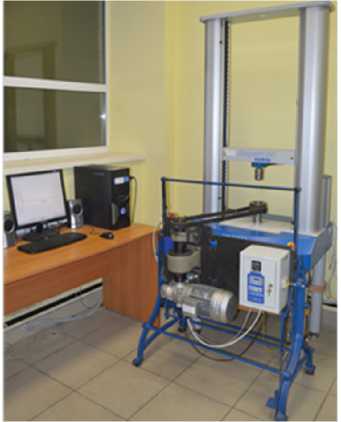
Р и с. 6. Общий вид устройства для определения фрикционных параметров пар трения
F i g. 5. Scheme for determining the friction parameters τ 0 and β : 1 – rotating sample; 2, 3 – flat test pieces; d 1, d 2 ‒ diameters of the upper test piece imprints; D 1, D 2 – diameters of the lower test piece imprints
F i g. 6. General view of the device for determining the friction parameters of friction pairs
центра отпечатка. Нагрузка при втором нагружении отличается на 15–20 %.
После испытаний образцы снимаются с испытательной установки, обезжириваются, а затем на верхнем и нижнем контробразце измеряются диаметры отпечатков в двух взаимно перпендикулярных направлениях при первом и втором нагружении с помощью профилографа–профилометра Form Talysurf фирмы Taylor Hobson.
Для измеренных диаметров отпечатков находятся их среднее значение отдельно для верхнего и нижнего контробразцов:
( d 0 + d 90 ) + ( d 20 + d 90 )
= 4 ,
( D + D 190 ) + ( D 0 + D 2 90 )
D = 4
где d 1, D 1 и d 2, D 2 – диаметры отпечатков на первом и втором контробразцах соответственно при первом и втором нагружении, мм.
Полученные значения диаметров отпечатков d, D и соответствующие им величины моментов сил трения m и M используются для определения фрикционных параметров τ0 и β по формулам т 0
0, 75
я ( ^ 2 - ^ )
m ° 2
J 0,5 d ) 3
M ^ i
( 0,5 D )3 у
P -
0, 75
л ( ^ 2 - ^ 1 )
M

m
( 0,5d ) 3 v
4P 4P где C1 = —2, о2 = —22 - средние вели-rnd nD чины нормальных контактных напряжений при первом и втором нагружениях соответственно, МПа.
Известно, что сопротивление разрушению при контактном взаимодействии пар трения, характеризуется кривой фрикционной усталости (кривая Велера). Кривая Велера показывает зависимость усилия, приложенного к поверхности материала F, от числа циклов его повторения n до предельного разрушения материала поверхностного слоя [20].
Испытания поверхностей образцов на фрикционную усталость проведены на трибометре TRB-S-DE (рис. 7).
Для проведения исследований были изготовлены цилиндрические образцы диаметром 20 мм и толщиной 10 мм. В качестве индентора использовался стальной шарик марки ШХ15 диаметром 3 мм.
Скорость вращения образца задается при условии отсутствия нагрева в паре трения (9 ∙ 10–3 м/сек) и автоматически поддерживалась в процессе всего испытания [21].
Нагрузка, действующая на индентор, подбирается таким образом, чтобы отсутствовал процесс резания. После определения количества циклов до отделения частиц с поверхности материала по скачку коэффициента трения и образованию усталостных трещин на бороздке нагрузка снижается на 15–20 % и эксперимент повторяется до получения координат второй точки.
По координатам двух точек строится график зависимости количества циклов от величины действующей нагрузки (рис. 8).
Затем с использованием программы «Компас-3D» определяется угол наклона построенной прямой к оси ne . Найденный угол наклона используется для определения коэффициента фрикционной усталости ty по формуле:
t y = ctg a , y . (10)
Триботехнические испытания образцов пар трения без покрытий и обработанных методом электроискровой обработки проводили на модернизированной
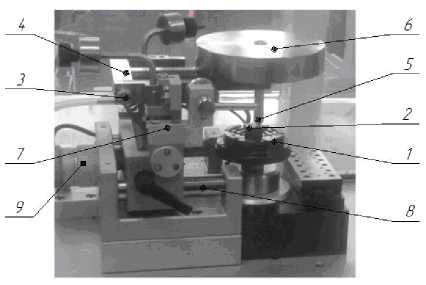
Р и с. 7. Общий вид трибометра TRB-S-DE: 1 – столик с вращательным движением; 2 – образец; 3 – ось; 4 – подвижная стойка; 5 – индентор; 7 – корпус;
8 – направляющие; 9 – микрометрический винт
F^H
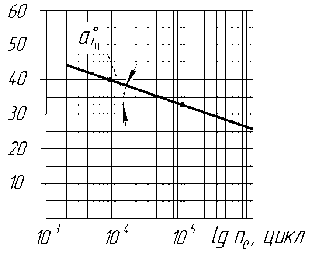
Р и с. 8. График зависимости F t от ne
F i g. 8. The graph of the dependence of F t on ne
F i g. 7. General view of the TRB-S-DE tribometer: 1 – table with a rotational motion; 2 – sample; 3 – axis; 4 – sliding bar;
5 – indentor; 7 – body; 8 – guides; 9 – micrometer screw машине трения СМТ-1М по типу «колодка – ролик» [22]. Машина трения СМТ-1М позволяет автоматически снимать комплекс триботехнических параметров.
Материал и размеры образцов, принятые для испытаний, представлены в таблице 2.
Триботехнические параметры, такие как максимальная нагрузка до предза-дира, коэффициент и момент трения, интенсивность изнашивания для базовой пары трения (табл. 2), определялись по ГОСТ 23.224-86.
Для остальных образцов определялась только интенсивность изнашивания при нагрузке в паре трения 3,2 МПа. Время стационарных испытаний составляло 8 ч.
Образцы прирабатывались друг к другу до площади прилегания не менее 90 %. Она контролировалась методом планиметрирования пятен контакта с погрешностью не более 1 %. После этого образцы маркировались, промывались в ацетоне, высушивались и взвешивались.
Подготовленные образцы устанавливали на машину трения и приводили в движение подвижный образец с частотой 300 об/мин (скорость скольжения пары трения 0,8 м/с). Использовали смазочный материал (масло индустриальное И-20А) по ГОСТ 20779-75, подача смазки разовая в картер.
После каждого вида испытаний образцы промывались в ацетоне, просушивались, а затем взвешивались на аналитических весах c точностью измерения до 0,00001 г с трехкратной повторностью.
Интенсивность изнашивания образцов определялась по формуле:
W L,
где W – линейный износ образца за пройденный путь, м; L – пройденный путь трения образца за время испытаний, м.
Линейный износ образцов определялся по формуле:
W =
A G
Г ■ F c ’
где A G - изменение массы образца от начала до конца испытаний, кг; γ – плотность испытуемого материала, кг/м3; Fc – контурная площадь контакта образцов, м2.
Т а б л и ц а 2
T a b l e 2
Параметры образцов для триботехнических испытаний
Parameters of samples for tribotechnical tests
Колодка / Pad Ролик / Roller

Размеры, мм / Dimensions, mm
А ВСD E F
25 34 10 45° 50
чугун ЧН19Х3Ш / cast iron ChN19Kh3Sh чугун ЧН19Х3Ш + бронза БрОС10-10 / cast iron ChN19Kh3Sh + bronze BrOS10-10
чугун ЧН19Х3Ш + сплав Х15Н60 / cast iron ChN19Kh3Sh + alloy Kh15N60
чугун ЧН19Х3Ш + сплав Х15Н60 + + MODENG Y ПТФЭ-А20 / cast iron ChN19Kh3Sh + alloy Kh15N60 + + MODENGY PTFE-A20
Пройденный путь трения образца за время испытаний [22]:
L - N • l, (13)
где l – линейный размер поверхности трения сопряженного образца, м; N – число циклов за время прохождения пути l .
Для пары трения интенсивность изнашивания I Σ определяется как сумма интенсивностей изнашивания колодки и ролика.
Результаты исследования
Проведенные триботехнические испытания образцов пар трения «колодка – ролик», выполненных из материала деталей механизма всасывания (чугун ЧН19Х3Ш), показали, что суммарная интенсивность изнашивания при эксплуатационной нагрузке в паре трения 3,2 МПа составила Technologies, machinery and equipment чугун ЧН19Х3Ш / cast iron ChN19Kh3Sh чугун ЧН19Х3Ш / cast iron ChN19Kh3Sh чугун ЧН19Х3Ш / cast iron ChN19Kh3Sh чугун ЧН19Х3Ш / cast iron ChN19Kh3Sh
18 ∙ 10 ‒ 12, что относится ко 2-му классу износостойкости [9; 14]. Таким образом, пара трения «колодка – ролик», выполненная из высоколегированного чугуна ЧН19Х3Ш, имеет упругий вид контактного взаимодействия поверхностей [9].
Полученные результаты физических, механических, фрикционных параметров и расчетных значений интенсивности изнашивания электроискровых покрытий представлены в таблице 3.
Согласно представленным в таблице 3 результатам расчетного и экспериментального исследования интенсивность изнашивания высоколегированного чугуна ЧН19Х3Ш с электроискровым покрытием из бронзы БрОС10-10 в 1,461 раза ниже базового образца, а с электроискровым покрытием из сплава Х15Н60 – ниже в 1,31 раза.
Т а б л и ц а 3
T a b le 3
Результаты физических, механических, фрикционных параметров и расчетных значений интенсивности изнашивания
Results of physical, mechanical, friction parameters and calculated values of wear rate
Бронза БрОС10-10 / Bronze BrOS10-10
Сплав Х15Н60 / Alloy Kh15N60
1,14 2,31,110,04 3 1,5
1,22 2,21,11 0,04 3 1,5
Материал покрытия / Coating material |
Коэффициенты / Coefficients |
ν |
p, кгс/см2 / p, kgf/cm2 |
Определяемые параметры / Defined parameters |
Интенсивность изнашивания, I × 10–12 / Wear rate, I × 10–12 |
|||||||||
К 2× 10–2 |
К tν |
α |
αГ |
k |
фрикционные / frictional |
физические / physical |
механические / mechanical |
I теор |
I экс |
|||||
t у |
τ 0, кгс/см2 / τ 0, kgf/cm2 |
β |
Е , кгс/см2 / Е , kgf/cm2 |
σ 0, кгс/см2 / σ 0, kgf/cm2 |
32 5,8 172 0,021 1 140 000 3 820 4,62
6,8
32 5,7 175 0,023 1 680 000 4 740 5,23
Таким образом, исследуемые материалы обладают высокими антифрикционными свойствами и их целесообразно использовать для восстановления изношенных рабочих поверхностей деталей.
В таблице 4 представлены результаты триботехнических характеристик колодки и ролика, изготовленных из высоколегированного чугуна ЧН19Х3Ш базовых образцов, полученных по ГОСТ 23.224-86.
Т а б л и ц а 4
T a b le 4
Статистические характеристики параметров выборок трибосопряжений базовых образцов Statistical characteristics of the sample parameters of the tribocouple base samples
Окончание таблицы 4 / End of table 4
1 л |
2 |
] 3 |
4 1 |
5 |
6 |
Оптимальное давление в паре трения P ОП, МПа / Optimal pressure in the friction pair P ОП, MPa |
14 |
13,1 |
18,3 |
0,6751 |
2,16 |
Минимальный коэффициент трения при P ОП = 14 МПа f min / Minimum coefficient of friction at P ОП = 14 MPa f min |
0,0131 |
0,0082 |
0,022 |
0,8842 |
0,004 |
Интенсивность изнашивания |
|||||
колодки при нагрузке P ОП= 14 MPa I к / Rate of pad wear under load P ОП = 14 MPa I к |
18 ∙ 10–12 |
8,37 ∙ 10–12 |
23,2 ∙ 10–12 |
0,6752 |
1,59 ∙ 10–12 |
Интенсивность изнашивания |
|||||
ролика при нагрузке P ОП= 14 МПа I p / Rate of roller wear under load P ОП = 14 MPa I p |
14 ∙ 10–12 |
6,2 ∙ 10–12 |
19,1∙ 10–12 |
0,3927 |
1,1 ∙ 10–12 |
Суммарная интенсивность изнашивания при нагрузке P ОП = 14 MPa Σ I / Total intensity of wear under load P ОП = 14 MPa Σ I |
32 ∙ 10–12 |
11,5 ∙ 10–12 |
52,6 ∙ 10–12 |
0,3426 |
6,3 ∙ 10–12 |
Фактор износа Ф / Wear factor Ф |
2,3 ∙ 10–12 |
0,82 ∙ 10–12 |
1,9 ∙ 10–12 |
0,4230 |
0,45 ∙ 10–12 |
Из таблицы 4 видно, что интенсивность изнашивания колодки в 1,28 раза больше интенсивности изнашивания ролика, следовательно, в паре трения колодка является изнашивающейся поверхностью, а ролик – изнашиваемой поверхностью, поэтому электроискровое покрытие наносилось на поверхность колодки.
Результаты экспериментальной оценки интенсивности изнашивания при нагрузке в паре трения 3,2 МПа представлены в таблице 5 [22].
Т а б л и ц а 5
T a b l e 5
Результаты экспериментальной оценки интенсивности изнашивания при нагрузке в паре трения 3,2 МПа
Results of experimental evaluation of wear rate at a load of 3.2 MPa in the friction pair
1 |
] 2 |
3 |
4 |
5 |
1 6 |
||||
Интенсивность изнашивания колодки I к / Pad wear rate I к |
6,8 |
∙ 10–12 |
3,4 |
∙ 10–12 |
9,1 |
∙ 10–12 |
0,5198 |
1,8 |
∙ 10–12 |
Интенсивность изнашивания ролика I p / Roller wear rate I p |
4,9 |
∙ 10–12 |
2,4 |
∙ 10–12 |
7,5 |
∙ 10–12 |
0,3255 |
1,7 |
∙ 10–12 |
Окончание таблицы 5 / End of table 5
Суммарная интенсивность изнашивания Σ I / Total wear rate Σ I
12 ∙ 10–12
3 4 5 6
4,5 ∙ 10–12 18,7 ∙ 10–12 0,6188 4,6 ∙ 10–12
пара трения 2: ролик – чугун ЧН19Х3Ш; колодка чугун ЧН19Х3Ш с ЭИО из бронзы БрОС10-10 / friction pair 2: roller – cast iron ChN19Kh3Sh; pad ‒ cast iron ChN19Kh3Sh with elektrospark alloying bronze BrOS10-10
Интенсивность изнашивания колодки I к / Pad wear rate I к |
5,6 ∙ |
10–12 |
3,2 ∙ |
10–12 |
7,4 ∙ |
10–12 |
0,6131 |
1,45 |
∙ 10–12 |
Интенсивность изнашивания ролика I p / Roller wear rate I p |
3,1 ∙ |
10–12 |
1,8 ∙ |
10–12 |
4,62 |
∙ 10–12 |
0,8572 |
0,97 |
∙ 10–12 |
Суммарная интенсивность изнашивания Σ I / Total wear |
8,7 ∙ |
10–12 |
7,4 ∙ |
10–12 |
9,7 ∙ |
10–12 |
0,8234 |
0,7 ∙ |
10–12 |
rate Σ I |
Расчетные и экспериментальные значения интенсивности изнашивания изнашивающихся образцов представлены на рисунке 9.
Из рисунка 9 видно, что все теоретические (расчетные) значения интенсивности изнашивания попадают в диапазоне 95-процентного доверительного интервала экспериментальных значений. Полученные результаты показывают высокую степень достоверности выбора электродных материалов с использованием апробированных методик определения параметров и расчетно-экспериментальной оценки интенсивности изнашивания.
Обсуждение и заключение
Проведенные в работе триботехнические испытания показали, что интенсивность изнашивания колодки после нанесения покрытия из оловянисто-свинцовистой бронзы марки БрОС10-10 становится ниже, чем для базовой пары трения в 1,45 раза. При этом интенсивность изнашивания ролика уменьшилась в 1,36 раза. Таким образом, суммарная интенсивность изнашивания уменьшилась в 1,4 раза (рис. 10)16 [14].

□ Среднее / Average
I Q Среднее ± 0,95 Дов, интервал / Average ± 0.95 confidance interval
I Среднее ± Ст. откл. / Average ± Standart deviation
---Расчетно-экспериментальное значение / Calculated-experimental value
Р и с. 9. Расчетные и эксплуатационные значения интенсивности изнашивания изнашивающихся образцов из высоколегированного чугуна ЧН15Х3Ш:
-
1 – без покрытия; 2 – после ЭИО электродом из бронзы БрОС10-10;
3 – после ЭИО электродом из сплава Х15Н60
F i g. 9. Calculated and operational values of the wear rate of highly alloyed ChN19Kh3Sh cast iron wear samples: 1 – uncoated; 2 – after elektrospark alloying with bronze BrOS10-10; 3 – after elektrospark alloying with alloy Kh15N60
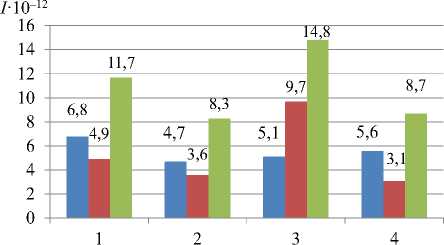
Р и с. 10. Интенсивность изнашивания пар трения: 1 – колодка ЧН19ХЗШ, ролик ЧН19ХЗШ;
-
2 – колодка ЧН19ХЗШ+БрОС10-10ЭИО, ролик ЧН19ХЗШ; 3 – колодка ЧН19ХЗШ+Х15Н60ЭИО, ролик ЧН19ХЗШ; 4 – колодка ЧН19ХЗШ+Х15Н60ЭИОMODENGY, ролик ЧН19ХЗШ;
синий – интенсивность изнашивания колодки; красный – интенсивность изнашивания ролика; зеленый – суммарная интенсивность изнашивания
F i g. 10. Wear rate of friction pairs: 1 – pad ChN19Kh3Sh, roller ChN19Kh3Sh;
-
2 – pad ChN19Kh3Sh+BrOS10-10ESP, roller ChN19Kh3Sh; 3 – pad ChN19Kh3Sh+Kh15N60ESP, roller ChN19Kh3Sh; 4 – pad ChN19Kh3Sh+Kh15N60ESPMODENGY, roller ChN19Kh3Sh; blue – pad wear rate; red – roller wear rate; green – total wear rate
Интенсивность изнашивания колодки после нанесения покрытия из хромоникелевого сплава Х15Н60 уменьшается по отношению к базовой паре трения в 1,33 раза. При этом Technologies, machinery and equipment интенсивность изнашивания ролика увеличивается в 1,97 раза. Таким образом, суммарная интенсивность изнашивания увеличивается в 1,26 раза (рис. 10).
Для снижения истирающей способности электроискрового покрытия из сплава Х15Н60 необходимо повысить его антифрикционные свойства, используя после ЭИО твердосмазочное покрытие на основе политетрафторэтилена компании «Моделирование и инжиниринг».
Проведенные в работе [14] исследования показали, что «интенсивность изнашивания колодки уменьшилась в 1,21 раза относительно базовой пары трения, а интенсивность изнашивания ролика уменьшилась в 1,58 раза. Таким
Том 33, № 1. 2023 образом, суммарная интенсивность изнашивания уменьшилась в 1,34 раза»17.
Следовательно, электроискровые покрытия из оловянисто-свинцовистой бронзы БрОС10–10 и сплава Х15Н60 обладают высокими триботехническими свойствами.
Полученные результаты исследований коррелируют с результатами других авторов и имеют практическую значимость для предприятий технического сервиса, занимающихся ремонтом тестоделительных машин.
Поступила 08.10.2022; одобрена после рецензирования 02.12.2022; принята к публикации 15.12.2022
Об авторах:
Все авторы прочитали и одобрили окончательный вариант рукописи.
Submitted 08.10.2022; revised 02.12.2022; accepted 15.12.2022
Список литературы Оценка триботехнических свойств консолидированных материалов, полученных методом электроискровой обработки
- Арабей Е. В., Балабанов В. Н. Характеристика оборудования для формования и разделки теста // Вестник современных исследований. 2017. № 5-1. С. 120-123. URL: https://elibrary.ru/item. asp?id=29345309 (дата обращения: 06.10.2022).
- Алексеев Г. В., Громцев А. С., Леу А. Г. Экспериментальное уточнение условий повышения точности дозирования жидкостей // Техника машиностроения. 2016. Т. 23, № 3. С. 57-63 URL: https://elibrary.ru/item.asp?id=27539434 (дата обращения: 06.10.2022).
- Ivanov V. I., Burumkulov F. K. Hardening of Objects and the Increase of Their Lifetime by the Electrospark Method: the Object Classification and the Specific Features of the Technology // Surface Engineering and Applied Electrochemistry. 2010. Vol. 46, Issue 5. P. 416-423. doi: https://doi.org/10.3103/ s1068375510050042
- Formation of Thick Electrospark Coatings with Increased Contact Continuity / S. A. Velichko [et al.] // Russian Engineering Research. 2021. Vol. 41, Issue 7. P. 657-660. doi: https://doi.org/10.3103/ S1068798X21070248
- Влияние молибдена на структуру и свойства электроосажденных сплавов железа и никеля / И. М. Ковенский [и др.] // Известия высших учебных заведений. Нефть и газ. 2021. № 6. С. 134-143. doi: https://doi.org/10.31660/0445-0108-2021-6-134-143
- Дорогой В. Н., Михлин В. М. Использование нового ресурсосберегающего метода для обслуживания деталей машин // Грузовое и пассажирское автохозяйство. 2014. № 1. С. 69-72. URL: https://www.elibrary.ru/item.asp?id=21289248 (дата обращения: 06.10.2022).
- New Possibilities of Plasma Spraying of Wear-Resistant Coatings / S. N. Grigorev [et al.] // Journal of Friction and Wear. 2013. Vol. 34, Issue 3. Р. 161-165. doi: https://doi.org/10.3103/S1068366613030070
- Ремонт тестоделительных устройств вакуумного типа методом электроискровой наплавки / Ф. Х. Бурумкулов [и др.] // Хлебопечение России. 2004. № 2. С. 34-36. URL: https://elibrary.ru/item. asp?id=19069614 (дата обращения: 06.10.2022).
- Velichko S. A., Martynov A. V., Kolomeichenko A. V. Surface Profile Formed by Electric Discharge Machining // Russ. Engin. Res. 2019. Vol. 39. P. 982-985. doi: https://doi.org/10.3103/ S1068798X19110182
- Определение модуля упругости электроискровых покрытий инструментальным индентиро-ванием / С. А. Величко [и др.] // Проблемы машиностроения и автоматизации. 2022. № 1. С. 91-97. doi: https://doi.org/10.52261/02346206_2022_1_91
- Сивцов В. Н. Применение электроискровой обработки и клея-компаунда для восстановления посадочных отверстий корпусных деталей машин // Вестник Российского государственного аграрного заочного университета. 2021. № 37. С. 23-27. URL: https://www.elibrary.ru/item. asp?id=46223224 (дата обращения: 06.10.2022).
- Сивцов В. Н. Восстановление ресурсных деталей машин // Вестник Российского государственного аграрного заочного университета. 2016. № 22. С. 21-25. URL: https://www.elibrary.ru/item. asp?id=29154929 (дата обращения: 06.10.2022).
- Ильин К. А. Влияние шероховатости поверхности на триботехнические показатели поверхностей // Научные труды студентов Ижевской ГСХА. 2019. Т. 2, № 9. С. 1103-1106. URL: https:// www.elibrary.ru/item.asp?id=42391481 (дата обращения: 06.10.2022).
- Влияние природы электродных материалов на эрозию и свойства легированного слоя. Критерии оценки эффективности электроискрового легирования / А. Д. Верхотуров [и др.] // Вестник Мордовского университета. 2018. Т. 28, № 3. С. 302-320. doi: https://doi.org/10.15507/0236-2910.028.201803.302-320
- Величко С. А., Мартынова Е. Г., Иванов В. И. Оценка предельного состояния тестодели-тельных машин вакуумно-поршневого типа по критерию расхода масла // Инженерные технологии и системы. 2020. Т. 30, № 3. С. 448-463. doi: https://doi.org/10.15507/2658-4123.030.202003.448-463
- Стопалов С. Надежность тракторов. Сбор и обработка информации для оценки надежности в реальной эксплуатации // Сельскохозяйственная техника: обслуживание и ремонт. 2011. № 12. С. 27-35. URL: https://www.elibrary.ru/item.asp?id=22598156 (дата обращения: 06.10.2022).
- Вовк Л. П. К определению комплекса механических характеристик неоднородных материалов ударным вдавливанием индентора // Заводская лаборатория. 2003. № 1. С. 45-48.
- Булычев С. И., Калмакова А. В., Кравченков А. Н. Определение модуля Юнга по твердости // Заводская лаборатория. Диагностика материалов. 2009. Т. 75, № 9. С. 63-66. URL: https:// www.elibrary.ru/item.asp?id=12890609 (дата обращения: 01.05.2021).
- Богодухов С. И., Гарипов В. С., Солосина Е. В. Определение модуля упругости различных материалов с применением средств тензометрии // Вестник Оренбургского государственного университета. 2014. № 4. С. 289-294. URL: https://www.elibrary.ru/item.asp?id=21638519 (дата обращения: 01.05.2021).
- Determination of the Heat Resistance of Polymer Construction Materials by the Dynamic Mechanical Method / V. O. Startsev [et al.] // Polymer Science. Series D. 2017. Vol. 10, Issue 4. P. 313-317. doi: https://doi.org/10.1134/s1995421217040141
- Моделирование температурного поля поверхности при электроискровом легировании металлов / В. Д. Власенко [и др.] // Инженерные технологии и системы. 2019. Т. 29, № 2. С. 218-233. doi: https://doi.org/10.15507/2658-4123.029.201902.218-233
- Трибологические характеристики и коррозионная стойкость покрытий, полученных методами электроискрового легирования, импульсного катодно-дугового испарения и гибридной технологии с использованием электродов TiCNiCr и TiCNiCr-Al2O3 / А. Д. Сытченко [и др.] // Известия вузов. Цветная металлургия. 2020. №. 2. С. 73-79. doi: https://doi.org/10.17073/0021-3438-2020-2-73-79