Определение оптимальных режимов термической обработки валков станов холодной прокатки через исследование их влияния на микроструктуру и свойства заготовки
Автор: Крапивина П.А., Гервасьев М.А.
Журнал: Журнал Сибирского федерального университета. Серия: Техника и технологии @technologies-sfu
Статья в выпуске: 4 т.12, 2019 года.
Бесплатный доступ
Качество, надежность и долговечность прокатных валков - решающие факторы, определяющие качество готовой продукции и производительность прокатных станов. Основной проблемой, возникающей в процессе производства стальных кованых прокатных валков, признан выбор рациональных режимов термической обработки. Так как значительную роль в формировании конечных свойств изделия играет величина зерна исходной структуры и характер распределения отдельных структурных составляющих в заготовке, целями настоящей работы являются исследование влияния термической обработки на микроструктуру и твердость стальных прокатных валков и разработка на этой основе рациональных технологических режимов, а именно: определение оптимального режима первичной термической обработки после ковки валков холодной прокатки для получения однородной структуры и уменьшения балла карбидной сетки и карбидной ликвации; определение оптимального режима вторичной термической обработки валков холодной прокатки для обеспечения твердости в диапазоне около 300 HB, благоприятной структуры перед закалкой токами промышленной частоты и уменьшения балла карбидной сетки и карбидной ликвации; определение температуры закалки, времени выдержки и скорости охлаждения для получения оптимальной структуры и твердости в диапазоне 650-700 HB...
Высоколегированная сталь, фазовый состав, термическая обработка, прокатный валок, микроструктура
Короткий адрес: https://sciup.org/146281209
IDR: 146281209 | DOI: 10.17516/1999-494X-0152
Текст научной статьи Определение оптимальных режимов термической обработки валков станов холодной прокатки через исследование их влияния на микроструктуру и свойства заготовки
-
2) определение оптимального режима вторичной термической обработки валков холодной прокатки для обеспечения твердости в диапазоне 250-315 HB, благоприятной структуры перед закалкой токами промышленной частоты (ТПЧ) и уменьшения балла карбидной сетки и карбидной ликвации;
-
3) определение температуры закалки, времени выдержки и скорости охлаждения для получения оптимальной структуры и твердости в диапазоне 650-700 HB.
В связи с тем что качество закаленного слоя в большой степени зависит от характера и состояния исходной структуры, ее, безусловно, необходимо принимать во внимание. Значительную роль играют величина зерна исходной структуры и характер распределения отдельных структурных составляющих [3]. Наиболее благоприятной при закалке ТПЧ является исходная структура в виде сорбита или мелкопластинчатого перлита. Разнородность структуры не обеспечивает удовлетворительные механические и эксплуатационные свойства. Для обеспечения заданных эксплуатационных и механических характеристик наиболее желательно равномерное распределение мелких скоагулированных карбидов, не превышающих 3 балла. Присутствие на бочке валка вторичных карбидов и карбидов в виде пластин, располагающихся по границам зерен, увеличивает ее склонность к хрупкому разрушению.
Материал и методика исследования
Отработка режимов термической обработки производилась на образцах цилиндрической формы (диаметр 30 мм, высота 20 мм), вырезанных с пробы и темплета.
При выборе температуры перекристаллизации необходимо руководствоваться положением точки Ас1, которая зависит от химического состава. Значение точки Ас1 было взято из марочника сталей и сплавов [2] и теоретически рассчитано:
-
• по марочнику Ас1 = 780 ºС;
-
• теоретическое значение (в зависимости от химического состава) Ас1 = 780,6 ºС.
Время выдержки при температуре перекристаллизации зависит от размеров образца и рассчитывается теоретически. Скорость охлаждения необходимо назначать в соответствии с диаграммой изотермического превращения аустенита в данной стали.
Результаты исследования
Определение оптимального режима первичной термической обработки после ковки
Для получения структуры как после ковки на образцах был осуществлен отжиг. После отжига были проведены следующие режимы:
-
1) нормализация при 940-960 ºС + нормализация при 840-860 ºС + отпуск при 670-690 ºС;
-
2) нормализация при 960-970 ºС + нормализация при 850-880 ºС + отпуск при 600-620 ºС;
-
3) нормализация при 910 ºС + нормализация при 1100 ºС + отпуск при 670-690 ºС;
-
4) нормализация при 1100 ºС + нормализация при 880 ºС + отпуск при 670-690 ºС;
-
5) нормализация при 1100 ºС + отпуск при 670-690 ºС.
Результаты оценки микроструктуры и балла действительного зерна представлены в табл. 1.
Карбидная ликвация на образцах как в исходном состоянии, так и после термической обработки отсутствовала.
Полученные данные показали, что повышение температуры перекристаллизации до 1100 °С обеспечивает снижение балла карбидной сетки, однако при этом происходит рост действительного зерна и ухудшение структуры.
Таблица 1. Результаты оценки микроструктуры
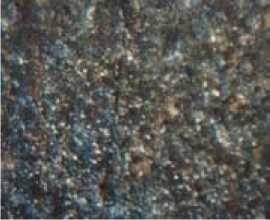
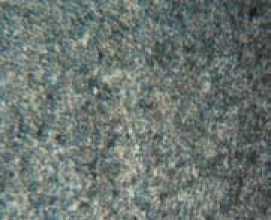
Рис. 2. Микроструктура образцов из стали 75ХМФ после отжига (х500)
Рис. 1. Микроструктура образцов из стали 75ХМФ в исходном состоянии (х500)
Fig. 1. The microstructure of a sample of 1.2067 steel in the initial state (х500)
Fig. 2. The microstructure of a sample of 1.2067 steel after annealing (х500)
Table 1. Results of microstructure study
Проводимая термическая обработка |
Карбидная сетка, балл |
Микроструктура |
Балл действительного зерна |
Исходная структура |
3,5 |
Сорбитообразный и скрытопластинчатый перлит + карбиды (рис. 1) |
7 |
Отжиг при 850 ºС (в течение 2 ч) |
2,5 |
Зернистый перлит + карбиды (рис. 2) |
8-7 |
Нормализация при 940-960 ºС (выд. 30 мин) + нормализация при 840-860 ºС (выд. 20 мин) + отпуск при 670-690 ºС (выд. 50 мин) |
2,5 |
Зернистый перлит + карбиды (рис. 3) |
8-7 |
Нормализация при 960-970 ºС (выд. 1 ч) + нормализация при 850-880 ºС (выд. 20 мин) + отпуск при 600-620 ºС (выд. 4,5 ч) |
2,5 |
Зернистый перлит + карбиды (рис. 4) |
8-7 |
Нормализация при 910 ºС (выд. 1 ч) + нормализация при 1100 ºС (выд. 1 ч) + отпуск при 670-690 ºС (выд. 1,5 ч) |
2,0 |
Бесструктурный и зернистый перлит + карбиды (рис. 5) |
4-6 |
Нормализация при 1100 ºС (выд. 1 ч) + нормализация при 880 ºС (выд. 1 ч) + отпуск при 670-690 ºС (выд. 1,5 ч) |
2,0 |
Бесструктурный и зернистый перлит + карбиды (рис. 6) |
4-5 |
Нормализация при 1100 ºС (выд. 1 ч) + отпуск при 670-690 ºС (выд. 1,5 ч) |
2,0 |
Бесструктурный и зернистый перлит + карбиды (рис. 7) |
4-6 |
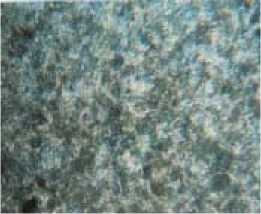
Рис. 3. Микроструктура образцов из стали 75ХМФ после термической обработки (х500)
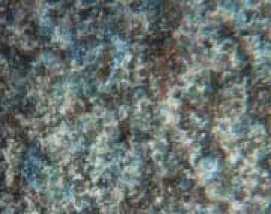
Рис. 4. Микроструктура образцов из стали 75ХМФ после термической обработки (х500)
Fig. 3. The microstructure of a sample of 1.2067 steel after heat treatment (х500)
Fig. 4. The microstructure of a sample of 1.2067 steel after heat treatment (х500)
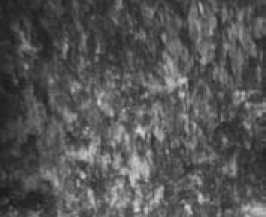
Рис. 5. Микроструктура образцов из стали 75ХМФ после термической обработки (х500)
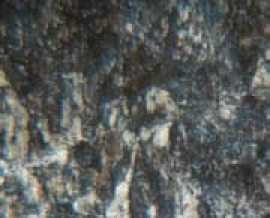
Рис. 6. Микроструктура образцов из стали 75ХМФ после термической обработки (х500)
Fig. 5. The microstructure of a sample of 1.2067 steel after heat treatment (х500)
Fig. 6. The microstructure of a sample of 1.2067 steel after heat treatment (х500)
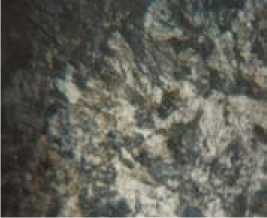
Рис. 7. Микроструктура образцов из стали 75ХМФ после термической обработки (х500)
Fig. 7. The microstructure of a sample of 1.2067 steel after heat treatment (х500)
Определение оптимального режима вторичной термической обработки
Наиболее желательной при закалке ТПЧ является исходная структура в виде сорбита или мелкопластинчатого перлита, что соответствует твердости 250-315 НВ. С этой целью после отжига на образцах целесообразно проводить сорбитизацию. Сорбитизация проводилась с температуры 860, 880, 900 ºС + отпуск при температуре 570 ºС.
Результаты оценки микроструктуры и балла действительного зерна представлены в табл. 2.
Таблица 2. Результаты оценки микроструктуры
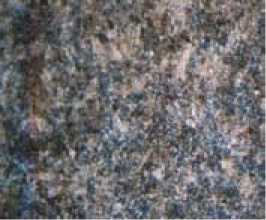
Рис. 8. Микроструктура образцов из стали 75ХМФ после термической обработки (х500)
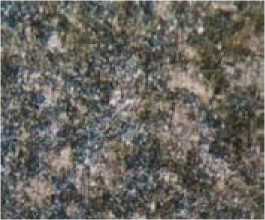
Рис. 9. Микроструктура образцов из стали 75ХМФ после термической обработки (х500)
Fig. 8. The microstructure of a sample of 1.2067 steel after heat treatment (х500)
Fig. 9. The microstructure of a sample of 1.2067 steel after heat treatment (х500)
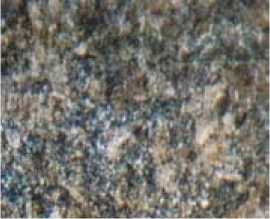
Рис. 10. Микроструктура образцов из стали 75ХМФ после термической обработки (х500)
Table 2. Results of microstructure study
Проводимая термическая обработка |
Карбидная сетка, балл |
Микроструктура |
Балл действительного зерна |
Отжиг при 850 ºС (в течение 2 ч) |
2,5 |
Зернистый перлит + карбиды (рис. 2) |
8-7 |
Сорбитизация с температуры 8600 ºС (выд. 1 ч) + отпуск при 570 ºС (выд. 1,5 ч) |
2,0 |
Сорбит + карбиды (рис. 8) |
8-7 |
Сорбитизация с температуры 880 ºС (выд. 1 ч) + отпуск при 570 ºС (выд. 1,5 ч) |
2'0 |
Сорбит + карбиды (рис. 9) |
8-7 |
Сорбитизация с температуры 900 ºС (выд. 1 ч) + отпуск при 570 ºС (выд. 1,5 ч) |
2,0 |
Сорбит + карбиды (рис. 10) |
8-7 |
Fig. 10. The microstructure of a sample of 1.2067 steel after heat treatment (х500)
На других образцах после термообработки проведена вторичная термообработка - нормализация при 960-970 ºС + нормализация при 850-880 ºС + отпуск при 600-620 ºС.
Результаты оценки микроструктуры и балла действительного зерна отражены в табл. 3.
На следующих образцах после термообработки проведена сорбитизация с температуры 860, 880, 900 ºС + отпуск при температуре 570 ºС.
Таблица 3. Результаты оценки микроструктуры
Table 3. Results of microstructure study
Проводимая термическая обработка |
Карбидная сетка, балл |
Микроструктура |
Балл действительного зерна |
Нормализация при 940-960 ºС (выд. 30 мин) + нормализация при 840-860 ºС (выд. 20 мин) + отпуск при 670-690 ºС (выд. 50 мин) |
2,5 |
Зернистый перлит + карбиды (рис. 3) |
8-7 |
Нормализация при 960-970 ºС (выд. 1 ч) + нормализация при 850-880 ºС (выд. 20 мин) + отпуск при 600-620 ºС (выд. 4,5 ч) |
2,0 |
Сорбит + карбиды (рис. 11) |
8-7 |
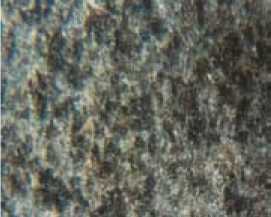
Рис. 11. Микроструктура образцов из стали 75ХМФ после термической обработки (х500)
Fig. 11. The microstructure of a sample of 1.2067 steel after heat treatment (х500)
Результаты оценки микроструктуры и балла действительного зерна представлены в табл. 4.
Еще на одних образцах после термообработки проведена сорбитизация с температуры 860, 880, 900 ºС + отпуск при температуре 570 ºС.
Таблица 4. Результаты оценки микроструктуры
Table 4. Results of microstructure study
Проводимая термическая обработка |
Карбидная сетка, балл |
Микроструктура |
Балл действительного зерна |
Нормализация при 940-960 ºС (выд. 30 мин) + нормализация при 840-860 ºС (выд. 20 мин) + отпуск при 670-690 ºС (выд. 50 мин) |
2,5 |
Зернистый перлит + карбиды (рис. 3) |
8-7 |
Сорбитизация с температуры 860 ºС (выд. 1 ч) + отпуск при 570 ºС (выд. 1,5 ч) |
2,0 |
Сорбит + карбиды (рис. 12) |
8-7 |
Сорбитизация с температуры 880 ºС (выд. 1 ч) + отпуск при 570 ºС (выд. 1,5 ч) |
2,0 |
Сорбит + карбиды (рис. 13) |
8-7 |
Сорбитизация с температуры 900 ºС (выд. 1 ч) + отпуск при 570 ºС (выд. 1,5 ч) |
2,0 |
Сорбит + карбиды (рис. 14) |
8-7 |
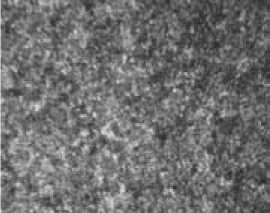
Рис. 12. Микроструктура образцов из стали 75ХМФ после термической обработки (х500)
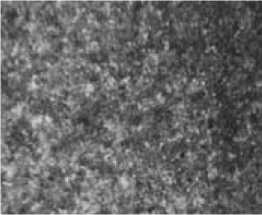
Рис. 13. Микроструктура образцов из стали 75ХМФ после термической обработки (х500)
Fig. 12. The microstructure of a sample of 1.2067 steel after heat treatment (х500)
Fig. 13. The microstructure of a sample of 1.2067 steel after heat treatment (х500)
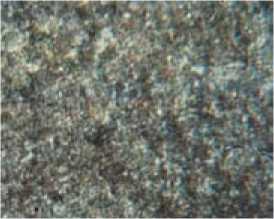
Рис. 14. Микроструктура образцов из стали 75ХМФ после термической обработки (х500)
Fig. 14. The microstructure of a sample of 1.2067 steel after heat treatment (х500)
Результаты оценки микроструктуры и балла действительного зерна представлены в табл. 5.
При проведении сорбитизации с температуры 900 °С на образцах образовывались трещины по поверхности. Таким образом, наиболее оптимальная температура сорбитизации 860 ºС.
Таблица 5. Результаты оценки микроструктуры
Table 5. Results of microstructure study
Проводимая термическая обработка |
Карбидная сетка, балл |
Микроструктура |
Балл действительного зерна |
Нормализация при 960-970 ºС (выд. 1 ч) + нормализация при 850-880 ºС (выд. 20 мин) + отпуск при 600-620 ºС (выд. 4,5 ч) |
2 5 , |
Зернистый перлит + карбиды (рис. 4) |
8-7 |
Сорбитизация с температуры 860 °С (выд. 1 ч) + отпуск при 570 ºС (выд. 1,5 ч) |
2,0 |
Сорбит + карбиды (рис. 15) |
8-7 |
Сорбитизация с температуры 880 °С (выд. 1 ч) + отпуск при 570 ºС (выд. 1,5 ч) |
2,0 |
Сорбит + карбиды (рис. 16) |
8-7 |
Сорбитизация с температуры 900 °С (выд. 1 ч) + отпуск при 570 ºС (выд. 1,5 ч) |
2,0 |
Сорбит + карбиды (рис. 17) |
8-7 |
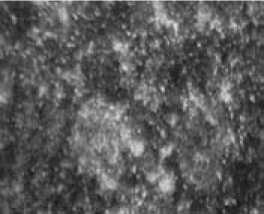
Рис. 15. Микроструктура образцов из стали 75ХМФ после термической обработки (х500)
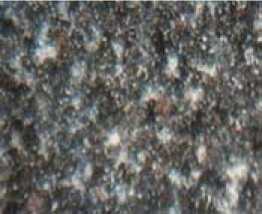
Рис. 16. Микроструктура образцов из стали 75ХМФ после термической обработки (х500)
Fig. 15. The microstructure of a sample of 1.2067 steel after heat treatment (х500)
Fig. 16. The microstructure of a sample of 1.2067 steel after heat treatment (х500)
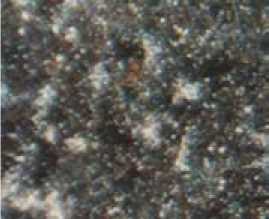
Рис. 17. Микроструктура образцов из стали 75ХМФ после термической обработки (х500)
Fig. 17. The microstructure of a sample of 1.2067 steel after heat treatment (х500)
Определение температуры закалки, времени выдержки и скорости охлаждения
На образцах, прошедших первичную и вторичную термическую обработку, были проведены режимы закалки с выдержкой 1 ч:
-
• закалка в холодную воду с температуры 860 ºС;
-
• закалка в холодную воду с температуры 880 ºС;
-
• закалка в холодную воду с температуры 900 ºС;
-
• закалка в холодную воду с температуры 920 ºС;
-
• закалка в холодную воду с температуры 950 ºС.
Результаты оценки микроструктуры и балла действительного зерна отражены в табл. 6.
Анализируя полученные результаты, можно сделать вывод, что нагрев под закалку ТПЧ необходимо производить до температуры 900 ºС. Охлаждение с температур закалки должно быть ускоренным, а значит, холодной водой (температура воды 15 ºС и ниже), так как ускоренное охлаждение обеспечивает получение структуры мартенсит или троостомартенсит с твердостью 650-700 НВ.
Таблица 6. Результаты оценки микроструктуры
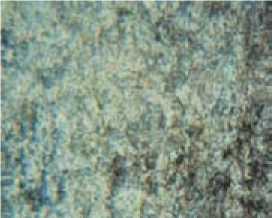
Рис. 18. Микроструктура образцов из стали 75ХМФ после термической обработки (х500)
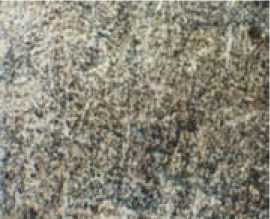
Рис. 19. Микроструктура образцов из стали 75ХМФ после термической обработки (х500)
Fig. 18. The microstructure of a sample of 1.2067 steel after heat treatment (х500)
Fig. 19. The microstructure of a sample of 1.2067 steel after heat treatment (х500)
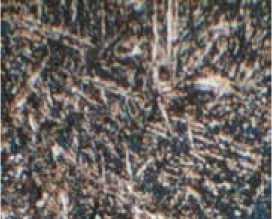
Рис. 20. Микроструктура образцов из стали 75ХМФ после термической обработки (х500)
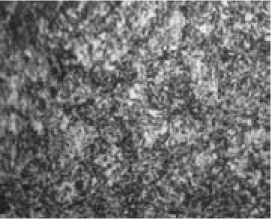
Рис. 21. Микроструктура образцов из стали 75ХМФ после термической обработки (х500)
Fig. 20. The microstructure of a sample of 1.2067 steel after heat treatment (х500)
Fig. 21. The microstructure of a sample of 1.2067 steel after heat treatment (х500)
Table 6. Results of microstructure study
Режим закалки |
Микроструктура |
Твердость, НВ |
Закалка в холодную воду с температуры 860 ºС |
Троостомартенсит + карбиды (рис. 18) |
606-637 |
Закалка в холодную воду с температуры 880 ºС |
Троостомартенсит + карбиды (рис. 19) |
637-645 |
— Закалка в холодную воду с температуры 900 ºС |
Мартенсит + троостомартенсит + карбиды (рис. 20) |
645-665 |
Закалка в холодную воду с температуры 920 ºС |
Троостомартенсит + остаточный аустенит + карбиды (рис. 21) |
576-637 |
Закалка в холодную воду с температуры 950 ºС |
Троостомартенсит + остаточный аустенит + карбиды (рис. 22) |
613-641 |
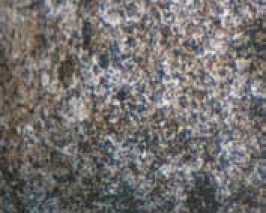
Рис. 22. Микроструктура образцов из стали 75ХМФ после термической обработки (х500)
Fig. 22. The microstructure of a sample of 1.2067 steel after heat treatment (х500)
Список литературы Определение оптимальных режимов термической обработки валков станов холодной прокатки через исследование их влияния на микроструктуру и свойства заготовки
- Гедеон М.В. Термическая обработка валков холодной прокатки. М.: Металлургия, 1973. 344 с
- Сорокин В.Г, Гервасьев М.А. Стали и сплавы. Марочник: Справ. изд-е. М.: Интермет Инжиниринг, 2001. 382 с
- Третьяков A.B. Валки обжимных, сортовых и листовых станов. М.: Интернет инжиниринг, 1999. 80 с