Очистка товарного электролита от примесей цветных металлов после десорбции золота с активированного угля
Автор: Лескив М.В., Белоусова Н.В., Дроздов С.В.
Журнал: Журнал Сибирского федерального университета. Серия: Техника и технологии @technologies-sfu
Статья в выпуске: 7 т.5, 2012 года.
Бесплатный доступ
В результате процесса десорбции золота с различных сорбентов получаются насыщенные растворы, в которые совместно с золотом элюируются цветные металлы. В процессе электролитического выделения золота последние переходят в катодный осадок, загрязняя его. В данной работе очистка электролита от примесей цветных металлов осуществляется добавлением перекиси водорода в раствор, в результате чего цветные металлы переходят в осадок в виде малорастворимых соединений, а золото остается в растворе, который отправляется на электролитическое получение металла. Установлено, что извлечение металлов примесей из раствора электролита повышается с увеличением температуры и расхода реагента-окислителя.
Очистка электролита, медь, никель, цинк, перекись водорода
Короткий адрес: https://sciup.org/146114701
IDR: 146114701
Текст научной статьи Очистка товарного электролита от примесей цветных металлов после десорбции золота с активированного угля
В настоящее время одной из наиболее важных задач цветной металлургии является оптимизация извлечения благородных металлов из упорных руд и концентратов. С изменением качества перерабатываемого золоторудного сырья, а также возросшими в последние годы требованиями к комплексности его использования необходимость решения данной задачи становится еще более актуальной.
Сейчас в процессах сорбционного выщелачивания золота в качестве сорбента широкое распространение получил активированный уголь. Одна из фабрик Олимпиадинского ГОКа работает по CIP-технологии [1] (уголь в пульпе), при этом в фазу сорбента переходит не только золото, но и ряд металлов-примесей, таких как никель, медь, цинк. В процессе десорбции цветные металлы десорбируются в раствор элюата вместе с золотом и, как следствие, при электролитическом выделении металла соосаждаются в катодный осадок, снижая его качество.
Попытки снизить содержание цветных металлов в электролите предварительной отмывкой насыщенного угля соляной кислотой приводили к удалению, в лучшем случае, до 50 % суммы примесей [2].
При проведении десорбции с активированного угля комплексы золота и металлов-примесей элюируются раствором щелочи [2]. Введение в раствор электролита перекиси водорода позволяет разрушить цианистые комплексы цветных металлов с образованием цианатов и нерастворимых соединений – гидроксидов [3]. Цианаты в конечном счете образуют аммоний и карбонат [4]:
[Cu(CNM2- + 4H2O2 + 2OH- = 4CNO- + Cu(OHM + 4H2O,(1)
[Ni(CNM2- + 4H2O2 + 2OH- = 4CNO- + Ni(OHM + 4H2O,(2)
Zn(CN)4]2- + 4H2O2 + 2OH- = 4CNO- + Zn(( )1 D_ + 4H2O,(3)
CNO- + 2H2O = NH4+ + CO32-.(4)
Цианистый комплекс золота (К у = 5-1039) не разрушается под воздействием перекиси водорода и полностью остается в растворе. Изменение устойчивости цианистых комплексов повышается в ряду [5]:
Ni(CN) 4 2- (1,84014) < Zn(CN) 4 2- (1,3^1017) < Cu(CN) 4 3- (54031) < Au(CN) 2 - (5D39).
К преимуществам данного способа относится и то, что он не предполагает введения каких-либо веществ, оказывающих негативное влияние на качество катодного золота.
Цель данной статьи – изучение условий очистки товарного электролита от металлов-примесей при введении в систему окислителя (перекиси водорода).
Методика эксперимента
Исследования проводились на промышленном электролите ЗИФ, отобранном на выходе из десорбера при температуре процесса 100 ° С. Состав электролита представлен в табл. 1.
В ходе экспериментов варьировались следующие показатели:
-
- температура процесса (60, 80 и 100 ° С);
-
- расход реагента окислителя (4, 5, 6 и 8 л/м3), где расход окислителя 4 л/м3 соответствует стехиометрически необходимому количеству на окисление комплексов цветных металлов и свободного цианид-иона, содержащихся в растворе электролита.
В качестве реагента-окислителя использовалась перекись водорода с концентрацией активного вещества 35-40 %.
Проба раствора электролита объемом 100 мл помещалась в колбу и нагревалась до заданной температуры. После чего добавлялся окислитель и включалось перемешивание. Пробы
Таблица 1. Состав электролита
Результаты
Изменения степени осаждения никеля, меди и цинка при расходе перекиси водорода 4 л/м3 представлены на рис. 1–3.
Как видно из зависимостей на рис. 1, увеличение температуры процесса оказывает влияние на полноту и начальную скорость осаждения никеля из раствора электролита. Изменение температуры с 60 до 100 ° С при расходе окислителя 4 л/м3 позволяет вдвое повысить степень осаждения никеля – с 40 до 80 %. Значение энергии активации процесса осаждения никеля,
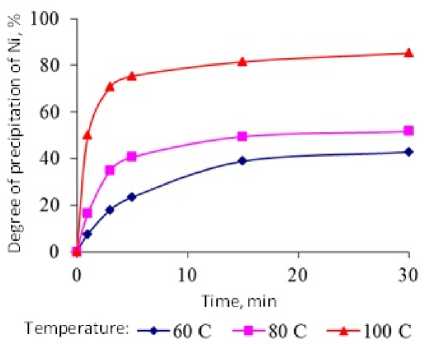
Рис. 1. Изменение степени осаждения никеля при обработке электролита перекисью водорода (4 л/м3) при температурах 60, 80, 100 ° С
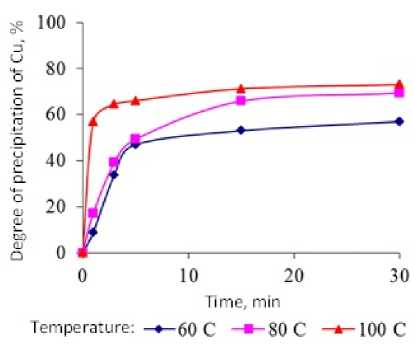
Рис. 2. Изменение степени осаждения меди при обработке электролита перекисью водорода (4 л/м3) при температурах 60, 80, 100 ° С
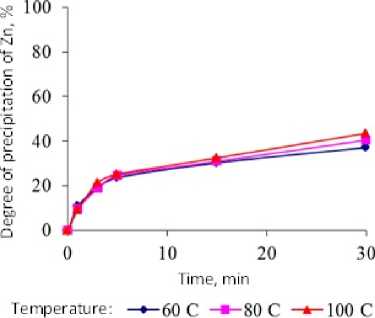
Рис. 3. Изменение степени осаждения цинка при обработке электролита перекисью водорода (4 л/м3) при температурах 60, 80, 100 ° С
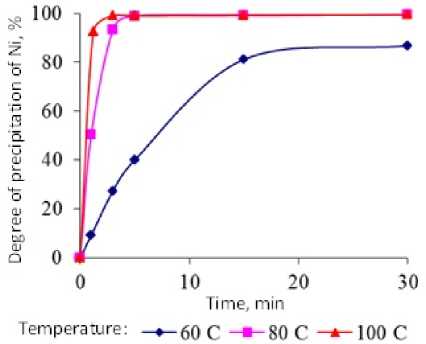
Рис. 4. Изменение степени осаждения никеля при обработке электролита перекисью водорода (8 л/м3) при температурах 60, 80, 100 °С определенное по начальным участкам кинетических кривых, составляет 52,1 кДж/моль, что говорит о том, что процесс протекает в кинетической области.
Степень осаждения меди из элюата в меньшей степени зависит от температуры, находится на уровне 50-65 % (рис. 2). Низкая степень осаждения меди связана с низкой концентрацией меди в исходном растворе электролита (40-50 мг/л) и с большей устойчивостью цианистого комплекса меди по сравнению с комплексом никеля.
Степень осаждения цинка, как видно из кинетических кривых рис. 3, не зависит от температуры процесса и остается на уровне 40 %.
Концентрация золота в растворе неизменна в течение всего процесса осаждения примесей.
При повышении расхода перекиси водорода до 8 л/м3 установленные закономерности сохраняются (рис. 4–6).

Рис. 5. Изменение степени осаждения меди при обработке электролита перекисью водорода (8 л/м3) при температурах 60, 80, 100 ° С
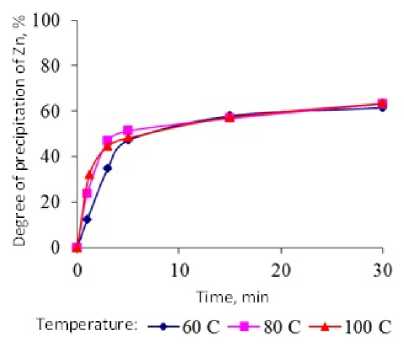
Рис. 6. Изменение степени осаждения цинка при обработке электролита перекисью водорода (8 л/м3) при температурах 60, 80, 100 ° С
При этом расходе при температурах 80-100 ° С степень осаждения меди и никеля достигает максимальных значений – 99 и 90 % соответственно (рис. 4 и 5). Анализ кинетических кривых свидетельствует, что окисление цианистых комплексов металлов полностью протекает за 2–4 мин после добавления перекиси водорода в систему. Образование осадка гидроксидов цветных металлов в этих условиях начинается сразу после введения Н2О2. Скорость фильтрации взвеси, полученной в результате осаждения примесей, достаточно высока. Цвет осадка зеленый, что свидетельствует о преобладании соединения никеля в осадке, что подтверждает химический анализ (табл. 2). Золото в осадке не обнаружено.
Степень осаждения цинка из элюата при увеличении расхода окислителя в два раза увеличивается на 20 % и также не зависит от температуры (рис. 6).
Сопоставление вышеприведенных данных позволяет сделать вывод: при минимальном расходе окислителя (4 л/м3) увеличение температуры способствует повышению степени – 748 –
Таблица 2. Состав осадка гидроксидов
Ni, % масс. |
Cu, % масс. |
Zn, % масс. |
27,95 |
0,58 |
1,10 |
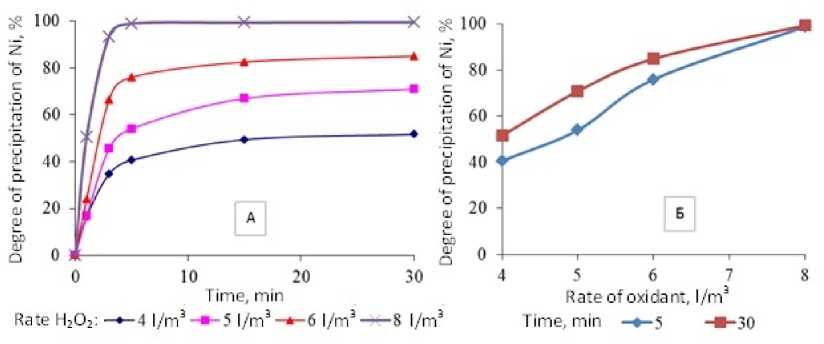
а
б
Рис. 7. Изменение степени осаждения никеля при температуре 80 °C: а - в зависимости от времени при различных расходах перекиси водорода; б – в зависимости от расхода перекиси водорода через 5 и 30 мин ведения процесса осаждения примесей, а при увеличении расхода до 8 л/м3 – скорости осаждения, тогда как полнота осаждения при достаточной продолжительности процесса остается на прежнем уровне.
Изменения степени осаждения цветных металлов в зависимости от расхода перекиси водорода и продолжительности эксперимента показаны на рис. 7–9. Видно, что степень осаждения никеля, меди и цинка существенно зависит от расхода перекиси водорода. Основное количество цветных металлов осаждается в первые 5 мин после введения в систему Н2О2 (рис. 7-9 б ). Так, при расходе окислителя 4 л/м3 и температуре 80 ° C за первые 5 мин Ni осаждается на 79 % относительно значения, полученного через 30 мин, медь - на 82 %, цинк - на 60 %, а при расходе 8 л/м3 к тому же моменту времени степень осаждения Ni изменяется до 99 % относительно значения, полученного через 30 мин, медь – до 98 %, цинк – до 81 %.
Так как основной примесью, влияющей на качество катодного осадка при электролитическом получении золота, служит никель, то оптимальным расходом перекиси водорода, позволяющим наиболее быстро и полно осадить примеси цветных металлов, является расход 8 л/м3. При этом расходе степень очистки от никеля достигает 99%, от меди – 90%, от цинка – 65-70%. Эти показатели достигаются при температуре 80 ° C.
Рассмотренный способ предварительной очистки товарного электролита от металлов-примесей позволяет на стадии электролиза получать металл более высокого качества, при этом цветные металлы доизвлекаются из промпродукта, образующегося на стадии очистки, что позволяет решить вопрос комплексного использования сырья.
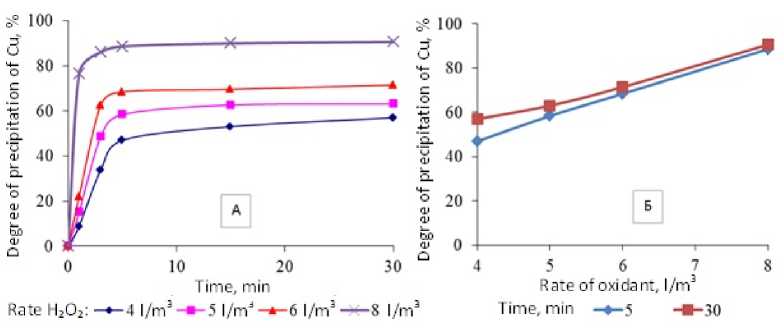
а
б
Рис. 8. Изменение степени осаждения меди при температуре 80 ° С: а - в зависимости от времени при различных расходах перекиси водорода; б – в зависимости от расхода перекиси водорода через 5 и 30 мин ведения процесса
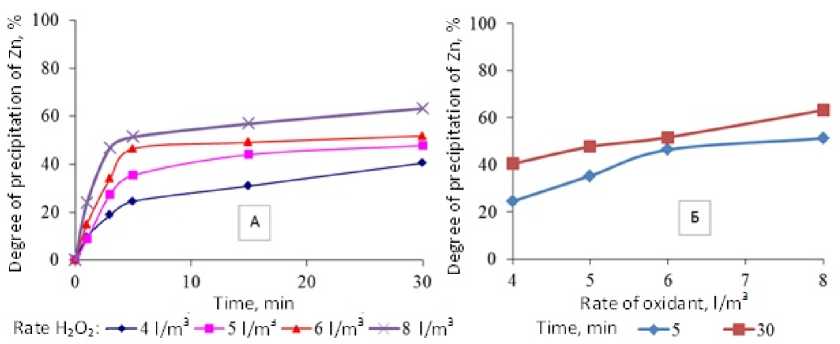
а
б
Рис. 9. Изменение степени осаждения цинка при температуре 80 ° С: а - в зависимости от времени при различных расходах перекиси водорода; б – в зависимости от расхода перекиси водорода через 5 и 30 мин ведения процесса
Выводы
-
1. Установлено, что извлечение металлов-примесей из раствора электролита повышается с увеличением расхода реагента-окислителя, при этом оптимальное количество H2O2 (8 л/м3) соответствует двукратному избытку от стехиометрии.
-
2. Показано, что при минимальном расходе окислителя (4 л/м3) увеличение температуры способствует повышению степени осаждения примесей, а при увеличении расхода до 8 л/м3 – скорости осаждения, тогда как полнота осаждения, при достаточной продолжительности процесса, остается на прежнем уровне.
-
3. Независимо от условий обработки электролита содержание золота в растворе остается постоянным.
-
4. Установлено, что основное количество примесей осаждается в течение 3–5 мин после добавления окислителя в систему.
-
5. При оптимальных параметрах ведения процесса осаждения в лабораторных условиях содержание никеля в растворе снижается на 99, меди – на 90, цинка – на 70 %.