Окисление порошков и пористых компактов TiB2
Автор: Иванов В.В., Нагибин Г.Е., Суходоева Н.В.
Журнал: Журнал Сибирского федерального университета. Серия: Техника и технологии @technologies-sfu
Статья в выпуске: 8 т.11, 2018 года.
Бесплатный доступ
Рассмотрено окислительное поведение порошков и пористых порошковых композитов на основе диборида титана - материалов смачиваемых катодов в электролизе алюминия - в технологических газовых средах (воздух, аргон, атмосфера под углеродной постелью). В воздухе при 800-1270 К полное окисление происходит за время от нескольких часов до десятков суток. В слабоокислительной среде (аргон, О2 не более 0,002 %) также наблюдается значительная окислительная деградация. Обнаружено явление окисления TiB2 при обжигах в защитной газовой среде под углеродной постелью (масса образцов закономерно возрастает, обнаруживаются продукты TiO2, TiBO3, B2O3, оксикарбид TiCхОy, графит, содержание которых зависит от времени и температуры. Долговременная работа смачиваемого катода, сравнимая со сроком службы электролизера (5-8 лет), требует исключения рассмотренных деградационных рисков.
Окисление, диборид титана, воздух, аргон, углеродная постель, электролиз алюминия
Короткий адрес: https://sciup.org/146279566
IDR: 146279566 | DOI: 10.17516/1999-494X-0121
Текст научной статьи Окисление порошков и пористых компактов TiB2
Рис. 1 СЭМ микроснимки порошков TiB2: а – СВС, б – КТС
Fig. 1 SEM micrographs of the TiB2 powders; (a) – self-propagating high-temperature synthesis (SHS), (b) – carbothermal synthesis (CTS)
Таблица 1. Рентгеноспектральный анализ используемых порошков TiВ 2 (мас. %)
Table 1. Results of XRS analysis of the TiB2 powders (wt. %)
TiB 2 * |
SiO 2 |
Fe 2 O 3 |
MgO |
CaO |
SO 2 |
NiO |
Al 2 O 3 |
W |
P |
|
СВС |
99,2 |
0,0217 |
0,399 |
0,131 |
0,0145 |
0,0397 |
0,0291 |
0,0183 |
0,124 |
0,00456 |
КТС |
98,8 |
0,414 |
0,138 |
0,335 |
0,186 |
0,0107 |
0,0184 |
- |
- |
0,0379 |
* Титан представлен в форме TiB2 на основе рентгенодифракционных данных.
в широком диапазоне от единиц до 50-70 мкм (рис. 1 а ). В ряде опытов для сравнения был использован порошок карботермического синтеза (КТС), подобный [8]. Это более однородный порошок с размером основной доли частиц в диапазоне 1-4 мкм (рис. 1 б ). По результатам рентгенофазового анализа порошки состоят из фазы TiB 2 без заметного количества посторонних фаз
. Рентгеноспектральный анализ показал наличие ряда примесей, наиболее значимые из которых представлены в табл. 1.
Микроснимки получены на сканирующем электронном микроскопе JEOL JSM-7001F. Рентгеноспектральный анализ выполнен на спектрометре Axios Advanced (Panalytical). Образцы готовили прессованием таблеток из тонко растертого порошка. Оценку концентраций проводили по методу фундаментальных параметров. Порошковые дифракционные данные получены с использованием Cu Kα-излучения на дифрактометре X'Pert PRO с детектором PIXcel (Panalytical), снабженным графитовым монохроматором. Образец растирали в агатовой ступке и подготавливали методом прямой набивки кюветы. Условия съемки: диапазон от 5 до 90° по 2θ, шаг 0.013°, ∆ τ 25с.
Термический анализ (термогравиметрия – ТГ и дифференциальная сканирующая калориметрия – ДСК) проводили на приборе Netzsch STA 449C Jupiter. Навеску порошка около 50 мг разравнивали по дну алундового тигля (внутренний диаметр 5 мм). Линейный нагрев осуществляли в потоке воздуха или аргона. Подаваемый воздух не сушили, относительная – 991 – влажность при комнатной температуре составляла около 60-70 %. При изотермических измерениях первоначальный нагрев до заданной температуры осуществляли в потоке аргона. После выхода на сегмент изотермы напускали воздух и проводили окисление в течение заданного времени.
Порошковые образцы формовали в стальных пресс-формах при давлении 60-300 МПа с использованием временных технологических связок (вода, растворы фенолоформальдегидной смолы – ФФС – и поливинилбутираля в этиловом спирте). ФФС служила также в качестве углеродной добавки в состав композита (коксовый остаток после термолиза в аргоне – около 55 %). Добавку Al2O3 вводили в виде продукта термолиза насыщенного раствора хлористой соли алюминия [9]. После сушки при 350 К до постоянной массы прессовки подвергали термообработке в течение определенного времени в закрытом контейнере под углеродной засыпкой (активированный уголь) при фиксированной температуре. Относительная плотность образцов составляла около 0,6. Контролировали изменение массы образцов, их плотность, линейные размеры, а также фазовый состав. Плотность компактов правильной формы определяли по массе и объему, относительную плотность вычисляли по отношению к теоретической плотности беспористого композита заданного состава в предположении аддитивного вклада фазовых компонентов.
Анализ процесса окисления, записываемого в виде суммарной реакции
TiB2 + 5/2 O2 = TiO2 + B2O3,
проводили на основе данных термогравиметрии, представленных в координатах а , т (степень превращения – время) и α ,T (Т – температура). Величину α выражали через m о (масса образца исходная), m , (масса образца при полном окислении в соответствии с уравнением (1)) и m T (масса образца в момент времени т ):
α=
mo
-
mτ
⋅ 100.
mo - m
Результаты и обсуждение
На рис. 2 представлены термограммы изотермического окисления порошков TiB2 (кинетические кривые) в координатах а,т. Стадии нагрева и выдержки в аргоне на графиках исключены. Начальный резкий прирост массы на термограммах при всех изученных температурах объясняется ускоренным окислением слабозащищенной поверхности и самых мелких фракций порошка, имеющих наибольшую удельную поверхность, при этом на более крупных частицах формируется оксидный слой, замедляющий дальнейшее окисление. Как видно, уже при небольшой температуре 770 К окисление идет достаточно интенсивно. Наиболее эффективно порошки окисляются в области температур 970-1170 К, что объясняется изменениями в структуре защитной окалины [7]. Уже через 1 ч контакта с воздухом полному окислению подвергается 25-35 % первоначальной массы образца СВС и порядка 80-90 % – КТС. Окисление СВС-порошка происходит медленнее из-за более низкой дисперсности и, возможно, влияния примесей на кислородную проницаемость окалины.
Окалина, образующаяся на плотной диборидной керамике [5], достигает 50 мкм толщины за 10 ч окисления на воздухе при 1073 К (это соответствует 12-15 мкм по толщине прореа- – 992 –
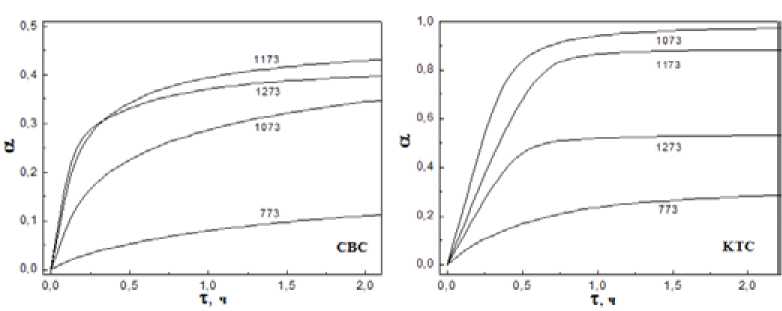
Рис. 2. Кинетические кривые окисления порошков TiB2 различной дисперсности
Fig. 2 Oxidation kinetics of the TiB2 powders of different size гировавшего поверхностного слоя TiB2), что подтверждает возможность полного окисления в указанных условиях не только мелких фракций и порошков размером менее 5 мкм, но и более крупных – порядка 30-40 мкм.
Из изложенного следует, что порошки TiB 2 , независимо от их особенностей, окисляется интенсивно уже при относительно невысоких температурах 800-1000 К: мелкие порошки до 5 мкм полностью превращаются в оксиды за несколько часов, более крупные – 40-100 мкм – за несколько суток. Таким образом, при прямом доступе воздуха к пористому порошковому изделию на основе TiB 2 , работающему при температуре выше 770 К, для окислительной деградации материала требуется относительно короткое время, определяемое лишь скоростью диффузии кислорода по пористой структуре к внутренним областям этого изделия. Причем высокая дисперсность исходного порошка TiB2 является отрицательным фактором.
Эксперименты по окислению порошков TiB 2 в слабоокислительной среде (товарный аргон, ГОСТ 10157-79, объемная доля Ar не менее 99,987 %, кислорода – не более 0,002 %) показывают, что при нагреве от 800 до 1473 К в течение около 1 ч образцы, находящиеся в открытом тигле, прибавляют в весе порядка 10 %, а также имеют характерные ДСК-сигналы около 790, 880 и 1000 К, относящиеся к процессу окисления [6]. Эти результаты согласуются с литературными данными [10] по окислению TiB2 в газовых смесях, содержащих малые контролируемые количества кислорода: (1) – аргон+10 ppm O 2 и (2) – аргон+0,05 ppm O 2 . Пер -вая смесь соответствует товарному аргону средней степени чистоты, вторая – специально очищенному аргону. Окислительный процесс зафиксирован в обеих смесях. В период нагревания от 670 до 1170 К за время около 0,5 ч приращение массы образцов TiB2 составило 2,56 и 0,78 % соответственно.
Таким образом, присутствие О2 в рабочей атмосфере катодного материала даже при таком малом содержании, как 10-3-10-4 %, может быть причиной заметной окислительной деградации, не катастрофичной лишь в течение ограниченного времени обжига или эксплуатации изделий из рассматриваемых композитов.
Термообработка окисляющихся материалов в защитной атмосфере под углеродной засыпкой (или углеродной, коксовой постелью) широко используется в химической технологии. При этом обычно считается, что такая среда обладает восстановительным потенциалом и надежно защищает материалы от окисления. Однако нами было установлено, что при обжиге пористых катодных композитов всех основных составов (компакты TiB2 без добавочных гетерогенных компонентов, TiB2/Al2O3, TiB2/C, TiB2/Al2O3/C) наблюдается их химическое взаимодействие с газовой фазой, приводящее к значительному росту массы образцов. Рассмотрим далее результаты, полученные на компактах TiB2. На других композитах закономерности соблюдаются с учетом более низкого содержания диборида.
На рис. 3 представлены результаты кинетических экспериментов на образцах из СВС-порошка (размер 4 x 7 x 24 мм), обожженных в закрытом контейнере под углеродной засыпкой при указанных на графике температурах. Изотермы а , т свидетельствуют, что в процессе обжига масса образцов возрастает за счет взаимодействия TiB2 c газовой фазой. Возможные процессы, вызывающие это явление, - окисление диборида и диспропорционирование CO с выделением твердого углерода [11, 12]. Протекание обоих процессов подтверждает рентгенофазовый анализ образцов после обжига: кроме основного фазового компонента TiB2 обнаруживаются продукты TiO2, TiBO3, H3BO3, а также оксикарбиды переменного состава TiСхОу [13] и углерод в виде графита, интенсивность рефлексов которых закономерно зависит от температуры и времени термообработки (рис. 4). Борная кислота здесь появляется в результате гидратации борного ангидрида при хранении и обработке образцов на воздухе.
Конденсация углерода в отсутствие катализаторов невелика, и поэтому очевидно, что при температурах 970-1170 К основной процесс - это окисление TiB2 и за ограниченное время – 15 ч – ему подвержена заметная часть (10-15 %) от исходного количества диборида в образце.
Кинетические кривые (рис. 3) удовлетворительно описываются параболической зависимостью, что свидетельствует о диффузионных ограничениях кинетики процесса. На рис. 3 результаты представлены в координатах a, VT с соответствующими уравнениями и коэффициентами корреляции. Уравнения позволяют оценить время полного превращения (α=100 %)
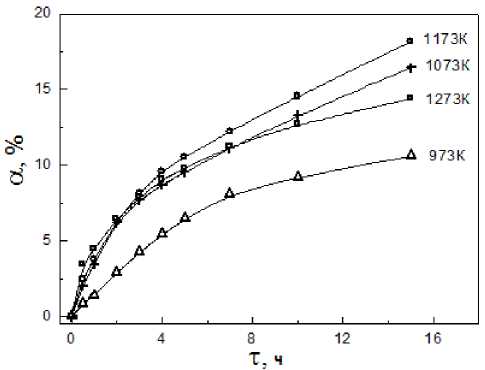
Рис. 3. Кинетические кривые взаимодействия прессовок TiB2 с атмосферой углеродной постели
Fig. 3 Kinetic curves of interaction of the TiB2 compact in reducing atmosphere
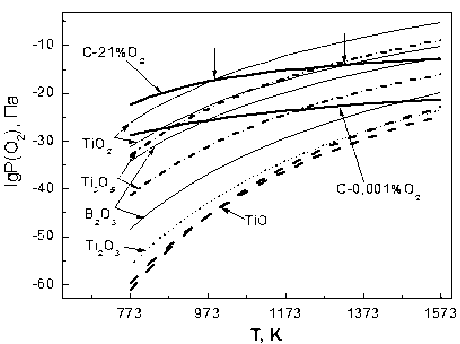
Рис. 4. Совмещенный график парциального давления O2 в системе С-воздух (21 % О2), С-0,001 % О2 с кривыми упругости диссоциации оксидов
Fig. 4. O2 partial pressure and elastic dissociation curves for C-air (21% O2), C-0.001% O2 systems порошка диборида дисперсностью -44 мкм в слое смачиваемого покрытия толщиной 4 мм на подине электролизера, находящемся в контакте с указанной атмосферой, например при 973 К τ≈930 ч, т.е. порядка 40 сут (что много меньше срока службы ванны).
Следует заметить, что для потери основного функционального свойства материала - смачиваемости алюминием - не требуется полной окислительной деградации диборидного компонента в композите. Уже после окисления половины TiB2 в приповерхностном слое смачиваемость катода оказывается под вопросом, а с учетом ускоренного окисления мелких фракций это наступит еще раньше.
Рассмотрим термодинамический аспект этого химического взаимодействия, так как ранее вопрос, по-видимому, не изучался и не отражен в литературе. Газовая фаза в этом случае образуется в результате реакции кислорода воздуха с углеродом, присутствующим в избытке, и состоит в основном из азота и монооксида углерода, а также определенной доли углекислого газа, зависящей от температуры. Но в результате термической диссоциации CO2 в смеси присутствует также в малом количестве кислород, который и задает уровень окислительной способности данной газовой среды. В системе углерод–воздух при повышенных температурах идут следующие основные реакции (с соответствующими зависимостями их изобарного потенциала от температуры) [11]:
– полного горения
С + О2 = СО1, A GT(3) =-393290 - 2,29Т, Дж,
– неполного горения
С + 1/202 = СО, A GT (4) =-110560 - 89,875Т, Дж ,
– догорания монооксида
СО + 1/202 о СО2, A GT (5) =-282695 + 87,585Т, Дж ,(5)
– газификации углерода
С + СО 2 о 2СО, A G T(6) = 172130 - 177,46 7 , Дж . (6)
Как известно, реакции (3, 4) – кинетически необратимые, а (5, 6) – обратимые. Причем реакция, обратная (5), обеспечивает равновесное содержание кислорода и окислительный потенциал газовой смеси в системе С-О 2 .
На рис. 4 представлены результаты термодинамических расчетов зависимости парциального давления кислорода P O 2 в системе С–воздух (21 % О 2 ) и С–обедненный воздух (0,001 % О 2 – по-существу, очищенный азот или аргон) от температуры, совмещенные с литературными данными [14-16] по упругости диссоциации оксидов титана и бора. Данные по упругости диссоциации имеют, как правило, значительный разброс, на графике приведены наиболее близко согласующиеся между собой результаты.
Температурная зависимость PO2, Т имеет меньший наклон по сравнению с подобными зависимостями упругости диссоциации оксидов и пересекает их для TiO 2 при температуре в интервале 1000-1300 К (на рис. 4 точки пересечения показаны стрелками). В то же время соответствующие кривые низших оксидов Ti 3 O 5 , Ti 2 O 3 и TiO лежат ниже. Это означает, что при термообработке оксидов титана в атмосфере углеродной засыпки при температуре ниже 1300 К может наблюдаться восстановление диоксида, но низшие оксиды Ti 2 O 3 и TiO во всем рассмотренном интервале температур не восстанавливаются. То есть окисление TiB2 при температурах ниже 1300 К может происходить с образованием высшего оксида, в то время как выше указанного интервала в продуктах остаются оксиды все меньших степеней окисления. Борный ангидрид вплоть до температуры ~1600 К остается стабильным.
Обеднение газовой смеси по кислороду снижает температуру восстановления диоксида (рис. 4, кривая С–0,001 % О 2 ), но окисление TiB 2 и в таком случае происходит во всем рассматриваемом ∆Т до низших оксидов титана и оксида бора и, возможно, до бората титана TiBO3. К сожалению, термодинамические характеристики TiBO 3 в литературе отсутствуют, как это отмечают и другие авторы, что не позволяет провести соответствующие расчеты.
Таким образом, окислительная деградация диборида титана при рассматриваемых температурах в атмосфере, формирующейся в контакте С-О2 при избытке углерода, происходит с измеримой скоростью и может существенно ограничивать срок службы смачиваемого алюминием катода в виде покрытия или объемных изделий на основе этого химического соединения.
Механизм гетерогенных взаимодействий в системе TiB2-C-О2 не изучен, весьма сложен и требует детального исследования. Наряду с возможностью протекания суммарной реакции (2) полного окисления TiB2 авторы работы [17], например, обоснованно (с учетом поправок на синтез оксикарбида) считают, что окисление диборида может осуществляться по реакции
TiB 2 + 3/2 O 2 + С = TiС + B 2 O 3 , Δ G1173K = -894 кДж/моль , (7)
для инициации которой требуется всего порядка 5×10-16 Па O 2 . Такое давление кислорода обеспечивается за счет диссоциации остаточного углекислого газа в системе углерод–воздух при температуре до ~1400 К (рис. 4).
Заключение
Окислительная деградация диборидсодержащих катодных материалов в воздушной среде, а также в слабоокислительных газовых смесях, содержащих до 10-3-10-4 % кислорода, происходит с измеримой скоростью, не катастрофичной для сохранения смачиваемости катода алюминием лишь в течение ограниченного времени эксплуатации электролизера.
Обжиг пористых порошковых материалов под углеродной постелью вызывает окисление TiB2 до оксидов TiO2, TiBO3, B2O3 и оксикарбида TiCхОy, которые неустойчивы в контакте с расплавами алюминия и электролита, что ведет к потере смачиваемости катода. Полное окисление слоя смачиваемого покрытия катода толщиной порядка 4 мм из порошка TiB2 дисперсностью -44 мкм в такой атмосфере происходит в течение нескольких десятков суток, что много меньше срока службы алюминиевого электролизера (5-8 лет).
Рассмотренные процессы окислительной деградации диборидного компонента в смачиваемом алюминием катодном материале имеют место в период изготовления объемных изделий при их обжиге в защитных атмосферах, во время пуска электролизера, когда катод практически не защищен от контакта с окислительными газами О2 и СО2, а также в самом технологическом процессе электролиза. Уже на первых двух этапах окисление функционального компонента TiB2 может быть существенным и очень сократит срок службы катода в режиме смачивания.
Эффективное применение катода с диборидным смачиваемым покрытием в технологии электролиза алюминия требует новых научно-технических и конструктивных решений для исключения доступа воздуха в рабочее пространство катода и на всех предварительных этапах его термообработки.
Работа выполнена в рамках Договора с Минобрнауки России № 02.G25.31.018 (проект «Разработка сверхмощной, энергоэффективной технологии получения алюминия РА-550»).
Список литературы Окисление порошков и пористых компактов TiB2
- Ibrahiem, M.O., Foosnes, T., Oye, H.A. Properties of pitch and furan-based TiB2-C cathodes. Light Metals: 2008 TMS Annual Meeting, New Orleans, 2008, 4, 1013-1018.
- Li, J., Lu, X.-j., Lai, Y.-q., Li, Q.-y., Liu, Y-x. Research progress in TiB2 wettable cathode for aluminum reduction. JOM, 2008, 8, 32-37.
- Serebryakova, T.I., Neronov, V.A. and Peshev, P.D. Vysokotemperaturnye boridy (High-Temperature Borides). Moscow: Metallurgiya, 1991.
- Voitovich, V.B., Lavrenko, V.A., Adejev, V.M. High-temperature oxidation of titanium diboride of different purity. Oxid. Met., 1994, 42, 145-161.
- Koh, Y.H., Lee, S.Y., Kim, H.E. Oxidation behavior of titanium boride at elevated temperatures. J. Am. Ceram. Soc., 2001, 84, 239-241.
- Иванов, В.В., Черноусов, А.А., Иртюго, Л.А. Термические процессы взаимодействия TiB2 с воздухом. Огнеупоры и техническая керамика, 2012, 1-2, 9-15.
- Ivanov, V.V., Blokhina, I.A., Kirik, S.D. High temperature oxidation kinetics of TiB2 powders in air, Oxid. Met., 2014, 82(1), 71-84.
- Ivanov V.V., Kirik S.D., Shubin A.A., Blokhina I.A., Denisov V.M., Irtugo L.A. Thermolysis of acidic aluminum chloride solution and its products. Ceramics International, 2013, 39, 3843-3848.
- Kulpa, A., Troczynski, T. Oxidation of TiB2 Powders below 900 °C. J. of the American Ceramic Society, 1996, 79(2), 518-520.
- Борнацкий, И.И. Теория металлургических процессов. Киев-Донецк: Вища школа, 1978, 287 с.
- Slovetskii, D.I., Chistov, E.M. Catalytic Processes on Membrane Palladium Alloys: I. Carbon Monoxide Disproportionation. Kinetics and Catalysis, 2010, 51(2), 255-265.
- Davydov D.A. Preparation of Nanostructured TiCxOy. Inorganic Materials, 2013, 49 (1), 62-65.
- Физико-химические свойства окислов. Справочник. Под ред. Г.В. Самсонова. М.: Металлургия, 1978, 471 c.
- Кубашевский, О., Олкокк, С.Б. Металлургическая термохимия. Москва: Металлургия, 1982, 390 c.
- Термодинамика оксидов. Справочник. Под ред. И.С. Куликова. Москва: Металлургия, 1986, 344 с.
- Dionne, M., Gilies, L., Mirchi A. Microscopic сharacterization of a TiB2-carbon material composite: raw materials and composite characterization. Metallurgical and Materials Transactions A, 2001, 23A, 2649-2656.